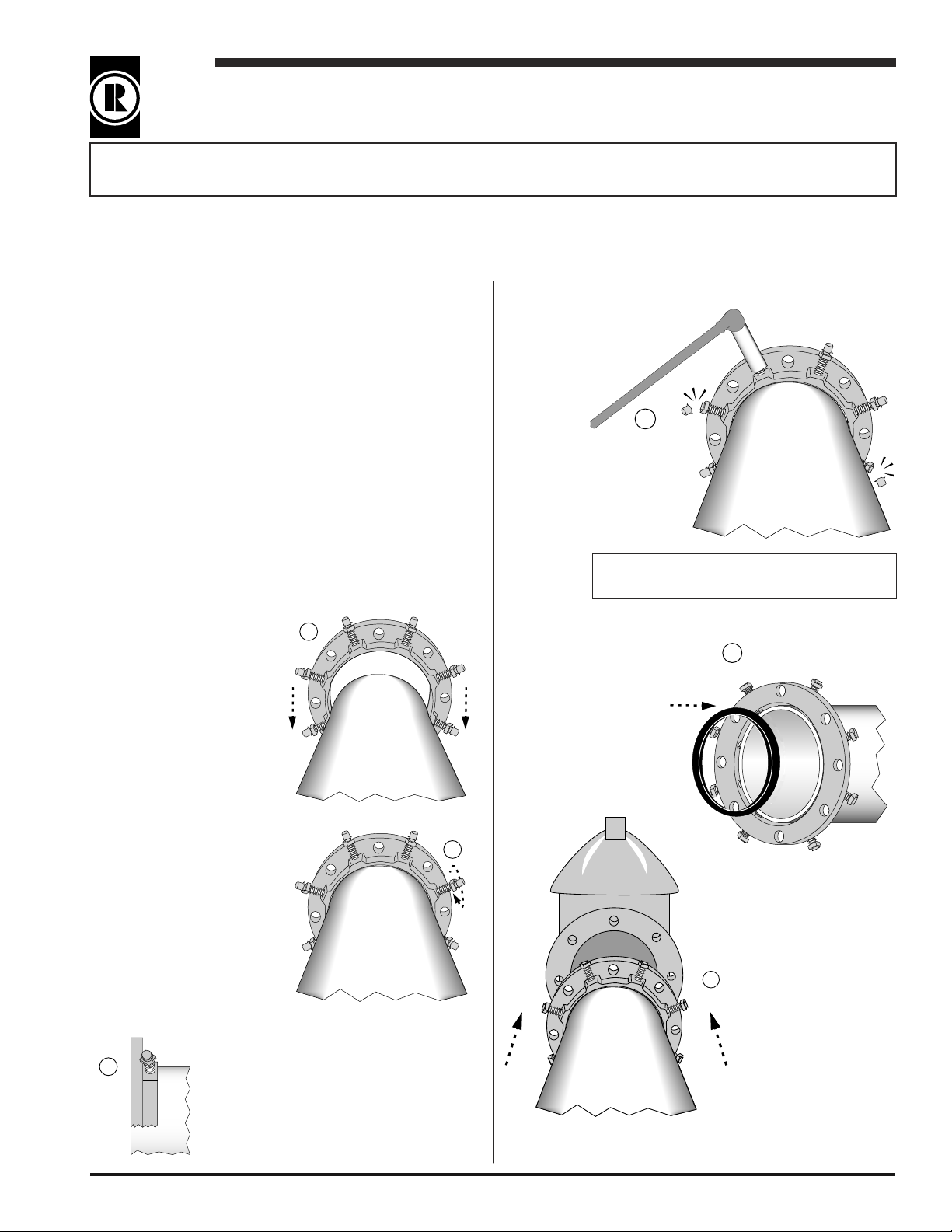
INSTALLATION INSTRUCTIONS
Read installation instructions rst before installing. Check parts to ensure that no damage has occurred during transit and that no parts
are missing. Also check the diameter of the pipe and the range marked on the restrainer to ensure you have the proper size.
Romac Field Flange
NOTE: Not for use on plain end mechanical joint ttings or Class 50 ductile iron pipe.
Step 1 • Check the parts to insure that no damage has
occurred during transit and that no parts are missing.
Step 2 • Cut pipe to length. Pipe must be cut square and
clean.
Step 3 • Clean pipe end for a distance of at least 2" past
where the ange will sit.
Step 4 • Check area where gasket will seat to make sure
there are no dents projections, gouges, etc., that will interfere
with the gasket seal.
Step 5 • Slip ange over
end of pipe.
Step 8 • Tighten pins
evenly, checking to be sure
that even gap between
pipe and ange
is maintained.
Continue until
80-85 ftlbs. torque
is reached or
until the pin heads break off
above the notch.
Note:
85 ft-lbs. torque = 12" wrench w/85 lbs. force
Step 9 • Clean and
lubricate gasket. Stretch
gasket over pipe end with
beveled edge pressed
rmly into Field Flange.
Step 6 • Tighten pins so
that they are touching the
pipe all around. Inspect to
make sure that any gap between pipe and ange is even
all the way around the pipe.
Document #05-9-FF-0003 05/05/03
21919 20th Avenue SE • Suite 100 • Bothell, WA 98021 • Phone (425) 951-6200 • 1-800-426-9341 • Fax (425) 951-6201
Step 7 • Tap ange into place. Face
of the ange should be ush with the
end of the pipe.
Step 10 • Bolt Field Flange
to mating ange.
Step 11 • Pressure test for leaks before backlling.
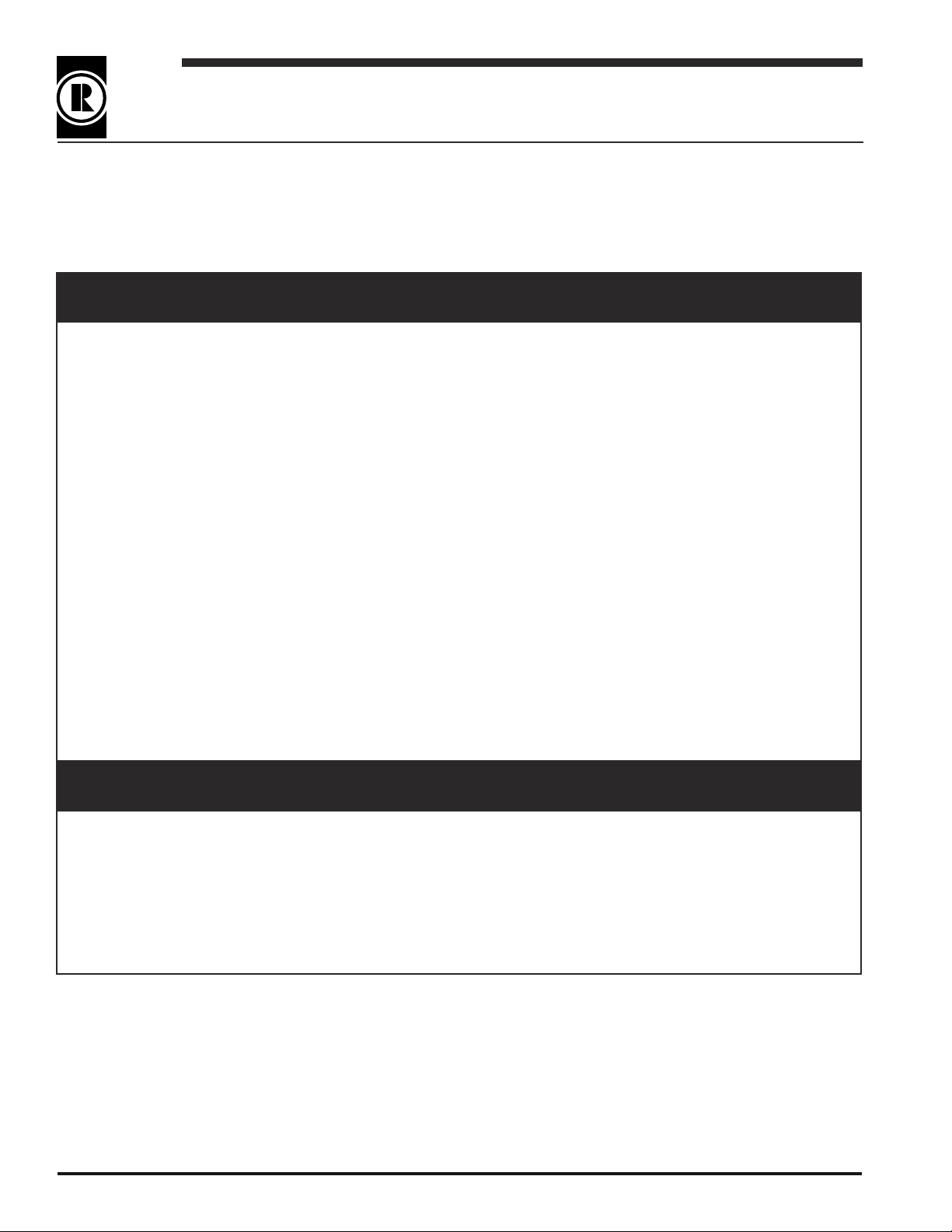
INSTALLATION INSTRUCTIONS
Romac Field Flange
PRECAUTIONS:
1. Check diameter of pipe to make sure you are using the correct size Field Flange; also check gasket
to make sure it is the size you think it is.
2. Be sure to clean pipe of as much dirt and corrosion as possible in the area that the gasket will
seal.
3. Lubricate both the gasket and the pipe end with soapy water or approved pipe lubricant per ANSI/
AWWA C11 1/A21.11.
4. Make sure no foreign materials lodge between gasket and pipe.
5. Avoid loose tting wrenches, or wrenches too short to achieve proper torque.
6. Keep threads free of foreign material to allow proper tightening.
7. Take extra care to follow proper bolt tightening procedures and torque recommendations. Bolts are
often not tightened enough when a torque wrench is not used.
8. Be sure that the ange is centered around the pipe.
9. Pressure test for leaks before backlling.
10. Backll and compact carefully around pipe and ttings.
COMMON INSTALLATION PROBLEMS:
1. Bolts are not tightened to the proper torque.
2. Rocks or debris between pipe and gasket.
3. Dirt on threads of bolts or nuts.
4. Pipe is not cut square.
5. Flange face not even with pipe end.
21919 20th Avenue SE • Suite 100 • Bothell, WA 98021 • Phone (425) 951-6200 • 1-800-426-9341 • Fax (425) 951-6201