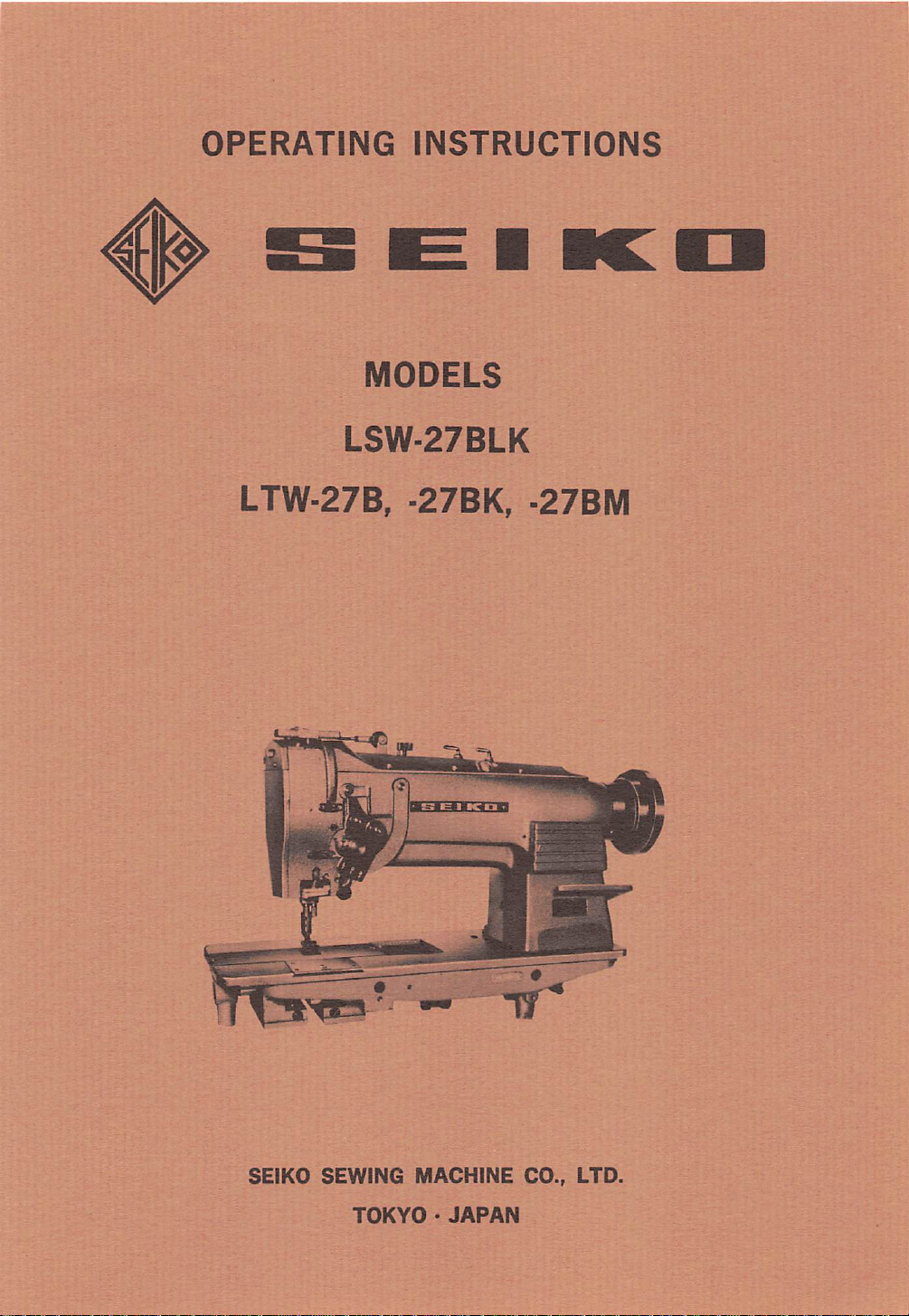
OPERATING
LSW-27BLK
INSTRUCTIONS
MODELS
LTW-27B,
•27BK,
-27BM
SEIKO
SEWING
TOKYO•JAPAN
MACHINE
CO.,
LTD.
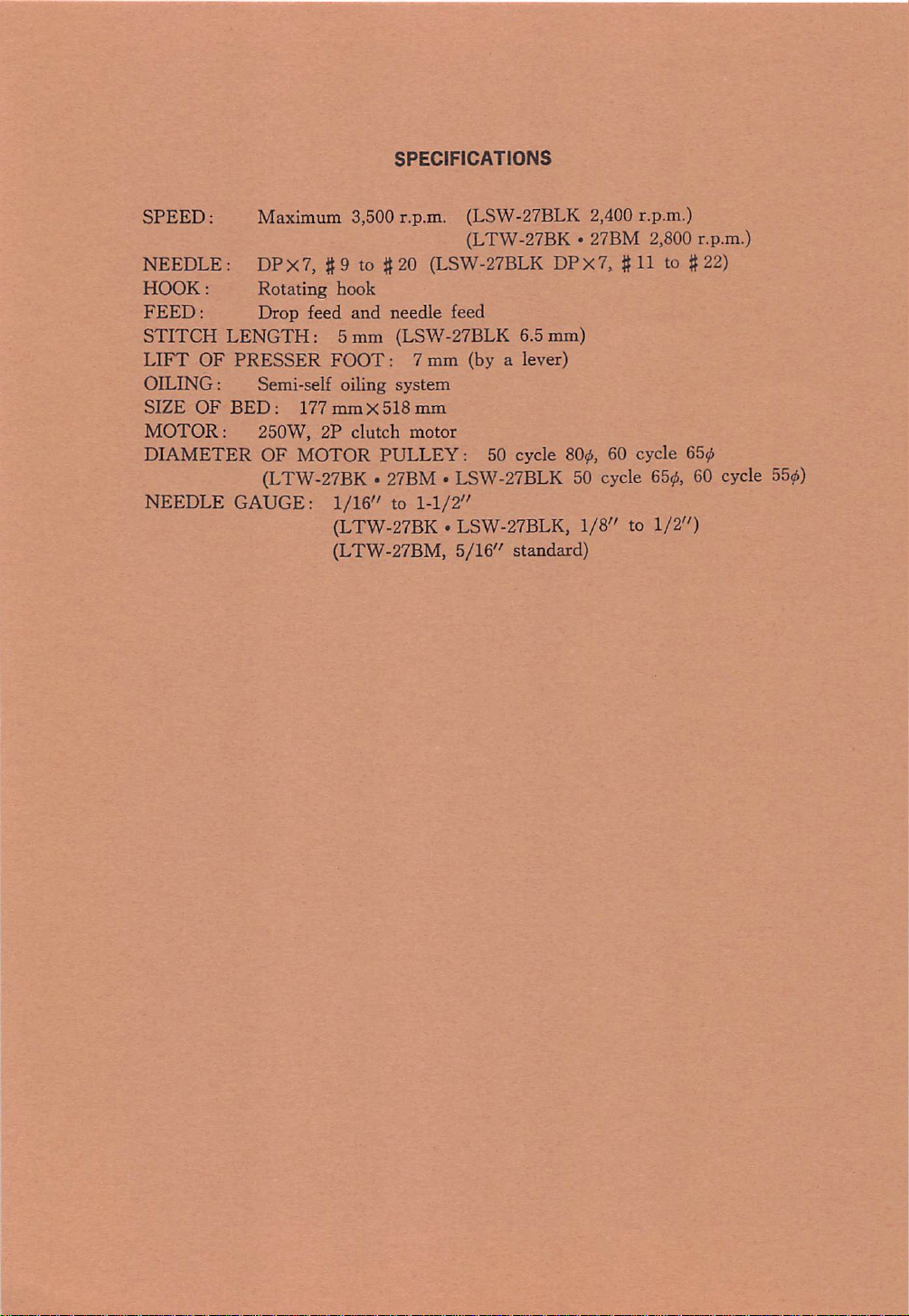
SPECIFICATIONS
SPEED:
Maximum 3,500 r.p.m. (LSW-27BLK 2,400 r.p.m.)
NEEDLE: DPX7,
HOOK:
FEED:
STITCH
LIFT
OILING:
SIZE
MOTOR:
DIAMETER
OF
OF
Rotating hook
Drop
LENGTH:
PRESSER
Semi-self oiling system
BED:
177
250W, 2P clutch motor
OF
MOTOR
(LTW-27BK•27BM•LSW-27BLK50cycle
NEEDLE
GAUGE:
(LTW-27BK . 27BM 2,800 r.p.m.)
#9to#20
feed
and
5mm
FOOT:
mmX518
1/16"
(LSW-27BLK DPX7, #11 to #22)
needle feed
(LSW-27BLK 6.5mm)
7 mm (by a lever)
mm
PULLEY:
to
1-1/2"
50 cycle
(LTW-27BK.LSW-27BLK,
(LTW-27BM,
5/16"
80^6,
standard)
60 cycle
6656,60cycle
1/8" to 1/2")
65,6
55?^)

CONTENTS
Page
Setting up the machine 1
Oiling I
Oil adjuster 2
Needle 2
Thread
Inserting
Winding
Threading
Regulating
and
removing bobbins 3
bobbins
the
the
and
its adjustment 3
machine 4
thread
tension 5
Adjustment of the presser foot pressure 5
Adjusting the stitch length 6
Reverse stitch 6
3
INFORMATION
FOR
ADJUSTMENT
Replacement of the timing belt 6
Adjusting the height of the feed dog 7
Adjusting the timing of the needle plate, needle and feeder 7
Adjusting
Timing
Timing
Adjusting
the
heightofthe
between
adjustment 9
the
the hook
clearance 10
needle
and
bar
needle 9
Relative position between bobbin case and opener 10
Adjusting the height of the presser foot 11
Fine
adjustment of the needle feed 11
Changing the needle gauge 11
SPECIAL
SPECIAL
INSTRUCTIONS
INSTRUCTIONS
FOR
FOR
MODEL
MODEL
LTW-27BK
LTW-27BM
&
LSW-27BLK...12
20
8
LSW-27BLK
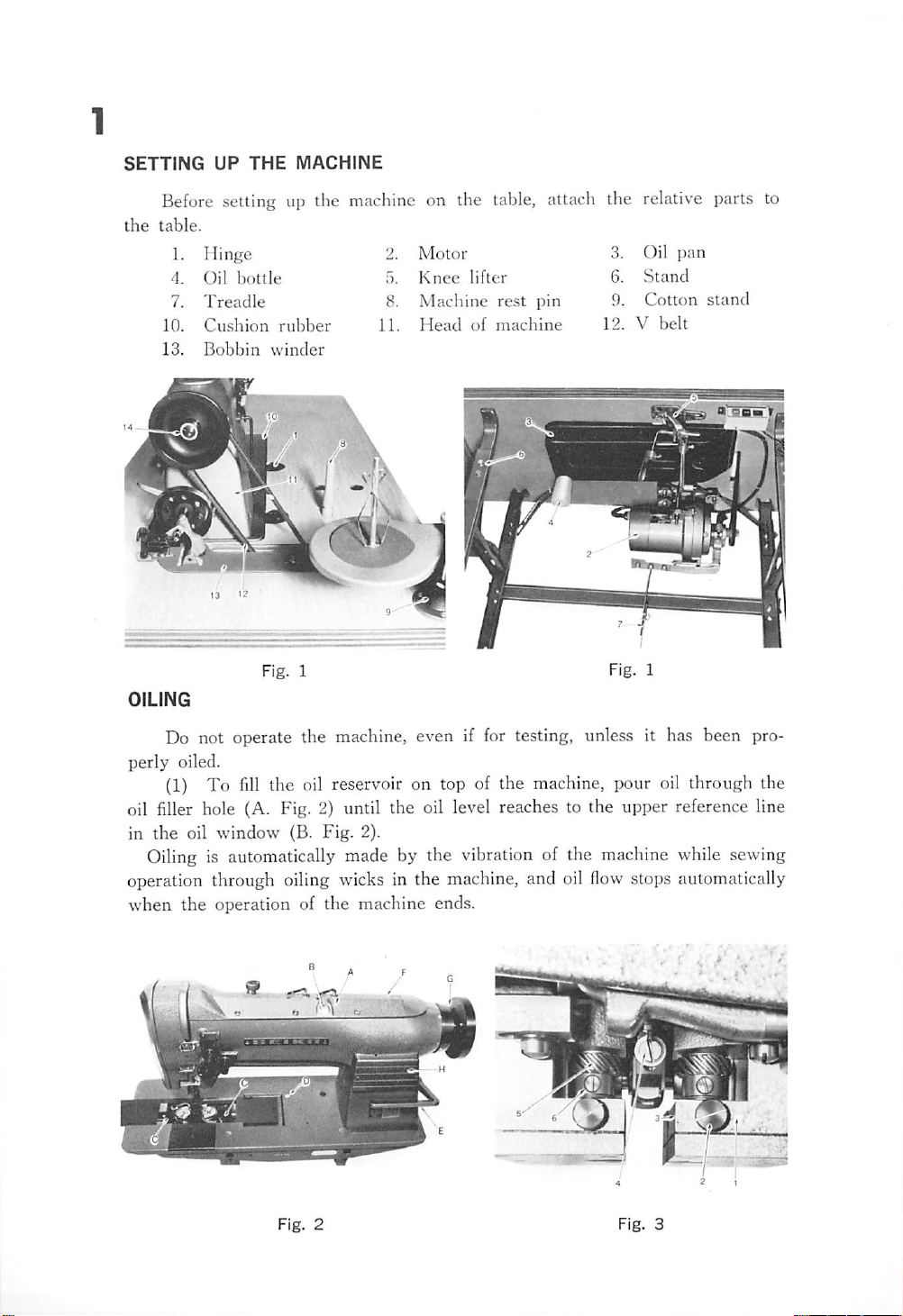
SETTING
UP
THE
MACHINE
Before setting up the machine on the table, attach the relative parts to
the
table.
1. Hinge 2. Motor 3. Oil pan
4.
Oil
7.
10.
13.
OILING
bottle
Treadle
Cushion
Bobbin
rubber
winder
Fig.
1
5.
Knee
lifter
6.
Stand
8. Machine rest pin 9. Cotton stand
11.
Head
of
machine
12. V
Fig.
belt
1
Do not operate the machine, even if for testing, unless it has been pro
perly oiled.
(1)
To
fill
oil
in
the oil reservoir on top of the
filler
hole (A. Fig. 2) until the oil level reaches to the upper reference line
the
oil
window
(B.
Fig.
2).
machine,
pour oil through the
Oiling is automatically made by the vibration of the machine while sewing
operation through oiling wicks in the machine, and oil
when the operation of the machine ends.
Fig.
2
flow
stops automatically
Fig.
3
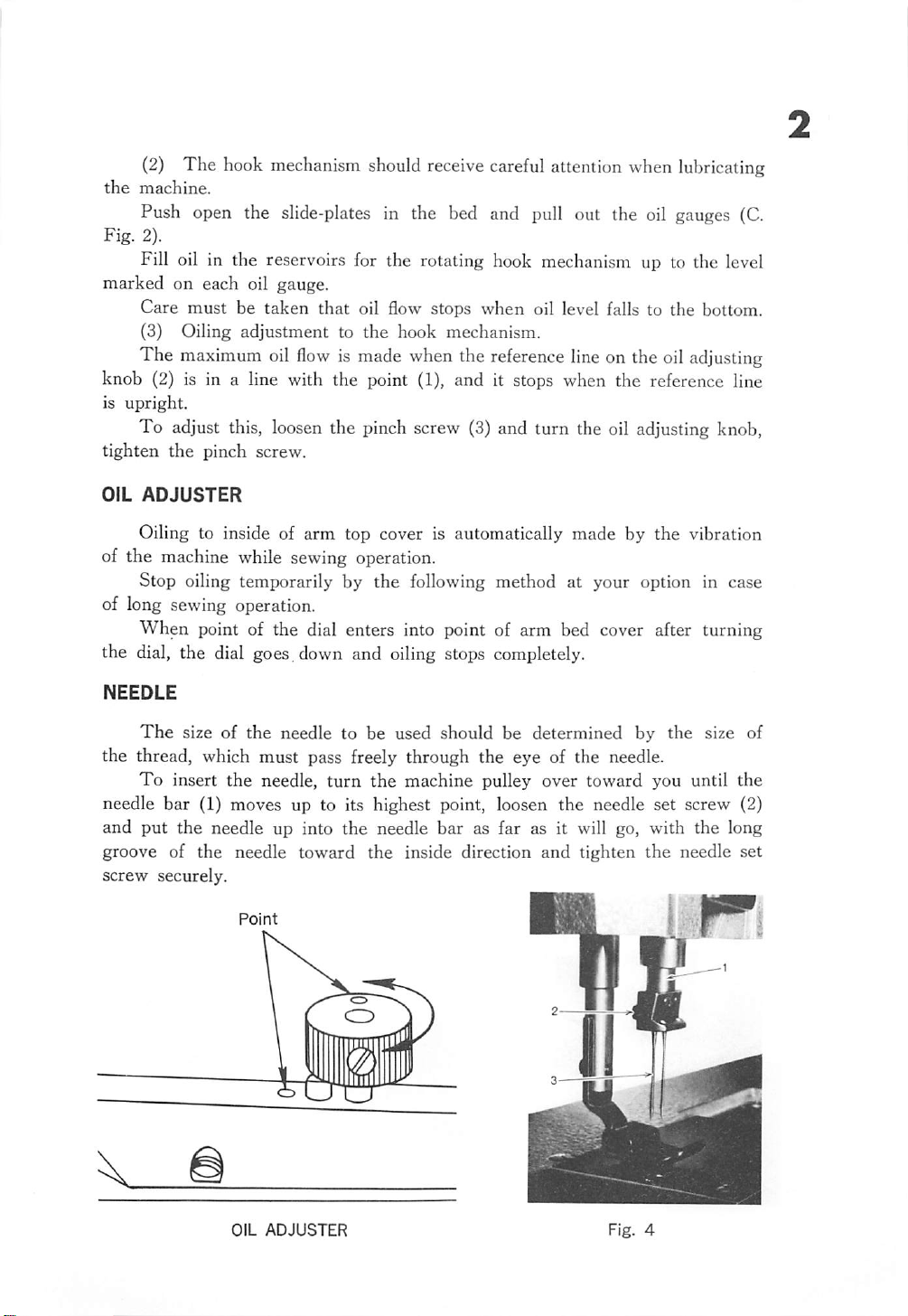
(2)
The
hook
mechanism
the
machine.
Push open the slide-plates in the bed and pull out the oil
Fig.
2).
should
receive
careful
attention whenlubricating
gauges
(C.
Fill oil in the reservoirs for the rotating hook mechanism up to the level
marked on each oil gauge.
Care
must
be
taken
that
oil flow stops
when
oil level falls to
the
bottom.
(3) Oiling adjustment to the hook mechanism.
The maximum oil
flow
is made when the reference line on the oil adjusting
knob (2) is in a line with the point (1), and it stops when the reference line
is
upright.
To adjust this, loosen the pinch screw (3) and turn the oil adjusting knob,
tighten
OIL
the
pinch screw.
ADJUSTER
Oiling to inside of arm top cover is automatically made by the vibration
of the machine while sewing operation.
Stop oiling temporarily by the following method at your option in case
of long sewing operation.
When point of the dial enters into point of arm bed cover after turning
the dial, the dial goes, down and oiling stops completely.
NEEDLE
The
size of the needle to be used should be determined by the size of
the thread, which must pass freely through the eye of the needle.
To
insert the needle,
turn
the
machine pulley over toward you until the
needle bar (1) moves up to its highest point, loosen the needle set screw (2)
and
put
the needle up into the needle bar as far as it will go, with the long
groove of the needle toward the inside direction and tighten the needle set
screw
securely.
OIL
ADJUSTER
Fig.
4
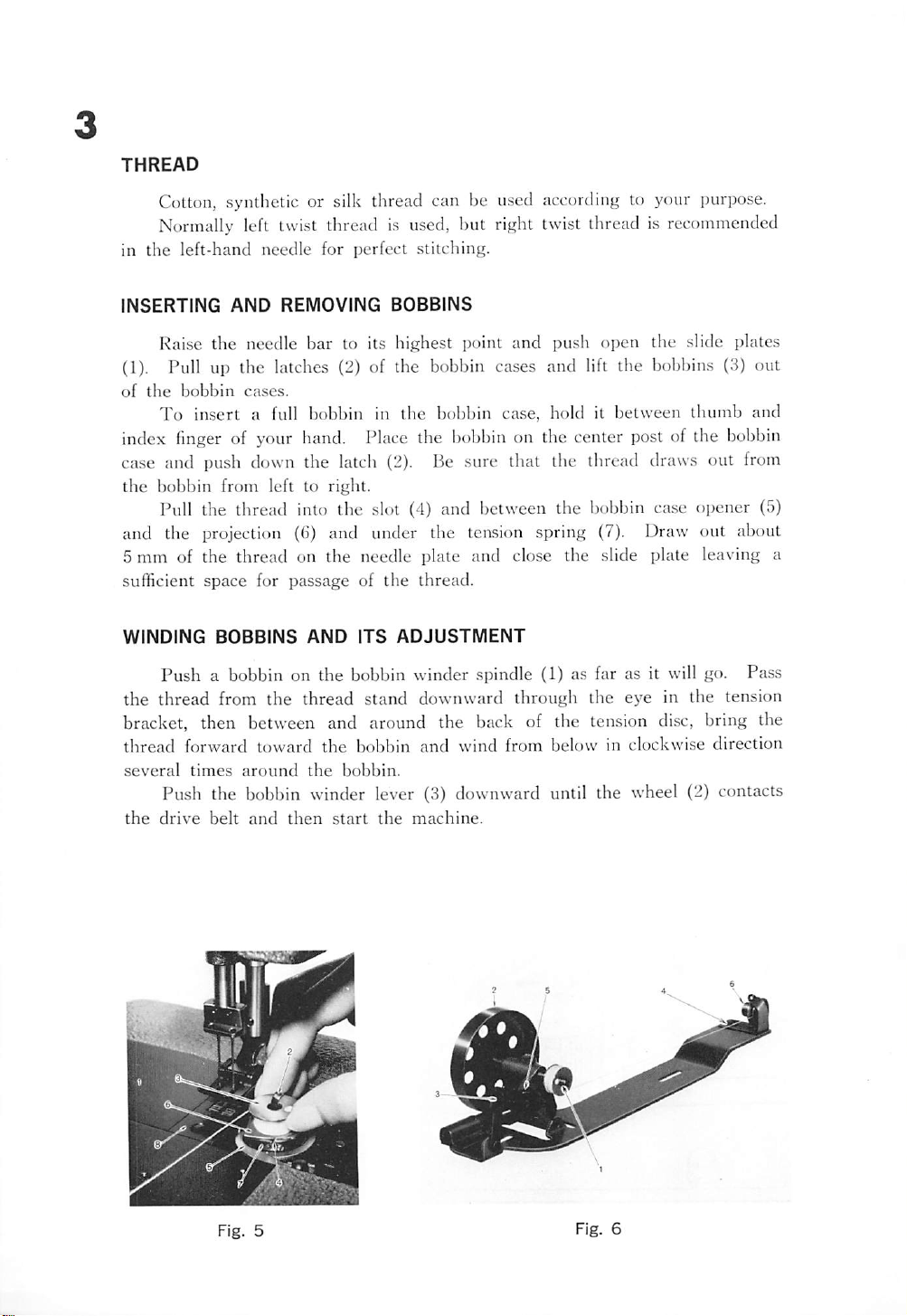
THREAD
CoUon,
synthetic or silk tliread can be used according to your purpose.
Normally left twist thread is used, but right twist thread is recommended
in the left-hand needle for perfect stitching.
INSERTING
Raise the neetlle bar to its highest
AND
REMOVING
BOBBINS
iK)int
and push open the slide plates
(1). Pull up the latches (2) of the bobbin cases and lift the bobbins (3) out
of
the
index
bobbin
To
finger
cases.
insert
a full bobbin in
the
bobbin case, hold it between
thumb
of your hand. Place the bobbin on the center post of the bobbin
and
case and push down the latch (2). Be sure that the thread draws out from
the
bobbin
Pull the thread into the slot (4) and between the bobbin
from left to right.
ca.se
ojjener (5)
and the projection (6) and under the tension spring (7). Draw out about
5 mm of the thread on the needle plate and close the slide plate leaving a
sufficient
WINDING
space
BOBBINS
for passage of
AND
the
ITS
ADJUSTMENT
thread.
Push a bobbin on the bobbin winder spindle (1) as far as it will go. Pass
the thread from the thread stand downward through the eye in the tension
bracket, then between and around the back of the tension
thread
several
forward
times
toward
around
the
the
bobbin
bobbin.
and
wind
from
belowinclockwise
disc,
bring the
direction
Push the bobbin winder lever (3) downward until the wheel (2) contacts
the
drive
belt
and
then
start
the
machine.
Fig.
Fig.
5
6
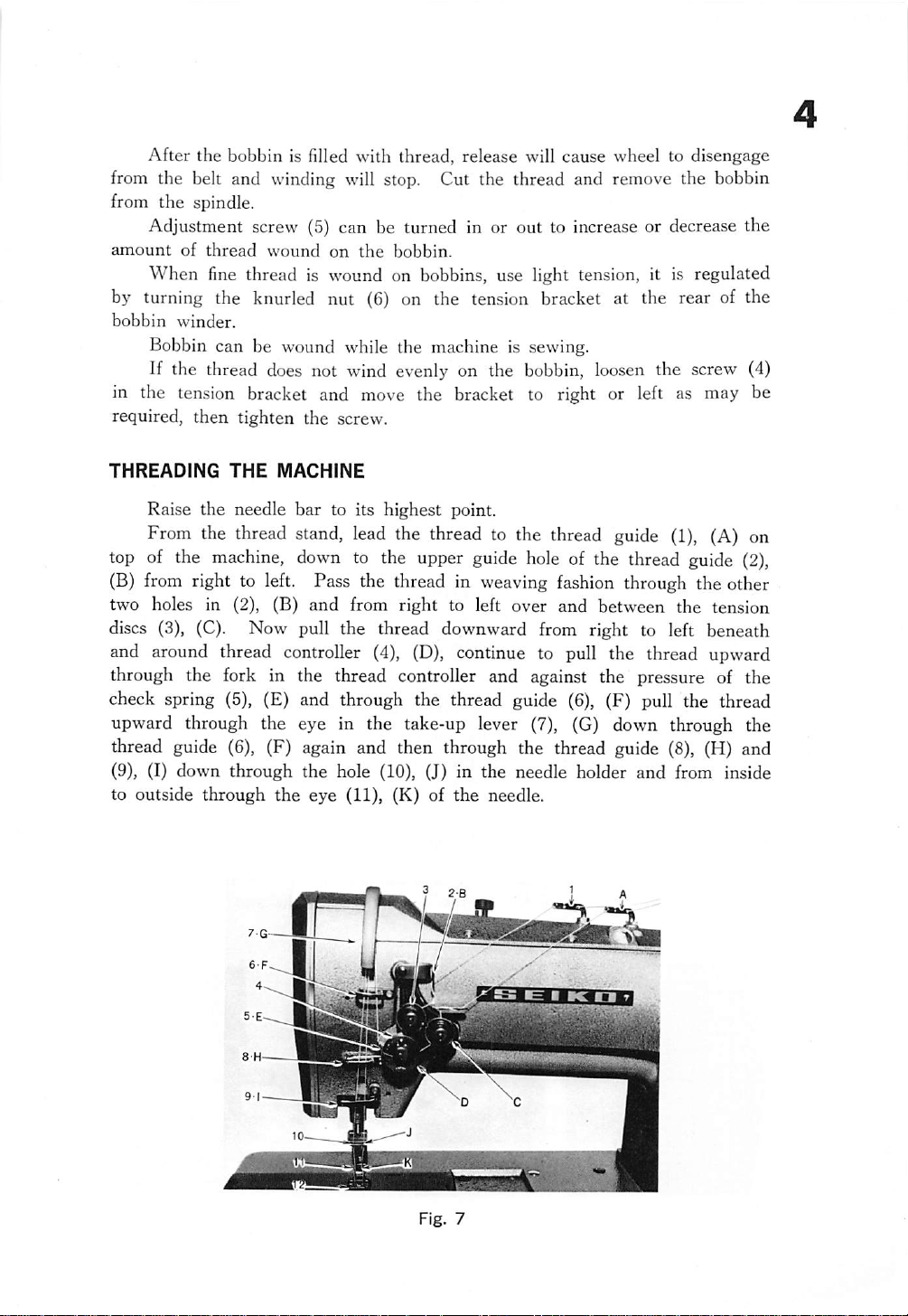
After
the
bobbin
from the belt and winding will stop. Cut the thread and remove the bobbin
from
the
spindle.
is filled
with
thread,
release
will
cause
wheeltodisengage
Adjustment screw (5) can be turned in or out to increase or decrease the
amount
of
thread
wound
on
the
bobbin.
When fine thread is wound on bobbins, use light tension, it is regulated
by turning the knurled nut (6) on the tension bracket at the rear of the
bobbin
winder.
Bobbin can be wound while the machine is sewing.
If the thread does not wind evenly on the bobbin, loosen the screw (4)
in the tension bracket and move the bracket to right or left as may be
required, then tighten the screw.
THREADING
Raise the needle bar to its highest point.
From the thread stand, lead the thread to the thread guide
top of the
(B)
from right to left. Pass the thread in weaving
two holes in (2), (B) and from right to left over and between the tension
THE
machine,
MACHINE
down
to the upper
guide
hole
of the thread
fashion
(1),
(A) on
guide
(2),
through the other
discs (3), (C). Now pull the thread downward from right to left beneath
and around thread controller (4), (D), continue to pull the thread upward
through the fork in the thread controller and against the pressure of the
check spring (5), (E) and through the thread guide (6), (F) pull the thread
upward through the eye in the take-up lever (7), (G) down through the
thread guide (6), (F) again and then through the thread guide (8), (H) and
(9), (I) down through the hole (10), (J) in the needle holder and from inside
to outside through the eye (11), (K) of the needle.
?
28
ltj
Fig.
7
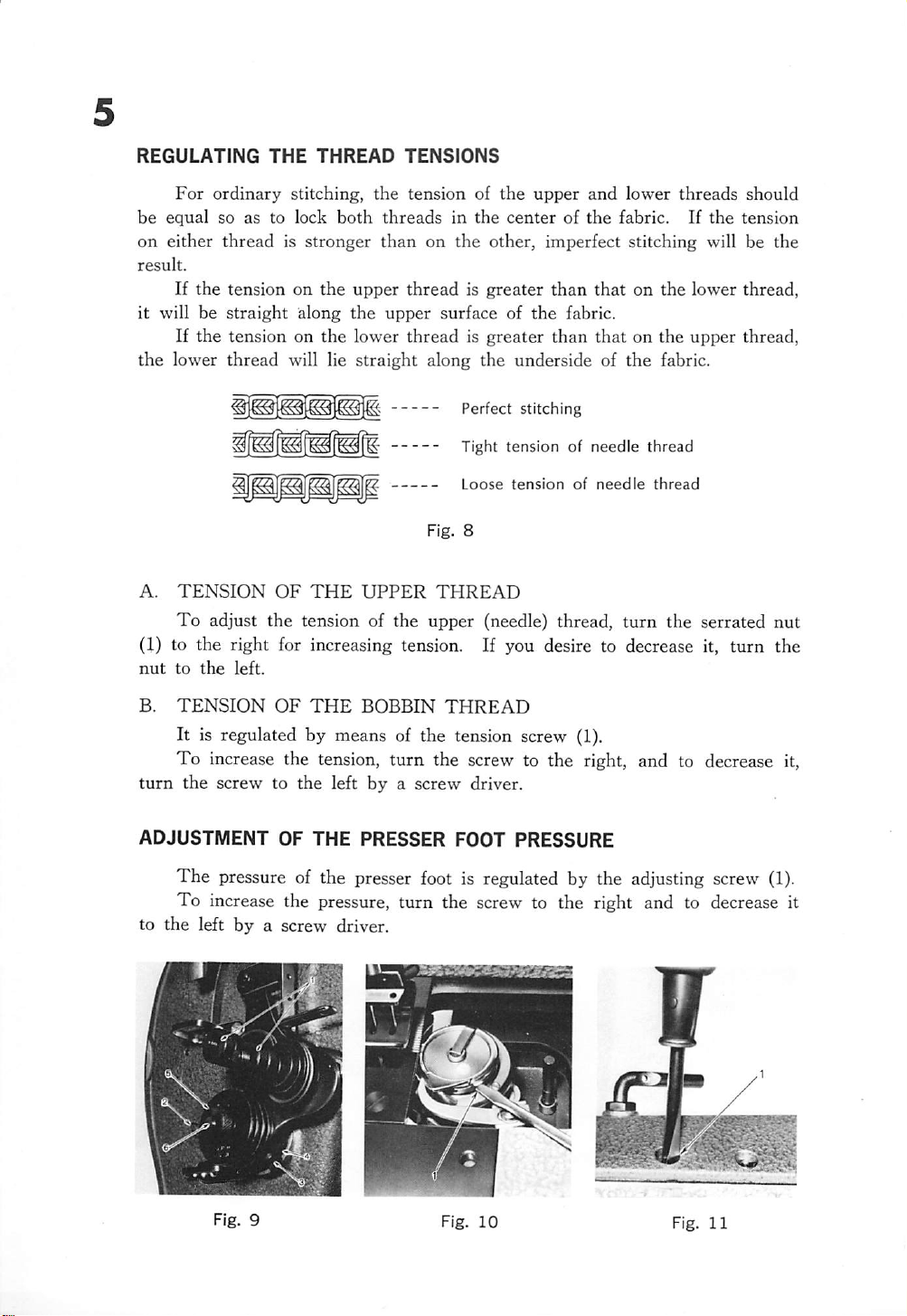
REGULATING
For
ordinary stitching,
be
equal
on either thread is stronger
result.
If the tension on the upper thread is greater than
it
will be straight along
the
If
THE
so as to
tension on
THREAD
lock
the
TENSIONS
the
tension of
both
threads
than
the
upper surface of
lower
threadisgreater
the
upper
and
in
the
centerofthe
on the other, imperfect stitching will be the
that
the
fabric.
than
thatonthe
the lower thread will lie straight along the underside of
Perfect stitching
lower threads should
fabric.
If
the
tension
on the lower thread,
upper thread,
the
fabric.
A.
Tight tension of needle
Loose
tension
Fig. 8
TENSION
To
adjust the tension of the upper (needle) thread, turn the serrated
OF
THE
UPPER
THREAD
of
needle
thread
thread
(1) to the right for increasing tension. If you desire to decrease it,
nut
to
the
left.
B.
TENSION
OF
THE
BOBBIN
THREAD
It is regulated by means of the tension screw (1).
To increase the tension, turn the screw to the right, and to decrease it,
turn
the screw to the left by a screw driver.
ADJUSTMENT
OF
THE
PRESSER
FOOT
PRESSURE
The pressure of the presser foot is regulated by the adjusting screw
To increase the pressure, turn the screw to the right and to decrease it
to
the
left
by
a screw driver.
turn
nut
the
(1).
Fig.
10
Fig.
11
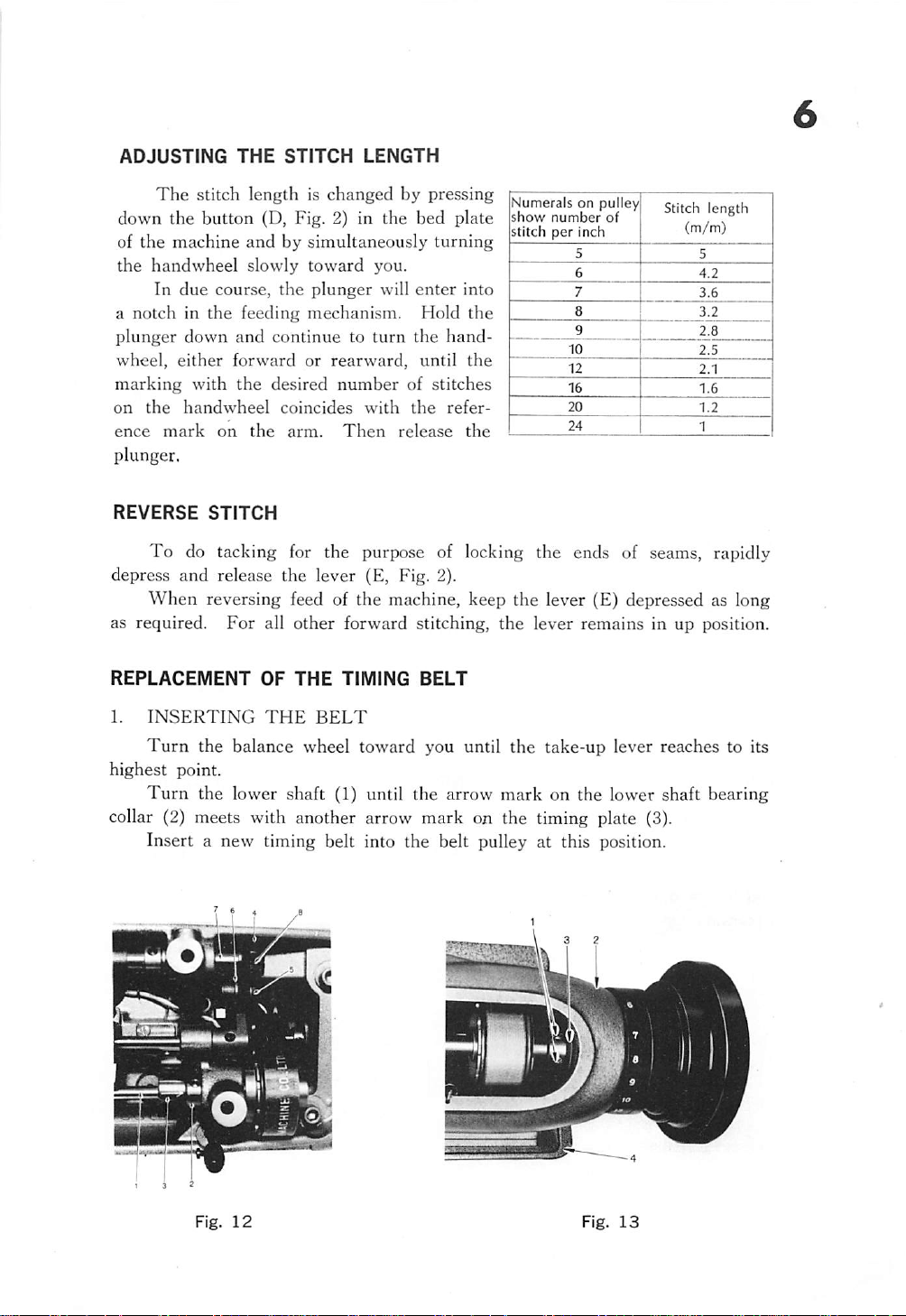
ADJUSTING
The
the
down
of
the
machine
the
handwheel
In
due
a notch in
plunger
wheel,
down
either
marking
on
the
handwheel
ence
mark
plunger.
THE
STITCH
LENGTH
stitch length is changed by pressing
button
the
with
(D, Fig. 2) in the bed plate
andbysimultaneously
slowly
course,
the
toward
plunger
you.
will
feeding mechanism. Hold
and
continuetoturn
forward
the
on
the
or
desired
coincides
arm.
rearward,
number
with
Then
enter
the
until
of
the
release
turning
into
the
hand-
the
stitches
refer
the
Numerals on pulley
show
stitch
number
per
of
inch
Stitch length
(m/m)
REVERSE
To
depress
When
as required.
REPLACEMENT
1.
INSERTING
Turn
highest
Turn
STITCH
do tacking for the purpose of locking the ends of seams, rapidly
and
release the lever (E, Fig. 2).
reversing feed of the machine, keep the lever (E) depressed as long
For
all other forward stitching, the lever remains in up position.
OF
THE
THE
the
balance wheel
TIMING
BELT
toward
BELT
you until
the
take-up
lever reaches to its
point.
the lower shaft (1) until the arrow mark on the lower shaft bearing
collar (2) meets with another arrow mark on the timing plate (3).
Insert a new timing belt into the belt pulley at this position.
I