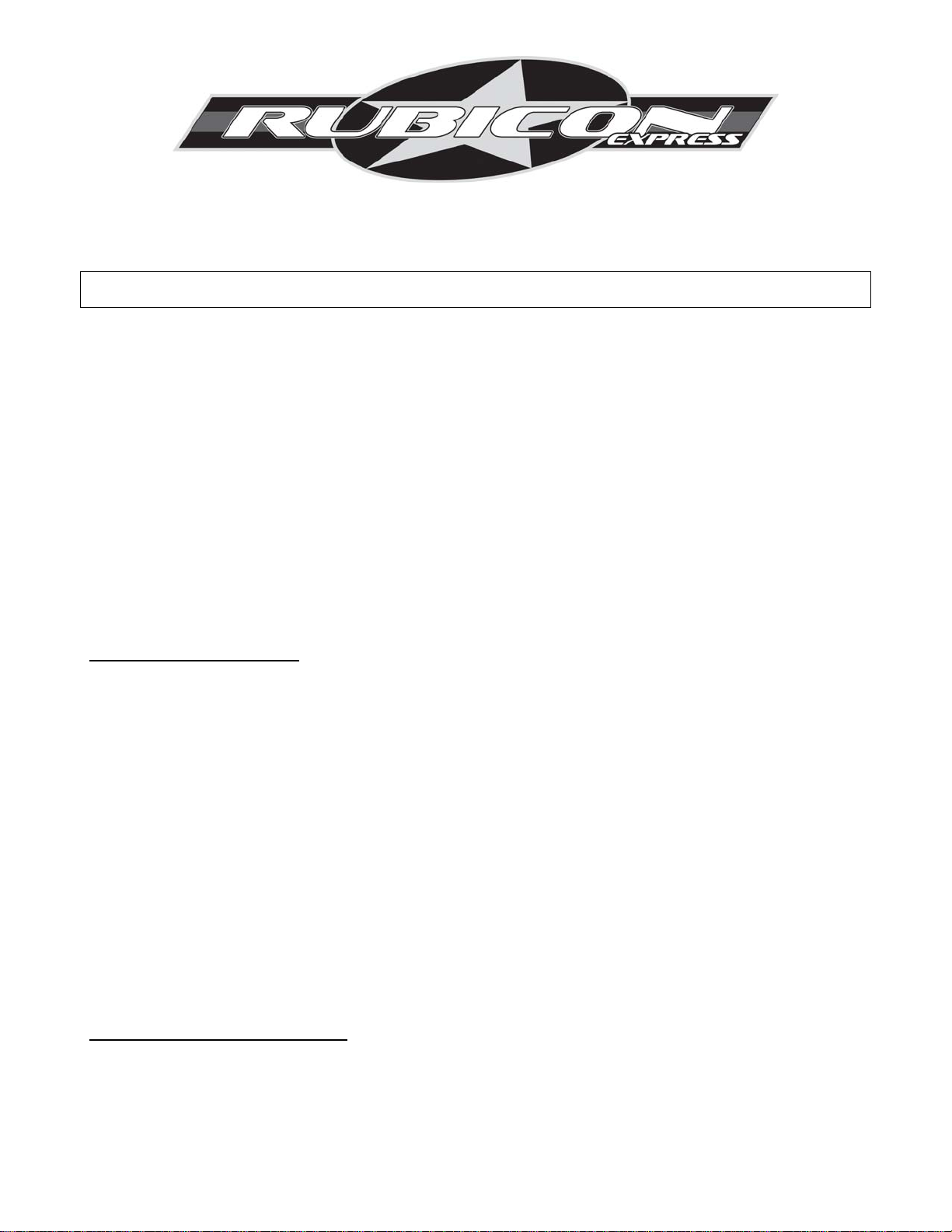
RUBICON EXPRESS 3290 MONIER CIR., RANCHO CORDOVA, CA. 95742 916-473-4600
INSTALLATION INSTRUCTIONS FOR:
RE6300 XJ EXTREME DUTY LONG ARM SUSPENSION SYSTEM
***********READ THIS FIRST **********
Congratulations on purchasing the ultimate suspension for the Jeep XJ Cherokee. This instruction sheet is designed to
replace steps 11-13 of our RE6200 5.5” Extreme Duty XJ Suspension instructions until final RE6300 instructions are
complete. Review and understand this instruction sheet and the RE6200 instructions completely before proceeding. The
system includes the same extreme duty upper and lower control arm design as the front of our famous TJ Long Arm
System, plus an extreme duty crossmember specifically designed for the XJ uni-frame. The long arms and crossmember
essentially replace the control arms and drop brackets in the RE6200 system, plus it adds the RE2500 drop pitman arm.
Safety Warning:
Suspension systems or components that enhance the off-road performance of your vehicle may cause it to handle differently, on and off-road, than it did
from the factory. Care must be taken to prevent loss of control or vehicle rollover during sudden maneuvers. Failure to drive the vehicle safely may result
in serious injury or death to driver and passengers. We recommend you always wear your seat belt, drive safely and avoid quick turns and other sudden
maneuvers. Constant maintenance is required to keep your vehicle safe. Thoroughly inspect your vehicle before and after every off-road use.
Installation Warning:
We recommend that certified technicians perform the installations of our products. Attempts to install these products without knowledge or experience
may jeopardize the safety of the vehicle. These instructions only cover the installation of our products and may not include factory procedures for
disassembly and reassembly of factory components. Read instructions from start to finish and be sure all parts are present before disassembling the
vehicle. Included instructions are guidelines only for recommended procedures and in no way are meant to be definitive. Installer is responsible to insure a
safe and controllable vehicle after performing modifications. Do not perform test drives on public roads with partially completed installations. Always
double and triple check your work before use.
RE6300 KIT CONTENTS
RE1141 Gen2 sway bar disconnects
RE1345 Front coil springs
RE1383 Front bump stop extensions
RE1462 Leaf pack w/bushings x 2
RE1515 Rear brake hose
RE1550 Front brake lines
RE1660 Adjustable track bar
RE1665 Track bar frame bracket
RE1670 Track bar frame bracket brace
RE2421 or RE1225 U-bolt kit (2421 = Dana 35/44, 1225 = Chrysler 8.25)
RE2500 Drop pitman arm
RE2700 Extended shackle
RE4000 Front Lower Left Extreme Duty Control Arm w/ hardware
RE4010 Front Lower Right Extreme Duty Control Arm
RE4020 Front, pair Upper Extreme Duty Control Arms w/ hardware
RE9920 XJLA Crossmember Sides (Bo x 1 o f 2)
RE9922 XJLA Crossmember center section (Box 2 of 2)
RE9921 Front sway bar relocation brackets
TYPICAL TOOLS REQUIRED
1-1/8” hole saw, ½” drill & drill bits, angle grinder,
Basic mechanical hand tools, several C-clamps or vise grips, pitman arm puller
Floor jack & jack stands Plasma cutter, or reciprocating saw w/metal cutting blades and Mig Welder
RI6300 Page 1 of 4
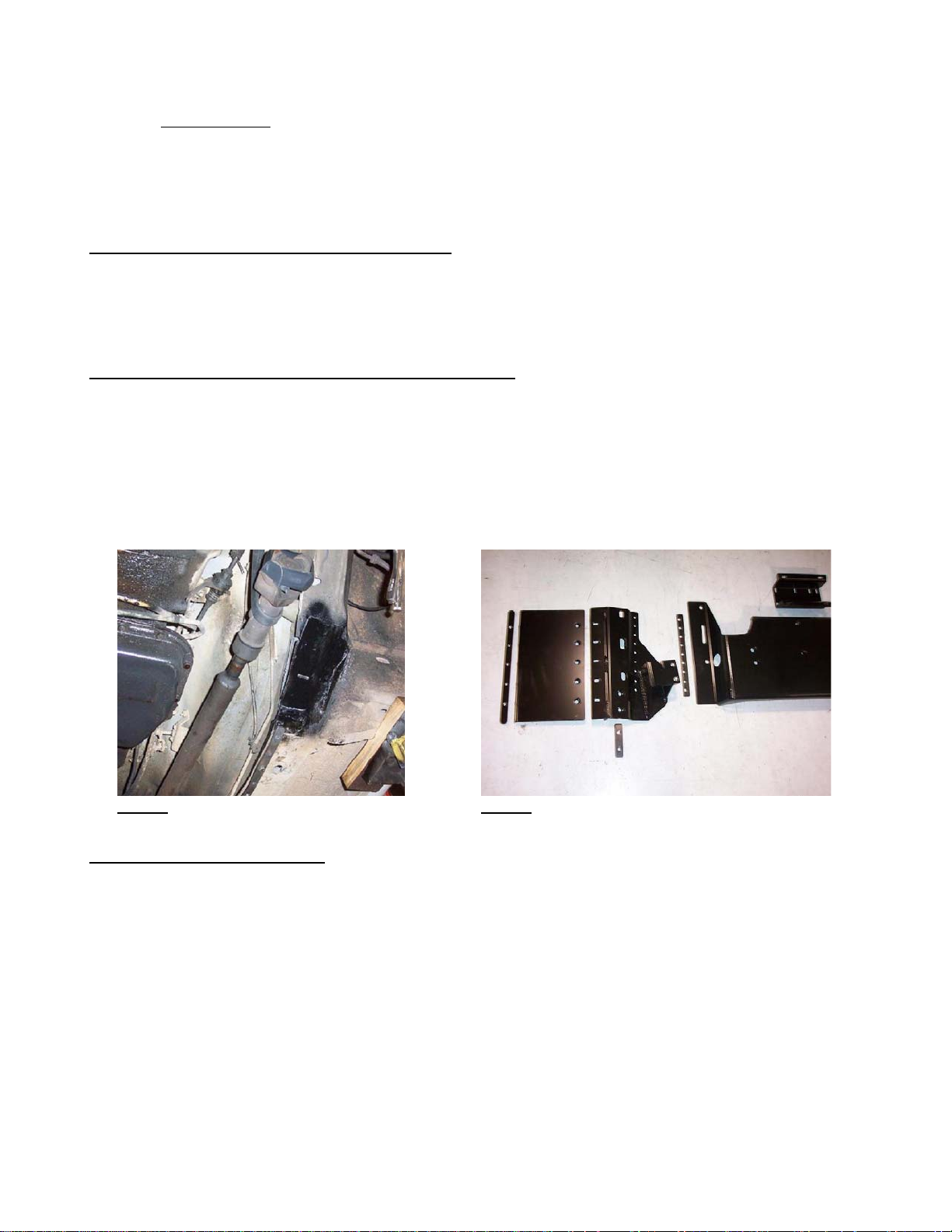
PRE INSTALLATION NOTE:
Control arm bushings are pre-lubed during initial assembly at Rubicon Express. As general maintenance the control arm bushings should be
lubed with a silicone base grease
The Super-flex joints are also pre-lubed during initial assembly at Rubicon Express. As general maintenance the super-flex joints should be
greased as needed and the outer spanner nut tightened on the joint. Any type of grease will work on the Super-flex joints. Spanner nut
tools are available through Rubicon Express (RE3771 & RE3772) if needed for tightening of the joints.
as needed. Silicone base grease can be purchased at your local auto parts store.
LONG ARM INSTALLATION OVERVIEW (after steps 1-10 of RE6200 Instructions)
The installation of the long arm portion of the kit can be broken down into the following tasks:
1. Removal of factory lower control arm mounts from uniframe.
2. Front 3- piece crossmember.
3. Control arms.
Step 1 - Removal of factory lower control arm mounts on frame.
First, support vehicle by uni-frame (preferably on a lift) and work on a stable level surface. Support axle with jack
stands and perform steps 1-10 of the RE6200 system. Be sure to keep the front bolts from the lower arms as they
will be reused.
A. Cut off the factory lower control arm mounts from the uni-frame. Use extreme care as not to damage the
uniframe, or cut into existing brake, fuel, or electrical lines.
B. Grind rough areas smooth and repaint – refer to Photo 1 for typical bracket removal.
Photo 1
Photo 2
Step 2 - Front 3-piece crossmember
A. First, support transmission/transfer case and remove factory crossmember (and skid plate if there). Loosely bolt
transmission adapter plate to transmission mount so fitment can be checked with new crossmember in position.
The adapter should be positioned with the eight-hole surface up and off set to one side just like the factory
crossmember holes.
B. Note that the factory crossmember is held up by two bolts and two studs. The studs will have to be removed with a
stud removal tool or it may be possible to double nut them and back them out.
C. Refer to Photo 2 for a layout of the right side components of the “3-Piece Crossmember”. Generally align the
center slots of the crossmember over the center slots of the left and right control arm mounts and loosely bolt them
together (through the four large counter sunk holes in the crossmember into the PEM nuts of the control arm
mounts) with the four supplied 1/2” flat head bolts. Loosely bolt assembly up into the four factory holes with the
supplied 10mm bolts and flat washers (early models use the front and middle holes and later models use the
middle and rear holes of the crossmember and control arm mounts) – refer to Photo 3. Align control arm mounts
so their pinch weld holes can be transferred through the horizontal pinch welds along the inside of the uni-frame
rails and tighten the four 10mm and four ½” flat head bolts. Check transmission adapter for hole alignment.
RI6300 Page 2 of 4