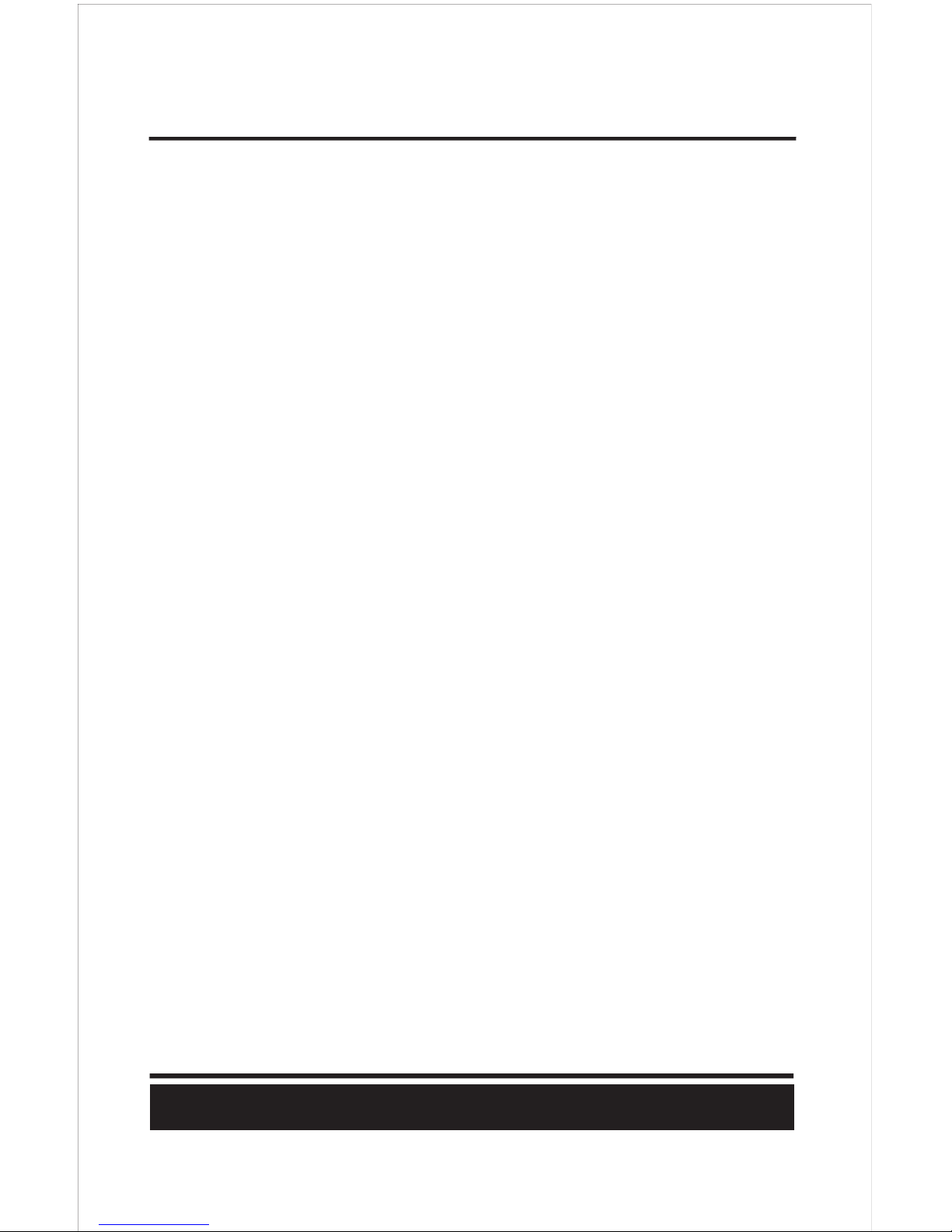
Diagram & Equipment Specifications..........4
Safety Instructions......................................5
Pro-Built......................................................6
Pro-Built with Diagram................................7
Tips in the Field.......................................8-9
Trouble Shooting.................................10-16
Warranty Information................................17
TABLE OF CONTENTS
3
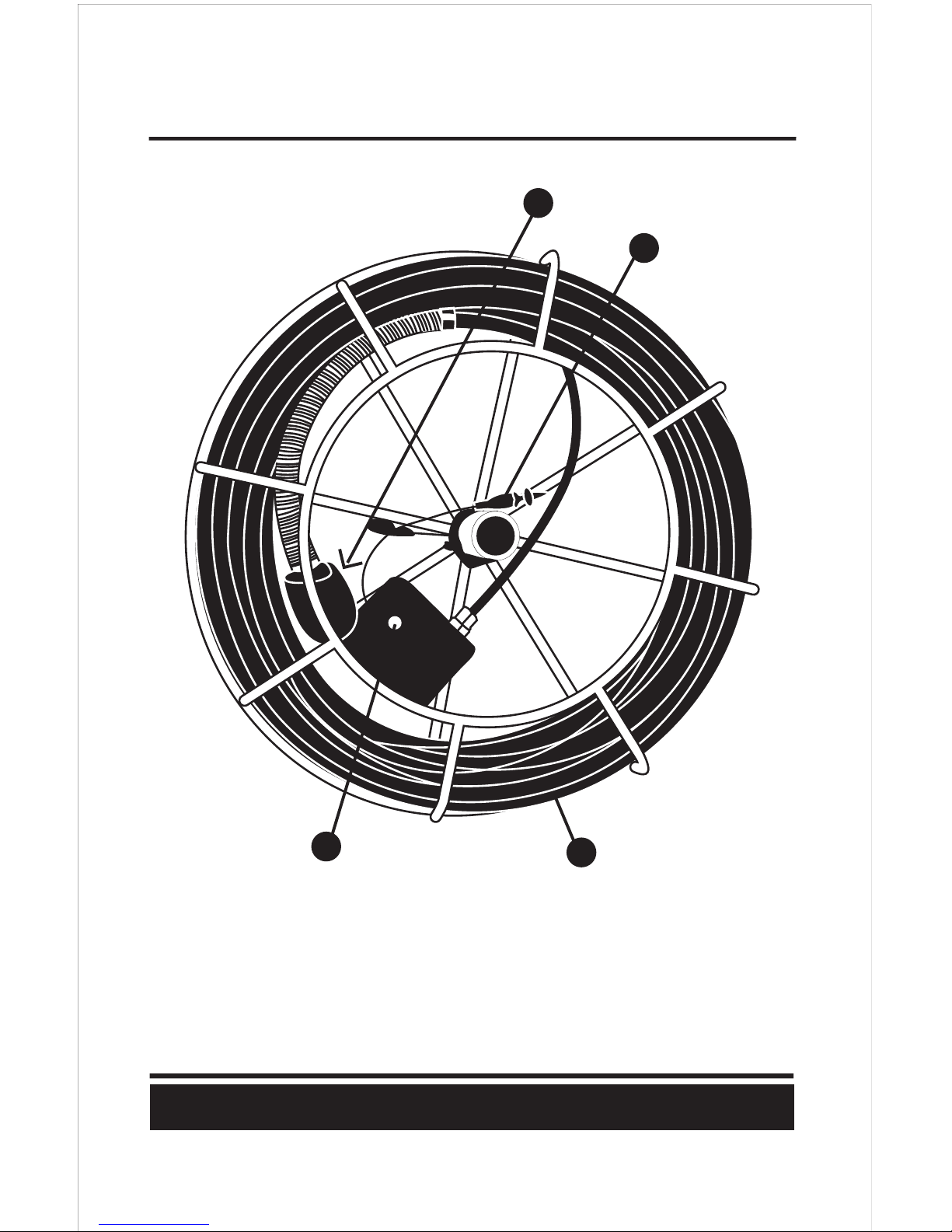
DIAGRAM & SPECIFICATIONS
4
d
A .Inductive Locator Terminal
B. Camera Head
C. Video In/Out
D. Heat Treated Epoxy Sealed SV Cable
a
b
c
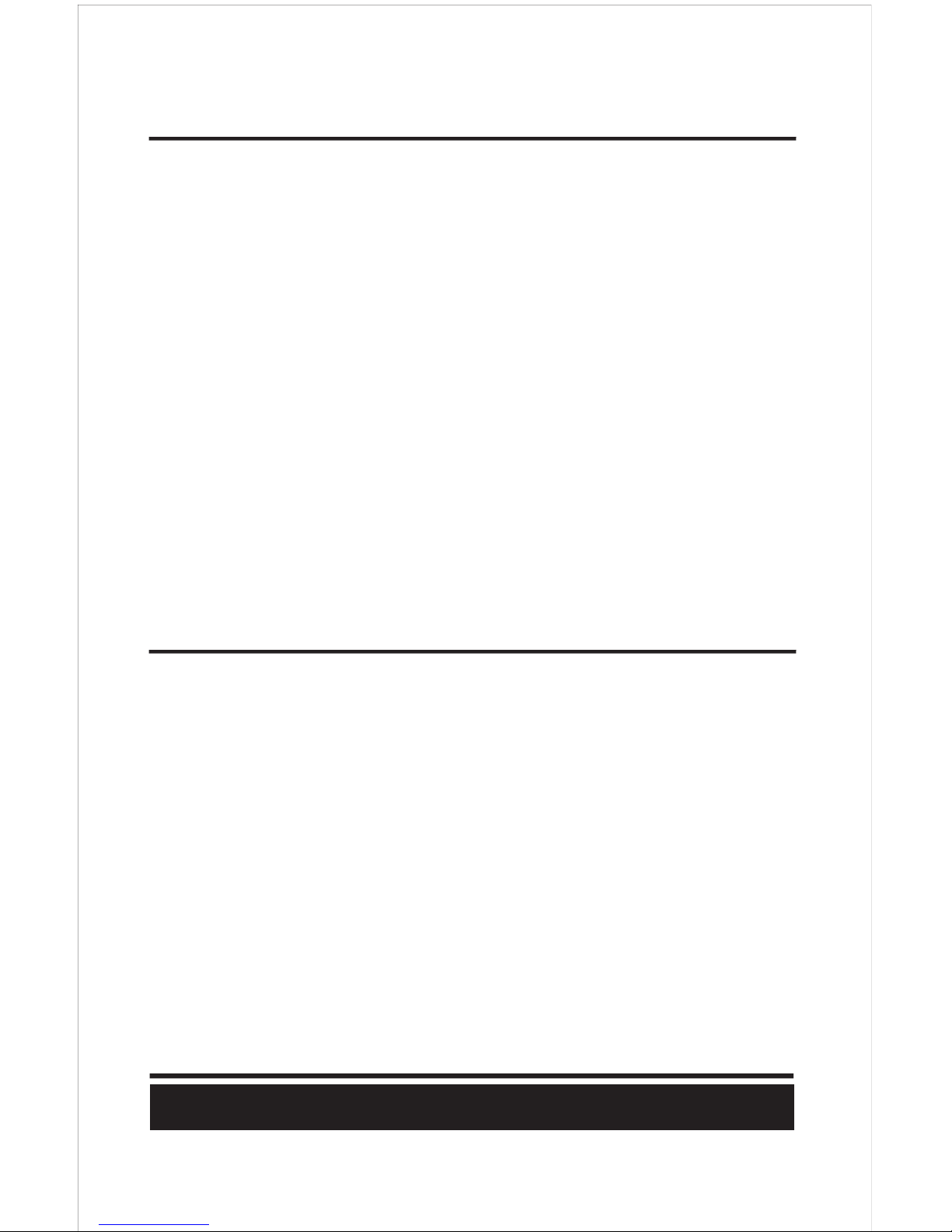
EQUIPMENT SPECIFICATIONS
SAFETY INSTRUCTIONS
5
• PB1200 Camera Head
Dimension: 1 1/4” Diameter
Pipe Size: 2“ Pipe + (2” Pipe Depends on Condition of Pipe)
• High Tension Pro Built Inspection Cable Push Capacity:
100’ – 500’ (depending on condition of line)
• Steel Cage
16” -20” in Diameter Depending on Model Purchased
• Camera Material
Air Craft Aluminum
• Depth Rated
Submersible to 100’
1.) Keep all buttons, handles, switches clean of oils & grease.
Please avoid setting monitor directly in water.
2.) Prior to use inspect all buttons, handles, switches to make
sure they are in working order. If equipment is malfunctioning
please do not operate. See trouble shooting guidelines in back
of manual.
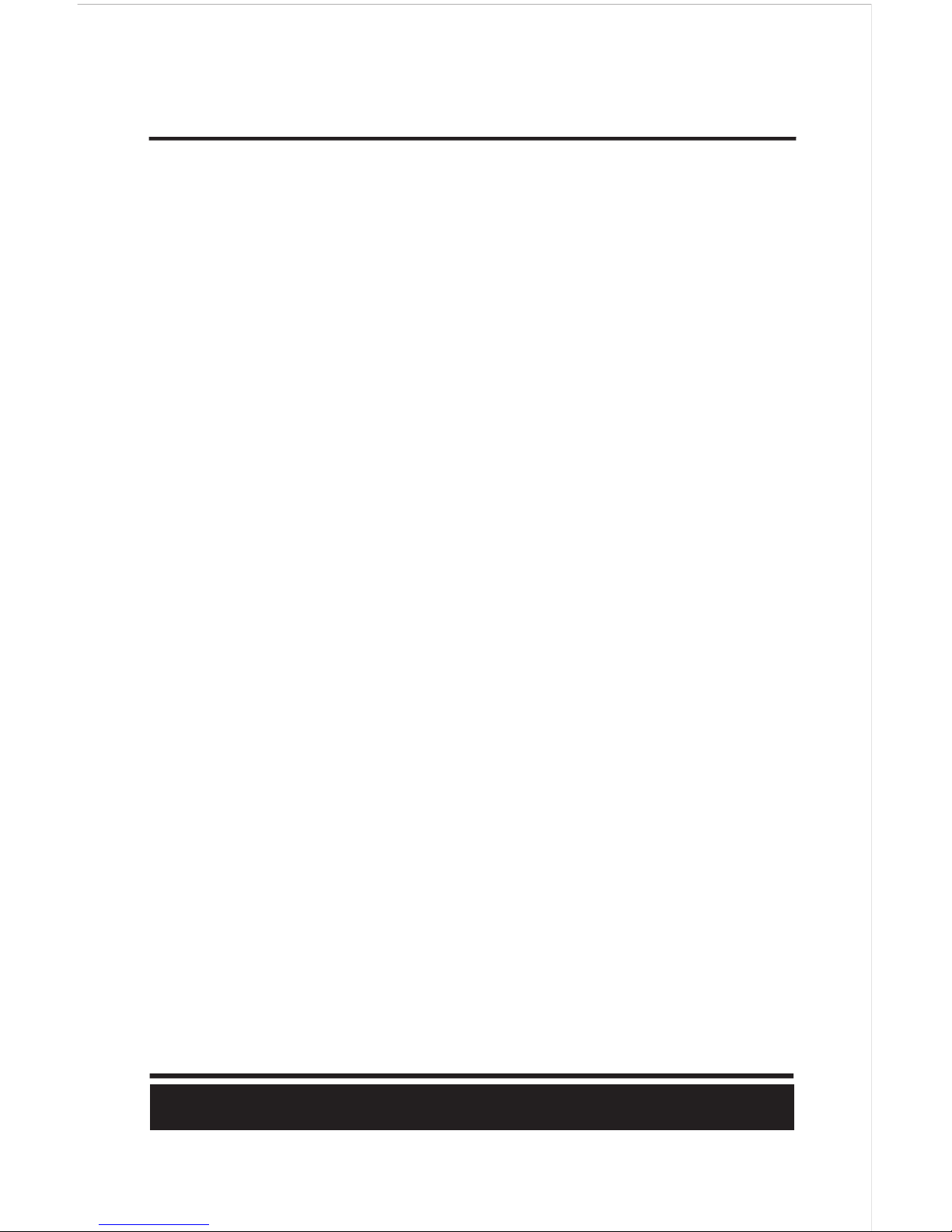
Pro-Built Tools
6
PB1200 Series Inspection Camera
Once you have inspected all components to make sure
that they are not damaged or broken, plug the power
cord into a grounded outlet.
The camera should turn on. Check to see if the lights on
your camera head are on. If they are
proceed to the next step. If they are not check your
outlet and refer the troubleshooting section of your
manual.
Next you will plug the provided Video Cable into your
monitor Video Input.

Pro-Built Tools
7
At this point you will plug the free end of your video cable
into the monitor that you are using to view the camera
with. Please refer to monitor manual for any further
instruction.
If your camera model came equipped with a 512 Hz
transmitter built inside the camera head please see the
diagram below to activate the built in transmitter.
H
O

TIPS IN THE FIELD
8
1.) Run water down line to keep sapphire window clean
and clear. Jiggle the head a little bit in the water for best
clarity.
2.) If you stand too far back while pushing cable it may
cause the cable to kink. Give your self enough room to
push but not too much slack.
3.) DO NOT FORCE camera or cable down line. If you
feel it just doesn’t want to push stop pushing. It is for this
reason cable will snap or fail.
4.) In some cases it is necessary to give the camera a
little more momentum to go through certain areas of a
pipe. Back up the camera holding one hand at the entry
point and gathering up slack with the other as it feeds
from the reel. With the slack make a figure eight with
cable and twist back and fourth. This will pop the camera
through. Please see diagram below.

TIPS IN THE FIELD cont.
9
5.) DO NOT hammer or slam the camera into pipe
where it is just not pushing through. Use the technique
described on tip 4. After you are comfortable with your
system it may be easier to push thru the pipe fast and
slowly pull back for your actual inspection. Pulling the
camera back is always easier than pushing it through
6.) Pro-Built tool sysems have an automatic light
adjustment. If the automatic light adjustment is not
enough due to unusual circumstances in different or
difficult pipe use your dimmer control knob to adjust for
better picture quality.
7.) This camera is made to function through several
bends and 90 degree angles. If it is resisting in any
T or P-Trap do not force the unit. If you do manage to
get through a tough T be careful not bend the camera
head back on itself, as it may cause damage to the unit.
8.) After using your camera in a pipe pull it out and wipe
the cable and head down with a moist warm towel and
regular household detergent or soap. This will keep your
equipment functioning longer.

TROUBLE SHOOTING
10
The trouble shooting guide lines below are designed to
help you out in the field. If you cannot figure out the
problem or fix it without voiding your warranty, please call
the number listed in the back of your manual to speak
with a repair technician.
LIGHTS TURN ON – NO VIDEO
Possible problems:
-Monitor Not Functioning
-Faulty Video Cable
-Broken or loose connection in Camera Head
TRY THIS:
First plug the camera system into another monitor or
standard television that accepts standard RCA
connections. If you get a picture then you know the problem
is located in your monitor.
If you still have no picture on another monitor try
changing the video cable that goes from your reel to
your monitor. Any standard RCA adapter will work with
your camera system.
If you have no picture with a new
cable and another monitor then the problem is located
with the camera system. Call the repair department to
get the proper instructions on how to have the equipment
diagnosed.

TROUBLE SHOOTING
11
VIDEO WORKS–LIGHTS DON’T TURN ON
Possible Problems:
-Lights Burnt out
-Dimmer Control Switch Turned Down
-Dimmer Control Switch Broken
-Broken or loose connection in Camera Head.
TRY THIS:
Turn dimmer control all the way down and then all the
way back up. Check to see if GFCI is working properly
with the camera system. If problem still persists please
contact the repair department to have unit diagnosed.
NO LIGHTS - NO VIDEO
Possible Problems:
-Ground Fault Interruption
-Broken or damaged control box.
-Damaged or faulty connection with in camera head

TROUBLE SHOOTING
12
TRY THIS:
First check to see if your GFCI is tripping. Try to plug the
unit into another location with different electricity. If GFCI
will not re-set it is not working and will prevent the
camera system from turning on. IF GFCI IS REMOVED
FROM UNIT AND THEN CAMERA SYSTEM IS USED
WITH OUT IT, WARRANTY WILL BE VOID. The GFCI is
designed to protect your camera system from bad power.
If it no longer works please call South Coast Equipment
for a replacement. IF GFCI is functioning fine, and you
still have no lights and no video the problem is within the
control box or camera head assembly. Please call the
repair department for instructions on how to have the
equipment diagnosed.
HORIZONTAL WAVY LINES ACROSS SCREEN
Possible Problems:
-512 Hz Transmitter Built in Head is in the ON position.
-Faulty Video Cable
-Dirty Monitor

TROUBLE SHOOTING
13
TRY THIS:
If the transmitter that is built inside the camera
head is in the ON position, the frequency that it puts out
interferers with the camera head frequency, and will
create wavy lines across your monitor. Inspect your pipe
and then locate to avoid picture distortion.
If your equipment is not equipped with a
transmitter built in the head or you have lines across
your screen while it is in the OFF position try changing
the video cable that goes from your reel to your monitor.
Any standard RCA adapter will work with your camera
system.
If the suggestions above have not eliminated
the problem there is a possibility that your MONITOR or
RECORDING DEVICE is dirty and needs to be cleaned.
See Monitor Instruction Booklet for cleaning instructions.
If problem persists please contact a repair technician
at South Coast Equipment.

TROUBLE SHOOTING
14
“NO SIGNAL” FLASHING ON MONITOR
Possible Problems:
-Wrong setting set on Monitor or Recording Device
-Faulty Video Cable
-Broken or damaged monitor or recording device
-Broken or loose connection in camera head or control box.
TRY THIS:
Read Monitor or Recording Device instruction
manual to make sure you are on the proper settings. Be sure
to check the batteries in all remote controls.
If you are on the proper settings plug the camera
system into another monitor or standard television that
accepts standard RCA connections. If you get a picture then
you know the problem is located in your monitor.
If you still have no picture on another monitor try
changing the video cable that goes from your reel to your
monitor. Any standard RCA adapter will work with your
camera system.
If you can play back on the Monitor or Recording
Device and none of the solutions above have worked, the
equipment will need to be diagnosed by a technician
please call the repair department at South Coast Equipment.

TROUBLE SHOOTING
15
BLURRY OR SCRAMBLED PICTURE
Possible Problems:
-Monitor Broken or Damaged
-Seal broken or compromised
-Moisture in head
-Camera Head Fried
-Faulty Video Cable
TRY THIS:
First plug the camera system into another
monitor or standard television that accepts standard RCA
connections. If you get a clear picture then you know the
problem is located in your monitor. (See monitor
instructions).
If you still have a blurry or scrambled picture on
another monitor try changing the video cable that goes from
your reel to your monitor. Any standard RCA adapter will
work with your camera system.
Look at camera head and check for any type of
moisture. If head has been tampered with or abused a seal
may have broken and allowed moisture into the head. This
would cause a blurry or scrambled picture. Camera System
should then be diagnosed by a repair technician.

TROUBLE SHOOTING
16
COLORFUL IMAGES DISTORTED COLORS
Possible Problems:
-Monitor Broken or Damaged
-Seal broken or compromised
-Moisture in head
-Camera Head Fried
-Faulty Video Cable
TRY THIS
First plug the camera system into another monitor
or standard television that accepts standard RCA
connections. If you get a clear picture then you know the
problem is located in your monitor. (See monitor instructions)
If you still have a distorted or bright colorful
images on another monitor try changing the video cable that
goes from your reel to your monitor. Any standard RCA
adapter will work with your camera system.
Look at camera head and check for any type of
moisture. If head has been tampered with or abused a seal
may have broken and allowed moisture into the head. This
would cause the camera head to fry and create strange
distorted colors to form on the screen. Camera System
should then be diagnosed by a repair technician.

WARRANTY INFORMATION
17
For warranty or service work please contact manufacture ProBuilt
Tools. Read following information for contact details.
Pro-Built Tools service center
11711 Coley River Circle, Ste #11
Fountain Valley, CA 92708
Phone: (714) 437-1255