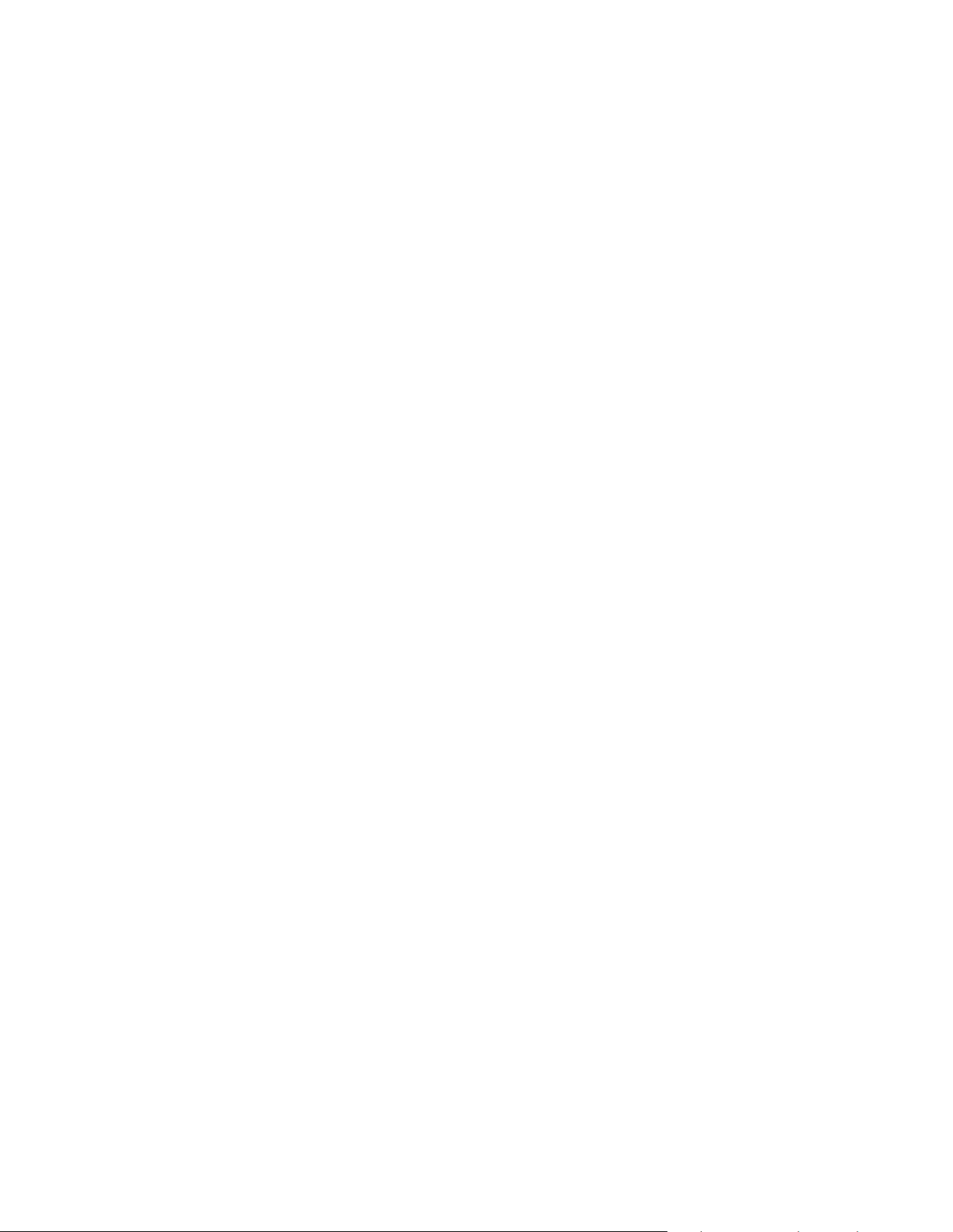
c(SJ
SACHS
-
Repair Instructions No. 4075.8 E
$ACHS
Type
Snowmobile
SA340
Engine
.
340
370
SS
(super
sport)
~
Edition
FICHTEL&SACHS
December
1969
AG · 8720
SCHWEINFURT
.
·~·
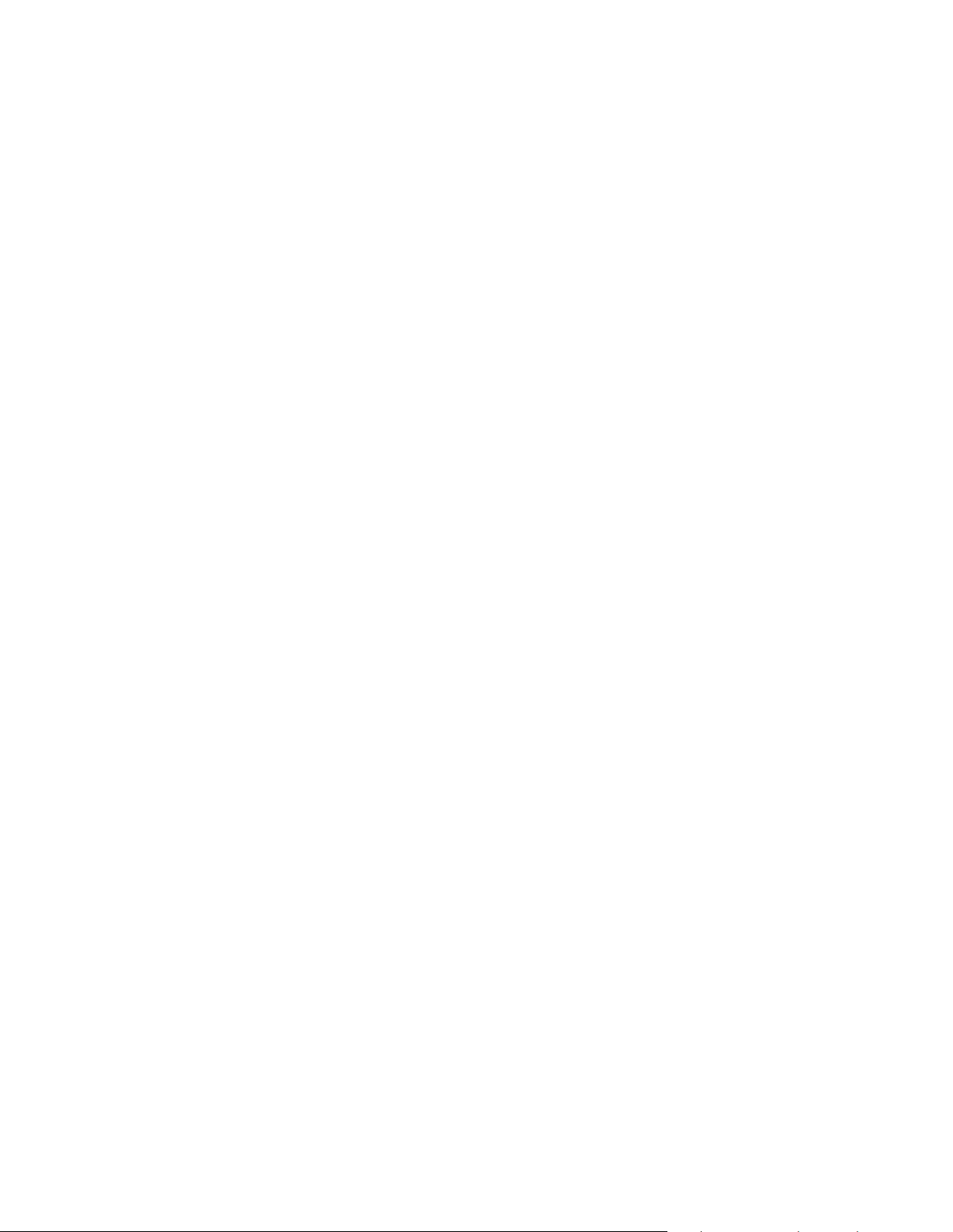
CONTENTS
Preface
Installation
{with
Installation
(with
Installation
Technical
Repair
Taking
Work
Asse
Test
Engine
Engine
Instructions
Instructions
Instructions
BOSCH solenoid
Instructions
BOSCH
In
structions and
BOSCH iner
Laying-up
Lubrication
Tightening
Repair
Engine
. . . . . . . . . . . . . . . . . . . . . .
dimensions
solenoid-controlled
dimensions
inertia-pinion
dimensions
data
tools
and
down
the
on
individual
SACHS
(without
spe
dismantling
Changing
Recoil
star
Flywheel
Replacing
Carburettor
Decarbonizing
mbling
the
-runn
ing
and
with
BOSCH
with
BOSCH
Operation,
Starter
faults
and
and
and
and wiring
solenoid-controlled
tia-pinion
the engine ..
and
torques
dimensions
fault
s .
for
for
type
for
assembly
SACHS
starter)
SACHS
starter)
SACHS
jig
SA 340
..
.
SA 340
SA 370
and
...
and
engine
parts
. . .
cial
extracting
crankshaft
ter
..
dynamo
the
magneto
magneto
the
bearings
.
..
housing
tool for
crankshaft
engine)
..
. . .
..
centering tool
or
. 0 •
..
the
. . . . 0 • • 0 • • • • • • • • •
the
exhaust
engine
. . . . . .
running-in
solenoid-controlled
inertia-pinion
maintenance
o o o o o
wiring
d i
agram
wiring
diagram
wiring
diagram
-controlled
diagram
wirin g d i
agram for
type
maintenance chart
for
bolts and
..
.
...
muffler,
the
engine
type
and
lubrication
••••
for
dynamo
for
dynamo
for
dynamo
starter (Type
for
dynamo
starter
(Type DD) . . . . . . . . . .
dynamo
starter
(Type DG)
o
••
••
nuts
. . . .
cylinder
..
. o •
...
starter
starter
o
•••
magneto
magneto 12 V 75 W .
magneto
DD) . . .
magneto
magneto
.
SA
340 SS
..
..
SA
340 SS
oil
.
flywheel
and
•••••
. . . . .
(Type DD)
(Type DG)
of
electric starters
o • •
12
12 V
12 V 75
12 V 75
.
seals
cylinder head
••
• •
V 40 W .
40
Wand
......
Wand
Wand
Folding
Folding
Folding
Foldi
.
ng
Page
2
sheet
sheet
sheet
sheet
4
6
9
9
11
13
16
18
19
22
23
28
29
30
31
33
34
35
36
37
38
39
40
41
42
44
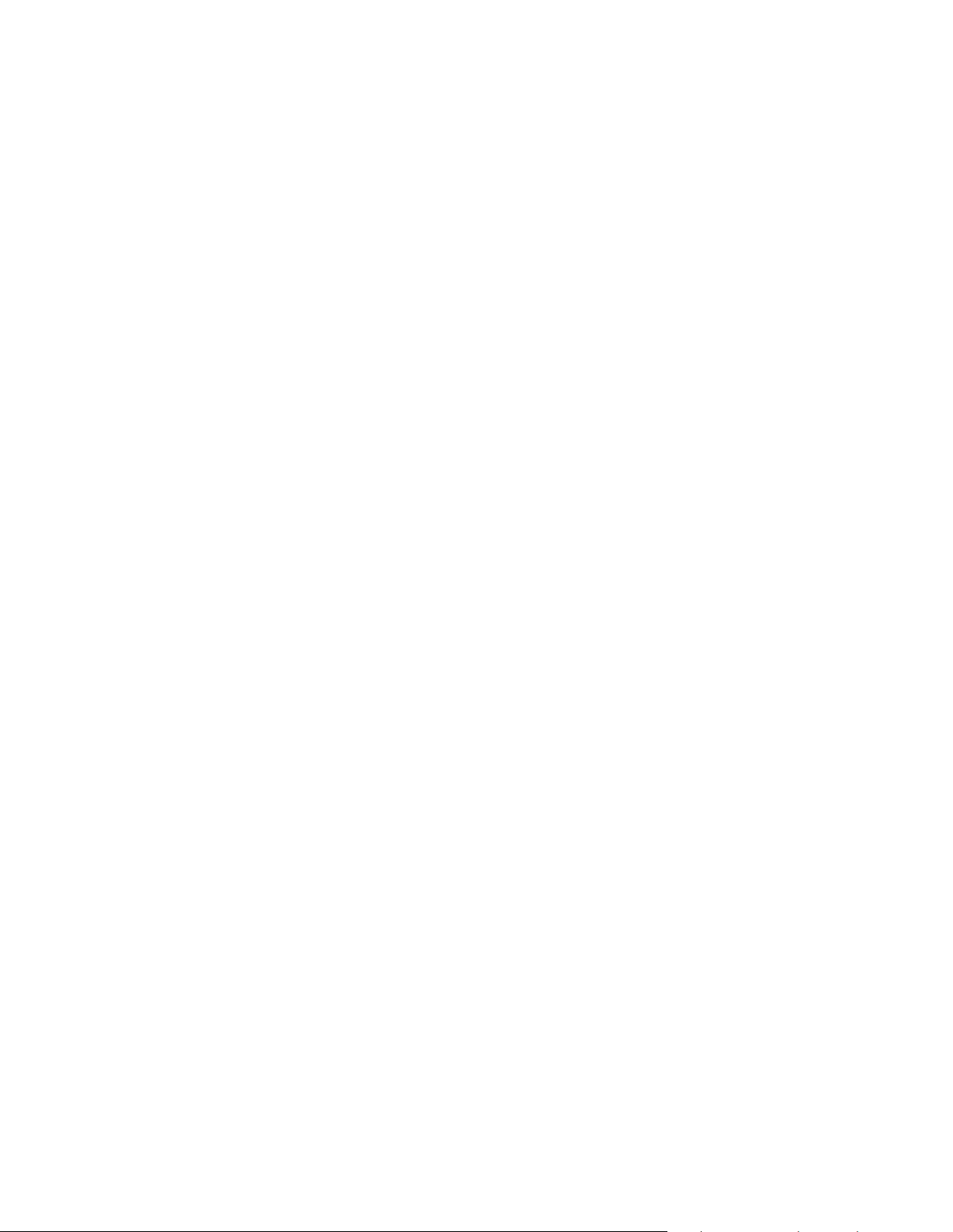
PREFACE
This
manual
guidance
an
efficient
intended
training
school.
It
workshop
details
found
Of
service
workshop,
.
Dealers
circulars
available
It
for
available
will
be
of
helpful when
course,
to
are
is
emphasized
u,se
in
is
designed
and
information
repair
as
and
a substitute
to
found
useful
practice.
the
various
good
maintenance
customers
and
trained
requested
containing
to
every
that
the
workshops
to
necessary
maintenance
for
personnel
as a ready
Our
illustrated
units
and
used
in
call
for
personnel.
to
make
technical
individual
all
information
give
dealers
to
service,
the
practical
at
our
customer
reference
Spare
their
construction
conjunction
and
repair
good
equipment,
this
manual
information
responsible
of
and
not
and
enable
Parts
with this
work
and
for
this
nature
for
their
them
to
but
it
is
in
and
theoretical
service
in
day-to-day
List,
containing
, will
booklet.
and
a well
and
all
modifications
actual
servicing.
is
office
staff all
provide
no
way
training
also
be
efficient
fitted-out
SACHS
intended
filing.
We
to
2
hope
all
our
that
this
dealers,
manual
agents
will
and
be
of
real
practical
associates.
FICHTEL & SACHS
SCHWEINFURT
Service Dept.
assistance
AG
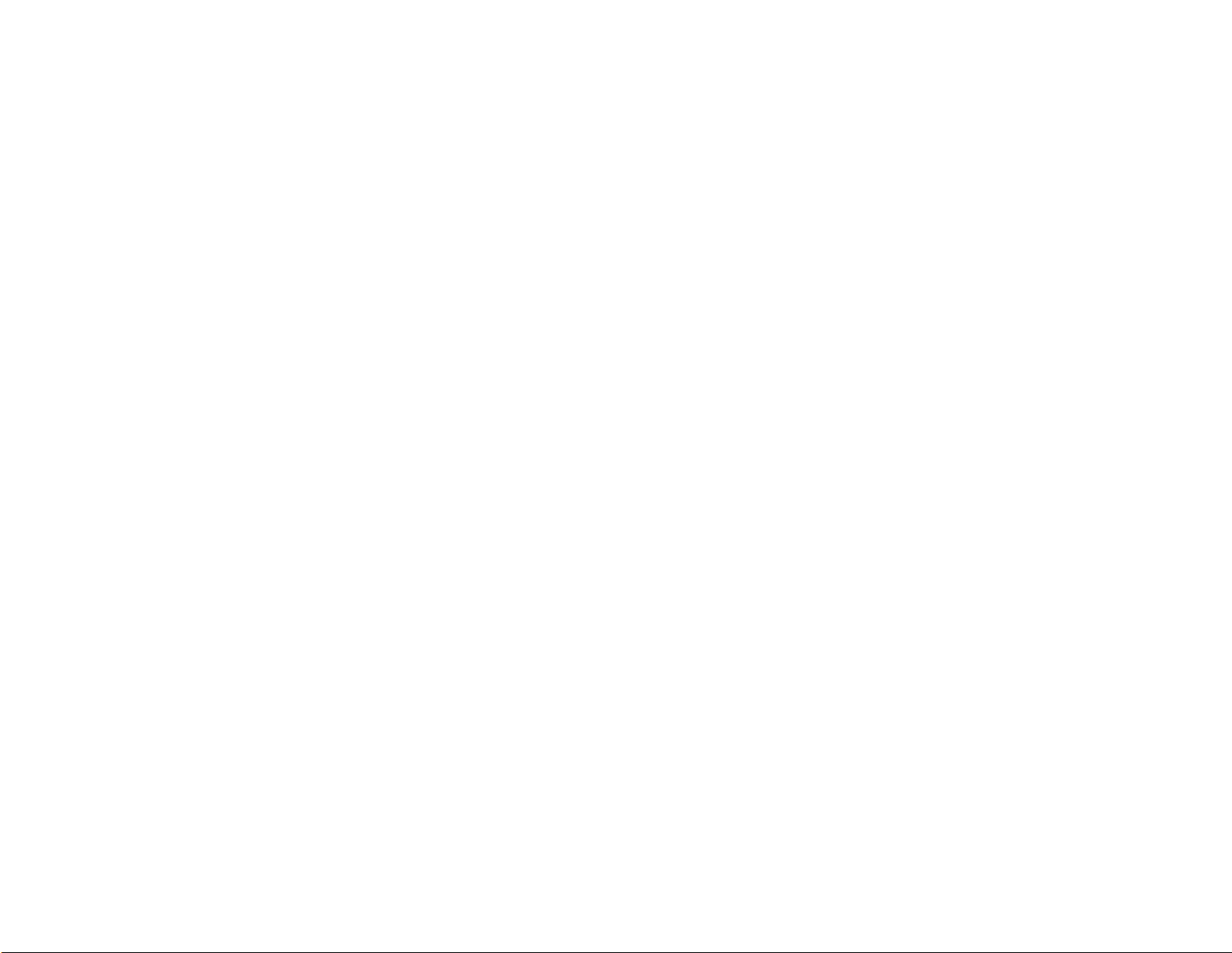
Technical
Descripti
Type: Fan-cooled single-cylinder two-stroke gasoline
Direction
Swept
Bore:
~
Stroke :
Comp
Output:
Ignition:
Ignition
Contact b reaker
Pole shoe
Spark
Carburettor:
Carbure ttor setting :
Air
Exhaust muffler:
Method
Engine lubricati
w
Data
on:
of
rotation: Anti-clockwise
capaci
ty:
ression
ratio:
ti
ming:
gap:
gap:
plug:
cleaner:
of
starting:
•
on:
SACHS
SA
340
9
22
HP (DIN
) at
525
0 rpm
12 V
12 V 75
240
= 1 tu
rn
T 1
open
BOSCH M
Main jet = 1 turn open
Idling j
et
SAC
HS
as
cu in.)
in.)
rJ;
3
36
75
cc
(20.503
.5
mm (2.972
I
I
I
I
26
i
BOSC
0.4 ± 0.05
running engine
running engine 7 ...
I
Tl
LLOTSON diaphr
HD-13
~
12 V
stopped engine : 0.2 ... 0
runn ing engine: 4.1.. .4.7
40
W equipme nt : stopp
W equipment: sto
I
Swirl-type exhaust silencer
on
,~·
request solenoid-controlled starte r 12 V 0.4 H
or
inerti
necessary battery
Two
-stroke mixture mixed
SA
340
seen on the output sh
75
mm
(2.779 in
11
HP
(DIN)
H flywheel magneto
40Wor
.4
mm
mm
mm (0.
ed
engine
pped
engine
BOSCH M
A 1
'h''
(38.10
Intake silencer
Recoil starter
a-pini
on type
SS
(super sport)
.)
at
6000
rpm
12
V75
W
before
TDC
before
TDC (0.1968 ... 0.2283
016
± 0.002 in.)
32
...
36
14
...
18
25
...
29
11
260
T 1
agm
car
burettor
mm
dia
Main j
Idl
starter
}2 Volt
32
25
: 1 ratio
I
engine
aft
of the engine
I
'·
I
I
I
(0.00
79 ... 0.01
mm
(1.2598
...
(
0.5511
mm
mm
mm (0.2756 ... 0
...
(0.9842 ... 1.
I
.)
I
et
= 1
in
1f,
g jet = 1 t
12
V- 0.4
.. ,
38
Ah
HP.
23.5
with carburett
24.5
wi
57
in.l
in.
1.4
173 in.l
0.7087
1417
.4331
HR-1
turn open
urn
open
P.
SA
CHS
SA
368
cc (22.4
55
rJ;
79
mm
(3.1
9.7
HP
(DIN)
or HR-
HP (DI
N)
th carbu rettor
in.
in.l
in.
BOSCH M 240
8 A
1'
11•"
(
30.
370
cu in.)
10
at
5250
at 5250
HD-
T 1
16
mm
in.
)
rpm
18
A
rpm
13
A
dia.
)
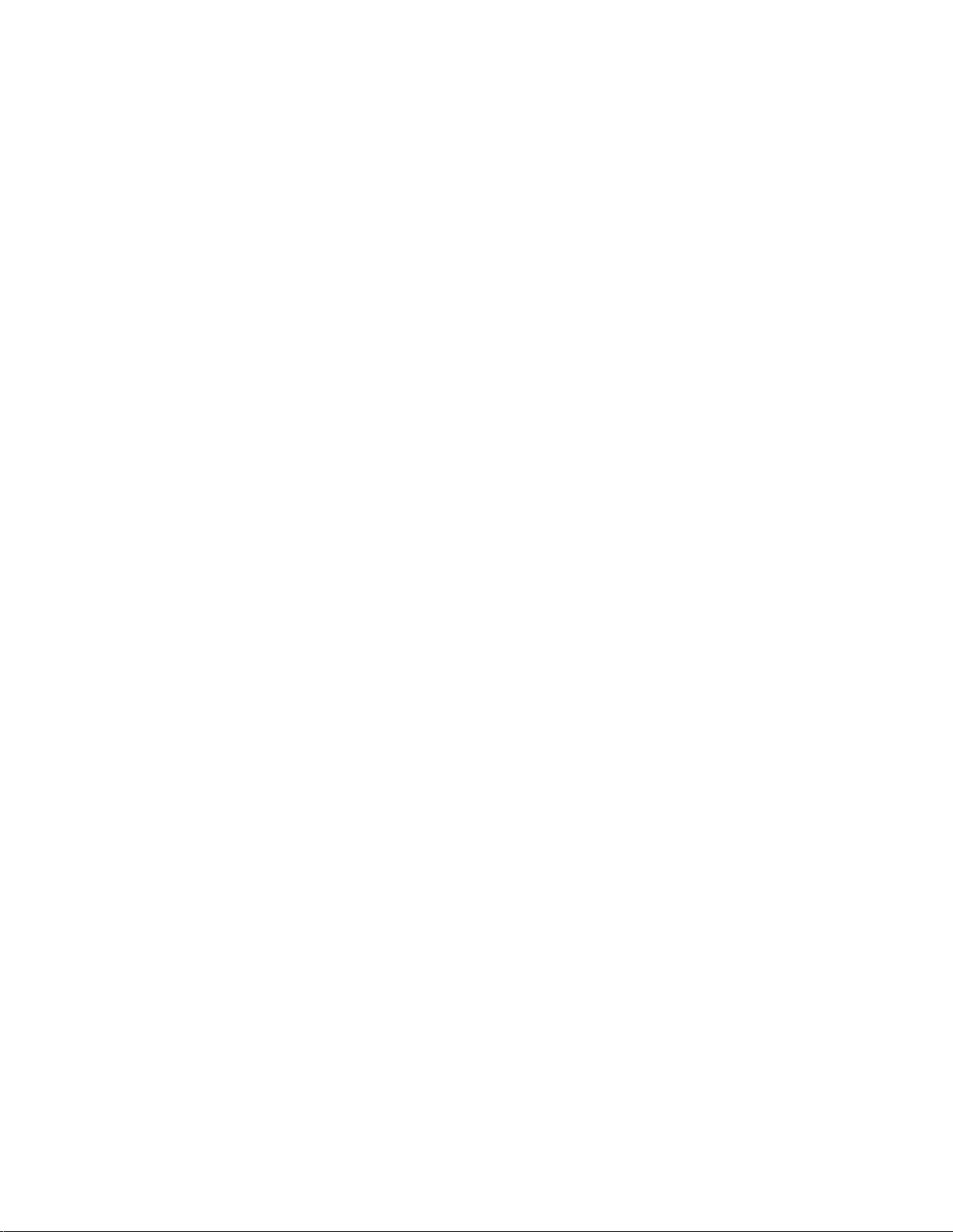
lllustr.
No.
1
2
3
4
5
6
7
8
9
10
11
12
13
14
15
16
Part number
0276 065101
1447 020 000.8
011
1449
000.8
0976 088 100
0976
111
100 Retaining lever
0276161
101
0276 164 102
1476 012 000
0977 063105
0276 135 000
137 6 020 000.8
0276 170 000
1476 013 000.8
1447 009 000.8
1476 014 024.8
1476 014 000.8
1447 009
001
147 6 014 023.8
Repa
I
Gudgeon
I
nsert
Locating pin
Protective
Oil
seal
Ex
tra
.8
Thrust b
spare
Extractor
Ti
ming
Revolu
rque
To-
xt
ractor sleeve
E
cons
1476
1440 027 001.8 h
1476 012 000.8
Clampi ng ring,
Extractor
of
tractor
Ex
(recoil
Clampin
.8
xtr
actor
E
bea
D
es
cription
ir
too
ls
pin ex
tractor
for gudgeon
cap,
for
pin
piston
14 mm
extra
ctor
dia. bore
extractor
ctor hook
gauge
ti
ear
ing a·ssy.,
part
for
on
counter
4 mm
for
magn
for
(1
0276161
eto
fly
spark
advanc
piece
101
whe
)
el M 50x1
e
key X
assy
.,
isting of:
011
roll
000.8 extra
she
lls
er
bearings
shells
st
arter)
g ring,
shells f
ctor
exagon
thrust
I.
D.
for
for
sleeve
head
bearing
bolt
assy.
58 mm X X
inner races
NJ 306 C3
bearing
NA
bushing
. . . . . . .
I.
D.
85.5 mm
or groo
ved
ball
ring 6306 C3
for
engine
tn
tn
0 0 0
.... ....
""
""
<(
<( <(
tn tn tn
X X
X
X
X X
X X
X X
X
X
X
X
X X X
X X
X X
X
X
X
X X
X
X
X
X
X X
X X
,.._
""
X
X
X
X
X
X
X
X
X
X
X
X
X
X
X
X
X
I
17
0276
081
18
0276 082 000 Swi
19
0276 085 005 S
20
0977 0
41
000
000
Assembly jig
Clamping
ve
base
l unit
etscrew
Mounting
plate
X X X
X
X X
X X
X X
I
I
X
X
I
5
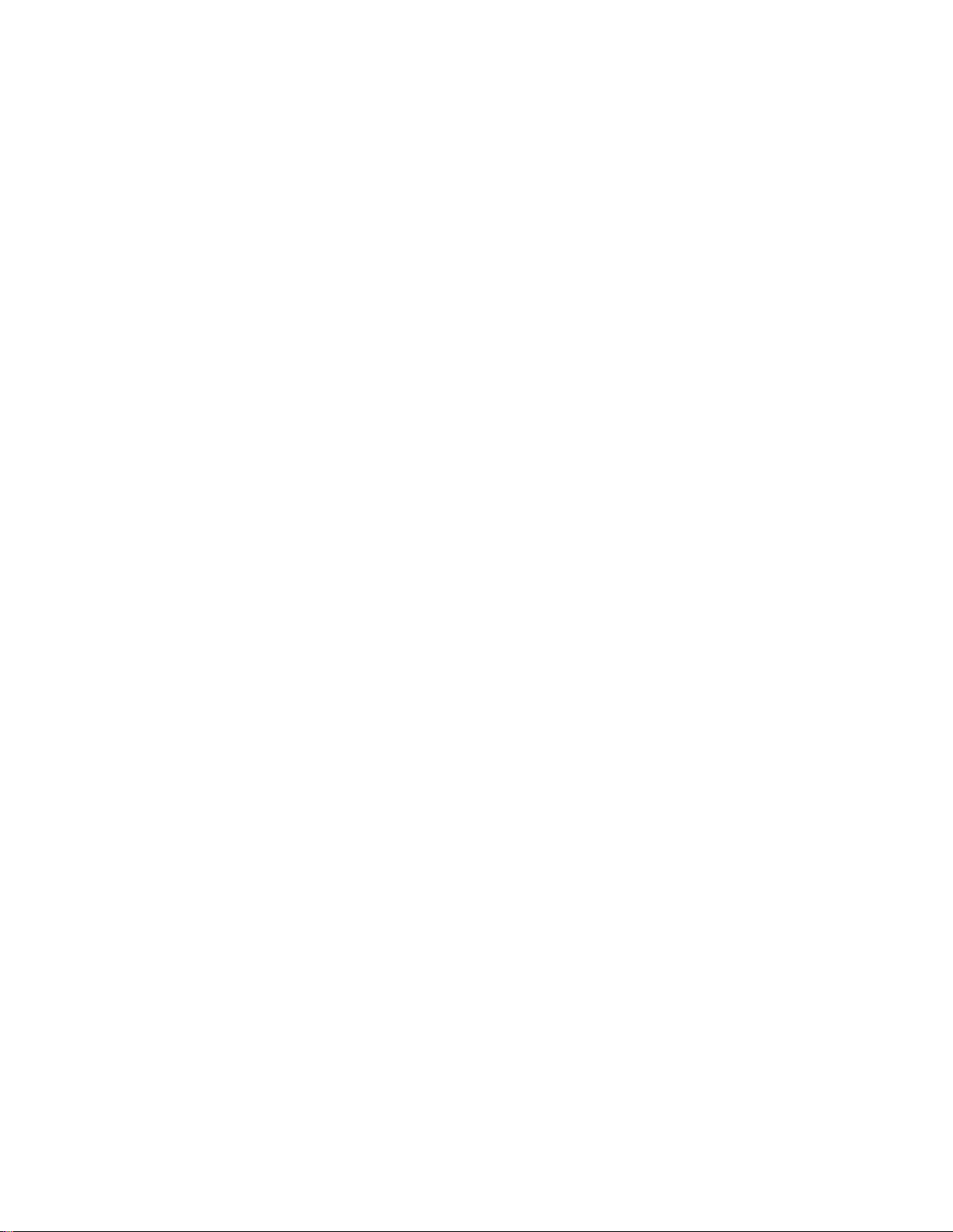
TAKING
DOWN
THE ENGINE
Remove
etc
U
Un
Rem
When
se
Fi
all
deflector
the
giving
conn
engine
.).
nscrew
screw exhaust mu
ove
quence indicated.
g.
1
ections
from engine
on
cyl
inder
on
ffl
er, i.e.
man
and clean thoroughly bef
the
engine a gen
eral
to
frame
SACHS SA
ifold
and
ove
rhaul , comp
and
340
and
bracket.
ore
taking
unit (cables, ele
SA 370,
onents shou
Exhaust
electric
Fig. 1
Scr
sembly
bolts
adjoining illustration.
Pull
Remove
carburettor
Rem
insulating
Rem
sary.
Unsc
Re
Fig. 2
Detach
Un
Hold
lev
screw
hub
Rem
s
Unscrew
ga
if there is one.
down.
muffler, carburettor
starter
ew
dow
jig w ith 3_
M l 0 x 40, as shown in the
off impu
ov
e rns.ul
ove flan
rew
coil
starter, starter
reco
lock nut in the
sta·rter h
er
(3,
th e n
with
ove
pace
r.
sket.
ctric
ld
be removed in t
n engine on the as-
hexagon
lse pipe
int
ake
sile n
(2)
.
ating
flange.
ge
{l) only
electric
spr
2 cylin
starter
il
starte
ub with r
repair too
ut
and re
ing ri
ng
dri
fan
(l)
starter
connections
hecid
(4).
cer
(3) and
sleeves
if
neces-
(5).
hub
and
r.
hub
etaining
l no. 5), un-
move starter
and
washer.
cal pins
and
and
remo
he
and
and
fan
(2)
ve
.
Fig. 2
6
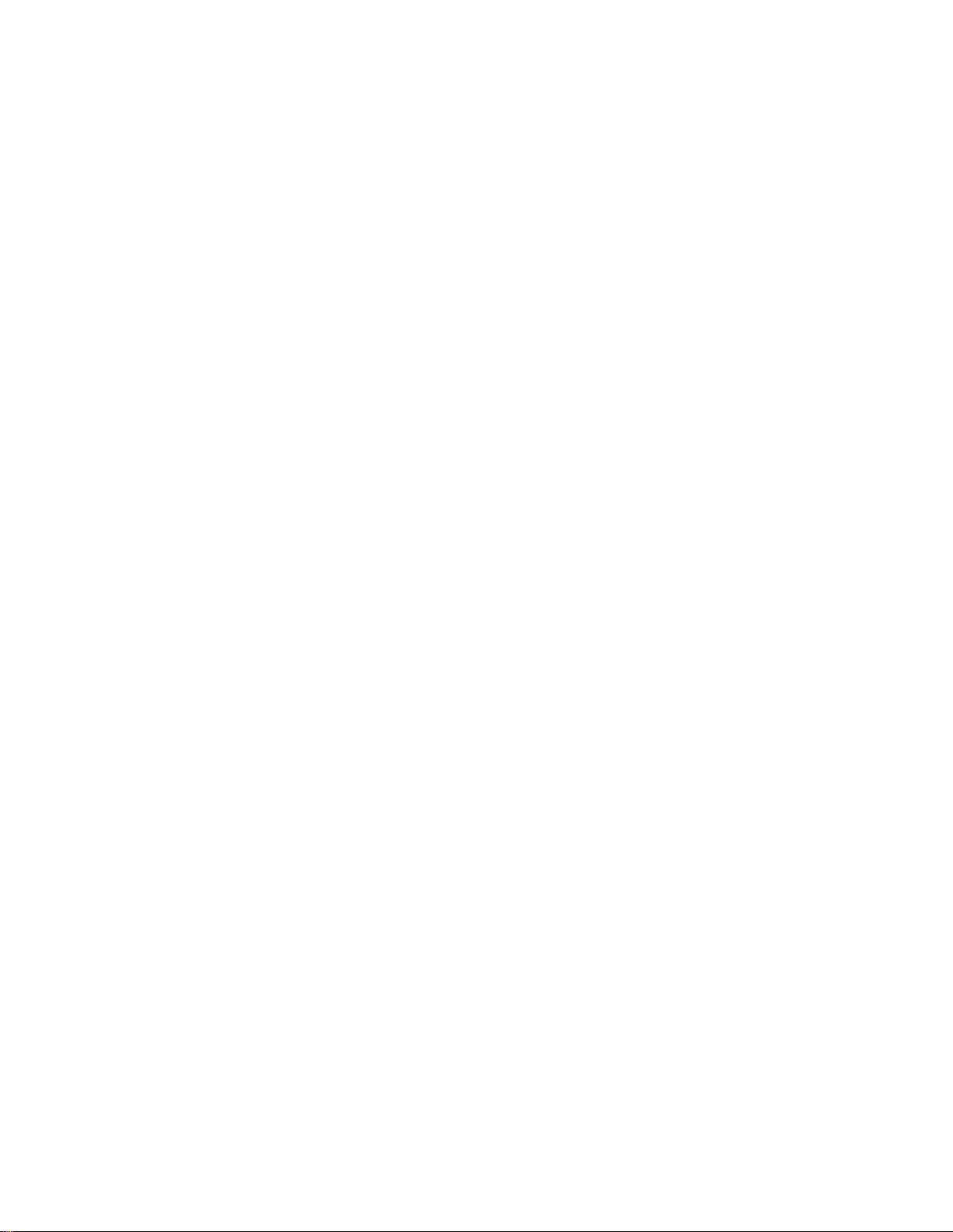
Cover
plate
(onl y
and
fixing
wit
(l
).
Fig. 3
Unscrew
lead
and
cover
Detach leads
and 3 of
remove fan
Note:
Remove _
housing
nection, if
the
terminal
housing
cover
for
electric starter con-
fitted.
When removing
pull
the
insu
l
ead through
T
ake
Note:
Rem
ove
on
ly
if
Re
mov
circuit
Detach
in_s
ulator
mount
Re
lating hose
.
care of c!owel
. ·
short-circuiti
necessary.
e ·ru
bber
ing button.
short-cir
. :
part
s in
fan
housing
clip
for
h 40 W
equipm
at term
box
(3)
flanges on
the
fan
tub
ng
cap
(2)
c~itin
g.le
reverse ord
ignition
ent)
inal
s 1, 2
(6)
and
.
fan
housin
(5)
with
es.
button
and short
·
ad
f
rom
er.
g,
F & SL.-075: 22
Fi
g. 3
-
Magneto
Fig. 4
F
it
.
4)
F
it
no.
pull
th
e ex
no
Labyrinth ring
ba
Fig. 5
Un
On
pull
of
pull
rubber cap
protect
to
threaded
ret
aini
5)
to
off
the fly
tra
. 7
).
se
plate
screw lab
engin e
ignition
the
spark
off
rubber
flywheel
ive
ng lever (l ,
magne
ctor
wit
(2)
ignition lead
Un
screw
rem
and
).
armature
ove
(on
insul
Woodr
and
tion lead
ment)
ead
l
Remove
cap
(re
pair too
end
of
crankshaft.
repa
to
flywheel
wheel
by
(2,
repair tool
and
armature
yrinth
rin
g (5).
h 40 W equipm
lead
with
spri
plug terminal
sleeve (1) a
and
screw
socket.
base
it together w
ly with
40 W eq
ating
tube (w
uff
key
.
ir tool
means
ng
out the
plat
e (4)
ith
igni-
uip-
l no .
and
of
ent,
out
(6),
nd
ith
Fig. 4
Fig. 5
7
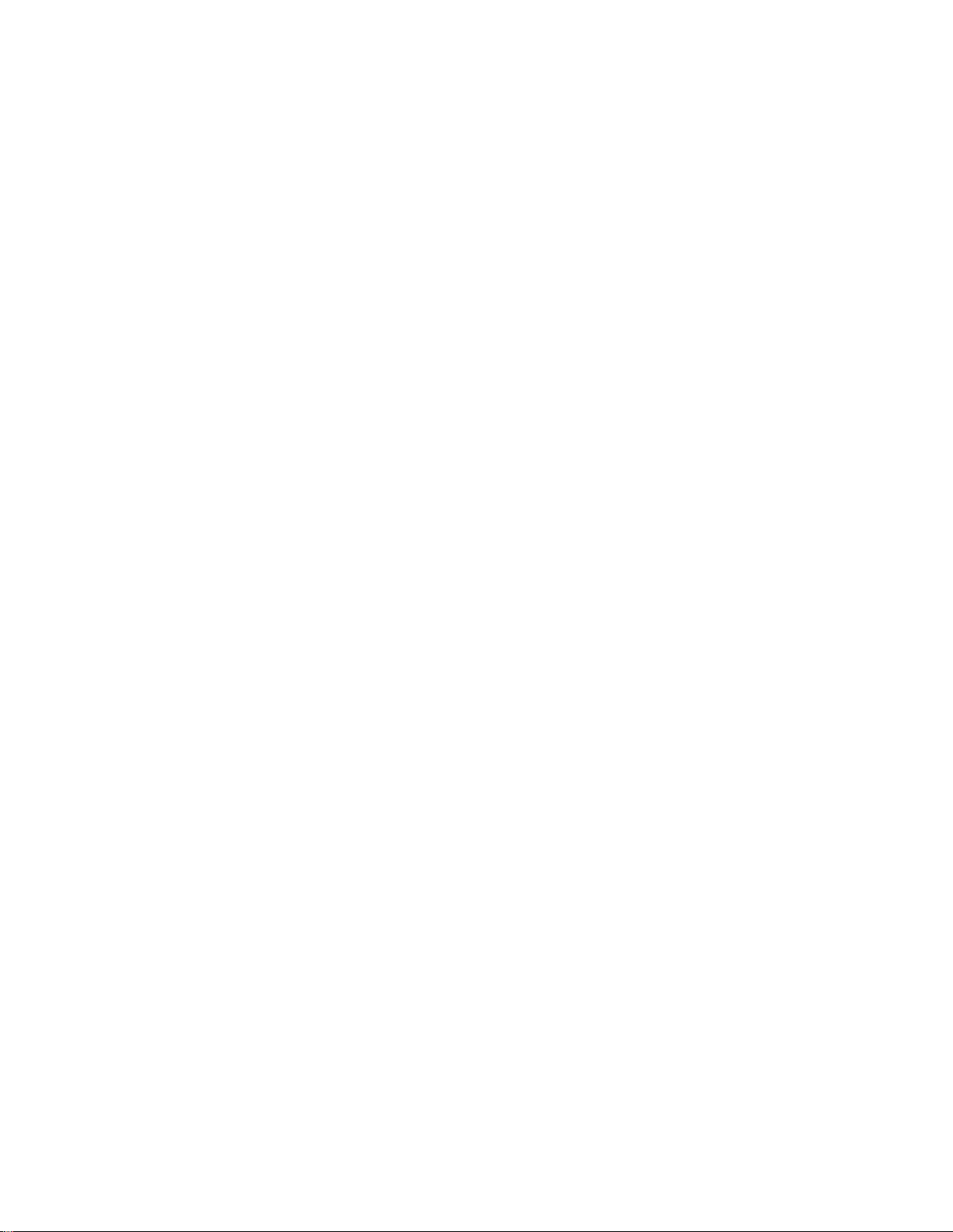
Fig. 6
Use only genuine
SACHS
spares.
Cylinder
head,
cylinder and
piston
Fig. 6
Unscrew
cylinder
head
and
linder.
On
SACHS SA 340 SS,
cylinder
Pull
Dang
(
rings
Remove
off
er
.)
head
cylinder
of
cylinder
gasket.
without
breaking
flange
remove
twisting.
gaske
Note:
The
cylinder
twice.
A
(see
cylinder
Use
Spare
piston
be
rebored.
Place
cylinder
s
lott
ed
wooden
Cov
er
the
the
two
sar
y,
force
gudgeon
tool
no.
tool
no. 2).
When
fitting
should
the
be
piston
ves. (Danger
can
appropriate
Parts
List).
with chromium
bearing
surface
on
board
crankcase,
wire
circlips. If
out
gudgeon
pin
extractor
1}
and
insert
the
steel
taken
rings
are
of
breaking
be
home-made
(1
take
(3,
(2,
band,
to
ensure
in
their
rebored
-pla
cannot
).
neces-
pin with
repair
piston
rings.)
Remove
slotted
wood
en
board.
Crankcase and crankshaft
Fig. 7
Unscrew 6 hexagon
screws
from
crankcase.
socket
Unscrew hexagon head bolt
Fig.
3)
t
apping
er
takeoff
rubber
Remove
tak
eoff
care
of
Unscrew
oil
drain
Uns
crew
side
from
he
at
it
F)
for
(grooved
Clean
all
for
wear
and split
the
hammer.
crankcase
side
dowel
screwed
cock
crankcase
the asse
to
1 00
removing
ball
parts
and rep
crankcase
crankcase
side slightly
ha lf
with a
half
and
gasket.
tubes.
nipple {1}
(2).
half
magneto
mbly
...
150 ° C (212 .. . 302 °
the
bearing)
jig
crankshaft
.
thoroughly,
lace
when ne-
power
cessary.
cy-
piston
t.
piston
ted
out
repair
care
that
groo
head
{4,
by
pow
Take
and
and
check
-
-
8
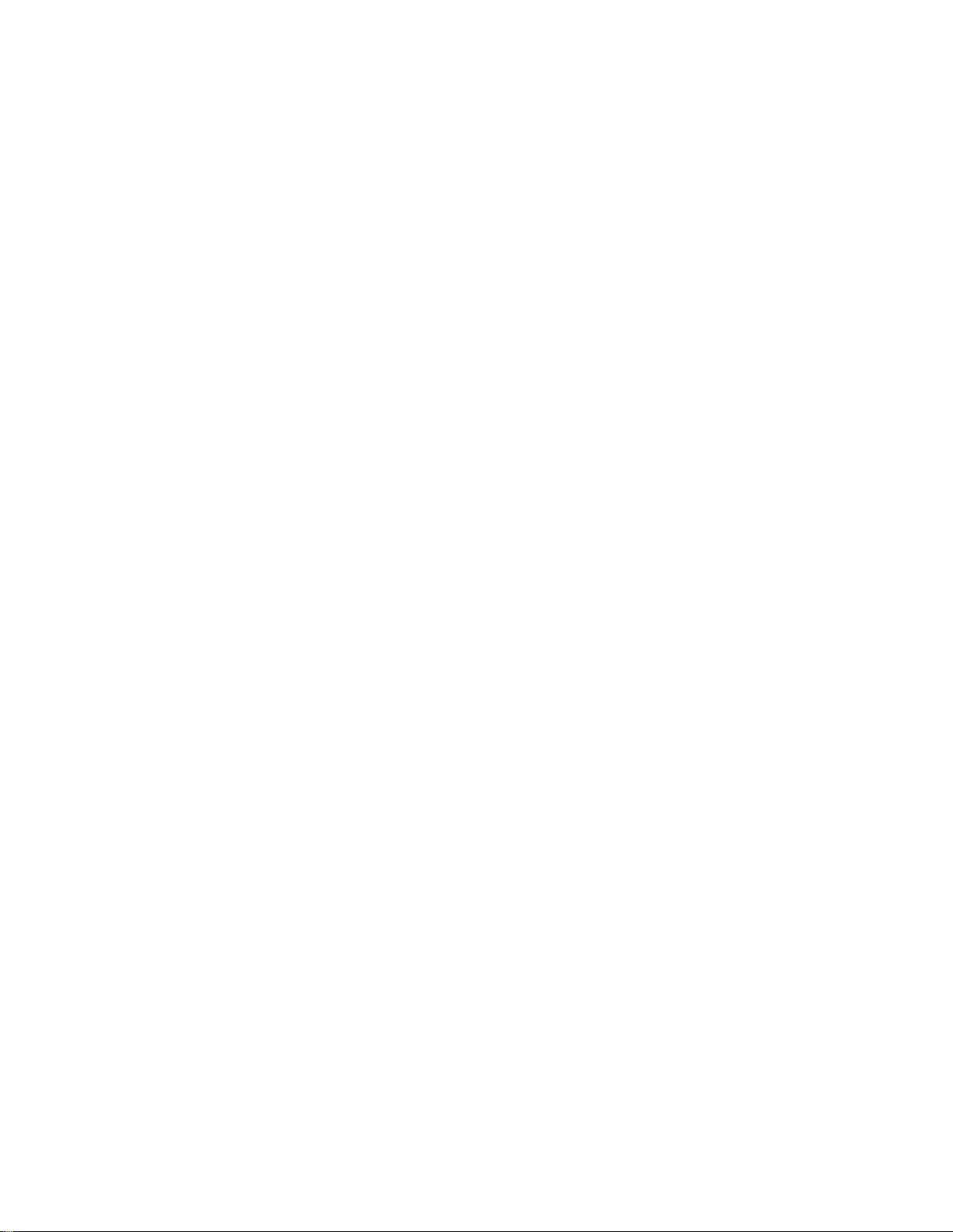
WORK
ON
INDIVIDUAL
PARTS
SACHS
special extracting tool
for
(without dismantling the engine)
FICHT
EL
da
mag
ed
oil
necessary.
& SACHS
Engine t
roubles
relatively short time.
When
replacing
Extracting oil
Fig. 8
Before
ext
racting
to
record
sure
si
on
x, o
new
same
or
oil
seal can
dimension.
Note:
If
the
correct
ion
is
s
troubles
bor
tati
not
may
es
in the era n kcase
ng
parts
parts.
AG
have
sea
ls
caus
oil
can
ed
seal
be
repla
by leak
s,
the
deve
seals
the
oil
ord
seal be
er
that the
dimen-
to
the
dim
en-
installation
y,
in
be fitted
installation
adhered to, engine
occur
by
closed oil
or
by
moving
again
ro-
st other
loped a special
ced w
ing
or
foll
owing
F
crankshaft oil seals
ithout a major
damaged
poin
ig.
8
extra
disasse
oil
seals can thu s be
ts should
cting
be
tool
mbly
borne
by
of
in m
means
the
engi
remedied
ind:
F l S
of
ne
which
being
1n
077:
l
a
Fi
g.
If
outs
or
not
9
the
ide
other
be
oil seal
by
means
locking
extracted
is locked t
owards
of a collar
element, it can-
.
Q
(a)
Fig. 9
9
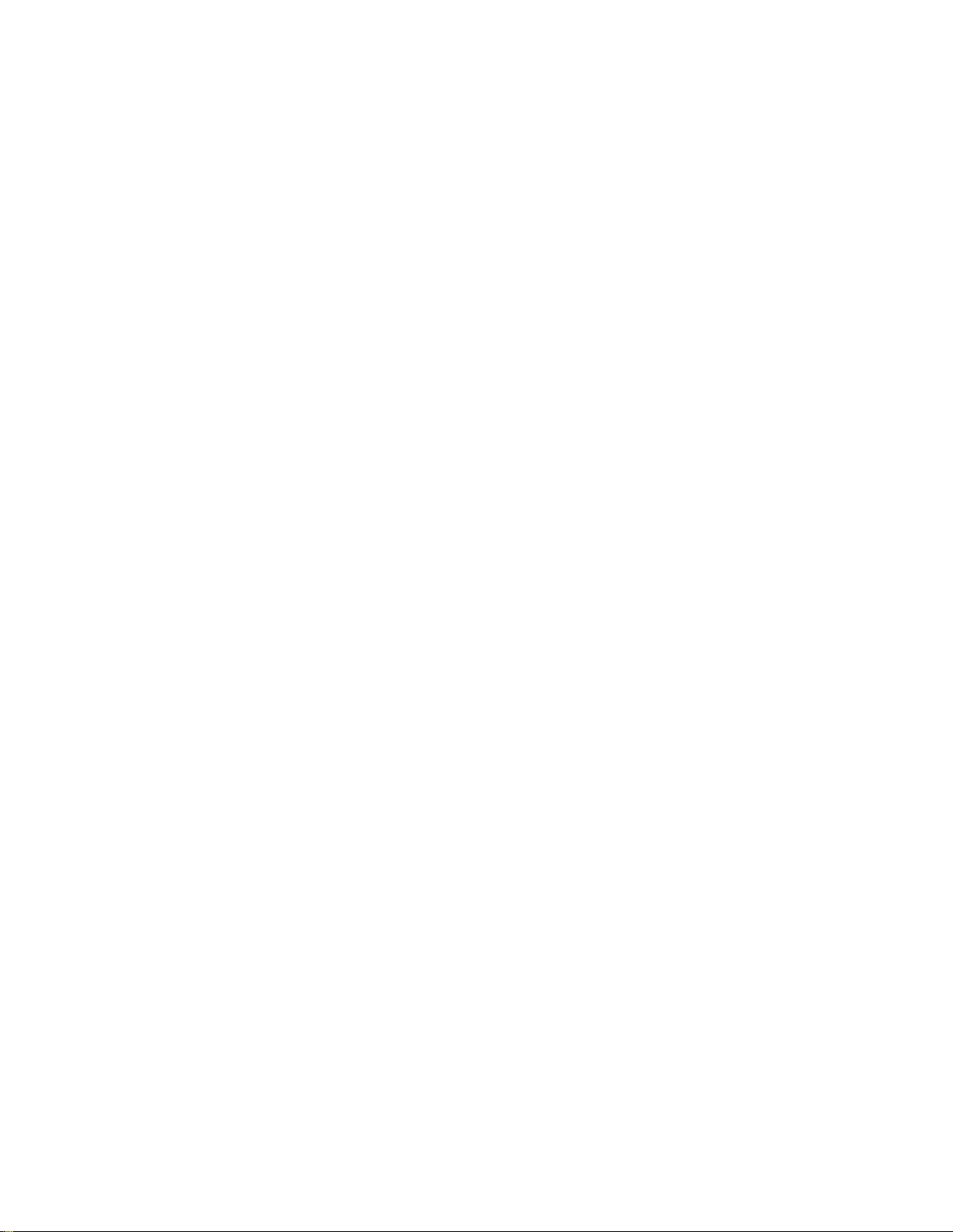
Fi
Fi9.
F
ig.
10
Place
the
sition
extracting tool
in such a
ho
oks
(4) grip behind
steel rim of
on
the
si
cylinder
care
that
rew
(3)
sc
Screw in
oil
seal.
F & S
400:58
g.
10
Fig.
11
If the gap
sheet steel
narro
w and
can n
ot compl
position,
racting
ext
hooks
(l) in in c
Rem
ount
as
described
Note
:
If the
oil
dation
),
break.
There
11
to knock
force fit by
way
th
e o
legs
screws {1
shaft
in a
st s
il
(2)
(5)
lign
crew
two
head
are
thru
betwee
rim
of
oil
the
extracting tool
ete
leg
tool
off
lin
and
ly
one leg
and
ed
ext
take
under Fi
seal has
got
the sheet steel rim m
fore it
th
e oi I sea I out
mea ns
of a tub
in
po-
that the two
the sheet
seal. Pre-ten-
even
ly with
),
taking
and thr
ust
ment.
and
extra
n sha
ft
and
seal is t
oo
be placed
of
ert
the
bot
ins
position.
ract
oil seal
g. l 0.
stuck (
oxi
is
advisab
of
e.
ct
in
h
-
ay
le
its
Fitting
Fi
g. 12
10
the
oil
seal
Fig.
12
Before
fitt
pace a·ro
s
wi
th a littl
and ligh
To
oil seal
sh
arp
sh
ell slee ve. If necessary, p
sm
sh
arp edges.
und the tens
e hea t-resisting
tly smear
protect
th e sea
from damag
edges on the
ooth adhesive
Place o il seal in pos
ing the o
pr
ess
it
in
e,
8).
by
taking
dim ens
tub
lation
ig.
(F
The oil seal
when
bei
ng pressed in.
means
care
ion
must
il
seal,
ion
the
sea
ling
lip
e caused
shaft
tape arou
ition a
of a suitab
of
exact
x, o
not
be
fil
l the
spri
grease
lin
g l
of
, use
instal-
and
tilted
ng
ip.
the
by
ut
nd
nd
le
y

Changing crankshaft bearings
H
eat
crankcase
bearings
In
sert new
strike a stop
ess
in
Pr
side
case
new
until
halves
hal
and
crankshaf
outer
. Press in oil
grooved
they
strike a sto
have
ves
races
been
to
about
t oils
of
roller
sea
ls (with
ball
bearings
p. Press
screwed
100 ... 150 ° C (212
seals.
bearings into
in
together.
sealing lips
into
the
crankshaft
the
inwards)
warm
oil
...
302 ° F). Remo
wa rm
crankcase
until t
crankcase
seals
until flush only
hey
are
halves
ve
outer
halves
flush.
on
after
the
races
until
magneto
the
crank-
of
they
Removal
bearings
ing
Fig. 13
Pull
off
ed ball
the
appropr
(9
and
7)
a nd wi
pair
tool no.
Remove
sat
ing
washers
of
and
inner
bearing
6),
clamping
thdrawal
spacers
inner
grooved
race
(4)
iate
extractor
11
to
(3)
(2).
races
(1)
and
by
rings
tool
16).
and
of
roller
ball
bear-
groov-
means
shells
(8
(10, re-
compen-
of
and
F&S
1..075:25
Fi
g.
13
11
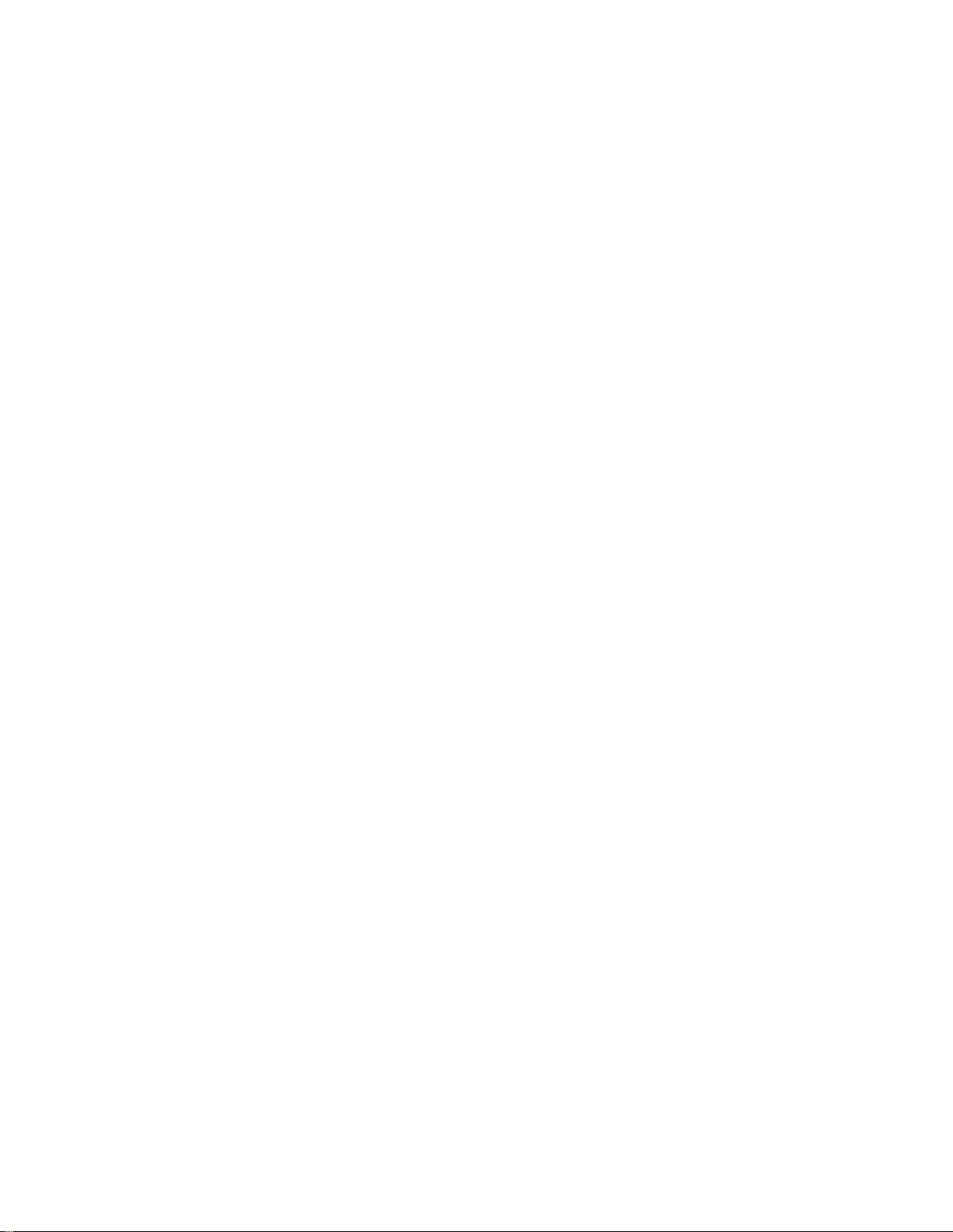
Fig. 14
The
diff
(3, Fig .
erence
13) and
pin
power takeoff side.
of
0.90 mm is
the inn e r
rac
tak
e o f
en
the
up
by
cylindrica
Gauging
Fi
g.
14
Permissible
mm (0.0039 ... 0.0079 in.).
Example:
Inse
rt
inner
cylindrical
into
outer
C
rankcase power takeoff
side:
seali
(with
gas
ra·ce
of
bear
Crankcase
s
ide:
seali
inn
erraceofbearing
C
rankcase
Dimension
crankshaft,
over
both crank
with
a 5 mm thick
s
pac
er
on
takeoff
and
side - 79.00 mm
Axial
play
Pe rmissible axia
play
Difference
to
be taken
inser
ting shims (2, Fig. 13) betwee
l rolle r
bearin
g (1, Fig. 13)
axial
play
of
crankshaft
axial
play
race
of
roller
bearing
race.
ng surfac
ket)
to
e
inner
ing 40.60 mm
magneto
ng su
rface
to
+ 39.
gap
of
measured
power
magneto
up
webs,
l
n the spac
on
80.10 mm
1.10 mm
- 0.20 mm
0.90 mm
the crank
0.1
50
...
0.2
mm
er
-
Fitting the inner race of the cylindrical roller bearing
Wh
en fitting the
Fig.
13
on
way
s be positioned betwee
that
it ca n be s
in
po
sition.
Ne
ver clam
the
inner
uns
erviceable
crankpin
upported
p th e
race
by
.
inner
race of
pow
crankshaft
the
er
at
cylindrical
takeoff sid e),
n th e
two
bo th e nd s, the re
in a
vice at a crankpin
rolle r bearing (
an
inte rmedia te
crank webs
by permitting the
striking it. This will crush the we
. This
12
or
at
bs
do
not
plate
(5, Fig. 13) should a l-
plate must
crankshaft
the
webs
and render
forg
be
and
the
et spa ce rs 3,
of
such a si
to lie fre ely
neve
r try
cra·nkshaft
to
ze
fit