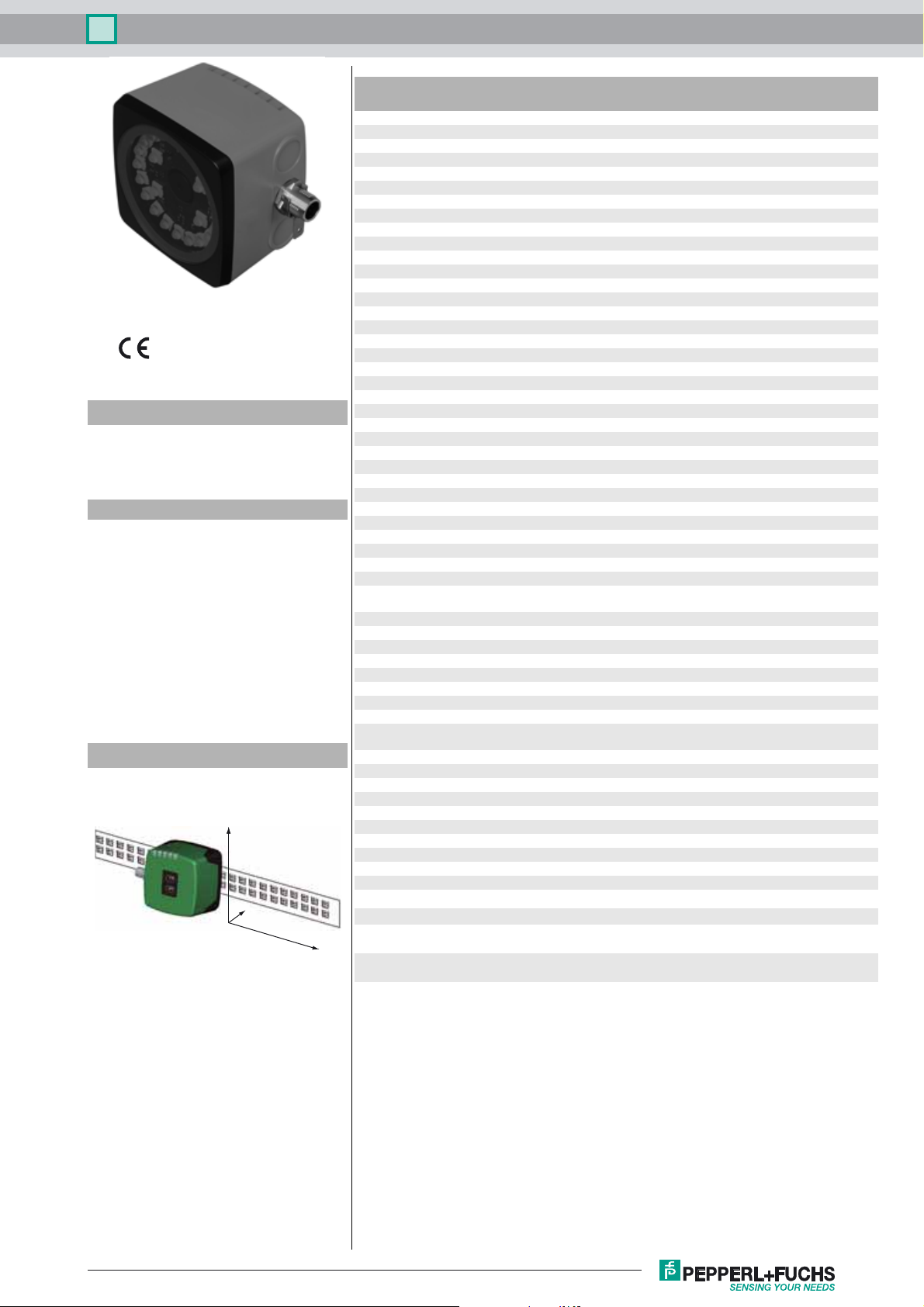
Optical reading head PCV80-F200-R4-V19
Technical data
General specifications
Passage speed v ≤ 12.5 m/s
Measuring range max. 10000 m
Light type Integrated LED lightning (red)
Read distance 80 mm
Depth of focus ± 15 mm
Reading field 40 mm x 25 mm
Ambient light limit 100000 Lux
Resolution ± 0.1 mm
Nominal ratings
Camera
Type CMOS , Global shutter
Processor
Clock pulse frequency 600 MHz
Speed of computation 4800 MIPS
Functional safety related parameters
MTTFd 100 a
Mission Time (TM) 50 a
Diagnostic Coverage (DC) 0 %
Indicators/operating means
LED indicator 7 LEDs (communication, alignment aid, status information)
Model Number
PCV80-F200-R4-V19
Read head for incident light positioning
system
Features
• RS 485 interface
• Non-contact positioning on Data
Matrix code tape
• Travel ran ges up t o 10 km, in X an d
Y direction
• Mechanically rugged: no wearing
parts, long operating life, maintenance-free
• High resolution and precise positioning, especially for facilities
with curves and switch points as
well as inclines and declines.
Diagrams
Coordinates
Y
Electrical specifications
Operating voltage U
No-load supply current I
Power consumption P
Interface
Interface type RS 485 interface
Data output code binary code
Transfer rate 38400 ... 230400 Bit/s
Termination Switchable terminal resistor
Query cycle time ≥ 10 ms
Input
Input type 1 to 3 functional inputs , programmable
Output
Output type 1 to 3 switch outputs , PNP , programmable , short-circuit
Switching voltage Operating voltage
Switching current 150 mA each output
Standard conformity
Emitted interference EN 61000-6-4:2007+A1:2011
Noise immunity EN 61000-6-2:2005
Shock resistance EN 60068-2-27:2009
Vibration resistance EN 60068-2-6:2008
Ambient conditions
Operating temperature 0 ... 60 °C (32 ... 140 °F) , -20 ... 60 °C (-4 ... 140 °F)
Storage temperature -20 ... 85 °C (-4 ... 185 °F)
Relative humidity 90 % , noncondensing
Mechanical specifications
Connection type 8-pin, M12 x 1 connector
Housing width 70 mm
Housing height 70 mm
Degree of protection IP67
Material
Housing PC/ABS
Mass approx. 160 g
B
0
0
15 ... 30 V DC , PELV
max. 200 mA
3 W
protected
(noncondensing; prevent icing on the lens!)
Z
X
Release date: 2017-03-24 11:32 Date of issue: 2017-03-24 218195_eng.xml
Refer to “General Notes Relating to Pepperl+Fuchs Product Information”.
Approvals and certificates
UL approval cULus Listed, General Purpose, Class 2 Power Source,
CCC approval CCC approval / marking not required for products rated ≤36
Type 1 enclosure
V
1
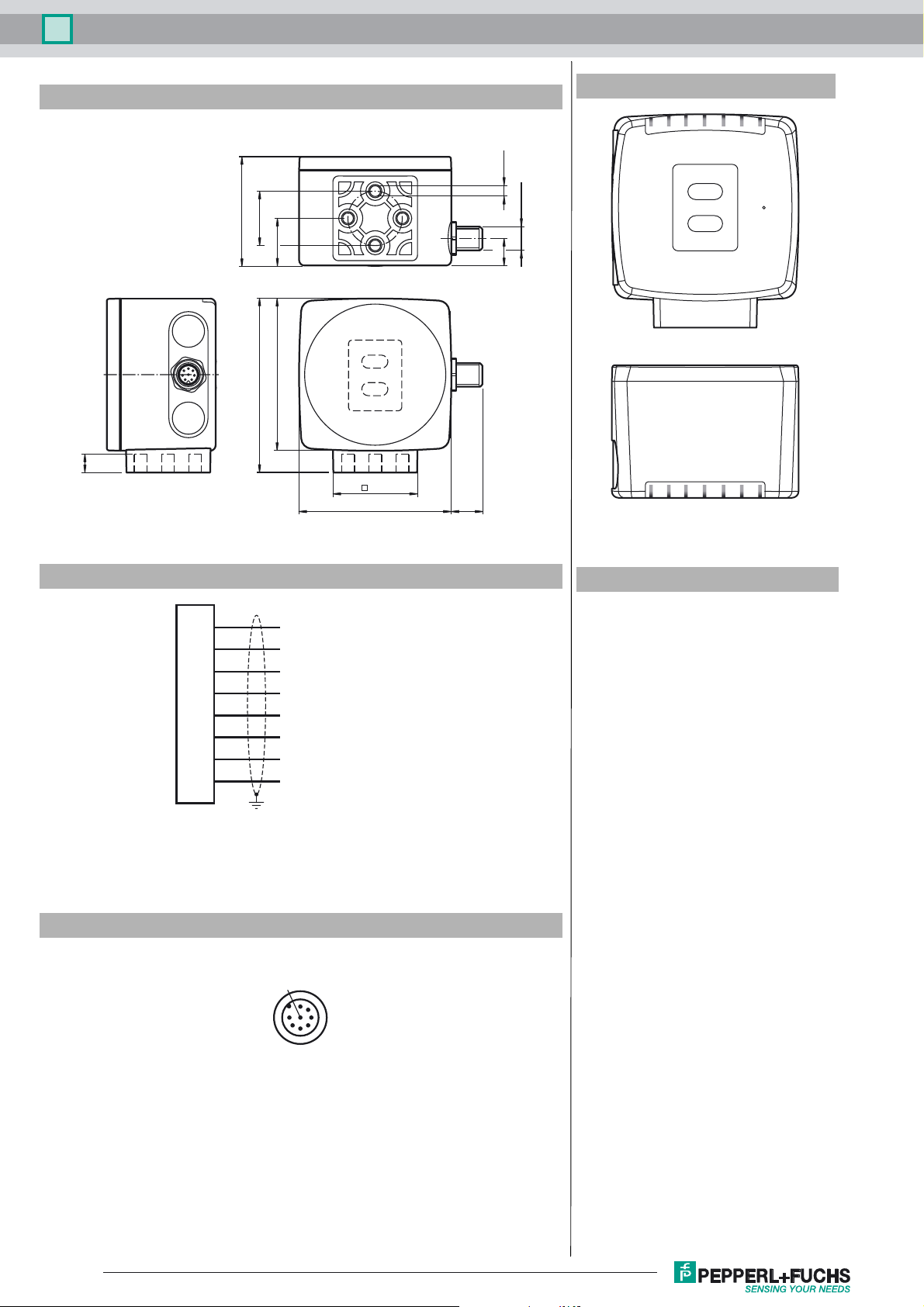
Optical reading head PCV80-F200-R4-V19
Dimensions
9
Additional Information
4 x M6
51
ø 25
22
4
5
8
3
6
2
1
7
70
80
1
2
38.5
70 14.5
M12 x 1
12
ADJUST
CONFIG
COM
LED 1 2 3 4 5 6 7
1
2
OUT1
OUT2 / ADJ Y
PWR / ADJ
ERR / NO CODE
OUT3 / ADJ Z
INTERNAL
DIAGNOSTIC
Electrical Connection
Pinout
Accessories
PCV-USB-RS485-Converter Set
1
2
3
4
5
6
7
8
OUT 2 / IN 2
+ UB
Data+ / TX / 485+
Data- / RX / 485-
OUT 1
IN 1
GND
OUT 3 / IN 3
1
8
2
4
7
6
53
USB to RS 485 interface converter
PCV-KBL-V19-STR-RS485
Cable unit with power supply for USB / RS485 interface converter
V19-G-ABG-PG9
Female connector, M12, 8-pin, shielded,
field attachable
V19-G-ABG-PG9-FE
Female connector, M12, 8-pin, shielded,
field attachable
PCV-SC12
Grounding clip for PCV system
PCV-LM25
Marker head for 25 mm code tape
PCV-AG80
Alignment guide for PCV80-* read head
PCV-MB1
Mounting bracket for PCV* read head
Vision Configurator
Operating software for camera-based
sensors
General
The reading head is part of the positioning system in the method for measurement by Pepperl+Fuchs. It consists of a camera module and an integrated illumination unit among other
things. The reading head detects position marks, which are put on an adhesive code band in
the form of Data Matrix code. The mounting of the code band is as a rule stationary on a firm
part of the plant (elevator shaft, overhead conveyor mounting rails…); that of the reading head
is parallel on the moving "vehicle" (elevator car, overhead conveyor chassis…).
Refer to “General Notes Relating to Pepperl+Fuchs Product Information”.
2
Release date: 2017-03-24 11:32 Date of issue: 2017-03-24 218195_eng.xml

Optical reading head PCV80-F200-R4-V19
Mounting and commissioning
Mount the reading head such that its optical surface captures the optimal read distance to the code band (see Technical Data). The stability of
the mounting and the guidance of the vehicle must be provided such that the depth of field of the reading head is not closed during operation.
All reading heads can be optimally customized by parameterization for specific requirements. The parameterization of reading heads with a bidirectional interface (all except SSI-interface) can take place via the interface itself (internal parameterization) or via an optical parameterization
code (external parameterization). The reading heads with SSI interface only have the possibility of external parameterization via optical parameterization codes.
Displays and Controls
The reading head allows visual function check and fast diagnosis with 7 indicator LEDs. The reading head has 2 buttons on the reverse of the
device to activate the alignment aid and parameterization mode.
LEDs
LED Color Label Meaning
1 Yellow COM Communication active
2 Green/red PWR/ADJ
3 Yellow OUT1 Output 1
4 Yellow OUT2/ADJ Y Output 2, Alignment aid Y
5 Yellow OUT3/ADJ Z Output 3, Alignment aid Z
6,7 red/green/yellow INTERNAL
ERR/NO CODE
DIAGNOSTICS
External parameterization
For external parameterization you require the parameterization code as Data Matrix with the desired reading head parameters. Data Matrix code
cards for step-by-step external parameterization are printed in the reading heads operating instructions.
Parameterization is only possible within 10 minutes of switching on the reading head. If a button is pressed after 10 minutes subsequent to switching on, there is visual signaling via the LEDs (LED1, yellow/LED2, red/LED3, yellow/LED4, yellow/LED5, yellow flash for 2 seconds)
• The switchover from normal operation to parameterization mode is via button 2 on the reverse of the reading head. Button 2 must be pressed
for more than 2 seconds. LED3 now flashes.
Note: Parameterization mode automatically ends after 1 minute of inactivity. The reading head returns to normal operation and works with
unchanged settings.
• Place the parameterization code in the view of the camera module. After recognition of the parameterization code, the green LED2 lights up
for 1s. In the event of an invalid parameterization code, the red LED2 lights up for 2 s.
• A short press on button 2 ends the parameterization mode and the changed parameters are not stored volatile in the reading head.
Alignment aid for the Y and Z coordinates
The activation of the alignment aid is only possible within 10 minutes of switching on the reading head. The switchover from normal operation to
“alignment aid operating mode is via button 1 on the reverse of the reading head.
• Press the button 1 for longer than 2 s. LED2 flashes green for a recognized code band. LED2 flashes red for an unrecognized code band.
•Z coordinate
band too large, the yellow LED5 lights up. Within the target range, the yellow LED5 flashes at the same time as the green LED2.
•Y coordinate
axis is too high, the yellow LED4 extinguishes. Within the target range, the yellow LED4 flashes at the same time as the green LED2.
• A short press on button 1 ends the alignment aid and the reading head changes to normal operation.
: If the distance of the camera to the code band too small, the yellow LED5 lights up. If the distance of the camera to the code
: If the optical axis of the camera is too deep in relation to the middle of the code band, the yellow LED4 lights up. If the optical
Code recognized/not recognized, Error
Internal diagnostics
Release date: 2017-03-24 11:32 Date of issue: 2017-03-24 218195_eng.xml
Refer to “General Notes Relating to Pepperl+Fuchs Product Information”.
3