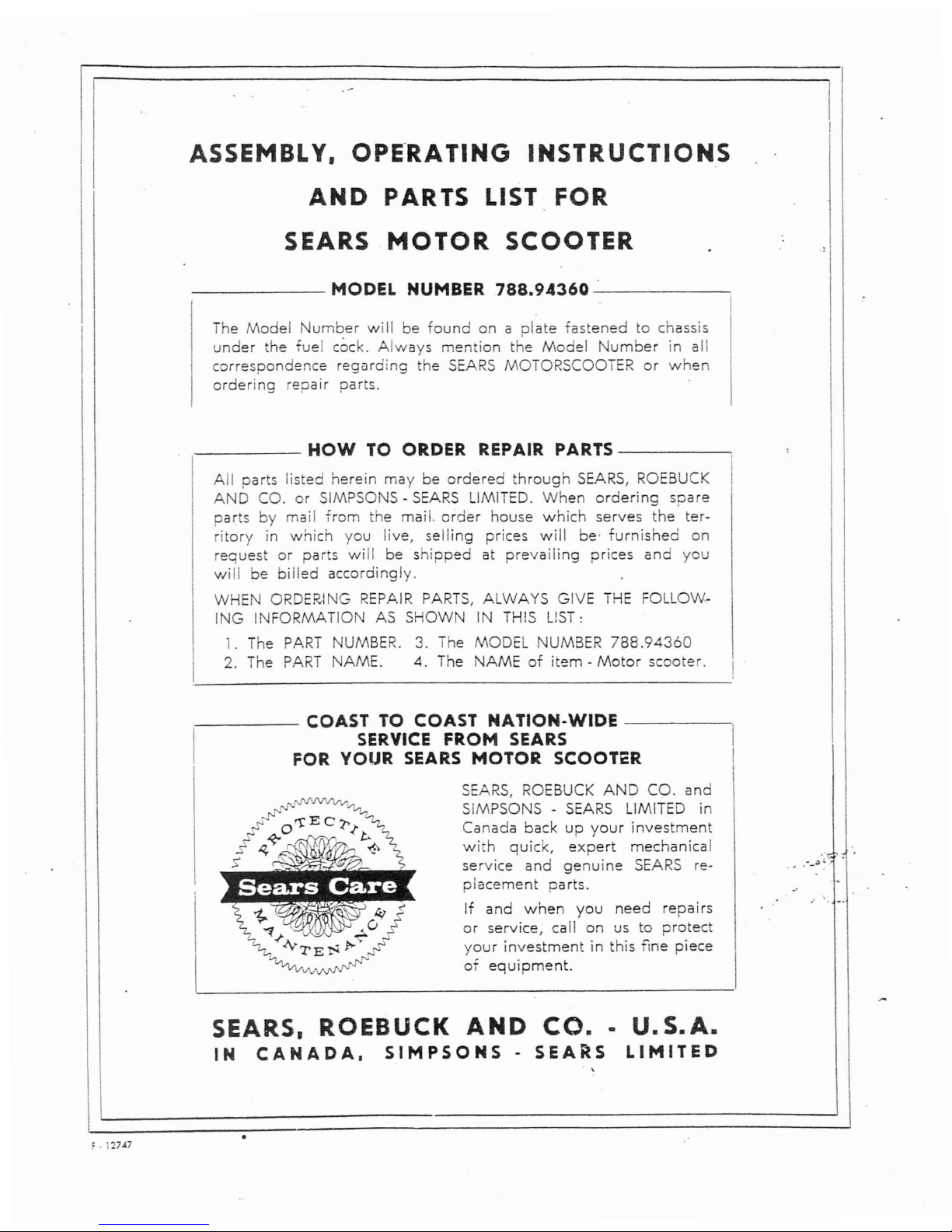
ASSEMBLY.
OPE'RATING
INSTRUCTIONS
AND
PARTS LIST
FOR
SEARS
MOTOR
SCOOTER
------
MODEL NUMBER
788.94360-'----_
The
Model
Number
will
be
found
on a
plate
fastened to chassis
under
the
fuel
cock.
Always
mention
the
Model
Number
in all
correspondence
regurding
the
SEARS
MOTORSCOOTER
or
when
ordering
repair parts.
,----
HOW
TO ORDER REPAIR PARTS
------,
All
parts listed herein may be
ordered
through
SEARS,
ROEBUCK
AND
CO. or SIMPSONS -
SEARS
LIMITED.
When
ordering
spare
parts
by
mail
from
the mail.
order
house
which
serves the ter-
ritory
in
which
you live, selling prices
will
be'
furnished
on
request
or
parts
will
be
shipped
at
prevailing
prices and
you
will
be
billed
accordingly.
WHEN ORDERING
REPAIR
PARTS,
ALWAYS GIVE
THE
FOLLOW-
ING
INFORMATION
AS
SHOWN IN
THIS
LIST:
1. The
PART
NUMBER.
3.
The MODEL NUMBER
788.94360
2. The
PART
NAME. 4. The
NAME
of
item-Motor
scooter.
,.----
COAST TO COAST
NATION-WIDE
-----,
SERVICE
FROM
SEARS
FOR
YOUR
SEARS
MOTOR
SCOOTER
SEARS,
ROEBUCK
AND
CO. and
SIMPSONS
-
SEARS
LIMITED in
Canada back
up
your
investment
with
quick,
expert
mechanical
service and
genuine
SEARS
re-
placement
parts.
If
and
when
you need repairs
or
service,
calion
us
to
protect
your
investment
in this fine piece
of
equipment.
f •
127A7
SEARS.
ROEBUCK
AND
CO
..
U.S.A.
IN
CANADA.
SIMPSONS
-
SEA~S
LIMITED
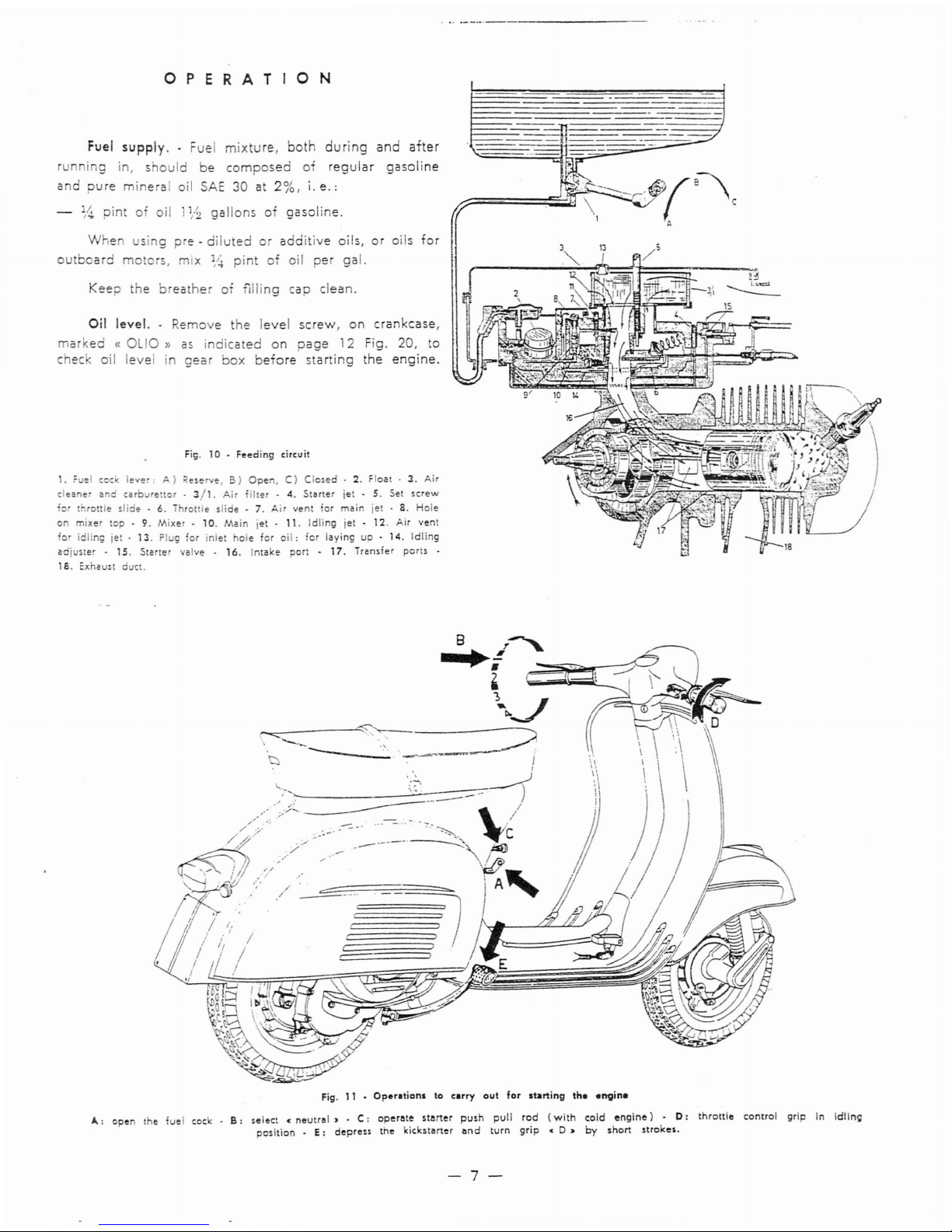
OPERATION
Fuel
supply..Fuel
mixture,
both
during
and
after
r n
ing
in,
should
be
composed
of
regular
gasoline
and
pure
mineral
oil
SAE
30 at
2%,
i.
e.:
%
pintofoil
1
1
,.2
gallonsofgasoline.
When
using
pre·
dilutedoradditive
oils,oroils
for
o
board
mo
ors,
mix
%
pint
of
oil
per
gal.
Keep
the
brea
her
OT
filling
cap clean.
Oil
level.
. Remove the
level
screw,
on
crankcase,
mar.
ed«OLIO»
as
indicated
on
page
12 Fig. 20,
to
chec o'il
levelingear
box
before
starting
the
engine.
Fig.10.
Feeding
circuit
1.
Fu~1
cock
lever:A)<eserve,
B)
Open,C)Closed·2.Float·3.Air
c1eane
and
carburenor.3/1.
Air
'ilter-4.
Stoner
iet - 5. Set
screw
'or
thronle
slide·6.Throltle
slide-7.
Air
ven
for moin iel .8.Hole
on
mixer
top'9.Mixer·
10.
Main
iet -
11.
Idling iet .
12.
Air
vent
for
idling iet .
13.
Plug
ior
inlet
hole
for
oil:
ror
layingup-
14.
Idling
odj Sler -
15.
Stoner
valve -
16.
Intake
port·
17.
Transfer
ports·
1
a.
Exhaust duct.
.....
~-..-
OW
------
.-
3-
-'
-'
.----=-_~!
B
•
Fig. 11 •
Operotionltocarry
out
for
starting
the
."Vin.
A:
open
the
fuel
cock _B:select<neutrol•.C:
ope
rote
storter
push
pull
rod
(with
cold
engine)•D:
throttle
control
grip In
idling
position.E:
depre..the
kickstorter
ond
turn
grip
<
D.
by
short
stroke
•.
-7-
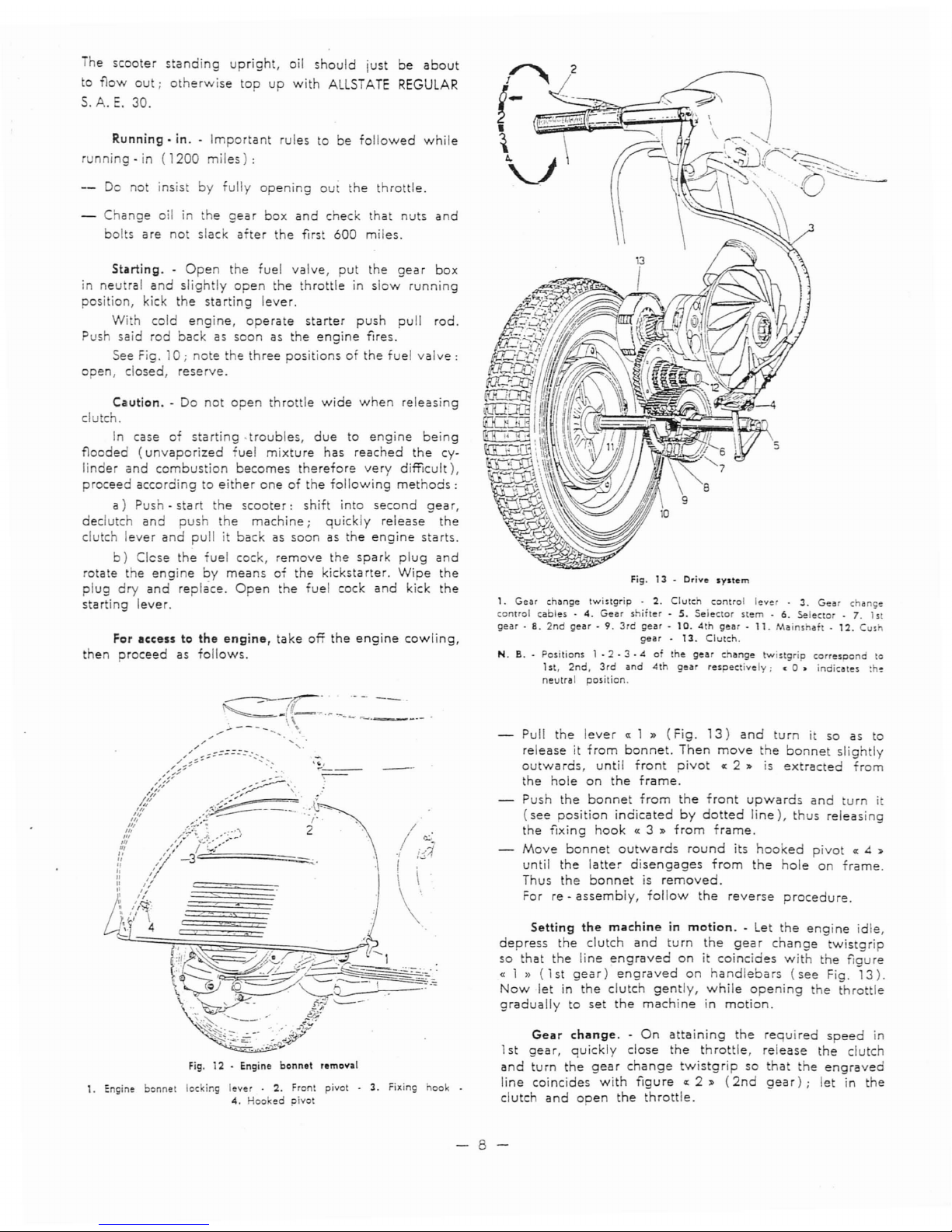
he
scooter
standing
upright,
oil
should
just
be
about
to
flow
out;
otherwise
top
up
with
ALLSTATE
REGULAR
S.A.E.
30.
Running.
in. -
Important
rulestobe
followed
while
running-in
(1200
miles):
Do
not insist
by
fully
opening
out
the
throttle.
Change
oil in
the
gear
box
and
check
that
nuts
and
bolts
are
not
slack
after
the
first
600
miles.
Starting.-Open
the
fuel
valve,
put
the
gear
box
in
neutral
and
slightly
open
the
throttleinslow
running
posi ion, kick
the
starting
lever.
With
cold
engine,
operate
starter
push
pull
rod.
Push
said
rod
backassoonasthe
engine
fires.
See
Fig.
10;
note
the
three
positionsofthe
fuel
valve:
open,
closed,
reserve.
Caution.
- Do
not
open
throttle
wide
when
releasing
clutch.
In
case
of
starting
.troubles,
due
to
engine
being
flooded
(unvaporized
fuel
mixture
has
reached
the
cy-
linder
and
combustion
becomes
therefore
very
difficult),
proceed
accordingtoeither
oneofthe
following
methods:
a)
Push-start
the
scooter:
shift
into
second
gear,
declutch
and
push
the
machine;
quickly
release
the
clutch
lever
and
pullitbackassoonasthe
engine
starts.
b)
Clese
the
'uel
cock,
remove
the
spark
plug
and
rotate
the
engine
by
means
of
the
kickstarter.
Wipe
the
plug
dry
and
replace.
Open
the
fuel
cock
and
kick
the
starting
lever.
For
ac:c:esstothe
engine,
take
ofT
the
engine
cowling,
then
proceed
as
follows.
.~~--
Fig.
12 • Engine
bonnet
removal
1. Engine
bonnet
locking
lever.2.
Front pivot .3.Fixing hook .
4.
Hooked
pivot
Fig.13.
Drive
system
1.
Gear
change
twistgrip.2.
Clutch
control
lever .3.Ge..change
control
cables-4.
Gear
shifter
-S.Selector
stem-6.
Selector.
7. 1st
gear
- 8.
2nd
gear-9.
3rdge..-10.
4th
gear·
11.
Mainshal.12.
Cush
gear-13.
Clutch.
N. B. - Positions
1·2
- 3
.401the
gear
change
twistgrip
corresoond
to
1st.
2nd,
3rd
and
4th
gear
respec
ively;•0»
indicates
,he
neutral
position.
Pull
the
levera:1 »
(Fig.
13)
and
turnitso
as
to
releaseitfrom
bonnet.
Then
move
the
bonnet
slightly
outwards,
until
front
pivota:2"
is
extracted
from
the
hole
on
the
frame.
Push
the
bonnet
from
the
front
upwards
and
turn
it
(see
position
indicated
by
dotted
line),
thus
releasing
the
fixing
hook
« 3 "
from
frame.
Move
bonnet
outwards
round
its
hooked
pivota:4 "
until
the
latter
disengages
from
the
hole
on
frame.
Thus
the
bonnet
is
removed.
For re -
assembly,
follow
the
reverse
procedure.
Setting
the
machineinmotion.
- Let
the
engine
idle,
depress
the
clutch
and
turn
the
gear
change
twistgrip
so
that
the
line
engraved
onicoincides
with
the
fiaure
«
1»
(1st
gear)
engraved
on
handlebars
(see
Fig.
13).
Now
let in
the
clutch
gently,
while
opening
the
throttle
gradually
to
set
the
machine
in
motion.
Gear
change.-On
attaining
the
required
speed
in
1st
gear,
quickly
close
the
throttle,
release
the
clutch
and
turn
the
gear
change
twistgrip
so
that
the
engraved
line
coincides
with
figurea:2"
(2nd
gear);
let in
the
clutch
and
open
the
throttle.
-8-
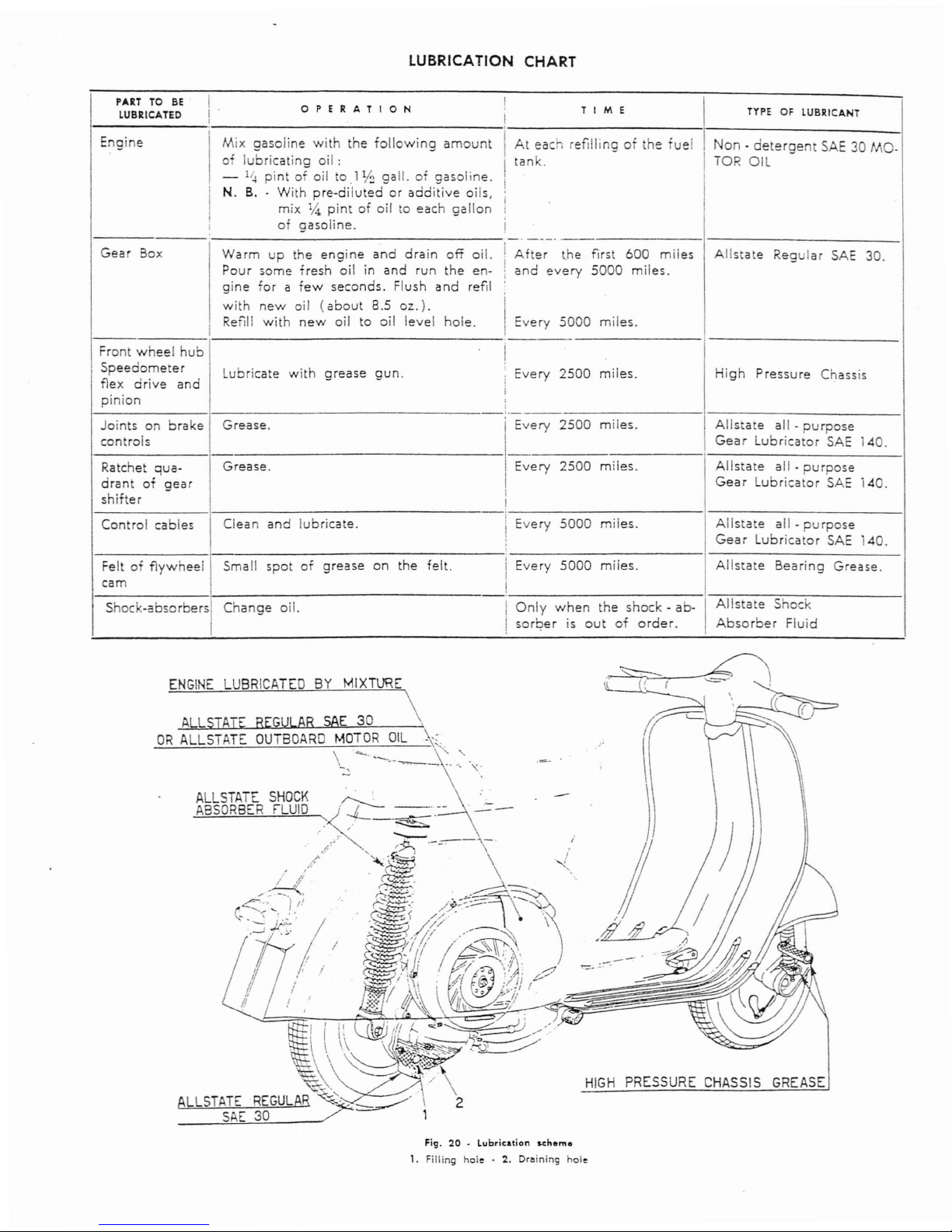
LUBRICATION CHART
PART
TO
BE
.
I
OPERATION
I
I
LUBRICATED
I
I
T I
III
E
TYPEOFLUBRICANT
Engine
Mix
gasoline
with
the
following
amount
i
At
each
refillingofthe
uel
i
Non·
detergent
SAE30MO-
I
I
of
lubricating
oil:
!
tank.
I
TOR OIL
-
l~
pintofoil
to.l
V:!
gall.ofgasoline.
I
N. B
..
With
pre-dilutedoradditive
oils,
I
i
mix %
pintofoil to
each
gallon
;
I
of
gasoline.
I
i
._-_.
Gear
Box
Warm
up
the
engine
and
drain
off
oil.
i
Af
er
the
first
600
miles
Allsta
e
Regular
SAE
30.
Pour
some
fresh
oil
in
and
run
the
en-iand
every
5000
miles.
gine
forafew
seconds.
Flush
and
refil
with
new
oil
(about
8.5
oz.).
i
I
Refill
with
new
oil
to
oil
level
hole.
I
Every
5000
miles.
-
Front
wheel
hub
I
Speedometer
!
Lubricate
with
grease
gun.
Every
2500
miles.
High
Pressure
Chassis
flex
drive
and
i
i
pinion
,
Joints
on
brake
Grease.
Every
2500
miles.
Allstate
all -
purpose
controls
Gear
Lubricator
SAE
140.
Ratchet
qua-
Grease.
Every
2500
miles.
Allstate
all -
purpose
drant
of
gear
Gear
Lubricator
SAE
140.
shifter
i
Control
cables
Clean
and
lubricate.
i
Every
5000
miles.
Allstate
all -
purpose
i
Gear
Lubricator
SAE
40.
Feltofflywheel
Small
spot
of
the
felt.
I
Every
5000
miles.
Allstate
Bearing
Grease.
grease
on
I
I
cam
I
Shock-absorbers
Change
oil.
I
Only
when
the
shock-ab-
Allstate
Shock
!
sorber
is
out
of
order.
Absorber
Fluid
ALLSTATE
SHOCK
ABSORBER
fLUID
ALLSTATE
REGULAR
SAE
30
ENGINE
LUBRICATED
BY
MIXTURE
\
\
1
OR
ALLSTATE
OUTBOARD
MOTOR
OIL-'".
\
--.
'-"--...-~
.~..~.
\;.
~
'L
f (
;;
I
\
;
~"
HIGH
PRESSURE
CHASSIS
GREASE
Fig_20. Lubrication scheme
1.
Filling
hole.2.
Dr.ining
hole
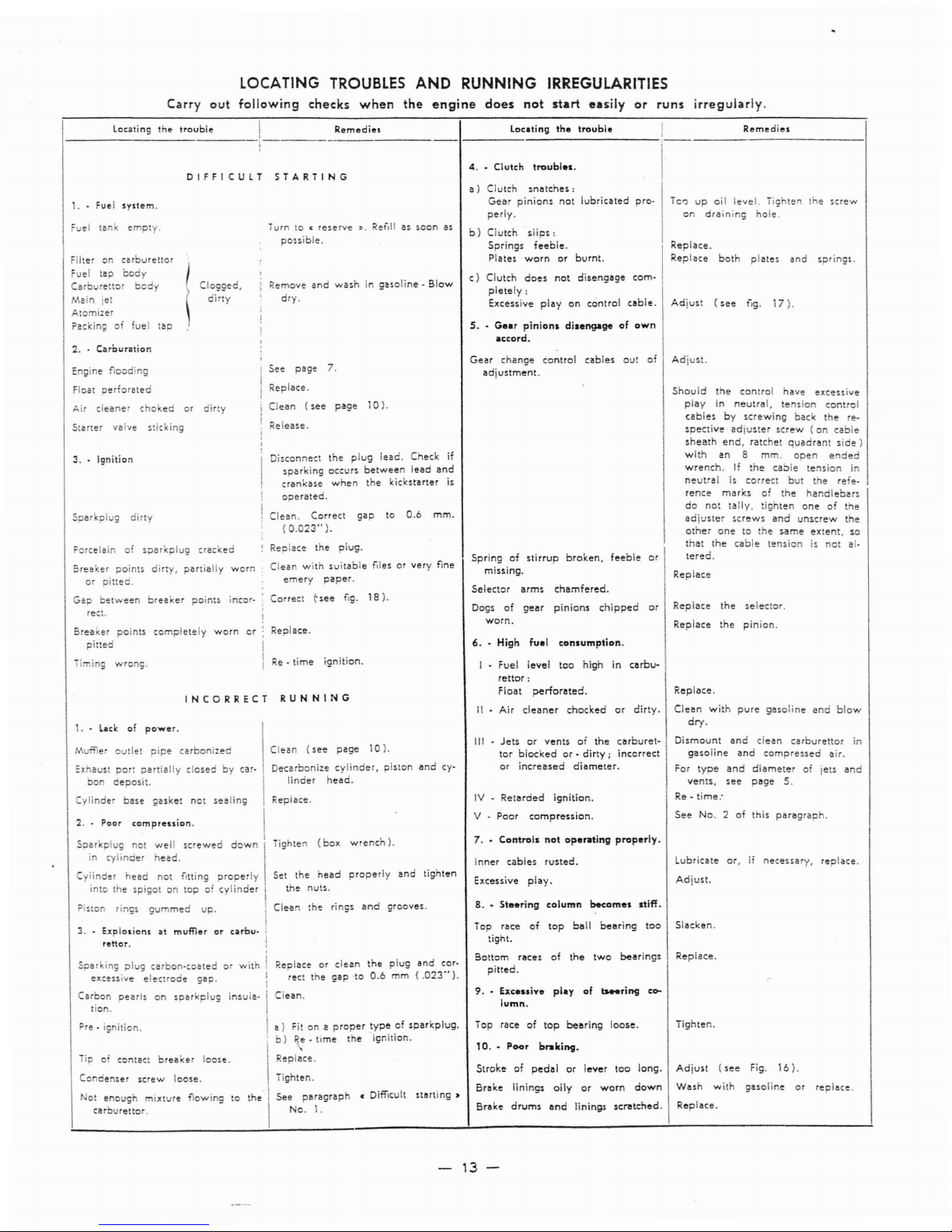
LoeA
T1NG
TROUBLES
AND
RUNNING IRREGULARITIES
Carry
out
following
checks
when
the
engine
does
not
start
easily
or
runs
irregularly.
Locati ng
the
trouble
I
R.emedies
Loc.ting
the
trouble!
Remedies
1---------.----
1
-------.---------1--------------:---------------1
4.•Clulch
trouble
•.
DIFFICULT
STARTING
INCORRECT
RUNNING
1. -
Lockofpower.
Tur toc:reserve
:l.
Refill as
~oon
as
po,sible.
I
See
page
7.
i
Replace.
replace.
iighten.
Adjust
(see
Fig.
16).
Wash
with
gasoline
or
Replace.
Replace.
Clean
with
pure
gasoline
and
blow
dry.
Replace
the
seleclor.
Replace
the
pinion.
Replace.
See
No.2of
this
paragraph.
Adjust.
Dismount
and
clean
carburettor
in
gasoline
and
compressed
air.
For
type
and
diameter
of
jets
and
vents,
see
page
5.
Re-time:
Lubricate
or,ifnecessary.
replace.
Slacken.
Should
the
control
have
excessive
play
in
neutral,
tension
control
cablesbyscrewing
back
the
re-
spective
adjuster
screw
(on
cable
sheath
end,
ratchet
quadrant
side)
with
an
8
mm.
open
ended
wrench.tfthe
cable
tension
in
neutraliscorrect
but
the
re'e·
rence
marks
of
the
handlebars
do
not
tally,
tighten
oneofthe
adjuster
,crew,
and
unscrew
the
ocher
onetothe
same
extent,
so
that
the
cable
tensionisnot
ai-
lered.
Replace
Adjust.
Replace.
Replace
both
plates
and
spring'.
Adjust
(see
f,g.
17).
Te')upoil
level.
Tighten
the
screw
on
draining
hole.
6.
High
fuel
consumption.
I
Fuel
level
too
highincarburettor:
Float
perforated.
II
Air
cleaner
chocked
or
dirty.
Inner
cables
rusted.
Excessive
play.
8
.•
Steering
column
become••tiff.
Top
raceoftop
bearing
loose.
III -
Jetsorventsofthe
carburet-
tor
blockedor-
dirty;
incorrect
or
increased
diameter.
7.•Control.
not
operating
properly,
9
.•
Exce
..inployof_ring
c0-
lumn.
Springofstirrup
broken,
feeble
or
missing.
Selector
arms
chamfered.
Dogsofgear
pinions
chipped
or
worn.
IV
-
Retarded
ignition.
V -
Poor
compression.
Gear
chanoe
control
cables
out
of
adjustm;nt.
10
.•
Poor
braking.
Strokeofpedalorlever
too
long.
Brake
linings
oilyorworn
down
Brake
drums
and
lininit'
SCrlltcned.
Top
raceoflop
ball
bearing
too
light.
Bottom
racesofthe
two
bearings
pitted.
5.
-
Gear
pinion.
di.engageofown
.ccord.
a)
Clutch
snotches:
Gear
pinions
not
lubricated
pro·
perly.
b)
Clutch
slips:
Springs
feeble.
Plates
wornorburnt.
c}
Clutch
does
not
disengage
com-
pletely:
Excessive
playoncontrol
cable.
mm.
gap
to
0.6
Replace.
Tighten.
See
paragraph
• Difficult
starting»
No.1.
Replaceorclean
the
plug
and
cor·
rect
the
gap
to
0.6mm(.023'·).
Clean.
a)
Fitona
proper
typeofsparkplug.
b)Re-
time
the
ignition.
Clean
the
ring,
and
grooves.
Tighten
(box
wrench).
Set
the
head
properly
and
tighten
the
nuts.
Replace.
Clean
(see
page
10).
Decarbonize
cylinder,
piston
and
cy-
linder
head.
Clean.
Correct
(0.023"
).
:
Replace
the
plug.
Clean
with
suitable
flies
or
very
fine
emery
paper.
Correct
(-see fig.
18).
!
:
Replace.
I
I
Re-time
ignition.
,
,
Remove
and
washingasoline-Blow
dry.
Clean
(see
page
10).
i
Release.
i
!
I
Disconnect
the
plug
lead.
Check
if
I
sparking
occurs
between
lead
and
crankase
when
the
kickstarter
is
!
operated.
!
Clogged,
dirty
Cylinder
ba,e
gasket
not
sealing
2.
Poor
compression.
I
Soarkplug
not
well
screwed
down
\
in
cylinder
head.
Cylinder
head
not
fitting
properly
into
the
spigotontop0'cylinder
I
Piston
rings
gu
med
up.
I
3.•Explosionsatmufflerorcarburettor.
!
Sparking
plug
carbon-coatedorwith
i
excessive
electrode
gap.
I
Carbon
pearl,onsparkplug
insula-,'
tion.
Pre -
ignition.
i
iip
of
contact
breaker
loose.
Condenser
screw
loose.
Not
enoug'
mixture
flowing
to
carburettor.
Muffler
outlet
pipe
carbonized
:xhaust
pOr!
partially
closedbycar·
bo
oeposit.
Breaker
points
completely
worn
or
pitted
3..Ignition
Timing
wrong.
Porcelain0sparkplug
cracked
Breaker
points
dirty,
partially
worn
or
pitted.
Gap
between
breaker
points
incor·
rect.
Engine
flooding
Float
perforated
Air
cleaner
choedor
dirty
Starter
vaIve
'tick
ing
Sparkplug
dirty
Filteroncarburettor
Fuel
tap
body
Carboetor
bedy
Main
jet
Atomizer
Packingoffuel
tap
2.-Carcuntion
1. Fuel
system.
~
ueItan
empty.
-
13-
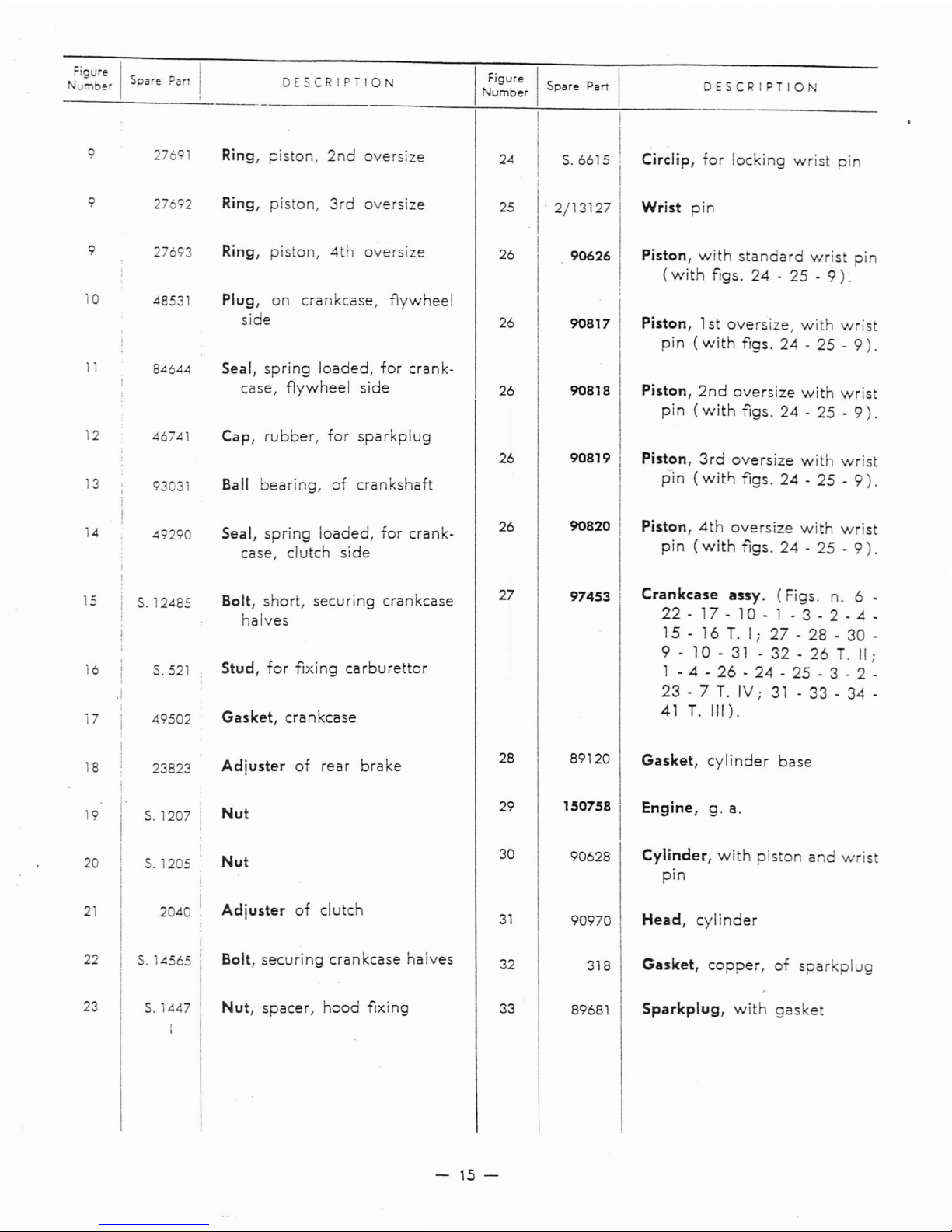
Figure I
umbe
Spare
Par
DESCRIPTIO
I
~~~~:r
I
Spare
Part
DESCRIPTION
9 2769
Ring,
piston,
2nd
oversize
I
24
I
S.6615
!
Circlip,
for
locking
wrist
pin
90626
9
9
10
27692
27693
48531
Ring,
piston,
3rd
oversize
Ring,
piston,
4th
oversize
Plug,
on
crankcase,
f1ywheel
side
25
26
26
I
I'
2/13127
I
I
I
90817
Wrist
pin
Piston,
with
standard
wrist
pin
(with
figs.
24-25-9).
Piston,1st
oversize,
with
wrist
pin
(with
figs.
24-25
-
9).
11
84644 Seal,
spring
loaded,
for
crank-
case,
f1ywheel
side
26
90818
Piston,
2nd
oversize
with
wrist
pin
(with
figs.
24-25
-
9).
12
46741
Cap,
rubber,
for
sparkplug
3
93031
Ball
bearing,
of
crankshaft
26
90819
Piston,
3rd
oversize
with
wrist
pin
(witf:
figs.
24-25
-
9).
14
49290
Seal,
spring
loaded,
for
crank-
case,
clutch
side
26
90820
Piston,
4th
oversize
with
wrist
pin
(with
figs.
24-25
-
9).
15
16
17
S.
12485
S.521
49502
Bolt,
short,
securing
crankcase
halves
Stud,
for
fixing
carburettor
Gasket,
crankcase
27
97453
.
Crankcase
assy.
(Figs.
n. 6 .
22
- 17 - 10 - 1 - 3 - 2 - 4 -
15 - 16T.Ii
27
- 28 - 30 -
9
-
10-31
- 32 - 26T.II
i
1 - 4 -
26
-
24.25
- 3 - 2 .
23
- 7T.IVi31
- 33 - 34 -
41
T.
III).
2040
23823
S,1205
I
S.
4565 I
Head,
cylinder
Cylinder,
with
piston
and
wris
pin
Engine,
g.
a.
Gasket,
copper,
of
sparkplug
Gasket,
cylinder
base
318
90970
89120
1507581
90628
32
30
31
28
29
Nut
Bolt,
securing
crankcase
halves
Adjuster
of
clutch
Nut
Adjuster
of
rear
brake
I
I'
S.1207
I
I
I
I
19
18
20
2
22
23
S.1447
Nut,
spacer,
hood
fixing
33
89681
Sparkplug,
with
gaske
-
15-