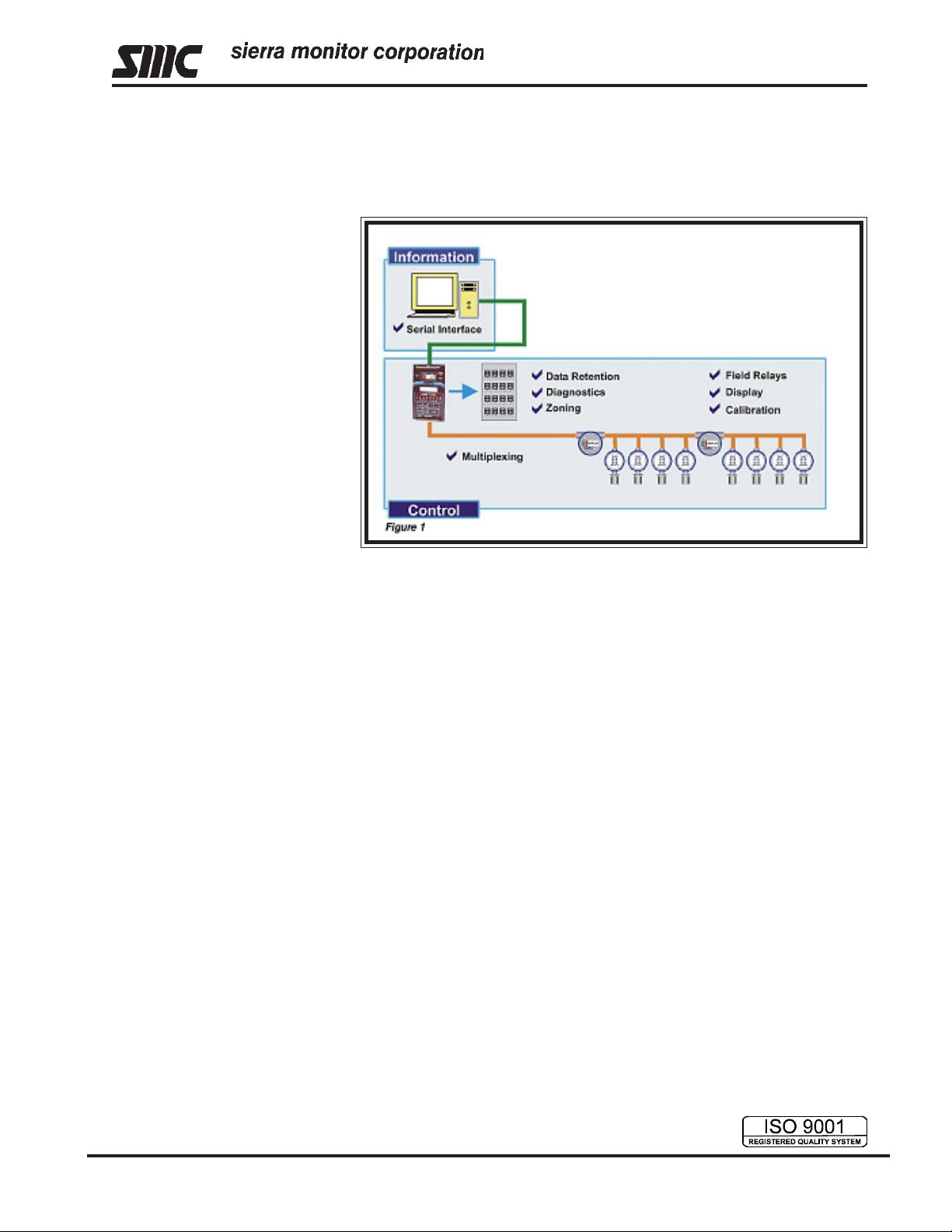
Gas Detection Systems
How to make your facility's monitoring data accessible
by Gordon Arnold
Y ou really hav e to have backbone to survive in the safety
monitoring world today. No,
there is no heavy lifting required. I am referring to the
data backbone of the facility,
plant or process to which the
monitoring system is applied.
In times past, gas monitoring systems were free-standing, and any data they generated was collected and used
on a local basis. T oday, plants
and other facilities most likely
require that all data be centralized so monitoring systems can perform their functions and provide data to
higher-level systems. Data must be accessible
on plant-wide backbones, which come in many
flavors.
In addition to various proprietary data busses,
some plant backbones are serial-based
(Modbus RTU, DF1, Metasys), many are based
on Ethernet architecture (Modbus TCP,
EtherNet/IP, BACnet/IP) and others are based
on fieldbusses such as Profibus, DH+ and
ControlNet. This discussion is confined to serial data busses and Ethernet networks, but
the principals and issues are universal.
Technical Reprint TR-005
For purposes of meeting future requirements
to integrate data to a facility backbone, this
minimum system with serial communications
is now well on the way to plant-wide integration. At the Control level the system provides
sensor monitoring and also controls the alarm
activities. At the Information level data can be
retrieved from the controller via the serial connection. The facility IT group, plant process
control team or the building automation consultants are now free to investigate opportunities to interface to the gas detection system
via the plant backbone.
A strong backbone
The challenge for industrial hygiene professionals is to determine which backbone interface is required and then ensure that the selected equipment meets that requirement.
Figure 1 represents the minimum requirements
for a gas detection system that are generally
well understood. The system must include gas
detection modules, a method to communicate
to a controller , flexible alarm handling with relay
outputs, and a method for communicating data
to higher-level systems. In this case, serial
communications are used to provide data to a
dedicated computer.
Sierra Monitor Corporation 1991 Tarob Court Milpitas, CA 95035 USA (408) 262-6611 (800) 727-4377 Fax: (408) 262-9042
Visit our website: www.sierramonitor.com E-mail: sierra@sierramonitor .com
The terms “serial communication” or “Ethernet”
describe only the electrical hardware characteristics of the backbone, such as the type of
wires and the methods of connection. Comparing to an office equipment environment, a
serial connection would interface a computer
to a modem, while an Ethernet connection
would network the computer and allow it to
communicate with a server, a network printer
or many other devices. The aspect that is not
yet described is the protocol, which is the data
format and handling instructions that travel
on the backbone.
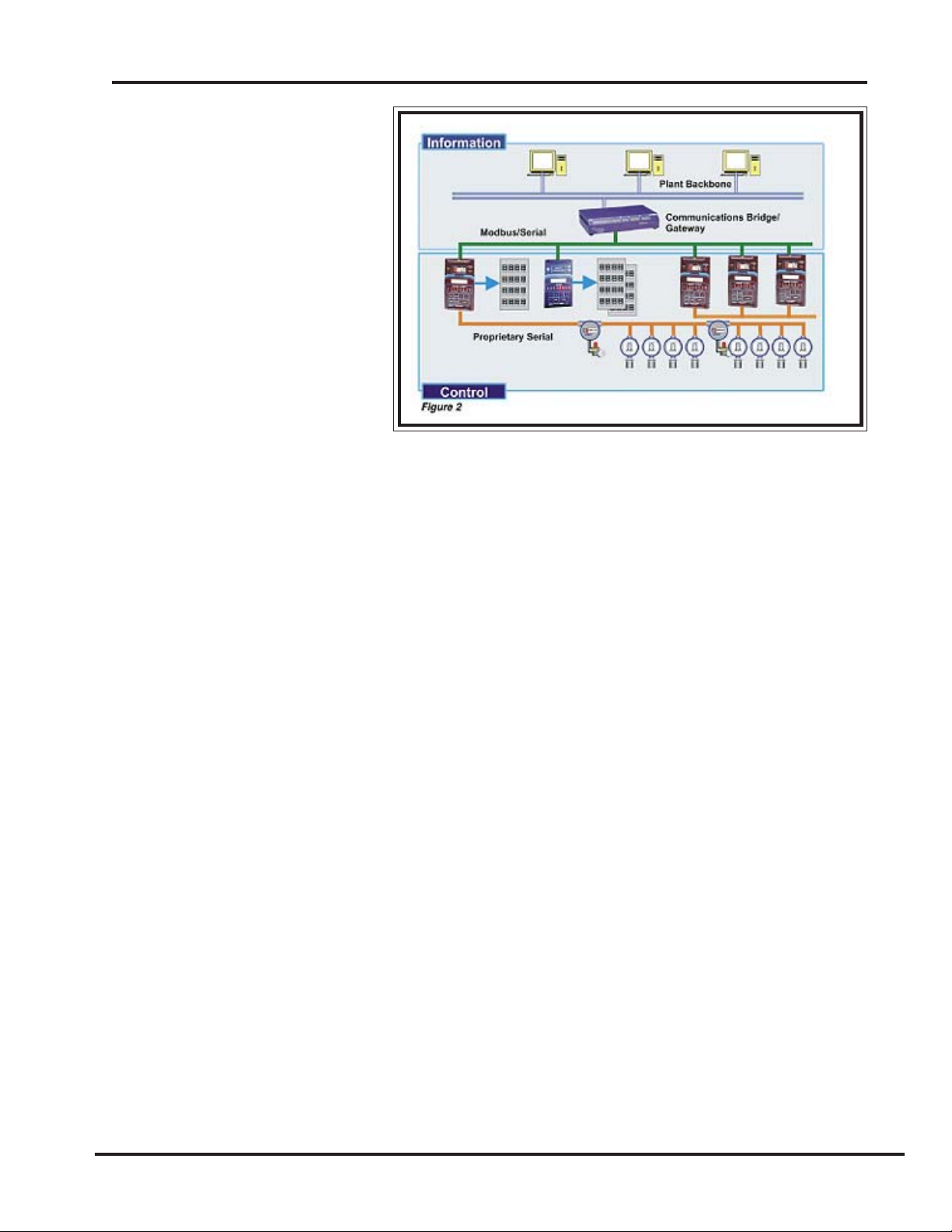
Knowing the protocol
When a specification states that
a product has an RS-485 interface, it only defines the serial electrical hardware connection and
not the protocol. It is important
for the safety professional to also
know the protocol. While hundreds of serial protocols exist in
the instrumentation world, the
most common serial protocol is
Modbus RTU.
Likewise, when a specification
states that a product has an
Ethernet port, it only defines the
form of the hardware interface,
commonly known as a Cat-5 cable connection.
The most common Ethernet protocol in the
industrial world is Modbus/TCP. The Modbus/
TCP de-facto standard is being rapidly challenged by EtherNet/IP in the industrial world
and standards such as BACnet/IP in the building automation world.
The gas monitoring system must be able to
hand off data and accept inputs in the protocol
format demanded by the plant-wide control
system. In Figure 2 the original single system
concept has been expanded to indicate that
multiple gas detection controllers might be
connected via a serial interface, but the primary Information layer now includes an
Ethernet backbone. Now multiple PCs can have
access to data from the gas monitoring system. Many other devices will also reside on the
backbone, including process control or monitoring equipment, building management devices and control room systems.
New features
Once the Ethernet interface is established, new
features of monitoring systems become available. Possibly the most useful is a Web server
function. A Web server can be installed in the
Communications Bridge/Gateway or in another
Ethernet node so authorized personnel have
desktop access to graphical representation of
the gas monitoring system status. Graphical
representation is no longer relegated to expensive, license-based, control room packages.
Other features include report by exception, redundancy functions and remote datalogging,
all enabled by the Communications Bridge and
accessible via the plant backbone.
No heavy lifting here, it is all done for you.
Critical to the ability to connect to the plant
backbone is the Communications Bridge or
Gateway. This device enables hardware platform and protocol conversion interoperability
between dissimilar systems and the backbone.
The safety professional can breathe a sigh of
relief because his choice of monitoring system
is no longer restricted to the backbone protocol.
Gordon Arnold is president of Sierra Monitor, a leading manufacturer of plant-wide gas risk monitoring
systems. He has been closely involved in the gas detection industry for more than 25 years. Gordon can
be contacted at garnold@sierramonitor.com or (408)
262-6611.
© 2004 by Sierra Monitor Corporation
Sierra Monitor Corporation 1991 Tarob Court Milpitas, CA 95035 USA (408) 262-6611 (800) 727-4377 Fax: (408) 262-9042
Visit our Web site: www.sierramonitor.com E-Mail: sierra@sierramonitor.com