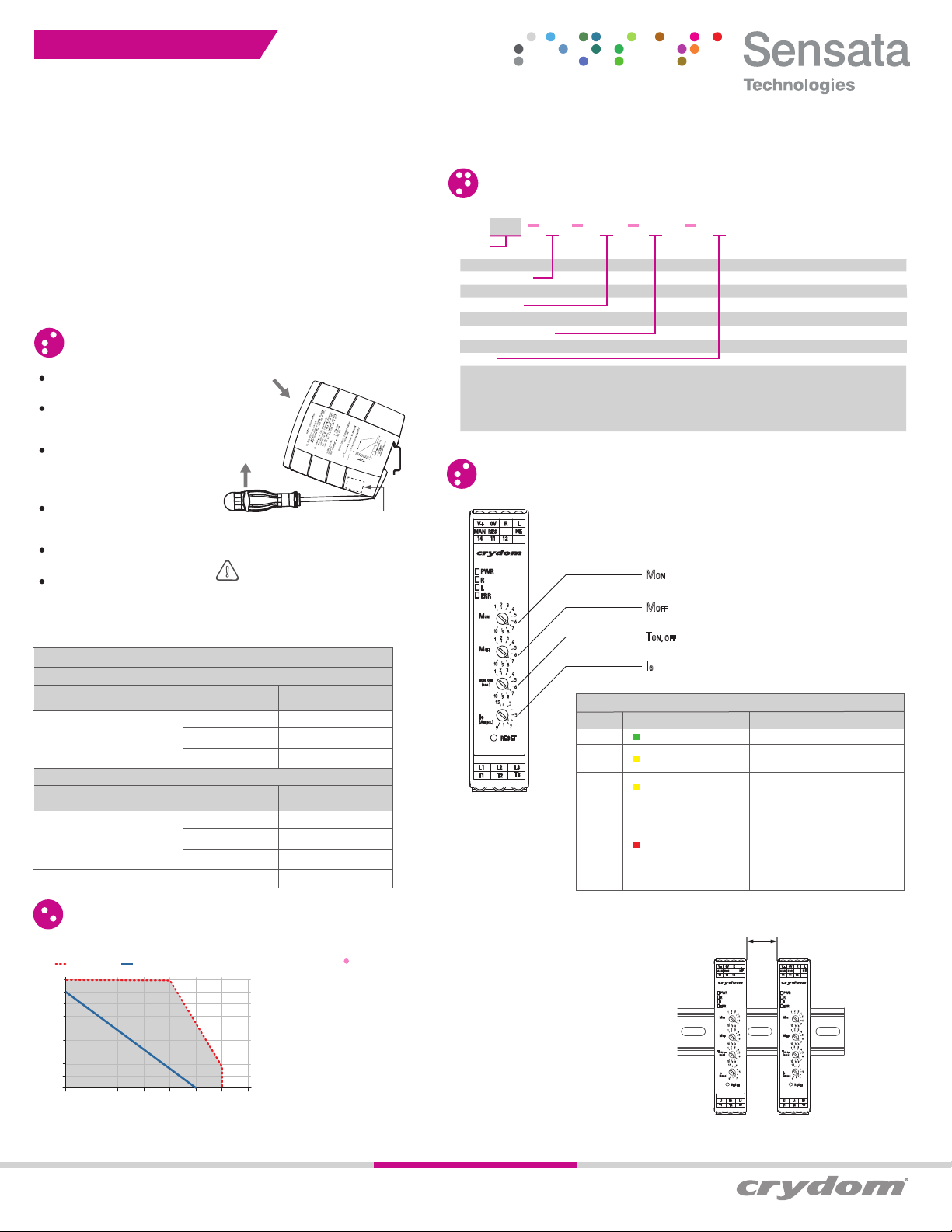
INSTALLATION GUIDE
|DRMS Series
HYBRID MOTOR STARTERS
DRMS Hybrid Motor Starters are intelligent and convenient solutions for controlling
3-phase asynchronous motors. These compact devices can provide up to 6 different
functions: Forward / Reverse, Soft Start / Soft Stop, Motor Overload Protection, and
Mains Isolating Relay.
Read all installation instructions before using the DRMS Hybrid Motor Starter and
refer to the product datasheet for more information.
For assistance, please contact Tech Support.
INSTALLATION INSTRUCTIONS
Install the motor starter on the DIN
rail (as shown in fig.1).
Wire the motor starter to the control
side. AWG #22 (0.5 mm
AWG #14 (2.5 mm
Wire the motor starter to the output
side. AWG #30 (0.05mm
AWG #12 (4 mm
2
) minimum,
2
) maximum.
2
) minimum,
2
) maximum
(stranded/solid).
Maximum terminal screw torque
control side 3.46 lb-in (0.39 Nm) &
output side 5-7 lb-in (0.564-0.79 Nm).
Use 60°C / 75°C copper conductors
only.
If multiple units are installed, be sure
to follow derating curves.
WARNING! Latching system could be damaged if product is removed incorrectly out
of the DIN rail.
TABLE 1. DRMS Motor Circuit Ratings
Per UL508, CSA C22.2 No. 14-13
Network Voltage
200-480VAC, 3-phase, 50/60Hz
Per UL 60947-4-2, CSA 60947-4-2
Network Voltage
200-300VAC, 3-phase, 50/60Hz
301-480VAC, 3-phase, 50/60Hz
Push to install on DIN rail
Pull to remove from
DIN rail
When designing circuits with this motor starter
unit, components that generate magnetic fields
like contactors, transformers, or high current
wires, should not be placed close to the current
sensor.
Ambient
Temperature
40ºC
50ºC
60ºC
Ambient
Temperature
40ºC
50ºC
60ºC
60ºC
Current sensor position
fig. 1
FLA / LRA
7.6 / 45.6
4.8 / 28.8
2.1 / 12.6
FLA / LRA
7.6 / 45.6
4.8 / 28.8
2.1 / 12.6
2.1 / 12.6
DIN rail
(35mm)
ORDERING OPTIONS
DRMS
Series
DRMS
Operating Voltage
48:
200-480 VAC
Control Voltage
D: 10-30 VDC
Load Current per Phase
9: 9 Amps
Function
1: Reversing Starter with Overload Protection
2: Reversing Starter with Soft Start, Soft Stop and
Overload Protection
3: Reversing Starter with Soft Start, Soft Stop,
Overload Protection and Mains Isolating Relay
48 D 9 1
INDICATORS AND SETTING FACILITIES
M : Starting torque at Soft Start, 30 to 80 %
M : Deceleration torque at Soft Stop, 30 to 80 %
: Starting / Deceleration ramp, 1 to 10 s
Nominal motor current, 1.6 to 9.0 Arms
LED COLOR
PWR
R
L
fig. 2
ERR
Green
Yellow
Yellow
Red
TABLE 2. Indicators
STATUSINDICATOR
Permanent ON
Permanent ON
Flashing
Permanent ON
Flashing
Flashing
1 pulse
2 pulses
3 pulses
4 pulses
5 pulses
6 pulses
7 pulses
8 pulses
Auxiliary supply connected.
Forward, power semiconductors bridged.
Forward, ramp operation.
Reverse, power semiconductors bridged.
Reverse, ramp operation.
Error detected:
Over temperature on semiconductors.
Wrong mains frecuency.
Phase reversal detected.
At least 1 phase is missing.
Motor overcurrent detected.
Mains isolating relay not disconnected.
Incorrect mesurement circu t.
Motor protection has responded.
DESCRIPTION
DERATING CURVES
Single unit
9
8
7
6
5
4
3
2
Load Current (Amps)
1
0
DRMS48D9x
Multiple units, without spacing
100 20 30 40 50 60 70
Ambient Temperature (ºC)
Important Considerations
Be sure to use input and output voltages within operating
ranges.
To achieve maximum ratings, there must be a minimum
spacing of 0.9 in (22 mm) between the devices in free air.
(See fig. 3)
For optimal thermal performance, motor starter should be
aligned vertically to maximize natural convection air flow.
Maximum surrounding air temperature is 60 °C (please see
derating curve). For maximum ratings the surrounding air
temperature should not exceed 40°C.
0.9 in
[22 mm]
Minimum
fig. 3 Clearence on multiple units mounting for achieving maximum rating
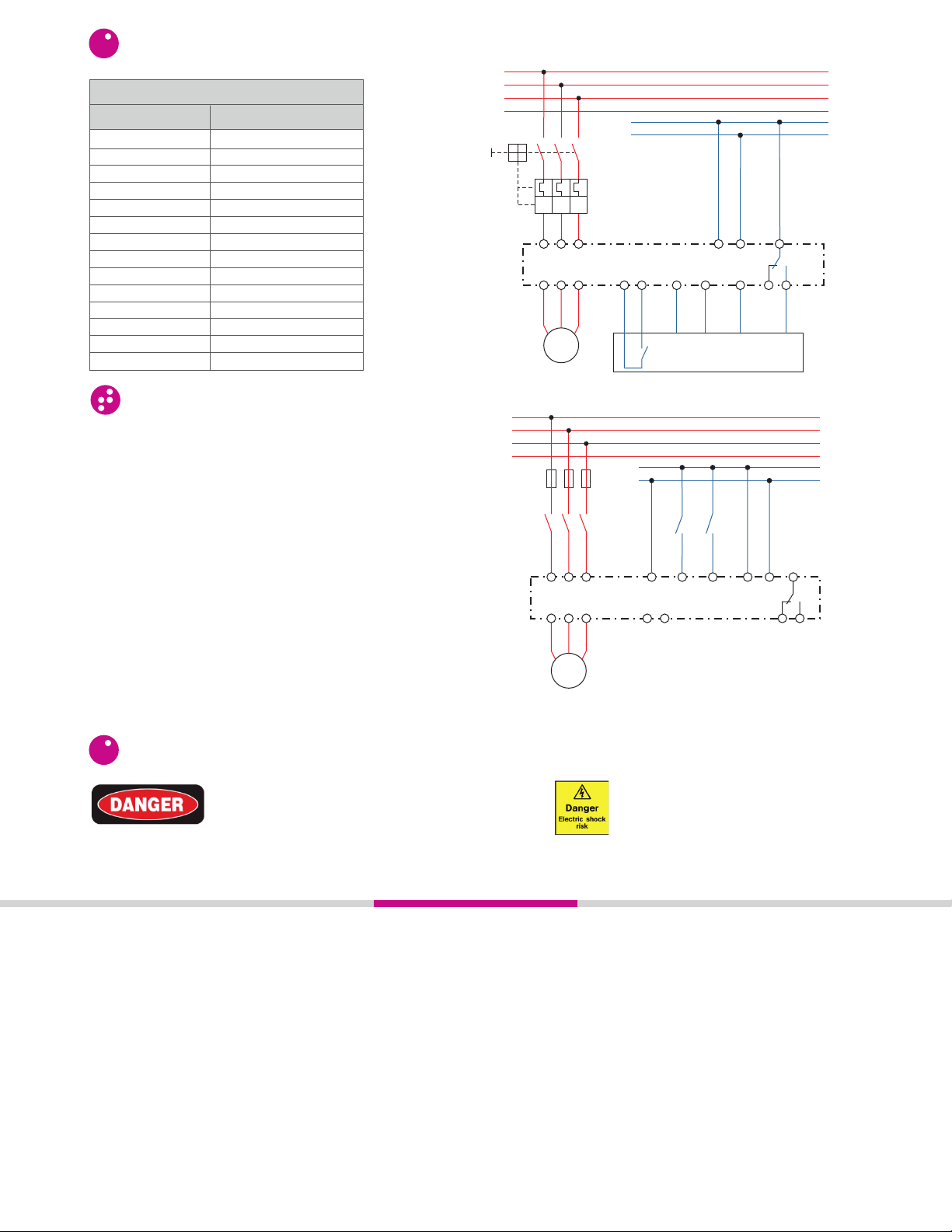
WIRING DIAGRAMS
TABLE 3. Connection Terminals
Terminal Designator
V+
0V
R
L
NE
MAN
RES
11, 12, 14
L1
L2
L3
T1
T2
T3
Description
Auxiliary voltage +
Auxiliary voltage Control input Forward
Control input Reverse
Earth connection control input
Input for remote Reset
Output for remote Reset
Indicator relay for operation
Phase voltage L1
Phase voltage L2
Phase voltage L3
Motor connection T1
Motor connection T2
Motor connection T3
Motor control by PLC
L1
L2
L3
N
24 VDC
Q1
I> I> I>
L1 L2 L3
T1 T2 T3
U
M
3~
RES
V
+
-
MAN
L R
Out
Out
PLC
+
V
0V
NE
11
0V
14
12
Ready
In
ADDITIONAL NOTES
• This device is intended for use on supply systems with a maximum voltage from phase
to ground of 300 V (e.g. for a three phase-four wire system 277/480 V or on a three
phase-three wire systems of 240 V), rated impulse withstand voltage of max. 4 kV.
• Suitable for use on a circuit capable of delivering not more than 5000 rms symmetrical
Amperes, 480 Volts maximum when protected by class CC, J or RK5 fuse rated
maximum 20 A.
• For use in pollution degree 2 Environment or equivalent.
• The control circuits of this device shall be supplied by an isolated 24 VDC power
supply which output is protected with a fuse rated max. 4 Adc.
• For installations according to Canadian National Standard C22.2 No. 14-13 (cUL Mark
only) and supply voltages above 400V:
- For 415 V max. supply voltage, transient surge suppression devices shall be installed
on the line side of this equipment and shall be rated 240 V (phase to ground), 415 V
(phase to phase), suitable for overvoltage category III, and shall provide protection for
a rated impulse withstand voltage peak of 4 kV.
- For 480 V max. supply voltage, transient surge suppression devices shall be installed
on the line side of this equipment and shall be rated 277 V (phase to ground), 480 V
(phase to phase), suitable for overvoltage category III, and shall provide protection for
a rated impulse withstand voltage peak of 4 kV.
• For reliable operation the 24 VDC auxiliary power supply needs to be fully stable
during the entire operation of the device. Removing this voltage while the output is
under load could cause permanent damage to the device.
WARNINGS
RISK OF MATERIAL DAMAGE AND HOT ENCLOSURE
• The product’s side panels may be hot, allow the product to cool before
touching
• Follow proper mounting instructions including torque values
• Do not allow liquids or foreign objects to enter this product
Failure to follow these instructions can result in serious injury, or equipment
damage.
Motor control by switches
L1
L2
L3
N
F1
L1 L2 L3
T1 T2 T3
V
U
M
3~
+
24 VDC
-
RES
Hazard of electric shock, explosion or arc flash
• Disconnect all power before installing or working with this equipment
• Verify all connections and replace all covers before turning on power
Failure to follow these instructions will result in death or serious injury.
Reverse
MAN
LNE
Forward
11
V+
0VR
12 14