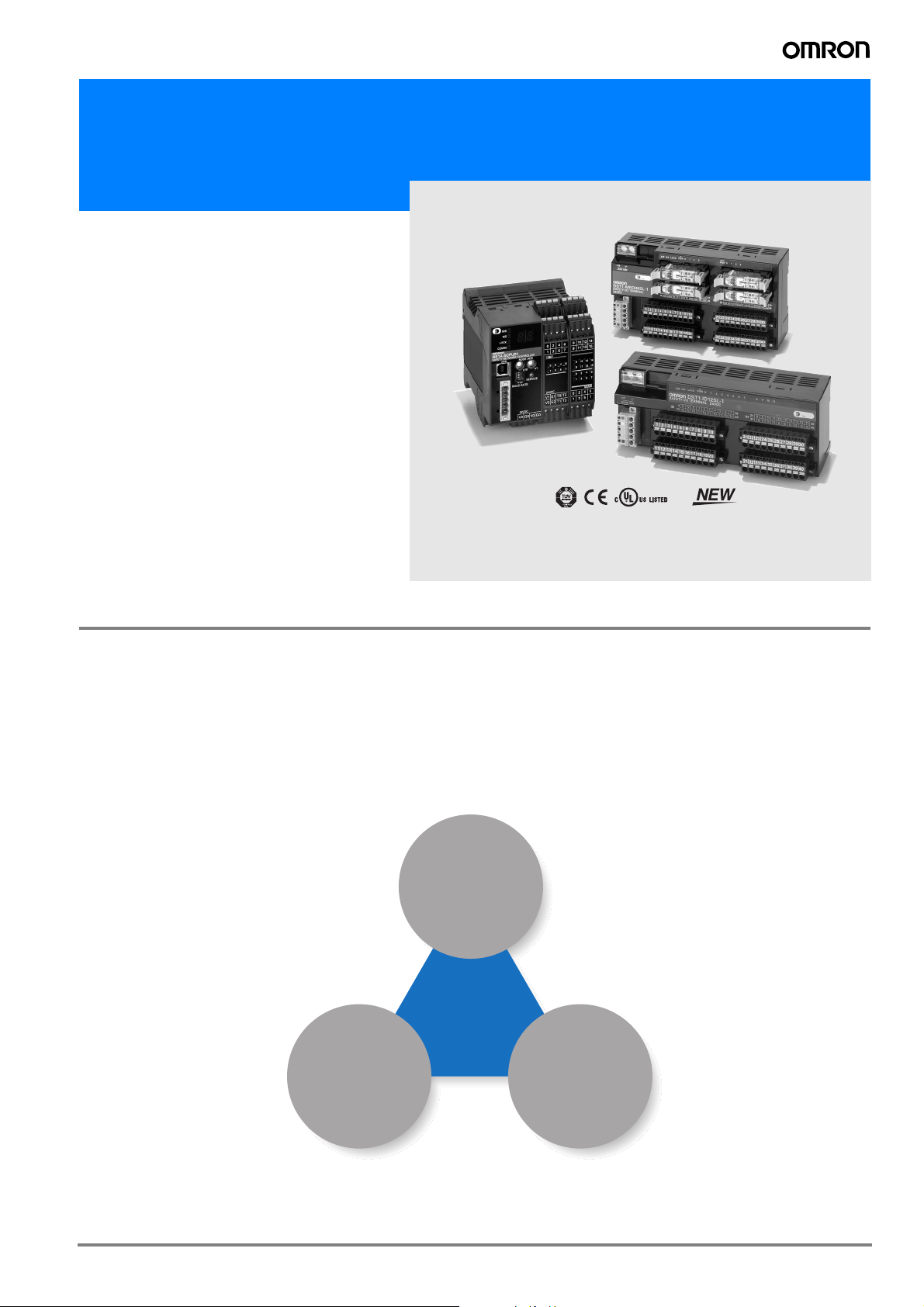
DeviceNet Safety System
NE1A/DST1
Omron now offers a DeviceNet
compatible Safety System, that
can be used 3-ways: as a Standalone controller, as a Safety network expandable with remote I/O
blocks, or combined with
DeviceNet to form a combined
Network.
• Conforms to Global Safety Standards
• Individual I/O LED status and error indicators
• USB Programming Port
• IEC 61508 SIL 3
• EN954-1 Category 4
• UL1604 Class 1, Div. 2 Group A,B,C,D
Product Information
Introducing a Safety Network System that dramatically alters previous safety design.
Programmable safety circuits are incorporated to facilitate efficient designing and modifications. Moreover, Safety I/O Terminals
can be added to increase safety I/O capacity for distributed allocation through the network. DeviceNet wiring on the existing network can be used as is, facilitating efficient design by expanding on the existing system.
The programmability of safety circuits, expandability of I/O using the network, and compatibility with the DeviceNet open network
effects major changes to the framework of previous safety design systems.
Programmable
Safety Circuits
DeviceNet
Safety
System
Safety I/O Can Be
Expanded through the
Network.
Compatible with
DeviceNet Open
Network
Safety
D-1NE1A/DST1
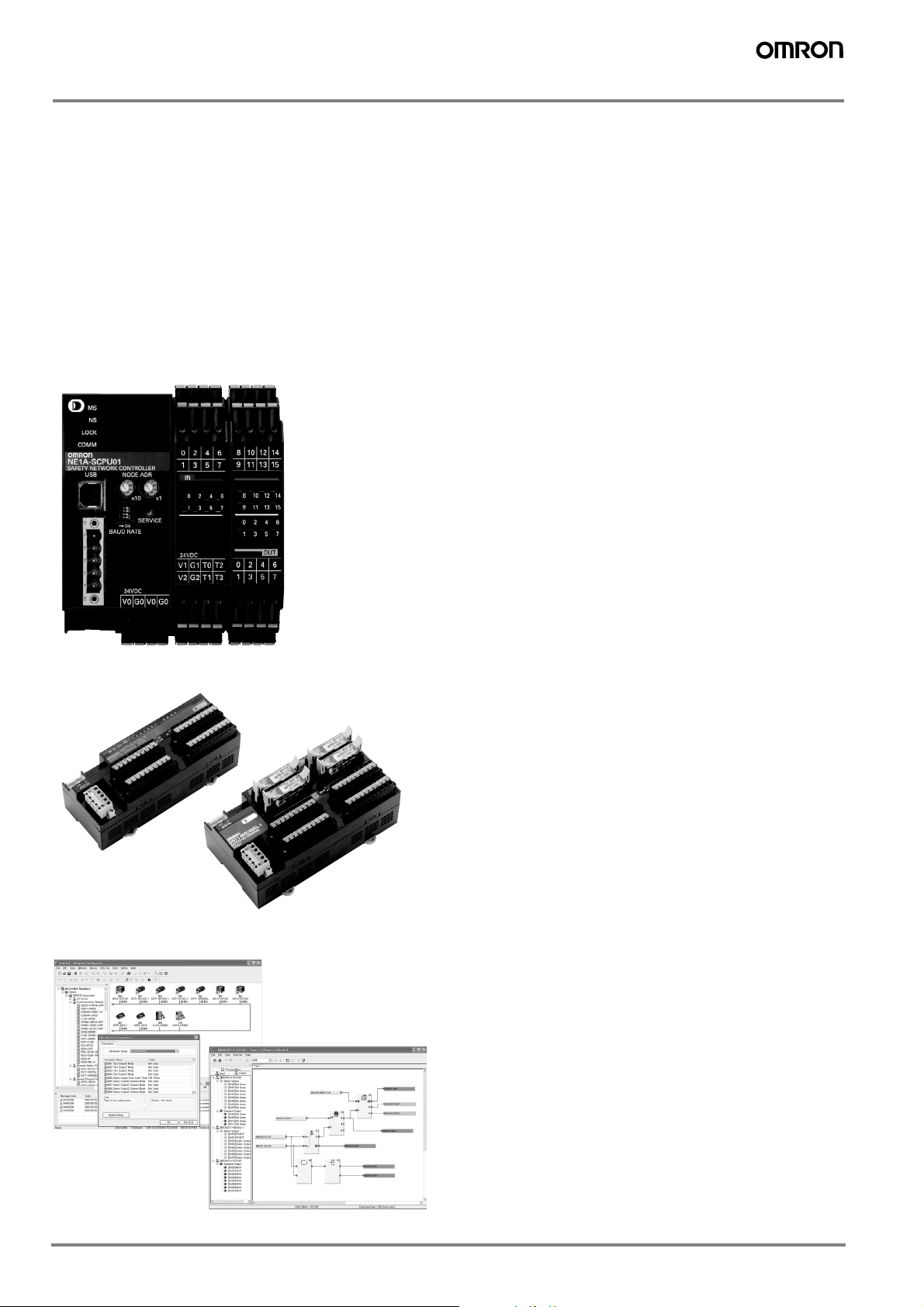
Complies with the Highest Safety Standards in the world
The DeviceNet Safety System conforms to IEC 61508 SIL3 for functional safety, and EN 954-1 Category 4 for machine safety,
complying with the world's highest level of safety standards.
IEC 61508 SIL 3
Safety circuits must be able to function to provide safety at anytime.
Conversely, the degree of lack of safety is used as the indicator. In
IEC 61508, safety is defined as the Probability of Failure per Hour, or
PFH. Based on this, the SIL (Safety Level) is classified into four levels. SIL 3 indicates a probability of dangerous failure of once in 1,000
years, which is the highest level in machine safety.
EN 954-1 Safety Category 4
EN standards evaluate the level of machine risk and require the incorporation of risk minimization measures. In EN 954-1, five safety categories have been established, with Safety Category 4 indicating
designs that require the highest safety design level. This category is
demanded for machines with the highest level of danger, wherein "serious injury (severed limbs, death, etc.) will occur frequently, with little
chance of escaping danger." This category demands that a single
fault (failure) in any part of the machine, or a series of faults, will not
lead to loss of the machine's safety functions.
NE1A-SCPU01 Safety Network Controller
Programmable Safety Control
• Incorporates 16 safety inputs and 8 safety outputs.
Functions as a compact safety PLC even without using a network.
• Construct safety circuits easily with special Function Blocks.
• Up to 128 Function Blocks can be used.
DeviceNet Safety Communications Functions
• Provides DeviceNet Safety Master functionality.
Connect up to 16 Safety Slaves.
Expand using up to sixteen Input Slaves with 12 points each
(192 points total) and eight I/O Slaves with 16 points each
(128 points total).
• Safety Slave functionality is also included. Interlock control can
be incorporated between Safety Network Controllers.
DeviceNet Slave Functionality
• Monitor safety I/O and status information from the DeviceNet
Master.
DST1-series Safety I/O Terminals
Safety Input and Safety I/O Models Available
• Safety inputs: 12-point model (DST1-ID12SL-1)
• Safety I/O: 8-point/8-point model (DST1-MD16SL-1)
• Safety I/O: 4-point/4-point (relay outputs) model
(DST1-MRD08SL-1)
DeviceNet Slave Functionality
• Safety I/O and status information can be allocated as a DeviceNet
Slave.
• Maintenance functions are provided for measuring the number of
operations or the operating time for safety devices.
Easy Wiring
• Superior construction and preventive maintenance using clamp
connectors.
WS02-CFSC1-E Safety Network Configurator
Network Configurator Functions
• Includes previous DeviceNet Configurator functions.
• Performs setup for the DeviceNet Safety network configuration.
Programming Functions
• I/O configuration functions for Safety Network Controllers and
Safety I/O Terminals.
• Programming functions for safety circuits.
• Monitor programs.
D-2 DeviceNet Safety System
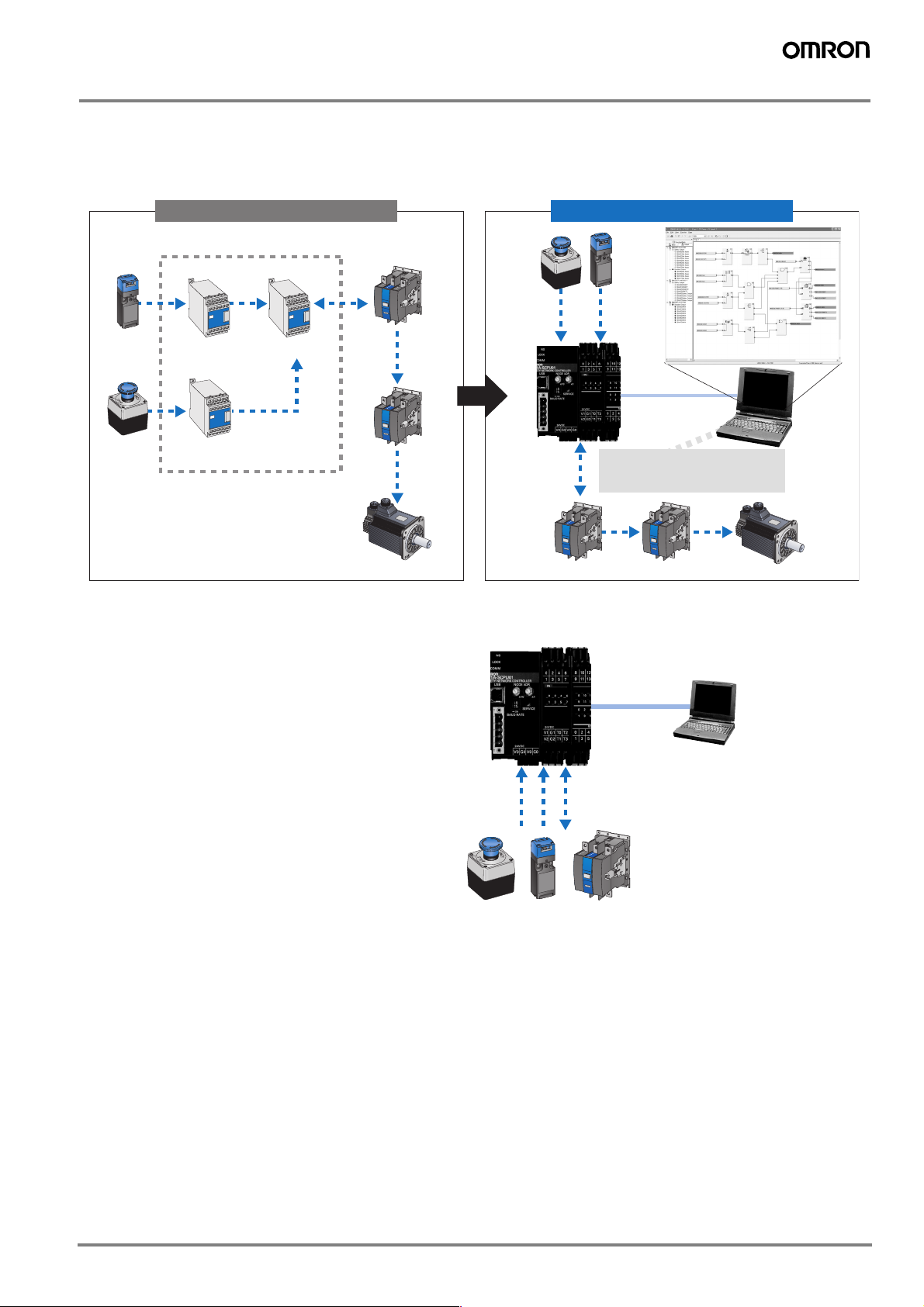
Stand-Alone Programmable Controller
Programmable Safety Circuits
Until now, safety design involved combining safety relays to configure safety control circuits. This process involved tedious wiring, and moreover,
any changes required direct modification of the wiring. The DeviceNet Safety System uses programmable safety circuits, dramatically improving
the ease of design and modification.
Previous Safety Control Circuits Programmable Safety Circuits
Safety Door
Switch
Emergency
Stop Pushbutton
Switch
Safety Relay
Unit
Safety Relay
Unit
System Configuration 1
Configuration Example for High-speed Safety
I/O Response Using Small Number of Points
● NE1A-SCPU01
● WS02-CFSC1-E
Delivers high-speed I/O response in a single Unit
with up to 16 safety inputs and 8 safety outputs.
Safety Relay
Unit
Contactor
Contactor
Motor
NE1A-SCPU01
Safety Network
Controller
Emergency
Stop Pushbutton
Switch
Safety Door
Switch
Safety Network
Controller
USB
Safety logic operations can be
programmed using Function Blocks.
Contactor Contactor
USB
Motor
WS02-CFSC1-E
Safety Network
Configurator
Safety Network
Configurator
Stop Pushbutton
Switch
Safety Door
Switch
ContactorEmergency
D-3NE1A/DST1
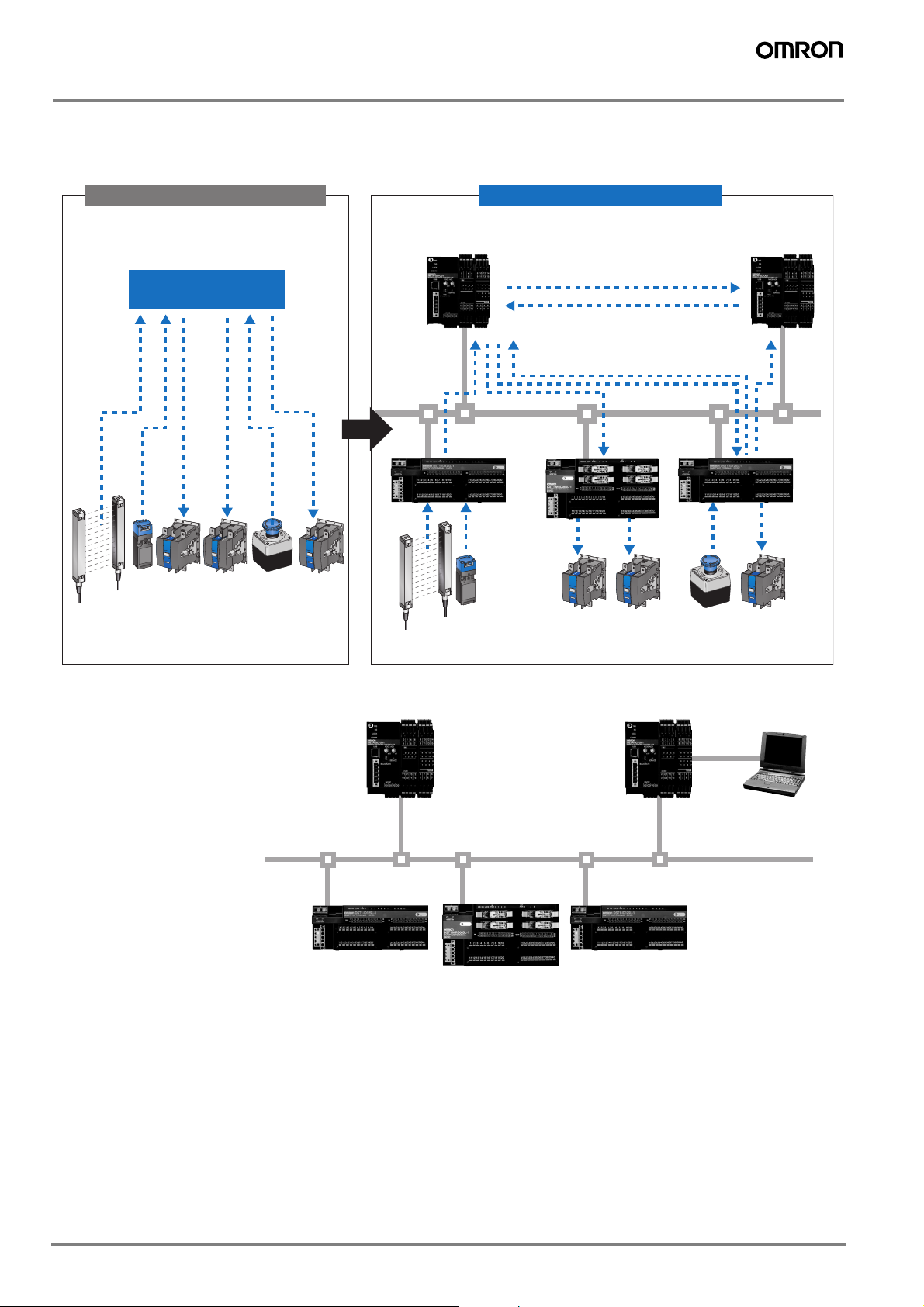
Safety Network
Expand Safety I/O Through Networks
Safety components distributed over many different installation locations required long and complicated wiring.
Replacing the wiring with a network between safety components greatly improves productivity
Previous Machine Connections
Safety control
Safety Light
Curtain
Safety
Door Switch
Contactor
Contactor
Emergency
Stop Pushbutton
Switch
Contactor
Connecting Devices Using DeviceNet Safety
By using Safety I/O Terminals, safety I/O can be expanded easily
through the network.
Safety Network
Controller
Safety Network
Controller
DeviceNet Safety
Safety I/O
Terminal
Safety
Door Switch
Safety Light Curtain
Expand a Safety Network Controller using up to sixteen Input Slaves with 12 points each
(192 points total), and up to eight I/O Slaves with 16 points each (128 points total).
Safety I/O
Terminal
ContactorContactor
Emergency Stop
Pushbutton Switch
Safety I/O
Terminal
Contactor
System Configuration 2
Example of Safety I/O Configuration for
Distributed Hazard Sources
● NE1A-SCPU01
● DST1 Series
● WS02-CFSC1-E
Distributed allocation of safety I/O devices
can be achieved easily using Safety
I/O Terminals and the DeviceNet Safety Network.
DST1-ID12SL-1
Safety I/O Terminal
NE1A-SCPU01
Safety Network
Controller
DeviceNet Safety
DST1-MRD08SL-1
Safety I/O Terminal
NE1A-SCPU01
Safety Network
Controller
DST1-MD16SL-1
Safety I/O Terminal
USB
WS02-CFSC1-E
Safety Network
Configurator
D-4 DeviceNet Safety System