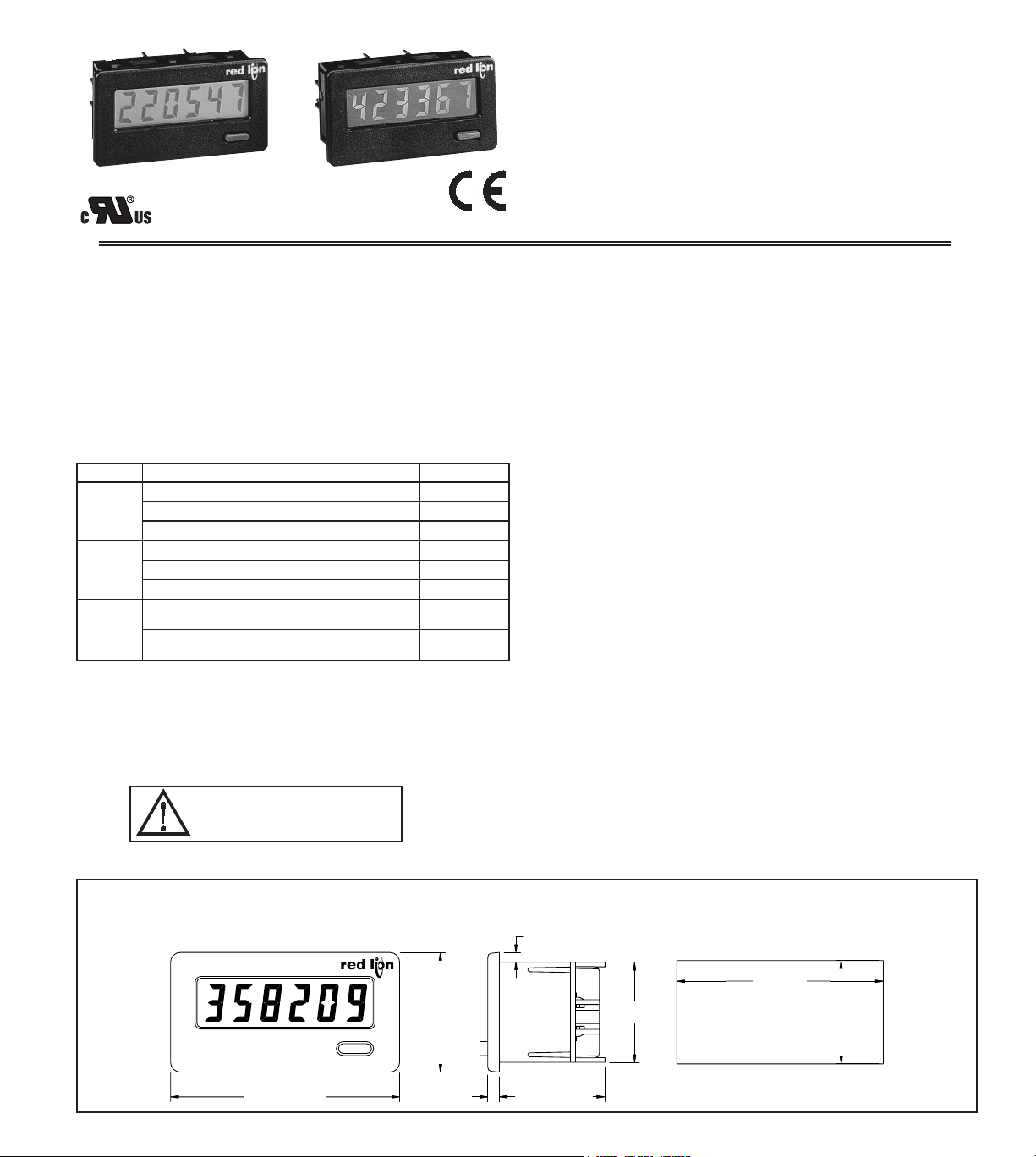
MODEL CUB4L & CUB4L8 - MINIATURE ELECTRONIC COUNTERS
LCD, POSITIVE REFLECTIVE OR NEGATIVE TRANSMISSIVE
WITH YELLOW/GREEN OR RED LED BACKLIGHTING
INTERNAL LITHIUM BATTERY PROVIDES UP TO 6 YEARS OF
UNINTERRUPTED OPERATION
NEMA 4X/IP65 SEALED FRONT BEZEL
FRONT PANEL RESET, REMOTE RESET, OR BOTH
COUNT SPEEDS UP TO 5 KHz
WIRE CONNECTION MADE VIA SCREW CLAMP TYPE
TERMINALS
DESCRIPTION
The CUB4 offers a large display in a miniature package with a choice of three
displays; reflective, red backlight or green backlight.
The backlight versions require power from an external 9–28 VDC supply. The
optional power supply (MLPS) is designed to be attached directly to the rear of
the CUB4 and is powered from an 85–250 VAC source.
The CUB4 series has a lightweight, high impact plastic case with a clear
viewing window. The sealed front panel with the silicone rubber reset button
meets NEMA 4X/IP65 specifications for wash-down and/or dusty environments,
when properly installed.
ORDERING INFORMATION
MODEL NO. DESCRIPTION PART NUMBERS
CUB4L
(6-digit)
CUB4L8
(8-digit)
MLPS
Counter Positive Image Reflective CUB4L000
Counter w/Yel-Grn Backlighting CUB4L010
Counter w/Red Backlighting CUB4L020
Counter Positive Image Reflective CUB4L800
Counter w/Yel-Grn Backlighting CUB4L810
Counter w/Red Backlighting CUB4L820
+12 VDC Micro-Line Power Supply, 85 to 250 VAC
source, 400 mA max out
+24 VDC Micro-Line Power Supply, 85 to 250 VAC
source, 200 mA max out
MLPS1000
MLPS2000
SAFETY SUMMARY
All safety related regulations, local codes and instructions that appear in the
manual or on equipment must be observed to ensure personal safety and to
prevent damage to either the instrument or equipment connected to it. If
equipment is used in a manner not specified by the manufacturer, the protection
provided by the equipment may be impaired.
CAUTION: Risk of Danger.
Read complete instructions prior to
installation and operation of the unit.
SPECIFICATIONS
1. DISPLAY:
CUB4L: 6-Digit, LCD, 0.48" (12.2 mm) high digits.
CUB4L8: 8-Digit, LCD, 0.46" (11.7 mm) high digits.
2. POWER SOURCE: Internal 3.6 V lithium battery will provide up to 6 years
of continuous operation (high speed counting and extreme temperatures will
decrease battery life).
3. BACKLIGHT POWER REQUIREMENTS: 9 to 28 VDC, 30 mA typical,
50 mA max. Above 26 VDC, derate operating temperature to 50°C.
Must use an RLC model MLPS or an NEC Class 2 or Limited Power Source
(LPS) rated power supply.
4. COUNT INPUT:
SNK mode (DIP switch 1 off, internal pull-up to battery)
VIN High Min = 1.25 VDC; VIN Low Max = 0.45 VDC
IIN Max = 5 µA; VIN Max = 3.6 VDC
Count Speed: (count on negative edge)
High freq mode (DIP switch 2 off): max 5 kHz @ 50% duty cycle
Low freq mode (DIP switch 2 on): max 50 Hz @ 50% duty cycle
SRC mode (DIP switch 1 on, internal 20 kW pull-down to common)
VIN High Min = 1.25 VDC; VIN Low Max = 0.45 VDC
IIN Max = 5 mA; VIN Max = 28 VDC
Count Speed: (count on negative edge)
High freq mode (DIP switch 2 off): max 5 kHz @ 50% duty cycle
Low freq mode (DIP switch 2 on): max 50 Hz @ 50% duty cycle
5. RESET INPUT:
VIN Low Max = 1.5 VDC (internal pull-up to battery)
IIN Max = 20 µA
5 msec min (active low for count reset to zero)
6. ENVIRONMENTAL CONDITIONS:
Operating Temperature: 0 to 60°C (above 50°C, derate backlight operating
voltage to 26 VDC max.).
Storage Temperature: -30 to 85°C
Operating and Storage Humidity: 85% max. (non-condensing) from 0°C
to 50°C.
Vibration to IEC 68-2-6: 5 to 500 Hz, 5 g.
Shock to IEC 68-2-27: Operational 30 g.
Altitude: Up to 2000 meters
DIMENSIONS In inches (mm)
2.95 (74.9)
Note: Recommended minimum clearance (behind the panel) for mounting clip
installation is 2.15" (54.6) H x 3.00" (76.2) W.
0.13 (3.2)
1.54 (39.1) 1.29 (32.8)
0.15 (3.8)
1.36 (34.5)
PANEL CUT-OUT
+.025
2.68
-.000
+.6
(68 )
-.0
1
1.30
(33 )
+.6
+.024
-.0
-.000
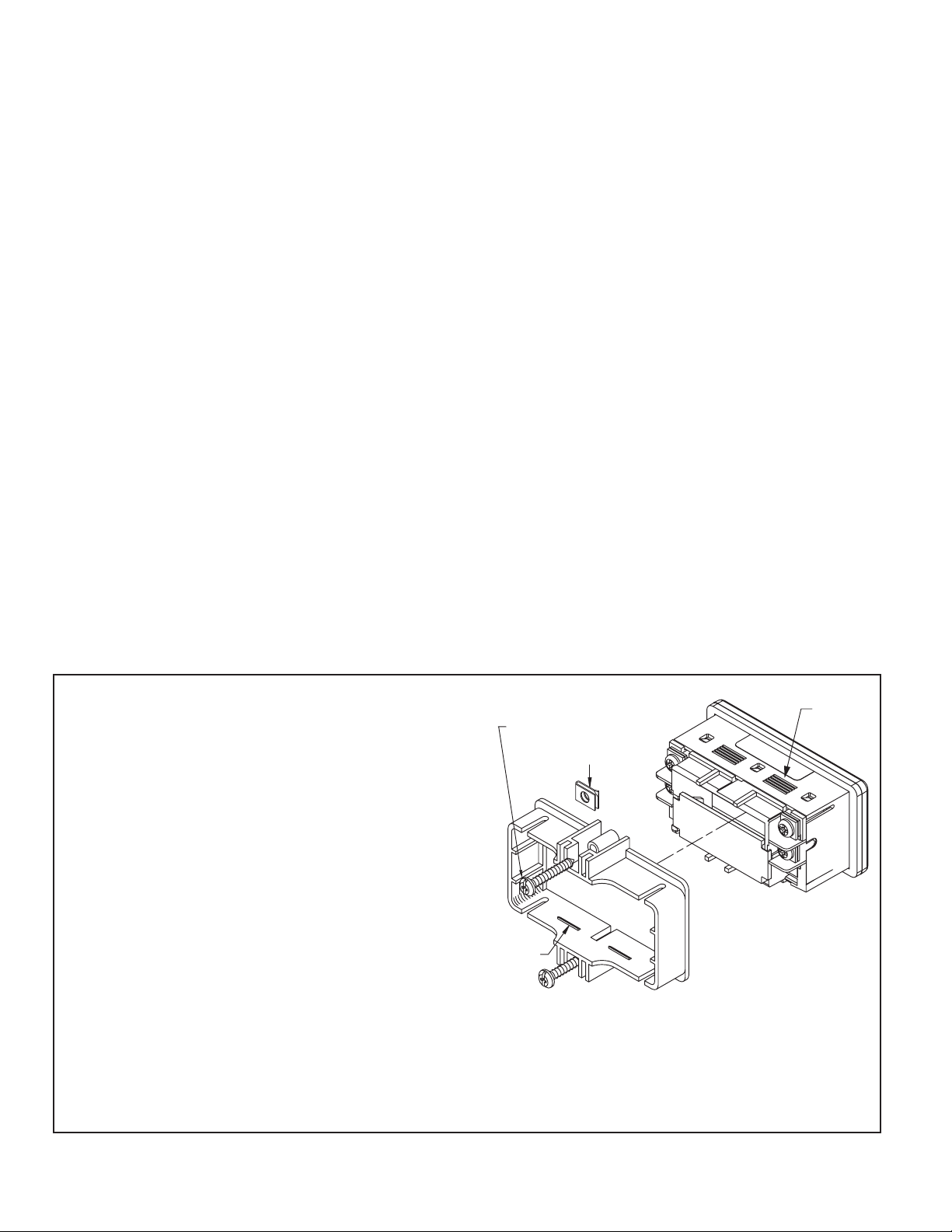
7. CERTIFICATIONS AND COMPLIANCES:
CE Approved
EN 61326-1 Immunity to Industrial Locations
Emission CISPR 11 Class B
IEC/EN 61010-1
RoHS Compliant
UL Recognized Component: File #E179259
Type 4X Indoor Enclosure rating (Face only)
IP65 Enclosure rating (Face only)
Refer to EMC Installation Guidelines section of the bulletin for additional
information.
8. CONSTRUCTION:
This unit is rated for NEMA 4X/IP65 indoor use. Installation Category I,
Pollution Degree 2
9. WEIGHT: 3 oz. (85 grams)
EMC INSTALLATION GUIDELINES
Although Red Lion Controls Products are designed with a high degree of
immunity to Electromagnetic Interference (EMI), proper installation and wiring
methods must be followed to ensure compatibility in each application. The type
of the electrical noise, source or coupling method into a unit may be different
for various installations. Cable length, routing, and shield termination are very
important and can mean the difference between a successful or troublesome
installation. Listed are some EMI guidelines for a successful installation in an
industrial environment.
1. A unit should be mounted in a metal enclosure, which is properly connected
to protective earth.
2. Use shielded cables for all Signal and Control inputs. The shield connection
should be made as short as possible. The connection point for the shield
depends somewhat upon the application. Listed below are the recommended
methods of connecting the shield, in order of their effectiveness.
a. Connect the shield to earth ground (protective earth) at one end where the
unit is mounted.
b. Connect the shield to earth ground at both ends of the cable, usually when
the noise source frequency is over 1 MHz.
3. Never run Signal or Control cables in the same conduit or raceway with AC
power lines, conductors, feeding motors, solenoids, SCR controls, and
heaters, etc. The cables should be run through metal conduit that is properly
grounded. This is especially useful in applications where cable runs are long
and portable two-way radios are used in close proximity or if the installation
is near a commercial radio transmitter. Also, Signal or Control cables within
an enclosure should be routed as far away as possible from contactors,
control relays, transformers, and other noisy components.
4. Long cable runs are more susceptible to EMI pickup than short cable runs.
5. In extremely high EMI environments, the use of external EMI suppression
devices such as Ferrite Suppression Cores for signal and control cables is
effective. The following EMI suppression devices (or equivalent) are
recommended:
Fair-Rite part number 0443167251 (RLC part number FCOR0000)
Line Filters for input power cables:
Schaffner # FN2010-1/07 (Red Lion Controls # LFIL0000)
6. To protect relay contacts that control inductive loads and to minimize radiated
and conducted noise (EMI), some type of contact protection network is
normally installed across the load, the contacts or both. The most effective
location is across the load.
a. Using a snubber, which is a resistor-capacitor (RC) network or metal oxide
varistor (MOV) across an AC inductive load is very effective at reducing
EMI and increasing relay contact life.
b. If a DC inductive load (such as a DC relay coil) is controlled by a transistor
switch, care must be taken not to exceed the breakdown voltage of the
transistor when the load is switched. One of the most effective ways is to
place a diode across the inductive load. Most RLC products with solid
state outputs have internal zener diode protection. However external diode
protection at the load is always a good design practice to limit EMI.
Although the use of a snubber or varistor could be used.
RLC part numbers: Snubber: SNUB0000
Varistor: ILS11500 or ILS23000
7. Care should be taken when connecting input and output devices to the
instrument. When a separate input and output common is provided, they
should not be mixed. Therefore a sensor common should NOT be connected
to an output common. This would cause EMI on the sensitive input common,
which could affect the instrument’s operation.
Visit RLC’s web site at http://www.redlion.net/Support/InstallationConsiderations.
html for more information on EMI guidelines, Safety and CE issues as they
relate to Red Lion Controls products.
INSTALLATION ENVIRONMENT
The unit should be installed in a location that does not exceed the maximum
operating temperature and provides good air circulation. Placing the unit near
devices that generate excessive heat should be avoided.
The bezel should be cleaned only with a soft cloth and neutral soap product.
Do NOT use solvents. Continuous exposure to direct sunlight may accelerate
the aging process of the bezel.
Do not use tools of any kind (screwdrivers, pens, pencils, etc.) to operate
the keypad of the unit.
Installation
The CUB4 series of products meet NEMA 4X/IP65 requirements for indoor
use, when properly installed. The units are intended to be mounted into an
enclosed panel. The viewing window and reset button are factory sealed for a
washdown environment. A sponge rubber gasket and mounting clip are
provided for sealing the unit in the panel cut-out.
The following procedure assures proper installation:
1. Cut panel opening to specified dimensions. Remove burrs and clean around
panel opening.
2. Carefully remove the center section of the panel gasket and discard.
Slide gasket over rear of the unit to the back of the bezel.
3. Assemble nut fastener first and then mounting screw onto both sides of
mounting clip. Tip of screw should not project from hole in mounting clip.
4. Install CUB4 unit through the panel cut-out until front bezel flange contacts
the panel-mounted gasket.
5. Slide the mounting clip over the rear of the unit until the mounting clip is
against the back of the panel. The mounting clip has latching features which
engage into mating features on the CUB4 housing.
Note: It is necessary to hold the unit in place when sliding mounting clip
into position.
LATCHING
MOUNTING
SCREW
LATCHING
FEATURE
6. Alternately tighten each screw to ensure uniform gasket pressure. Visually
inspect the front panel gasket. The gasket should be compressed about 75 to
80% of its original thickness. (Recommended torque is 28 to 36 in-oz.) If
not, gradually turn mounting screws to further compress gasket.
7. If gasket is not adequately compressed, and mounting screws can no longer
be turned, loosen mounting screws and check that mounting clip is latched
as close as possible to panel.
Repeat procedure for tightening mounting screws.
NUT
FASTENER
FEATURE
2

WIRING CONNECTIONS
The electrical connections are made via rear screw-clamp terminals located
on the back of the unit. When wiring the unit, use the label to identify the wire
position with the proper function. All conductors should meet voltage and
current ratings for each terminal. Also cabling should conform to appropriate
standards of good installation, local codes and regulations. It is recommended
that power supplied to the unit (AC or DC) be protected by a fuse or circuit
breaker. Strip the wire, leaving approximately 1/4" bare wire exposed (stranded
wires should be tinned with solder). Insert the wire into the screw-clamp
terminal and tighten down the screw until the wire is clamped tightly. Each
terminal can accept up to two #14 AWG wires.
Backlight Wiring
Optional backlight versions of the CUB4 require an external 9-28 VDC
power supply. The external supply is connected between the V+ and Common
terminals.
3 RESET
1 COM
CUB4
!
M1406_
_
Backlight Power Supply
COUNT 4
9-28 VDC 2
YORK, PA.
MADE IN U.S.A.
(MLPS)
Warning: Lithium battery may explode if incinerated.
+
COUNT INPUT WIRING
Current Sinking Output
SRC
LO FREQ
KEY ENKEY DIS
ON
*
3
1
2
SNK
HI FREQ
Logic Output
SRC
LO FREQ
KEY ENKEY DIS
ON
*
3
1
2
SNK
HI FREQ
Switch/Contact Sourcing Output
Reset
3
Com
1
Reset
3
Com
1
CNT
9-28VDC
CNT
9-28VDC
Current Sourcing Output
+V
SRC
LO FREQ
KEY ENKEY DIS
ON
*
3
1
4
2
2
SNK
HI FREQ
Switch/Contact Sinking Output
KEY EN
LO FREQ
SRCSNK
ON
*
3
1
4
2
2
KEY DIS
HI FREQ
Reset
3
Com
1
Reset
3
Com
1
CNT
9-28VDC
CNT
9-28VDC
4
2
4
2
ON
SRC
1
SNK
LO FREQ
KEY ENKEY DIS
*
3
2
HI FREQ
+V
Switch position is application dependent.
Reset
3
Com
1
CNT
9-28VDC
4
2
3

SETTING THE DIP SWITCHES
The switches must be positioned appropriately prior to wiring. Placing the
key disable/enable DIP switch in the off position disables the front panel key.
LO FREQHI FREQ
SRCSNK
ON
9-28 VDC 2
YORK, PA.
MADE IN U.S.A.
CUB4L
9-28 VDC 2
YORK, PA.
MADE IN U.S.A.
CUB4L8
COUNT 4
COUNT 4
1
2
1
2
3
3 RESET
1 COM
!
M1406_
3 RESET
1 COM
!
M1406_
CUB4
CUB4
RESETTING THE DISPLAY
The display may be reset to zero via the front RST key, the remote reset input
or both. The front RST key must be enabled for front panel reset by setting DIP
switch # 3 ON. The remote reset is activated via an external momentary contact
closure between the reset input and the common.
KEY ENKEY DIS
TROUBLESHOOTING
For further technical assistance, contact technical support at the appropriate
company numbers listed.
3
ON
SRCSNK
LO FREQHI FREQ
KEY ENKEY DIS
The Company warrants the products it manufactures against defects in materials and workmanship
LIMITED WARRANTY
for a period limited to two years from the date of shipment, provided the products have been stored,
handled, installed, and used under proper conditions. The Company’s liability under this limited
warranty shall extend only to the repair or replacement of a defective product, at The Company’s
option. The Company disclaims all liability for any affirmation, promise or representation with
respect to the products.
The customer agrees to hold Red Lion Controls harmless from, defend, and indemnify RLC against
damages, claims, and expenses arising out of subsequent sales of RLC products or products
containing components manufactured by RLC and based upon personal injuries, deaths, property
damage, lost profits, and other matters which Buyer, its employees, or sub-contractors are or may be
to any extent liable, including without limitation penalties imposed by the Consumer Product Safety
Act (P.L. 92-573) and liability imposed upon any person pursuant to the Magnuson-Moss Warranty
Act (P.L. 93-637), as now in effect or as amended hereafter.
No warranties expressed or implied are created with respect to The Company’s products except
those expressly contained herein. The Customer acknowledges the disclaimers and limitations
contained herein and relies on no other warranties or affirmations.