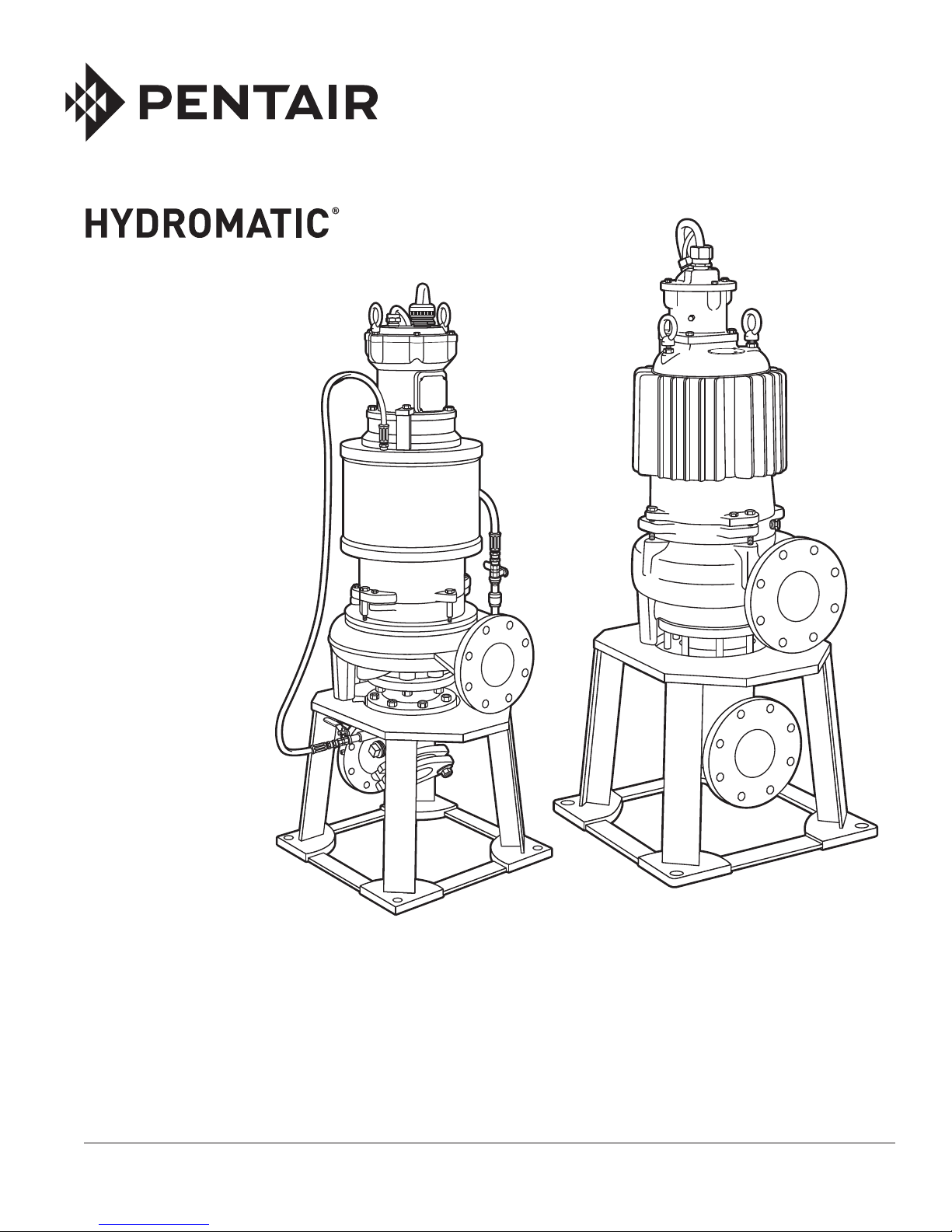
MODEL DRY PIT
SOLIDS HANDLING DRY PIT PUMPS
INSTALLATION AND SERVICE MANUAL
NOTE! To the installer: Please make sure you provide this manual to the owner of the equip ment or to the responsible
party who maintains the system.
Item # E-03-458 | Part # 5625-458-1 | © 2013 Pentair Ltd. | 11/11/13
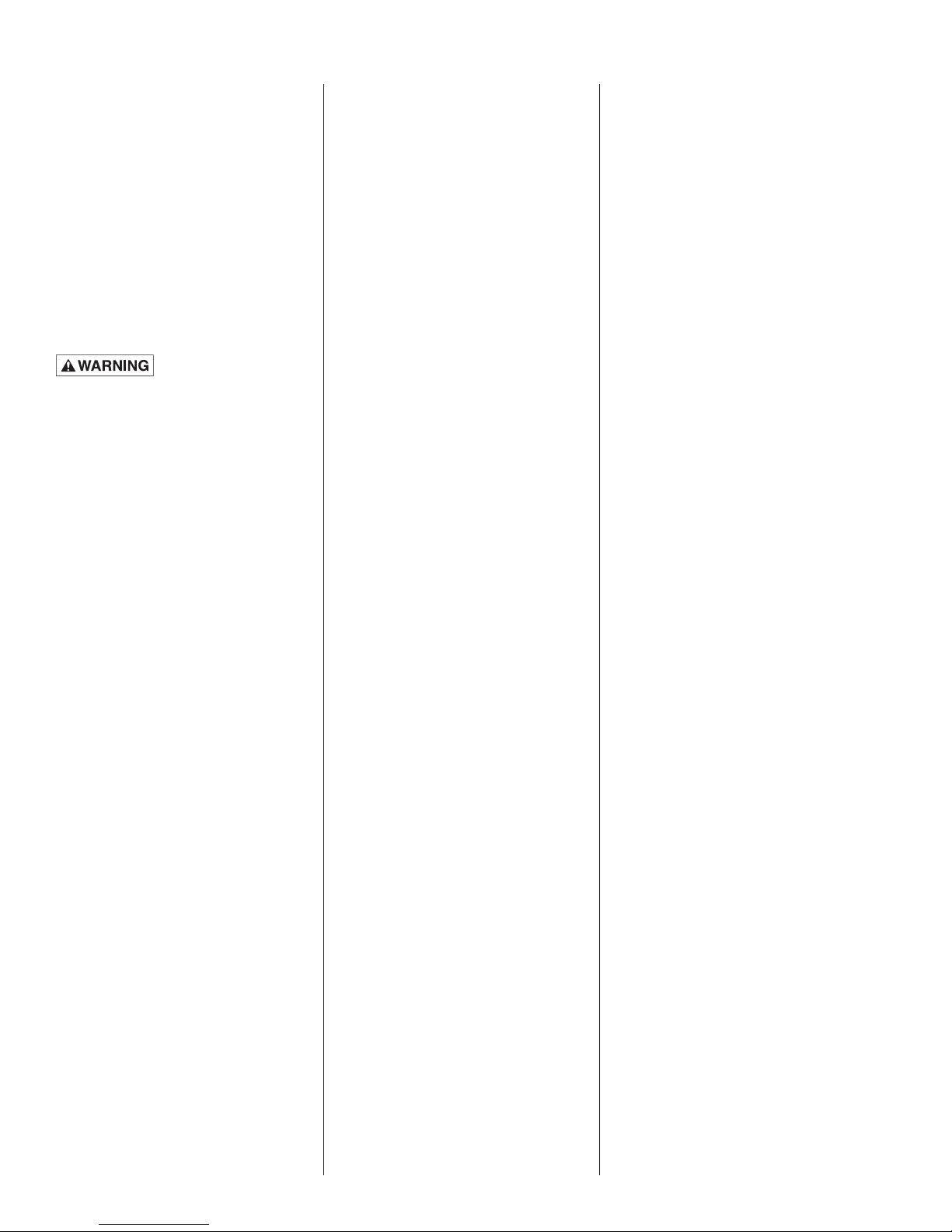
General
Information
Shipping:
When unpacking unit, check
for concealed damage. Claim
for damage must be made at the
receiving end through the delivering
carrier. Damage cannot be processed
from the factory.
CALIFORNIA PROPOSITION
65 WARNING:
This product
and related accessories contain
chemicals known to the State of
California to cause cancer, birth
defects or other reproductive harm.
Pumps Not Operating or in
Storage:
Pumps with carbon ceramic seals
must have impellers manually
rotated (6 revolutions) after setting
nonoperational for 3 months
or longer and prior to electrical
start-up.
Pumps with carbide seals must
have impellers manually rotated
(6 revolutions) after setting
nonoperational for 3 weeks
or longer and prior to electrical
start-up.
Seal Failure:
An electrode is installed in the
seal chamber so if water enters
the chamber through the first seal,
the electrode will be energized and
a signal will be transmitted to
the sensing unit at ground surface,
causing an alarm activation. The
electrode probe is installed in
all units, but the sensing unit is
supplied at an extra cost and must
be ordered.
In operation the seal failure unit
indicates only that there is some
water in the seal chamber. The pump
will continue to operate, but the
seal should be checked immediately
after failure is indicated.
2
The sensing unit is recommended on
all installations as good insurance
against motor failure.
Pump:
The dry pit submersible pump is
supplied for 1 or 3 phase and for
200, 230, 460 or 575 volts. Power
cable is supplied with green wire to
connect to a good ground such as
water pipe or ground stake.
Heat Sensors:
All motors have heat sensor units
embedded in the motor winding
to detect excessive heat. The heat
sensors are set to trip at 120ºC. The
sensors automatically reset when
the motor cools to safe temperature.
The sensors are connected in
series with the motor starter coil
so that the starter is tripped if heat
sensor opens. The motor starter is
equipped with overload heaters so
all normal overloads are protected
by the starter.
IMPORTANT: If Hydromatic
electrical starting equipment
is not supplied, the heat sensor
circuit must be connected in
series with the starter coil or
warranty is void.
Wet Well Level Control:
Sump level is controlled by
Hydromatic switch controls. The
float is held in position in the sump
by a weight attached to the power
cord above the float. The cord
supports the float and is adjusted
for height from the surface.
Duplex systems use three controls:
one set at turn-off, one set at turnon for one pump, and one set at
turn-on for both pumps. Pumps
then alternate lead and lag on each
successive cycle. Two pumps
operate together only when the
sump level rises to the third or
override control. The override
control also brings on the second
pump in case of failure of the first
pump. Extra floats with appropriate
®
controls can be supplied for alarm
functions. Triplex systems use four
controls: One set at turn-off, one
set at turn-on for one pump, one
set at turn-on for two pumps, and
one set at turn-on for three pumps.
The pumps alternate with each
successive cycle.
Three pumps operate together only
if the sump level rises to the fourth
control (second override). This
control also brings on the third
pump in case of failure of either or
both of the first two pumps.
Alarm Controls:
The alarm level is usually set above
the override level so the alarm
will signal only if the override
level is exceeded. However, some
engineers prefer to have the alarm
level set below the override level
as it is possible for one pump to
fail and the other pump to operate
on the override level with the sump
level never reaching the alarm level.
This is particularly true in cases of
low inflow capacity.
Electrical Control Panel:
It is recommended that the
Hydromatic control panel be used
with all pumps as proper starter
heaters and connections for heat
sensor wires are furnished.
Hydromatic electrical equipment
is installed in a weatherproof
NEMA 3R enclosure. The electrical
equipment includes a main circuit
breaker for each pump, a magnetic
starter with overload protection for
each pump, an H-O-A switch and a
run light for each pump, an electrical
alternator and a transformer to
provide appropriate control for
control circuit and alarms.
Overload Heaters:
Starters with 3 leg overload
protection must be supplied if the
Hydromatic electrical panel is not
used. The heaters must be sized
in accordance with the nameplate
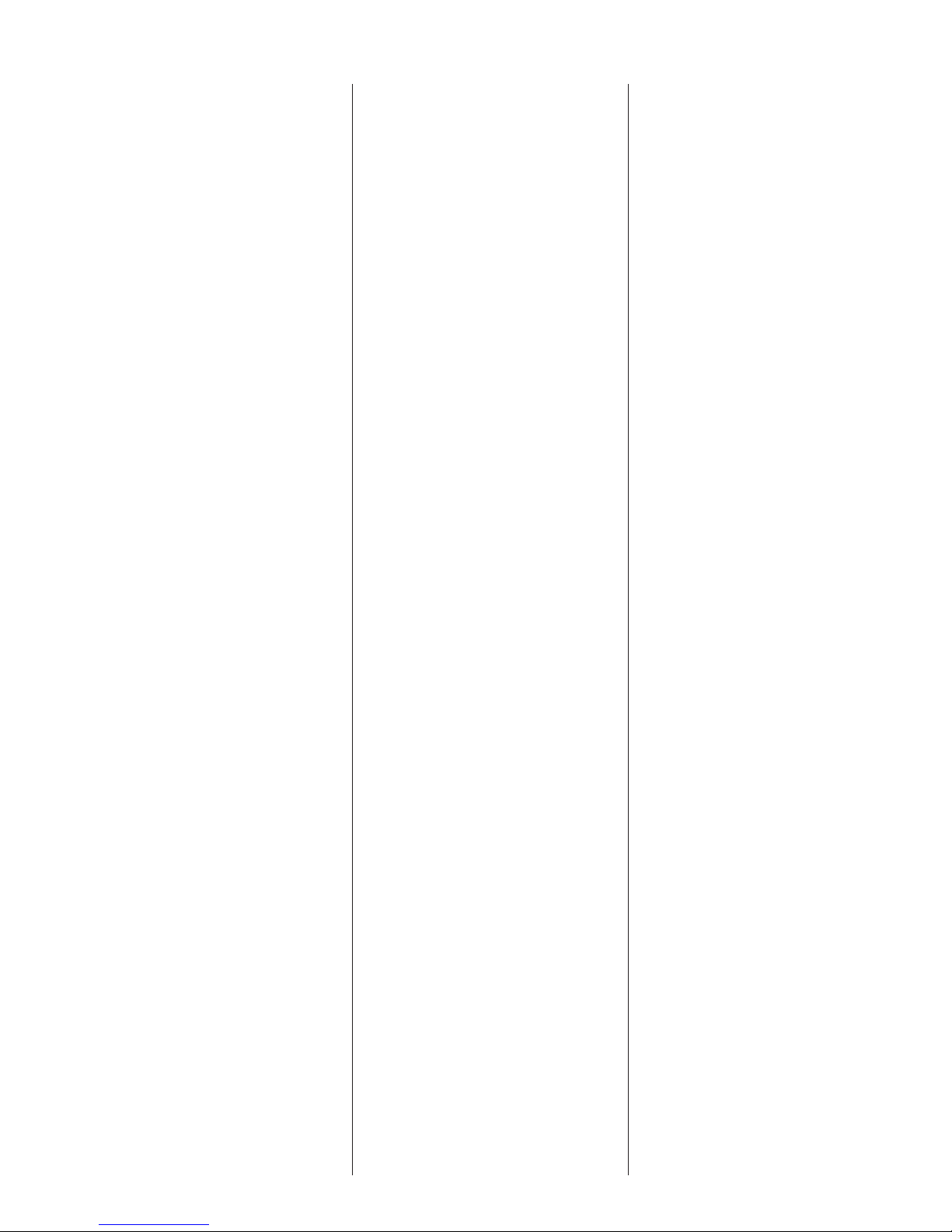
amps on the motor. The amp
draw on these oil-filled motors
is slightly higher than a
corresponding horsepower surface
motor, so heaters must be sized by
the nameplate rating.
Installation
Instructions
Installing Pump in Dry Pit:
Before installing pump in the dry pit,
lay it on side and turn the impeller
manually. The impeller may be
slightly stuck due to factory water
testing, so it must be broken loose
with a small bar or screwdriver in
the edge of the vanes. The impeller
must turn freely.
Clean all trash and debris from
pump installation area and connect
pump to plumbing.
A check valve must be installed on
each pump. A gate or plug valve
in each pump discharge line is also
recommended. This valve should
be installed on the discharge side of
the check valve so the line pressure
can be cut off to service the check
valve. Single pump systems are
sometimes installed without a
check valve where it is desirable
to self drain the discharge line to
prevent freezing. This can be done
only with short discharge lines.
Otherwise water will return to the
sump and cause short cycling of
the pump.
Mounting Pump Stand:
The pump will ship from the
factory on a dry pit pump stand.
The suction and discharge of the
pump will be oriented at the factory
per the prescribed customer order.
The dry pit pump must be anchored
to the pump station floor. This
must be done to alleviate stress on
the suction and discharge piping
while the pump is in service. When
securing the pump stand to the
contractor supplied anchor bolts, it
may be necessary to shim the stand
to ensure the suction and discharge
piping properly aligns.
Plumbing (General):
The site contractor must supply
the use of necessary pipe hangers
or other piping supports. Both the
suction and discharge piping must
be independently supported and
properly aligned to ensure no strain
is transmitted to the pump when
connections are tightened. The use
of expansion joints or vibration
pads does not preclude the need to
properly support the piping.
NOTE: Do not support the piping
by the pump. Do not force piping
when making connections.
Suction-Inlet Piping:
The correct sizing and installation
of the suction plumbing is
particularly important. The suction
piping must be selected and
installed in such a manner that
it minimizes pressure losses and
allows for sufficient flow during
starting and operation. Most NPSH
problems can be traced directly
to improper design of suction
piping systems.
It is recommended that the piping
be as direct as possible and the
length should be at least 10 times
the diameter of the pipe. When
a pipe diameter larger than the
suction of the pump is used, an
eccentric reducer should be used
with the eccentric side down.
This will allow for the elimination
of a potential air pocket in the
suction plumbing.
NOTE: A pipe diameter smaller
than the suction of the pump
must never be used.
It is also recommended that a valve
be installed in the suction piping
to isolate the pump during routine
maintenance and shutdown. A
globe valve should not be used
when NPSH is critical.
It is recommended that a
compound pressure gauge be
installed in the suction piping to
assist in troubleshooting potential
performance problems.
Discharge-Outlet Piping:
The discharge piping for short
runs can be of the same size as
the discharge of the pump. It is
recommended that longer runs be
1 to 2 sizes larger depending on
the length. Any elevated points
will retain air pockets, and it is
recommended that air vents or
bleed lines be installed at these
points to evacuate the entrapped
air. Installation of a valve near
the discharge of the pump is
recommended to isolate the pump
during maintenance and shutdown.
It is recommended that a pressure
gauge be installed near the
discharge of the pump to
assist in troubleshooting potential
performance problems.
NEMA 4 Junction Box
(Optional):
A NEMA 4 junction box should
be used to make power and control
connections if electrical control
panel is to be set remote from
the pump station. The Hydromatic
NEMA 4 junction box is provided
with compression connections
for sealing all wires. No sealing
compound is needed to make
connections waterproof.
Wiring diagrams are provided with
the panel for making connections.
An extra set of diagrams is included
so that one set can be used in the
station when making connections.
The size wire to use from panel to
station depends on motor size and
distance in feet.
Be sure each wire is checked out so
that a wrong connection will not be
made. An ohmmeter or Megger can
be used to check the continuity.
®
3