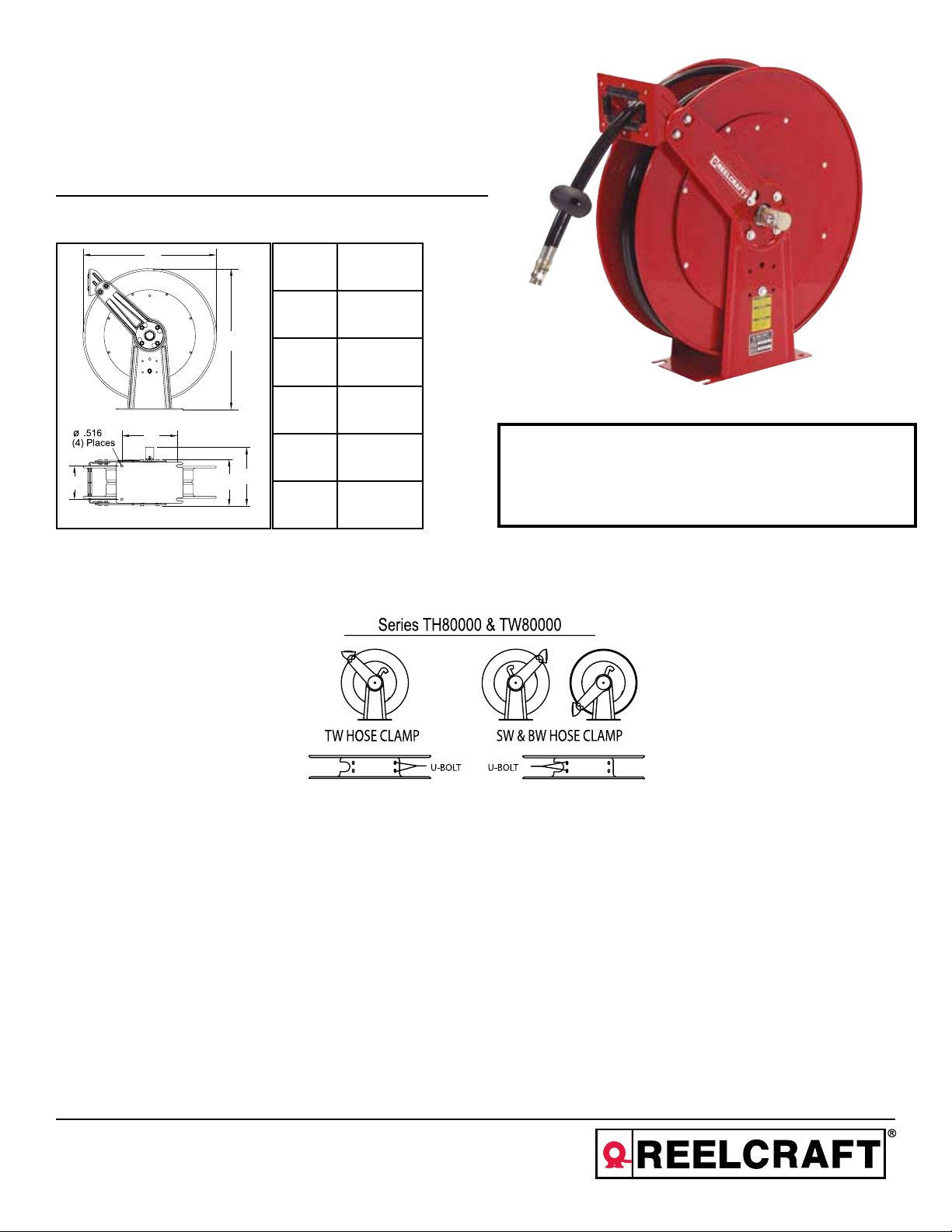
Operating Instructions
Series TH80000 Spring Driven Hose Reels
TH86050 OMP TH86000 OMP
TH88050 OMP TH88000 OMP
Dimensions
B
A
C
E
D
F
A 25 3/8”
B 24”
C 10”
D 6”
E 12 7/8”
F 9 3/8”
IMPORTANT
Read this manual carefully before installing, operating or
servicing this equipment.
Figure A
SAFETY
Personal injury and/or equipment damage may result if proper
safety precautions are not observed.
• Ensure that reel is properly installed before connecting input and
output hoses.
• Bleed fluid/gas pressure from system before servicing reel.
• Before connecting reel to supply line, ensure that pressure does
not exceed maximum working pressure rating of reel.
• Remember, even low pressure is very dangerous and can cause
personal injury or death.
• Be aware of machinery and personnel in work area.
• If a leak occurs in the hose or reel, remove system pressure
immediately.
• A high tension spring assembly is contained within the reel.
Exercise extreme caution.
• Pull hose from reel by grasping the hose itself, not the control
valve.
• If reel ceases to unwind or rewind, remove system pressure
immediately. Do not pull or jerk on hose!
• Treat and respect the hose reel as any other piece of machinery,
observing all common safety practices.
Reelcraft Industries, Inc. • 2842 E Business Hwy 30, Columbia City, IN 46725
Ph: 800-444-3134 / 260-248-8188 • Fax: 800-444-4587 / 260-248-2605
Customer Service: 855-634-9109 • reelcraft@reelcraft.com • www.reelcraft.com
Form# 964-998 Rev: 5/2013
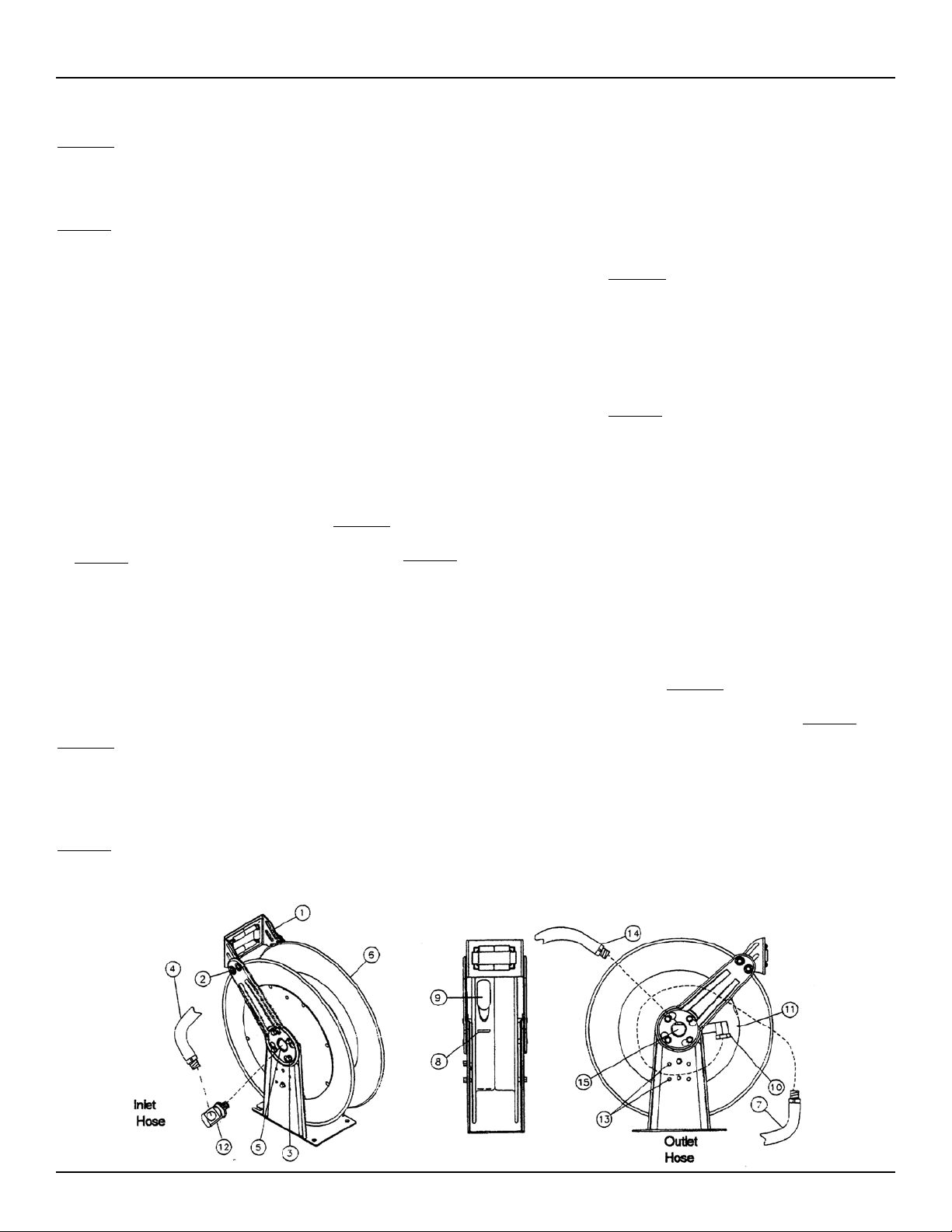
Series TH80000 Spring Driven Hose Reels
INSTALLATION INSTRUCTIONS
Warning: Ensure that reel, hose, and
equipment are properly grounded. Use an
ohmmeter to check ground continuity.
MOUNTING
Caution: Unless reel was specified
differently when ordering, maximum
installation height is 16 feet. Do not
exceed this distance.
Maximum Operating Temperature:
Low pressure (300 PSI) = 150°F (66°C)
Medium pressure (3000 PSI) = 210°F (99°C)
High pressure (4800 PSI) = 210°F (99°C)
1. Unpack and inspect reel for damage.
Turn by hand to check for smooth
operation. Check for completeness.
2. Configure reel for top, side or
bottom-wind hose dispensing by
removing bolts (2) from one side of
the guide roller bracket and loosening
the four guide arm bolts (3) on each
side of the hose reel. Rotate and
remove each guide arm then reinstall
in the desired configuration.
Caution: When changing guide arm
positions, the U-bolt must be placed in
the proper location as instructed in
figure A on page 1. The reel can
“latch out” during use if this
instruction is not adhered to.
3. Position reel on floor, wall, or ceiling.
Secure into place using four (customer
supplied) bolts.
INSTALLING THE INPUT HOSE(S)
Warning: Ensure that supply line pressure
does not exceed maximum working pressure
rating of reel. Apply pipe thread sealant where
applicable to all threads on standard reels. Do
not overtighten connection. Recommended
torque not to exceed 70 ft. lb.
Caution: Use flexible hose connection at
input. Do not use rigid plumbing.
For twin hydraulic reels:
1. Apply thread sealant as directed and
connect swivels (12 and 15) to main
shaft inputs (5) on opposite sides of
the reel.
2. Connect customer supplied supply
line hose (4) to swivel input (15) as
indicated in illustration. Note that the
supply line and return line hoses can
be switched as long as caution is
taken when installing output hoses;
paying attention to hook -up locations
on goosenecks.
3. Thread sealant is not recommended
on swivel union fittings.
For single line high pressure reels:
1. Apply thread sealant as directed and
connect swivel (12 ) to main shaft
input (5).
2. Connect customer supplied input
hose (4) to swivel input (12).
INSTALLING THE OUTPUT HOSE(S)
Warning: Use extreme caution; reel
under tension. Avoid releasing latch
mechanism. Caution: Apply pipe thread
sealant where applicable to all threads on
standard reels. Do not overtighten connection.
Recommended torque not to exceed 70 ft. lb.
1. Manually turn sheave (6) until spring
is tight, back off 3 turns, then latch.
2. Route output hose(s) (7) through
roller bracket (1), U-bolts (8),
then through cutout (9) in spool as
indicated in illustration.
3. Connect output hose/s (7) to
gooseneck (10) paying special
attention to which gooseneck should
be used depending on application.
4. Verify U-bolt position conforms with
guide arm position using label inside
spool. Then tighten nuts (11) on
U-bolt (8).
5. Charge hoses. Momentarily open
control valve to purge hose of gases.
When fluid appears at control valve,
close valve. With hose fully charged,
release latch and wind output hose/s
onto reel.
6. Install hose bumper assembly.
ADJUSTMENTS
Warning: Use extreme caution; reel
under tension. Avoid releasing latch
mechanism. If necessary, adjust spring
tension on reel by adding or removing
wraps of hose from spool, one wrap at a
time, until desired tension is obtained. Add
wraps to increase tension. Remove wraps to
decrease tension.
Caution: When adding wraps of hose, add
just enough wraps to achieve the desired
tension without exceeding the winding mechanism’s spring capacity. Properly tensioned
reels allow all hose to be freely removed from
the spool until the point of U-bolt contact.
Damage to the winding mechanism will result
if spring is over-tensioned.
SERVICE INSTRUCTIONS
User servicing of the reel is limited to
replacing input/output hoses only. Refer all
other repairs to an authorized service
person or directly to Reelcraft. Failure to
do so can result in personal injury and/or
equipment damage and may void the
warranty. Warning: Rewind hose on reel,
then bleed pressure from system before performing the following procedures. Caution:
Remove all spring tension before disassembling the hose reel. Do not attempt to open
the riveted spring case assembly.
1. Replace hoses in accordance with
procedures given in “Installation
Instructions” section of this manual.
2. All mating moving parts have been
factory lubricated as required.
Page 2
www.reelcraft.com
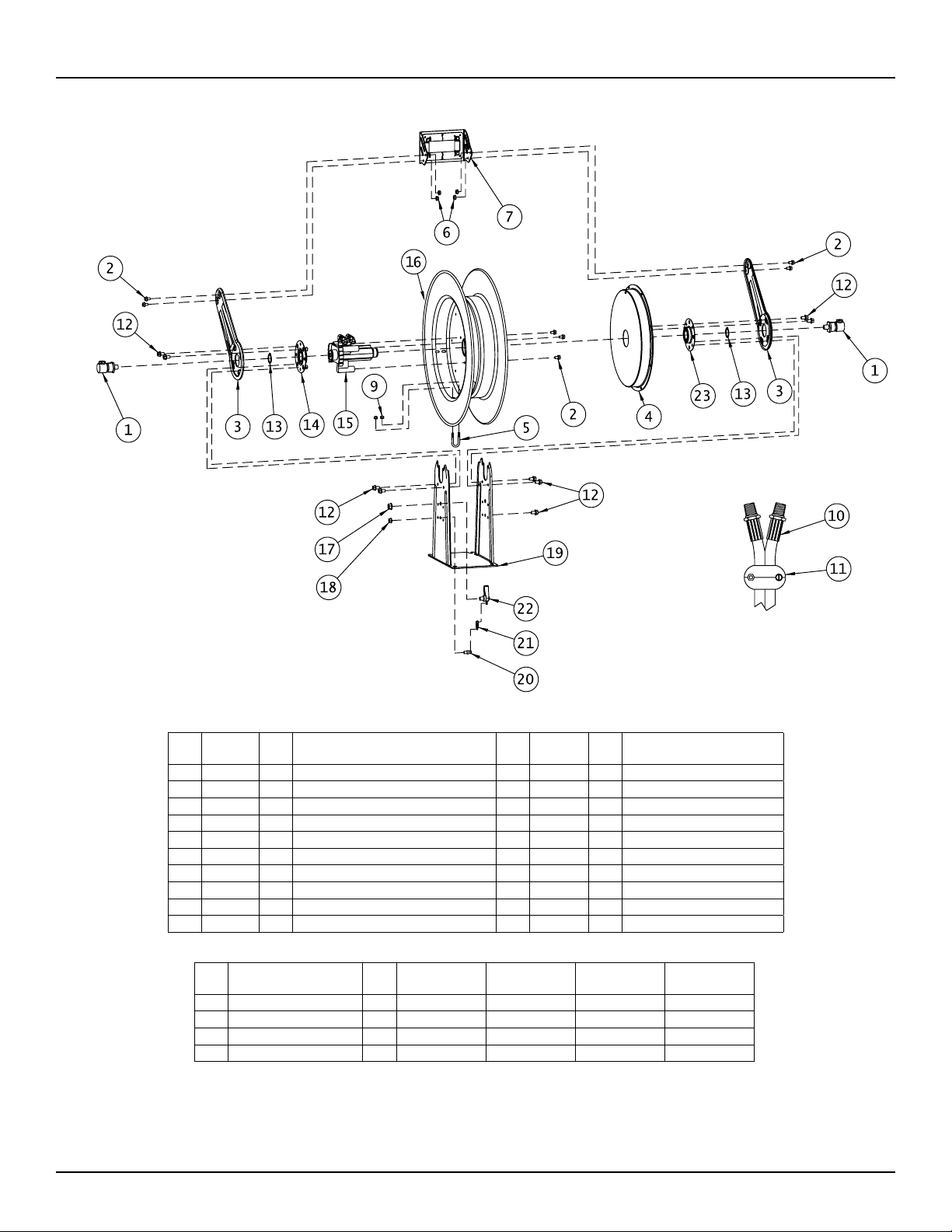
Series TH80000 Spring Driven Hose Reels
www.reelcraft.com
Item
#
Part #
#
Req.
Description
Item
#
Part #
#
Req.
Description
2 * 7 5/16-18 x 1/2” flange screw 16 600649 1 Sheave assembly
3 261299 2 Guide arm 17 * 1 1/2-20 x 5/8” hex nut
4 S600645-2 1 Spring and case assembly 18 * 1 3/8-16 hex nut **
5 * 1 U-bolt 18 * 1 10-32 Nyloc nut
6 * 4 5/16-18 locknut 19 600641 1 Base and upright assembly
7 S600642 1 Roller bracket assembly 20 261351 1 Latch spring stud **
9 * 2 1/4-20 locknut 20 S393-2 1 Shoulder screw
12 * 9 3/8-16 x 5/8” screw 21 S260067 1 Latch spring
13 * 2 1 3/8” snap ring 22 S600675 1 Latch pawl assembly
14 S600651 1 Flange w/bearing and nut sert assembly 23 S600644 1 Bearing and flange assembly
Item
#
Description
#
TH88000 OMP TH88050 OMP TH86000 OMP TH86050 OMP
Req.
1 Swivel assembly 1-2 S602033 S602033 600668 S600608
10 Hose assembly 1 None 600669-1 None 600670-1
11 Hose bumper assembly 1 None 600522 None 600521
15 Ratchet, flow casting 1 600667-1 600667-1 600667-2 600667-2
*Included in hardware kit part #600654
**Prior to March 2012
Page 3