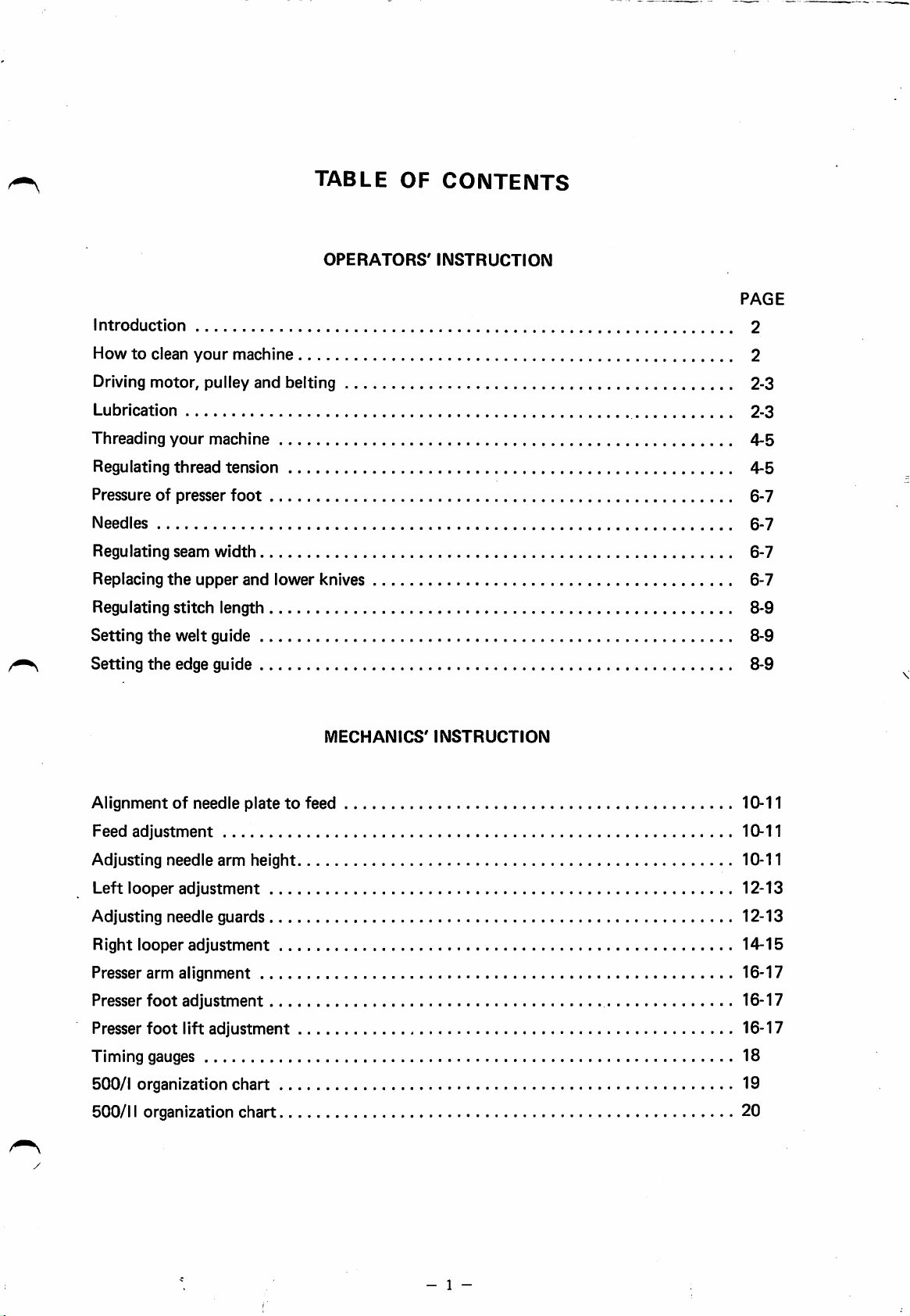
TABLE
OF
CONTENTS
Introduction
Howtoclean
Driving
Lubrication
Threading
Regulating
Pressureofpresser
Needles
Regulating
Replacing
Regulating
Setting
Setting
motor,
your
thread
seam
the
stitch
the
welt
the
edge guide
your
pulley and belting 2-3
machine
width
upper
guide 8-9
machine
tension
foot
and
length
OPERATORS'
INSTRUCTION
PAGE
2
2
2-3
4-5
4-5
6-7
6-7
6-7
lower knives 6-7
8-9
8-9
Alignmentofneedle
Feed
adjustment
MECHANICS'
platetofeed 10-11
INSTRUCTION
10-11
Adjusting needle arm height 10-11
Left
looper
adjustment
12-13
Adjusting needle guards 12-13
Right looper
Presser
Presser
Presser
arm
foot
foot
adjustment
alignment
adjustment
lift
adjustment
14-15
16-17
16-17
16-17
Timing gauges 18
500/1 organization
500/11 organization
chart
chart
19
20
- 1 -
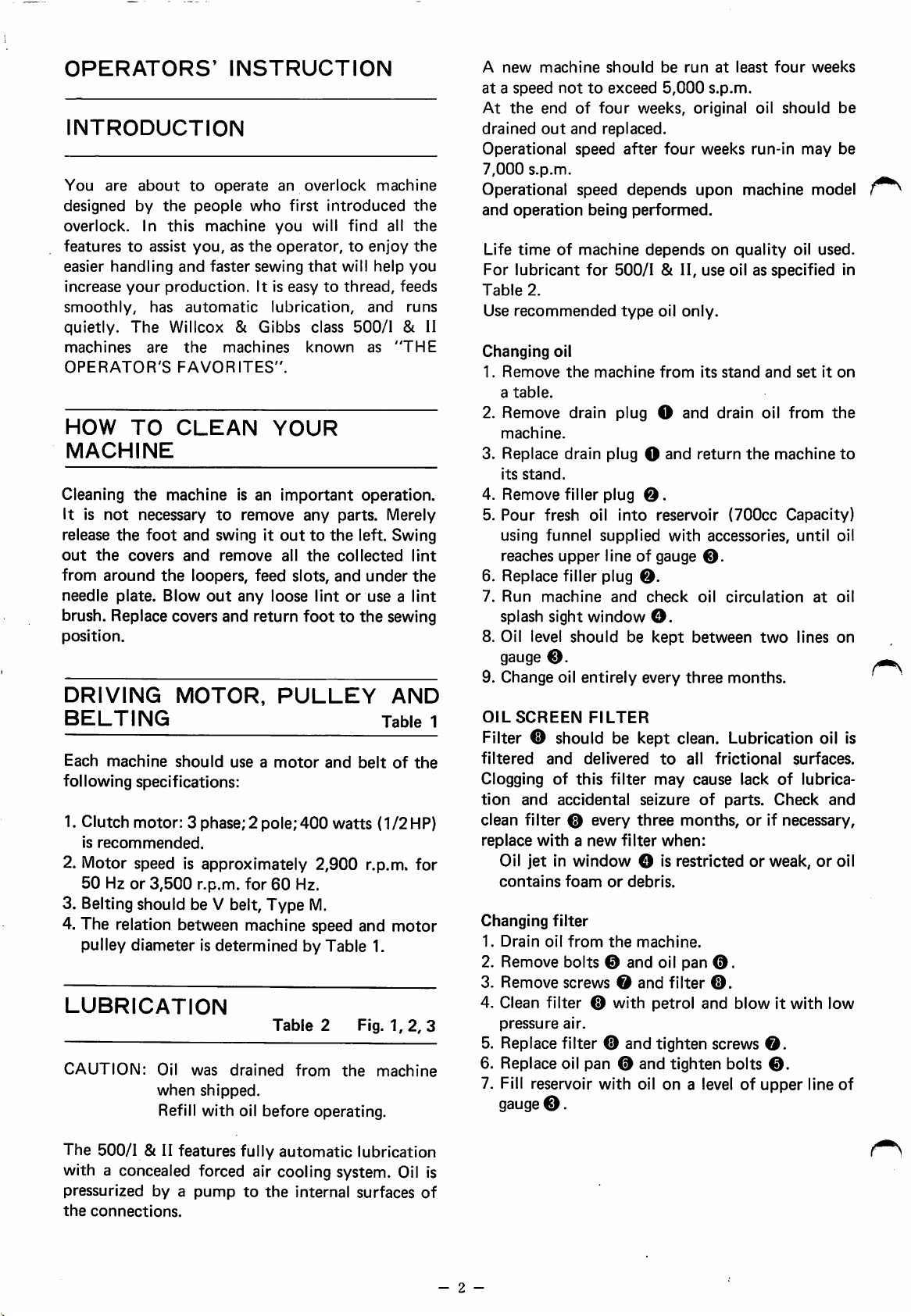
OPERATORS'
INSTRUCTION
INTRODUCTION
You
are
about
designed
overlock.
by
featurestoassist
easier
handling
increase
smoothly,
quietly.
machines
OPERATOR'S
HOW
your
The
TO
to
the
In
this
and
production.
has
automatic
operate
people
machine
you,asthe
faster
an
overlook
who
first
introduced
you
will
operator,toenjoy
sewing
It is
that
easytothread,
lubrication,
find
will
Willcox & Gibbs class 500/1 &
are
the
machines
FAVORITES".
CLEAN
known
YOUR
machine
all
help
feeds
and
as
"THE
the
the
the
you
runs
MACHINE
Cleaning
It is
release
out
from
needle plate. Blow
brush. Replace covers and return
position.
DRIVING
BELTING
Each
following specifications:
1. Clutch motor: 3 phase; 2 pole;
is
2. Motor speed is approximately 2,900 r.p.m. for
50 Hz or
3. Beltingshould be V belt. Type
4. The relation between machine speed and
pulley diameter is determined by Table 1.
LUBRICATION
CAUTION:
the
machine is an
not
necessary
the
foot
the
covers
around
machine
recommended.
the
3,500
Oil
when
Refill with oil before operating.
important
to
remove
and
and
swing it
remove
outtothe
all
loopers, feed slots,
out
any
loose
MOTOR,
should
useamotor
r.p.m. for
was
drained
PULLEY
60
Table
shipped.
any
parts. Merely
the
collected
and
lintoruse a
foottothe
and
400
watts {112HP)
Hz.
M.
2 Fig.
from
the
operation.
left. Swing
lint
under
the
lint
sewing
AND
Table 1
beltofthe
motor
1,2,
machine
11
3
A
new
machine
ataspeed
At
the
drained
nottoexceed
end
out
Operational
7,000
s.p.m.
Operational
and
operation
Life
time
of
For
lubricant
Table
2.
Use
recommended
Changing
1.
Remove
a
oil
table.
2. Remove drain plug O and drain oil from
machine.
3. Replace
its
stand.
4. Remove filler plug
5.
Pour
fresh oil
using
funnel
reaches
upper
6. Replace filler plug
7.
Run
machine
splash sight
8. Oil level
gauge
©.
9. Change oil
OIL
SCREEN
of
and
speed
speed
being
machine
for
the
drain
window
should
entirely
FILTER
four
machine
supplied
should
be
5,000
weeks,
run
at
least
s.p.m.
original oil
four
should
weeks
replaced.
after
four
depends
weeks
upon
run-in
machine
may
model
performed.
depends
on
quality
oil
used.
500/1 & II, use oil as specified in
type
oil
only.
from
its
stand
and
setiton
plug O
and
return
the
machine
0.
into
reservoir
with
line of gauge
(700cc
accessories,
0.
Capacity)
until
0.
and
check
oil
circulation
at
O.
be
kept
every
between
three
two
months.
lines
be
be
the
to
oil
oil
on
Filter 0 should be kept clean. Lubrication oil is
filtered
Clogging
tion
clean
replace
Changing
1.
2. Remove bolts 0 and oil pan
3.
4. Clean filter 0 with petrol and blow it with low
5. Replace filter 0 and tighten screws
6. Replace oil pan 0 and tighten bolts
7. Fill reservoir
and
of
and
accidental
filter
withanew
Oil
jetinwindow
contains
filter
Drain
oil
Remove
pressure
gauge
0.
delivered
this
filter
seizure
0 every
three
filter
O is restrictedorweak,oroil
foam
or
debris.
from
the
machine.
screws0and
air.
with
oil on a levelofupper
to
all
frictional
may
cause lack
of
parts.
of
Check
months,orif necessary,
when:
©.
filter
0.
0.
0.
surfaces.
lubrica
and
line
of
The 500/1 & II features fully automatic lubrication
with a concealed forced air cooling system. Oil is
pressurized by a
the
connections.
pump
to
the
internal
surfaces
of
- 2 -
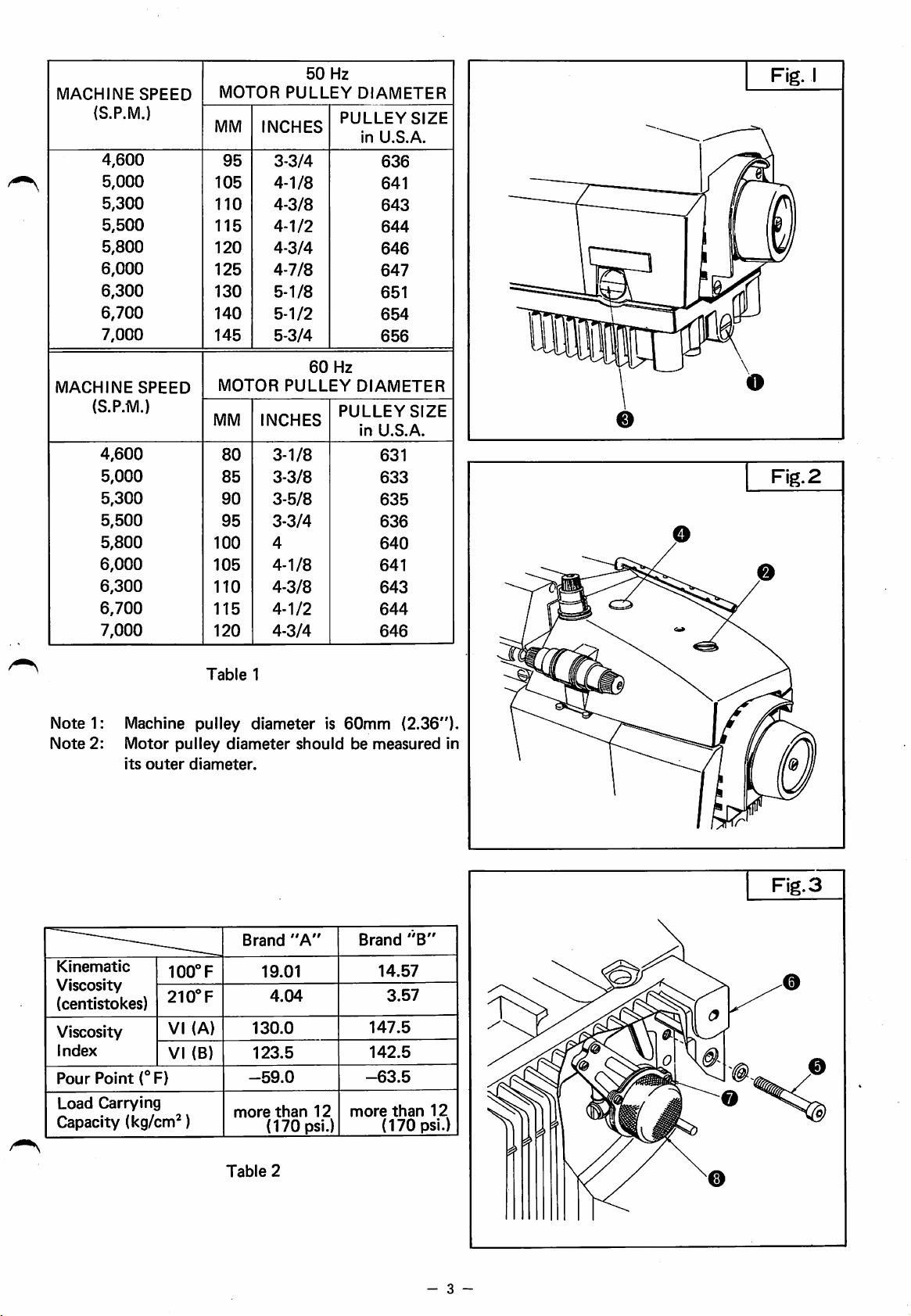
MACHINE
(S.P.M.)
4,600
5,000
5,300
5,500
5,800
6,000
6,300
6,700
7,000
MACHINE
(S.P.M.)
4,600
5,000
5,300
5,500
5,800
6,000
6,300
6,700
7,000
SPEED
SPEED
MOTOR
MM
95
105
110
115
120
125
130
140
145
MOTOR
MM
80
85
90
95
100
105
110
115
120
PULLEY
INCHES
3-3/4
4-1/8
4-3/8
4-1/2
4-3/4
4-7/8
5-1/8
5-1/2
5-3/4
PULLEY
INCHES
3-1/8
3-3/8
3-5/8
3-3/4
4
4-1/8
4-3/8
4-1/2
4-3/4
50
60
Hz
DIAMETER
PULLEY
in
Hz
DIAMETER
PULLEY
in
U.S.A.
636
641
643
644
646
647
651
654
656
U.S.A.
631
633
635
636
640
641
643
644
646
SIZE
SIZE
Fig.
Fig.
I
2
Notel:
Note
Kinematic
Machine pulley diameter is
2:
Motor
its
outer
Viscosity
(centistokes)
Viscosity
Index
Pour
Point
(®F)
Load
Carrying
Capacity (kg/cm^)
pulley
diameter.
lOO^F
210®F
VI
(A)
VI (B)
Table
diameter
more
1
Brand
19.01
130.0
123.5
-59.0
(170
4.04
than
should
"A"
12
psi.)
60mm
{2.36").
be measured in
Brand
more
14.57
147.5
142.5
-63.5
(170
3.57
than
"B"
12
psi.)
Fig.
3
Table
2
- 3 -
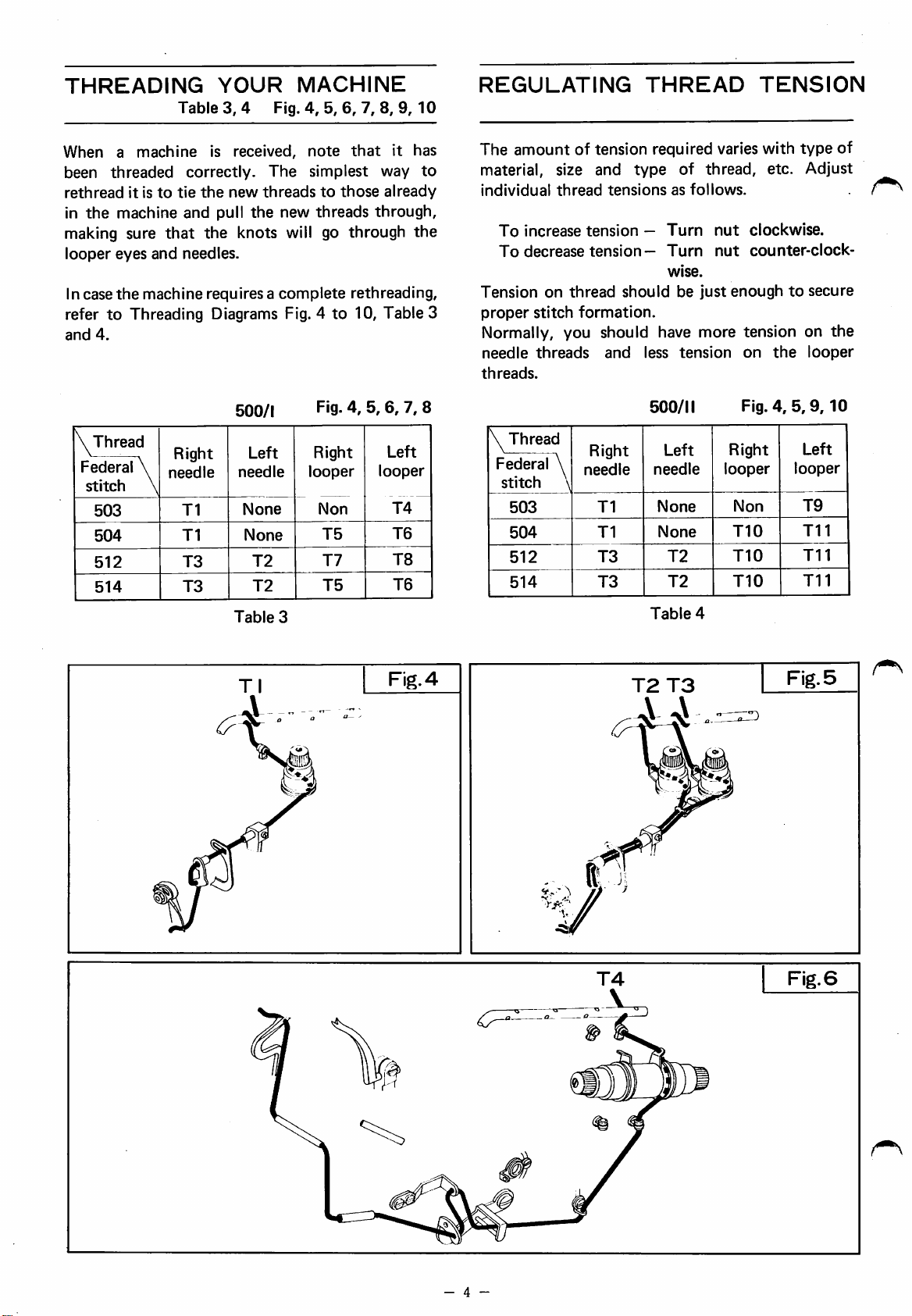
THREADING
When
been
rethread
in
making sure
looper
In case
refer
and
a
machine
threaded
it istotie
the
machine
eyes
and
the
machine
to
Threading Diagrams Fig. 4 to 10, Table 3
4.
YOUR
MACHINE
Table3,4 Fig.4,5,6,7,8,9,
is received,
correctly.
the
new
and
pull
the
that
the knots will go through
note
that
The
simplest
threadstothose
new
threads
needles.
requires a
complete
rethreading,
10
it
has
way
to
already
through,
the
REGULATING
The
amount
material, size and
individual
To
increase
To
decrease
Tension
proper
of tension required varies with
thread
tension
tension—
on
thread
stitch
formation.
type
tensions
—
should
THREAD
of
thread,
as
follows.
Turn
Turn
wise.
be
just
TENSION
type
etc. Adjust
nut
clockwise.
nut
counter-clock
enoughtosecure
Normally, you should have more tension on
needle
threads.
threads
and
less
tension
on
the
of
the
looper
Thread
Federal
stitch
503
504
512
514
Right
looper
4
Fig.4,5,9,10
Left
looper
Non
T10
T10
T10
T9
Til
Til
Til
500/1
Right
\
needle
Left
needle
Fig.4,6,6,7,
Right
looper
\
T1
T1
T3
T3
None
None
T2
T2
Table
Tl
Non
T5
T7
T5
3
Left
looper
T4
T6
T8
T6
Fig.
8
\
Thread
Federal \
stitch
503
504
512
514
Right
needle
\
T1
T1
T3
T3
4
T2
500/11
Left
needle
None
None
T2
T2
Table
T3
- 4 -
Fig.
6
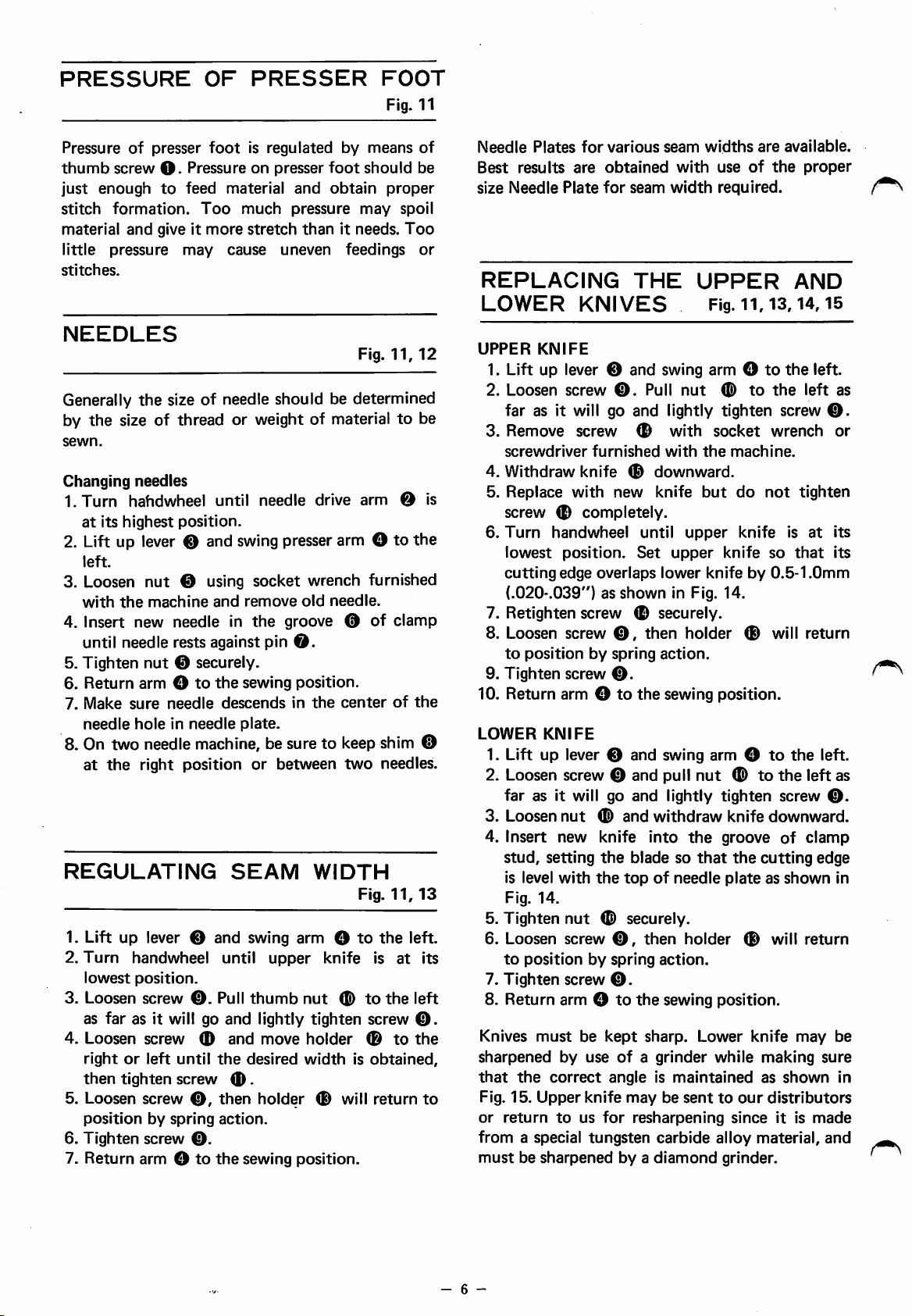
PRESSURE
OF
PRESSER
FOOT
Fig.
11
Pressure
thumb
just
stitch
material
little
stitches.
of
screw
enough
formation.
and
pressure
presser
Oto
give it
foot
Pressureonpresser
feed
material
Too
more
may
cause
is regulated by
foot
and
obtain
much
stretch
pressure
thanitneeds.
uneven
means
should
proper
may
feedings
spoil
Too
NEEDLES
Fig.
11,12
Generally
by
the
sewn.
Changing
1.Turn
at
2. Lift up
left.
3. Loosen
with
4. Insert new needle in
until needle rests against pin
5. Tighten
6.
Return
7.
Make
needle
the
size of needle should be determined
size of thread or weight of material
needles
hahdwheel
its
highest
the
lever
nut
machine
until
position.
0 and
0 using
and
needle
swing
socket
remove
the
drive
presserarm O to the
wrench furnished
old
needle.
groove 0
0.
nut
0 securely.
arm O
sure
holeinneedle
to
needle
the
sewing
descends
plate.
position.
in
the
arm
center
of
to
0 is
clamp
of
the
8. On two needle machine, be sure to keep shim ©
at
the
right position
REGULATING
1. Lift up lever 0 and swing arm O
2.
Turn
lowest
3. Loosen
as
4.
Loosen
rightorleft
then
5. Loosen
positionbyspring
6.
Tighten
handwheel
position.
screw
far
as it will go
screw
tighten
screw
screw
©.
0
until
screw
0,
0.
7. Return arm Otothe
or
between
SEAM
until
upper
Pull
thumb
and
lightly
and
move
the
desired
0.
then
holder
action.
sewing position.
two
needles.
WIDTH
Fig.
11,13
to
the
left.
knife
nut
tighten
holder
widthisobtained,
0 will
is
at
©
to
the
left
screw
©
to
0.
the
return
be
of
or
be
its
to
Needle
Best
size
REPLACING
LOWER
UPPER
Plates
results
Needle
KNIFE
for
various
are
obtained
Plate
for
KNIVES
seam
THE
seam
with
width
widths
use
required.
UPPER
Fig.
ii,
are
of
the
13,14,15
1. Lift up lever 0 and swing arm Otothe
2.
Loosen
screw
0.
Pull
nut
©
to
the
far as it will go and lightly tighten screw
3.
Remove
screwdriver
4.
Withdraw
5.
Replace
screw
6.
Turn
lowest
cutting
(.020-.039")asshown
screw
furnished
knife
with
0
completely.
handwheel
position.
edge
overlaps
0
©
new
Set
with
with
downward.
knife
until
upper
upper
lower
in Fig. 14.
socket
the
but
knifeby0.5-1.0mm
machine.
do
knife
knife
wrench
not
so
7. Retighten screw 0 securely.
8. Loosen
to
9.
Tighten
10. Return arm Otothe
LOWER
1. Lift up lever 0 and swing arm O
2. Loosen screw 0 and pull
far
3.
Loosen
4.
Insert
stud,
is level
Fig.
5. Tighten
6. Loosen
to
7.
Tighten
8. Return arm O
Knives
sharpened
that
Fig. 15.
or
return
from
mustbesharpened
screw
0,
positionbyspring
screw
KNIFE
0.
as it will go
nut
©
and
new
knife
setting
14.
positionbyspring
with
nut
screw
screw
the
the
topofneedle
© securely.
©,
0.
to
must
be
kept
by
useofa
the
correct
Upper
to
a special
angleismaintained
knife
maybesenttoour
us
for
tungsten
byadiamond
then
holder
action.
sewing position.
nut
and
lightly
withdraw
into
the
blade so
then
the
sharp.
resharpening
that
holder
action.
sewing position.
Lower
grinder
carbide
© will
to
©
to
tighten
knife
downward.
groove
the
cutting
plateasshown
© will
knife
while
making
as
distributors
since
it is
alloy
material,
grinder.
available.
proper
AND
left.
left
tighten
is
at
that
return
the
the
left as
screw
of
clamp
edge
return
may
shown
made
as
0.
or
its
its
left.
0.
in
be
sure
in
and
- 6 -