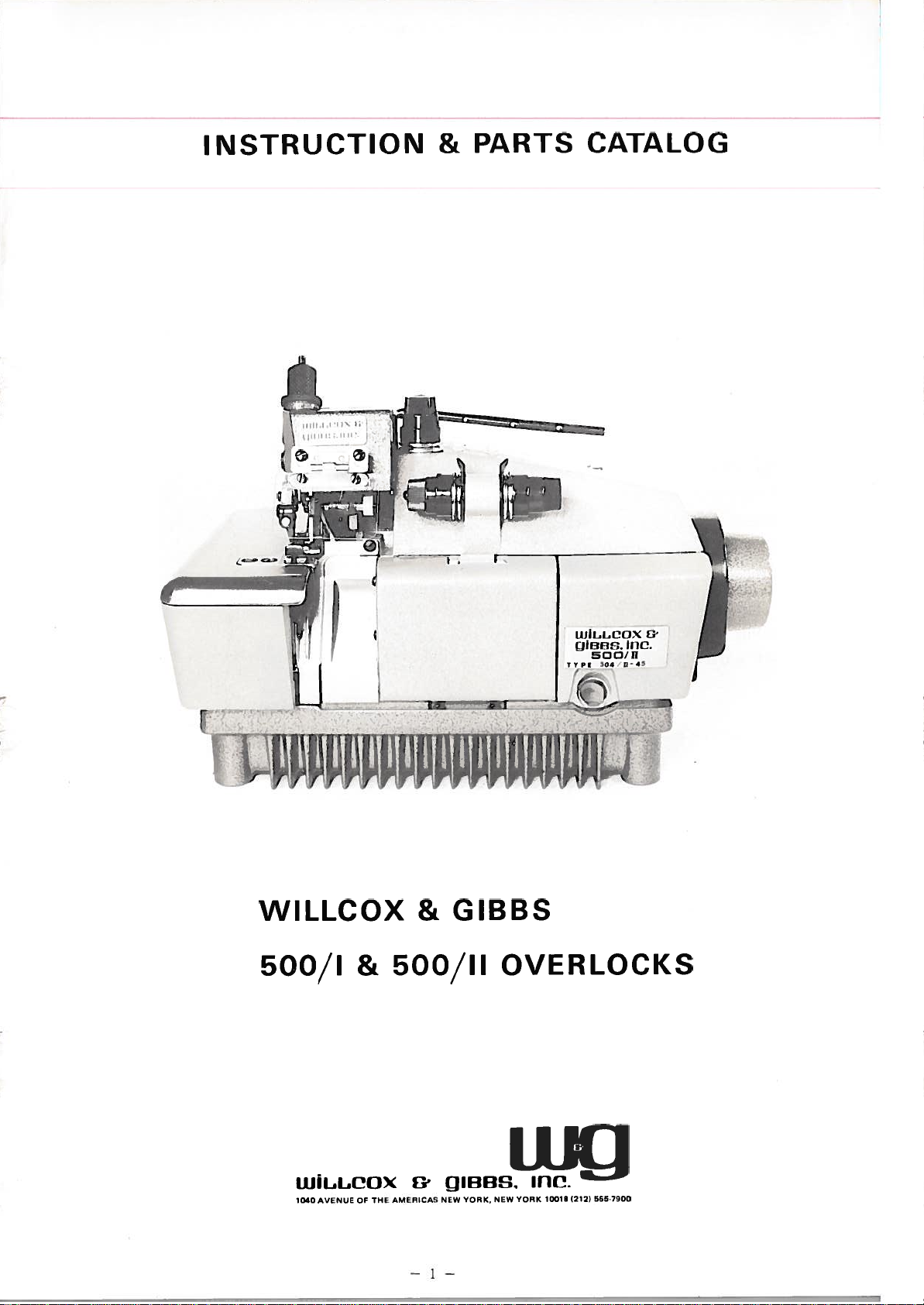
INSTRUCTION
PARTS
&
CATALOG
-
:
r
GIBBS
WILLCOX
500/I
&
&
500/Il
OVERLOCKS
WILLCOX
1040
AVENUE
OF
THE
8’
AMERICAS
—1
gIBrn!’!!°
YORK.
NEW
NEW
YORK
10018
(212)
565-7900
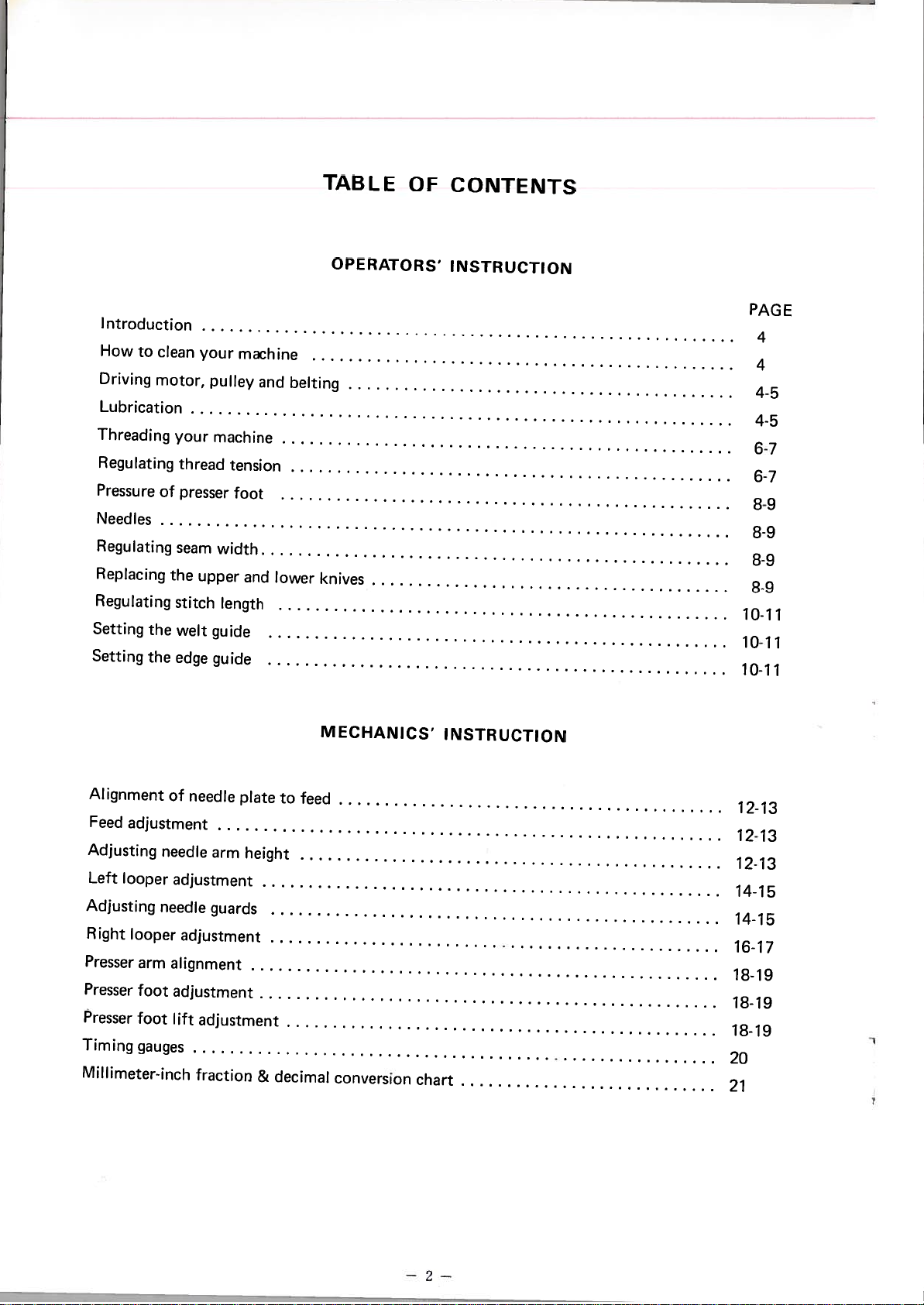
TABLE
OF
CONTENTS
Introduction
How
to
Driving
Lubrication
Threading
Regulating
Pressure
Needles
Regulating
Replacing
Regulating
Setting
Setting
the
the
clean
motor,
your
thread
of
presser
seam
the
stitch
welt
edge
your
pulley
machine
width
upper
length
guide
guide
machine
and
tension
foot
and
belting
lower
OPERATORS
knives
INSTRUCTION
PAG
4
4
4-5
4-5
6-7
6-7
8-9
8-9
8-9
8-9
10-11
10-1
10-11
E
1
Alignment
Feed
Adjusting
Left
looper
Adjusting
Right
Presser
Presser
Presser
Timing
of
adjustment
needle
needle
looper
arm
alignment
foot
foot
gauges
Millimeter-inch
needle
arm
adjustment
guards
adjustment
adjustment
lift
adjustment
fraction
plate
height
&
to
feed
decimal
MECHANICS’
conversion
INSTRUCTION
chart
12-13
12-13
12-13
14-15
14-15
16-17
18-19
18-19
20
21
1
—2—

Mdclii
iC
Ma
n
Irarne
Crankshalt
Needle
Right
Right
Left
Main
Upper
Presser
(1)
(2)
Plain
Attachments
Chain
Suction
Mounting
Accessories
Thread
drive
looper
looper
looper
and
and
foot
Pump
Pump
feed
cutter
stand
bed
[raine
and
niechanisrn
mechanism
drive
drive
drive
diflerential
lower
and
lubricating
lubricating
mechanism
models
device
accessories
miscellaneous
mechanism
mechanism
mechanism
feed
knife
mechanism
lifting
mechanism
mechanism
KSR-570,
model
VSA-200
covers
for
for
mechanism
mechanism
KSR-571
for
PARTS
500/I
500/Il
chain
and
cutter
LIST
KSR-572
SECTION
503/I&11-4,
503/I
PAGE
22-23
24-25
26-27
28-29
30-31
32-33
34-35
36-37
38-39
40-41
42-43
44-45
11-8
&
46-47
48-49
50-51
52-53
54-55
56-57
58-59
504/1-5.
504/1-47.
503/1-4.
504/I-i.
504/11-5.
504/11-47.
1-4.
503/I
Additional
Numerical
Numerical
504/1-45.
514/1-41.
503/1-8.
504/I-9-Z7.
504/11-45.
514/11-41.
503/11-8.
organization
index
of
index
of
new
old
504/1-43
514/1-42
503/1-25
504/1-10
504/11-43
514/11-42
503/11-25
chart
product
numbers
ORGANIZATION
NUMERICAL
code
numbers
with
new
product
INDEX
with
code
CHARTS
PARTS
old
numbers
numbers
60-61
62-63
64-65
66-67
68
69-73
74-78
—3—
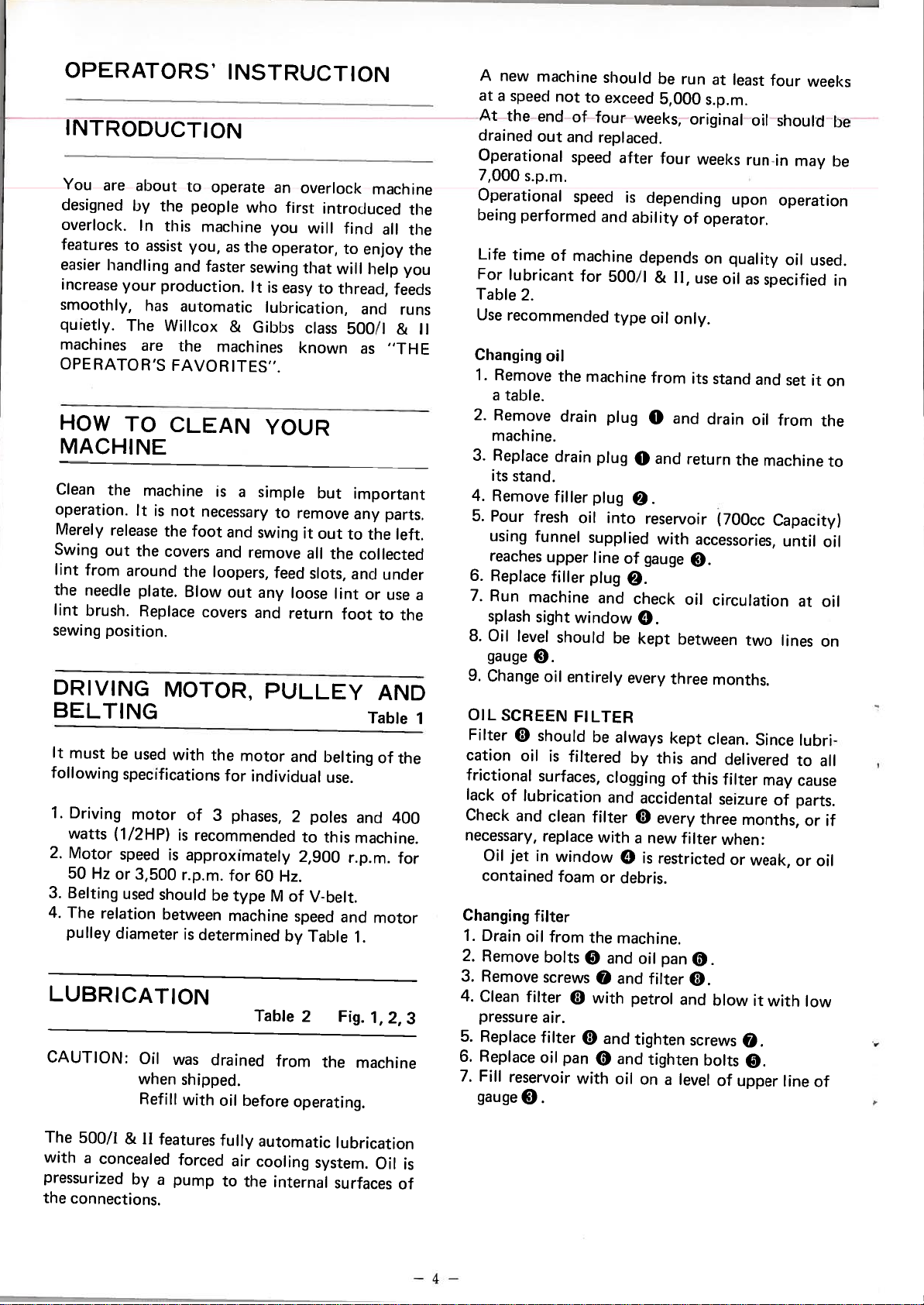
OPERATORS’
INTRODUCTION
You
are
aliou
t
designed
overlock.
features
easier
increase
smoothly,
quietly.
machines
OPERATOR’S
HOW
by
In
to
assist
handling
your
has
The
are
TO
the
this
production.
Willcox
FAVORITES”.
CLEAN
MACHINE
Clean
operation.
Merely
Swing
lint
the
lint
sewing
DRIVING
the
release
out
from
needle
brush.
position.
machine
It
is
the
around
plate.
Replace
riot
the
covers
MOTOR,
BELTING
It
must
be
used
with
following
1.
Driving
watts
2.
Motor
50
3.
Belting
4.
The
pulley
specifications
(1/2HP)
speed
Hz
or
used
relation
diameter
motor
is
3,500
should
between
LUBRICATION
CAUTION:
Oil
when
Refill
was
INSTRUCTION
to
opera
people
macli
you,
as
and
[aster
automatic
&
the
machines
is
necessary
foot
and
and
the
loopers,
Blow
out
covers
the
for
of
3
phases,
is
recommended
approximately
r.p.m.
shipped.
with
be
is
determined
drained
oil
for
type
machine
Ic
an
who
me
you
the
operator,
sewing
It
is
lubrication,
Gibbs
YOUR
simple
a
to
swing
remove
feed
any
and
PULLEY
motor
individual
60
M
Table
from
before
overlock
first
will
that
easy
class
known
remove
it
all
slots,
loose
return
and
2
poles
to
2,900
Hz.
of
V-belt.
speed
by
Table
2
operating.
introd
wi
to
thread,
but
out
the
lint
belting
use.
this
Fig.
the
ii
iced
[mt
to
enjoy
I
help
and
500/I
as
important
any
to
the
collected
and
or
foot
Table
arid
machine.
r.p.m.
and
motor
1.
1,
machine
ach
the
LuIthe
the
you
feeds
ru
&
‘‘TH
parts.
left.
under
use
to
the
AND
of
the
400
for
2,3
no
is
a
1
II
E
A
new
Lit
Li
At
drained
Operational
7,000
Operational
being
Life
For
Table
Use
Changing
1.
Remove
a
table.
2.
Remove
machine.
3.
Replace
its
4.
Remove
5.
Pour
using
reaches
6.
Replace
7.
Run
splash
8.
Oil
gauge
9.
Change
OIL
SCREEN
Filter
cation
frictional
lack
of
Check
necessary,
Oil
contained
Changing
1.
Drain
2.
Remove
3.
Remove
4.
Clean
pressure
5.
Replace
6.
Replace
7.
Fill
gauge
ii
ach
inc
speed
not
the
end
of
oLit
arid
speed
s.p.m.
speed
performed
time
of
machine
lubricant
2.
recommended
for
oil
the
drain
drain
stand.
filler
fresh
oil
funnel
upper
filler
machine
sight
window
level
should
0.
oil
entirely
FILTER
should
0
oil
is
filtered
surfaces,
lubrication
and
clean
replace
jet
in
window
foam
filter
oil
from
bolts
screws
filter
0
air.
filter
oil
pan
reservoir
with
9.
sl
iou
to
exceed
bLur
replaced.
and
500/I
type
machine
plug
plug
plug
into
supplied
line
plug
and
be
be
always
clogging
and
filter
with
or
the
machine.
and
0
and
0
with
and
0
and
0
oil
Id
weeks,
alter
is
depending
ability
depends
0
0.
reservoir
of
gauge
0.
check
0.
kept
every
by
accidental
0
a
is
0
debris.
oil
petrol
tighten
on
I
run
rn
5,000
four
&
II,
oil
only.
from
and
0
and
with
between
three
kept
this
of
every
new
filter
restricted
pan
filter
and
tighten
a
level
at
s.p.m.
original
weeks
of
operator.
on
quality
use
oil
its
stand
drain
return
(700cc
accessories,
9.
oil
circulation
months.
clean.
and
delivered
this
filter
seizure
three
when:
or
0.
0.
blow
screws
bolts
of
least
oil
run-
upon
as
and
oil
the
two
Since
months,
weak,
it
0.
0.
upper
[our
should
in
may
operation
oil
specified
set
from
machine
Capacity)
until
at
lines
lubri
to
may
cause
of
parts.
or
or
with
low
line
weeks
used.
it
on
the
to
oil
oil
on
all
if
oil
of
he
be
in
p.
The
500/1
&
II
with
a
pressurized
the
connections.
concealed
by
features
a
pump
forced
fully
air
to
automatic
cooling
the
internal
lubrication
system.
surfaces
Oil
is
of
—4—
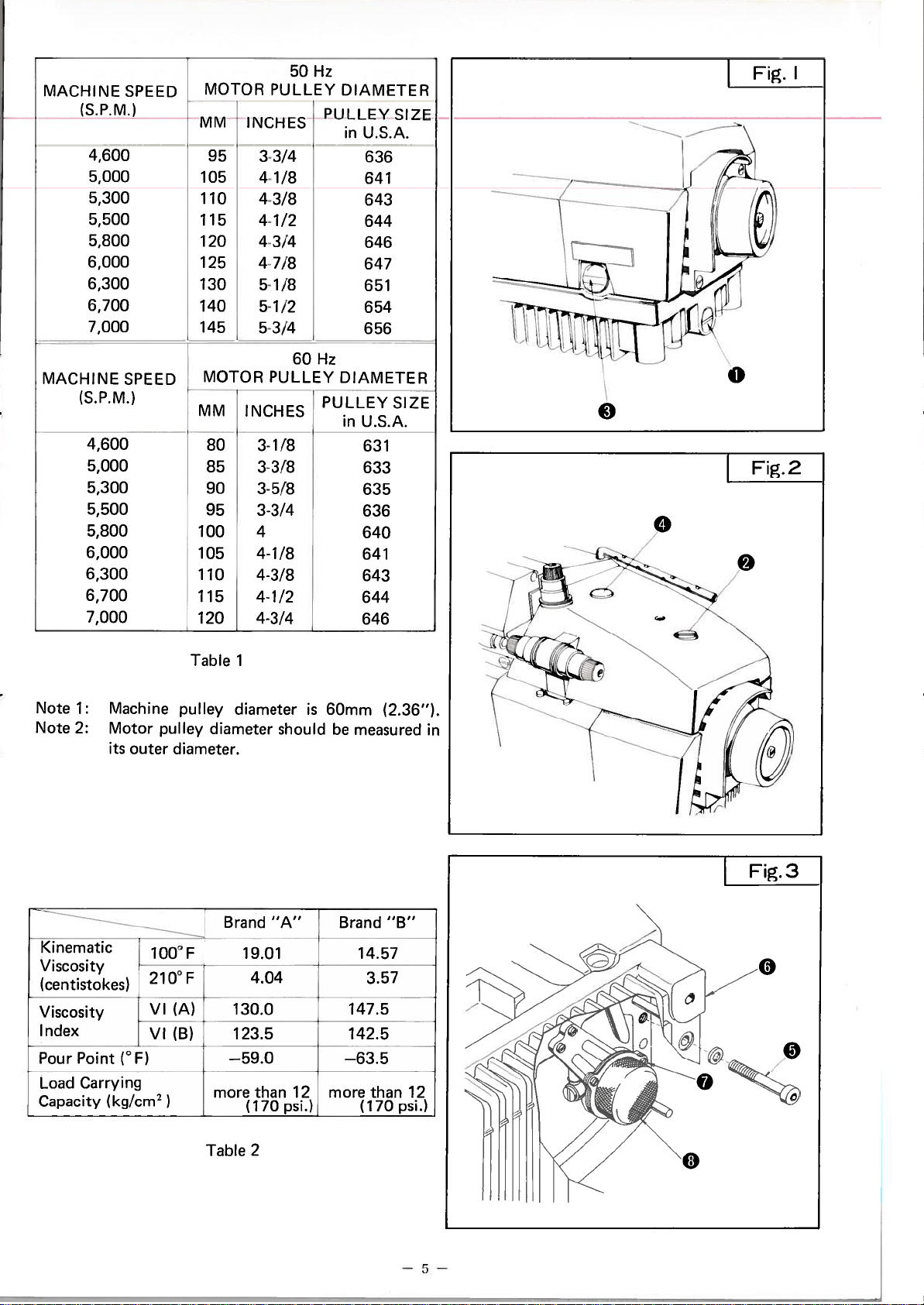
MACHINE
(S.P.M.)
4,600
5,000
5,300
5,500
5,800
6,000
6,300
6,700
7,000
MACHINE
P.M.)
(S.
4,600
5,000
5,300
5,500
5,800
6,000
6,300
6,700
7,000
SPEED
SPEED
MOTOR
MM
95
105
110
115
120
125
I
130
140
145
MOTOR
MM
80
85
90
95
100
105
110
115
120
50
PULLEY
INCH
ES
3-3/4
4-1/8
4-3/8
4-1/2
4-3/4
4-7/8
5-1/8
5-1/2
5-3/4
PULLEY
INCHES
3-1/8
3-3/8
3-5/8
3-3/4
4
4-1/8
4-3/8
4-1/2
4-3/4
60
Hi
DIAMETER
PULLEY
in
Hz
DIAMETER
PULLEY
in
U.S.A.
636
641
643
644
646
647
651
654
666
U.S.A.
631
633
635
636
640
641
643
644
646
SIZE
SIZE
Fig.
L
Fig.2
0
Note
1:
2:
Note
(<inematic
Viscosity
(centistokes)
Viscosity
Index
Pour
Point
Carrying
Load
Capacity
Machine
Motor
its
outer
—
I
F)
(°
(kg/cm
2
)
pulley
diameter.
100°F
210°F
VI
(A)
VI
(B)
Table
pulley
[
1
diameter
diameter
Brand
19.01
4.04
130.0
123.5
—59.0
more
(170
than
should
“A”
psi.)
12
is
60mm
be
measured
Brand
147.5
142.5
—63.5
more
14.57
3.57
than
(170
(2.36”).
in
Fig.3
“B”
—0
/0
12
psi.)
Table
2
—5—
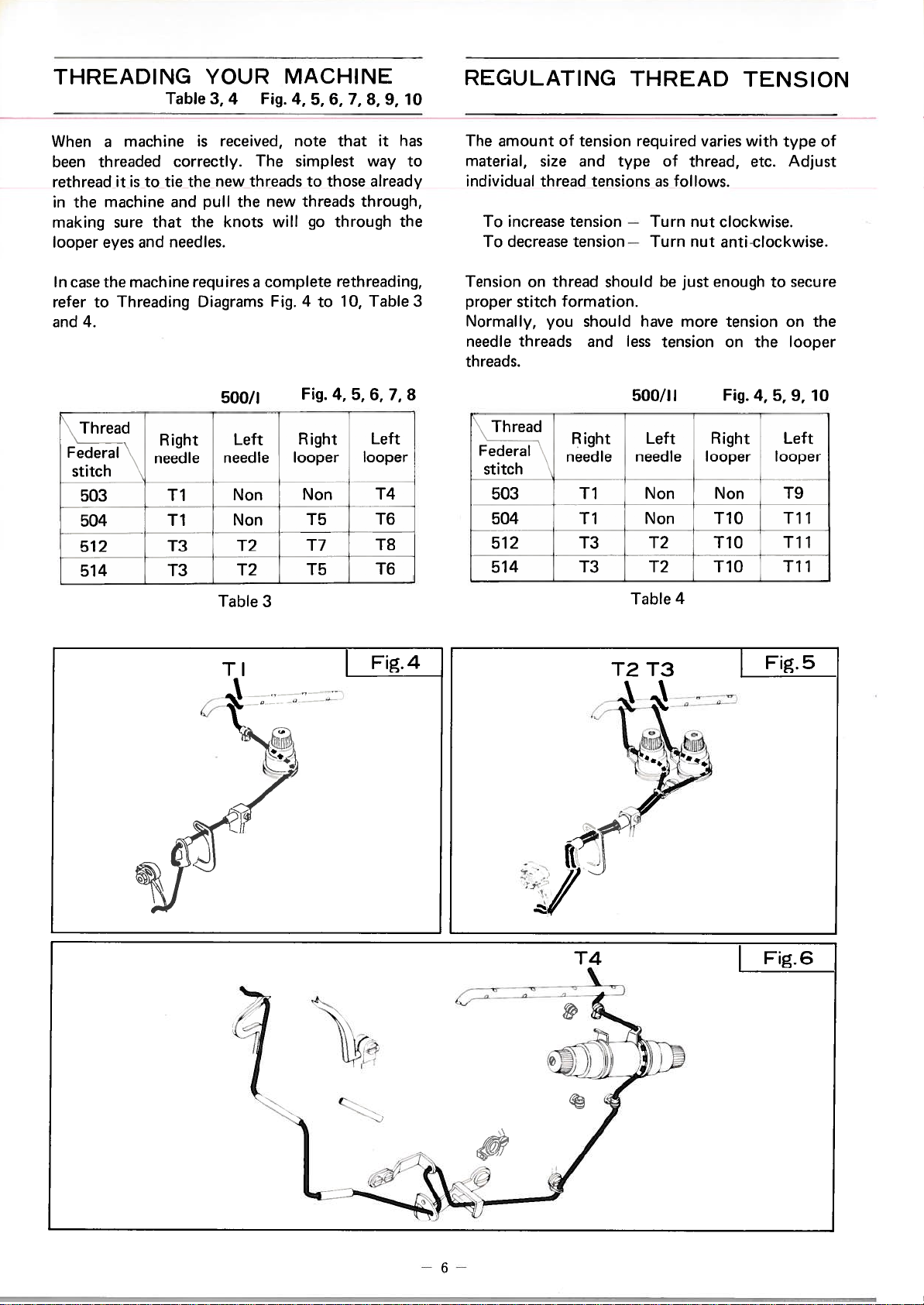
THREADING
Table
YOUR
3,
4
MACHINE
Fig.
4,
5,6,7,
REGULATING
8,
9,
10
THREAD
TENSION
When
been
rethreacl
in
the
making
looper
In
case
refer
and
4.
Thread
Federal
stitch
503
504
512
514
machine
a
threaded
it
is
machine
sure
eyes
the
machine
Threading
to
to
and
correctly.
tie
and
that
needles.
Right
needle
Ti
Ti
T3
T3
received,
is
the
flCW
pull
the
requires
Diagrams
500/I
needle
the
knots
Left
Non
Non
T2
T2
The
threads
new
will
complete
a
Fig.
note
simplest
those
to
threads
go
4
to
Fig.
Right
looper
Non
T5
T7
T5
that
it
way
already
through,
through
rethreading,
Table
10,
4,
5,6,7,
Left
looper
T4
T6
T8
T6
has
the
8
The
amount
to
material,
individual
To
increase
To
decrease
Tension
3
proper
Normally,
needle
size
thread
on
stitch
you
threads
of
tension
and
tensions
tension
tension—
thread
formation.
should
and
type
—
should
less
required
of
as
follows.
Turn
Turn
be
have
tension
varies
thread,
nut
clockwise.
nut
anti-clockwise.
just
enough
more
with
etc.
tension
on
the
to
type
Adjust
secure
on
looper
of
the
threads.
Thread
Federal
stitch
503
504
512
514
needle
.
Right
Ti
Ti
T3
T3
—.
500/Il
needle
V
Left
Non
Non
T2
T2
Fig.
Right
looper
Non
TiO
Ti0
TiC
4,5,9,
I
10
Left
looper
T9
Tli
Tii
Tii
Table
Table
3
Fig.4
T4
//V
/
4
Fig.5
Fig.6
C
—
6
—

%-,-,
T5\
Fig.7
\T,
D
Fig.8
t
JJ
Fig.9
Fig.
10
—7—

PRESSURE
Pressure
tilunhl)
just
stitch
material
little
stitches.
of
screw
enough
formation.
and
pressure
presser
0.
to
give
NEEDLES
Needles
organization
Generally
by
sewn.
Changing
Turn
1.
at
2.
Lift
left.
Loosen
3.
with
4.
Insert
until
Tighten
5.
Return
6.
Make
7.
needle
On
8.
at
the
its
two
the
for
the
size
of
needles
hahdwheel
highest
up
lever
nut
machine
the
new
needle
nut
arm
sure
hole
needle
right
500/I
charts
size
needle
rests
0
0
needle
in
REGULATING
Lift
1.
2.
3.
4.
5.
6.
7.
Turn
lowest
Loosen
far
as
Loosen
right
then
tighten
Loosen
position
Tighten
Return
up
lever
handwheel
position.
screw
asitwill
screw
or
left
screw
by
screw
arm
until
screw
spring
0
OF
loot
Pressure
lend
Too
it
more
may
&
as
of
thread
until
position.
and
0
using
0
and
against
securely.
the
to
descends
needle
machine,
position
and
0
until
Pull
0.
and
go
and move
D
the
then
0,
action.
0.
the
to
PRESSER
is
on
material
much
stretch
cause
II
shown
needle
weight
or
needle
swing
socket
remove
in
the
pin
sewing
plate.
be
or
SEAM
swing
upper
thumb
lightly
desired
di.
holder
sewing
requlated
presser
and
pressure
than
uneven
series
in
should
presser
wrench
old
groove
0.
position.
in
the
sure
between
WIDTH
arm
nut
tighten
holder
width
®
position.
are
pages
of
drive
needle.
to
0
knife
by
foot
should
obtain
may
it
needs.
feedings
Fig.
specified
60
be
determined
material
arm
arm
furnished
of
0
center
keep
two
Fig.
to
is
to
Ij
screw
®
is
obtained,
will
return
FOOT
Fig.
means
proper
Spoil
11,
to
to
0
to
0
clamp
of
shim
needles.
11,
left.
the
at
the
to
the
Too
68.
the
the
0
13
its
left
0.
to
be
or
12
be
11
of
in
is
CAUTION:
REPLACING
LOWER
UPPER
1.
2.
3.
4.
5.
6.
7.
8.
9.
10.
LOWER
1.
2.
3.
4.
5.
6.
7.
8.
Knives
sharpened
that
Fig.
or
from
must
KNIFE
Lift
up
Loosen
far
as
Remove
screwdriver
Withdraw
Replace
screw
Turn
cutting
to
Tighten
Return
Lift
Loosen
far
Loosen
Insert
stud,
is
Fig.
Tighten
Loosen
to
Tighten
Return
15.
return
handwheel
lowest
(.020-.039”)
Retighten
Loosen
position
KNIFE
up
it
as
setting
level
14.
position
must
by
the
correct
Upper
to
a
special
sharpened
be
it
edge
arm
nut
new
with
nut
screw
screw
arm
When
extremely
needle
width
See
pages
KNIVES
lever
screw
will
screw
furnished
knife
with
completely.
position.
overlaps
as
screw
screw
by
screw
0
lever
screw
will
Ij
knife
the
the
ji’
by
0
be
kept
use
angle
knife
us
for
tungsten
seam
wide
plate
recommended.
is
organization
to
60
THE
and
0
Pull
0.
go
and
downward.
®
new
knife
until
Set
lower
shown
securely.
then
0,
spring
0.
0
0
go
0,
spring
0.
to
of
by
action.
to
the
and
swing
and
pull
and
and
withdraw
into
blade
top
of
securely.
then
action.
the
sewing
sharp.
grinder
a
is
may
be
resharpening
carbide
diamond
a
width
or
for
larger
charts
68.
UPPER
Fig.
swing
sewing
lightly
maintained
nut
lightly
with
with
upper
upper
in
Fig.
holder
nut
the
so
that
needle
holder
Lower
sent
arm
socket
the
but
knife
position.
arm
tighten
groove
position.
while
to
alloy
grinder.
is
narrow,
or
11,
0
to
tighten
machine.
do
knife
knife
by
14.
®
0
Iii
knife
the
plate
®
knife
our
since
material,
changed
replace
to
narrower
as
shown
AND
13,
14,
to
the
the
left
screw
wrench
not
tighten
is
at
so
that
0.5-1.0mm
will
return
to
the
to
the
left
screw
downward.
clamp
of
cutting
shown
as
will
return
may
making
shown
as
distributors
itismade
to
seam
in
15
left.
as
0.
or
its
its
left.
as
0.
edge
in
be
sure
in
and
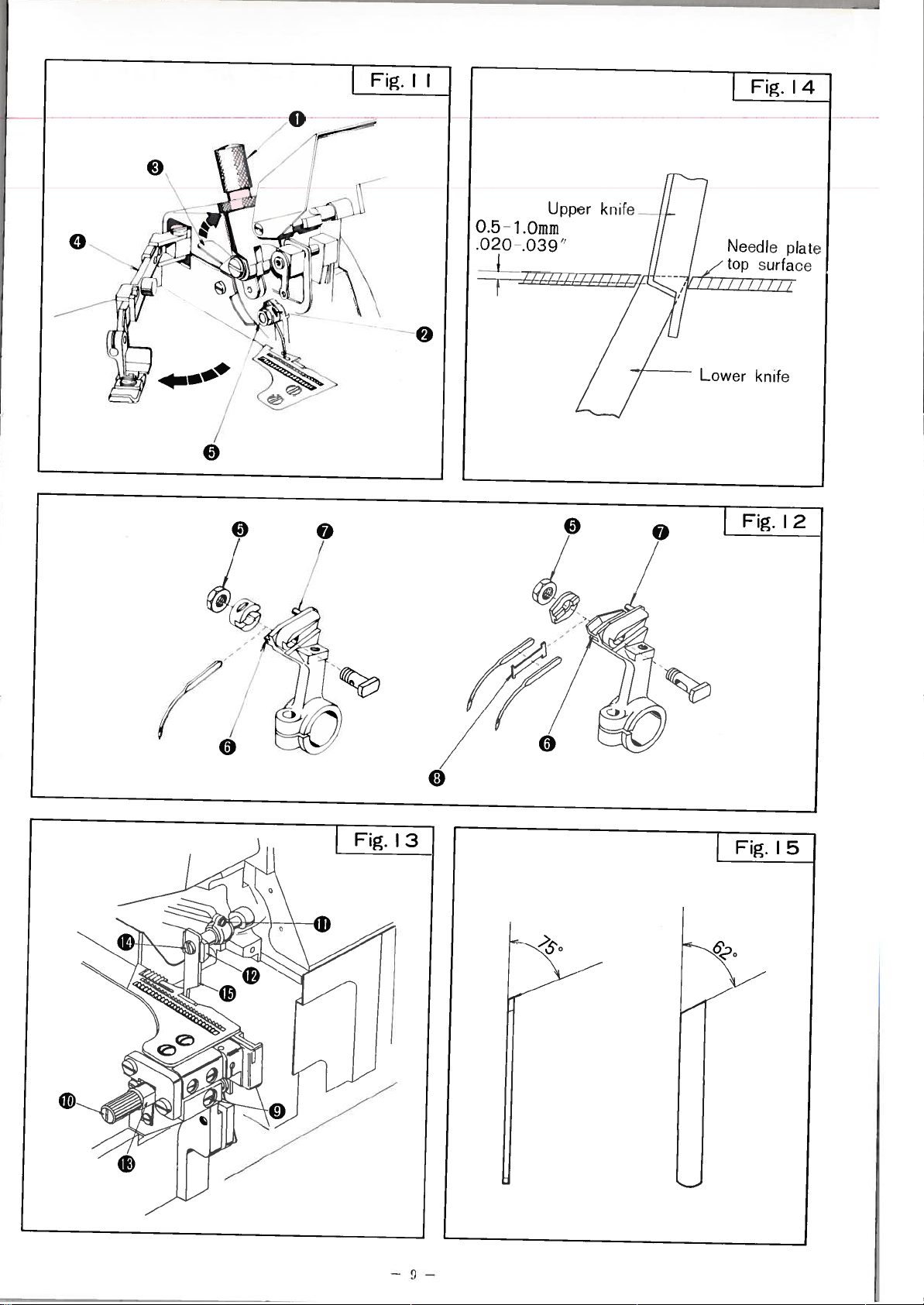
LLL
FigH4
0
Upper
0.5-
1.0mm
0
.020
.039”
knife
Needle
top
surfa(n
plak
0
Lower
/
0
0
/
0
/
0
/
knife
Fig.12
13
Fig.
15
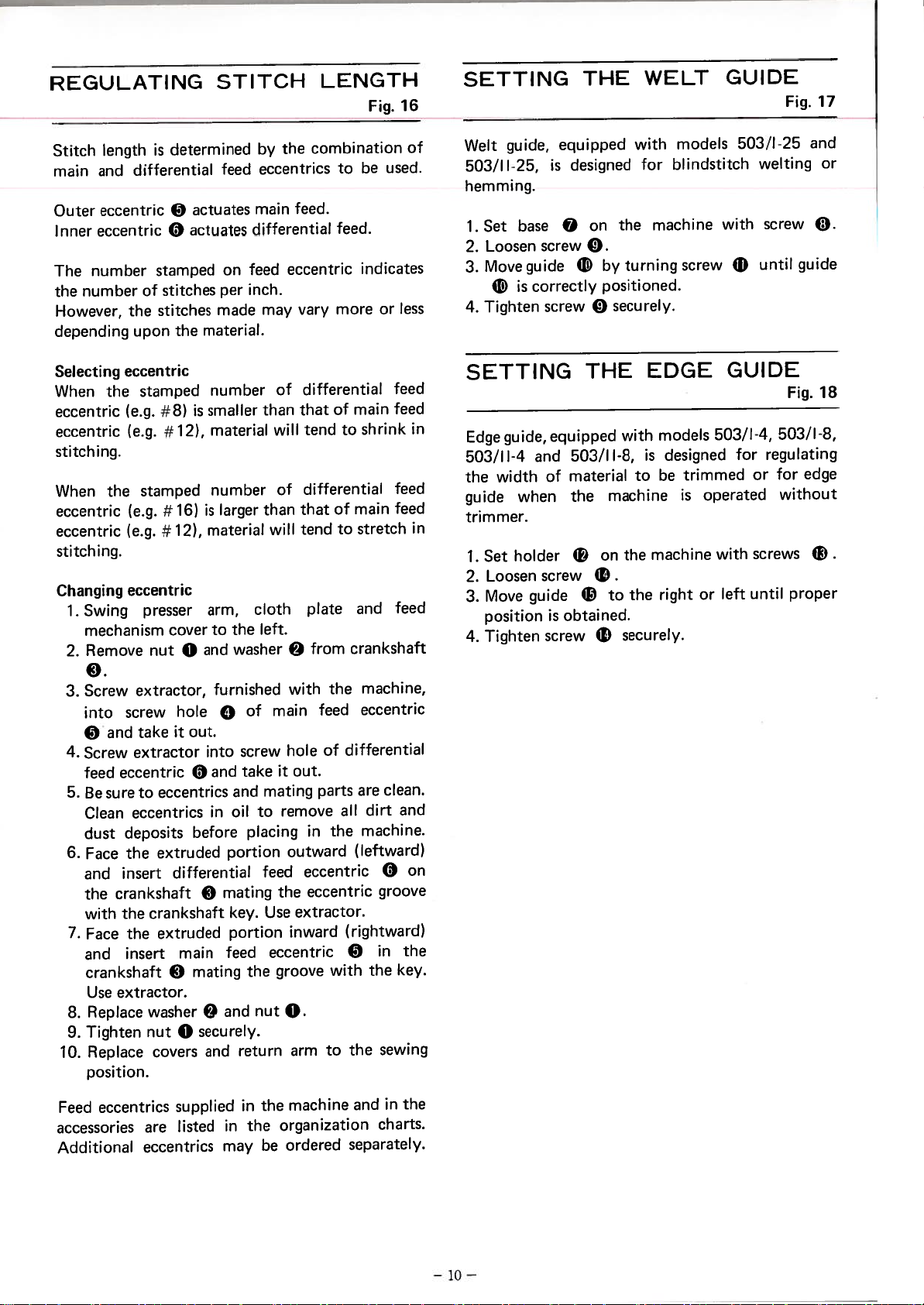
REGULATING
STITCH
LENGTH
Fig.
16
SETTING
THE
WELT
GUIDE
Fig.
17
eccentric
Tiller
number
number
Swing
1.
mechanism
Remove
2.
length
and
eccentric
the stamped
SUtch
main
Outer
The
the
However,
depending
Selecting
When
eccentric
eccentric
stitching.
When
eccentric
eccentric
stitching.
Changing
0.
Screw
3.
into
O
4.
Screw
feed
5.
sure
Be
Clean
dust
6.
Face
and
the
with
7.
Face
and
crankshaft
Use
Replace
8.
Tighten
9.
Replace
10.
position.
dillerential
of
the
upon
eccentric
(e.g.
(e.g.
the
stamped
(e.g.
(e.g.
eccentric
presser
nut
extractor,
screw
take
and
extractor
eccentric
to
eccentrics
deposits
the
insert
crankshaft
crankshaft
the
the
insert
extractor.
washer
nut
determined
is
feed
actuates
0
actuates
0
feed
is
0
hole
out.
0
before
main
mating
securely.
0
on
per
made
material.
number
smaller
material
number
is
larger
material
arm,
to
the
washer
and
furnished
0
screw
into
take
and
and
oil
in
mating
0
key.
portion
feed
and
0
return
and
Inch.
of
placing
the
stamped
stitches
stitches
the
=8)
12),
#16)
#12),
cover
it
eccentrics
extruded portion
differential
extruded
0
covers
the
feed.
eccentric
vary
differential
of
that
will
tend
differential
of
that
will
tend
plate
0
with
main
hole
it
out.
remove
outward
eccentric
eccentric
the
extractor.
Use
inward
eccentric
groove
0.
arm
combination
from
in
by
eccentrics
main
differential
may
than
than
cloth
left.
mating
to
feed
nut
to
feed.
more
of
to
of
to
the
feed
differential
of
parts
all
the
(rightward)
0
with
the
to
used.
be
indicates
or
less
feed
feed
main
shrink
feed
feed
main
stretch
feed
and
crankshaft
machine,
eccentric
clean.
are
dirt
and
machine.
(leftward)
0
groove
in
the
key.
the
sewing
of
on
in
in
guide,
Welt
503/11-25,
hemming.
base
Set
1.
Loosen
2.
guide
Move
3.
correctly
is
€i
4.
Tighten
SETTING
guide,
Edge
503/11-4
the
width
guide
trimmer.
1.
2.
3.
4.
when
holder
Set
Loosen
Move
position
Tighten
guide
equipped
is
0
screw
screw
equipped
and
of
screw
obtained.
is
screw
designed
on
0.
by
positioned.
securely.
0
THE
503/11-8,
material
machine
the
on
®
to
®
with
for
machine
the
turning
EDGE
models
with
is
to
be
machine
the
right
the
securely.
models
blindstitch
screw
designed
trimmed
operated
is
or
503/1-25
with
GUIDE
503/1-4,
for
or
screws
with
until
left
welting
screw
guide
until
Fig.
503/1-8,
regulating
for
without
proper
and
or
0.
18
edge
eccentrics
Feed
accessories
Additional
supplied
listed
are
eccentrics
in
may
in
the
the
be
machine
organization
ordered
and
charts.
separately.
—
10
—
the
in
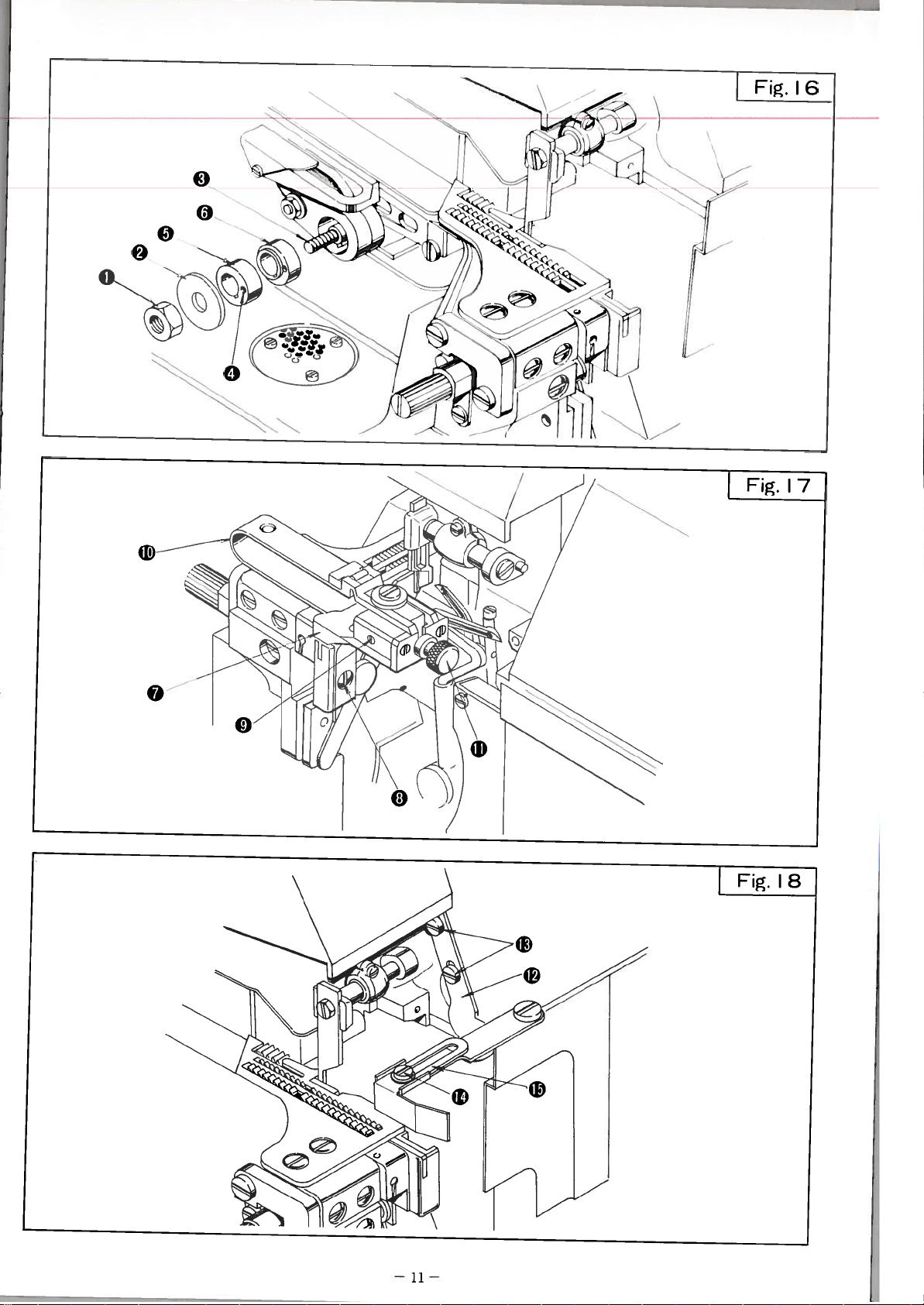
d
0
L!d
0
8
—
IT
—
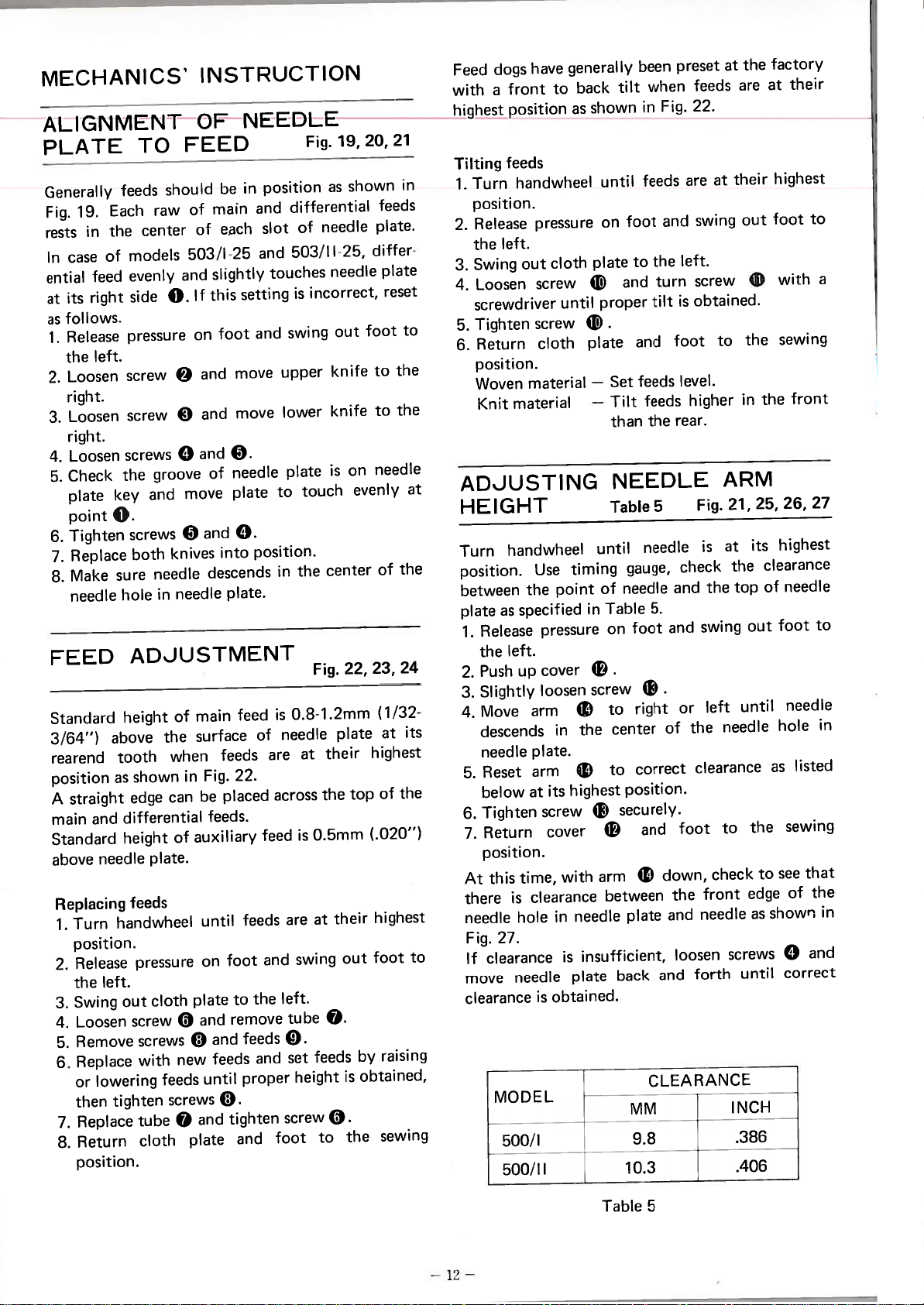
MECHANICS’
ALIGNMENT
PLATE
Generally
19.
Fig.
in
rests
case
In
[ial
en
right
its
at
follows.
as
Release
1.
the
Loosen
2.
right.
Loosen
3.
right.
Loosen
4.
Check
5.
plate
point
Tighten
6.
Replace
7.
Make
8.
needle
FEED
Standard
3/64”)
rearend
position
straight
A
main
Standard
above
Replacing
Turn
1.
position.
Release
2.
the
Swing
3.
Loosen
4.
Remove
5.
Replace
6.
or
then
Replace
7.
Return
8.
position.
TO
feeds
raw
Each
CCfl
the
models
of
evenly
feed
side
pressure
left.
screw
screw
screws
groove
the
and
key
0.
screws
both
needle
sure
in
hole
ADJUSTMENT
height
above
tooth
shown
as
edge
differential
and
height
feeds
handwheel
pressure
left.
out
screw
screws
with
tighten
tube
cloth
plate.
cloth
needle
lowering
INSTRUCTION
NEEDLE
OF
FEED
n
be
Id
sliou
main
of
each
of
[Cr
503/1-25
slightly
and
setting
this
II
0.
foot
on
move
and
move
and
@
and
of
move
and
0
descends
main
surface
Fig.
in
be
feeds.
auxiliary
until
on
plate
and
and
0
feeds
until
and
plate
0.
needle
plate
0.
into
plate.
feed
22.
placed
feeds
foot
to
remove
feeds
proper
0.
tighten
and
0
knives
needle
of
the
when feeds
can
of
0
new
feeds
screws
0
position
differential
and
slot
503/11-25,
and
touches
swing
and
upper
lower
plate
to
position.
in
0.8-1.2mm
is
needle
of
are
across
feed
are
and
left.
the
tube
0.
set
and
screw
foot
Fig.19,20,21
as
needle
of
needle
incorrect,
is
out
knife
knife
is
touch
center
the
22,
Fig.
plate
their
at
the
0.5mm
is
their
at
out
swing
0.
feeds
height
is
0.
to
shown
feeds
plate.
differ-
foot
to
to
needle
on
evenly
of
23,
(1/32-
highest
of
top
(.020”)
highest
foot
by
obtained,
sewing
the
—
in
plate
reset
to
the
the
at
the
24
its
at
the
to
raising
have
dogs
Feed
front
a
with
highest
Tilting
1.
2.
3.
4.
position
feeds
Turn
position.
Release
left.
the
Swing
Loosen
handwheel
pressure
out
screw
screwdriver
5.
6.
Tighten
Return
screw
cloth
position.
Woven
Knit
material
material
ADJUSTING
HEIGHT
between
as
plate
Release
1.
the
Push
2.
Slightly
3.
Move
4.
descends
needle
Reset
5.
below
Tighten
6.
Return
7.
position.
this
At
there
needle
27.
Fig.
clearance
If
move
clearance
MODEL
-
500/I
-
500/Il
handwheel
Use
the
specified
pressure
left.
cover
up
loosen
arm
plate.
arm
at
screw
cover
time,
clearance
is
hole
needle
is
Turn
position.
generally
back
to
shown
as
cloth
Ij
until
plate
timing
point
in
screw
the
in
highest
its
with
needle
in
insufficient,
is
plate
obtained.
been
tilt
until
foot
on
to
plate
and
proper
and
feeds
Set
—
Tilt
—
than
NEEDLE
Table
until
gauge,
needle
of
Table
foot
on
right
to
center
correct
to
position.
securely.
®
®
arm
between
plate
back
MM
9.8
10.3
preset
Fig.
and
[lie
turn
tilt
feeds
22.
are
swing
left.
screw
obtained.
is
at
when
in
feeds
foot
level.
higher
feeds
rear.
the
Fig.
5
needle
is
check
the
and
5.
swing
and
left
or
the
of
clearance
foot
and
the
and
check
front
needle
down,
loosen
forth
and
CLEARANCE
the
at
are
their
out
the
to
in
ARM
21,
at
the
top
out
until
needle
to
edge
screws
until
INCH
.386
--
factory
at
highest
foot
with
D
sewing
the
25,
highest
its
clearance
of
foot
hole
as
the
see
to
shown
as
-
their
to
front
27
26,
needle
needle
listed
sewing
that
of
the
and
0
correct
a
to
in
in
—
12
—
Table
5
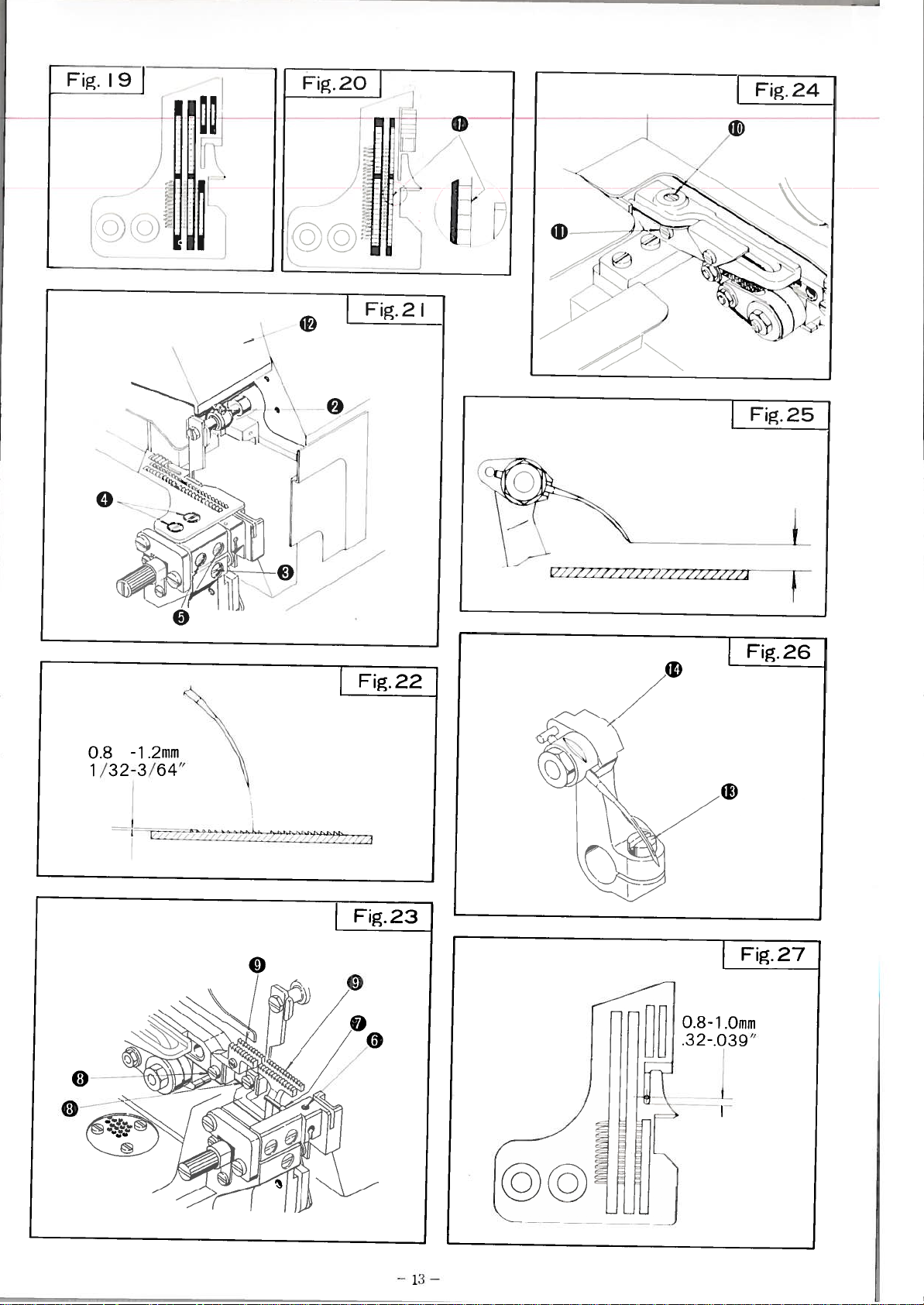
Fig.24
/
0.8
-1
1/32-3/64”
0
.2mm
H
II:>
0
L
‘/V77ZZ7Z7?ZZ7772ZX7J
_Fig.25
Fig.26
Fg.22
N
/
®
Fg.23
L
0
—
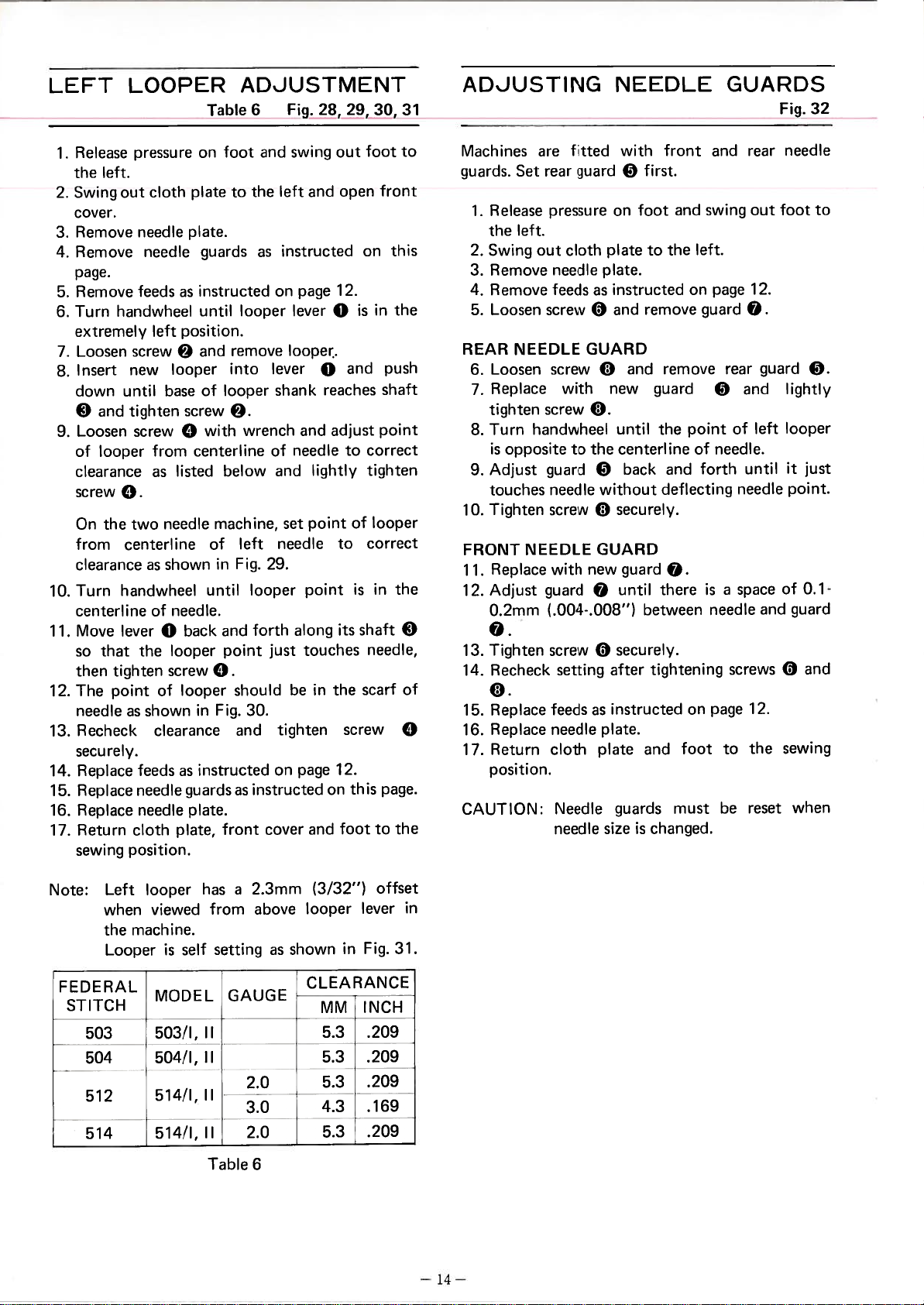
LEFT
LOOPER
ADJUSTMENT
Table
Fig.
6
28, 29,
30,
31
ADJUSTING
NEEDLE
GUARDS
Fig.
32
.
R
elease
1
the
2.
Swing
cover.
Remove
3.
4.
Remove
page.
Remove
5.
Turn
6.
extremely
Loosen screw
7.
Insert
8.
down
and
o
Loosen
9.
looper
of
clearance
screw
On
from
clearance
Turn
10.
centerline
Move
11.
so
that
then tighten
The
12.
needle
Recheck
13.
secu
Replace
14.
Replace
15.
Replace
16.
Return
17.
sewing
pressure
left.
out
cloth plate
needle
needle
feedsasinstructed
handwheel
left
position.
0
looper
new
until
base
tighten
screw
from
listed
as
0.
the two
point
rely.
needle
centerline
shown
as
handwheel
needle.
of
lever0back
the
looper
screw
of
looper
showninFig.
as
clearance
feedsasinstructed
needle
needle
cloth
plate,
position.
on
plate.
guards
until
and
of
screw
with
0
centerline
machine,
of
in
until
0.
guards
plate.
[001
to
looper
remove
into
looper
wrench
below
left
Fig.
looper
and
point
should
30.
and
as
front
and
swing
left
the
as
forth
instructed
and
instructed
on
page
lever
looper..
lever
shank
and
needletocorrect
of
lightly
and
point
set
needle
29.
point
along
touches
just
be
in
tighten
on
page
cover
and
out
open
12.
0
and
0
reaches
adjust
of
to
its
the
screw
12.
this
on
foot
loot
on
is
tighten
looper
correct
is
shaft
needle,
scarf
front
in
push
shaft
point
in
page.
to
to
this
the
the
0
0
the
of
Machines
guards.
4.
REAR
6.
10.
FRONT
11.
12.
Set
1.
Release
the
left.
Swing
2.
Remove
3.
Remove
Loosen screw
5.
NEEDLE
Loosen screw
Replace
7.
tighten
Turn
8.
opposite
is
Adjust
9.
touches
Tighten
NEEDLE
Replace
Adjust
0.2mm
0.
Tighten
13.
Recheck
14.
0.
Replace
15.
Replace
16.
17.
Return
position.
CAUTION:
guard
plate
plate.
as
0
GUARD
with
0
on
instructed
and
are
rear
pressure
out
cloth
needle
feeds
fitted
0
with
screw
handwheel
guard
needle
screw
with
guard
(.004-.008”)
screw
setting
feedsasinstructed
needle
cloth
Needle
needle
to
new
0.
until
the
centerline
0
without
securely.
0
GUARD
new
until
securely.
0
after
plate.
plate
guards
size
back and
guard
first.
foot
to
remove
and
guard
the
between
tightening
and
changed.
is
front
swing
and
the
left.
on
guard
remove
point
of
forth
deflecting
0.
is
there
on
foot
must
and
page
rear
0
of
needle.
needle
space
a
needle
screws
page
to
be
rear
out
12.
0.
and
left
until
12.
the
reset
foot
guard
of
and
0
sewing
needle
0.
lightly
looper
it
just
point.
0.1-
guard
and
when
to
in
offset
lever
Fig.
.209
.209
.209
.169
.209
31.
in
—
14—
Note: Left
when
the
Looper
FEDERAL
STITCH
503
504
512
514
looper
viewed
machine.
is
MODEL
503/1,11
504/I,
514/I
514/1,11
self
has
from
setting
II
II
Table
2.3mm
a
above
i
GAUGE
2.0
-
3.0
2.0
6
(3/32”)
looper
shown
as
CLEARANCE
[
MMIINCH
5.3
5.3
5.3
4.3
5.3

Fig.
28
\\\
\\
Fig.
30
H
H
\\
\\
Fig.
\
29
\S—
Fig.31
2.3mm
3/32”
Fig.
32
\\
\\
0.1
-
.0O4-.OO8”
0.2mm
zz:
15—
—
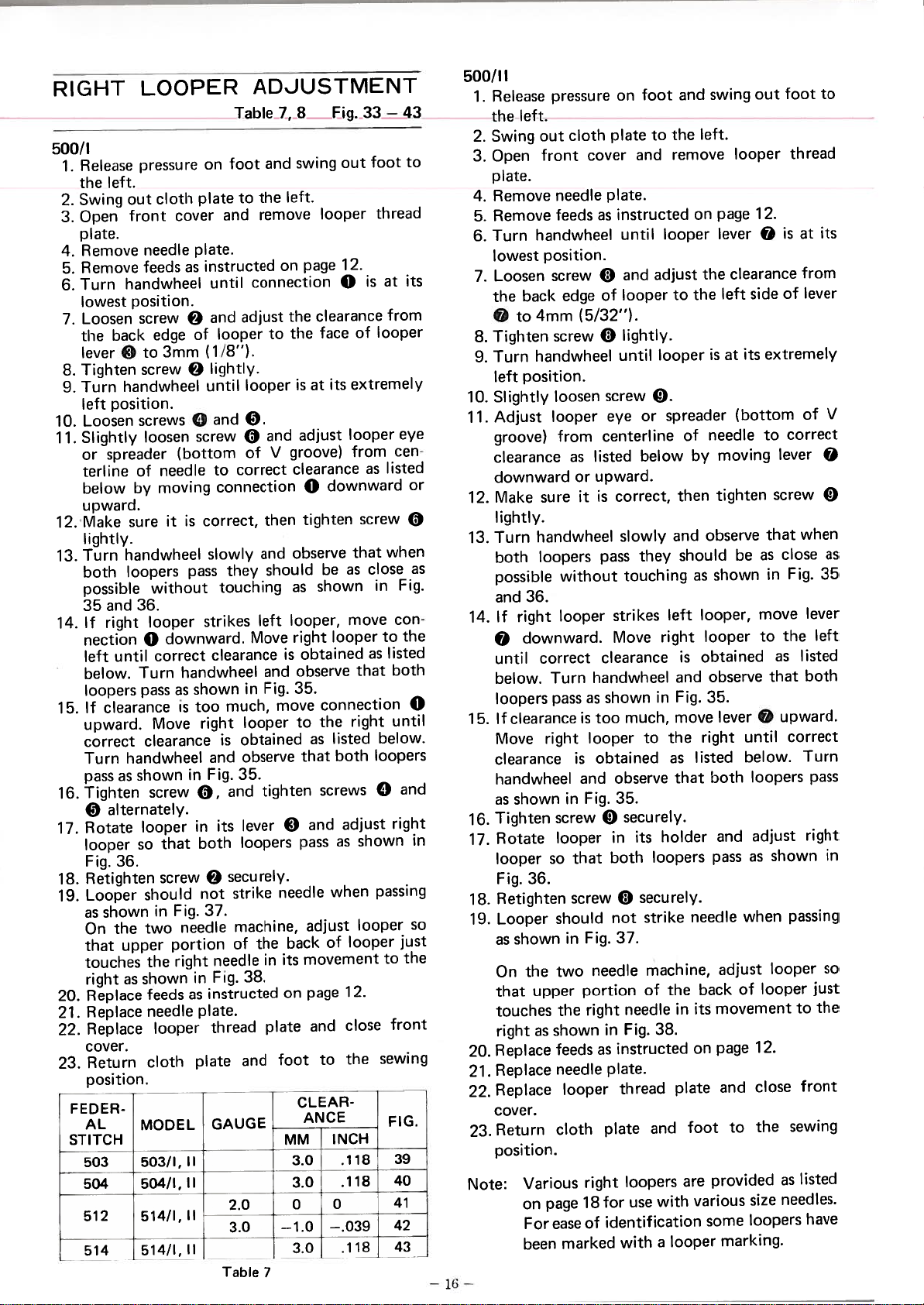
RIGHT
500/I
.
Release
1
[lii’
Svving
2.
Open
3.
I
i
Remove
4.
Remove
5.
Turn
6.
lowest
Loosen
7.
[lie
lever
Tigh
8.
Turn
9.
left
Loosen
10.
Slightly
11.
or
terline
below
upward.
Make
12.
lit
Ii
g
Turn
13.
both
possible
35
If
14.
nection
left
below.
loopers
If
15.
upward.
correct
Turn
pass
Tighten
16.
o
Rotate
17.
looper
Fig.
Retighten
18.
Looper
19.
as
On
that
touches
right
Replace
20.
Replace
21.
Replace
22.
cover.
Return
23.
position.
rERf
AL
STITCH
503
L504
LOOPER
essii
pi
left.
out
Iron
[C
needle
feeds
handwlioel
position.
screw
edge
hack
to
0
screw
ten
handwheel
position.
screws
loosen
spreader
of
by
sure
I
y.
handwheel
loopers
without
36.
and
looper
right
0
correct
until
Turn
pass
clearance
Move
clearance
handwheel
shown
as
screw
alternately.
looper
so
36.
should
the
upper
shown
as
MODEL
j5031l,
J50411,
in
two
the
feeds
needle
looper
cloth
shown
re
plate
cloth
cover
t
plate.
as
of
3mm
0
0
screw
(bottom
needle
moving
it
is
pass
downward.
hanclwheel
shown
as
too
is
right
in
0,
in
both
that
screw
not
Fig.
needle
portion
right
in
as
plate.
plate
II
II
on
inst
(1/8’’).
correct,
strikes
0
37.
ADJUSTMENT
Table
and
toot
to
the
remove
aiid
toil
mc
connection
until
adjust
and
tly.
looper
0.
0
of
correct
then
and
they
left
Move
and
Fig.
in
much,
looper
obtained
observe
35.
tighten
and
lever
loopers
securely.
strike
machine,
the
of
in
38.
plate
and
JCLEAR
-
-
to
and
V
should
looper
ugh
until
and
to
connection
slowly
touching
clearance
is
and
Fig.
its
needle
Fig.
instructed
thread
-
GAUGE
7,
8
Svving
left.
page
on
the
the
is
adjust
groove)
clearance
0
tighten
observe
as
looper,
right
obtained
is
observe
35.
move
to
that
0
pass
needle
back
movement
its
on
foot
MM
3.0
3.0
Fig.
out
looper
12.
0
clearance
face
its
at
downward
be
shown
looper
connection
the
listed
as
both
screws
adjust
and
as
when
adjust
of
12.
page
close
and
the
to
TINCH
.118
.i18
33—
foot
thread
at
is
from
looper
of
extremely
looper
from
listed
as
screw
when
that
close
as
in
move
to
listed
as
that
right
below.
loopers
0
shown
passing
looper
looper
to
front
sewing
FIG.
43
to
its
eye
cen
or
0
as
Fig.
con
the
both
0
until
and
right
in
so
just
the
31
40
:
Table
7
500/Il
1.
2.
3.
4.
5.
6.
7.
8.
9.
10.
11.
12.
13.
14.
15.Ifclearance
16.
17.
18.
19.
20.
21.
22.
23.
Note:
--
—
Release
left.
the
Swing
Open
plate.
Remove
Turn
lowest
the
o
Tigh
Turn
Slightly
out
front
Remove
handwheel until
position.
Loosen
back
4mni
to
ten
handwheel
left
position.
Adjust
groove)
clearance
downward
sure
Make
lightly.
handwheel
Turn
loopers
both
possible
36.
and
right
If
downward.
o
correct
until
below.
loopers
shown
36.
shown
the
upper
as
Various
on
For
been
right
page
Move
clearance
handwheel
as
Tighten
Rotate
looper
Fig.
Retighten
Looper
as
On
that
touches
right
Replace
Replace
Replace
cover.
Return
position.
pressure
needle
feeds
screw
screw
loosen screw
looper
from
without
looper
Turn
pass
screw
looper
so
should
two
the
shown
feeds
needle
cloth
ease
cloth
cover
edge
(5/32”).
listed
as
upward.
or
it
handwheel
as
is
looper
is
and
Fig.
in
that
screw
Fig.
in
needle
portion
right
looper
right
18
of
marked
loot
on
to
plate
and
Plate.
instructed
as
and
0
of
0
adjust
looper
lightly.
until
0.
or
eye
centerline
below
correct,
is
slowly
they
pass
touching
strikes
Move
clearance
shown
much,
too
to
obtained
observe
35.
securely.
0
its
in
loopers
both
securely.
0
strike
not
37.
machine,
of
needle
38.
Fig.
in
instructed
as
plate.
thread
and
plate
loopers
use
for
identification
with
and
the
remove
looper
to
looper
spreader
of
then
and
should
left
right
is
and
Fig.
in
move
the
as
that
holder
the
in
plate
are
with
looper
a
swing
left.
on
the
the
isatits
needle
by
observe
shown
as
looper,
looper
obtained
observe
35.
right
listed
both
pass
needle
back
its
on
foot
provided
various
some
out
looper
12.
page
lever
0
clearance
side
left
extremely
(bottom
to
moving
tighten
that
as
be
in
move
to
lever
0
until
below.
loopers
adjust
and
as
when
adjust
looper
of
movement
12.
page
close
and
the
to
size
loopers
marking.
loot
thread
is
of
correct
lever
screw
close
Fig.
the
as
that
upward.
correct
shown
passing
looper
sewing
as
needles.
at
from
lever
of
when
lever
listed
both
Turn
pass
right
to
front
listed
have
to
its
V
0
0
as
35
left
in
so
just
the

-Il
()
‘1
()
z
N.
-I,
(*)
r

PRESSER
alignment
With
.
right
hole
to
arm
hack
foot
Pn;sei
and
and
needle
Front
1
0.
Adjust
2.
is
there
Tighten
3.
4.
Position
Tighten
5.
set
Once
left
to
Right
Loosen
1.
bracket
Shift
2.
until
left
in
hole
Check
3.
straight.
is
arm
Tighten
4.
PRESSER
Setting
1.
foot
Remove
anti-clockwise.
IIi’
niust
to
in
arm
no
screw
regulator
screw
do
screws
the
needle
bar
screws
pressure
ARM
he
to
left
the
of
needle
alignment
attached
back
in
bind
0.
0.
not
alignment
0
0
needle
plate
is
on
0
0
FOOT
square
aligned
insure
needle
plate.
to
and
bar
loosen
and
and
are
guide
and
and
from
ALIGNMENT
correctly
lilting
hole
loosen
arm,
while
forth
0.
against
0
screw
gLlide
hole
in
aligned.
properly
0
0
foot
0.
ADJUSTMENT
flat
by
foot
44,
Fig.
front
without
loot
in
screws
lilting
connection
the
to
and the
and
Fig.
turning
45,
to
a
with
to
right
46
hack
bind
the
and
0
insure
0.
needle
presser
46
45,
screw
or
handwheel
Turn
2.
Position.
ten
for
screw
plate.
screw
so
foot
screw
or
the
should
lower
Loosen
3.
needle
Tiqli
4.
screw
Pressure
5.
evenly
Adjusting
Loosen
1.
Raise
2.
tilt
Retighten
3.
PRESSER
ADJUSTMENT
1.
2.
3.
4.
5.
6.
7.
8.
Turn
Tighten
While
When
Loosen
lowest
Loosen
(15/64”)
for
500/I),
between
of
Tighten
®
bottom
—
2
Tighten
nut
position.
nut
screw
500/I)
nut
lifting
turn
screw
0.5mm
nut
presser
and
of
3mm
nut
clockwise.
proper
that
tilt
regulator
weight
screw
FOOT
1J.
D
when
U.
presser
screw
®
(.020”).
foot
adjust
screw
(5/64
®
until
and
he
just
of
and
until
presser
and
is
the
—1/8”)
feeds
and
reset
enoLigh
stitch
material
turn
lift
a
foot
foot
®
stopper
needle
on
play
to
posi
pressure
is
LIFT
screw
obtained
is
6.0mm
of
until
clearance
top
turning
by
are
Lion
to
formed.
give
to
being
Fig.45,46,47
lifted.
is
the
®
plate,
of
at
loot
by
feed
the
sewn.
®
(4.5mm
is
loosen
lever
screw
lowest
its
flat
Lu
material
desired
until
6.0mm
of
(4.5mm
clearance
obtained
from
J
on
i
its
for
nut
the
to
MODEL
500/I
-1
500/Il
THREADS
2
3
4
4
2
3
3
4
4
RIGHT
FEDERAL
STITCH
LOOPERS
503
504
512
514
503
504
521
512
514
FOR
LOOPER
MARKING
2
1
4
2
3
7
1
USE
Table
WITH
SINGER
13-16
13-16
11-14
13-16
13-16
—
IDENTI
9-12
9-12
9-12
9-12
9-12
9-12
9-12
9-14
8
—
VARIOUS
NEEDLE
FICATION
25-32
34-40
25-32
34-40
30-36
25-32
25-32
25-32
-
34-40
25-32
25-32
34-40
25-36
SIZE
G
SIZE
METRIC
65-80
85-100
65-80
85-100
759Qi
65-80
65-80
65-80
85-100
65-80
65-80
85-100
65-90
NEEDLES
NEWNO.
323-810-003
323-810-013
323-810-001
323-810-004
323-810-001
323-810-004
323-810-213
323-810-211
.323-810-224
323-810-213
323-810-214
323-810-007
323-810-211
PART
NUMBER
QLDNO.
201234A
202475
201067A
201287A
201067A
201287A
202842
202874
202828
202842
202872
202989
202874
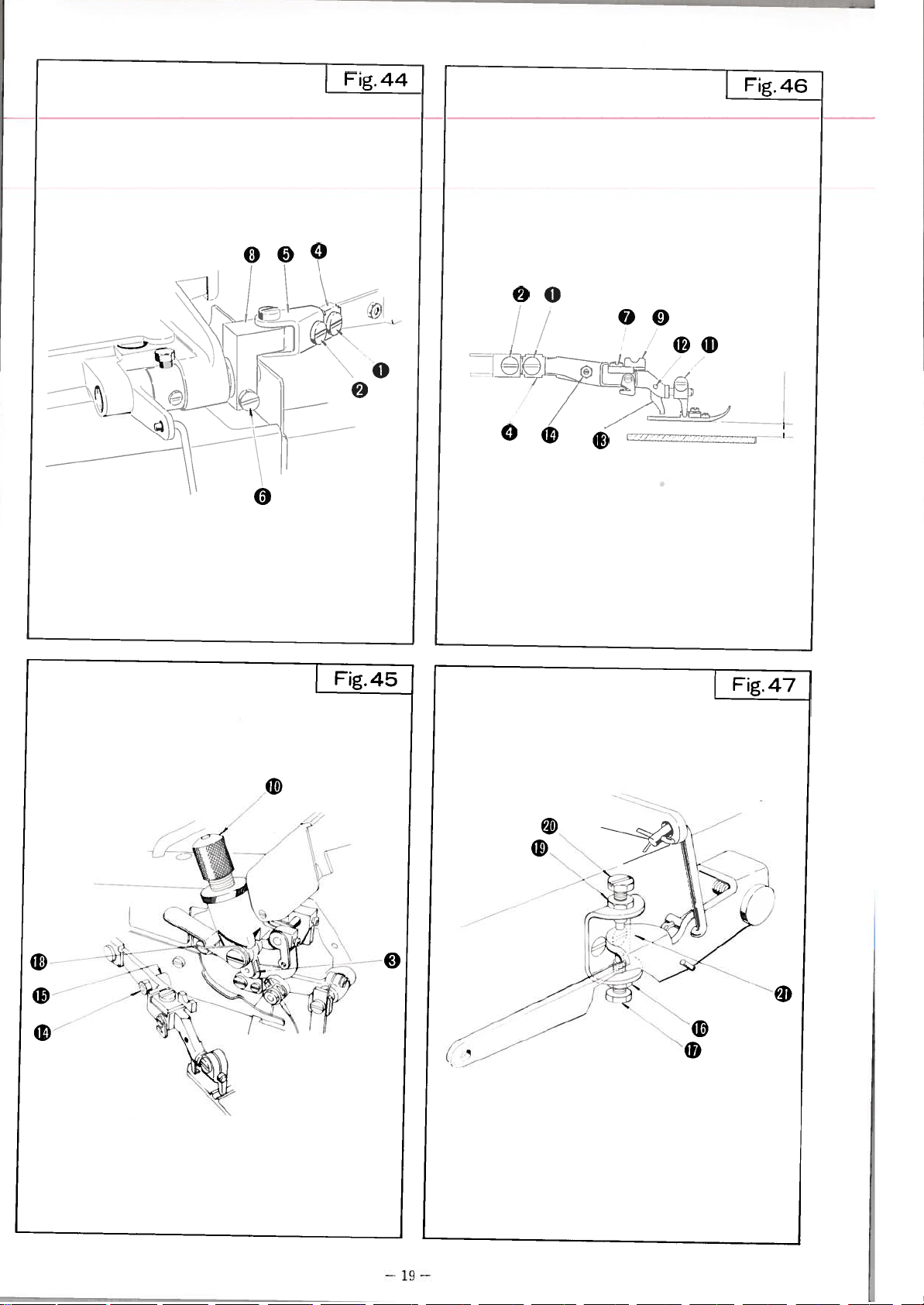
1
0
0
0
8
N
-
-
0
8
0
-n
01
1
a
\
\
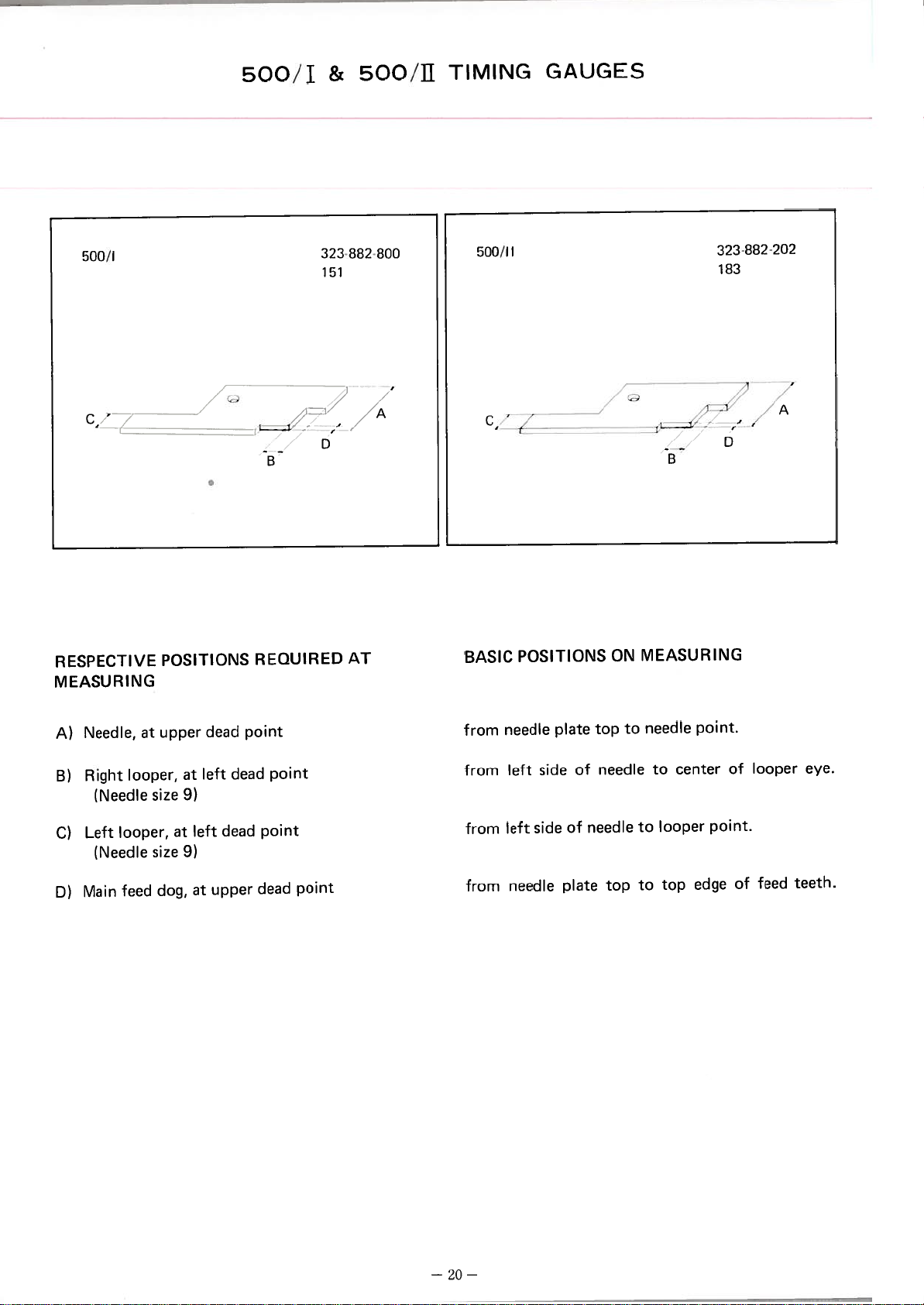
500/I
&
500/11
TIMING
GAUGES
500/I
C’
RESPECTIVE
MEASURING
.
POSITIONS
323
151
D
B
REQUIRED
882
AT
800
A
500/I
C’
BASIC
I
POSITIONS
MEASURING
ON
323-882202
183
A
D
B
A)
B)
C)
D)
Needle,
Right
(Needle
Left
(Needle
Main
at
looper,
looper,
feed
upper
size
size
dog,
to
point.
center
of
looper
eye.
needle
to
top
side
plate
of
needle
needle
point
dead
point
dead
left
at
from
from
left
9)
to
point
dead
left
at
from
needle
of
side
left
looper
point.
9)
teeth.
feed
of
at
upper
dead
point
from
needle
plate
top
to
top
edge
—
20
—

MILLIMETER-INCH
DECIMAL
CONVERSION
FRACTION
CHART
&
MM
1.6
1
1.8
1
2.0
2.1
2.2
2.3
2.4
2.5
2.6
2.7
2.8
2.9
3.0
3.1
3.2
3.3
20.0
30.0
40.0
0.1
0.2
0.3
0.4
0.5
0.6
0.7
0.8
0.9
1
1.1
1
1
1
1.5
.7
.9
.0
.2
.3
.4
!
I
APPROX.
INCH
FRACTION
1/64
1/64
1/32
3/64
3/64
1/1
6
5/64
3/32
7/64
1/8
25/32
1
1
-37/64
-3/1
6
DECIMAL
.004
.008
.01
2
.01
6
.020
.024
.028
.032
.035
.039
.043
.047
.051
.055
.059
.063
.067
.071
.075
.079
.083
.087
.091
.094
.098
.1
02
.1
06
.11
0
.114
.11
8
.1
22
.125
.1
30
.787
.1
81
1
1
.575
+
50.0
60.0
70.0
MM
3.4
3.5
3.6
3.7
3.8
3.9
4.0
4.1
4.2
4.3
4.4
4.5
4.6
4.7
4.8
4.9
5.0
5.1
5.2
5.3
5.4
5.5
5.6
5.7
5.8
5.9
6.0
6.1
6.2
6.3
6.4
6.5
6.6
APPROX.
INCH
FRACTION
9/64
5/32
11/64
3/1
1
3/64
7/32
1
5/64
-31
1
/32
I
2-23/64
2-3/4
1/4
6
j
DECIMAL
34
.1
.1
38
.1
42
46
.1
.1
50
.1
54
.1
57
.1
61
.1
65
.1
69
.1
73
.1
77
.1
81
.1
85
.1
89
.1
93
.1
97
.201
.205
.209
.21
3
.21
7
.220
.224
.228
.232
.236
.240
.244
.248
.252
.256
.260
1.968
2.362
2.756
I
10.0
1
MM
6.7
6.8
6.9
7.0
7.1
7.2
7.3
7.4
7.5
7.6
7.7
7.8
7.9
8.0
8.1
8.2
8.3
8.4
8.5
8.6
8.7
8.8
8.9
9.0
9.1
9.2
9.3
9.4
9.5
9.6
9.7
9.8
9.9
80.0
90.0
00.0
APPROX.
INCH
FRACTION
1
7/64
9/32
1
9/64
5/1
+
21/64
11/32
23/64
3/8
25/64
3-5/32
3-35/64
5/1
3-1
6
6
DECIMAL
.264
.268
.272
.276
.280
.283
.287
.291
.295
.299
i
.303
.307
.31
.31
.31
.323
.327
.330
.335
.339
.343
.346
.350
.354
.358
.362
.366
.370
.374
.378
.382
.386
.390
.394
3.1
50
3.543
3.937
1
5
9
—
21
—
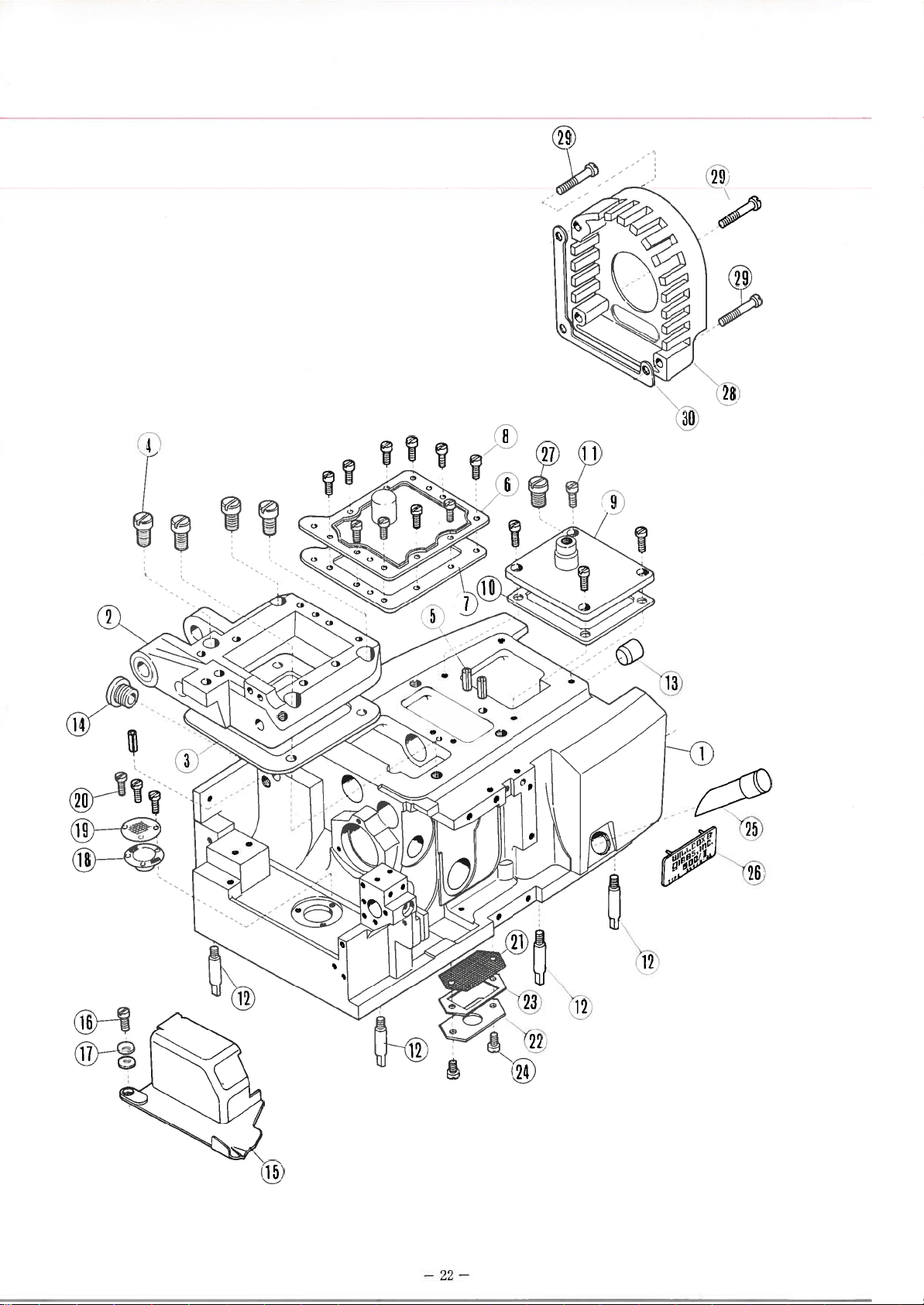
29
29
29
28
)
14)
2
19
U)
()
4
8
11
21
60
13
‘25)
26
)23
16:
:
-
0
—
22:
12
12
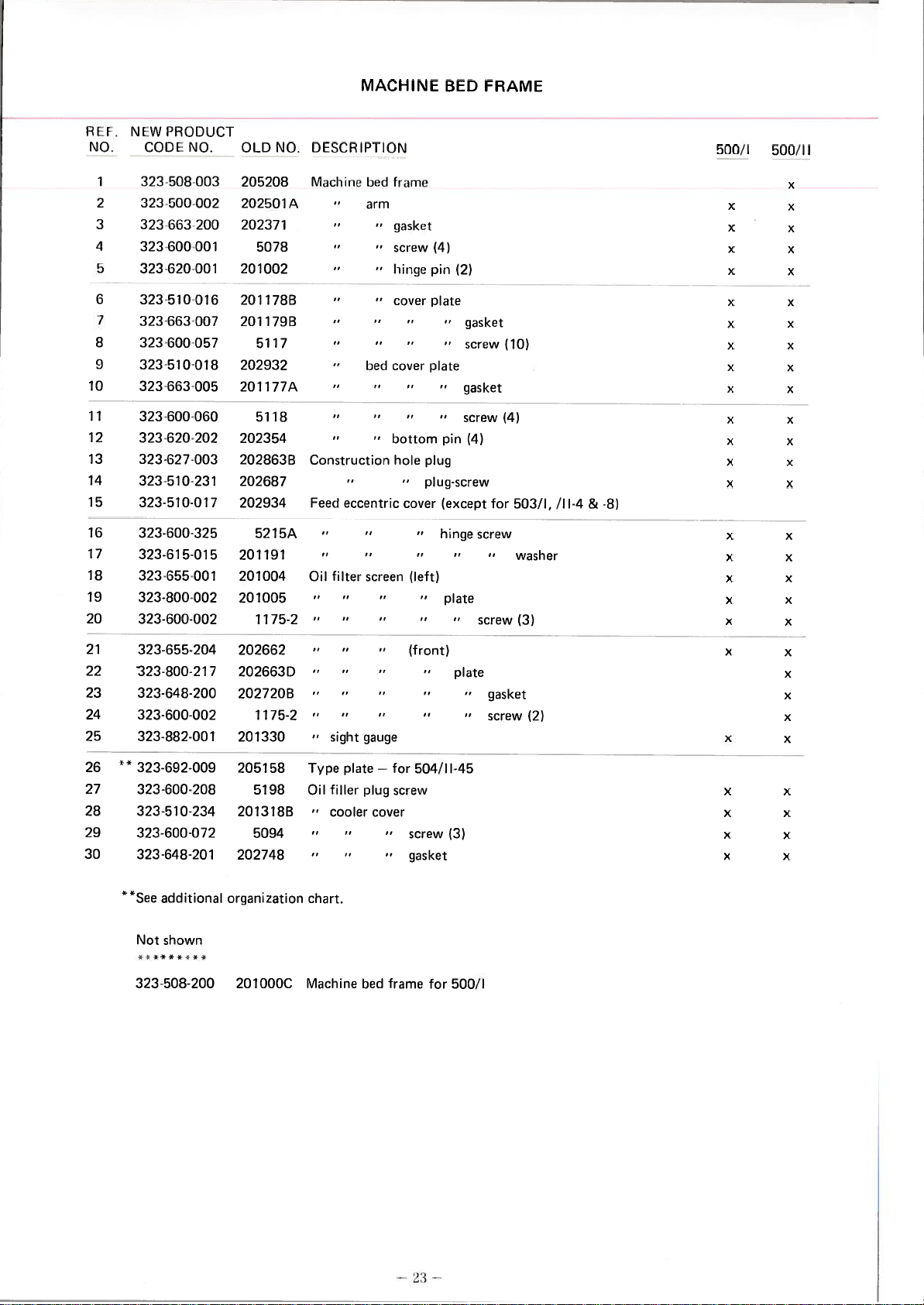
MACHINE
BED
FRAME
lEE.
ND.
10
11
12
13
14
15
16
17
18
19
20
I
2
3
‘1
5
6
1
3
0
IRODUCT
NEW
CODE
:123
503
323
500-002
323
663-200
373
600
323620001
323510-016
323-663-007
323-600-057
323-510-018
323663-005
323-600-060
323-620-202
323-627-003
323-510-231
323-510-017
323-600-325
323-615-015
323-655-001
323-800-002
323-600-002
NO.
003
001
OLD
205208
202501A
202371
5078
201002
201178B
201179B
5117
202932
201177A
5118
202354
202863B
202687
202934
5215A
201191
201004
201005
1175-2
NO.
DESCRIPTION
i(
)i(
arm
bed
Construction
Feed
eccentric
Ill
ter
screen
Oil
iI11f
gasket
screw
hinge
cover
cover
bottom
hole
cover
(left)
(4
pin
(2)
plate
gasket
screw
plate
gasket
screw
pin
(4)
pILIg
plug-screw
(except
hinge
plate
for
screw
screw
(10)
(4)
503/I,
washer
(3)
/11-4
500/I
500/Il
x
x
x
x
x
x
x
x
x
x
x
x
x
x
&
-8)
x
x
x
x
x
x
x
x
x
x
x
x
x
x
x
x
x
x
x
x
x
x
x
27
28
29
30
21
22
23
24
25
26
323-655-204
323-800-217
323-648-200
323-600-002
323-882-001
323-692-009
323-600-208
323-510-234
323-600-072
323-648-201
See
additional
shown
Not
**+
*
*
*
202662
2026630
202720B
1
1
201330
205158
5198
2013
5094
202748
organization
323-508-200 201000C
75-2
18B
“
sight
Type
Oil
filler
cooler
chart.
Machine
plate
“
gauge
—
plug
cover
bed
for
screw
frame
(front)
504/11-45
screw
gasket
for
plate
)3)
500/I
gasket
screw
(2)
x
x
x
x
x
x
x
x
x
x
x
x
x
x
x

30
24
1
29
(11)-
25
21
II
26
16
20
56)
c
28
c13
2)
33)
\4
U
1
)
5’
3
8)
j
—
24—