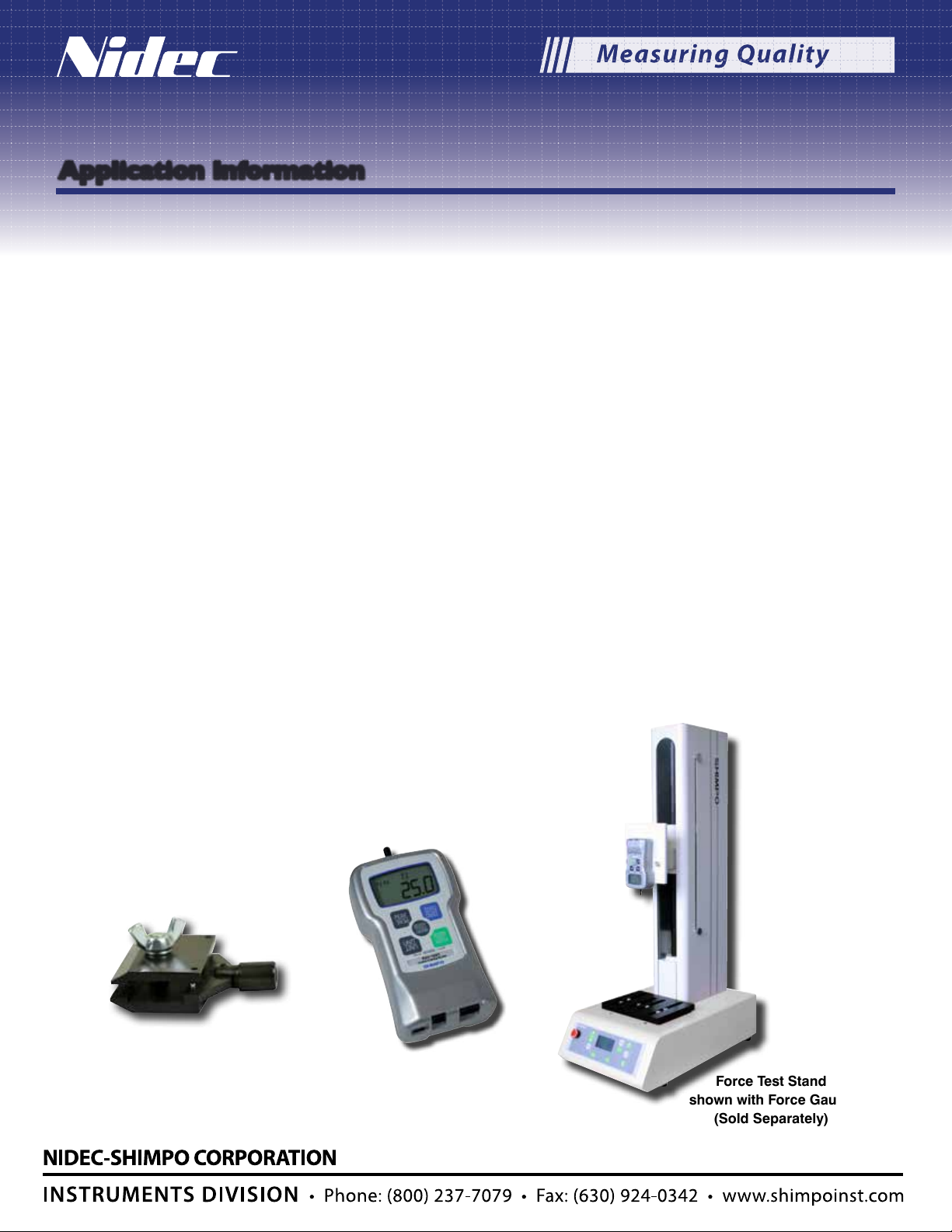
Application Information
Adhesion Force of Lithium-Ion Batteries
Rechargeable lithium-ion batteries have altered the landscape of battery usage and have become the go-to offering for manufacturers
of portable electronic devices, tools, landscaping equipment, and particularly the automotive industry with electric vehicles. A multitude
of benefits can account to this increased usage in these various applications. The primary factor is their longer operation capacity due
to a higher energy density compared to other varieties available. In addition to their extended operation, lithium-ion (Li-ion) batteries do
not require prolonged charging, have low self-discharge, are low maintenance and produce minimal memory effect that similar offerings
possess. Memory effect is the condition where batteries gradually lose their maximum energy capacity when they are recharged after
being partially discharged. Memory effect alone makes (Li-ion) batteries the sole choice for electric vehicles as full-charge capacity degradation eliminates the other technologies.
In rechargeable Li-ion batteries, the electrode and anode will switch positions. The electrode where electrons leave during discharging
will act as the electrode where electrons flow in during charging. Thus, the anode and cathode will swap places when the cell switches
between charging and discharging states. A potential downfall of the lithium-ion battery is that the electrodes must be meticulously
produced to ensure proper operation. In particular, the strength of the adhesion of the substrate coating to the electrode can directly
affect the lifetime of the battery. After application, the coating can undergo further stresses from subsequent manufacturing operations,
potentially decreasing the useful lifetime performance of the battery.
To combat this potential downfall, a prominent electric car manufacturer utilizes Nidec-Shimpo’s quality control instruments to test the
adhesion strength of their substrates on the battery’s electrodes via a tensile test. Through the combination of the FGS-220VC Motorized
Data-Logging Test Stand with the FGV-10XY 10 lb. (5 kg) capacity Digital Force Gauge, plus an FG-M6FLM50U Film Grip the manufacturer was able to consistently and reliably measure the tensile forces to peel the coating from the electrodes. With the ability to review
and analyze the data after each test on a PC, this system proved perfect for testing and comparing multiple designs and manufacturing
processes. By testing the adhesion force of the substrate to the electrodes with Shimpo’s force test stand apparatus, they were able to
create a quality control protocol that enabled ongoing quality inspection. The quality engineers were able to determine when manufactured electrodes complied with their newly developed standards and were acceptable for usage in the Li-ion electric car batteries. Their
Nidec-Shimpo tensile force testing system maintains their output of top quality product as well as enables them to make improvements
in their manufacturing processes.
Equipment Used
• FGS-220VC Force Test Stand
• FGV-10XY 10 lb (5 kg) Digital Force Gauge
• FG-M6FLM50U Film Grip
FG-M6FLM50U
Film Grip
FGV-XY with Memory &
Data Output
Force Test Stand
shown with Force Gauge
(Sold Separately)