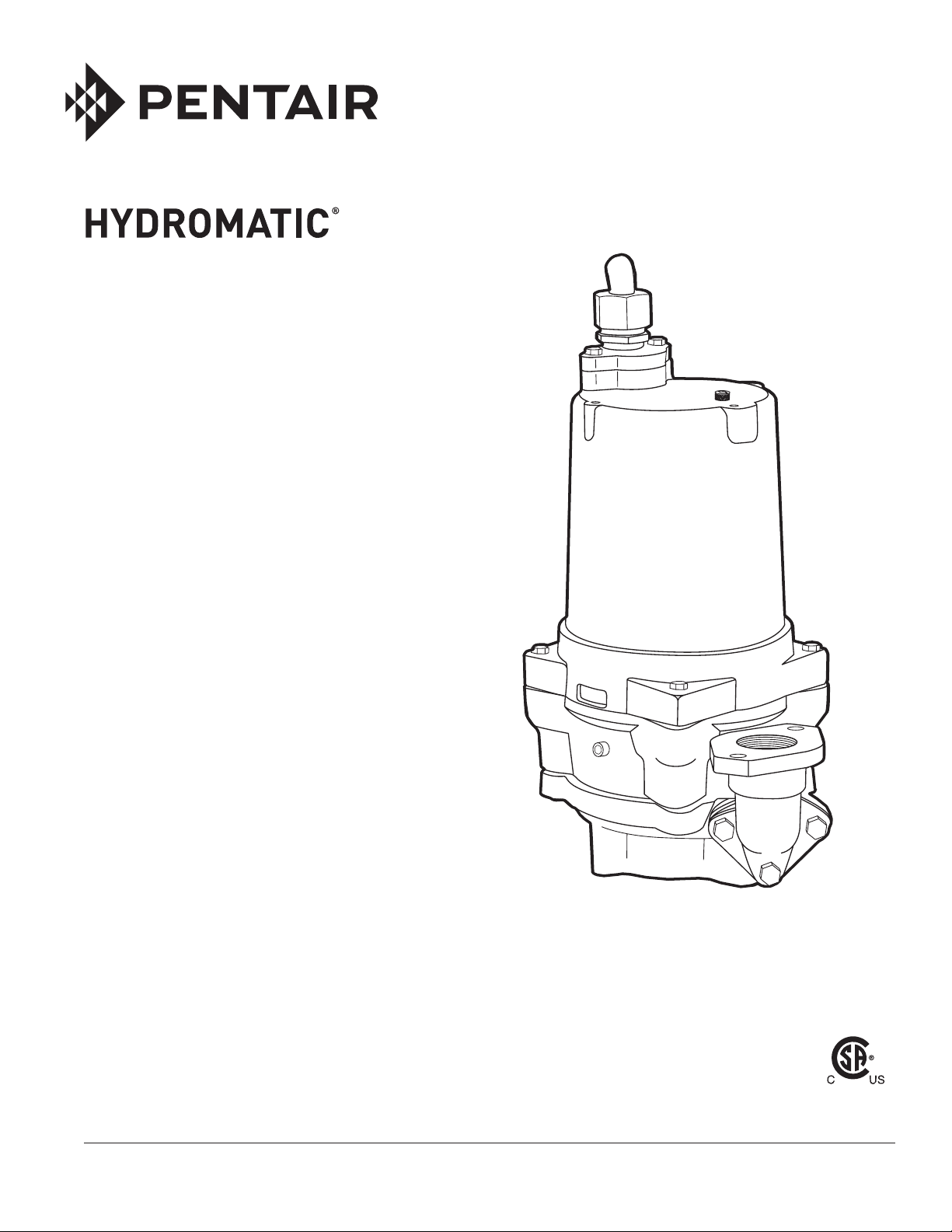
MODEL HPG200
ADVANCED SUBMERSIBLE
GRINDER PUMP
INSTALLATION AND SERVICE MANUAL
NOTE! To the installer: Please make sure you provide this manual to the owner of the equip ment or to the responsible
party who maintains the system.
Item # E-03-407 | Part # 5625-407-1 | © 2017 Pentair plc | 02/17/17
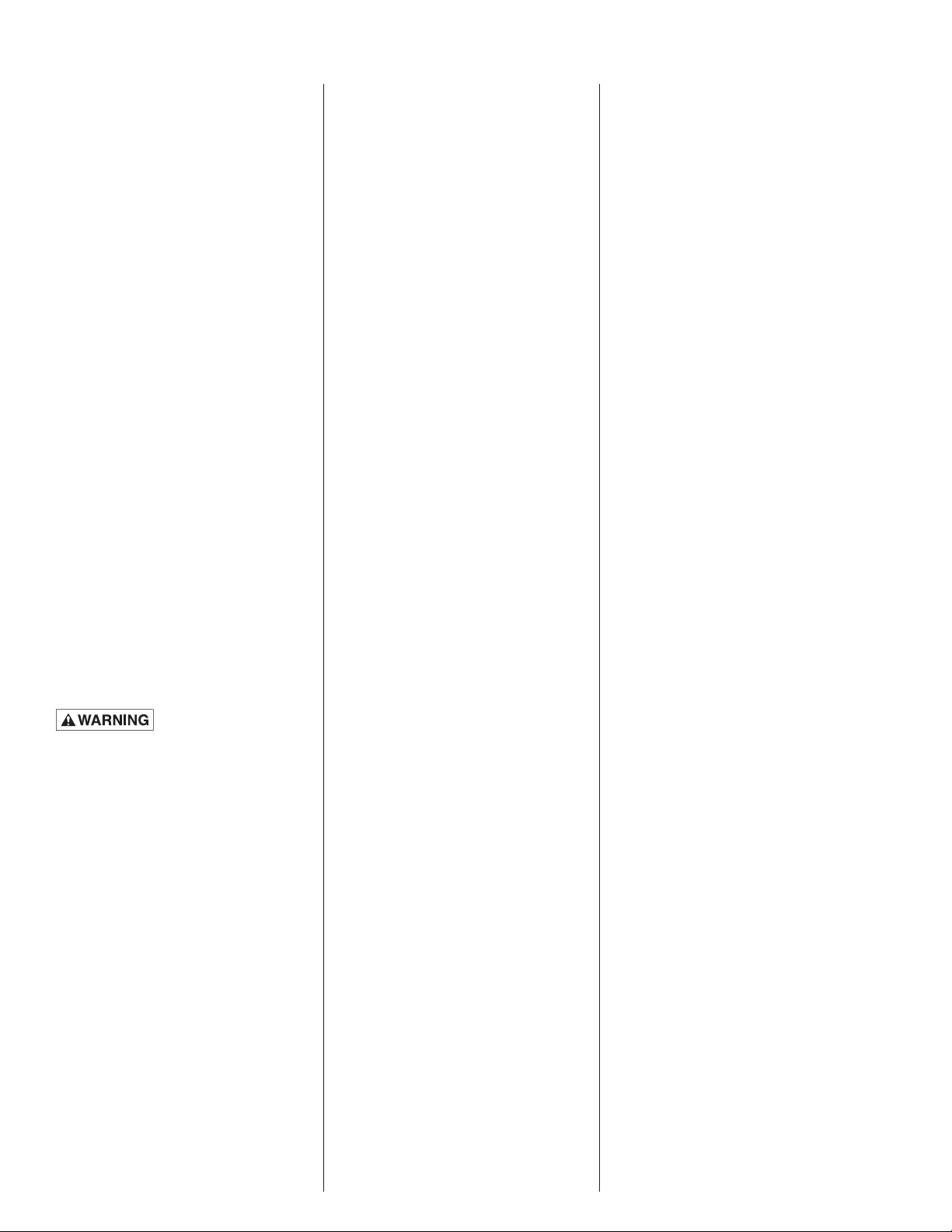
General
Information
Attention:
This manual contains important
information for the safe use of
this product. Read this manual
completely before using this
product and refer to it often for
con tin ued safe product use.
DO NOT THROW AWAY OR
LOSE THIS MAN U AL. Keep it in
a safe place so that you may refer
to it often. Reasonable care and
safe meth ods should be practiced.
Check local codes and
requirements before installation.
WARNING: Before handling
these pumps and controls, always
disconnect the power first. Do not
smoke or use sparkable electrical
devices or flames in a septic
(gaseous) or possible septic sump.
exists. Installer(s) and/or service
personnel must use proper personal
protective equipment and follow
handling procedures per OSHA
29 CFR 1910.1030 when handling
equipment after wastewater source
has been connected to system.
DANGER: Risk of Asphyxiation.
Installer(s) and/or service
personnel must use proper personal
protective equipment and follow
OSHA 29 CFR 1910.146 or OSHA
29 CFR 1926. Pump may be
installed in a location classified as
a confined space.
DANGER: Risk of Fire or
Explosion. Do not smoke or use
open flames in or around this
system. HPG200 systems are not
intended for use in hazardous
locations per NFPA 70: National
Electric Code. Do not pump
flammable liquids.
common. This specialized pump is
designed to incorporate a grinding
mechanism to remove wastewater
particulate and pump the resulting
slurry from a residential structure to
a collection system.
Examine all lifting devices, rope or
chain for damage before and after
each lift.
DO NOT exceed manufacturers
recommendation for maximum
performance, as this could cause
the motor to overheat.
Secure the pump in its operating
position so it cannot tip over, fall or
slide.
DO NOT pump without safety
devices in place.
Basin must be vented in accordance
with the local plumbing codes.
Pump Cautions
and Warnings
CALIFORNIA PROPOSITION
65 WARNING:
This product and
related accessories contain
chemicals known to the State of
California to cause cancer, birth
defects or other reproductive
harm.
DANGER: Risk of Electrical
Shock or Electrocution. May result
in serious injury or death or fire
hazard. Installer must disconnect
all electrical sources prior to
installation, handling or servicing.
Only qualified personnel may
install this system. NFPA 70:
National Electric Code
or local codes must be followed.
System must be properly grounded
according to NEC. Do not lift pump
by power cord.
DANGER: Biohazard Risk.
Once wastewater source has been
connected to system, biohazard risk
2
®
(NEC)
DANGER: Cutting Risk. Risk
of serious cutting or amputation
exists. Disconnect all power
sources prior to servicing pump or
grinding mechanism. Pump may
start without warning. Grinding
mechanism is extremely sharp.
Use caution when handling grinder
mechanism.
DO NOT modify the cord strain
relief. When wiring to a system
control, connect the pump ground
lead to the system ground.
DO NOT run the pump dry. Dry
running can overheat the pump
(causing burns to anyone handling
it) and will void the warranty.
The pump normally runs hot. To
avoid burns, allow it to cool for
30 minutes after shutdown before
handling it.
Submersible grinder pumps are
not approved for use in swimming
pools, recreational water
installations, decorative fountains
or any installation where human
contact with the pumped fluid is
The Pump
Pump Description:
The Hydromatic
covered by these instructions are
submersible grinder pumps.
The cutter blades are on the
suction side of the cen trif u gal pump
impeller and dis charge directly
into the inlet of the im pel ler. The
integral stain less steel pump motor
shaft is sealed by two me chan i cal
seals with an oil chamber between
the seals to pro vide lubrication for
both seal faces.
Two ball bearings are used to
handle the loads in this de sign,
similar to most of Hydromatic’s
solids handling pumps. The upper
bearing takes radial load, while
the larger lower bear ing handles
both thrust and radial loads.
Both bearings are permanently
lu bri cat ed by the dielectric oil in
the motor housing. The motor is
fixed within the motor housing and
is com plete ly submerged in the
di elec tric oil for maximum heat
transfer. The motor housing and
®
pumps
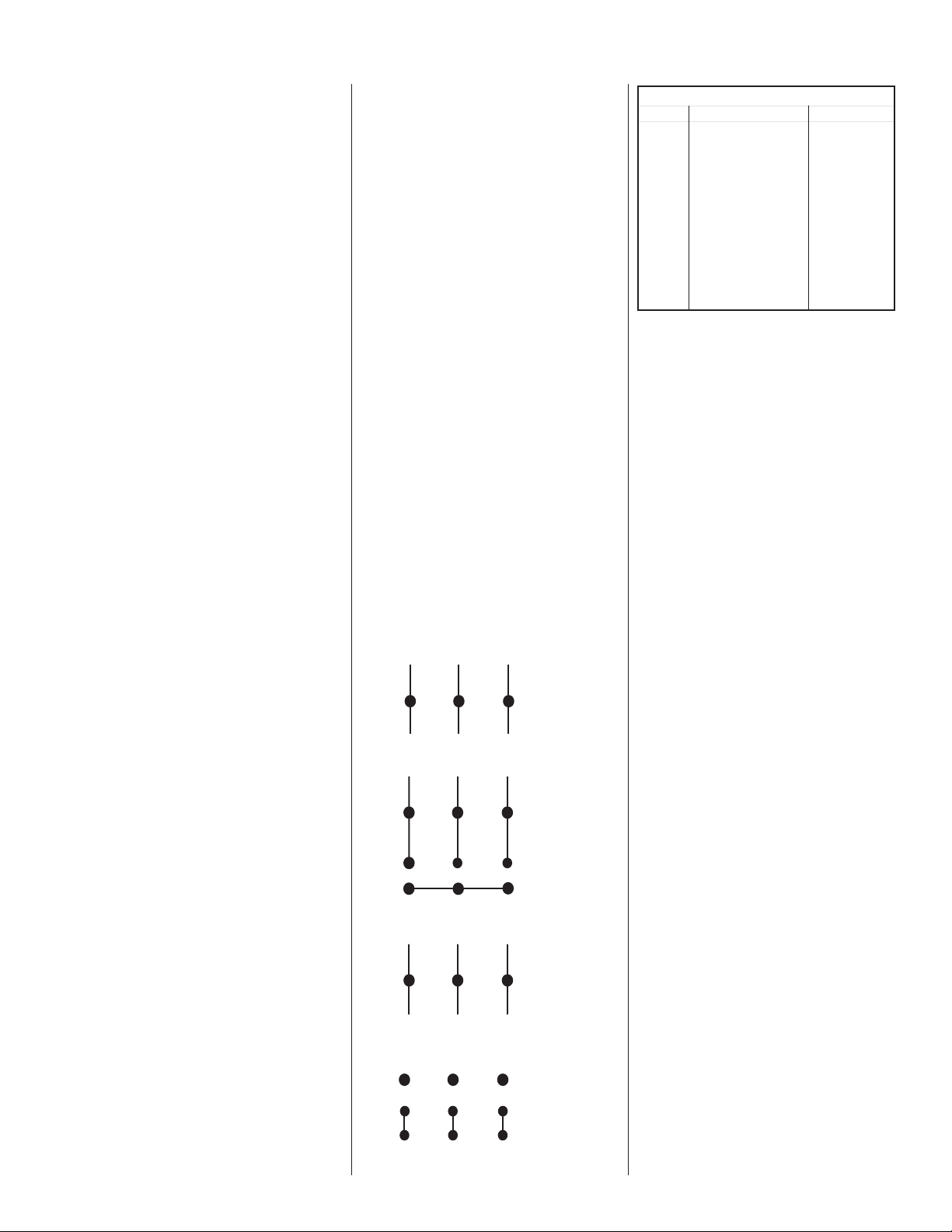
seal cham ber are com pletely sealed
WHITE W/BLACK STRIPE - P1
BLUE - P2
ORANGE - SEAL PROBE
SENSOR LEADS
208 - 230V SINGLE PHASE
T4
(WHITE) (BLACK) (RED)
T5 T8
BLACK
L2
WHITE
L1
RED
L3
P1 (PURPLE)
P2 (BROWN)
MOTOR LEADS
230V (DUAL VOLTAGE) THREE PHASE
P1 (PURPLE)
P2 (DARK BROWN)
T7
(PINK) (RED) (LT. BROWN)
(BLUE) (TAN) (ORANGE)
T8 T9
T1 T2 T3
T4
(YELLOW) (BLACK) (LAVENDER)
T5 T6
BLACK
L2
WHITE
L1
RED
L3
200V AND 575V THREE PHASE
T1
(BLUE) (TAN) (ORANGE)
T2 T3
BLACK
L2
WHITE
L1
RED
L3
P1 (PURPLE)
P2 (BROWN)
460V (DUAL VOLTAGE) THREE PHASE
PL (PURPLE)
P2 (DARK BROWN)
T7
(PINK)
(RED)
(LT. BROWN)
(BLUE) (TAN) (ORANGE)
T8 T9
T1 T2 T3
T4
(YELLOW) (BLACK) (LAVENDER)
T5 T6
BLACK
L2
WHITE
L1
RED
L3
with O-rings located at mating part
faces.
The power cord entry system is
designed to give double seal ing.
The chamfered pilot of the motor
housing mates with the molded
cord end to form the first seal. The
cord grip forms the second seal
around the molded cord end and
provides strain relief. The ca ble
on the HPG model includes the
leads for both heat sensors (motor
protection) and the seal sen sor lead
for seal leakage de tec tion.
The cutters are designed to be self
adjusting and will not need to be
shimmed or reset.
Application:
These pumps are designed for
either residential or industrial
sew age discharge ap pli ca tions
with a pH ranging from 5 to 9,
spe cif ic gravities from 0.9 to 1.1,
viscosities ranging from 28 to 35
S.S.U., and tem per a tures up to
140°F.
Codes:
All local wiring codes must
be observed. Consult the local
inspector before in stal la tion to
avoid costly delays that can
occur due to rejection after job
is finished.
Pump Installation
Unpacking Pump:
Remove pump from carton. When
un pack ing unit, check for
con cealed damage. Claims for
damage must be made at the
receiving end through the delivery
carrier. Dam age cannot be
processed from the factory.
Location:
If pumps are installed in an
existing basin or concrete sump,
the piping can either be connected
permanently or rails and brackets
can be fur nished for mounting to
walls of basin. In either case, be
sure that the Hydromatic
®
solids
handling check valve is used and
that the pumps are submerged in
a vertical position. The complete
factory built packaged system
is recommended for the most
satisfactory installation and
generally for the low est cost where
expensive instal la tion labor is
ELECTRICAL CONNECTIONS
1 Phase 3 Phase
Green Ground Ground
Red Start Power Line Power Line
White Main Power Line Power Line
Black Common Power Line Power Line
Orange Seal Failure Seal Failure
Blue Heat Sensor Heat Sensor
White Heat Sensor Heat Sensor
w/ black
stripe
involved.
Electrical Connections:
Make all connections from motor to
control panel to com ply with local
codes.
CAUTION: Make sure that
the ground wire is securely
connected and that the unit
Pump Operations
To reduce the risk of electrical
shock, install only on a GFCI
protected circuit. See pump
nameplate for electrical ratings.
To start the pump, perform the
following steps in order:
is properly grounded in
accordance with local codes.
1. When grinder pump is single
phase, no rotation check
is necessary. Correct rotation is
counter-clockwise.
2. Run water into sump until
motor is covered.
3. Open gate valve in discharge
line.
4. Turn pump on. If pump runs
and sump liquid does not pump
down, stop pump and close
discharge gate valve. Lift pump
until sealing ange is open to
vent off trapped air. Lower
pump, open discharge valve,
and start the pump again.
CAUTION: Positive displacement
pump is designed to operate at
minimum 5 GPM capacity. Running
pump at shut-off condition or with
gate valve closed can result in
damage to the pumping stator boot
and rotor.
5. Level control should be set so
that pump turns off when level
is about 2 inches above inlet
of pump suction and turns on
when level is about 2 inches
above motor.
3