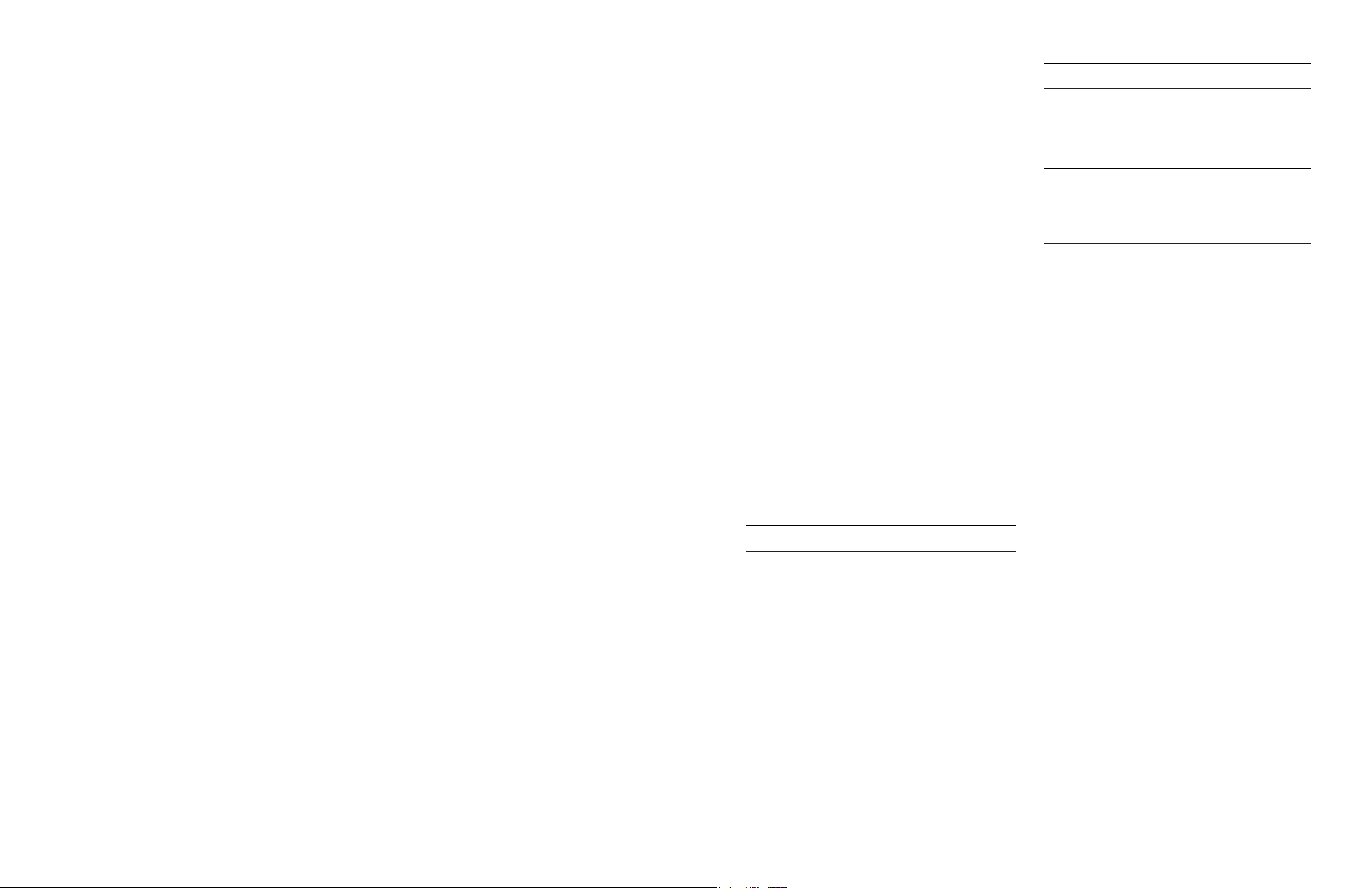
ALIGNMENTS
Presiona la tecla SOUND para
grabar los ajustes que hiciste y para
salir del modo de servicio
ALIGNMENTS (Continued)
Operating Conditions
Unless otherwise noted, the following conditions must be
observed when aligning this chassis:
Chassis must be operated from a 120VAC isolation
transformer, with line voltage set to 120VAC (±2.0V).
Picture controls (color, brightness etc.) must be set to
midrange.
Procedures must be performed in the sequence given.
A 10X probe must be used for oscilloscope and frequency
measurements.
The audio output leads must not be shorted together or to
ground with the chassis on.
All video signals must have -40 IRE sync tips unless
specified otherwise.
Chassis AC power must be removed for 10 seconds before
disconnecting any cable.
A 3-minute warm-up is required for chassis or module
related alignments. A 15-minute warm-up is required for
Kine related alignments.
Required Test Equipment
- Dual-Trace Oscilloscope
- Digital Voltmeter
- Frequency Counter
- Audio Signal Generator
- NTSC Signal Generator (B&K 1249, or equivalent)
- MTS Signal Generator (B&K 2009, or equivalent)
- Sweep/Marker Generator (or Standard Signal Generator)
- DC Power Supply (5.0V/0.25A) for TAG001
Entering the Service mode
1. Enter the service mode (S-Mode) by pressing the VOLUME DOWN key on the instrument until the volume
decreases to minimum.
2. Press the INFO key on the remote handset while holding
the VOLUME DOWN key on the instrument.
3. Press the PROGRAM UP/DOWN buttons to select the
different adjustments under the first menu and press the
VOLUME UP/DOWN buttons to adjust the setting
(value).
5. Press the OK button to toggle into the Main Menu selection mode and select the different Main menu sections
using the PROGRAM UP/DOWN buttons. Press the
OK button again to toggle back into the value adjustment mode.
6. Menus up to menu 19 can be selected directly using the
remote control by pressing digital buttons 1~9, 0, notebook, CAP, Display, Sleep, Calendar, System/INS,
Favourite, Return and Picture.
7. Press the Sound button to save the new settings and exit
the service mode.
Note: Many factory alignments appear in the menus but
only the ones listed here can be changed. The values
can be accessed and the value (hex number) on the
screen can be changed but the actual value the
instrument is using cannot be changed except at the
factory using special equipment.
The following is a list of all the menus and a
description of the individual adjustments under
each Main menu that can be changed. Only the
following menu items can actually be adjusted.
Menu 1 (Remote key: 1)
Item Remark
RC R cut-off setting
GC G cut-off setting
BC B cut-off setting
GD G drive setting
BD B drive setting
Menu 2 (Remote key: 2)
Item Remark
HIGH6 60Hz height
VP60 Vertical position
VLIN6 60Hz Vertical linearity
VSC6 Vertical S correction (60Hz)
Menu 3 (Remote key: 3)
Item Remark
HPOS6 Horizontal position (60Hz)
PARA6 Parabola
TRAP6 Trapazoid
HSIZE Horizontal size
CNRT6 Corners top
CNRB6 Corners bottom
Menu 4 (Remote key: 4)
No adjustments allowed
Menu 5(Remote key: 5)
No adjustments allowed
Menu 6(Remote key: 6 )
No adjustments allowed
Menu 7( Remote key: 7)
No adjustments allowed
Menu 8 (Remote key: 8 )
Item Remark
RFAGC RFAGC [12H, bit 5 ~ 0]
Menu 9 - 24
No adjustments allowed
B+ Adjustment
1. Tune the instrument to receive a crosshatch signal.
2. Set the Preset Picture Mode to normal.
3. Adjust VR802 for 130Vdc +/- 0.5V at C422+ (B+).
RF AGC Adjustment
The RF AGC has been preset at the time of manufacture
for optimum operation over a wide range of RF signal
input conditions. Readjustment should not be required
unless the tuner has been repaired or unusual signal conditions exist such as:
a. Cable TV—adjacent channel interference.
b. Picture bending and/or channel 6 color beats which are
usually due to excessive RF signal input. This occurs
when the receiver location is too close to the transmitting
tower. It may also occur when the receiver is connected
to an antenna distribution system where the RF signal
has been amplified. The signal should be attenuated at
the antenna input to a more satisfactory level.
c. Picture Noise caused by “broadcast noise” or weak sig-
nal. If the broadcast is “clean” and the received signal is
at least 1 mV, the picture will be noise free in any area.
NOTE: Adjustment of the RF AGC parameters may not have
any visible effect except under unusual conditions.
Adjusting the RF AGC to one extreme of it’s
parameter limits will usually provide a relatively
poor signal-to-noise ratio, while adjustment to the
other extreme of it’s parameter limits will cause a
degradation of overload conditions such as channel 6
color beats or Cable TV adjacent channel
interference. Use the weakest local signal to adjust
RF AGC parameter setting (Menu 8). If the RF AGC
parameter setting is adjusted, check all local
channels for proper operation.
Screen Adjustment
Test Point: Observe Display
Adjust: Screen Control Flyback
1. Tune the instrument to receive a crosshatch signal.
2. Set the Picture color temperature to Normal and set all
of the picture controls (brightness, contrast etc.) to
midrange.
3. Enter the Service mode and preset the Menu 1 values to
RC/GC/BC to 80 AND GD/BD to 40.
4. While still in the service mode, press the Input button on
the remote control. This will collapse the vertical.
5. Adjust the screen control to just produce a dim horizontal line on the CRT.
Focus Adjustment
Test Point: Observe Display
Adjust: Focus Control Flyback
1. Tune the instrument to receive a crosshatch signal.
2. Adjust the Focus control for best overall focus.
Color Temperature Adjustment
Test Point: Observe Display
Adjust: Menu 1 RC (Red Cutoff)
Menu 1 GC (Green Cutoff)
Menu 1 BC (Blue Cutoff)
Menu 1 GD (Green Drive)
Menu 1 BD (Blue Drive)
1. Perform the Screen adjustment.
2. Set the Picture color temperature to Normal and set all
of the picture controls (brightness, contrast etc.) to
midrange.
3. Tune the instrument to receive a grayscale stairstep test
pattern.
4. Enter the Service mode and adjust the values for the Cutoff and Drive controls to obtain proper color tracking
(no tinting - only black, white and shades of gray). Correct color temperature is 9300 degrees - X=284 Y=299.
5. Check the low light to high light gray scale tracking (black
and white picture). Should any color other than gray or
white be dominant in low light to high light areas the
color temperature settings have not been properly set.
Repeat the procedure if necessary.
NOTE: Color Cutoff adjustments affect the low light (dark)
areas while color drive adjustments affect the high
light (white) areas.
Page 2-1
Page 2-2

ALIGNMENTS (Continued)
CIRCUIT DESCRIPTION
Sub-brightness Adjustment
Test Point: Observe Display
Adjust: Menu 5 BRTC Sub-brightness
1. Tune the instrument to receive a grayscale stairstep signal from the A/V inputs.
2. Set the Picture color temperature to Normal and set all
of the picture controls (brightness, contrast etc.) to
midrange.
3. Enter the Service mode and select Menu 5.
4. Adjust the value of BRTC (Sub-brightness) to just light
the second dark bar making sure the first bar stays black.
Test Point: Observe Display
Adjust: Menu 3 HPOS6 H Position
Menu 3 PARA6 H Parabola
Menu 3 TRAP6 H Trapazoid
Menu 3 HSIZE6 H Size
Menu 3 CNRT6 H Corner top
Menu 3 CNRB6 H Corner bot
Menu 2 HIGH6 Height
Menu 2 VLIN6 Linearity
Menu 2 VP60 Vertical Center
Menu 2 VSC6 Vert S Correct
Note: Confirm correct convergence and purity before
adjusting geometry.
1. Tune the instrument to receive a circular test pattern suitable for making visual geometry adjustments.
2. Enter the Service mode.
3. Adjust the Menu 2 and Menu 3 values listed for the least
amount of geometric distortion and approximately 7%
overscan.
X-Ray Protection Test
1. Tune the instrument to receive a crosshatch signal.
2. Apply an external power supply to C249 (observe polarity). Slowly increase the voltage from the supply.
3. The instrument must shut down and remain off when
the voltage reaches 30 volts DC.
High Voltage Test
1. High voltage must not exceed 31.8 kV at any beam current.
Circuit Description
Tuner
The function of the tuner is to select the channel to be received and suppress the interference, amplify the high
frequency signal, improve the receiving sensitivity and SNR,
and to generate PIF signal through frequency conversion.
IF Channel
The IF Channel mainly ensures the sensitivity and selectivity of the complete instrument. The IF AMP integrated in
TMPA8802 is made up of the third-stage dual-differential
amplifier with gain value above 70db, SNR of 55dB and
bandwidth of 6MHZ. The video demodulation circuit is made
from the built-in PLL Sync Detector. The spectrum of the
demodulation carrier is unitary and not affected by the content of the video signal.
The PLL built-in the TMPA8802 generates 45.75MHz demodulation reference signal for sync detector to demodulate
the video signal, which is called ‘PLL sync demodulation’.
Chroma Signal Decoding Circuit
The external BPF (band-pass filter) singles out the chroma
signal and burst signal within the range of
fsc+1.3MHZ from among the composite signals output from
the video detector. After being amplified by ACC, the chroma
signal is fed into the synchronous detector to be demodulated
to obtain the color difference signal.
Luminance Channel and Matrix Circuit
The luminance channel of TMPA8802 has a black stretch
circuit to make dark picture content darker thus improving
the contrast and depth perception of the picture. It also has
the delayed definition-enhanced circuit to enable the details
of the picture seem more vivid. The luminance signal (Y) is
sent into the matrix circuit after being delayed for 0.6 s and
composes R/G/B signal combined with the three color-difference signals (B-Y, R-Y, G-Y).
Sync Separation and Deflection Processing Circuit
TMPA8802 has the 32fh PLL (fh = horizontal frequency). In
reference to the frequency and phase information carried by
the composite sync signal, the PLL generates a scan clock
signal with 32fh and a horizontal drive pulse that will be obtained through 32fh countdown. An integrating circuit is used
to extract vertical sync from the composite sync pulse to control the counter for vertical countdown. The circuit countdowns the 32fh clock signal, thus vertical frequency sync
pulses under various systems can be obtained.
TMPA8802 includes the vertical SW former (sawtooth
wave former) and can control the gain and linearity of the
SW (sawtooth wave).
Sound Channel
The second SIF goes via a filter of 4.5MHz, to MSP3425.
The MSP3425 then decodes the SIF into MONO, STEREO
or SAP. MONO, STEREO, SAP and sound effect processing modes are adjusted via the IIC bus.
Remote Control System
The MCU (TMPA8802) of an 8-bit CPU and the software
constitute the control core of the remote control system, mainly
accomplishing the following functions: decoding remote control commands; auto search memory; displaying characters
and patterns; switching the signal source between AV and TV.
The transmitter translates the commands from the buttons and
separately demodulates the 37.9KHZ carrier and 940nm infrared ray to generate the infrared transmitting signal at the
LED. The remote control system has three operating modes:
user-controlled mode (U-mode), service mode (S-mode) and
factory default mode (D-mode). U-mode includes the following functions: channel search and memory; channel selecting; volume control, brightness adjustment, contrast and color
adjustment. S-mode and D-mode are mainly used in production, checking & repairing, including the following functions:
horizontal & vertical centering control, vertical
amplitude and linearity adjustment; setting the adjusting range
for volume, contrast, brightness, tint and color; geometric
adjustment and white balance adjustment.
CRT Drive Circuit
A cascode amplifier is used to amplify the voltage and current of the R/G/B signal so the CRT drive circuit can demodulate the cathode beam current of the CRT. The R/G/ B
signal input into the cascode circuit is of negative polarity.
Page 2-3
Page 2-4