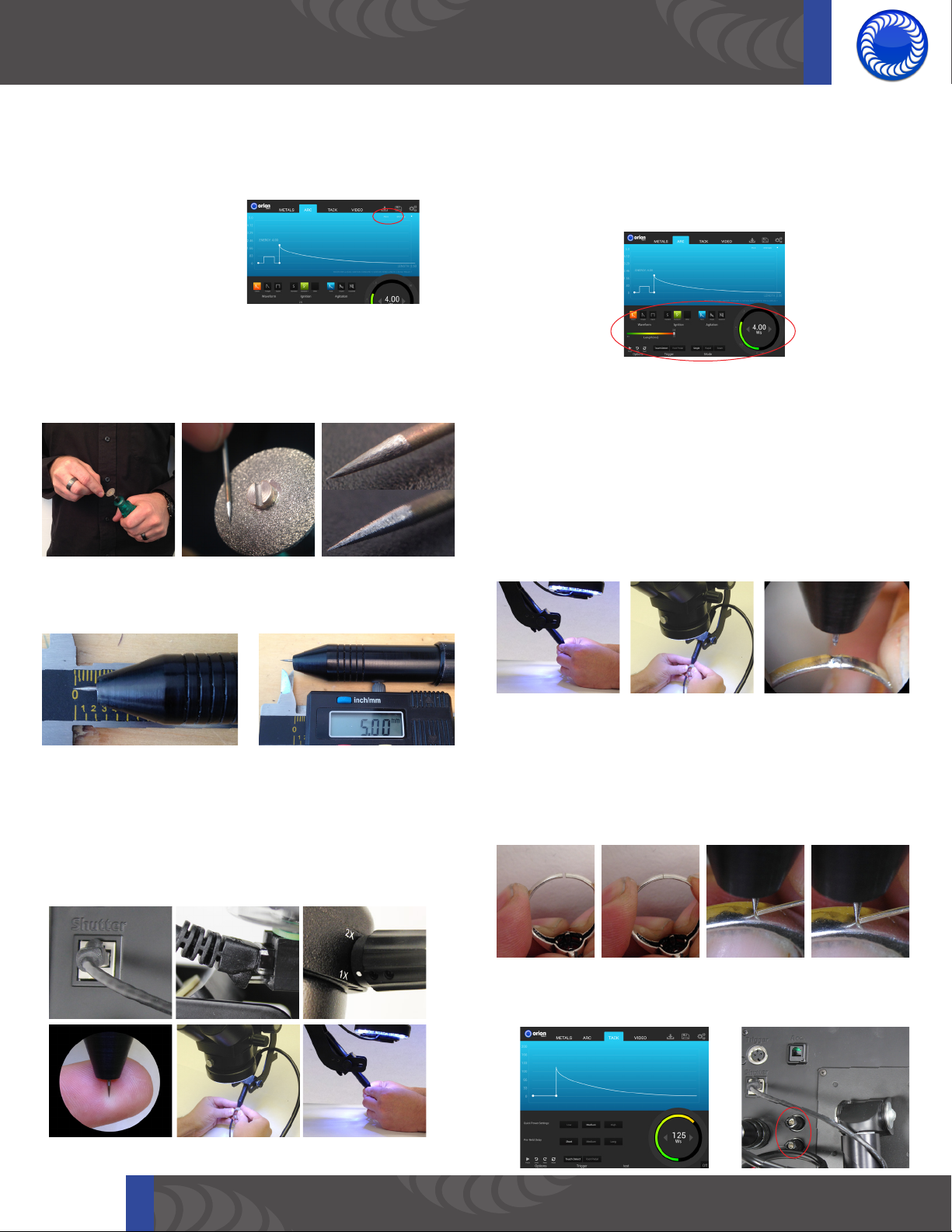
Orion Welders - 200i2 Getting Started
Follow these steps before welding. ese are also great
troubleshooting steps to follow if you feel like your welds are not
consistent or not looking the way you think they should.
STEP 1: Check the Gas Pressure
• Gas is at 7 - 9 psi
STEP 2: Shape the Electrode
• Hold the dremel in one hand (close to the body for support)
and the electrode in the other hand.
• Place the electrode on the diamond disk and spin it to
sharpen.
• Make sure the striations in the electrode are horizontal.
STEP 3: Verify Electrode Length
• e electrode should stick out of the Stylus Cone 4 - 6 mm
(1/8 - 1/4”). Make sure the Stylus Cone is pushed in all the
way (you will feel it click into place and bottom-out).
STEP 5: Welder Settings and when to use the Reset Button
• Before beginning, touch the reset button to make sure all
settings are at factory defaults.
• Verify Energy, Agitation, Ignition, Waveform, Length, Rate,
and Trigger type before beginning a weld. *Settings on p.2
• Push the play button.
STEP6: How to Touch the Electrode to the Work piece
• Clip the alligator clip to the workpiece.
• Rest your hands on the table under the microscope.
• Position the work piece so that it is right under the electrode
then look through the microscope.
• Lightly lift your fingers up and touch the work piece to the
electrode (the electrode will retract after it is touched).
• Hold the work piece steady after touching the electrode - if
you pull the work piece away after touching the electrode, it
will not weld. If you follow the electrode with the work piece
while it is retracting, the electrode will stick to the work piece.
STEP 4: Verify the Microscope Setup
• Microscope cable is securely connected to the back of the
welder and the microscope.
• Zoom knob is positioned on 1x or 2x (not in between).
• Electrode is centered in your field of view and in focus.
• Microscope/Electrode is at a height where you can rest your
hands on the workbench and lift your work piece up with
your fingers.
•
STEP7: How to Set up the Work pieces for Welding.
• When re-sizing a ring, closing a jump ring, or welding two
pieces together; make sure the two sides are pushed
together and flush before welding.
• When adding material, touch the wire to the work piece at a
45-degree angle then enter the electrode in at a 90-degree
angle. Touch the electrode between the work piece and the
wire.
STEP 8: Verify Welder Settings - Tack Screen
• Verify Energy, Length, Trigger type, and make sure one lead
is in the negative port and the other in the positive port.
OrionWelders.com
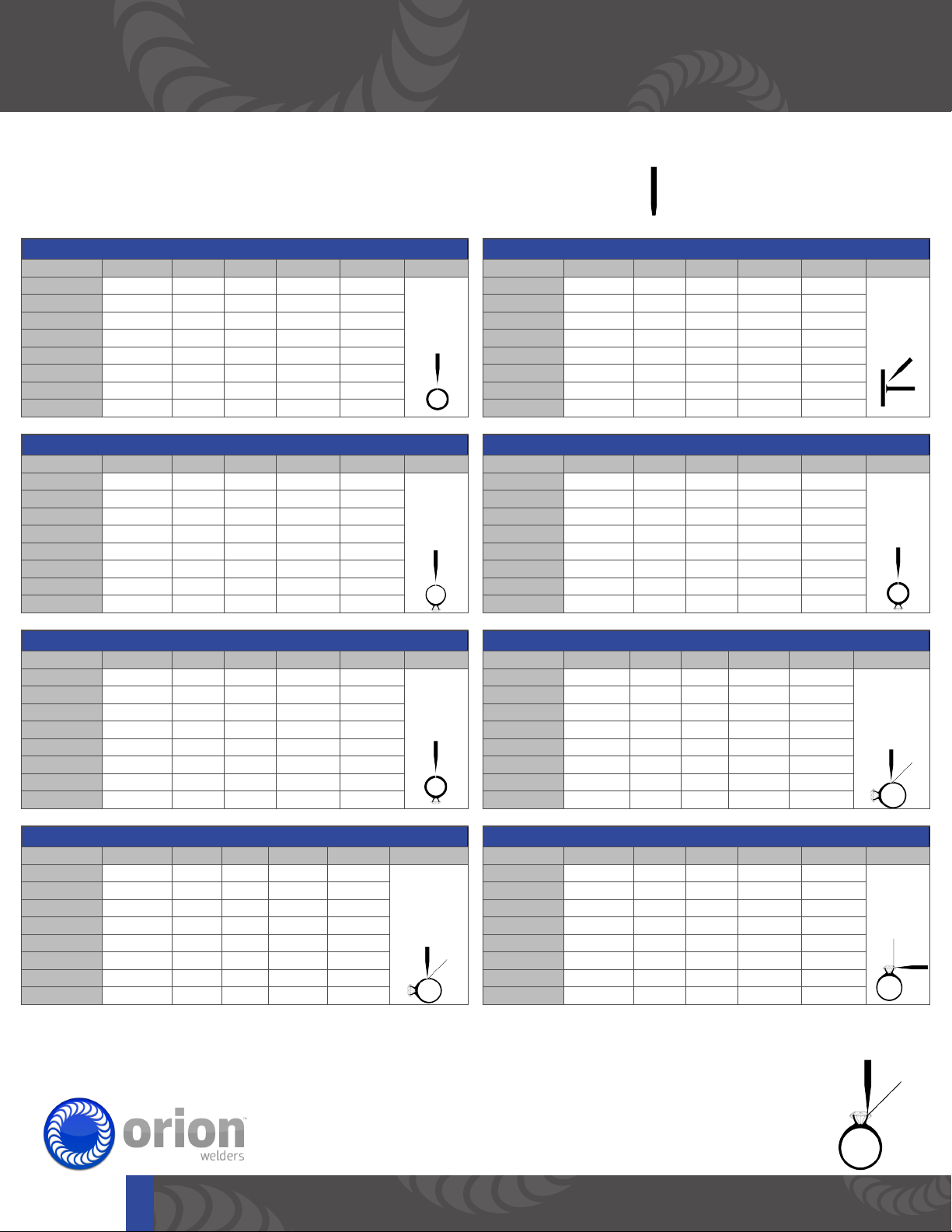
Orion Welders - 200i
2
General Settings for specific metals and applications
Remember:
1. When in doubt, start with your energy lower then work your way up.
2. The image to the right is an example of what a blunt electrode should look like:
3. All settings below are based on the classic waveform
General Settings - 26 AWG wire/chain/jump ring
Metal Tip Shape Energy Length Agitation Ignition Notes
14k Gold Sharp 9 ws 7.5 ms None Standard +
24k Gold Sharp 8 ws 15 ms None Standard +
Silver Sharp 10 ws 15 ms None Standard +
Platinum Sharp 10 ws 7.5 ms None Standard +
Stainless Steel Sharp 7 ws 15 ms Sloped Standard +
Palladium Sharp 6 ws 15 ms Sustained Standard +
Titanium Sharp 7 ws 15 ms Sloped Standard +
Brass Sharp 9 ws 7.5 ms None Standard +
Butt weld
with 90
degree
electrode
angle
General Settings - 0.5mm Ring
Metal Tip Shape Energy Length Agitation Ignition Notes
14k Gold Sharp 12 ws 7.5 ms None Standard +
24k Gold Sharp 11 ws 15 ms None Standard +
Silver Sharp 17 ws 15 ms None Standard +
Platinum Sharp 15 ws 7.5 ms None Standard +
Stainless Steel Sharp 15 ws 15 ms Sloped Standard +
Palladium Sharp 14 ws 15 ms Sustained Standard +
Titanium Sharp 13 ws 15 ms Sloped Standard +
Brass Sharp 15 ws 7.5 ms None Standard +
Butt weld
with 90
degree
electrode
angle
General Settings - 2mm thick Ring
Metal Tip Shape Energy Length Agitation Ignition Notes
14k Gold Sharp 50 ws 60 ms None Standard +
24k Gold Sharp 45 ws 60 ms None Standard +
Silver Blunt 80 ws 60 ms None Standard +
Platinum Sharp 60 ws 60 ms None Standard +
Stainless Steel Sharp 45 ws 60 ms Sloped Standard +
Palladium Sharp 40 ws 60 ms Sustained Standard +
Titanium Sharp 45 ws 60 ms Sloped Standard +
Brass Sharp 55 ws 60 ms None Standard +
Butt weld
with 90
degree
electrode
angle
General Settings - Earring Post
Metal Tip Shape Energy Length Agitation Ignition Notes
14k Gold Sharp 11 ws 7.5 ms None Standard +
24k Gold Sharp 10 ws 15 ms None Standard +
Silver Sharp 12 ws 15 ms None Standard +
Platinum Sharp 12 ws 7.5 ms None Standard +
Stainless Steel Sharp 9 ws 15 ms Sloped Standard +
Palladium Sharp 7 ws 15 ms Sustained Standard +
Titanium Sharp 9 ws 15 ms Sloped Standard +
Brass Sharp 11 ws 7.5 ms None Standard +
T joint with
45 degree
electrode
angle
General Settings - 1mm Ring
Metal Tip Shape Energy Length Agitation Ignition Notes
14k Gold Sharp 22 ws 7.5 ms None Standard +
24k Gold Sharp 20 ws 15 ms None Standard +
Silver Semi Blunt 45 ws 15 ms None Standard +
Platinum Sharp 24 ws 7.5 ms None Standard +
Stainless Steel Sharp 22 ws 15 ms Sloped Standard +
Palladium Sharp 20 ws 15 ms Sustained Standard +
Titanium Sharp 22 ws 15 ms Sloped Standard +
Brass Sharp 26 ws 7.5 ms None Standard +
Butt weld
with 90
degree
electrode
angle
General Settings - Add Material (30 AWG laser wire)
Metal Tip Shape Energy Length Agitation Ignition Notes
14k Gold Sharp 13 ws 7.5 ms None Standard +
24k Gold Sharp 12 ws 15 ms None Standard +
Silver Sharp 14 ws 15 ms None Standard +
Platinum Sharp 8 ws 7.5 ms None Standard +
Stainless Steel Sharp 10 ws 15 ms Sloped Standard +
Palladium Sharp 8 ws 15 ms Sustained Standard +
Titanium Sharp 10 ws 15 ms Sloped Standard +
Brass Sharp 13 ws 7.5 ms None Standard +
Wire at 45
degree angle.
Electrode
touching work
piece next to
wire.
General Settings - Add Material (24 AWG wire)
Metal Tip Shape Energy Length Agitation Ignition Notes
14k Gold Sharp 17 ws 7.5 ms None Standard +
24k Gold Sharp 16 ws 15 ms None Standard +
Silver Sharp 18 ws 15 ms None Standard +
Platinum Sharp 18 ws 7.5 ms None Standard +
Stainless Steel Sharp 15 ws 15 ms Sloped Standard +
Palladium Sharp 13 ws 15 ms Sustained Standard +
Titanium Sharp 15 ws 15 ms Sloped Standard +
Brass Sharp 17 ws 7.5 ms None Standard +
Wire at 45
degree angle.
Electrode
touching work
piece next to
wire.
Orion Welders
1-877-786-9353
1693 American Way #5
Payson, UT 84651 USA
General Settings - Retip Prong (26 AWG wire)
Metal Tip Shape Energy Length Agitation Ignition Notes
14k Gold Sharp 9 ws 7.5 ms None Standard +
24k Gold Sharp 8 ws 15 ms None Standard +
Silver Sharp 10 ws 15 ms None Standard +
Platinum Sharp 10 ws 7.5 ms None Standard +
Stainless Steel Sharp 7 ws 15 ms Sloped Standard +
Palladium Sharp 6 ws 15 ms Sustained Standard +
Titanium Sharp 7 ws 15 ms Sloped Standard +
Brass Sharp 9 ws 7.5 ms None Standard +
The above method will allow the user to attach the wire to the
prong tip. If the user desires to add metal to the tip without
the wire staying attched, use a 30 AWG wire and position the
electrode and 30 AWG wire as seen in the picture to the right.
This method will allow the user to add a little bit of metal at a
time, covering the top of the prong with every weld.
Wire at 45 degree angle.
Electrode touching work
piece next to wire.
Butt weld
with 90
degree
electrode
OrionWelders.com
angle