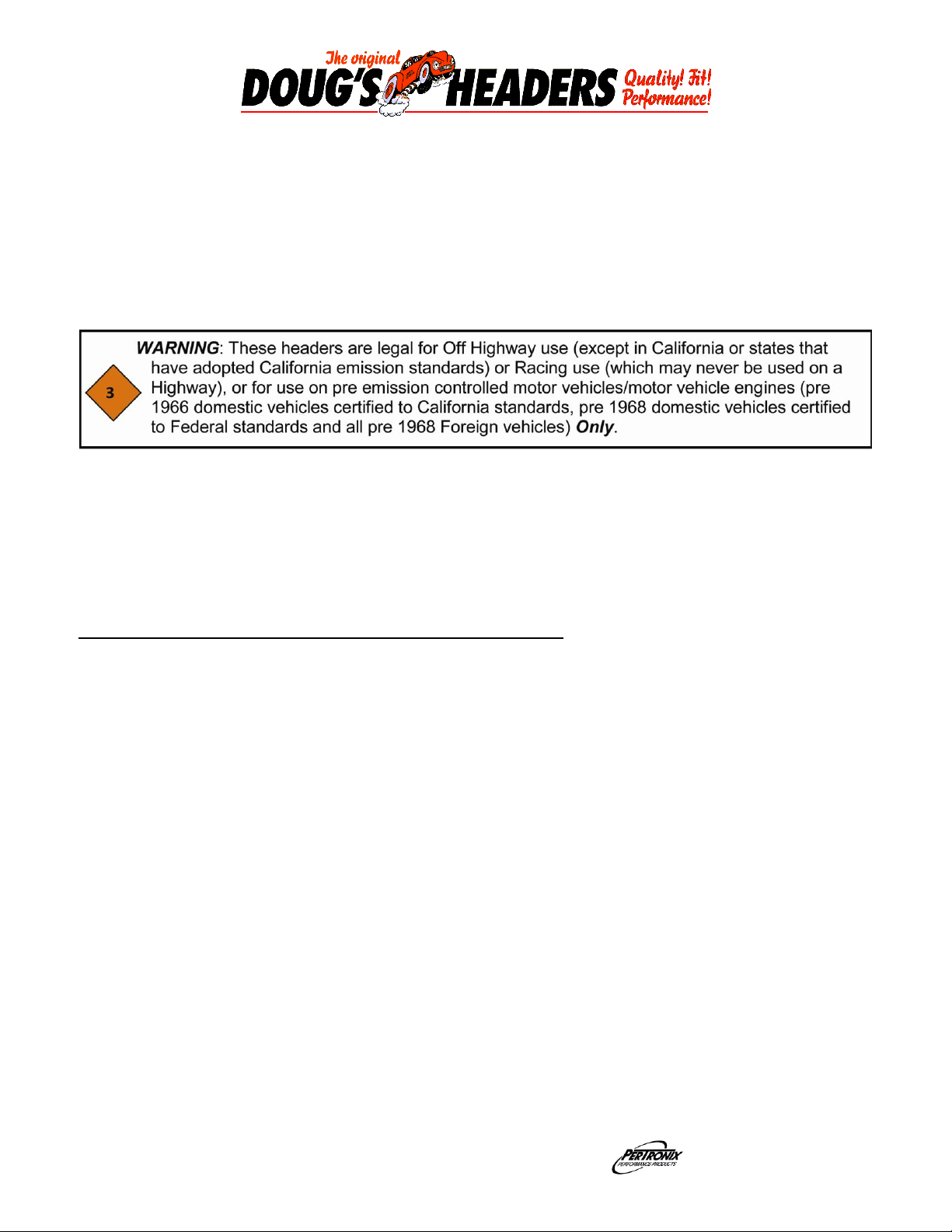
Corporate Office: PerTronix Inc. 440 E. Arrow Highway, San Dimas, California 91773 * Phone 909.599.5955 * FAX 909.599.6424 * www.dougsheaders.com
HEADER INSTALLATION INSTRUCTIONS
D3338
APPLICATION
64-72 BUICK SKYLARK, GRAN SPORT & WAGONS, LS1/LS6
64-72 CHEVROLET CHEVELLE, PASSENGER CARS & WAGONS, LS1/LS6
64-72 PONTIAC GTO & LE MANS, LS1/LS6
Note: Requires LS1 adapter plate kit P/N SK100
PerTronix
to realize the full potential of our good fit, please read and understand these instructions completely prior to starting work.
CHECK TO MAKE SURE YOU RECEIVED THE PROPER PARTS FOR YOUR APPLICATION. THE HEADER NUMBER WILL
BE STAMPED ON THE ENGINE FLANGE. IF YOU ARE UNSURE YOU HAVE RECEIVED THE PROPER PARTS CALL
BEFORE YOU START WORK.
BE SURE TO WORK SAFE! WHENEVER YOU WORK UNDER THE VEHICLE BE SURE THAT IT IS LOCATED ON LEVEL,
SOLID GROUND AND IS SUPPORTED BY ADEQUATE SAFETY STANDS!
REMEMBER: HOT ASPHALT WILL NOT SUPPORT MOST JACK STANDS!
Many factors affect the installation of headers, some of which are broken or aftermarket motor mounts, accidents that impact the
configuration of the frame, and/or the installation of different engines or aftermarket cylinder heads. Most installations require
some welding. If you are uncomfortable with welding operations, we recommend that you contact a professional exhaust
system specialist to install your new headers.
Attention Customers breaking in new engines: Due to the extreme heat generated during the break-in process, the
appearance of the ceramic coating may be altered in certain areas. The protection characteristics and thermal barrier properties
of the coating is never compromised. It is recommended that a cast iron manifold or old set of headers be used for this process.
Notice: The coating of these headers can be marred or scratched during installation. If the header needs to be returned and is
damaged, you will be charged for recoat.
©
thanks you for choosing
DOUG’S HEADERS
, the best fitting, highest quality header on the market. In order
DISASSEMBLY / ASSEMBLY
1. Disconnect the negative battery cable from the battery.
2. If a car lift is not available, raise the vehicle 2 feet or higher and support it with
adequate safety stands. Make sure the vehicle is on a flat solid surface and is stable.
3. Apply penetrating oil to all nuts and bolts to be removed.
4. Remove bolts from headpipe to exhaust manifolds.
5. Note the spark plug wire locations and remove them from the spark plugs. Use a
twisting motion while pulling the spark plug boot off of the spark plug. Be very careful
not to damage the spark plug boot and do not pull on the wire itself.
Part No. 0110-003066 Page 1 of 3 rev.1 9-6-13 DSL
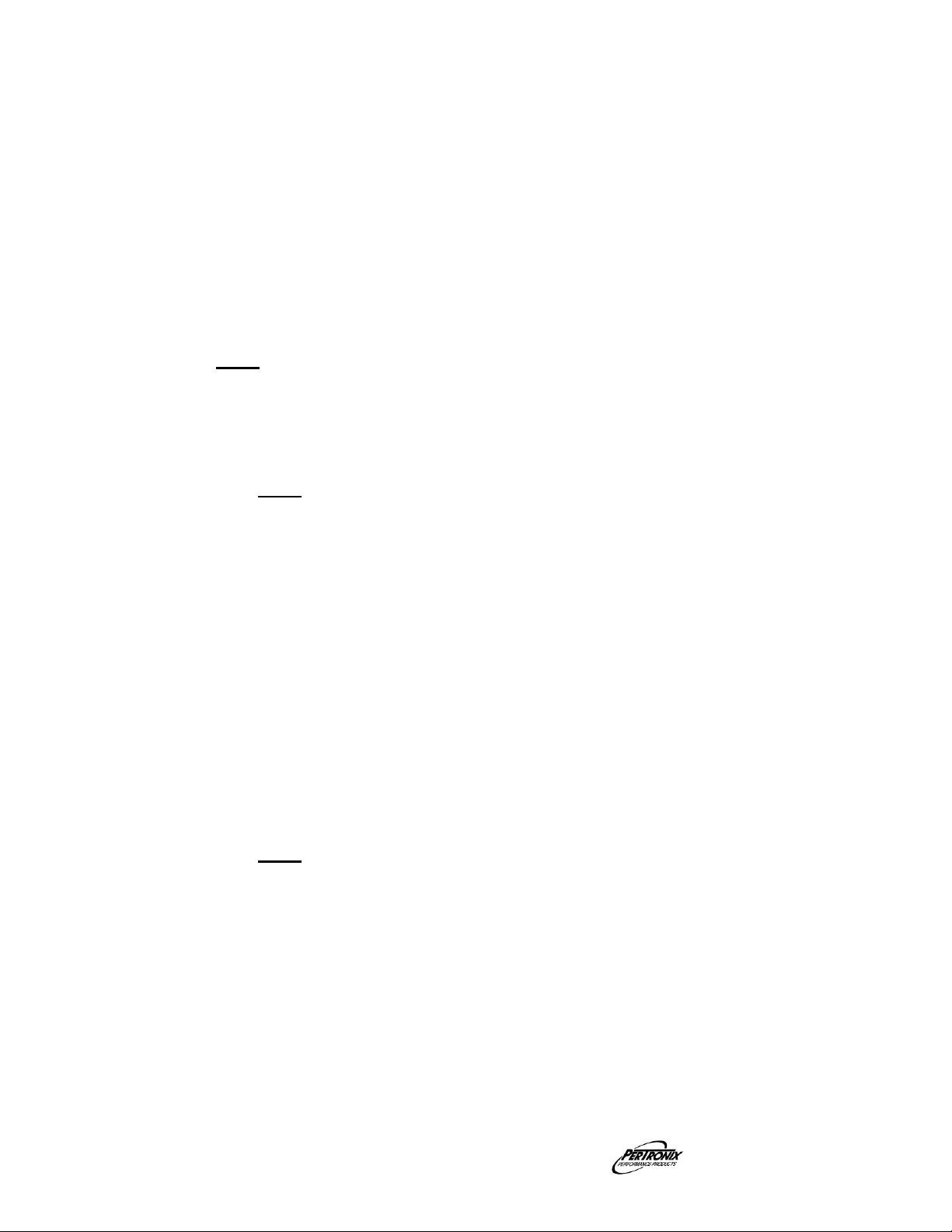
6. Remove spark plug wire looms, plugs and any brackets attached to the manifolds.
7. Disconnect the O2 sensor wiring.
8. Remove the O2 sensors.
9. Remove the oil dipstick and tube.
10. Remove both of the exhaust manifolds.
11. Remove the starter.
12. Replace the spark plugs finger tight so debris will not get into the cylinders while
cleaning the head surface. We recommend the use of a gasket scraper, wire brush,
and sanding block to adequately clean the surface.
13. After cleaning is complete remove the spark plugs again.
14. Remove the oil filter.
15. Apply a THIN film of Ultra Copper Hi-Temp Sensor-Safe Silicone Sealer to header side
of the header gaskets and stick the gaskets to the header flanges. Masking tape can
be used to help hold the gasket to the header.
RIGHT SIDE:
1. Apply a THIN film of Ultra Copper Hi-Temp Sensor-Safe Silicone Sealer to engine
side of the header gasket.
2. Apply anti-seize to all header bolts being used.
3. Starting from below, work the header and gasket up through the chassis into
position.
4. Start all header bolts.
5. Tighten all header bolts evenly (most restricted first) 18 ft./lbs on aluminum heads
or 25 ft/lbs on Iron Heads.
6. Reinstall the right side spark plugs, wire looms, starter and dipstick tube and
dipstick.
7. Reinstall the O2 sensor.
8. Reconnect the O2 sensor to the O2 harness with the supplied extension.
9. Install the slip-on reducer and band clamp.
10. Cut the old exhaust pipe and weld as necessary to the new reducer.
LEFT SIDE:
1. Apply a THIN film of Ultra Copper Hi-Temp Sensor-Safe Silicone Sealer to engine
side of the header gasket.
2. Apply anti-seize to all header bolts being used.
3. Starting from below, work the header and gasket up through the chassis into
position.
4. Start all header bolts.
5. Tighten all header bolts evenly (most restricted first) 18 ft./lbs on aluminum heads
or 25 ft/lbs on Iron Heads.
6. Reinstall the oil filter.
7. Reinstall the left side spark plugs, wire looms and any brackets.
8. Reinstall the O2 sensor.
9. Reconnect the O2 sensor to the O2 harness with the supplied extension.
10. Install the slip-on reducer and band clamp.
Part No. 0110-003066 Page 2 of 3 rev.1 9-6-13 DSL

11. Cut the old exhaust pipe and weld as necessary to the new reducer.
12. Connect the negative battery cable.
START THE ENGINE
Start the engine and allow it to warm up to operating temperature. Check for any unusual
noises or exhaust leaks. If every thing is OK, stop the engine and tighten all bolts while
the engine is still warm.
NOTE: Check the bolts periodically to make sure they have not loosened. Re-tighten
after the first 500 miles and then again at 1000 miles
IMPORTANT CHECK LIST
Be sure that all brake lines and fuel lines are clear of headers and/or connector
pipes.
All spark plug wires, battery cables, or other electrical components should be clear
of headers and/or connector pipes.
If dipstick tube was removed, make sure it is installed properly and that the
dipstick has been replaced.
Double-check the tightness of all bolts including brackets and accessories.
PARTS LIST
Qty Description
1 Left side header
1 Right side header
2 Header gasket
2 Slip-on reducer
2 Band clamp
12 Bolt, header, M8-1.25 x 25MM (1” long)
12 Lock washer, 3/8”
2 O2 Sensor extension
Part No. 0110-003066 Page 3 of 3 rev.1 9-6-13 DSL