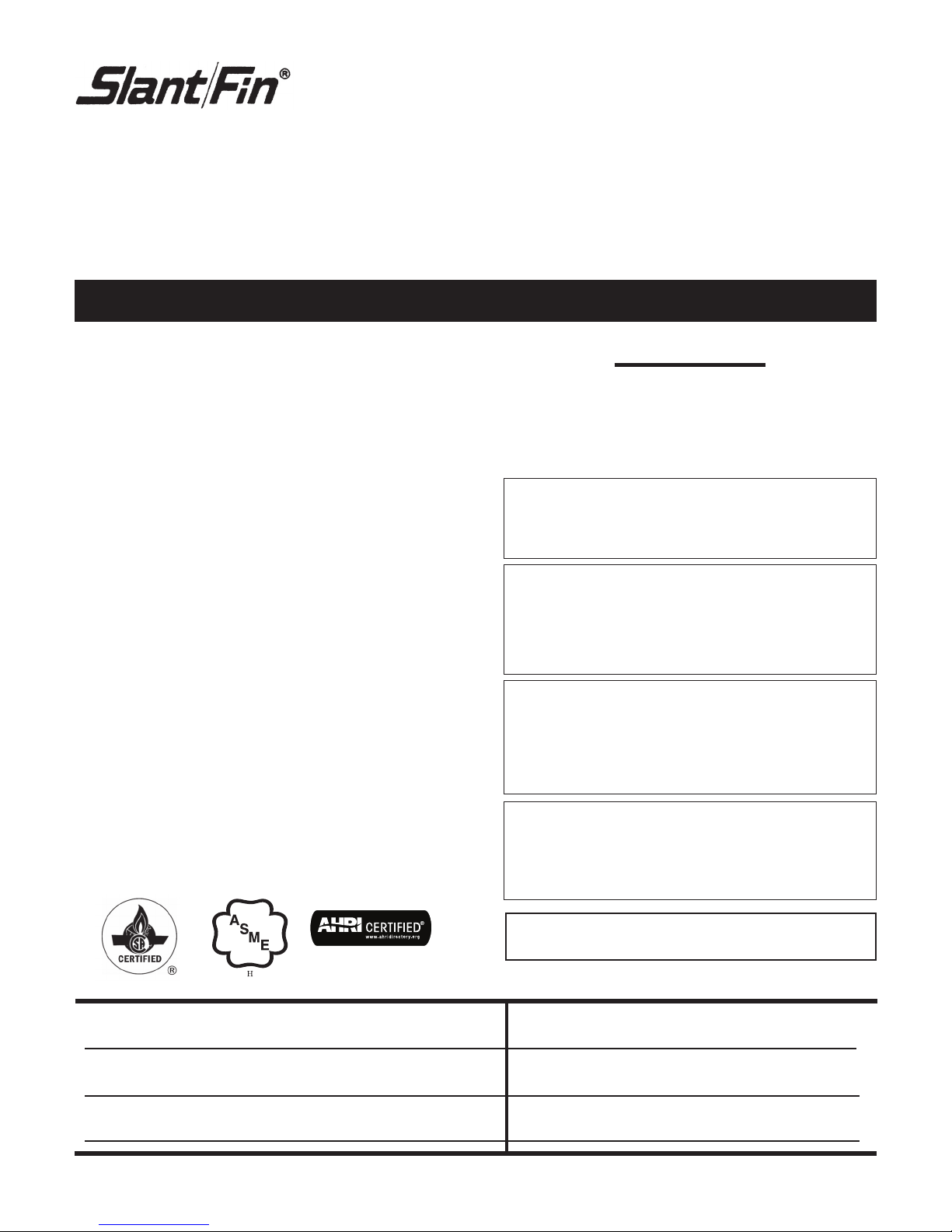
™
SENTRY
HOT WATER MODELS S-34 THROUGH S-150
GAS-FIRED CAST-IRON BOILERS FOR NATURAL AND L.P. PROPANE GASES
INSTALLATION AND OPERATING INSTRUCTIONS
CONTENTS . . . . . . . . . . . . . . . . . . . . . . . . . . . . . . . . . . . . . . PAGE
Dimensions . . . . . . . . . . . . . . . . . . . . . . . . . . . . . . . . . . . . . . . . . 2,3
Installation Requirements
Boiler Location . . . . . . . . . . . . . . . . . . . . . . . . . . . . . . . . . . . . . 3
Boiler Foundation. . . . . . . . . . . . . . . . . . . . . . . . . . . . . . . . . . . 3
Chimney Requirements . . . . . . . . . . . . . . . . . . . . . . . . . . . . . . 4
Minimum Clearance . . . . . . . . . . . . . . . . . . . . . . . . . . . . . . . . . 4
Draft Hood . . . . . . . . . . . . . . . . . . . . . . . . . . . . . . . . . . . . . . . . 4
Vent Piping . . . . . . . . . . . . . . . . . . . . . . . . . . . . . . . . . . . . . . . . 4
Vent Damper Installation . . . . . . . . . . . . . . . . . . . . . . . . . . 4,5,6
Gas Piping . . . . . . . . . . . . . . . . . . . . . . . . . . . . . . . . . . . . . . . . 6
Electrical Controls and Wiring . . . . . . . . . . . . . . . . . . . . . . . . . 6
Boiler Water Temperature Control . . . . . . . . . . . . . . . . . . . . 7–9
Multi-zoning . . . . . . . . . . . . . . . . . . . . . . . . . . . . . . . . . . . 10–11
Sequence of Operations . . . . . . . . . . . . . . . . . . . . . . . . . . . . 12
Boiler Room Air Supply and Ventilation . . . . . . . . . . . . . . . . 13
Water Piping at Boiler . . . . . . . . . . . . . . . . . . . . . . . . . . . . . . 13
Operating Instructions
Filling and Venting Water Systems . . . . . . . . . . . . . . . . . . . . 13
Burner Adjustment, Checking Gas Input. . . . . . . . . . . . . . . . 14
Care and Maintenance
General Maintenance . . . . . . . . . . . . . . . . . . . . . . . . . . . . . . . 15
Water Level Check . . . . . . . . . . . . . . . . . . . . . . . . . . . . . . . . . 16
Annual Inspection and Cleaning . . . . . . . . . . . . . . . . . . . . . . 16
Safety Check for Control Systems . . . . . . . . . . . . . . . . . . . . 16
Protection from Freezing/Water Treatment . . . . . . . . . . . . . . 16
Keeping Area Clear . . . . . . . . . . . . . . . . . . . . . . . . . . . . . . . . 16
Troubleshooting Guide . . . . . . . . . . . . . . . . . . . . . . . . . . . . . . . . 17
Replacement Parts . . . . . . . . . . . . . . . . . . . . . . . . . . . . . . . . . . . 18
Appendix A & B . . . . . . . . . . . . . . . . . . . . . . . . . . . . . . . . . . . . . . 18
Appendix C & D & E. . . . . . . . . . . . . . . . . . . . . . . . . . . . . . . . . . 19
READ ALL OF THE FOLLOWING
WARNINGS AND STATEMENTS
INSTALLATION INSTRUCTIONS
The installation must conform to the requirements of the authority
having jurisdiction or, in the absence of such requirements, to the
National Fuel Gas Code, ANSI Z223.1-latest edition or CSA
B149.1 latest edition for natural gas and propane. The installation
must also conform to the additional requirements in this Slant/Fin
Instruction Book.
In addition, where required by the authority having juris dic tion,
the installation must conform to American Society of Mechanical
Engineers Safety Code for Controls and Safety Devices for
Automatically Fired Boilers, No. CSD-1 or CSA B149.1 latest
edition
for natural gas and propane. If there is any conflict
in the above requirements, then the more stringent requirement
will apply.
This boiler, gas piping and accessories must be installed,
connected, serviced and repaired by a trained, experienced
service technician, familiar with all precautions required for gasfired equipment and licensed or otherwise qualified, in
compliance with the authority having jurisdiction.
IMPORTANT
BEFORE READING THE
WARNING
SEE "WARNING" ON PAGE 3
FOR LIQUEFIED PETROLEUM (L.P.)
PROPANE GAS-FIRED BOILERS
WARNING
Heating Contractor
Address
Phone Number
This manual must be left with owner and should be hung
on or adjacent to the boiler for reference.
Boiler Model Number
Boiler Serial Number
Installation Date
Printed in Canada 0713 Publication No. S-41
Part No. 46-0528C Revision B
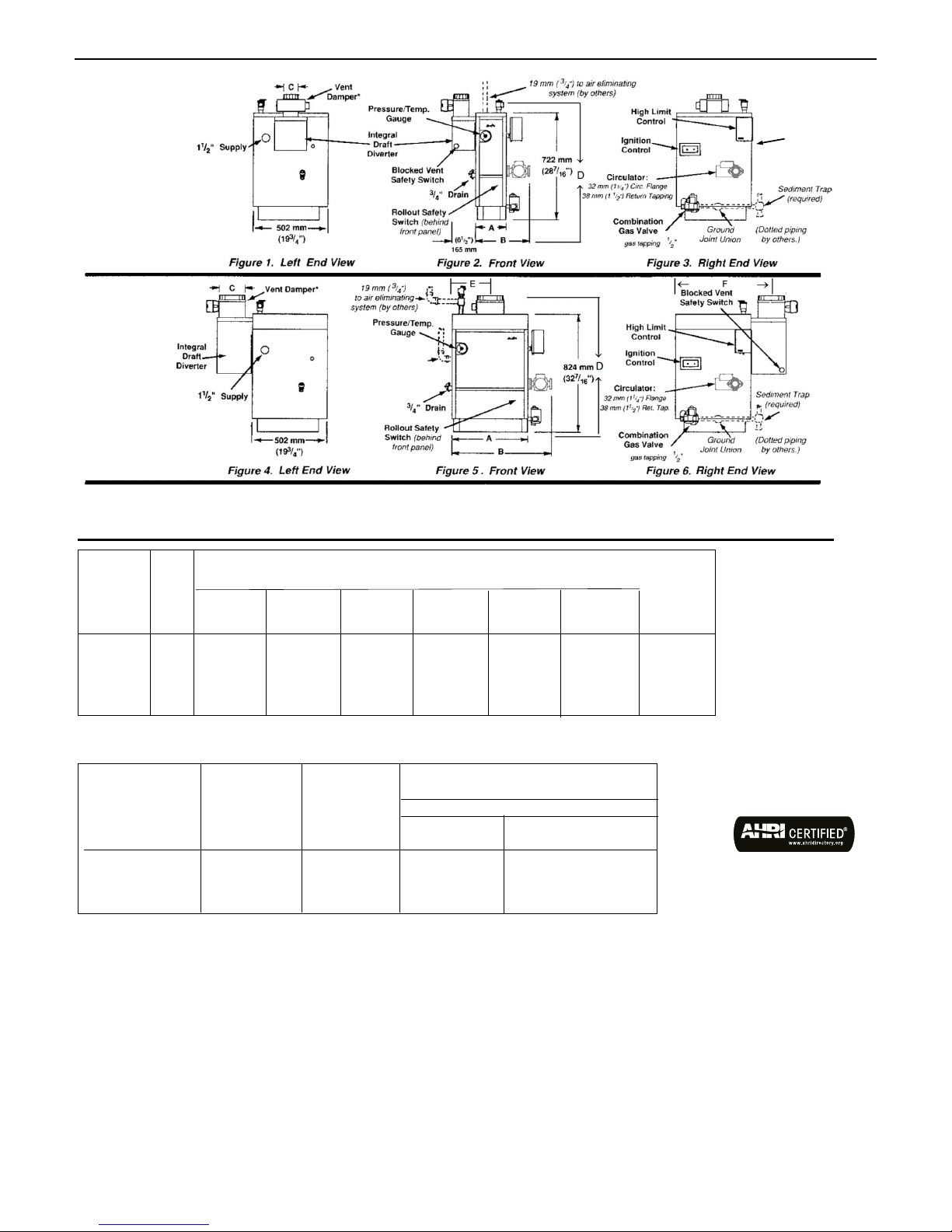
2
Dimensions
MODEL S-34
Dimensions
MODELS S-60
to S-150
Sentry
Install manual gas main
shutoff valve 1.52 m (5
ft.) above floor, when
required by local code.
Install sediment trap and
connect with ground
joint union. Dotted
piping by installing
contractor.
Install manual gas
main shutoff valve
1.52 m (5 ft.) above
floor, when required
by local code. Install
sediment trap and
connect with ground
joint union. Dotted
piping by installing
contractor.
Note: Height dimension increases by 1-3/4" when comustible floor kit is used.
* Vent damper may be installed horizontally on all models with use of a vent elbow. For more information, see figure 2, page 5.
Approx.
Total Wt.
Boiler No. of Full of
Model Sect.
A B C D E F
Water
mm in. mm in. mm in. mm in. mm in. mm in. kg lb.
S-34 2 206 81/8371 145/81024838 33 –––– 86 190
S-60 3 283 11
S-90 4 359 14
S-120 5 435 17
S-150 6 511 20
Boiler
Model
S-34
1
/8 448 175/8 1024940 37 114 41/2 660 26 113 250
1
/8 524 205/8 1275940 37 140 51/2 648 251/2 141 310
1
/8 600 235/8 1526940 37 191 71/2 635 25 166 365
1
/8 676 265/8 1787940 37 216 81/2 622 241/2 193 425
Orifice
Size
for
Gas Sea
Type Level
Orifice Sizes for High Altitudes
Reduce output 10%
Elevation
610-1220 m 1220-1375 m
(2000-4000 ft) (4000-4500 ft.)
Natural 47 48 49
Propane 56 56 57
S-60 thru S-150
Natural 50 51 51
Propane 57 58 59
Orifice indicated for sea level above are factory installed in boiler unless otherwise specified by the
local authority.
.
CHIMNEY RECOMMENDATIONS
HEIGHT: 4572 mm
(15 ft.) (minimum) from draft hood
skirt to top of chimney. INSIDE
DIAMETER: Same as dimension C (or
larger). NOTE: Larger chimney may
be required if two or more boilers or a
boiler and another appliance are
vented to a single chimney. Size of
Gas Line Connection to Boiler is 13
mm (1/2")
on both Natural and Propane boilers.
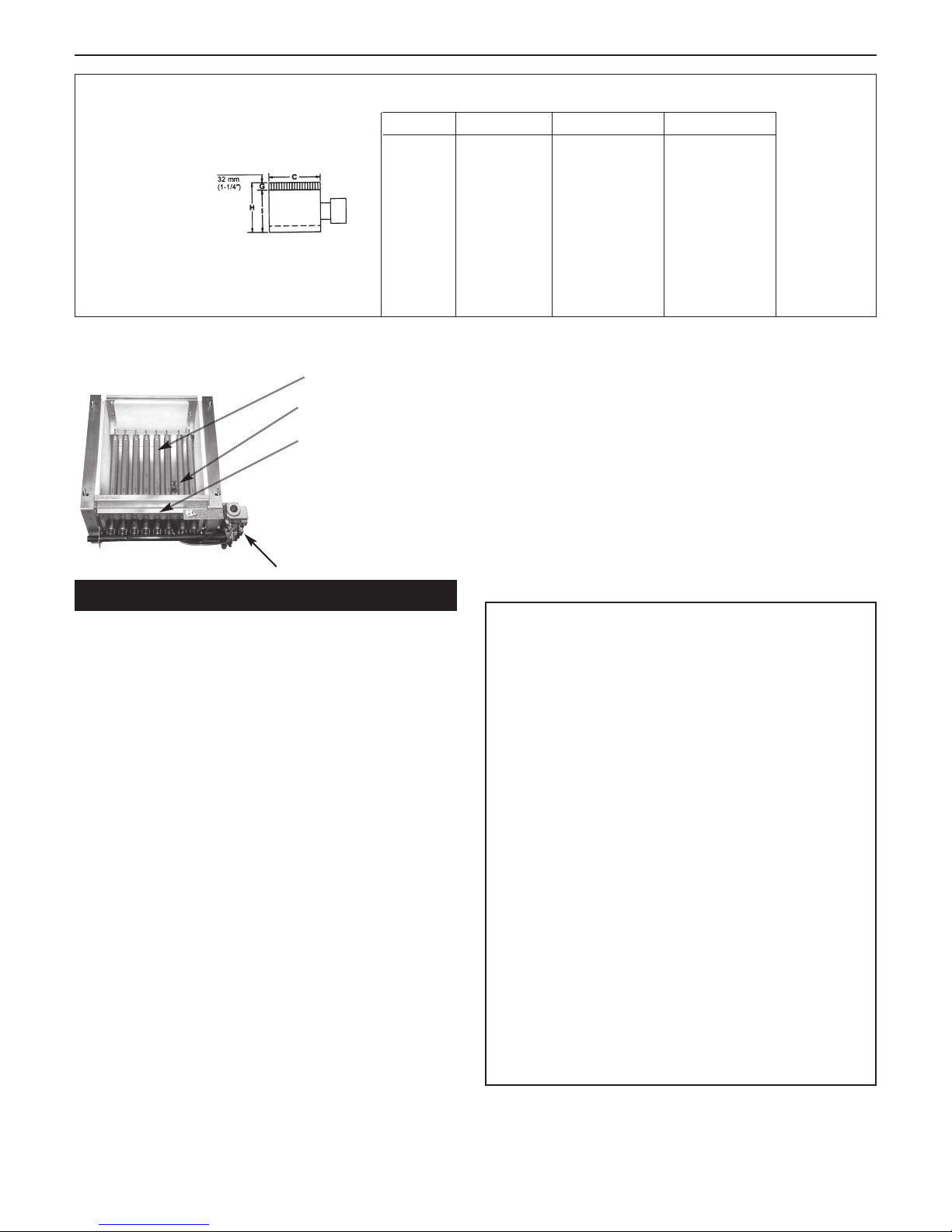
Sentry
3
VENT DAMPER DIMENSIONS
Base Assembly
Sentry Boiler
Burners
Pilot
Burner
Access
Door
Field Control (Effikal) Vent Damper
Model # C H I
S34 102mm 152mm 122mm
(4”) (6”) (4-13/16”)
S60 102mm 152mm 122mm
(4”) (6”) (4-13/16”)
S90 127mm 152mm 122mm
(5") (6") (4-13/16")
S120 152mm 165mm 135mm
(6") (6-1/2") (5-5/16")
S150 178mm 179mm 149mm
(7") (7-1/16") (5-7/8")
B. For installation on non-combustible floors only. The
Combustible Floor Kit part number printed on the boiler
rating plate is the only one to be used when installing on
combustible floors. The boiler must not be installed on
carpeting.
C. If boiler is to be located over buried conduit containing
electric wires or telephone cables, consult local codes or
the National Board of Fire Underwriters for specific
requirements.
Gas Valve
INSTALLATION REQUIREMENTS
IMPORTANT: This equipment must be installed in accordance
with the requirements of CSA B149.1 latest edition for natural
gas and propane. Installation Codes for Gas Burning Appliances must conform to requirements of the local gas company, local building codes, and other authorities which have
jurisdiction. Such requirements, where applicable, take precedence over these general instructions. All electrical connections must be in accordance with Canadian Electrical Code
C22.1 Part 1.
This installation must also conform to the additional requirements in this Slant/Fin Instruction Book.
NATURAL GAS-FIRED BOILER LOCATION
Provide a level, solid foundation for the boiler. Location
should be as near as possible to chimney or outside wall so
that the flue pipe from boiler is short and direct.
The location should also be such that the gas ignition system
components are protected from water (dripping, spraying,
rain, etc.) during appliance operation and service (circulator
replacement, condensate trap, control replacement, etc.).
BOILER FOUNDATION
A. Provide a solid, level foundation, capable of supporting
the weight of the boiler filled with water, and extending at
least 51 mm (2") past the jacket on all sides. See dimen-
of boiler, page 2.
sions
WARNING
LIQUEFIED PETROLEUM (L.P.) PROPANE
GAS-FIRED BOILER LOCATION
REQUIRES SPECIAL ATTENTION
Liquefied Petroleum (L.P.) propane gas is heavier than air.
Therefore, propane boilers, piping, valves must NOT be
installed in locations where propane leaking from defective
equipment and piping will “pool” in a basement or other
space below the leak.
A spark or flame from the boiler or other source may ignite
the accumulated propane gas causing an explosion or fire.
Provide a level, solid foundation for the boiler. Location
should be as near the chimney as possible so that the flue
pipe from boiler to chimney is short and direct.
The UNIFORM MECHANICAL CODE may be in effect in
your geographic area
The following precautions are cited by the 1994 UNIFORM
MECHANICAL CODE, section 304.6 or CSA B149.1 latest
edition for natural gas and propane:
“LPG Appliances. Liquefied petroleum gas-burning
appliances shall not be installed in a pit, basement or
similar location where heavier-than-air-gas might collect.
Appliances so fueled shall not be installed in an abovegrade under-floor space or basement unless such location is provided with an approved means for removal of
unburned gas.”
Consult Chapter 5 of
CODE or CSA B149.1 latest edition for propane for design
criteria of the “approved” means for removal of unburned
gas.
the 1994 UNIFORM MECHANICAL
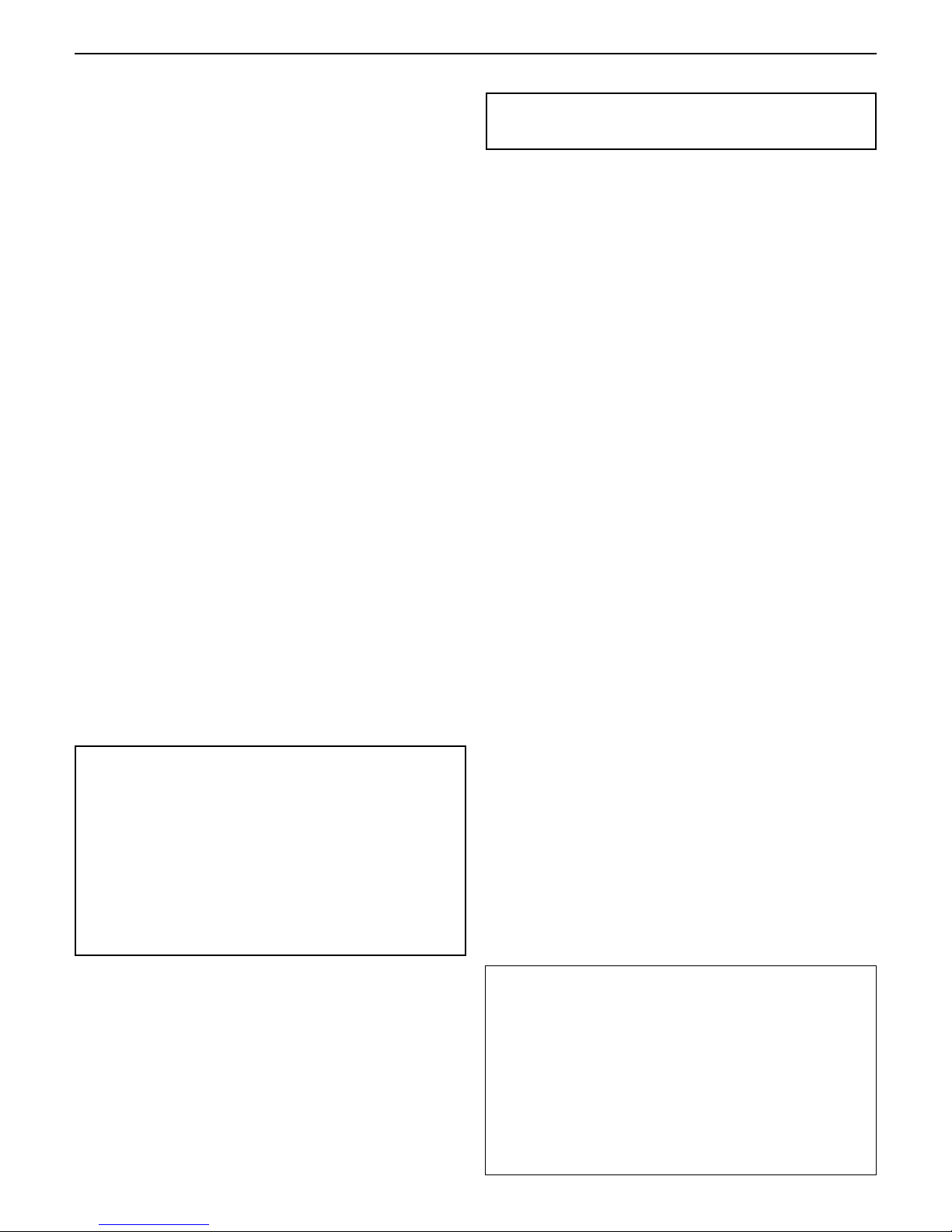
SAFETY
KEEP THE BOILER AREA CLEAR AND FREE FROM
COMBUSTIBLE MATERIALS, GASOLINE AND OTHER
FLAMMABLE VAPORS AND LIQUIDS.
VENT PIPING
A. Vent piping installation must be in accordance with the require-
ments of the local gas utility, local building codes and other
authorities having jurisdiction.
B. Boiler vent pipe must be the full diameter of the boiler outlet. See
dimensions, page 2.
C. If more than one appliance vents into a common breeching, the
area of the breeching must be equal to the area of the largest vent
plus 50% of the area of the additional vent areas. Vent connectors
serving appliances vented by natural draft shall not be connected
into any portion of mechanical draft systems operating under positive pressure. Horizontal breeching or vent pipe should be as high
as possible, consistent with codes, so that vertical vents from appliances will have a high rise above draft diverter openings. All horizontal runs must slope upwards not less than 20 mm/m (1/4 inch
per foot) of run. Horizontal portions of the venting system must be
supported to prevent sagging by securing each joint with metal
screws and by providing hanger spaced no greater than 1524 mm
(5 feet apart).
D. Vent or breeching into chimney should not be inserted past the
inside wall of the chimney liner.
E. All venting means should be inspected frequently. See Care and
Maintenance and separate User's Information Manual.
VENT DAMPER INSTALLATION
The vent damper referred to in the following instructions is
the Slant/Fin LTD/LTEE vent damper.
I. This device is design certified by C.S.A. for use ONLY on specific
Slant/Fin gas boiler models. These boilers must also be equipped
with a plate which states that the boiler must or may be used with
a Slant/Fin automatic vent damper device and indicates the proper vent damper model number. This device cannot be used with
a millivolt ignition system.
II. A. INSTALLATION INSTRUCTIONS BEFORE YOU START TO
INSTALL
1. Read this installation manual, the "DANGER" plate attached
to the top of the boiler, the "WARNING" on the wiring diagrams, vent damper carton and operator cover.
2. Perform pre-installation inspection as required by ANSI
specification Z21.66
or CSA B149.1latest edition for nat-
ural gas and propane
.
3. Turn off all electrical power, gas supply and wait for system to
cool (for previously installed boilers).
4. Carefully unpack the unit. DO NOT FORCE IT OPEN OR
CLOSED! Forcing the damper may damage the gear train
and void the warranty.
4
Sentry
CHIMNEY REQUIREMENTS
A. Sentry boilers may be vented into a masonry vitreous tile-lined
chimney or type “B” venting system NOT EXPOSED to the OUTDOORS below the roof line.
Venting and sizing of venting system must be in accordance with
the requirements of the local gas utility, local building codes and
other authorities having jurisdiction.
If a masonry chimney is exposed to the outdoors on one or more
sides below the roof line (exterior chimney), ONE of the following
options apply:
1. Chimney must be re-lined with an approved metallic liner.
When this is done, the chimney will be considered NOT
exposed to the outdoors and the requirements for NONexposed chimneys and/or local codes will apply.
2. If an exposed tile-lined chimney is to be used WITHOUT a
metallic liner, the boiler must first meet the requirements of the
following tables and paragraphs of the National Fuel Gas
Code:
I. For Single Sentry Boiler—Paragraph 11.2.9 and table
11.11.
II. For multiple appliances—Paragraph 11.3.18 and table
11.12 (or 11.13 if applicable).
In addition, all requirements of the local gas utility, local building codes and other authorities having jurisdiction apply.
B. If an existing boiler is removed from a common venting system,
the common venting system may be too large for proper venting
of the remaining appliances connected to the common vent. Follow the test procedure shown in Appendix “A” on page 19 of this
manual to insure proper operation of venting system and appliances.
C. Inspect for proper and tight construction. Any restrictions or
obstructions must be removed. An existing chimney may require
cleaning.
D. Chimney or vent must extend at least 914 mm (3 feet) above any
ridge within 3048 mm(10 feet) of the chimney.
MINIMUM CLEARANCES FOR COMBUSTIBLE
CONSTRUCTIONS
* Allow extra clearance from combustibles for additional venting
A. Minimum boiler clearances shall be as follows:
B. Provide accessibility clearance of 510 mm (24”) on sides requir-
ing servicing and 457 mm (18”) on sides used for passage.
C. All minimum clearances shown above must be met. This may
result in increased values of some minimum clearances in order
to maintain the minimum clearances of others.
D. Clearance from hot water pipes shall be 25 mm (1 inch)**.
** At points where hot water pipes emerge from a floor, wall or ceiling,
the clearance at the opening through the finished floor, wall or ceiling
boards may not be less than 13 mm (1/2 inch). Each such opening
shall be covered with a plate of non combustible material.
SENTRY SERIES
MINIMUM CLEARANCES FOR COMBUSTIBLE
CONSTRUC TION. MINIMUM ALCOVE AND CLOSET
CLEARANCE.
S-34 thru
S-150
Front 152 mm (6”)
Rear 152 mm (6”)
Left Side 152 mm (6”)
Right Side 305 mm (12”)
Top (above boiler) 305 mm (12”)*
Flue Connector 152 mm (6”)
WARNING—DANGER
Once you have begun vent damper installation procedure,
DO NOT restore electric power and gas supply until installation and inspection have been completed (in order to prevent the main burners from operating). DO NOT operate
the boiler until the vent damper harness "FEMALE PLUG" is
plugged into "MALE PLUG" (as described in the installation
instructions), and the vent damper installation and checkout procedures have been completed. Failure to observe
this warning may create a hazardous condition that could
cause an explosion or carbon monoxide poisoning.
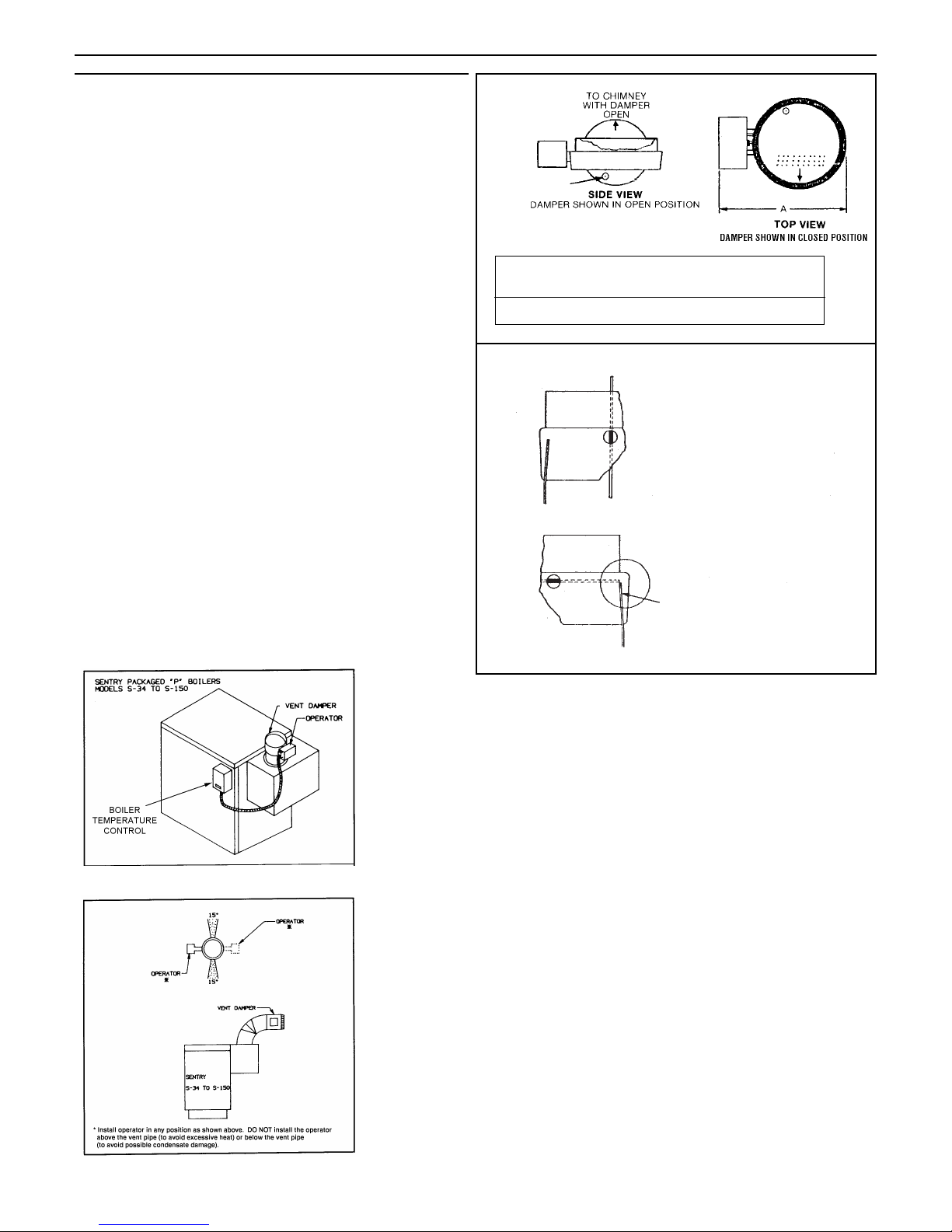
Sentry
5
. 5. This device must be installed after the appliance draft hood
(between the draft hood outlet and the connector to the outdoor chimney or vent) as close to the draft hood as practicable, and without modification of the draft hood or the
damper. (See figures 1 and 2.)
6. The inlet size of the vent damper must be the same nominal
trade size as the outlet of the draft hood.
7. This device must be located in a venting system or section of
a venting system so that it serves only the single appliance
for which it is installed. (See fig. 5.)
8. Clearances of not less than 152 mm (6 inches) must be
maintained from combustible materials, with provisions for
access for service.
B. NOW, PROCEED AS FOLLOWS:
1.Separate the vent pipe directly on top of the draft hood or
diverter and place damper in position as shown in figures 1 -
5. The vent damper must be installed so that the damper
position indicator is in a visible location after installation. See
figure 4 for position indicator description. The arrow imprint
on the damper should point in direction of vent gas flow
(towards chimney). Re-assemble the vent piping. Be sure
the vent damper is well seated and fastened with 3 sheet
metal screws. Screws should be no longer than 13 mm (
1
/2
inch). See figure 6.
2. Be sure that undersized vent pipe does not block movement
of damper vane (see figure 4).
3. Boilers that have a vent damper are factory wired with a male
plug.
a) Attach the flexible metallic conduit vent damper harness to
the right hand side of the jacket by passing the free end of
the harness through the 22 mm (
7
/8") diameter hole in the
top of the jacket, and using the BX connector at the free
end of the metallic conduit, fasten to jacket.
22 mm (7/8") DIA.K.O.
FIGURE 3
FIGURE 4
b) Connect "FEMALE PLUG" (free end of vent damper har-
ness) into "MALE PLUG" (see correct wiring diagram for
intermittent pilots).
c) The other end of the flexible metal conduit has a small
molex plug and a 90 degree metal conduit connector.
Route the molex receptacle through the conduit bracket
on the vent damper. Place the harness receptacle into the
damper plug. Securely fasten the harness conduit connector to the conduit bracket by carefully pushing it into
the hole in the bracket.
4. Restore electrical power and turn on gas supply.
C. AFTER INSTALLATION:
1. Operate system through two complete cycles to check for
opening and closing in proper sequence, and proper burner
operation. DAMPER MUST BE IN OPEN POSITION WHEN
BOILER MAIN BURNERS ARE OPERATING.
2. Perform installation checks as required by ANSI specification
Z21.66
or CSA B149.1 latest edition for natural gas and
propane
.
3. Replace the front cover of the boiler.
4. Check the troubleshooting section if problems arise with the
installation.
TABLE
Vent 102 mm 127 mm 152 mm 178 mm
Size (4") (5") (6") (7")
A 237 mm 262 mm 287 mm 313 mm
(9
5
/16") (105/16") (115/16") (125/16")
NOTE: DAMPER POSITION INDICATOR
MAY BE VIEWED THROUGH HOLE
IN THE CASTING ON THE SIDE
OPPOSITE THE OPERATOR
DAMPER VANE FULLY OPEN
UNDERSIZED VENT PIPE MAY BLOCK
THE MOVEMENT OF THE DAMPER
VANE. IF THIS OCCURS CUT OFF 1/2 OF
THE MALE (CRIMPED) END OF VENT
PIPE AND REFIT.
Figure 1. Vertical Installation of Vent Damper on
Sentry “S” Boilers
Figure 2. Horizontal Installation of Vent Damper
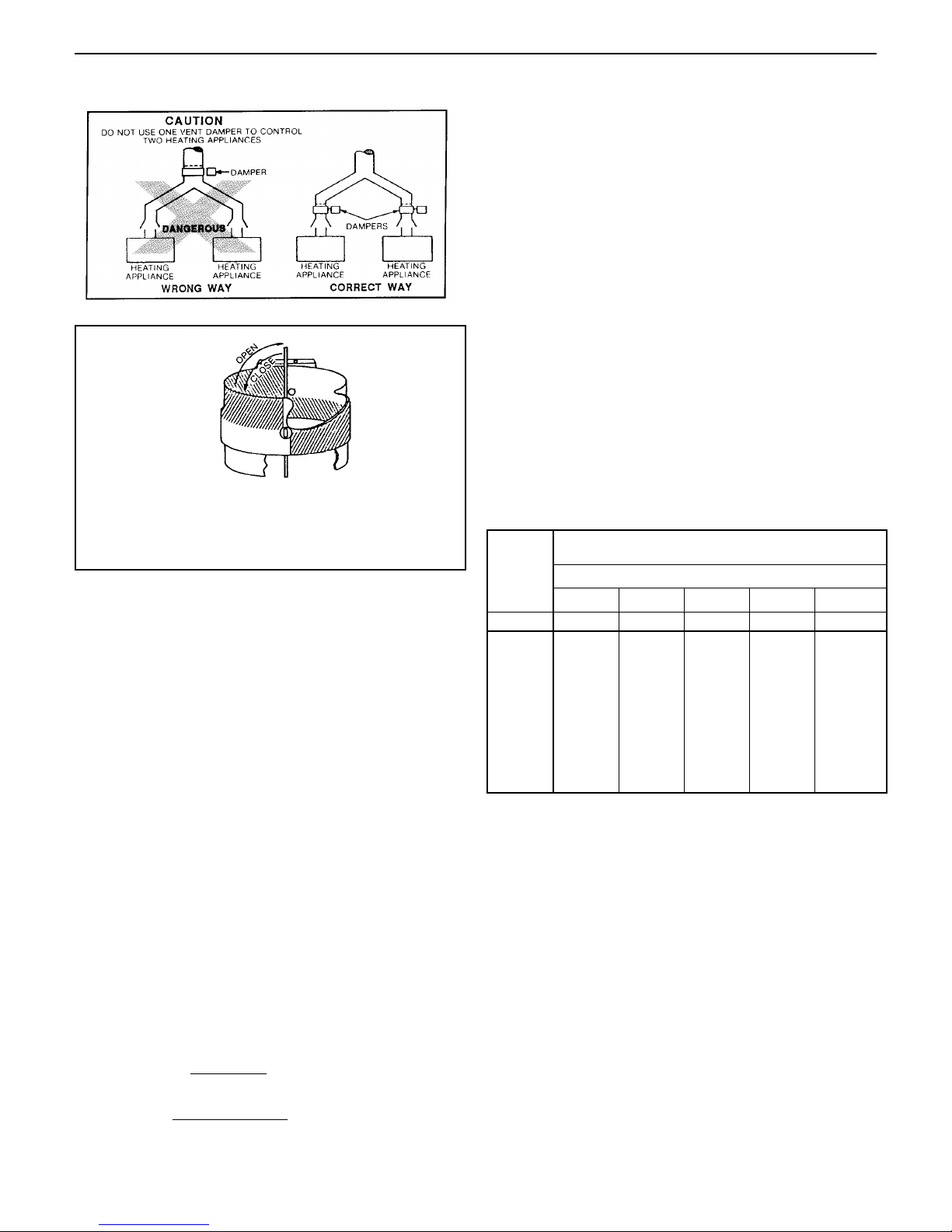
D. THERMOSTAT HEAT ANTICIPATOR ADJUSTMENTS
If the 24V room thermostat that controls the boiler has an
adjustment heat anticipator, it must be set to the AMP draw of
the boiler. Connect the system to the thermostat and run the
system. Measure the current draw through the thermostat
wires and set anticipator accordingly. See Appendix "B".
GAS PIPING
A. Local installation codes apply. The pipe joint compound
used on threads must be resistant to the action of liquefied
petroleum gases.
B. The gas supply line to the boiler should be run directly from
the meter for natural gas or from the fuel tank for L.P.
propane gas. See page 2 for location of union and manual
main shutoff valve that may be specified locally.
Selecting pipe size for natural gas:
1. Measure or estimate the length of piping from the meter
to the installation site.
2. Consult gas supplier for heating value of gas-W/m
3
(BTU/cu. ft.).
3. Divide boiler rated input by heating value to find gas
flow in piping (m
3
/hr) (cu. ft. per hour).
4. Use table below to select proper pipe size.
Example: Boiler model S-150 is to be installed. Distance
from gas meter to the boiler is 6.1m (20 ft). Heating value of
natural gas is 10560 W/m
3
(1020 BTU/cu. ft.) Select proper
pipe size.
At 6.1m (20 ft.) length of pipe, match required capacity
from table below (choose higher capacity, in this case is
5.4 m
3
[190 cu. ft.] per hour). Required pipe size is 3/4".
Improper gas pipe sizing will result in pilot flame outages,
insufficient heat and other installation difficulties. For more
information or if other appliances are to be attached to the
piping system, see Appendix C of National Fuel Gas Code
ANSI Z223.1-latest edition or CSA B149.1 latest edition for
natural gas and propane.
C. The boiler and its gas connection must be leak tested
before placing the boiler in operation. Use liquid soap solution for all gas leak testing. DO NOT use open flame.
This boiler must be isolated from the gas supply piping system by closing its individual manual shutoff valve during
any pressure testing of the gas supply piping system at test
pressures equal to or less than 3.5 kPa (1/2 PSIG).
D. All gas piping used should be inspected thoroughly for
cleanliness before makeup. A sediment trap must be provided, as illustrated on page 2.
E. The minimum and maximum gas supply pressure (at the
inlet of gas valve) are shown on the boiler rating plate for
the type of gas used. Gas supply pressure should never be
less than minimum or more than maximum pressure when
the boiler or any other appliance is turned on or off.
ELECTRICAL CONTROLS AND WIRING
A. The electrical power to the boiler must be on a separately
fused and live circuit.
B. If an external electrical source is utilized, the boiler, when
installed, must be electrically grounded in accordance with
the requirements of the authority having jurisdiction or, in
absence of such requirements, with the Canadian Electric
Code – CSA-C22.1, Part 1 – latest edition.
C. Basic control wiring diagrams are supplied. Other control
systems may be factory supplied, see User's Information
Manual and Instructions packed with control system supplied.
D. After placing the boiler in operation, the safety shutoff device
must be tested. See page 17 safety check.
Gas flow = = 4.2 m3/hr
44 000 W/hr
10 560 W/m
3
(Gas flow =
= 147.06 cu. ft. per hour)
150 000 BTU/hour
1020 BTU/cu. ft.
13mm (1/2”) 19mm (3/4”) 25mm (1”) 32mm (1 1/4”) 38mm (1 1/2”)
mft
m3/hr cu.ft./ hr. m3/hr cu.ft./ hr. m3/hr cu.ft./ hr. m3/hr cu.ft./ hr. m3/hr cu.ft./ hr.
3.0 10 3.7 132 7.9 278 14.7 520 29.7 1050 45.3 1600
6.1 20 2.6 92 5.4 190 9.9 350 20.7 730 31.1 1100
9.1 30 2.1 73 4.3 152 8.1 285 16.7 590 25.2 890
12.2 40 1.8 63 3.7 130 6.9 245 14.2 500 21.5 760
15.2 50 1.6 56 3.3 115 6.1 215 12.5 440 19.0 670
18.3 60 1.4 50 3.0 105 5.5 195 11.3 400 17.3 610
21.3 70 1.3 46 2.7 96 5.1 180 10.5 370 15.9 560
24.3 80 1.2 43 2.5 90 4.8 170 9.9 350 15.0 530
27.4 90 1.1 40 2.4 84 4.5 160 9.1 320 13.9 490
30.5 100 1.1 38 2.2 79 4.2 150 8.6 305 13.0 460
Length
of Pipe
Gas Flow In Piping
Pressure drop=8mm(0.3") water column, 0.60 specific gravity gas.
Iron Pipe Size (Ips) inches
At pressure drop of 0.3 in. water, specific gravity = 0.60 gas.
FIGURE 6
CAUTION
TO PREVENT INTERFERENCE WITH DAMPER VANE
MOVEMENT, SCREWS OR POP RIVETS MUST NOT
BE LOCATED IN SHADED AREAS AND MUST NOT
EXCEED 13 MM (
1
/2") IN LENGTH.
SECTION
REMOVED
TO SHOW
SHADED
AREA
FIGURE 5
Sentry
6