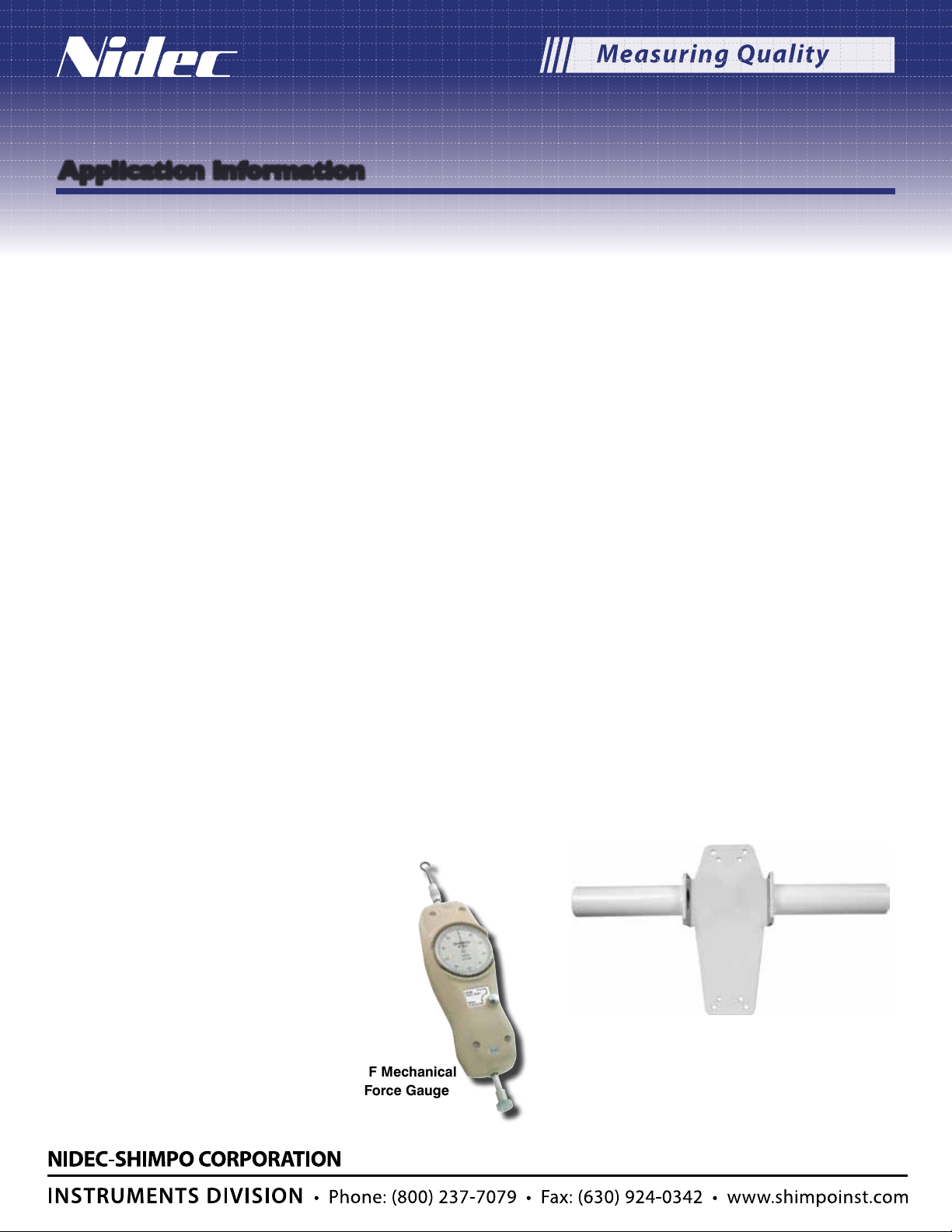
Application Information
Air Bag Deployment
A global aerospace company working for a government space agency was in the testing phases for its newly
designed reusable spacecraft. The lead project engineer encountered an issue with one of their quality verification tests and reached out to Nidec-Shimpo for a solution.
To ensure the craft endures a safe landing upon its return to earth, an air bag array located underneath must
quickly inflate. The inflation process commences with the automatic removal of a large canvas covering which
encloses the series of air bags. The verification involved testing that the canvas removed properly with the necessary force enabling uniform air bag deployment.
In order for the air bag system to properly protect the craft, the key requirement is that all airbags inflate at the
same time. The issue that the engineers routinely encountered was a simple method to acquire force readings
at the outer canvas so that each air bag inflation test point produced comparable results.
After reviewing their requirements, Shimpo recommended that they use the MF-100 Mechanical Force gauge with 100 lb range plus MFP-HANDLE to perform this test. The lead engineer mounted the gauge handle apparatus to six separate supports. Using reinforced cable, they connected each support to one central cable which was then attached to the canvas deployment apparatus.
The main release cable was then pulled to test the force which was produced when each bag deployed.
Utilizing the MF gauge’s Peak mode to obtain the maximum registered force, the results were recorded. After
comparing the readings from all the gauges, the engineers could readily verify if the air bags did in fact meet
the necessary deployment parameters.
This inflation test verified that the software, valve operation and inflation were all working correctly.
Equipment Used
• MF-100 Mechanical Force Gauge
with Peak Force Reading Mode
• MFP-HANDLE Handle Attachment
Optional MFP-HANDLE
MF Mechanical
Force Gauge