
Motorised lift-slide drive.
Window systems
Door systems
Comfort systems
INSTALLATION AND
OPERATING INSTRUCTIONS

Installation and operating instructions MHS400 smart
05.2017 3
Contents
1. General information ................................................................................................................................................................... 4
2. Safety notes ................................................................................................................................................................................ 5
3. Device functions .......................................................................................................................................................................... 6
4. Scope of delivery ........................................................................................................................................................................ 8
5. Size range .................................................................................................................................................................................10
6. On-site risk and hazard analysis .............................................................................................................................................. 11
7. Installation ................................................................................................................................................................................. 12
8. Commissioning – scheme A ..................................................................................................................................................... 38
9. Teaching in the intermediate stop – Scheme A........................................................................................................................40
10. Operation – scheme A ........................................................................................................................................................... 41
11. Commissioning – scheme C ...................................................................................................................................................43
12. Teaching in the intermediate stop – scheme C ......................................................................................................................46
13. Operation – scheme C...........................................................................................................................................................47
14. Manual emergency operation ...............................................................................................................................................50
15. Care and maintenance ..........................................................................................................................................................51
16. Rectification of malfunctions ..................................................................................................................................................52
17. Technical specifications ..........................................................................................................................................................53
18. Accessories ............................................................................................................................................................................. 53
19. Information concerning product liability ...............................................................................................................................54
20. Feedback on documentation ................................................................................................................................................. 54
21. EC declaration of incorporation ............................................................................................................................................55

4
MHS400 smart Installation and operating instructions
05.2017
1. General information
Please read these installation and operating instructions carefully and in full before commissioning
the HS system MHS400 smart.
1.1 Target group of this documentation
• This documentation is intended for use by specialists and end users.
• All instructions concerning installation, commissioning and repairs contained in this document are to be performed
exclusively by electricians with training and experience in the installation, commissioning, maintenance and servicing of
motorised drives.
• All instructions on operation, care and maintenance as well as the rectification of malfunctions described here are
intended for specialists end users.
• Following installation, the installation company must hand over the installation and operating instructions to the end user
and brief the user/owner of the building accordingly.
1.2 Intended use
• The MHS400 smart system uses an electric motor to open and close windows and patio doors with lift-slide hardware
(e.g. PORTAL HS).
• The standard MHS400 smart system is not suitable for use in swimming pools and/or damp rooms. Special designs are
possible and permitted only upon request and after having been tested by SIEGENIA.
• The MHS400 smart must only be operated with hardware and genuine accessories from SIEGENIA (hardware from
third-party manufactures upon request).
• It must be possible to access and disassemble the slide drive SA at all times should maintenance and service work be
required (curtain rods, lamps, ceiling covers, roller shutter housings, etc. must not hinder removal).
• The instructions contained in ASR A 1.6, VFF data sheet KB.01 as well as EN 12453 for power-operated windows, doors
and gates must be observed!
• If you are using the system for commercial purposes, you must also observe the safety instructions of your accident
insurance provider.
• Following installation of the MHS400 smart, you must carry out a reference run as well as a calibration and teach-in run
when the unit is commissioned for the first time.
1.3 Incorrect use
• Lift and slide elements that are equipped with the MHS400 smart HS system must not be used as escape doors/
emergency exits in the event of a fire!
• Any use of this product that is not in accordance with its correct use, or any adaptation of or modification to the product
and its associated components for which the express consent of SIEGENIA has not been obtained, is strictly prohibited.
SIEGENIA accepts no liability whatsoever for any material losses or injury to people caused by failure to comply with this
stipulation.
1.4 Dimensions
• All the dimensions in this documentation are specified in mm.

Installation and operating instructions MHS400 smart
05.2017 5
2. Safety notes
Risk of injury or fatal injury. Hands, arms, legs and feet can get trapped and/or crushed in systems
driven by an electric motor.
• Make sure that no parts of the body or objects are within the shearing and locking area of the system.
• Particularly when lowering lift and slide elements, make sure that no parts of the body or objects are under the lift & slide
sash.
• Do not leave children unattended near a lift and slide element.
Risk of injury or death due to electrical shock or fire. Systems driven by an electric motor can
overheat and cause fire.
• Insert the Euro mains plug of the standard connecting cable only into a suitable 230VAC mains power supply socket.
• Only a qualified electrician may perform any work on the 230V AC mains power supply.
• Current local regulations (such as VDE 0100 of the VDE in Germany) must be observed.
• Relevant country-specific regulations must be strictly followed for all work on the voltage supply system or building wiring
system.
• All-pole safety isolation is required when the mains cable is laid on-site because the power supply does not have a
separate line disconnector.
• Connect in-wall supply lines to the MHS400 smart HS system in branch boxes. These branch boxes must be kept
accessible for maintenance.
• When cleaning the lift & slide sash and the drives, make sure that no liquid gets inside the MHS400 smart HS system as
this could damage the electronics.
• The unit must be checked by a specialist in the event of a fault.
Injuries caused by falling objects.
• Please do not put or place objects on top of the MHS400 smart.
Hazard due to third party attacks on SIEGENIA WLAN devices! Please observe the following notes
to protect your system against attacks by third parties:
• Every SIEGENIA WLAN device is protected by two passwords (user and administrator). It is essential that you change
these passwords after the initial setup. Do not leave in the default setting.
• If the SIEGENIA WLAN devices are integrated in your home WLAN, this must be encrypted for operation.
• Please choose secure passwords consisting of lower case and capital letters, numbers and special symbols.

6
MHS400 smart Installation and operating instructions
05.2017
3. Device functions
3.1 General product description
• The MHS400 smart is a motorised HS system for the automatic locking, release and movement of lift & slide sashes (lift
and slide elements, scheme A and C).
• The MHS400 smart can be controlled by a tablet or smartphone and offers additional device functions via the
SIEGENIA Comfort app. Please follow the enclosed quick start instructions (H47.MOTS005EN).
• The slide drive SA features an electronic cut-off function (see “3.3 Information on safety cut-off and jam protection” on
page 7).
• To further increase safety during travel, the slide drive SA with terminal board allows for the integration of a light curtain.
If an object is moved into the path of the lift & slide sash, the lift & slide sash is stopped immediately.
• In the event of a power failure, the MHS400 smart can be operated manually using the emergency operating handle.
• The lift & slide sash can be moved into a freely programmed intermediate position (intermediate stop).
• The lift & slide sash can be moved into a secured night vent position (only the PORTAL HS).
3.2 Control
The MHS400 smart system offers the following control options:
Function Lift & slide sash
end position
Button on the
lift drive
SIEGENIA
Comfort App
Infrared remote
control
(optional
accessory)
On-site button
Reference run
Closed and locked
— — —
Calibration and
teach-in run
Closed and locked
— — —
Open
Unlocked and open
Close
Closed —
—
Lock
Closed and locked
Intermediate stop User-defined, limited
opening width
—
Night vent
Night vent position (locked
in locking bolt/locking
part)
—
—
10-min. night vent
—
Night vent timer
(0‒60 min.)
—
— —
Open up to the end
position
Unlocked and fully open
(up to stop)
— —

Installation and operating instructions MHS400 smart
05.2017 7
3.3 Information on safety cut-off and jam protection
General information on safety cut-off
As soon as the path of a lift & slide sash becomes blocked (e.g. due to an obstacle or because it is stuck), it stops, moves for
approx. 4 seconds in the opposite direction and then comes to a final stop (see figure below).
For increased safety in the area around the bottom shear points between the lift & slide sash and the HS frame, in normal
motor-powered operation, the lift & slide sash only moves as far as a defined opening position.
Lift & slide sash moves ... ... hits an obstacle and stops... ... then moves for approx. 4 seconds
in the opposite direction and stops
Safety shutdown in systems with light curtain
If additional safety requirements apply, the optional terminal board must be ordered. To prevent injuries and damage, the safety cut-off function is activated, which causes the lift & slide sash to stop immediately. If equipped with a light curtain, the lift &
slide sash is opened fully to its stop.
Lift & slide sash moves ... ... an object moves into the safety zone... Lift & slide sash stops
3.4 LED indicator
The LED is attached to the lower edge of the slide drive SA. Please note the light indicators in the LED. The indicators and their
meanings are listed in the table below:
Function and meaning LED
System test Flashes yellow or red/green alternately
Teach in Flashes red
Move in direction of "Open" position Continuously green
Move in direction of "Close/Lock" position Continuously red
10-min. night vent (timer running) Flashes green
Night vent (without timer) Off
Intermediate stop (limited opening width) Off
Locked Off
After a power failure Flashes red

8
MHS400 smart Installation and operating instructions
05.2017
4. Scope of delivery
Number
of pieces
Size by slide drive
MHS400 smart
Size range in mm Colour
1 Scheme A, size 1 (one slide drive each on left or right) 2144 – 2794
White RAL 9003
Silver RAL 9006
1 Scheme A, size 2 (one slide drive each on left or right) 2795 – 4099
1 Scheme A, size 3 (one slide drive each on left or right) 4100 – 6666
1 Scheme C, size 1 (one slide drive each on left and right) 4284 – 5584
1 Scheme C, size 2 (one slide drive each on left and right) 5585 – 8194
1 Scheme C, size 3 (one slide drive each on left and right) 8195 – 13328
Pos.
Number
of pieces
Contents of slide drive SA carton Version
A C
1a 1 – Scheme A - Slide drive SA
Including 24 V power supply
1b – 2 Scheme C - Slide drive SA
2 1 2 Catch For slide drive SA
3 1 2 Catch base For lift & slide sash top
4 1 2
Packer (2.5 / 5 / 8/ 10 mm thick depending on profile
system)
For catch on lift & slide sash top
5 1 2 Cover cap M For catch
6
1 1 Cover profile SA
For slide drive SA
– 2 Cover profile SA with profile connector
7 1 1 Cover cap SA left For cover profile SA
8 1 1 Cover cap SA right For cover profile SA
9 1 2 Sash cable (flat ribbon cable, 6-wire) For slide drive SA
10 12 24 Cable holder Clip-on or screw-on
11 1 1 Network connection cable with Euro plug On slide drive SA, 5 m cable length
12 1 1 Terminal board (optional) For connecting light curtain*
13 1 1 Installation and operating instructions
*e.g. if the result of the risk analysis requires a light curtain
Pos. Pieces Contents of lift drive HA carton Version
14 1 2 Lift drive HA
15 1 2 Fixing plate HA For lift drive HA
16 1 2 Cover cap HA top For lift drive HA
17 1 2 Cover cap HA bottom For lift drive HA
18 4 8
M5 x 10 mm fixing screws
(inc. washers)
For fixing plate lift drive HA
19 2 4
M4 x 25 mm fixing screws
(inc. washers)
For cover cap HA top
20 1 2
M5 x 19 mm fixing screw
with M5 square nut
For cover cap HA bottom
21 1 1
Emergency operating handle Hexagon wrench WAF 8

Installation and operating instructions MHS400 smart
05.2017 9
4.1 Component and accessories overview
Fenstersysteme
Türsysteme
Komfortsysteme
MHS400 smart
1a
2
10
1b
2
3
4
5
6
7 8
6*
11
11
12
12
16
21
13
9
19
17
20
18
14
15
18

10
MHS400 smart Installation and operating instructions
05.2017
5. Size range
Scheme A Scheme C
Inside frame width (RIB) size 1 2144 mm – 2794 mm 4284 mm – 5584 mm
1
Inside frame width (RIB) size 2 2795 mm – 4099 mm 5585 mm – 8194 mm
1
Inside frame width (RIB) size 3 4100 mm – 6666 mm 8195 mm – 13328 mm
1
Sash height2 (standard for PORTAL HS) 1175 mm – 2675 mm 1175 mm – 2675 mm
Sash weight PORTAL HS 200 max. 200 kg max. 200 kg
Sash weight PORTAL HS 300 max. 300 kg max. 300 kg
Sash weight PORTAL HS 400 max. 400 kg max. 400 kg
Max. permissible sash weight for MHS400 smart max. 400 kg max. 400 kg
Backset (gear) PORTAL HS 200 27.5 mm 27.5 mm
Backset (gear) PORTAL HS 300 37.5 mm 37.5 mm
1)
per slide drive = RIB/2
2)
for other sash heights (on request), note the special cable length!
Dimension drawing – Scheme A
= =
RIB (measured with cover) 1
slide drive SA
Other cowl lengths (on request)
1 1
Dimension drawing – scheme C
Dimension 1 = inside frame edge
as far as centre of sash join edge
slide drive SA
Other cowl lengths (on request)
slide drive SA
Dimension 2 = inside frame edge
as far as centre of sash join edge
RIB (measured with cover) 1
Cable outlet
(selectable)
Cable outlet
(selectable)
1 1

Installation and operating instructions MHS400 smart
05.2017 11
6. On-site risk and hazard analysis
In order to assess the potential hazards of a power-operated window and to take the appropriate protective measures, you
must assess risks in the planning phase. A risk analysis provides you with all the information needed to assess risks and make
decisions concerning the safety of the window elements. The lift and slide element of the MHS400 smart can cause crushing
and shearing. You must carry out a risk and hazard analysis during the planning phase in accordance with VFF data sheet
KB.01 and the current Machinery Directive relating to the safety equipment and installation location as appropriate for the
individual property and conditions of use (e.g. in case of persons requiring special protection or commercial properties).
6.1 Risk and hazard analysis
• Takes into account the protective measures necessary in the planning phase
• Must be carried out before commissioning
• Provides information based on the individual installation location and instructs users on how to install the window system
in order to prevent or minimise possible hazards
• Draws attention to possible residual risks
The following aspects must be checked:
• Public or non-public area (private or industrial property)
• Installation location
• Users (authorised users, persons in need of protection or trained personnel)
• Special structural conditions
• Type of access control
• Requirements for added safety can be met with a light curtain
6.2 Instructions for assembly and installation
• Use flexible supply lines (route conduit tubes if necessary)
• When routing cables, avoid damaging the cables by crushing, bending or stretching them
• The concealed mains supply lines running to the MHS400 smart must be connected in branch boxes (these branch boxes
must be easily accessible for maintenance)
• Protect the MHS400 smart system against contamination by site material and humidity
• The hardware components must be securely fixed in place
• Connect to the mains supply only after you have tested for proper mechanical function
• Observe the applicable fabrication guidelines from the profile manufacturer
• To avoid personal injury, it is important to observe the safety precautions provided in these instructions and make sure
that these instructions are accessible at all times
6.3 Cooperation between trades and interfaces
In the context of project management, the work of the various trades must be carefully coordinated. If SIEGENIA components
are being connected to third-party installations or SIEGENIA products are being combined with parts by other manufacturers
(e.g. drives and controls), technical compatibility must be verified in advance by authorised personnel. For data collation
purposes, the technical data sheets and the latest versions of the installation and operating instructions must be handed over
to the trades involved when work commences.

12
MHS400 smart Installation and operating instructions
05.2017
7. Installation
7.1 Installation requirements
General information about installation
• The following description of the assembly process is a recommendation from SIEGENIA and describes the major steps
involved. The specific details of the assembly process are determined, amongst other factors, by the HS element used, by
the production process and by the window manufacturer's equipment and facilities.
• You will find specific steps for installation of the MHS400 smart on our download portal:
downloads.siegenia.com/de/00007/index.html
Tools required (not included in scope of delivery)
• Drill
• Ø 3 mm, Ø 7 mm, Ø 10 mm, Ø 15 mm timber or metal drill
• Phillips screwdriver (size 2)
• 1 screwdriver bit 90 mm long
• 2 screw clamps
• Folding rule
• Router (for timber elements)
• Between 2 and 4 assembly racks
• Recommendation: For straightforward and accurate positioning or fixing of the catch on the lift & slide sash,
SIEGENIA recommends using the catch jig (see accessories, page 53).
Materials required (not included in scope of delivery)
Screws
Number of units
(depending on RIB)*
Scheme
For component
For timber and PVC elements For aluminium elements A C
Screw
PC 4.1 x 38 mm
Flow-drill screw
M4 x 18 mm
10–25 20–50 Slide drive SA*
2 4 Catch
Screw
PC 4.1 x 19 mm
Flow-drill screw
M4 x 18 mm
4–6 8–12 Fixing plate HA
6 12 Cable holder
Note: All screwing points must be pre-drilled to Ø 3 mm. The length of the fixing screws for PVC elements must be
sufficient to penetrate deep enough into the reinforcing material to ensure a sufficient hold. Materials for lining the slide
drive SA (PVC plates, for example) must be provided by the customer for certain lift & slide profile systems.

Installation and operating instructions MHS400 smart
05.2017 13
Risk of mechanical defects if the MHS400 smart system is put into operation
unassembled.
› You must assemble the MHS400 smart first before putting it into operation!
Requirements to be met by the HS element
• The HS element must not be warped.
• The HS element must be installed vertically plumb in the reveal.
• The threshold must be properly and sufficiently supported — especially for wide or heavy HS elements (e.g. 400 kg).
• The displacement force must not be > 60 N.
• To avoid the risk of the connection cable getting crushed in the sash groove, the locking bolt or the locking part for the
night vent must always be installed at the bottom on the locking side (see the latest assembly instructions for more
information).
• The lift & slide sash must lock into the locking bolts or locking parts evenly.
• The cable routing of the cable in the lift & slide sash must be checked prior to assembly. The lift & slide sash must be
prepared for an optimum cable channel in the eurogroove.
• For scheme A, the concealed mains cable guide must always be located on the horizontal top section of the HS frame
near the locking side.
• For scheme C, the concealed mains cable guide can be located on the outside of the HS frame on either the left-hand
side or the right-hand side.
Requirements to be met by the hardware
• You can find detailed specifications for size ranges and sash weights in the relevant assembly instructions (e.g. assembly
instructions for PORTAL HS 200, PORTAL HS 300 or PORTAL HS 400).
• The hardware must be able to run smoothly (be in unrestricted working order). The max. torque on the handle must not
exceed 25 Nm.
Requirements to be met by the drive
Risk of mechanical defects if the MHS400 smart system is put into operation with
lift and slide elements that are not able to move freely.
› Only put MHS400 smart into operation if the smooth running of the lift and slide element can be ensured!
• The MHS400 smart system has not been tested as a locking unit in accordance with ENV 1627-1630.

14
MHS400 smart Installation and operating instructions
05.2017
7.2 Information about mains cable running
Important information for safety and assembly
The fitting of the mains cable is determined by the prevailing conditions on site. There are two assembly options:
Assembly option 1 – surface-mounted mains cable running
The MHS400 smart system is delivered as standard with a mains cable. The cable outlet for scheme A is always at the top of
the slide drive SA on the locking side (Fig. 1); for scheme C, it can be located on the outside of the slide drive SA on either the
left-hand side or the right-hand side. A notch for the cable outlet must be made on the cover cap SA of the cover profile SA
(see Fig. 2). A suitable mains socket must be located near the cable outlet. It is recommended to route the mains cable
through an appropriate installation duct.
1
2

Installation and operating instructions MHS400 smart
05.2017 15
Assembly option 2 – concealed mains cable running
If the customer is responsible for the concealed routing of the mains cable for the slide drive SA and the connection of the
slide drive SA (for scheme A in the power supply, for scheme C in the 5-pin socket), this work must be carried out by a
qualified electrician. When running mains cables for HS elements which have not yet been installed (e.g. new build and
renovation projects), a flexible cable (5 x 1.5 mm
2
incl. connection) for buttons (not included in scope of delivery) must be
provided by the customer and fed concealed through the top section of the HS frame (Fig. 3).
3
Holes for the cable inlet and outlet (each approx. Ø 10 mm) must be made for this purpose, with the centre of each hole
being positioned approx. 7 mm away from the inside frame edge (Fig. 4). All-pole safety isolation is required if the customer
is routing the mains cable. The isolated end of the mains cable must be located inside the power supply housing (scheme A)
or 5-pin socket (scheme C). The connection to the slide drive is made in accordance with the wiring diagrams. In the mounting angle for the slide drive SA, there is a sufficiently dimensioned recess for the cable outlet on the HS frame profile for
scheme A (Fig. 5). The mounting angle for scheme C does not have a recess for the cable outlet (Fig. 6). Concealed mains
cable running to the slide drive SA is through the top edge of the frame on the locking side
5 6
4
Y
7 mm
Inside frame
edge
Bottom edge of HS frame (without cover)
Dimension Y = 15 mm for timber and PVC elements
Dimension Y = central in relation to hollow section in the
case of aluminium elements
Mains cable outlet Ø 10 mm
(drill and deburr)
Recess in
mounting angle
Mains cableinlet
Ø 10 mm
Mains cable outlet Ø 10 mm
(drill and deburr)
Mains cableinlet
Ø 10 mm
Scheme A Scheme C
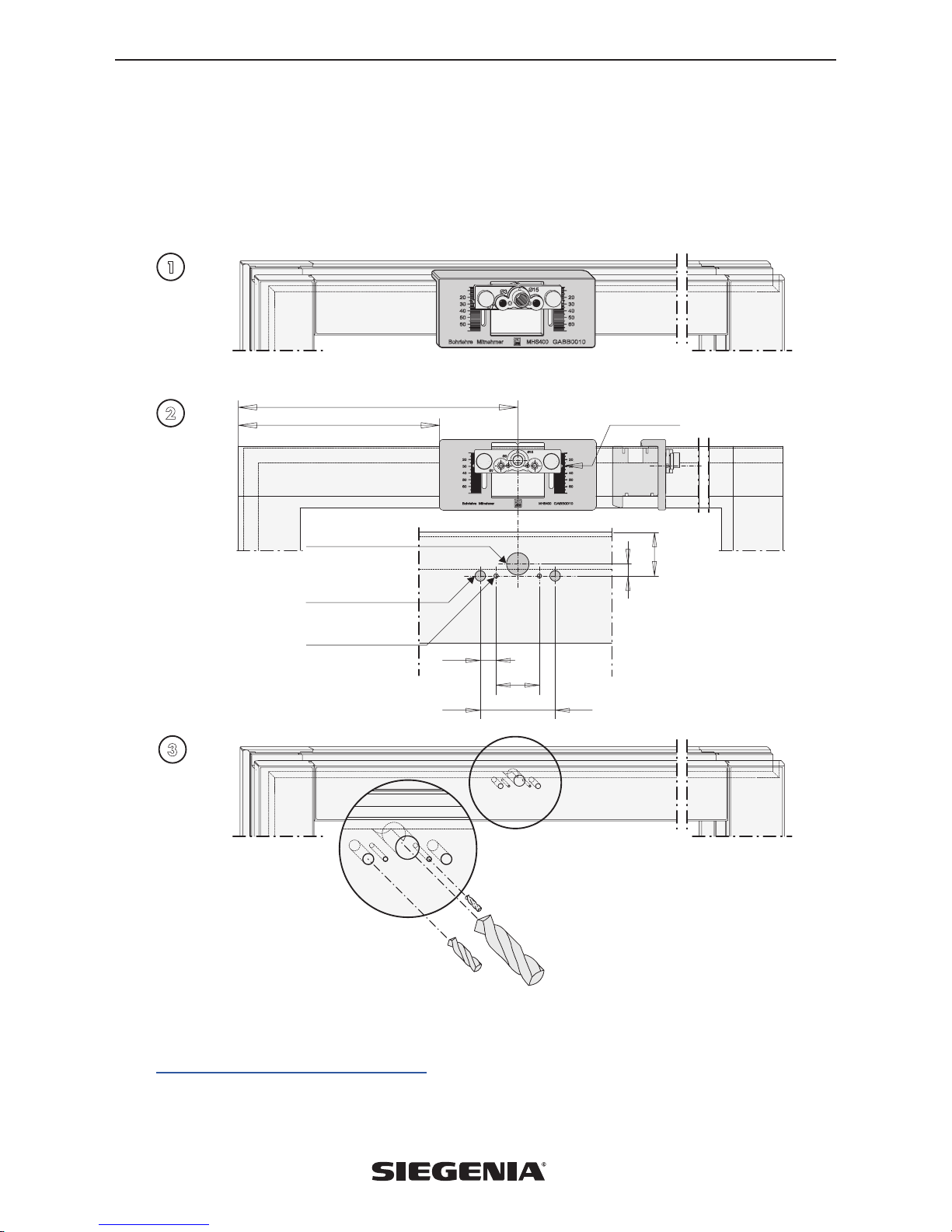
16
MHS400 smart Installation and operating instructions
05.2017
7.3 Drill holes on the lift & slide sash
7.3.1 Positioning and setting the catch jig (accessories)
Place the jig horizontally at the top of the lift & slide sash (Fig. 1), removing existing sash sealings first. Position and set the jig
in accordance with the dimensioning (Fig. 2).
Make the holes for the catch horizontally at the top, noting the drilling diameter (Fig. 3).
1
2
3
300
(416)
X
10,5
29
-0,2
50
8
Positioning and drilling dimensions for the drilled holes for the catch on
the lift & slide sash (Fig. timber profile DIN left - DIN right mirror image)
Adjustment dimension X
Cable feed-through
Ø 15
Supporting peg
Catch base Ø 7
Screw holes Ø 3
Hole Ø 3
for fixing screws
of the catch
Hole Ø 7
for supporting peg of the
catch base
Hole Ø 15
for cable feed-through
Attention: In order for the catch to be positioned correctly on the lift & slide sash, the correct set dimension X (Fig. 2) must
be used. The correct set dimension X for each HS profile system is listed in the installation steps for MHS400 smart on our
download portal:
downloads.siegenia.com/de/00007/index.html
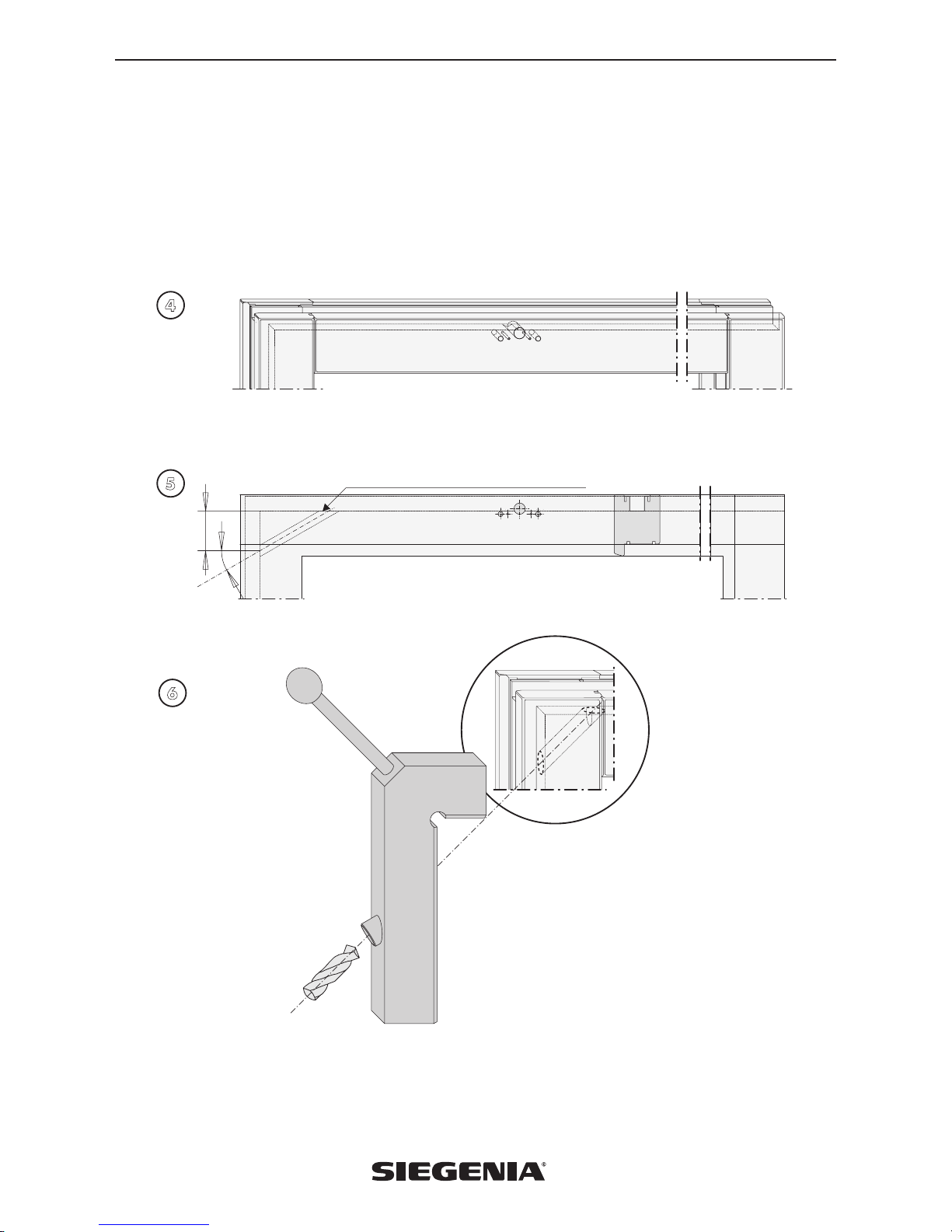
Installation and operating instructions MHS400 smart
05.2017 17
7.3.2 Through hole for cable channel in lift & slide sash
Timber elements require a through hole (Ø 15 mm) for the cable channel in the sash groove in the top corner of the lift & slide
sash on the locking side. This hole is created by pre-drilling to Ø 10 mm with a drill 180 mm long and then finish-drilling to Ø
15 mm (Fig. 5 and 6).
The through hole can be drilled with the through hole jig (see Fig. 6)
(see accessories, page 53).
Through holes do not have to be drilled for HS PVC and aluminium profiles. If necessary, the slider support can be machined
to accommodate the cable channel
4
50
30°
5
6
Drilling dimensions for the through hole on the lift & slide sash
(Fig. for timber profile DIN left - DIN right is a mirror image)
Through hole Ø 15 (for cable feed-through)
Jig
through hole
Drill 180 mm long
Ø 10 pre-drill and
then finish drilling to Ø 15