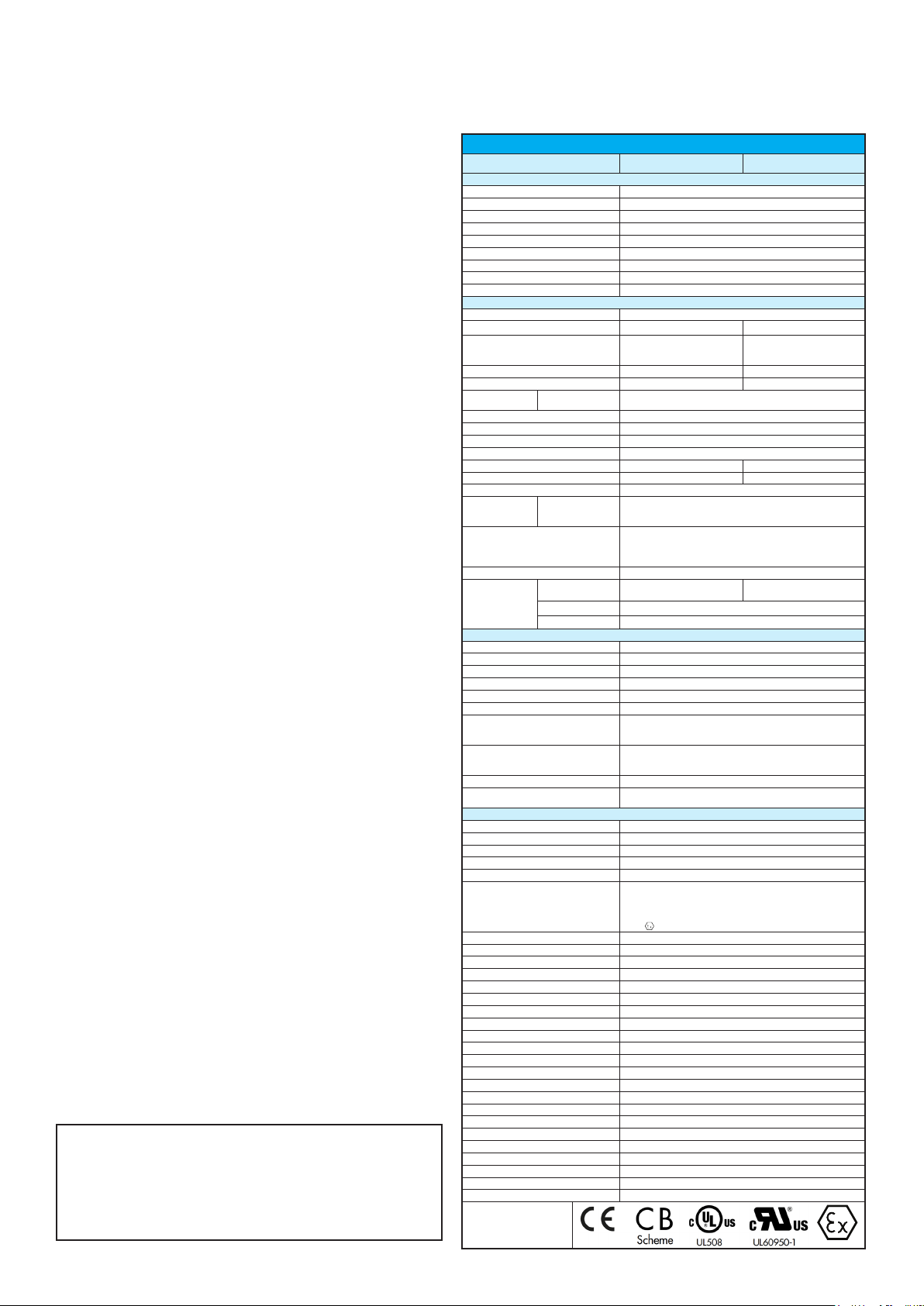
RHINO PSH-xx-480 Power Supplies
Installation Instructions
READ INSTRUCTIONS BEFORE INSTALLING OR OPERATING
THIS DEVICE. KEEP FOR FUTURE REFERENCE.
Safety Instructions and Warnings
• Do not open the device!
• Before any installation or maintenance, ensure that the main
switch is switched off and prevented from being switched on
again.
• The device must be installed and put into service by qualified
personnel only.
• Never work on the device if power is applied.
• Risk of electric arcs and electrical shock, which can cause death,
severe personal injury or substantial property damage.
• The unit must be connected to the mains supply in compliance
with national regulations (e.g., VDE0100 and EN50178). All wire
strands must be fastened in the terminal blocks. (Potential danger
of contact with the case.)
• All input and output wires must be properly rated for the power
supply and must be connected with the correct polarity (Fig. 3).
• The Power Supply wiring must be sufficiently fused.
• Sufficient cooling must be ensured (Fig. 2).
• Do not introduce any objects into the device.
• The output voltage adjustment potentiometer may only be
actuated using an insulated screwdriver.
• Keep away from fire and water.
• The internal fuse is not accessible. If this internal fuse has blown,
the power supply has an internal defect and, for safety reasons,
must be replaced.
• This device is designed for use in a clean, dry environment.
• The device must be mounted in an enclosure in the end
application and must not be accessible in operation.
Installation Instructions
• The device can be mounted onto 35mm DIN rails, compliant with
the specifications of DIN EN 50022. Observe the requirements for
ventilation space above and below the device (Fig. 2).
• The standard mounting orientation is with input terminals at the
bottom.
• Alternative side-mounting for flat panels: The case offers the
potentially useful feature to fix the DIN-rail clip to the side wall to
mount inside flat panels.
Recycling
• The device contains elements that are suitable for recycling,
and components that need special disposal. You are therefore
requested to make sure that the device will be recycled at the
end of its service life.
Notes for Technical Specifications Table:
1. Output voltage can be adjusted as indicated. However, output power has to be maintained at nominal value. This
means the output nominal current has to be reduced in accordance with the increase of output voltage.
2. In case of an internal error, a second voltage regulation loop keeps the output voltage at a safe level, and the power
supply turns off and restarts after 10 seconds.
3. When external voltage is supplied above set output voltage and below OVP threshold, the power supply will function
normally without switch off or destruction, even if external voltage is applied continuously.
4. In case of overload or short circuit, the unit switches the output voltage off after 4 seconds and tries to restart every
10 seconds.
1st Edition Rev. B, 05/08/2020
Technical Specifications
Input (AC)
Nominal Input Voltage 100–240 VAC
Nominal Input Current 5.8–2.5 A
Operational Input Voltage Range 85–264 VAC
Input Voltage Frequency Range 45–65 Hz
Inrush Current (115/230 VAC) 15/30 A
Standby Power Consumption 4.8/3.8 W (115/230 VAC)
Active Power Factor Correction (PFC) 0.99/0.97 (115/230 VAC)
Harmonic limits – acc. EN 61000-3-2 Class A, D
Circuit Breaker Rating / Characteristic 6-16 A /B, C (IEC); 20 A /B, C (USA)
Output (DC)
Max. Output Power 480W
Output Voltage 24V 48V
Max. Output Current / Max. Output Current 4s
("Boost power" which facilitates the activation of
stepper motors, solenoids or actuators)
Output Voltage Adjustment Range 23.5–28 V 47.5–56 V
Typical Efficiency (230 VAC) 95% 95%
Regulation
Output Power Derating - Temperature 2%/K above 60°C, refer to Fig. 5
Output Power Derating - Input Voltage 3%/V below 90 VAC, refer to Fig. 4
Hold-up time 20 ms min.
Start-up time 2s max.
Ripple and Noise (20MHz bandwidth) (Note 1) 100 mVp-p max. 200 mVp-p max.
Output Overvoltage Protection (OVP) (Note 2) 32–35V 56–60V
Power Back Immunity (Note 3) < OVP level
Operation
Duty Cycle (for peak and cc mode) (Note 4)
Threshold
CC or Peak Operation Timer
Normal Operation / Off Period
Short Circuit Protection Switch off after 4s delay, automatic restart (Note 4)
DC OK Signal
General Data
Weight 1018g [35.91 oz]
Leakage Current (max.) 2.3 mA
Network Configuration TN-S, TN-C, TT, IT
Enclosure Material (Chassis/Cover) Aluminum / Stainless Steel
Cooling Convection cooling, no internal fan
Over Temperature Protection Switch off at over temperature
Isolation Voltage
Creepage Clearance
Remote On/Off The unit can be controlled by external relay contact or open collector signal.
Contact Rating
Safety / Environmental
Surrounding Ambient Temperature Range -40°C to +70°C [-40°F to +158°F]
Temperature Coefficient 0.02 %/K
Humidity 5–95%, non-condensing
Storage Temperature -40°C to +85°C [-40°F to +185°F]
Maximum Altitude 2000m
Safety Standards
MTBF (acc. to IEC 61709 at 25°C) > 1,000,000 hrs
Protection Class Class I
Degree of Protection IP20
Electromagnetic compatibility (EMC)
Emissions EN 61000-6-3, EN 61204-3
Conducted RI Suppression On Input EN 55032, EN 55011 class B,
Radiated RI Suppression EN 55032, EN 55011 class B,
Immunity EN 61000-6-2, EN 61204-3
Railway Applications Signaling Apparatus EN 50121-4
Railway Applications Rolling Stock Apparatus
Electrostatic Discharge (ESD) IEC/EN 61000-4-2 4 kV/8 kV , criteria A
Radiated RF Field Immunity IEC/EN 61000-4-3 10 V/m , criteria A
Electrical Fast Transient / Burst Immunity IEC/EN 61000-4-4 2 kV , criteria B
Surge Immunity IEC/EN 61000-4-5 1 kV/2 kV , criteria B
Immunity To Conducted RF Disturbances IEC/EN 61000-4-6 10 V , criteria A
Power Frequency Field Immunity IEC/EN 61000-4-8 30 A/m , criteria A
Mains Voltage Dips And Interruptions IEC/EN 61000-4-11 criteria B/C
Voltage Sag Immunity SEMI F47 230VAC, criteria B/C
Environment
Railway Applications Shock and Vibration According EN 61373
Vibration Acc. IEC 60068-2-6-3 3 axis, 2 g sine sweep, 10–55 Hz, 11 oct/min
Shock Acc. IEC 60068-2-27 3 axis, 25 g half sine, 11ms
Approvals
Input Variation
Load Variation
Nominal Operation
Peak Power Operation
Constant Current (CC)
Threshold for Vout
DC ON Relay contact closed, max. 1A, < 100mOhm, also indicated by green LED
DC OFF Relay contact open, max 30V
PSH-24-480 PSH-48-480
20A 10A
0.1 % max.
(10–90 %) 0.5 % max.
100% of Iout nominal
105–150% of Iout nominal
155% of Iout nominal
> 105 %
4s max. (switch off)
< 10s typ (automatic restart after switch off or peak and cc operation timer reset)
ON: > 22.5 V typ.
OFF: < 21.5 V typ.
Input/Output 4250VDC
Input/Chassis 1500VDC
Output/Chassis 750VDC
Input/Output 8mm
Input/Chassis 4mm
Output/Chassis 1.5 mm
Open: 15V; leakage current max 100μA
Close: 0.3 V; max drop at 15mA
Information technology equipment IEC/EN 60950-1, UL 60950-1
CSA 22.2 No 60950-1-03, File E198298
Safety low voltage switchgear and controlgear UL 508, File E197592
Process Control Equipment Haz Loc, File E502478
ATEX II 3 G Ex ec nC IIC T4 Gcw
EN 50121-3-2
ON: > 45V typ.
OFF: < 43V typ.
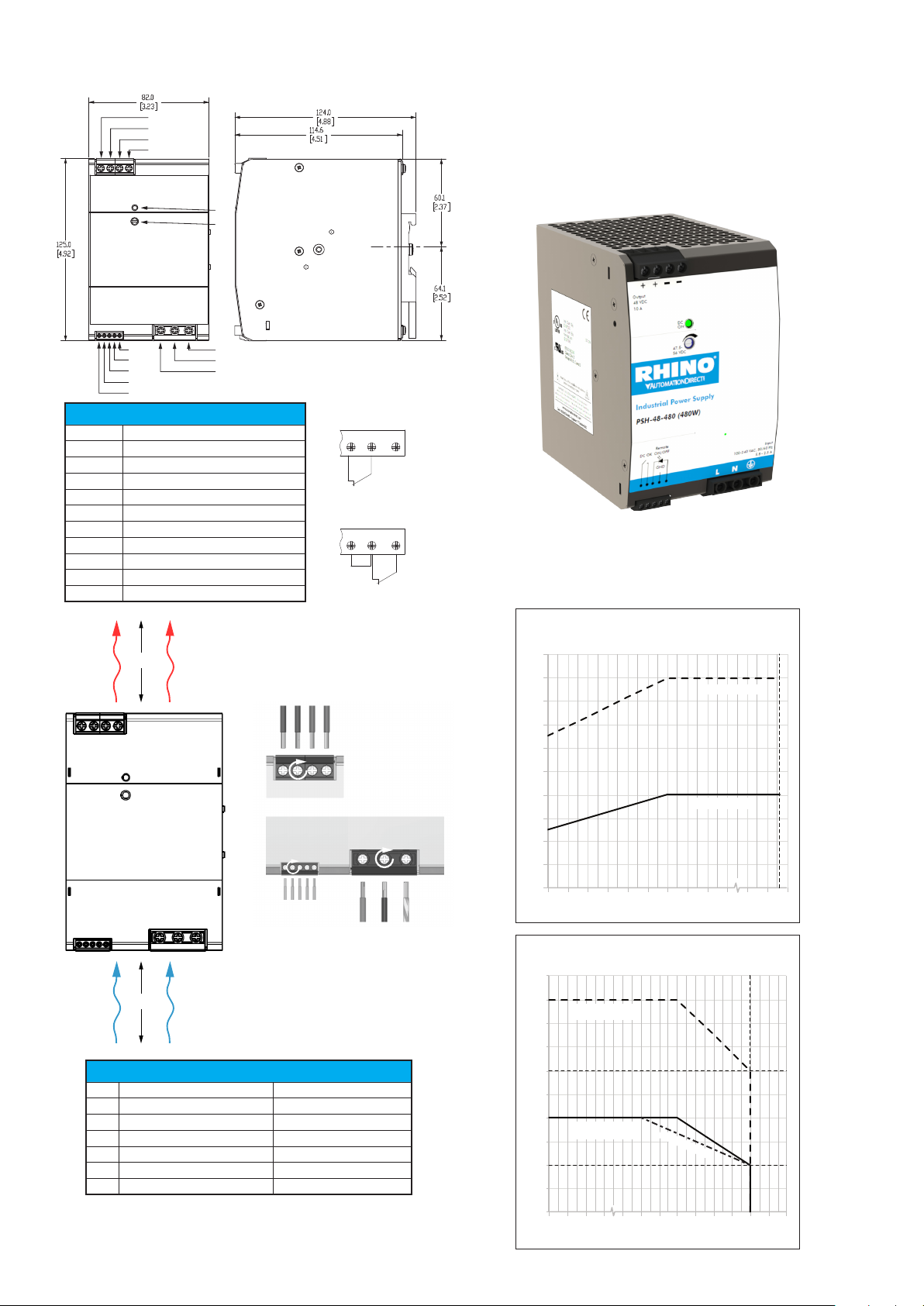
-40 -35 55 60 65 70 75
4 seconds
Continuous
60
70
80
90
100
110
120
130
140
150
160
T
(amb)
[°C]
P
(O/P)
- T
(amb)
P/Pmax
[%]
Fig. 5
PSH-48-480
Fig. 1
14
13
12
11
5
4
RHINO PSH-xx-480
Power Supplies
10
9
8
7
6
3
2
1
Identification of Features (Fig.1)
1
Input Terminal L
2
Input Terminal N
3
Input Terminal GND
4 Output Voltage adjustment potentiometer
5 DC ON LED
6/7 DC OK Contact
8–10 Remote On/Off
11
Output Connection Terminal –
12
Output Connection Terminal –
13
Output Connection Terminal +
14
Output Connection Terminal +
50mm
A
D
SIGNALS INPUT
Units: mm [in]
Remote On/Off
Normal operation
8
10
9
ON = open
OFF = closed
Reversed operation
8
10
9
ON = closed
OFF = open
(O/P)
(I/P)
[%]
Fig. 3Fig. 2
OUTPUT
F
G
E
C
F
D
B
160
150
140
130
120
110
100
4 seconds
90
80
70
60
85
90 95 100 105
(I/P)
Continuous
50mm
Wiring Specifications (see Fig. 3)
A Wire Size, Output 12–10 AWG
B Wire Size, Input 18–10 AWG
C Wire Size, Signal 30–16 AWG
D Strip Length, Input/Output 10mm [0.39 in]
E Strip Length, Signal 5mm [0.20 in]
F Tightening Torque, Input/Output 0.7 N·m [6.2 lb·in]
G Tightening Torque, Signal 0.2 N·m [1.8 lb·in]
FOR TECHNICAL ASSISTANCE CALL 770-844-4200
1st Edition Rev. B, 05/08/2020