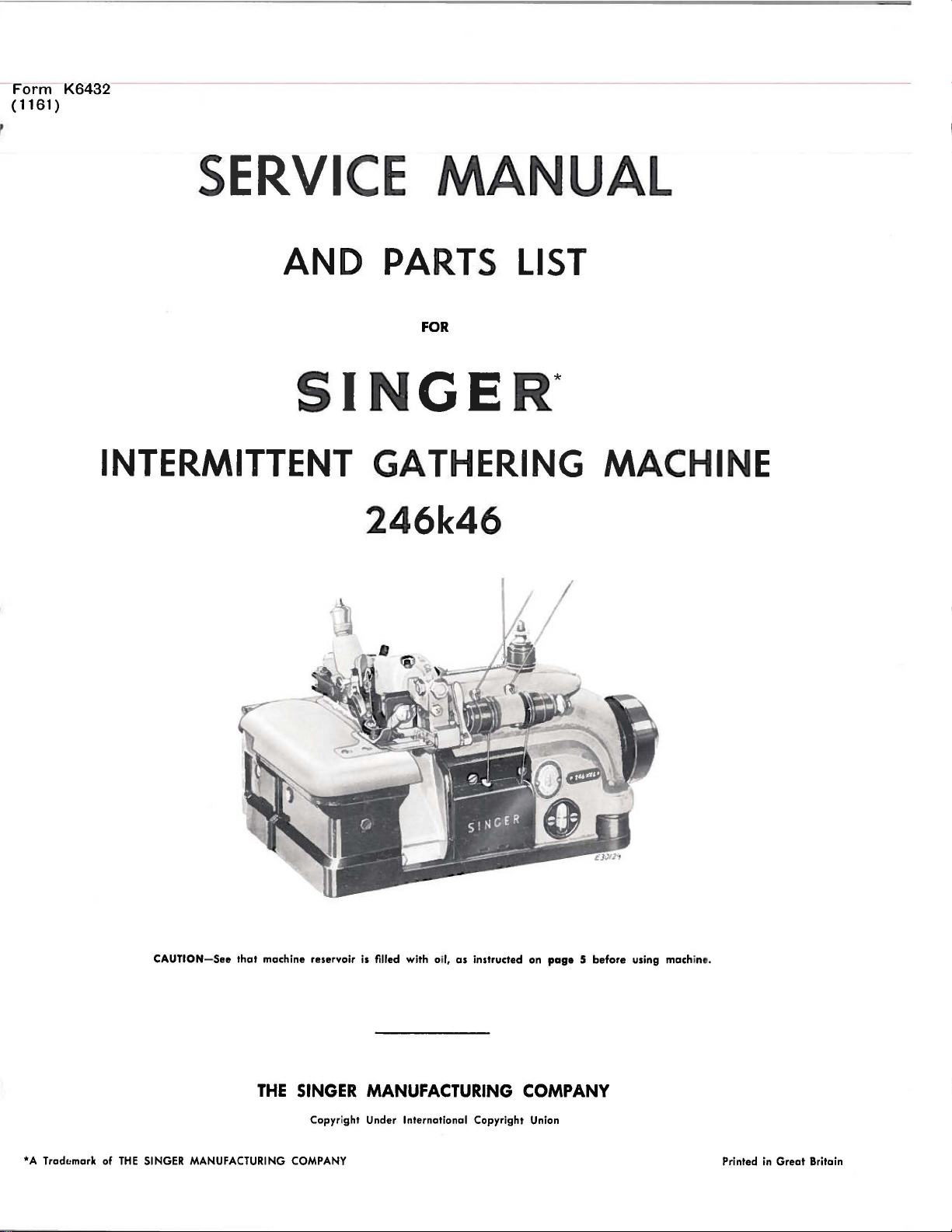
Form
(1161)
r
K6432
SERVICE
AND
PARTS
MANUAL
LIST
FOR
SINGER*
INTERMITTENT GATHERING MACHINE
246k46
*A
Trad<:mark of
CAUTION-
THE
SINGER MANUFACTURING COMPANY
See
that
machine
THE
reservoir
SINGER
Copyri
ght
is filled
with oil,
as
instructed
MANUFACTURING
Under
lnternotional
Copyright
on
page 5 before
COMPANY
Union
using
mach
ine.
Printed
in
Great
Britain
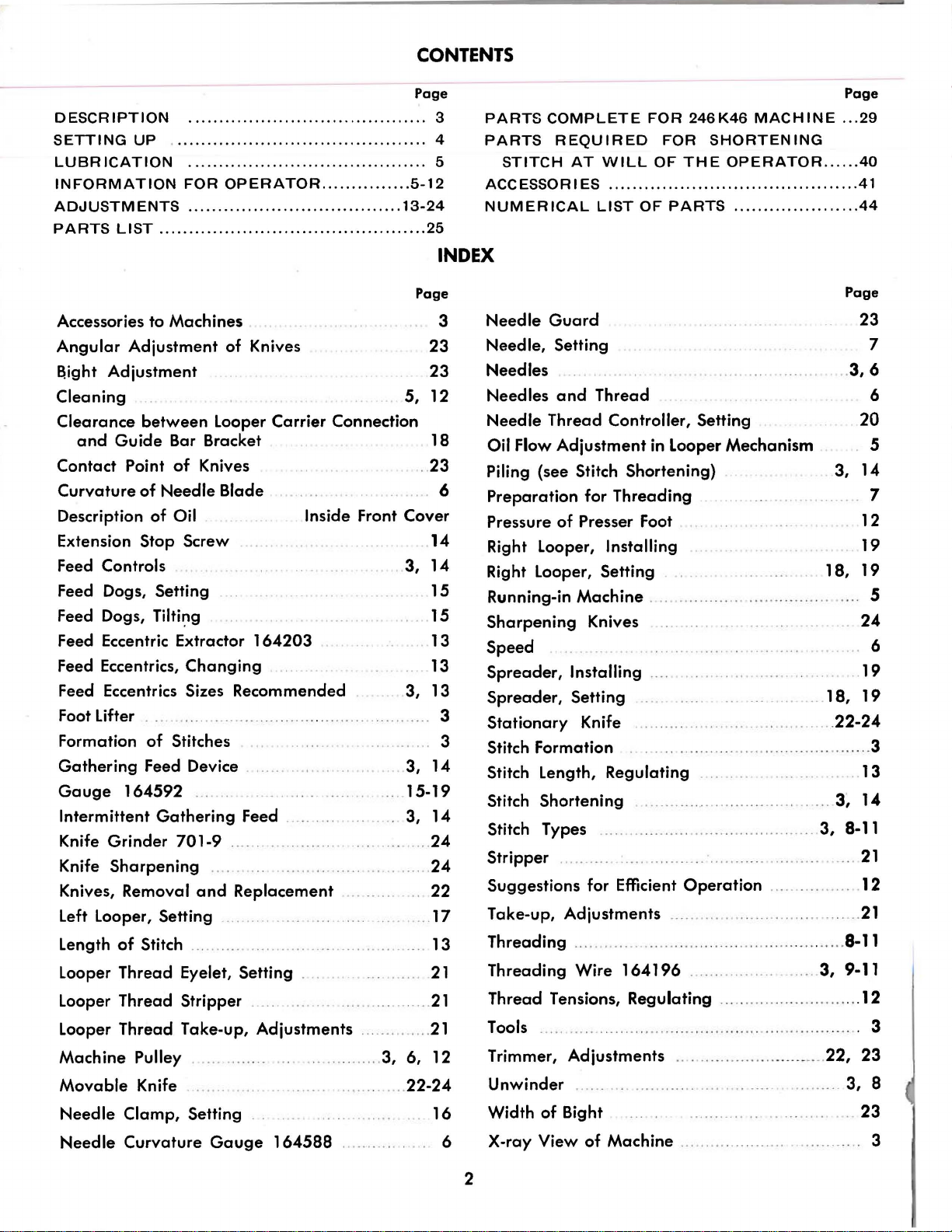
CONTENTS
Page
DESCRIPTION
SETTING
LUBRICATION
INFORMATION
ADJUSTMENTS ...................
PARTS
UP ......................
LIST .............................................
. ...
....................................
.....................
. .......................................
FOR
OPERATOR ...........
.................
....
4
5
5-12
13-24
25
Page
Accessories to Machines . . .
Angular
aight
Adjustment of Knives
Adjustment
23
23
Cleaning 5, 12
Clearance
and
Contact Point
Curvature
Description
Extension Stop Screw
Feed
Feed Dogs, Setting
Feed Dogs,
Feed Eccentric Extractor
Feed Eccentrics,
between
Guide
of
of
Controls
Tilti':lg
Looper Carrier Connection
Bar Bracket 18
of
Knives
..
23
Needle Blade . . . . 6
Oil
Inside Front Cover
14
3,
14
15
15
13
.
..
13
Changing
164203
...
Feed Eccentrics Sizes Recommended 3, 13
Foot Lifter . . . . . . . . . . . . . . . . . . . . . . . . . . . . . . . . . . . . . . . . . . . . . . .
Formation
Gathering
Gauge
Intermittent
Knife Grinder
Knife
Knives, Removal
Left Looper, Setting
Length
looper
Looper Thread Stripper .
of
Stitches . . .
Feed Device . . .
164592 ...
Gathering
701-9
Sharpening
of
Stitch . .
.... . . .
and
..
..
..
.. .. .. ..
..
..
. ...........
Feed
....
..
. ...
..
Replacement ... ......
..
.. ..
.. . ...
.....
Thread Eyelet, Setting .
..
. . .
.. . ..
. . .
..
..
..
. . .
..
. . . .
..
.. .. . .......
..
..
.. .. . .. . ..
. .
...........
..
. . .
..
. . . .
.. .. ..
.....
Looper Thread Take-up, Adjustments
..
. . . . 3
..
. . . 3
. . . .
..
3,
.. ..
15-19
.. ..
3, 14
...
...
. .. . .
.....
.. . ..
........... 13
..
. . .
.. . 21
...... ........
...........
..
..
..
14
24
24
22
17
21
21
3
PARTS
PARTS
ACCESSORIES
NUMERICAL
INDEX
3
Page
COMPLETE
REQUIRED
STITCH
Needle
AT
LIST
Guard
Needle, Setting
Needles
Needles
..
and
. .
Thread
Needle Thread Controller, Setting
Oil Flow Adjustment
FOR
246K46
FOR
WILL
OF
THE
.........................................
OF
PARTS ....................
MACHINE
SHORTENING
OPERATOR
....
in
Looper Mechanism . 5
...
29
...... 40
. 41
.44
Page
23
.3, 6
20
7
6
Piling (see Stitch Shortening) 3, 14
Preparation for Threading .
Pressure
Right
of
Presser Foot
looper,
Installing
Right Looper, Setting . .
Running-in Machine . .
Sharpening
Knives
Speed
Spreader,
Spreader,
Stationary
Installing ....
Setting
Knife
Stitch Formation .
Stitch
length,
Regulating . .
.. ..
.. . ..
..
.......... ......... ....
..
...
..
..
..
..
....
.. .........
Stitch Shortening ...... ..........
.. ..
..
.. .. ..
..
Stitch Types
Stripper
..
.. . ..
. . . .
.. . ..
..
..
. .
.. ..
Suggestions for Efficient
Take-up, Adjustments
Threading ....
Threading Wire
..............................................
164196 . ..
Thread Tensions,
Tools
............
................................................. 3
..
Regulating ............................
..
. . .
..
..
. . .
..
..
..
.. . 7
..
..
..
. .
....
.... .
.. ..
.. . .. . ..
..
......
..
..
. .
..
. .
..
. .
....
. .
..
.... .
..
...
...........
...
18, 19
.. ..
..
. .
..
..
. .... . . 24
..
. . . 6
.. . ..
18, 19
..........
22-24
................................. 3
.. ..
..
.. ....
..
. . . 13
..
..........
..
..
.. .. . .. . .. ..
..
..
. . .
..
..
.. .. . ..
Operation
... ...
3,
.... .
..
3,
.......
.....
. . . . . . . . . . . . . . . . 12
..................................
..
..
..
..
..
..
. . . ...
3,
12
19
..
. .19
14
8-11
21
21
8-11
9-11
12
5
Machine Pulley .
Movable
Knife . .
..
...
..
..
Needle Clamp, Setting
Needle
Curvature
Gauge
....
. . .
.....
..
..
..
164588
...
............. 3, 6, 12
..
.... . . .
...........
...............
22-24
... 16
Trimmer, Adjustments .................... ........
Unwinder
6
Width
X-ray View
of
Bight
2
....................
of
Machine
..............
..
..
.. . ..
.. . ..
.........
..
.. . ..
..
22,
23
. .
3,
8
..
23
..
..
. . .
.. ..
3
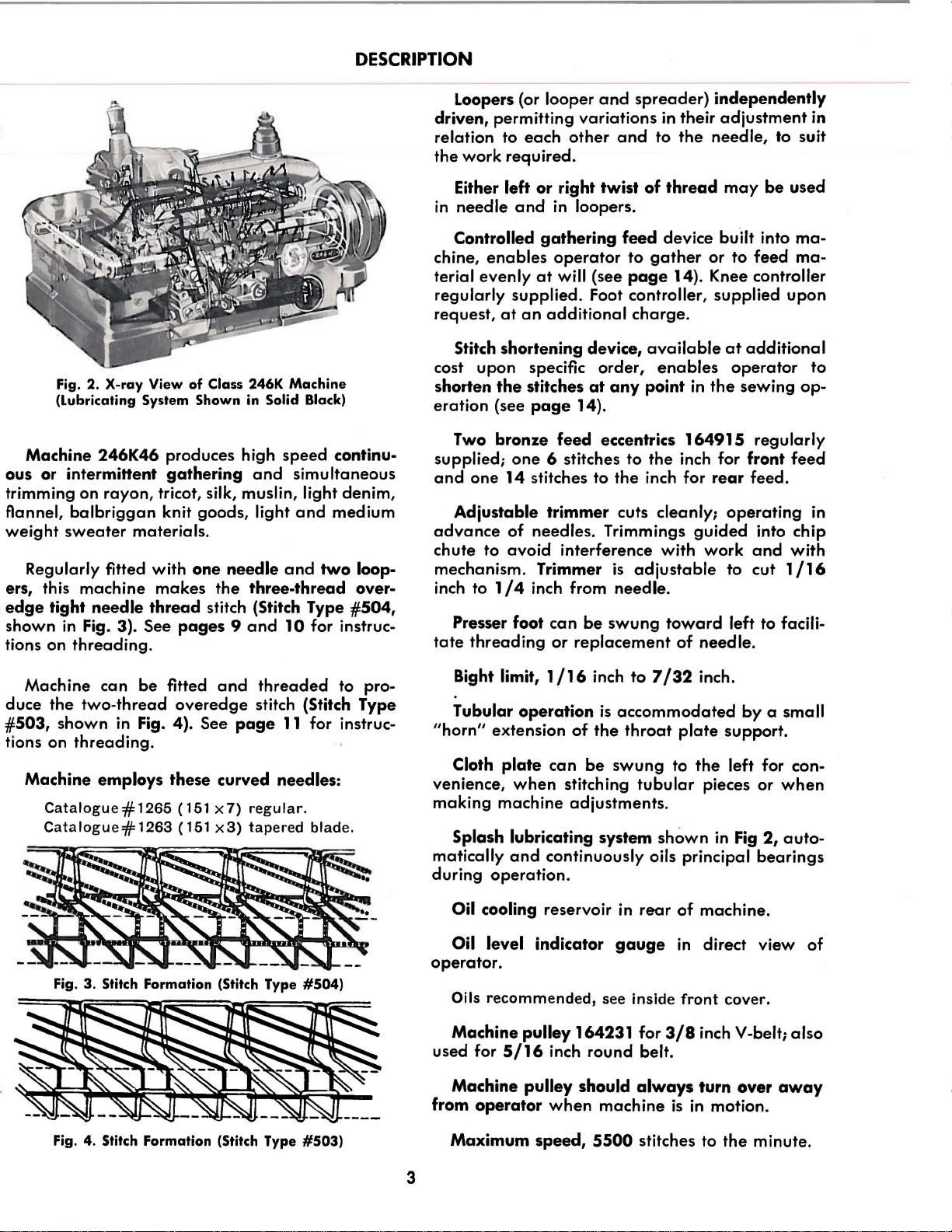
DESCRIPTION
Fig. 2. X-ray View
(Lubricating
System Shown in Solid Black)
of
Class 246K Machine
Machine 246K46 produces high
ous or intermittent
trimming on rayon, tricot,
Aannel,
weight
balbriggan
sweater
Regularly
fltted with
ers, this machine
edge
tight
needle
shown
tions on
in
Fig. 3). See
threading.
gathering
silk, muslin, light denim,
knit goods, light
materials.
one
makes
thread
the
stitch (Stitch Type
pages 9 and
speed
and
needle
and
three-thread
10
continu-
simultaneous
and
medium
two
loopÂover-
#504,
for instruc-
Loopers (or looper
driven, permitting variations
relation to
each
and
other
spreader)
in
and
to
the work required.
Either
in
needle
Controlled
chine,
terial evenly
regularly supplied.
request,
Stitch shortening device,
cost upon specific order,
shorten
eration
Two bronze
supplied;
and
left
enables
at
the
(see
one
14
or
right
twist
of
thread
and
in
loopers.
gathering
operator
at
will (see
feed
device built into
to
gather
page
Foot controller, supplied
an
additional
charge.
available
enables
stitches
page
one
stitches to
at
any
point
14).
feed
eccentrics
6 stitches to the inch for front
the
inch for
Adjustable trimmer cuts cleanly;
advance
chute to
mechanism. Trimmer
inch to
Presser foot
tate
of
needles. Trimmings
avoid
1/4
inch from needle.
threading
interference with
is
adjustable
can
be
swung
or
replacement
toward
independently
their
adjustment
the
needle, to suit
may
be
in
used
ma-
or
to
feed
ma-
14). Knee controller
upon
at
additional
operator
in
the
164915
sewing op-
regularly
to
feed
rear
feed.
operating
guided
work
to cut
into chip
and
in
with
1/16
left to facili-
of
needle.
Machine can
duce the
#503,
tions on
two-thread
shown
threading.
Machine employs
Catalogue#1265
Catalogue:tf:1263
Fig. 3. Stitch Formation (Stitch Type
be
fltted
overedge
in
Fig. 4). See
these
and
page
curved needles:
(151
x7)
regular.
(151
x3)
tapered
threaded
to pro-
stitch (Stitch Type
11
for instruc-
blade.
#504)
Bight limit,
Tubular
"horn"
extension
Cloth
venience,
making
machine adjustments.
1/16
operation
plate
can
when
inch
is
of
the
be
stitching
Splash lubricating system
matically
during
and
continuously oils principal
operation.
Oil cooling reservoir
Oil level indicator
operator.
Oils
recommended,
see
Machine pulley 164231 for
used for
Machine
from
5/16
pulley should
operator
inch round belt.
when
machine
to
7/32
inch.
accommodated
throat
swung
in
gauge
inside
plate
to
tubular
shown
rear
of
in
front
3/8
always
is
the
pieces or
in
machine.
direct view
inch V-belt;
turn
in
motion.
by
a small
support.
left for con-
when
Fig
2,
auto-
bearings
cover.
also
over
away
of
Fig. 4. Stitch Formation (Stitch Type
#503)
Maximum
speed,
3
5500
stitches to
the
minute.

Drill Holes (
to
Accommodate
\.._~for
3
A inch Diameter)
lnt~rmittent~
VGathermg
Feed Lever
#6
Flat
Head
1 inch
Wood
Fig. 5. Machine Base on Table, Showing Position
Screws
of
INSTALLATION
Chai~n
*Shortening
~'k"for
Lifting Lever
Holes Required
for
for
Stitch
Presser
#8
Round
*
inch
Wood
Installation
Device
Foot
Head
Screws
Wood
and
Drill Sizes
#7
Flat
Head
3
A inch
BELT
Screws
GUARD
INSTALLATION
OF
MACHINE
TABLE
Place
machine
groove
of
rectly
for intermittent
chain for stitch shortening device,
use,
machine
eter,
and
shown
with
of
of
machine
driving pulley.
Spot
position
below
Spot
position
as
instructed in Fig.
Remove
Drill all holes
to
Using
drill six holes
Fasten
the
Set
base.
machine
base
accommodate
base
in
Fig. 5
machine
six
machine
and
base
pulley
of
hole
cl--ain
slot
on
of
hole either
gathering
from
in position on
spotted
chains.
and
belt
in
table
base
wood
screws, described in Fig.
on
rubber
on
table
in
line
behind
presser foot lifting lever.
feed
5.
earlier,
guard
and
cushions
machine
in
lever
base.
top
as
for
belt
AND
with
3/4
wood
BASE
top
with belt
belt
groove
base,
line with chain
or
in
line with
to
suit device
Draw outline
of
table.
inch
in
template,
screws,
guard
at
to
four corners
ON
di-
in
of
diam-
spot
as
table
5.
FOOT
Machines with foot
lifter
treadle,
ever,
equipment
orders
is
extra
ACCESSORIES
specified on order.
nut).
nut).
bar
thread.
228706
supplied
cific order.
LIFTER:
As
the
stand
treadle,
will
the
machine
which
should
reqvired
Foot lifter. Knee lifter supplied
Threading
Tweezers
Socket
Flat,
Screwdriver
Wrench 164831 (for right looper carrier
oil plug screw nut).
Thread
Thread
and
charge.
wrench
open-end
unwinder
unwinder
(three-thread) for nylon
instead
recommended
lifter includes a
foot lifter chain
be
sent
with
is
fitted to a
does
not
state
that
foot lifter.
it
will also
AND
wire
164204.
85318.
TOOLS
164196.
164197
wrench
151 031 for
228705
of
regular
for Class 246K
suitable
6439,
the
machine. If, how-
stand
have a suitable
treadle
be
supplied,
instead,
(for
needle
8908
(for
feed
two
(two-thread)
threads
unwinder,
without
or
treadle,
without
when
clamping
eccentric
guide
or th rea-
will
upon
foot
the
other
4885
or
be
spe-
CAUTION
All
of
the
oil
is
ON
DO
PAGE
NOT
5.
drained
START
from
THE
the
machine
MACHINE
UNTIL
before
IT
HAS
it is
BEEN
shipped
THOROUGHLY
from
the
fadory.
LUBRICATED
AS
INSTRUCTED
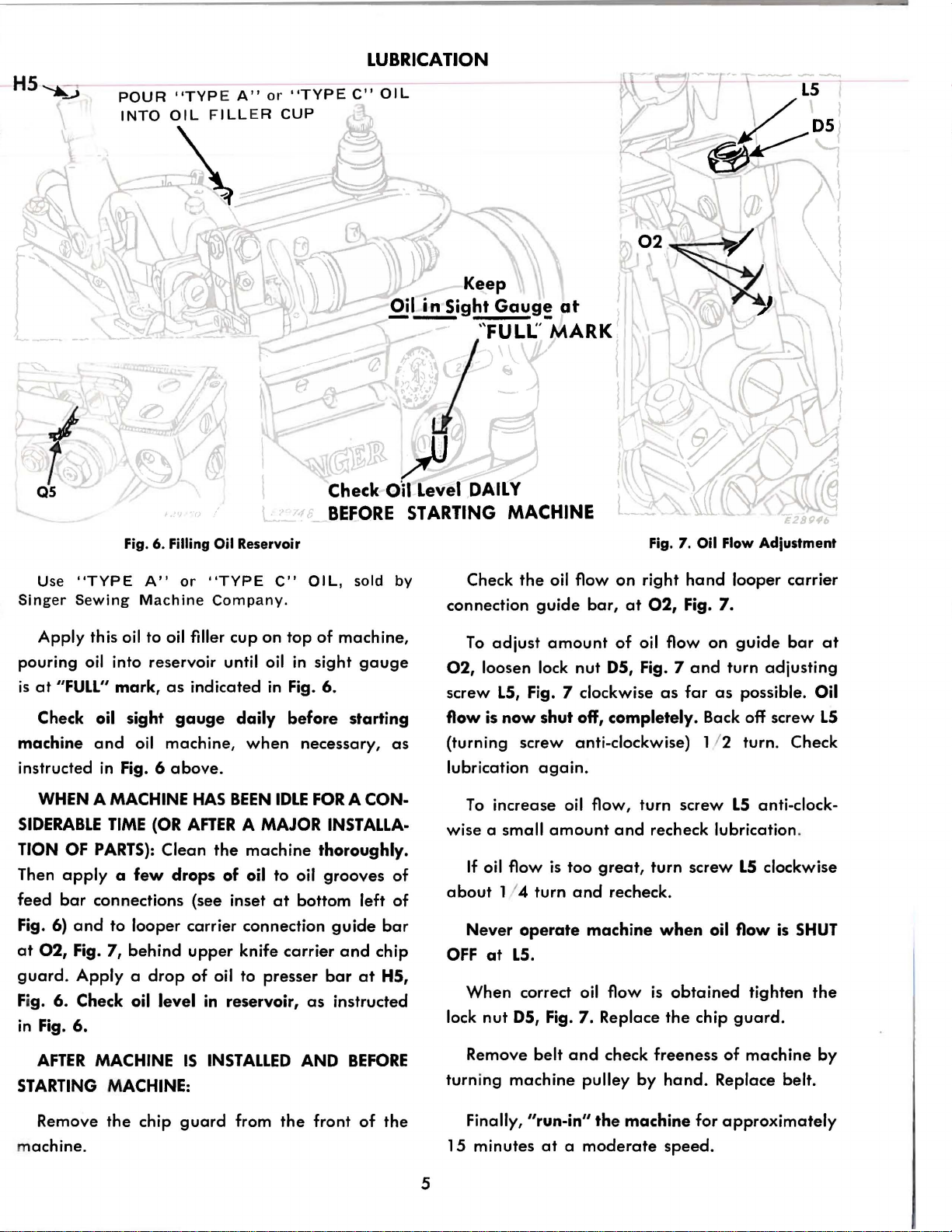
HS
.....:
LUBRICATION
_,
Fig. 6. Filling Oil Reservoir
Use
Singer
"TYPE
Sewing
A"
Machine
Apply this oil to oil filler
pouring
is
at
Check oil
machine
instructed
oil into reservoir until oil
"FULL"
mark,
sight
and
oil machine,
in
Fig. 6
as
gauge
above.
WHEN A MACHINE
SIDERABLE
TION OF
Then
feed
bar
Fig. 6)
at
02,
guard.
Fi
g.
6.
in
Fig.
TIME
(OR
PARTS):
apply a few
Clean
drops
connections (see inset
and
to looper carrier connection
Fig.
7,
behind
Apply a drop
Check oil level
6.
or
"TYPE
Company
cup
indicated
daily
HAS
BEEN
AFTER
A MAJOR
the
of
upper
of
knife
oil to presser
in
reservoir,
C"
.
on
top
in
in
Fig.
before
when
necessary,
IDLE
machine
oil to oil
at
bottom left
carrier
OJ
L,
sold
of
machine,
sight
gauge
6.
starting
FOR
A CON-
INSTALLA-
thoroughly.
grooves
guide
and
chip
bar
at
as
instructed
by
as
of
of
bar
HS,
Fig. 7. Oil Flow Adjustment
Check
connection
To
02,
screw
flow is
the
oil flow
guide
adjust
amount
loosen lock
LS,
Fig. 7 clockwise
now
shut
on
right
bar,
nut
DS, Fig. 7
at
of
oil flow
02,
as
hand
Fig.
far
looper carrier
7.
on
guide
and
turn
as
possible. Oil
bar
adjusting
off, completely. Back off screw
at
LS
(turning screw anti-clockwise) 1 12 turn. Check
lubrication
To
wise a small
If
oil flow
about
Never
OFF
at
When
lock
nut
again.
increase oil flow, turn screw
amount
is
1/4 turn
operate
too
great,
and
machine
and
recheck lubrication.
turn
screw
recheck.
when
oil flow is
LS.
correct oil flow
DS, Fig.
7.
Replace
is
obtained
the
chip
LS
anti-clock-
LS
clockwise
tighten
guard.
SHUT
the
AFTER
STARTING
Remove
machine.
MACHINE
MACHINE:
the
chip
IS
INSTALLED
guard
from
the
AND
front
BEFORE
of
the
Remove
turn ing
Finally,
15 minutes
belt
machine
"run-in"
at a moderate
5
and
pulley
check
the
freeness
by
hand.
machine
speed.
of
machine
Replace belt.
for
approximately
by
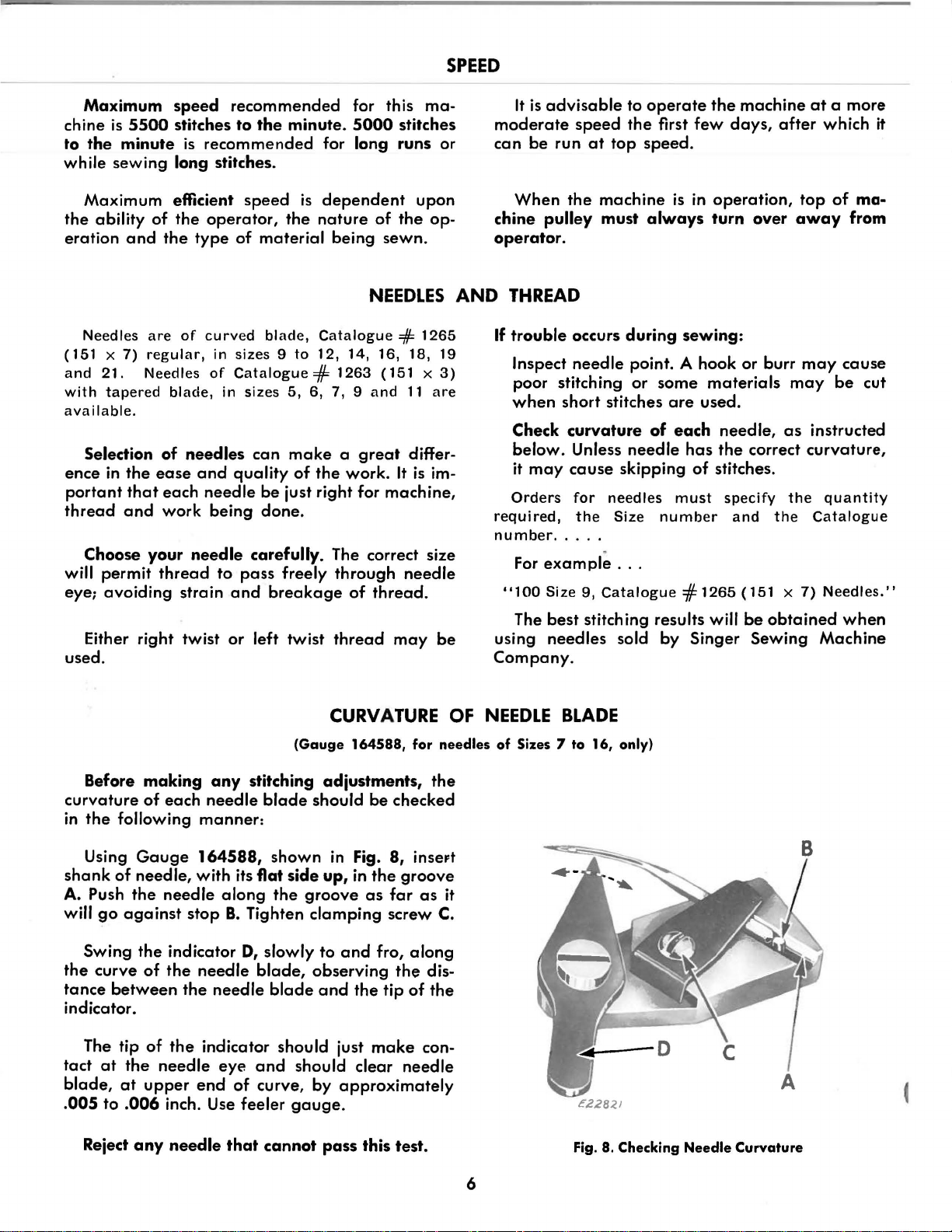
Maximum
chine
to
while
is
the
sewing
5500
minute
speed
stitches to
is
recommended
the
recommended
long stitches.
for this
minute.
5000
for long runs or
SPEED
ma-
stitches
It
is
advisable
moderate
can
be
run
speed
at
top
to
operate
the
speed.
first
the
few
machine
days,
at a more
after
which it
Maximum
the
ability
eration
Needles
(151 x 7)
and
21.
with
available.
Selection
ence
portant
thread
Choose
will permit
eye;
avoiding
and
are
regular,
Needles
tapered
in
the
that
and
your
of
the
blade,
of
ease
each
work
thread
Either right twist
used.
efficient
the
operator,
type
of
curved
in
of
in
needles
and
needle
being
needle
to
strain
speed
of
is
the
material
dependent
nature
being
of
sewn.
the
NEEDLES
blade,
sizes 9
Catalogue=#=
sizes 5,
can
quality
be
done.
carefully. The correct size
pass
and
breakage
or
left twist
Catalogue
to
12,
14, 16, 18, 19
1263
6,
7, 9
and
make a great
of
the
work.
just right for
freely
through
of
thread.
thread
=/1=
(151 x 3)
It
machine,
needle
may
upon
op-
1265
11
are
differ-
is
im-
be
AND
When
chine
the
pulley
operator.
THREAD
If
trouble
Inspect
poor stitching
when
Check
below.
it
Orders
required,
number
For
"1
00
The
using
Company
short
curvature
may
cause
.....
example
Size 9,
best
needles
.
occurs
needle
Unless
for
machine
must
during
is
always
sewing:
in
point. A hook
or
the
stitches
of
needle
skipping
needles
Size
some
number
ore
each
has
of
must
materials
used.
...
Catalogue # 1265
stitching results will
sold by Singer
operation,
turn
over
or
burr
needle,
the
correct
stitches.
specify
and
the
( 151 x
be
obtained
Sewing
top
of
away
may
may
as
instructed
curvature,
the
quantity
Catalogue
7)
Needles."
Machine
ma-
from
cause
be
cut
when
Before
curvature
in
the
following
Using
shank
of
A. Push
will
go
against
Swing
the
curve
tance
between
indicator.
The tip
tact
at
the
blade,
.005
to
at
.006
Reject
making
of
each
needle
manner:
Gauge
needle,
the
164588,
with
needle
stop
the
indicator
of
the
needle
the
of
the
indicator should just
needle
upper
end
inch. Use feeler
any
needle
any
stitching
its flat
along
B.
Tighten
D,
needle
eye
of
that
(Gauge
blade
should
shown
side
the
groove
clamping
slowly to
blade,
and
observing
blade
and
should clear
curve, by
gauge.
cannot
CURVATURE
164588,
adjustments,
in
Fig. 8, inseFt
up,
in
as
and
the
approximately
pass
this
be
checked
the
groove
for
screw C.
fro,
the
tip
make
needle
test.
for
as
along
of
con-
OF
needles
the
it
dis-
the
NEEDLE
of
BLADE
Sizes 7 to 16, only)
E228:<.1
Fig. 8. Checking
Needle
Curvature
6
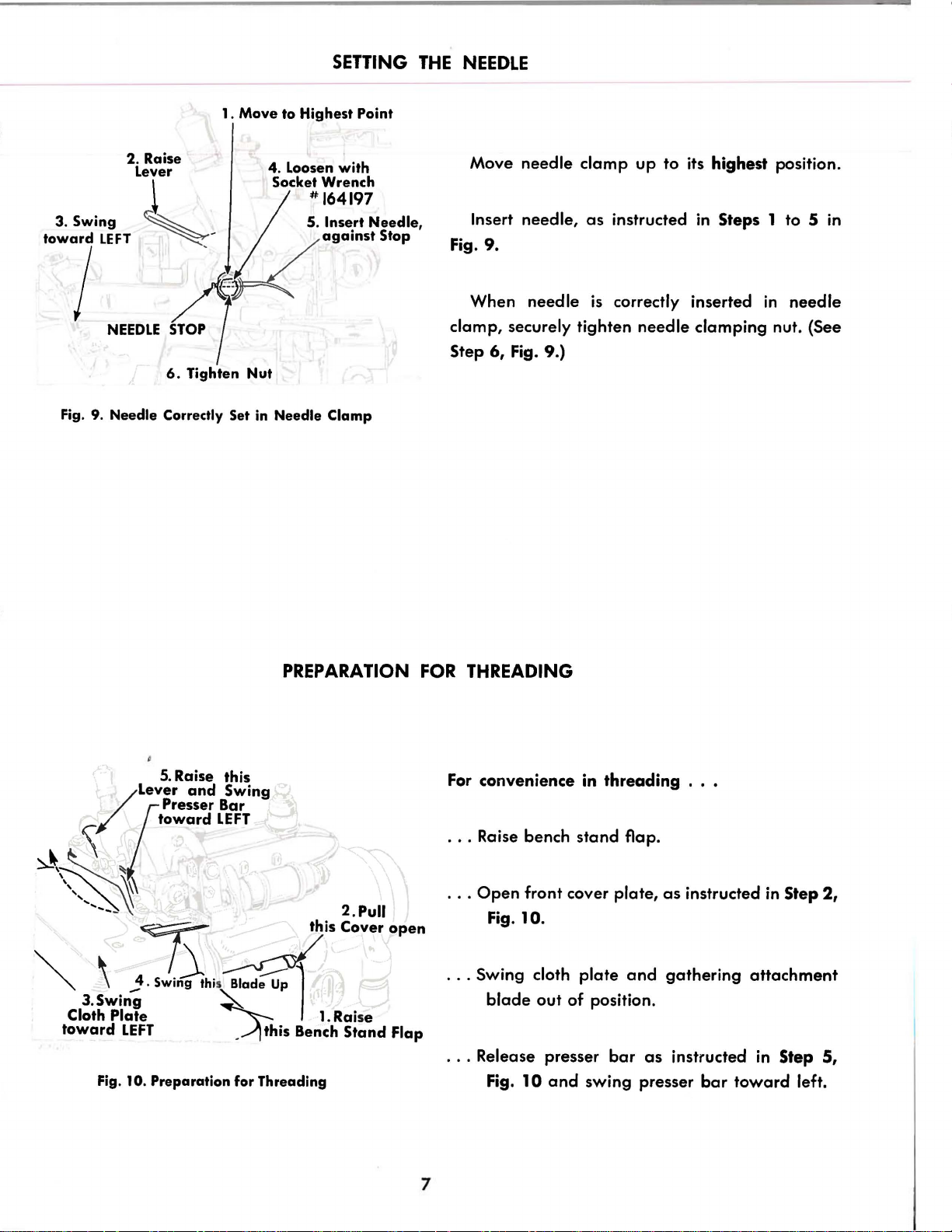
SETTING
1. Move to Highest Point
THE
NEEDLE
2. Raise
Lever 4.
1 / Socke!
3.
Swing ' 5.
towi
LEFT
NEEDLE
Fig.
9. Needle Correctly
STOP
6.
Tighten Nut
Set
Loosen
:419~
lns~rt
in
Needle Clamp
with
Needle,
Move
Insert
Fig.
9.
When
clamp,
Step
6,
needle
needle,
needle
securely
Fig.
9.)
clamp
as
tighten
up
instructed
is correctly
needle
to
its
inserted
clamping
highest
in
Steps
position.
1 to 5 in
in
needle
nut.
(See
/
\
\
~
~
~
~
\ j . Swing this Blade
l.Swing
Cloth Plate
toward
Fig.
PREPARATION
5.
Raise this
Lever
!
~\
and
Presser Bar
toward
Swing
LEFT
~
!i
LEFT
10. Preparation for Threading
~
Up
l
~
~
_,-~this
Bench
2.Pull
Is
Cover
1. Raise
Stand
FOR
For
...
...
open
_,;
Flap
...
...
THREADING
convenience
Raise
bench
Open
Swing
Release
front
Fig. 10.
cloth
blade
Fig.
10
cover
out
of
presser
and
in
threading
stand
plate,
plate
position.
bar
swing
flap.
and
as
presser
. . •
as
instructed
gathering
instructed
bar
in
Step
attachment
in
Step
toward
2,
5,
left.
7
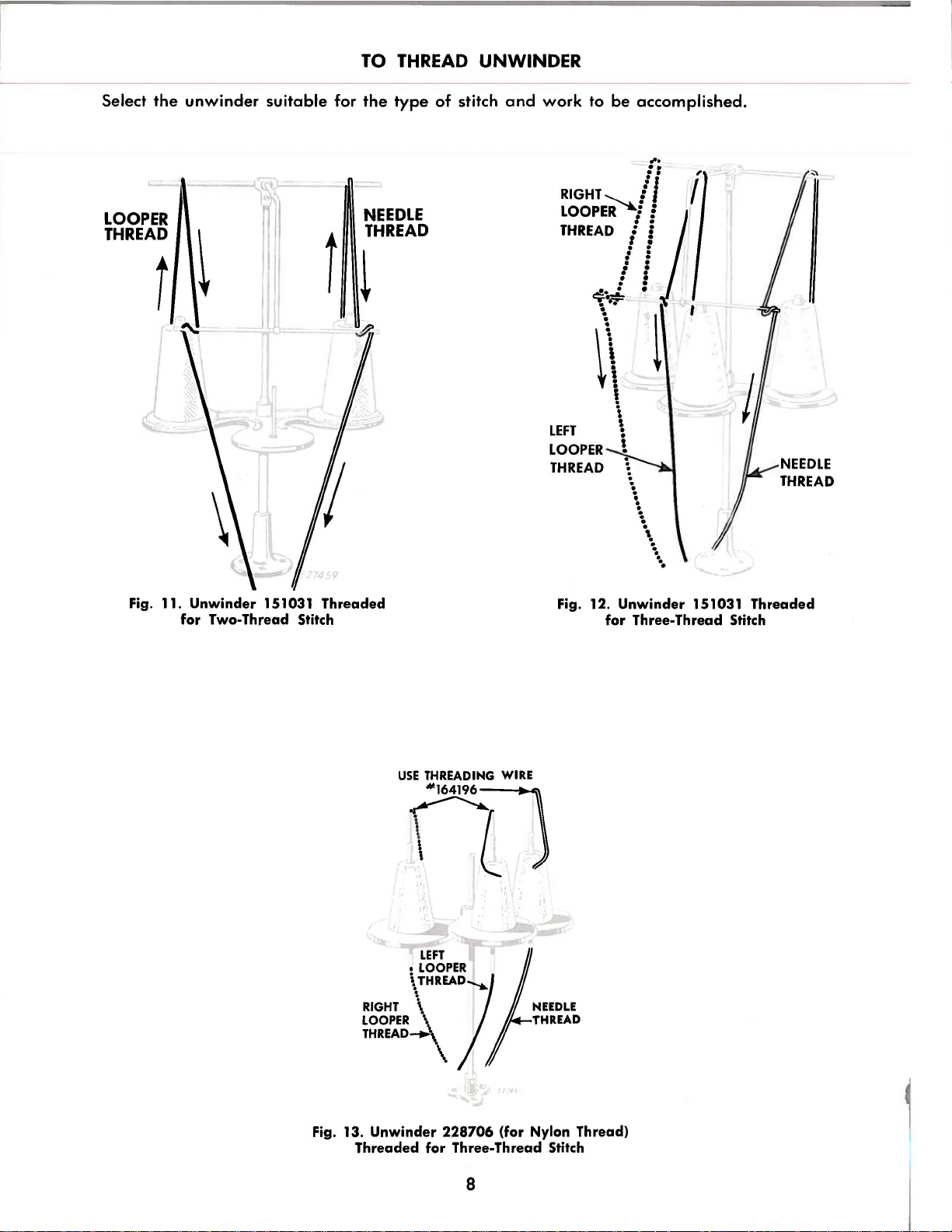
TO
THREAD
UNWINDER
Select
the
unwinder
'---l
LOOPER
mREAt
\
suitable
for
the
type
NEEDLE
i
{"READ
of
stitch
and
work
to
be
accomplished.
,,
..
RIGHT
LOOPE~
THREAD
,..!~
'l;r."""
\
/j
: f
' .
• •
. .
. .
.
.
I I
• •
• •
•
f
~\
\
LEFT
LOOPER
THREAD
\
•
1
,
I
NEEDLE
THREAD
Fig. 11. Unwinder 151031
for Two-Thread Stitch
Threaded
RIGHT \
LOOPER \
THREAD-+'
USE
THREADING WIRE
rn
·•\
I \
•'
\
'·
LEFT
:LOOPER
\THREAD~
\
Fig. 12. Unwinder 151031
for
Three-Thread Stitch
Threaded
Fig. 13. Unwinder
Threaded
228706
for Three-Thread Stitch
(for Nylon Thread)
8
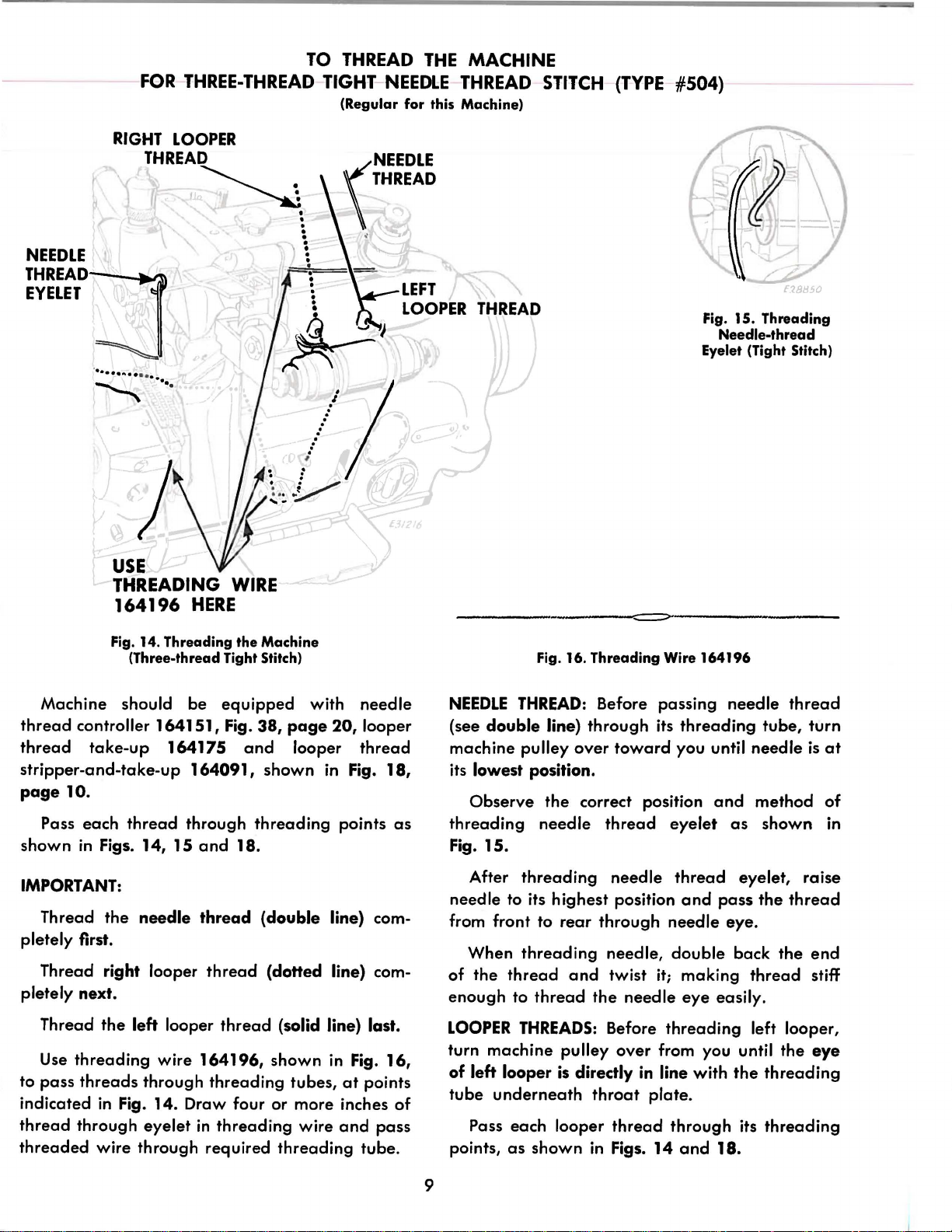
NEEDLE
FOR
THREE-THREAD
TO
THREAD
TIGHT
(Regular
rNEEDLE
THE
NEEDLE
for
\THREAD
MACHINE
THREAD
this Machine)
STITCH
(TYPE
#504)
THREAD
EYELET
~
~
·
·····"'·······
~
..
USE
THREADING
164196
Fig. 14. Threading
(Three-thread Tight Stitch)
Machine should be
thread
thread
stripper-and-take-up
page
shown
10.
Pass
controller
take-up
each
thread
in
Figs. 14,
164151,
164175
15
WIRE
HERE
the
equipped
Fig.
164091,
through
and
18.
Machine
38,
page
and
looper
shown
threading
with
20,
in
needle
looper
thread
Fig.
points
18,
as
Fig. 16.
NEEDLE
(see
machine pulley
its lowest position.
Observe
threading
Fig. 15.
THREAD:
double
line) through its
over
the
correct position
needle
Fig. 15. Threading
Needle-thread
Eyelet (Tight Stitch)
Threading
Before passing needle
toward
thread
Wire
164196
threading
you until needle
and
method
eyelet
as
thread
tube,
shown
turn
is
at
of
in
IMPORTANT:
Thread the
pletely
pletely
to
indicated
thread
threaded
first.
Thread right
next.
Thread
Use
pass
the
threading
threads
in
through
wire through required
needle
looper
left looper
through
Fig
. 14. Draw four or more inches
eyelet
wire
thread
thread
thread
164196,
threading
in
threading
(double
(doHed line) com-
(solid line) last.
shown
threading
line) com-
in
tubes,
wire
Fig. 16,
at
points
and
pass
tube.
of
After
needle to its highest position
from front to
When
of
the
enough
LOOPER
turn machine pulley
of
left looper
tube
Pass
points,
9
threading
rear
threading
thread
to
thread
THREADS:
is
underneath
each looper
as
shown
needle
through
needle,
and
twist
the
Before
directly
throat
thread
in
Figs.
thread
and
needle
double
it;
making
needle
over
eye
threading
from you until the
in
line with
plate.
through its
14
and
eyelet, raise
pass
the
eye.
back
the
thread
easily.
left looper,
the
threading
threading
18.
thread
end
stiff
eye
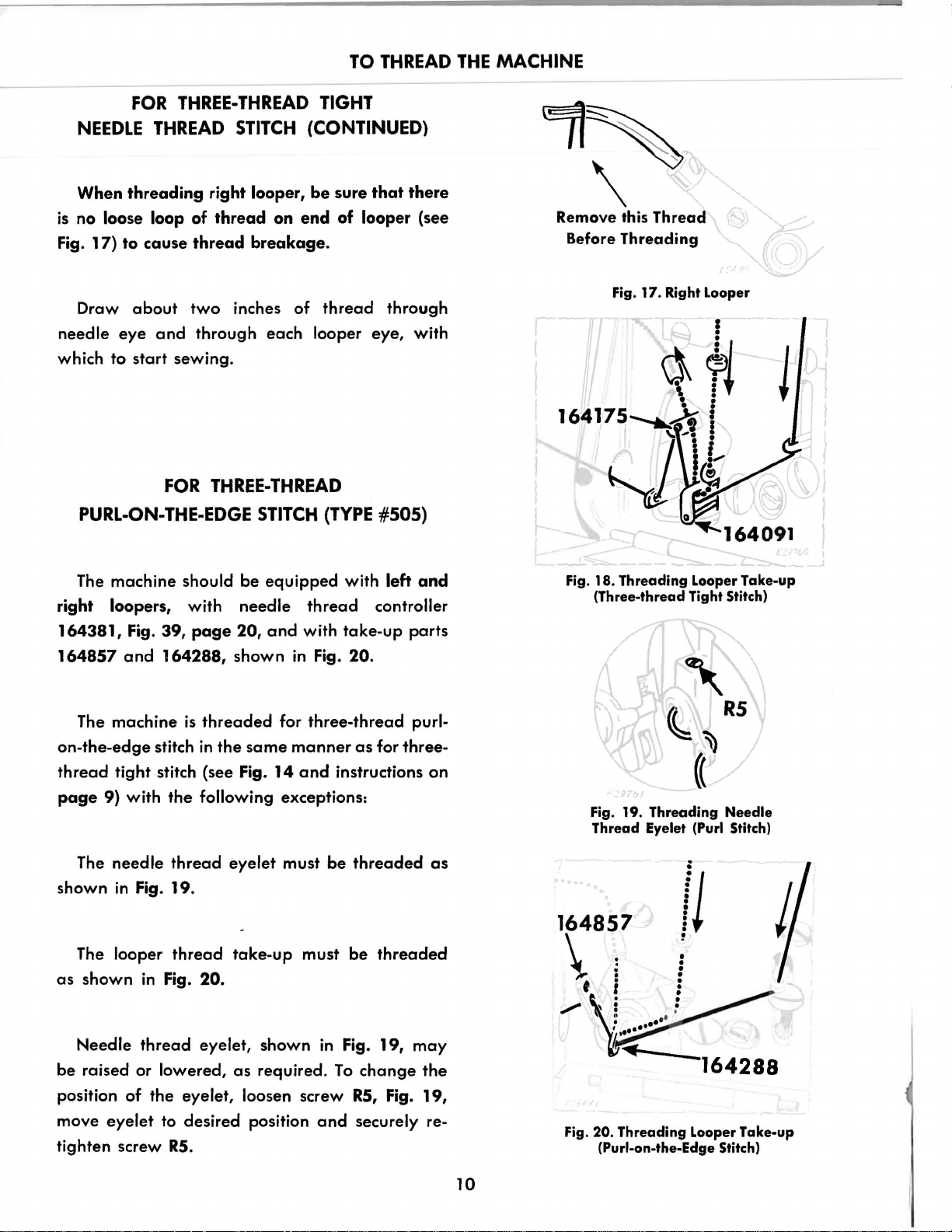
TO
THREAD
THE
MACHINE
FOR
NEEDLE
When
is
no loose loop of
Fig.
17)
Draw
needle
which to
THREAD
threading
to
cause
about
eye
and
start
PURL-ON-
THREE-
THREAD
STITCH
right looper,
thread
thread
two
inches
through
sewing.
FOR
THREE-
THE-EDGE
(CONTINUED)
be
on
end
breakage.
of
each
looper
THREAD
STITCH
TIGHT
sure
of
looper
thread
(TYPE
that
there
through
eye,
#505)
(see
with
,~
\~
Remove this Thread
Before Threading
Fig.
17.
r
I
I
I
Right
Looper
The
machine
right loopers, with
164381,
164857
The
on-the-edge
thread
page
The
shown
The looper
as
shown
Fig.
and
machine
tight
9)
with
needle
in
Fig. 19.
should
39,
page
164288,
is
threaded
stitch
in
stitch (see Fig.
the
following exceptions:
thread
thread
in
Fig.
20.
be
needle
20,
shown
the
same
eyelet
take-up
equipped
thread
and
with
in
Fig. 20.
for
three-thread
manner
14
and
must
be
must
with left
controller
take-up
as
instructions
threaded
be
parts
purl-
for
three-
threaded
and
on
as
Fig.
18. Threading
(Three-thread
Fig.
Thread
Looper
Tight
«,_
'
((
19. Threading Needle
Eyelet
(Purl
li
!
•
•
•
'>
Take-up
Stitch)
R5
/
Stitch)
- .
Needle
be
raised
position
move
tighten screw
thread
or
of
eyelet
eyelet,
lowered,
the
eyelet,
to
desired
RS.
shown
as
required.
loosen screw
position
and
in
Fig. 19,
To
change
RS,
securely re-
may
the
Fig. 19,
10
Fig.
20. Threading
(Purl-on-the-Edge
-164288
Looper
Take-up
Stitch)
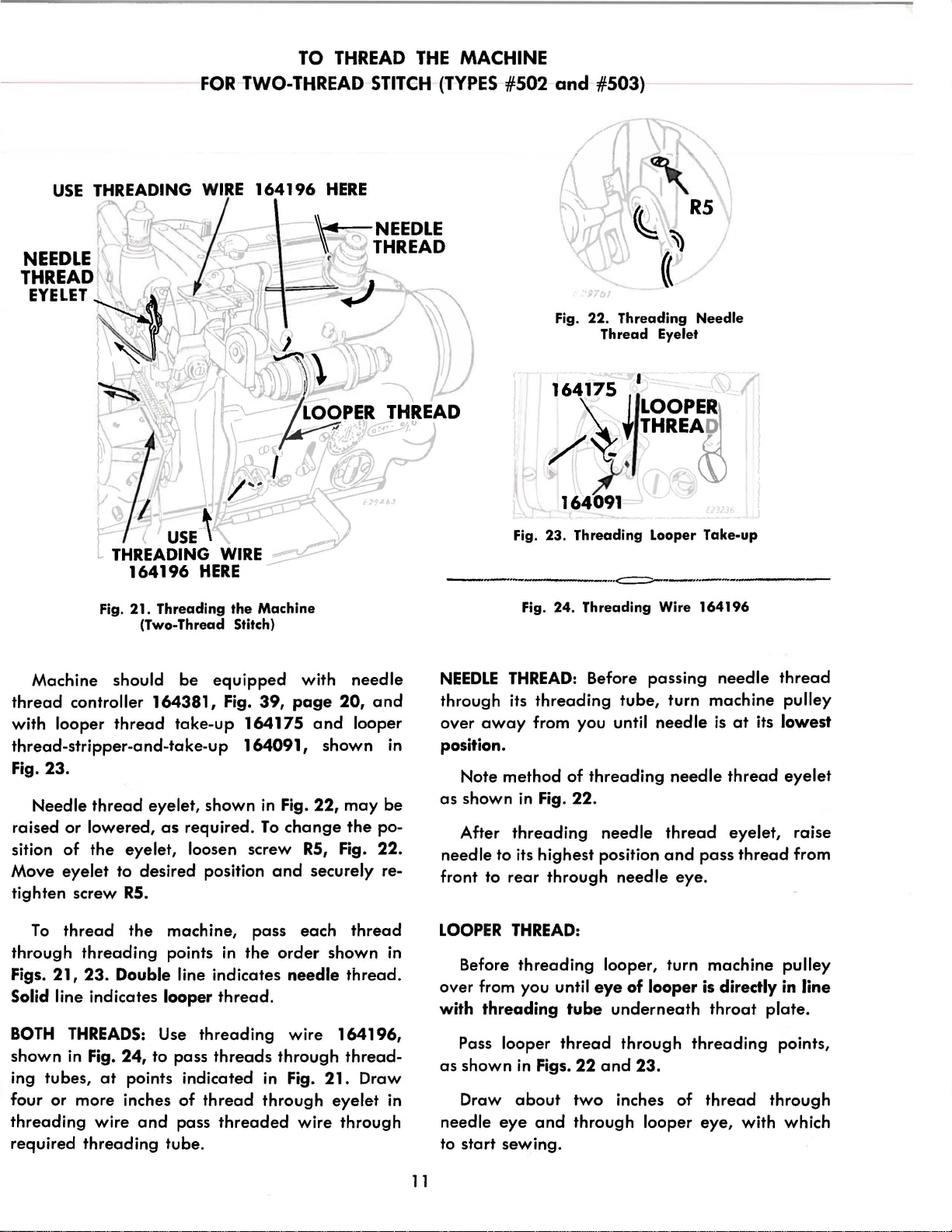
USE
THREADING
F0R TWO-
WIRE
164196
TO
THREAD
THREAD
HERE
THE
STITCH
MACHINE
(TYPES
#502
and
Fig.
#503)
22.
Threading
Thread
t_
Eyelet
RS
~
((
Needle
Fig. 21. Threading
(Two-Thread
Machine should
thread
with looper
thread-stripper-and-take-up
Fig.
raised or lowered,
sition
Move eyelet to desired position
tighten screw
through
Figs.
Solid line indicates looper
BOTH
shown
ing tubes,
four or more inches
threading
required
controller
23.
Needle
of
To
thread
21, 23.
THREADS:
in
thread
thread
the eyelet, loosen screw
RS.
the
threading
Double line indicates
Fig.
24,
at
points indicated
wire
threading
be
164381,
take-up
eyelet, shown
as
machine,
points
Use
to pass
of
and
pass
tube.
the
Stitch)
equipped
Fig.
164175
164091,
required.
in
the
thread.
threading
threads
thread
threaded
pass
Machine
with
39,
page
and
in
Fig.
22,
To
change
RS,
and
securely re-
each
order
needle
wire
through
in
Fig.
through
wire through
needle
20,
looper
shown
may
the
Fig.
thread
shown
thread.
164196,
thread-
21.
Draw
eyelet
and
in
be
po-
22.
in
in
Fig. 23.
Threading
------·.:::=::=:>------------
Fig. 24.
NEEDLE
through its
over
position.
as
After
needle to its highest position
front to
LOOPER
Before
over from you until
with
Pass looper
as
needle
to
THREAD:
away
method
Note
shown
rear
threading
shown
Draw
eye
start
sewing.
threading
from you until
in
threading
THREAD:
threading
in
Figs.
about
and
Threading
Before passing needle
tube,
of
threading
Fig.
22.
needle
through needle eye.
looper, turn machine pulley
eye
of
tube
underneath
thread
two
through looper eye, with which
22
and
through
23.
inches of
Looper Take-up
Wire
164196
thread
turn machine pulley
needle
thread
and
looper is directly
is
needle
pass
throat
threading
thread
at
its
lowest
thread
eyelet, raise
thread
in
plate.
points,
through
eyelet
from
line
11
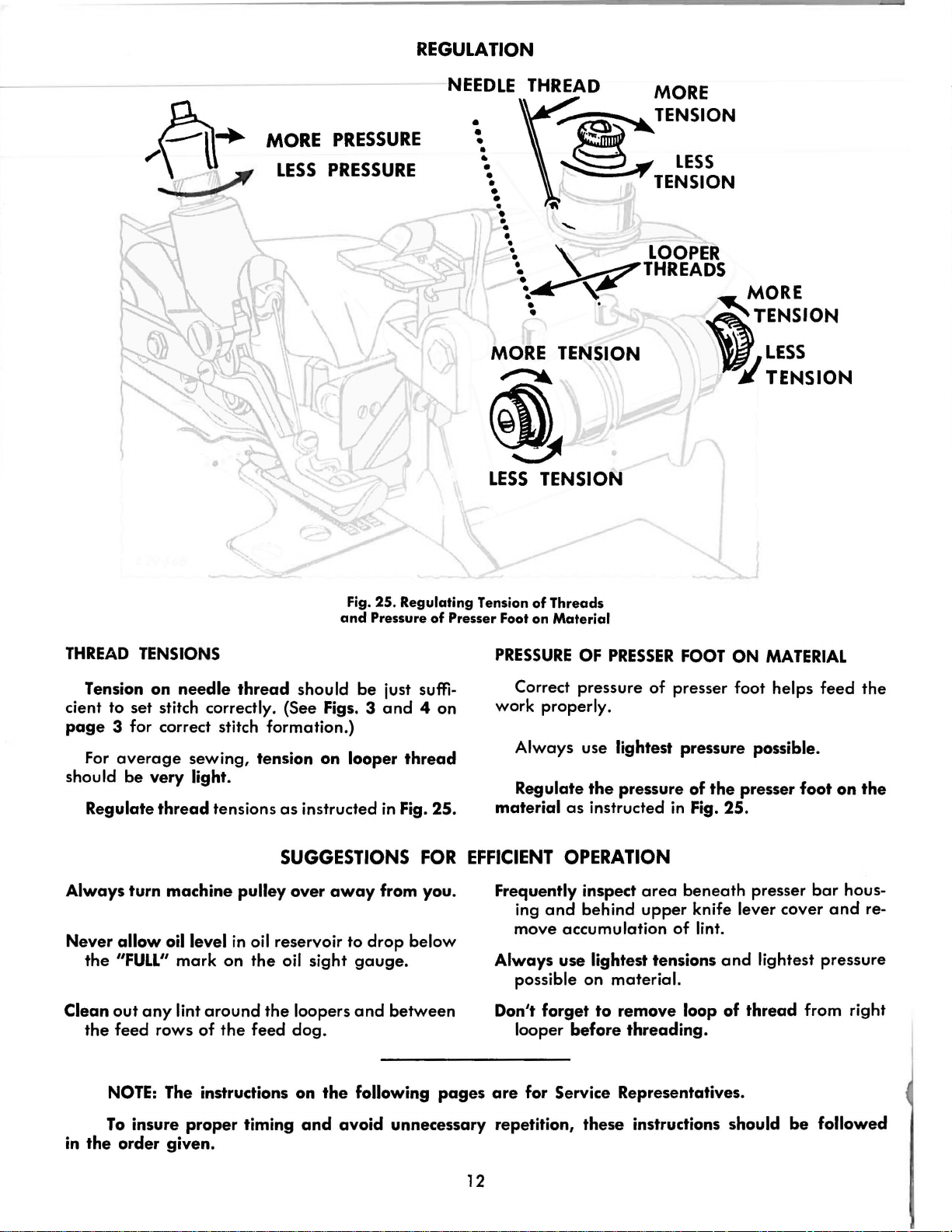
REGULATION
MORE
LESS
PRESSURE
PRESSURE
NEEDLE
\
~
~
•
•
-.:--oor.
•
~
•
\ '\.
\
..
MORE
~
~
~
LESS
THREAD
MORE
~TENSION
~LESS
I
........
~THREADS
~~
~
.
TENSION
TENSION
TENSION
LOOPER
MORE
~TENSION
jl
LESS
~TENSION
Fig. 25. Regulating Tension
and
THREAD
Tension
cient to set stitch correctly. (See Figs. 3
page
For
should
Regulate
TENSIONS
on
needle
3 for correct stitch formation.)
average
be
sewing, tension
very light.
thread
thread
tensions
should
on
as
instructed
be
looper
SUGGESTIONS
Always turn
Never
Clean
allow
the
"FULL"
out
the
feed rows
machine
oil level
mark
any
lint
pulley over
in
on
around
of
the
away
oil reservoir to
the
the
feed
oil sight
loopers
dog.
gauge.
and
Pressure
just suffi-
and
4 on
thread
in
Fig. 25.
FOR
from you.
drop
below
between
of
Threads
of
Presser Foot on Material
PRESSURE
Correct pressure
work properly.
Always use
Regulate
material
EFFICIENT
Frequently inspect
ing
move accumulation
Always use lightest tensions
possible on material.
Don't forget
looper
OPERATION
and
OF
the
as
instructed
behind
to
before
PRESSER
lightest pressure possible.
pressure
remove loop
threading.
FOOT
of
presser foot helps
in
area
beneath
upper
of
ON
of
the
presser
Fig. 25.
knife lever cover
lint.
and
of
MATERIAL
presser
lightest pressure
thread
feed
the
foot
on
the
bar
hous-
and
re-
from right
in
NOTE:
To
the
The instructions
insure proper timing
order
given.
on
and
the
following
avoid
pages
unnecessary repetition,
12
are
for Service Representatives.
these
instructions should
be
followed
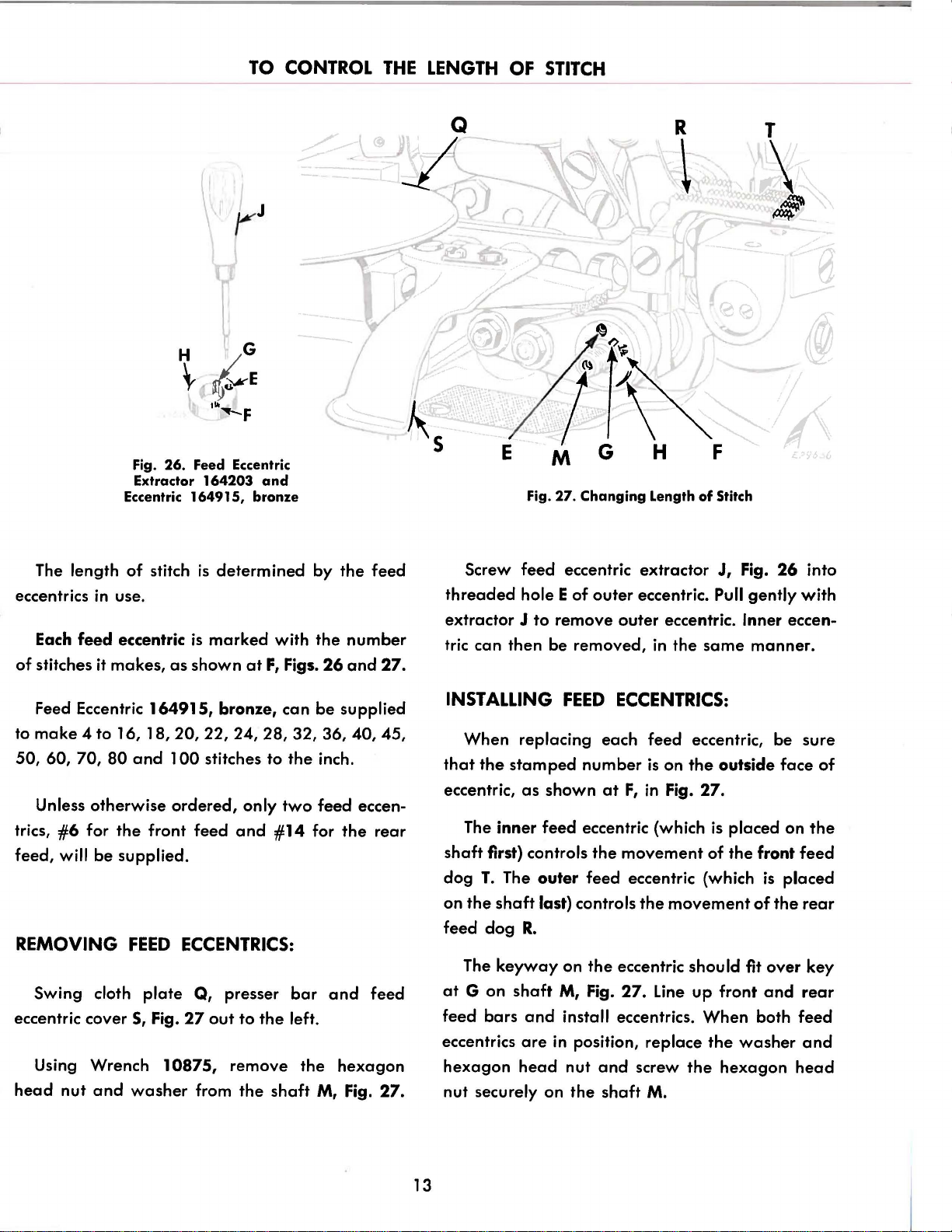
TO
J
Fig. 26. Feed Eccentric
Extractor
Eccentric
164203
164915,
and
bronze
CONTROL
THE
LENGTH
OF
Fig. 27.
STITCH
G
Changing
H
Length
of
F
Stitch
T
\
@
~
~
/1\
d
\...-
.....
---
(~
The length
eccentrics
Each
of
stitches it makes,
Feed Eccentric
to
make
50,
60, 70,
Unless otherwise
trics,
feed, will
in
feed
4 to 16, 18,
80
#6
for
be
use.
REMOVING
Swing cloth
eccentric
Using Wrench
head
coverS,
nut
and
of
stitch
eccentric
as
164915,
20,
and
100
ordered,
the
front
supplied.
FEED
plate
Fig.
10875,
washer
is
determined
is
marked
shown
bronze,
22, 24,
stitches to
feed
at
only
and
with
F,
28,
#14
Figs.
can
32,
the
two
ECCENTRICS:
Q,
27
from
presser
out
to
remove
the
the
shaft
bar
left.
by
the
the
number
26
and
be
supplied
36, 40, 45,
inch.
feed
for
the
and
the
hexagon
M,
Fig.
feed
27.
eccen-
rear
feed
27.
Screw
threaded
extractor J
tric can then be removed,
INSTALLING
When replacing each feed eccentric, be sure
that
eccentric,
The inner
shaft
dog
on
the
feed
The
at
G on
feed
eccentrics
hexagon
nut securely on
feed
eccentric extractor J, Fig.
hole E of
to
remove
FEED
the
stamped
as
shown
feed
first) controls
T.
The
outer
shaft
last) controls
dog
R.
keyway
shaft
bars
on
M,
and
install eccentrics. When both
are
in
head
outer
eccentric. Pull
outer
eccentric. Inner eccen-
in
the
ECCENTRICS:
number
eccentric (which
the
feed
the
Fig.
position, replace
nut
and
the
is
on
at
F,
in
Fig. 27.
movement
eccentric (which
the
movement
eccentric should fit
27.
Line
screw
shaft
M.
same
the
is
of
up
the
the
gently
manner.
outside
placed on
the
front
is
of
the
over
front
and
washer
hexagon
26
face
placed
into
with
of
the
feed
rear
key
rear
feed
and
head
13
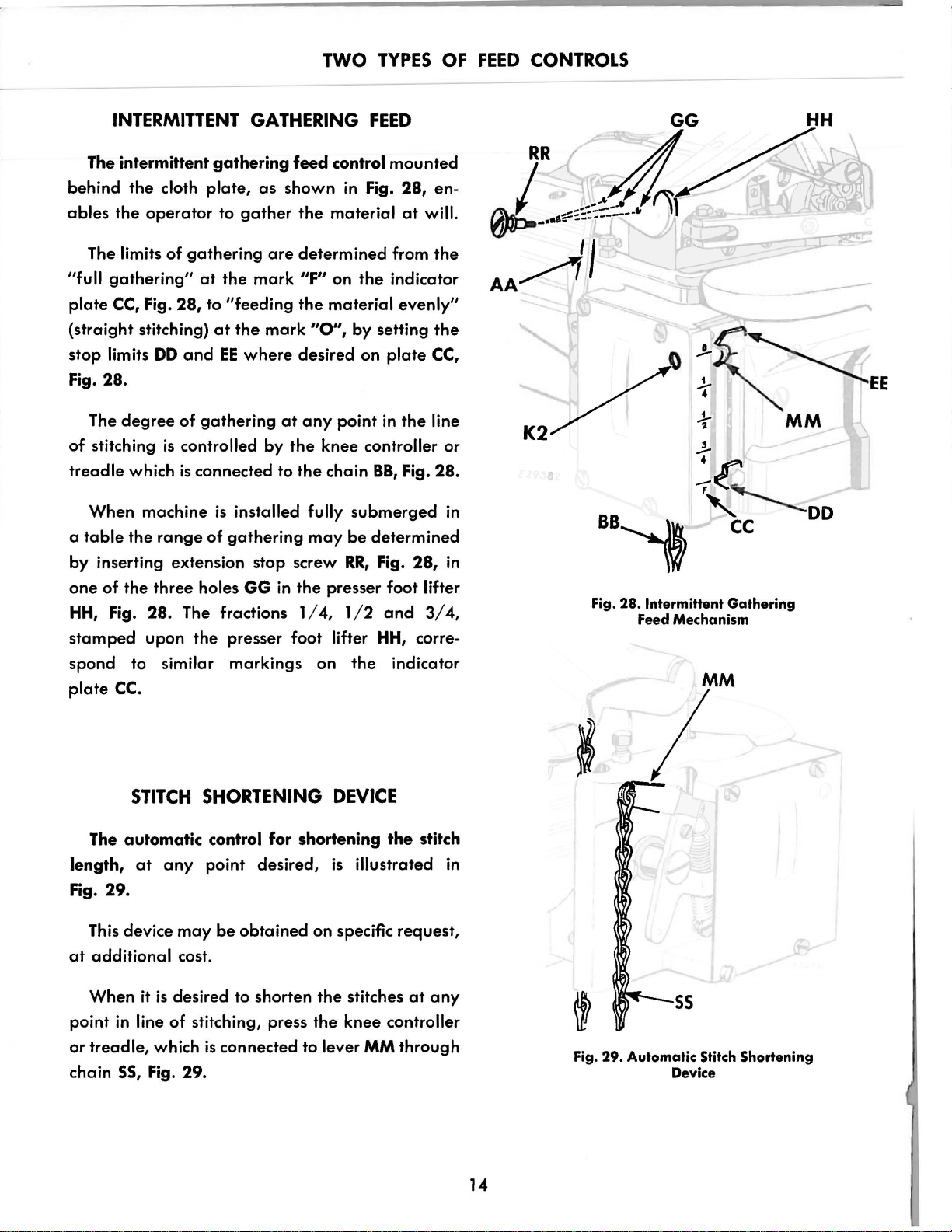
TWO
TYPES
OF
FEED
CONTROLS
INTERMITTENT
The intermittent
behind
ables
"full
plate
(straight stitching)
stop
Fig. 28.
of
treadle
a
by
one
HH,
stamped
spond
plate
the
cloth
the
operator
The limits of
gathering"
CC,
Fig.
limits
The
stitching
When
table
inserting extension
of
DD
degree
is
which
machine
the
range
the
three
Fig. 28. The fractions 1 /4,
upon
to similar
CC.
gathering
plate,
to
gather
gathering
at
the
28,
to
"feeding
at
the
and
EE
of
gathering
controlled
is
connected to
is
installed fully
of
gathering
holes GG in
the
presser foot lifter
markings
GATHERING
feed
control
as
shown
the
material
are
determined
mark
"F"
on
the
material
mark
"0",
where
by
stop
desired
at
any
point in
the
knee
the
chain
may
screw
the
presser foot lifter
on
FEED
mounted
in
Fig.
28,
at
from
the
indicator
evenly"
by
setting
on
plate
the
controller or
BB,
Fig.
submerged
be
determined
RR,
Fig.
28,
1/2
and
HH,
corre-
the
indicator
en-
will.
the
the
CC,
line
28.
in
in
3/4,
Fig. 28. Intermittent
Feed Mechanism
MM
HH
-~
Gathering
STITCH
The
automatic
length,
Fig.
This device
at
point in line
or
chain
at
29.
additional
When
treadle,
SS,
it
Fig. 29.
which
SHORTENING
control for
any
point desired,
may
be
obtained
cost.
is
desired to shorten
of
stitching, press
is
connected to lever
DEVICE
shortening
is
on specific request,
the
the
the
stitch
illustrated in
stitches
knee
controller
MM
through
at
any
14
I
ss
Fig. 29. Automatic Stitch Shortening
Device
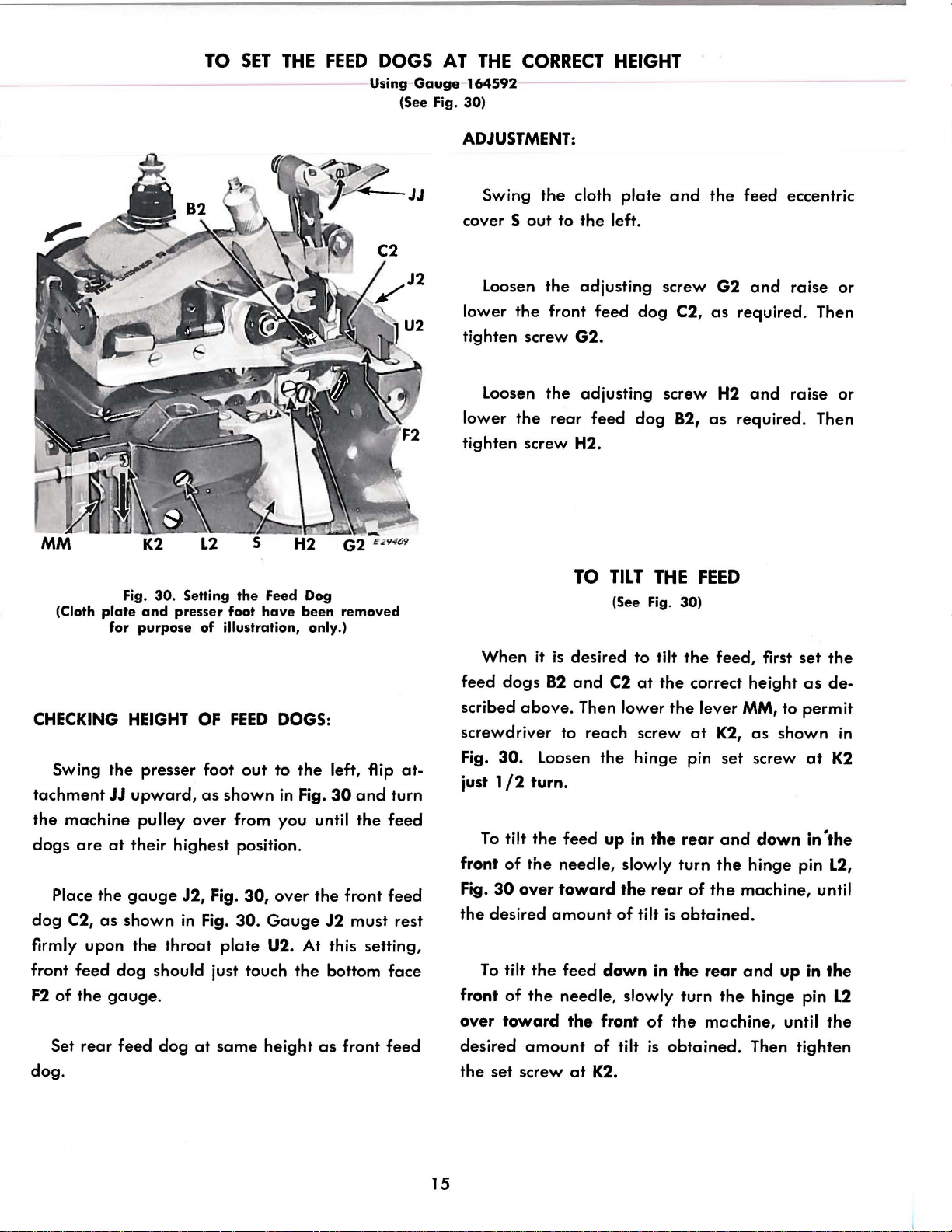
TO
SET
THE
FEED
DOGS
Using
(See Fig.
AT
Gauge
THE
CORRECT
164592
30)
ADJUSTMENT:
HEIGHT
(Cloth
Fig.
plate
for
30.
and
presser
purpose
Setting
the
foot
of
illustration, only.)
Feed Dog
have
been
removed
Swing
cover
loosen
lower
tighten screw
loosen
lower
S
the
the
the
out
cloth
to
the
front
G2
the
rear
the
adjusting
adjusting
feed
tighten screw H2.
TO
plate
left.
feed
dog
.
dog
TILT
THE
(See Fig. 30)
and
the
screw
C2,
G2
as
screw H2
82,
as
FEED
feed eccentric
and
raise or
required. Then
and
raise
or
required. Then
CHECKING
Swing
tachment
the
dogs
Place
dog
the
JJ
machine
are
at
the
C2,
as
firmly upon
feed
front
F2
of
the
gauge.
Set
rear
dog.
HEIGHT
presser foot
upward,
pulley
OF
FEED
out
as
shown
over
from you until
their highest position.
gauge
shown
the
dog
feed
J2,
Fig.
30,
in
Fig.
30.
throat
plate
should just touch
dog
at
same
height
DOGS:
to
the
in Fig.
over
Gauge
left, flip
30
the
front
J2
must rest
and
the
at-
turn
feed
feed
U2. At this setting,
the
bottom
as
front
face
feed
When
feed
scribed
dogs
above.
it
is
desired to tilt
82
and
Then lower
C2
at
the
the
screwdriver to reach screw
Fig.
30.
just 1
/2
To
tilt
front of
Fig.
30
the
desired
To
tilt
front
of
over
toward
desired
the
set
loosen
turn.
the
the
over
amount
the
the
amount
screw
the
hinge pin
feed
up
in
the
needle, slowly turn
toward
feed
the
of
down
tilt
rear
is
in
needle, slowly turn
the
at
front
of
K2.
tilt
of
is
obtained.
the
feed,
correct height
lever MM, to
at
K2,
as
set
screw
rear
and
the
hinge
of
the
machine, until
obtained.
the
rear
and
the
hinge pin
the
machine, until
Then tighten
first set
permit
shown
down
pin
up
the
as
de-
at
K2
in •the
L2,
in
the
L2
the
in
15
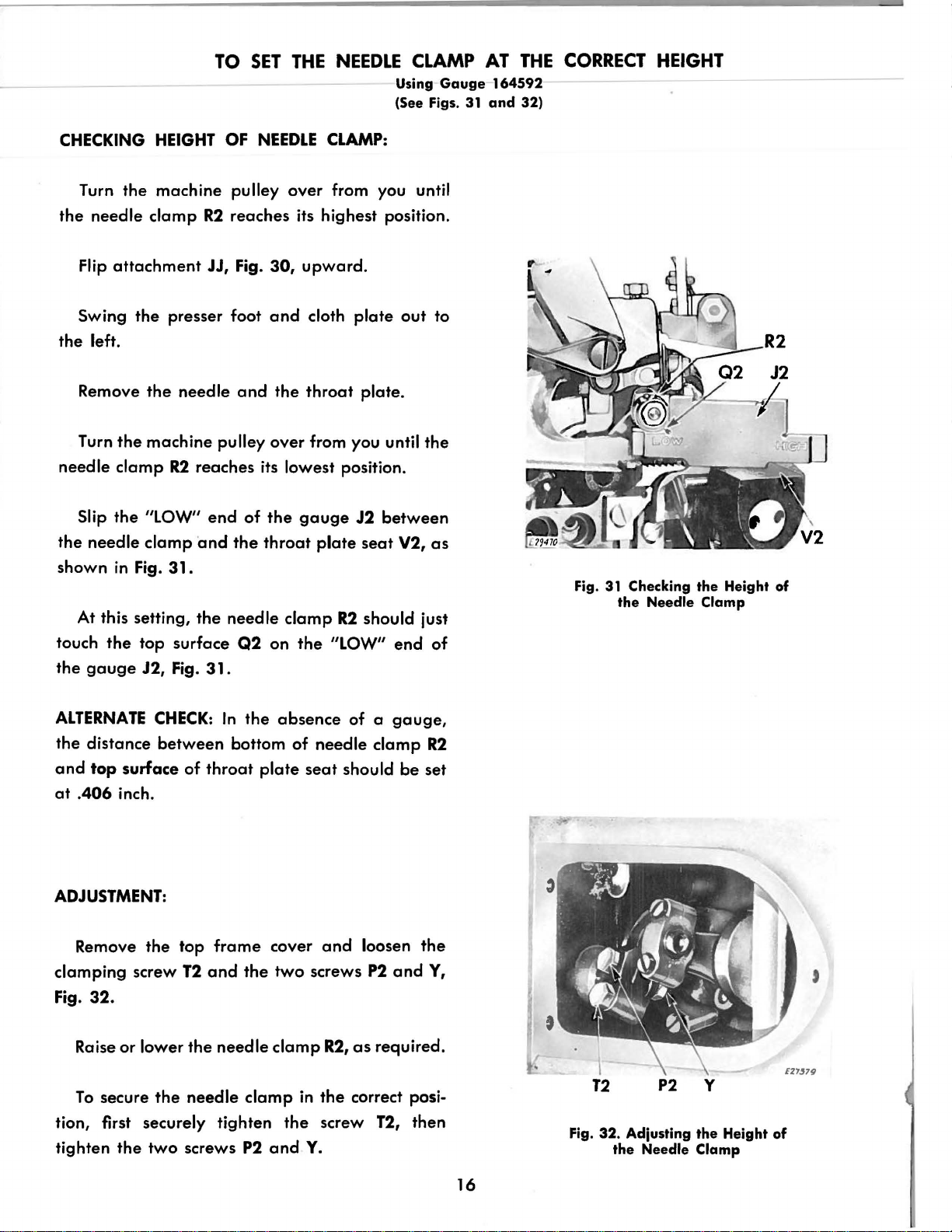
TO
SET
THE
NEEDLE
Using
(See Figs.
CLAMP
Gauge
31
AT
THE
164592
and
32)
CORRECT
HEIGHT
CHECKING
Turn
the
the
needle
attachment
Flip
Swing
the
Remove
Turn
needle
Slip
the
needle
shown
At this setting,
touch
the
gauge
left.
the
the
the
clamp
the
in
Fig.
top
J2,
HEIGHT
machine
clamp
the
machine
"LOW"
clamp
R2
presser foot
needle
R2
reaches
and
31.
the
surface
Fig.
OF
pulley
reaches
JJ, Fig.
and
pulley
end
of
the
needle
Q2
31.
NEEDLE
30,
and
the
over
its lowest position.
the
throat
on
CLAMP:
over
from you until
its highest position.
upward.
cloth
throat
gauge
clamp
the
plate
plate.
from you until
J2
between
plate
seat
R2
should just
"LOW"
out
V2,
end
to
the
as
of
Fig. 31 Checking
the
Needle
the
Height
Clamp
of
ALTERNATE
the
distance
and
top
at
.406
CHECK:
between
surface
inch.
of
In
the
bottom
throat
plate
ADJUSTMENT:
Remove
clamping
Fig.
32.
Raise or lower
To
tion, first securely tighten
tighten
screw
secure
the
the
the
two
top
frame
T2
and
the
needle
needle
screws P2
the
clamp
absence
of
seat
cover
two
screws P2
clamp
in
the
and
Y.
of a
gauge,
needle
and
R2,
the
screw T2, then
clamp
should
as
correct posi-
be
loosen
andY,
required.
set
the
R2
Fig.
32.
Adjusting
the
P2
Needle
Y
the
Height
Clamp
'
of
16
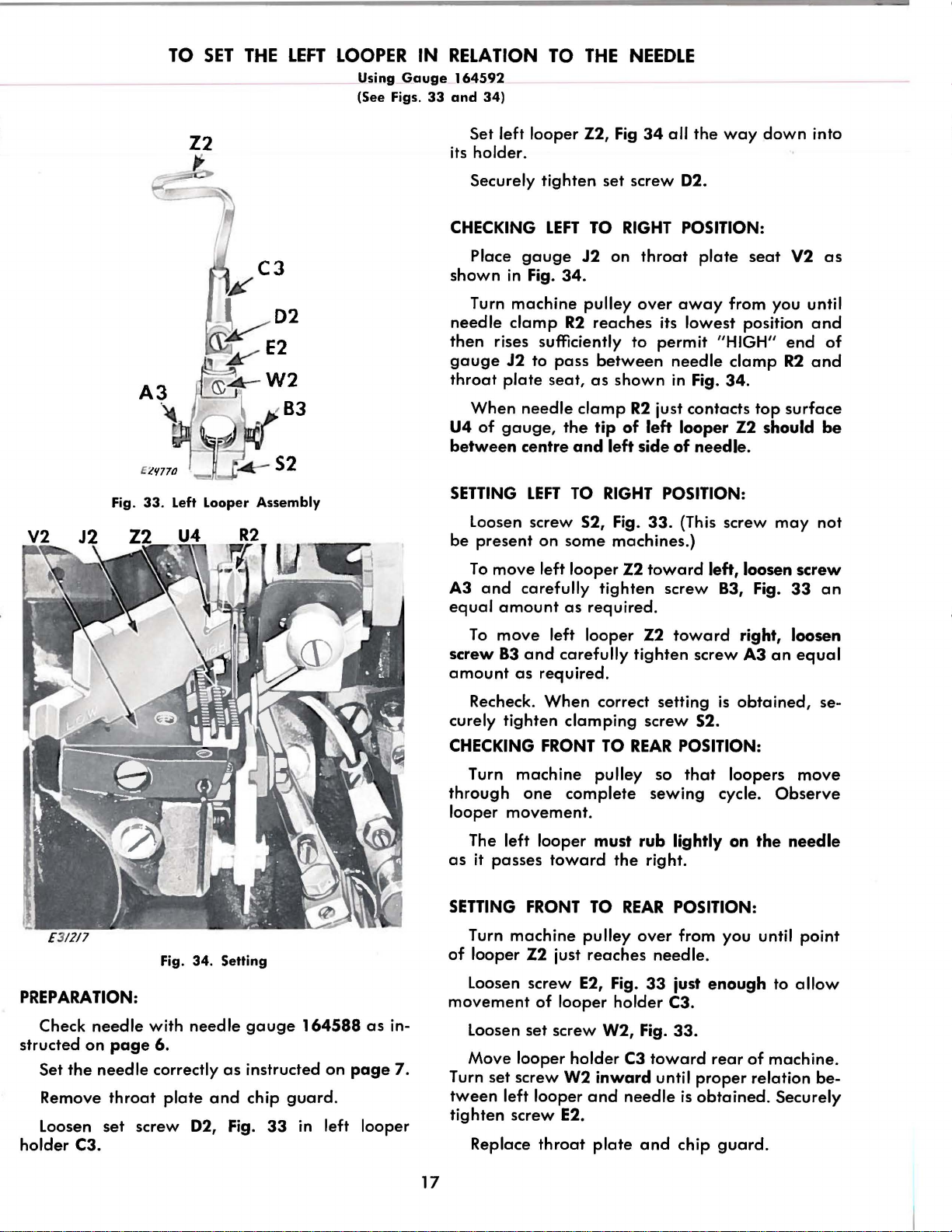
TO
SET
THE
LEFT
LOOPER
Using
(See Figs.
IN
Gauge
33
RELATION
164592
and
34)
TO
THE
NEEDLE
Fig.
33.
Left Looper Assembly
Set left looper Z2,
its holder.
Securely
CHECKING
Place
shown
Turn
needle
then
gauge
throat
When
U4
of
between
SETTING
loosen
be
present
To
move
A3
and
equal
tighten
LEFT
gauge
in
Fig.
machine
clamp
rises sufficiently
J2
to
pass
plate
seat,
needle
gauge,
centre
LEFT
screw 52, Fig.
on
left looper Z2
carefully
amount
TO
J2
34.
pulley
R2
reaches
between
as
clamp
the
tip
and
TO
some
as
required.
Fig
34
set
screw
RIGHT
on
throat
over
to
permit
shown
R2
just contacts
of
left
left
side
RIGHT
33.
machines.)
toward
tighten
all
the
way
02.
POSITION:
plate
away
its
needle
in
looper
of
from you until
lowest
"HIGH"
clamp
Fig.
34.
needle.
POSITION:
(This screw
left, loosen
screw
83,
down
seat
position
top
Z2
should
may
Fig.
into
V2
as
and
end
of
R2
and
surface
be
not
screw
33
an
PREPARATION:
Check
structed
Set
Remove
loosen
holder
on
the
C3.
needle
page
needle
throat
set
Fig.
with
6.
correctly
plate
screw
34.
Setting
needle
as
and
02,
Fig.
gauge
instructed
chip
33
164588
guard
in
as
in-
on
page
7.
.
left looper
To
move
screw
amount
curely
83
Recheck.
tighten
CHECKING
Turn
through
looper
The left looper
as
it
passes
SETTING
Turn
of
looper Z2 just
Loosen screw
movement
Loosen set screw W2, Fig.
Move looper holder C3
Turn set screw W2
tween
tighten
left looper
Replace
left looper Z2
and
carefully
as
required.
When
clamping
FRONT
machine
one
complete
movement.
toward
FRONT
machine
of
screw E2.
pulley
E2,
looper holder C3.
throat
correct setting
TO
pulley so
must
the
TO
reaches
Fig.
inward
and
plate
tighten
screw 52.
REAR
sewing
rub
right.
REAR
over
needle.
33
toward
until
needle
and
toward
right, loosen
screw A3
is
obtained,
POSITION:
that
loopers
cycle.
lightly
on
POSITION:
from
you
just
enough
33.
rear
proper
is
obtained.
chip
guard.
an
equal
se-
move
Observe
the
needle
until
point
to
allow
of
machine.
relation be-
Securely
17