
MODELS
WG75HH/100H/150H STANDARD
AND WGX75HH/100H/150H HAZARDOUS LOCATION*
*Used in Hazardous Locations Class 1, Division 1, Groups C & D
SUBMERSIBLE GRINDER PUMPS
INSTALLATION AND SERVICE MANUAL
NOTE! To the installer: Please make sure you provide this manual to the owner of the equip ment or to the responsible
party who maintains the system.
Part # 23833A530 | © 2018 Pentair plc. | 4/16/18
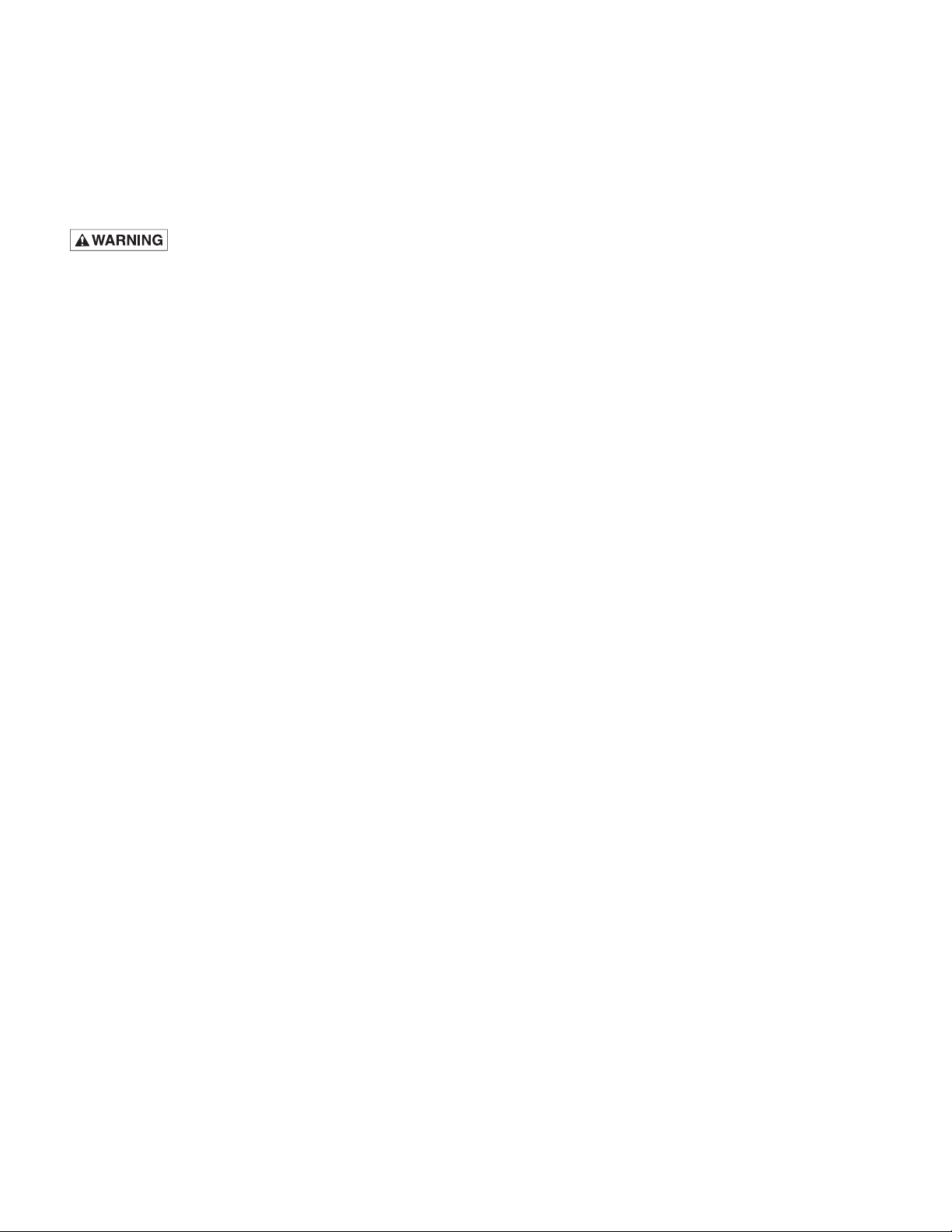
CAUTION!
Read these safety warnings rst before installing,
servicing, or operating any pump. Only qualied persons
shall conduct services and installations of this pump. The
pump must be wired by a qualied electrician, using an
approved starter box and switching device.
CALIFORNIA PROPOSITION 65 WARNING:
This product and related accessories
contain chemicals known to the State of California to
cause cancer, birth defects or other reproductive harm.
GENERAL
1. Most accidents can be avoided by using
COMMON SENSE.
2. Read the operation and maintenance instruction manual
supplied with the pump.
3. Do not wear loose clothing that can become entangled in
the impeller or other moving parts.
4. This pump is designed to handle materials
that could cause illness or disease through
direct exposure.
Wear adequate protective clothing when working
on the pump or piping.
ELECTRICAL
5. To reduce the risk of electrical shock, pump
must be properly grounded in accordance with the
National Electric Code and all applicable state
and local codes and ordinances.
6. To reduce risk of electrical shock, disconnect
the pump from the power source before handling
orservicing.
7. Any wiring to be done on pumps should be done by a
qualied electrician.
8. Never operate a pump with a power cord that has frayed
or brittle insulation.
9. Never let cords or plugs lie in water.
10. Never handle connected power cords with
wet hands.
20. Submersible grinder pumps are not approved for use
in swimming pools, recreational water installations,
decorative fountains or any installation where human
contact with the pumped uid iscommon.
21. Do not operate pump without safety devices in place.
IMPORTANT! Myers is not responsible for losses, injury
or death resulting from a failure to observe these safety
precautions, misuse or abuse of pumps or equipment.
GENERAL INFORMATION:
Motor HP & Voltages: These submersible grinder pumps
are offered in three phase, 7
1
/2, 10 and 15 HP. Voltages will
vary according to the application. Three phase stators are
available with dual voltage congurations that will allow either
230V or 460V internal connection.
Electrical Controls: All of these pump models must be used
with a control panel. Myers built control panels are designed
to supply the correct electrical controls, motor starting
equipment and include the circuitry for moisture and heat
sensors. It is recommended that a Myers built control panel
be used so that all warranties apply.
General Construction: The WGX75HH-150H motor
construction is designed to meet Factory Mutual requirements
for Class 1, Division 1, Groups C and D sewage applications.
These models are certied and nameplated with this approval.
The motor chamber and seal chamber are lled with a high
dielectric type oil for improved lubrication and heat transfer
of the bearings and motor. Since the bearings have been
designed for 50,000 hours of life, the oil should never require
replacement under normal operating conditions. An air space
above the oil level in both the seal and motor chambers
is provided to allow for the expansion of the oil when at
operating temperature. The power and control lines are sealed
and strain relieved on the outside entrance with a standard
cord grip, and internally through the use of a dielectric
potting resin surrounding the electrical wires. All of the
pump fasteners and shafts are made from corrosion resistant
stainless steel, while the pump castings are made of ASTM
A-48 Class 30 cast iron, and the multivane vortex impellers are
made from ductile iron.
PUMPS
11. Pump builds up heat and pressure during
operation; allow time for pump to cool before handling or
servicing.
12. Only qualied personnel should install, operate or repair
pump.
13. Keep clear of suction and discharge openings. DO NOT
insert ngers in pump with power connected.
14. Do not pump hazardous material not recommended for
pump (ammable, caustic, etc.).
15. Make sure lifting handles are securely fastened each time
before lifting.
16. Do not lift pump by the power cord.
17. Do not exceed manufacturer’s recommendation for
maximum performance, as this could cause the motor to
overheat.
18. Secure the pump in its operating position so it cannot tip
over, fall or slide.
19. Keep hands and feet away from impeller when power is
connected.
General Installation: Various congurations and methods of
plumbing this series of solids handling pumps may be used;
however, for ease of installation and service a Myers rail lift-out
system is recommended.
Note: If the WGX75HH-150H hazardous location pumps are
used in conjunction with a rail lift-out system, it must be a
Factory Mutual approved non-sparking, hazardous location
system.
Note: If these guidelines are not followed, the Factory Mutual
hazardous location approval is void.
Hazardous Location Service: These pumps are to be used
for handling sewage, wastewater and storm water only. Only
pumps labeled for use in hazardous locations may be used
in hazardous locations. These pumps must be repaired and
serviced only at Myers Authorized Service Centers or at the
Myers factory. Any unauthorized eld repair voids warranty
and the hazardous location rating.
2

Motor: Each motor is provided with heat sensor thermostats
attached directly to the motor windings. The thermostats open
if the motor windings see excessive heat and, in turn, open the
motor contactor in the control panel, breaking the power to the
pump.
The control cable has ve conductors: black, white, red,
orange and green. White and black connect to the heat sensor
terminals in the control panels; red and orange connect to
the seal failure terminals in the control panel; and the green
connects to the ground in the control panel.
When the motor is stopped due to an overheat condition, it will
not start until the motor has cooled and the heat sensor reset
button is manually pushed on the front of the Myers control
panel. This circuitry is provided in the Myers control panel
designs.
The WG75HH-150H and WGX75HH-150H pumps are
equipped with internal thermostats to meet Class H heat rise
of 356°F (180°C).
Note: Failure to use proper circuitry and to connect the motor
overheat protection in the control panel would negate all
warranties and Factory Mutual approval.
Motor Seal Failure Warning: The seal chamber is oil lled
and provided with moisture sensing probes to detect water
leakage through the lower shaft seal. The probes can also
detect moisture present in the upper motor housing.
The presence of water energizes a red seal leak
warning light at the control panel. This is a warning light only,
and does not stop the motor. It indicates a leak has occurred
and the pump must be repaired. Normally, this indicates the
outboard seal has leaked. Allowing the unit to operate after
the warning may cause upper seal leakage along with motor
failure.
The resistance across the moisture sensing (seal failure)
probes should be checked after a seal leak warning light
has lit. This can be done by disconnecting the red and
orange control wires from the control panel and measuring
the resistance with an ohmmeter between the wires. If the
measured values are below specication, the pump may have
a lower seal failure and require service.
On the Myers hazardous location control panels the seal leak
test switch tests the seal leak circuit continuity. When pushed
the seal leak test bulb should light. If the test bulb does not
light it means either the wiring circuitry to the seal leak probes
has been broken or the bulb has burned out.
Note: Myers built control panels supply the correct circuitry
for moisture and heat sensor connections. Failure to install the
correct circuitry with proper connection would negate warranty
and Factory Mutual approval.
Motor Power Cord, Control Cord and Cord Cap Assembly:
Each motor power cord has four conductors: white, black, red
and green. For a three phase motor the red, black and white
conductors connect to the three line leads, and the green is
connected to a good ground. Interchanging any two line leads
will reverse the rotation of the motor.
Note: Rotation should be clockwise when observed from
the top of the pump. This can be checked by noting which
direction the pump torques upon initial starting. A properly
rotating pump will torque counterclockwise upon start.
The cord cap is epoxy potted. The cord cap provides for a
sealed wire connection with terminals so that connections can
be made without breaking the motor seal. This allows the cord
cap, with cords, to be removed from the motor. An approved
hazardous location junction box is required for hazardous
locations. The control and power cables cannot be spliced!
Note: Each cable has a green ground wire and must be
properly grounded per the National Electric Code and local
codes.
Electrical Motor Controls: All electrical controls and
motor starting equipment should be as specied in these
instructions. Consult factory for any acceptable alternatives.
For hazardous locations the controls and control panel
must be installed outside the hazardous area, or approved
hazardous location controls that are intrinsically safe must be
used.
Junction Box: If a junction box is used in a hazardous
location, it must be a hazardous location approved type with
hazardous location cord connectors. Wires from the junction
box must pass through a hazardous location seal connector.
Level Sensing Controls: intrinsically safe type oat controls
are recommended for all applications and required for
hazardous location service. An intrinsically safe control panel
relay will limit the current and voltage to the level controls. A
Myers control panel can be supplied with this type circuitry.
The oat level controls maintain the basin sewage water level
by controlling pump turn-on and turn-off levels.
1. The lower turn-off control should be set so that the pump
stops with the water covering the entire motor housing.
Consult the factory for any settings below this point.
2. The upper turn-on control should be set above the lower
turn-off control. The exact height between the two controls
is determined by the number of pump starts desired and
the depth of the basin. A maximum of 10 starts per hour
should not beexceeded.
3. The override control is set at a specied height above the
upper turn-on control.
4. The alarm control is set about 6" to 12" above the override
control.
5. No control should be set above the inlet invert.
Electrical Connections: All electrical wiring must be in
accordance with local code and only qualied electricians
should make the installations. All wires should be checked
for shorts to ground with an ohmmeter or megger after the
connections are made. This is important, as one grounded
wire can cause failure of the pump, control panel or cause
personalinjury.
Pump: The uid end of the pump is eld serviceable and
can be disassembled in case of wear, damage, plugging or
outboard seal failure.
3