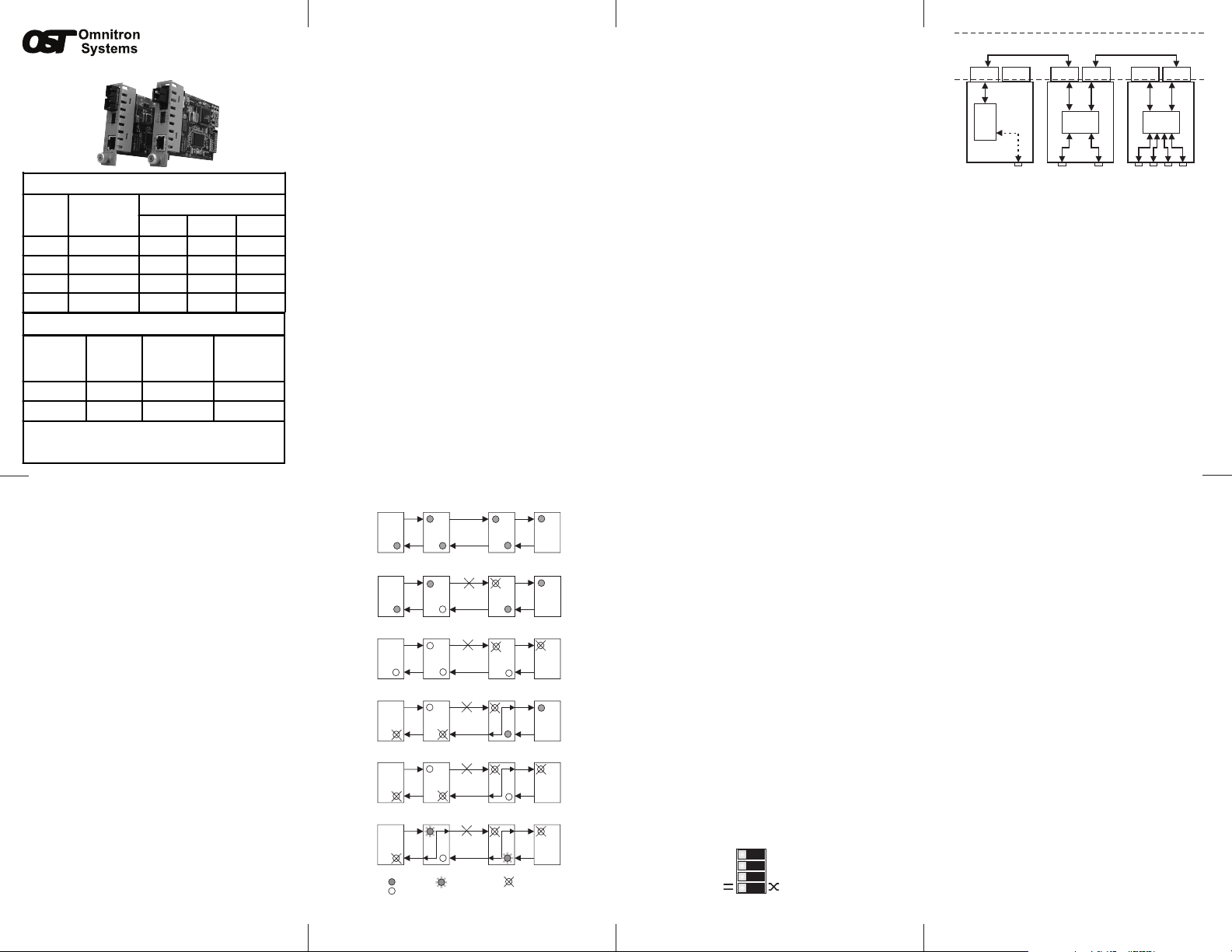
iConverter
LED Lit LED Blinking LED Off
LED Status depends on connected device
Switch 1 Converter A Converter B Switch 2
(a)
LS
Fiber
UTP
UTP
Fiber
LS
Switch 1 Converter A Converter B Switch 2
LS
(b)
LS
(c)
Switch 1 Converter A Converter B Switch 2
LP
LP
(d)
Switch 1 Converter A Converter B Switch 2
LP
RFD+LS
(e)
Switch 1 Converter A Converter B Switch 2
SFD
SFD
(f)
Switch 1 Converter A Converter B Switch 2
LP
RFD+LP
LP
RFD
SFD
=
=
=
=
Link Propagate
Remote Fault Detect
Symmetrical Fault Detect
Crossover
LS
Off
Off
=
=
Link Segment
Straight-Through
iConvert er
GX/T Dual Fiber Modules
Fiber
Type
Distance
Connector Type
SC MT-RJ LC
MM 220m / 550m
1
8522-0 8524-0 8526-0
SM 12 km 8523-1 8525-1 8527-1
SM 34 km 8523-2 - 8527-2
SM 80 km 8523-3 - 8527-3
iConvert er
GX/T Single-Fiber Modules
Fiber /
Connector
Type
Distance
Tx: 1310nm,
Rx: 1550nm
Tx: 1550nm,
Rx: 1310nm
SM / SC 20 km 8530-1 8531-1
SM / SC 40 km 8530-2 8531-2
For wide temperature (-40 to 60º C), add a "W" to the end
of the model number. Consult factory for extended
temperature (-40 to 75º C) models.
Port 1 (P1)
Port 2 (P2)
®
GX/T User Manual
OVERVIEW
The iConverter GX/T provides 10/100/1000BASE-T
UTP to 1000BASE-X Fiber conversion as well as
rate conversion between 10BASE-T, 100BASE-TX,
1000BASE-T and 1000BASE-SX/LX. Models are
available for multimode (MM) and single-mode (SM)
dual ber, and single-mode single-ber (SF).
The GX/T UTP port supports Half-Duplex and FullDuplex modes and features an automatic crossover
mode for easy attachment to hubs, switches and
workstations.
The GX/T can be used as a standard two-port UTP to
ber converter. It can also use its two additional 10/100
backplane ports to connect to adjacent modules and
accommodate flexible network configurations. The
iConverter 19-Module, 5-Module or 2-Module Chassis
have backplanes that facilitate connectivity between
adjacent modules.
The GX/T can be used in a managed or unmanaged
application. When managed, it must be installed in a
chassis with an iConverter Network Management Module
(NMM), GX/TM or 10/100M.
ADVANCED FEATURES
The GX/T features Port VLAN and Tag VLAN, which
allow complete control of trafc ow between the frontplane UTP port, the ber port and the chassis backplane
ports. The GX/T also features Port Access Control, which
facilitates enabling and disabling of individual ports. It
also supports reporting of MIB statistics.
NOTE: Using the advanced features listed above
requires the use of the Network Management Module
(NMM) and the NetOutlook™ Management Software
(or third-party SNMP management software) or Telnet.
For more information on using and conguring these
advanced features, please refer to the NetOutlook
Management Software user manual.
PORT STRUCTURE
Using a 4-port switch design, the GX/T features
two front-plane ports (1000Mbps ber Port 1 and a
10/100/1000 UTP Port 2) and two 10/100 Ethernet
backplane ports (A and B) that can connect to adjacent
modules within the same chassis.
When the GX/T backplane A and B ports are enabled
(using “BPAEN” and “BPBEN” DIP-Switches), they
connect via the chassis backplane to the slots on the
left and right sides of the GX/T module. When another
switch-based module with backplane port connections
(such as a second GX/T or an NMM) is installed in an
adjacent slot, it can be connected via the backplane
to the GX/T to facilitate a multi-module conguration.
GX/T Application Example:
Fig. 1 depicts a chassis with three modules plugged into
three adjacent backplane slots (beginning with an odd
numbered slot). The adjacent slots are connected via the
backplane using the A and B 10/100 links. In this example,
the GX/T in the center slot connects to the slot on its left
using the A link and the slot on its right using the B link.
Slot 1 (odd) Slot 2 (even) Slot 3 (odd)
Chassis
Backplane
“A” Link
A Port
B Port
NMM
front /
back
select
NMM UTP
10 port
Fig. 1 In-Band Managed GX/T Application
A Port
Fiber
1000 port
B Port
Internal
10/100/1000
switch chip
10/100/1000 port
UTP
“B” Link
A Port
Internal
10/100
switch chip
4-port 10/100 UTP
Switch
4Tx Module
B Port
In this example, the module on the left is a Network
Management Module (NMM), connecting via its A backplane
port to the GX/T, facilitating In-Band management (via the
ber uplink). The module on the right is a 4-port 10/100 switch
module, connecting via its B link port to the GX/T, facilitating a
1-Port GX/T and a 4-Port 10/100 Ethernet switch with a ber
uplink conguration. This 3-module conguration provides
an effective 10/100/1000 UTP to 4-Port 10/100 managed
switch with a gigabit ber uplink conguration.
This example shows how the GX/T can be used
either as a traditional managed or unmanaged media
converter, or to create exible and effective network
switch congurations.
For more information about individual chassis A and
B backplane links, please refer to the specic chassis
user manual.
LINK MODES
In order to accommodate different user needs, the GX/T
supports ve different linking modes (see Fig. 2).
In Link Segment (LS), a port transmits a Link signal
independently of any received Link at any other port.
For example, the UTP transmits a Link regardless of
the ber receiving a Link [Fig. 2(a) & (b)].
In Link Propagate (LP), a port transmits a Link signal only
when receiving a Link at its other port. For example, the
UTP transmits a Link only when receiving a Link at the
ber port [Fig. 2(c)].
In Remote Fault Detection + Link Segment (RFD+LS),
the ber port transmits a Link signal only when receiving
a Link at the ber port. As a result, ber faults (no
Link received at the ber) are looped-back and can be
reported to the network core [Fig. 2(d)].
In Remote Fault Detection + Link Propagate (RFD+LP),
the UTP port transmits a Link signal only when receiving
a Link at the ber port. The ber port transmits a Link
signal only when receiving Link signals at both the ber
port and the UTP port. As a result, ber faults (no Link
received at the ber) are propagated forward and looped
back for fault reporting at both the network core and the
customer location [Fig. 2(e)].
NOTE: Connecting two converters with both set to RFD
mode is not supported and will cause a “deadly embrace”
lockup.
Page 5 Page 6 Page 7 Page 8
Page 2 Page 3
In Symmetrical Fault Detection (SFD), the UTP port
transmits a Link signal only when receiving a Link at
the ber port. The ber port transmits a Link signal only
when receiving a Link signal at both the ber port and
the UTP port. As a result, ber faults (no Link received
at the ber) are looped back and can be reported to the
network core. In addition, connecting two back-to-back
converters which are both set to SFD facilitates dual-
loop-back, where ber faults are reported to both ends
of the network. A blinking ber link LED on a converter
indicates a fault of the transmit ber or UTP cables of
that converter [Fig. 3(f)].
NOTE: Converters in SFD mode must be deployed
in pairs.
Fiber set to Auto-Negotiation Mode
When the Fiber is set to Auto-Negotiation Mode, the
device receiving the fault acts as if it is in RFD mode.
Link Segment, Link Propagate and Symmetrical Fault
Detection modes operate in the same manner (refer to
Fig. 2(d), (e) and (f).
NOTE: “Remote Fault Detection” (RFD) is not a valid
mode when the ber is set to Auto-Negotiation. The user
should select LS, LP or SFD instead.
DIP-SWITCH SETTINGS
Front Panel DIP-Switch Settings
Fig. 2 GX/T Link Modes
Fig. 3 Front Panel DIP-Switches
Page 4
Link Segment/Link Propagate “LS/LP” DIP-Switch
This DIP-Switch controls the Link Propagate or Link
Segment modes. When the DIP-Switch is in the “LS”
position (factory setting), Link Segment mode is enabled.
In the “LP” position, Link Propagate mode is enabled.
Remote Fault Detection “RFD” DIP-Switch
When in the “RFD” position, the Remote Fault Detection
mode is enabled. Set the board-mounted Port 1
DIP-Switch to Manual Mode “MAN” for this feature.
NOTE: Connecting two converters with both set to
RFD mode is not supported and will cause a “deadly
embrace” lockup.
Symmetrical Fault Detection “SFD” DIP-Switch
When this DIP-Switch is in the “SFD” position, the
Symmetrical Fault Detection mode is enabled. When in
the “Off” position (factory setting), the Symmetrical Fault
Detection mode is disabled.
NOTE: Converters in SFD mode must be deployed
in pairs.
RJ-45 Manual Crossover “= / X” DIP-Switch
When the board-mounted Manual Crossover Enable
DIP-Switch is set to “MANX,” the front panel RJ-45
Manual Crossover Switch is enabled. When connecting
the UTP to a hub or switch, set the front panel switch to
Straight-Through “=” (factory setting). When connecting
to a workstation, set it to Crossover “X.” Only use this
setting with 10T or 100Tx mode.
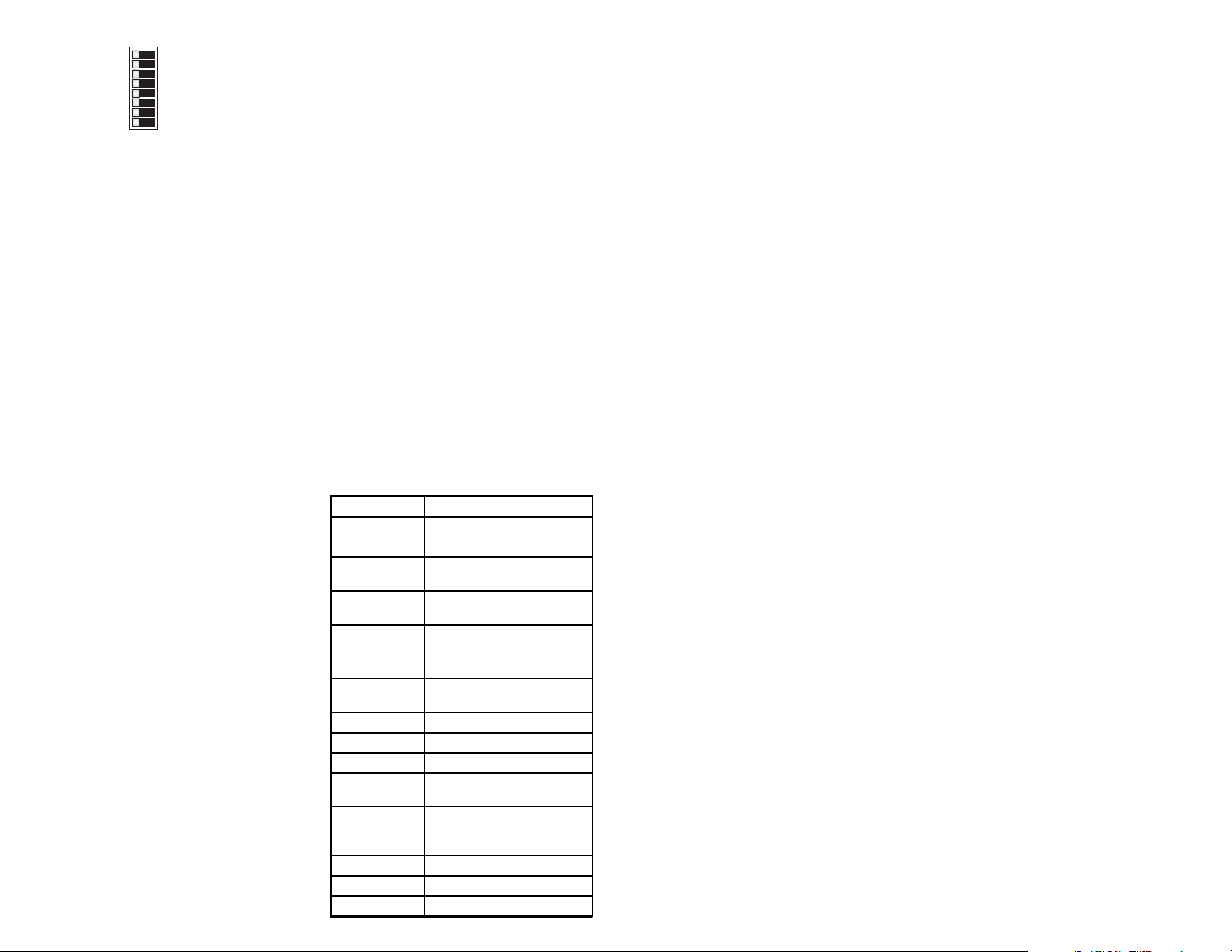
BOARD MOUNTED DIP-SWITCHES
10
10-100
MANX
=
=
=
UTP 10Mbps
UTP 10/100Mbps
Manual Crossover
BPAEN
BPBEN
MAN
=
=
=
Backplane “A” Enabled
Backplane “B” Enabled
P1 Manual FO
100
1000
AX
=
=
=
MAN=P2 Manual UTP
P2 Auto Negotiate
UTP 100Mbps
UTP 1000Mbps
Auto Crossover
AN
=
Off
Off
P1 Auto Negotiate
ON
HD
=P2 Half Duplex
FD
=P2 Full Duplex
AN
=
Model Type GX/T
Protocols
10BASE-T, 100BASE-TX,
1000BASE-T,
1000BASE-SX/LX
UTP
Connectors
RJ-45
Fiber
Connectors
SC, MT-RJ, LC, Single-Fiber
SC
Controls
BP Enable, X-Over, LS/LP,
RFD, SFD, UTP Auto/Man,
10/100/1000, UTP FDX/HDX,
F/O Auto/Man
LED Displays
Power, FO link, UTP link, Auto,
FDX/HDX, 10/100/1000
Dimensions
W:0.85" x D:4.5" x H:2.8"
Weight
8 oz.
Compliance
UL, CE, FCC Class A
Power
Requirement
1.4A @ 3.3VDC (typical)
Temperature
Standard: 0 to 50º C
Wide: -40 to 60º C
Storage: -40 to 80º C
Humidity
5 to 95% (non-condensing)
Altitude
-100m to 4000m
MTBF (hrs)
830,000
Fig. 4 Board Mounted DIP-Switches
Backplane A Enable DIP-Switch (BPAEN)
When the “BPAEN” DIP-Switch is in the “ON” position
(right), the iConverter GX/T module A backplane Ethernet
port is enabled. This port allows connectivity to an
adjacent module. When the “BPAEN” DIP-Switch is in the
“Off” position (left, factory setting), the A port is isolated
from the backplane.
Backplane B Enable “BPBEN” DIP-Switch
When the Backplane B Enable “BPBEN” DIP-Switch is
in the “ON” position (right), the iConverter GX/T module
B backplane Ethernet port is enabled. This port allows
connectivity to an adjacent module. When the “BPBEN”
DIP-Switch is in the “Off” position (left, factory setting),
the B port is isolated from the backplane.
Fiber Auto/Manual P1 “AN/MAN” DIP-Switch
Setting this DIP-Switch to P1 Auto-Negotiate “AN”
(factory setting) enables the Fiber Port to determine
duplex mode automatically. If the connected device
cannot provide the proper signal to indicate its own mode
of operation, this DIP-Switch should be set to P1 Manual
“MAN.” This feature allows connections with devices that
do not auto-negotiate properly.
Page 9
NOTE: When the fiber port is in Manual Mode,
sometimes a link-up will not occur with other devices.
Both devices must be set to the same mode (either
Manual or Auto-Negotiate) for the link-up to occur.
UTP Auto/Manual P2 “AN/MAN” DIP-Switch
Setting the P2 Auto/Manual Negotiate DIP-Switch to
Auto-Negotiate “AN” (factory setting) enables the
UTP port to determine the speed and duplex mode
automatically. If the connected device cannot
provide the proper signal to indicate its own mode of
operation, this DIP-Switch should be set to P2 Manual
“MAN.” This feature allows connections with devices
that do not auto-negotiate properly.
NOTE: Attaching an auto-negotiating UTP port to a non
auto-negotiating (manual/forced/hard-coded) UTP port
may result in an unpredictable port setting with excessive
collisions and poor link performance. When operating in
manual mode, both mating ports MUST be set manually
to the same speed and duplex mode.
Gigabit devices typically function only in Auto-Negotiate
Mode. 1000 Manual Mode is not a valid mode and will
result in an undened response. Use Manual mode only
when selecting the 10 or 100 mode.
UTP Full/Half-Duplex P2 “FD/HD” DIP-Switch
When the UTP P2 Auto/Manual DIP-Switch (described
above) is in the P2 Manual “MAN” position, the UTP P2
Full/Half Duplex “FD/HD” DIP-Switch selects the duplex
mode for the UTP port. When set to Full-Duplex “FD”
(factory setting), the UTP port operates in Full-Duplex
mode. When P2 is set to Half-Duplex “HD,” the UTP
port operates in Half-Duplex mode.
Page 10 Page 11
UTP 10/100 P2 “10/100” DIP-Switch
When the UTP P2 Auto/Manual DIP-Switch is in the
Auto-Negotiate “AN” position and the “10-100/1000”
DIP-Switch (described below) is set to “10-100,” the
“10/100” DIP-Switch determines the highest speed of
the UTP P2 port in the following manner:
When the “10/100” DIP-Switch is set to the “100” position,
P2 operates at 100Mbps or less, depending on the speed
of the connected device.
When the “10/100” DIP-Switch is set to the “10” position,
P2 operates only at 10Mbps.
When the UTP P2 Auto/Manual DIP-Switch is in the
Manual “MAN” position and the UTP “10-100/1000”
DIP-Switch (described below) is set to “10-100,” the
“10/100” DIP-Switch determines the speed of the UTP
P2 port. When set to “100” (factory setting), the UTP port
will operate at 100Mbps. When set to “10,” the UTP port
will operate at 10Mbps.
UTP 10-100/1000 P2 “10-100/1000” DIP-Switch
When the P2 “AN/MAN” DIP-Switch is set to the
Auto-Negotiate “AN” position, the “10-100/1000”
DIP-Switch operates in the following manner:
When set to “1000,” P2 operates at 1000Mbps or less,
depending on the speed of the connected device. When
set to the “10-100” position, the speed is selected by the
UTP “10/100” DIP-Switch.
When the P2 “AN/MAN” DIP-Switch is set to Manual
“MAN” mode, the “10-100/1000” DIP-Switch must be
set to the “10-100” position and the speed is selected
by the “10/100” DIP-Switch.
NOTE: Setting the “10-100/1000” DIP-Switch to the
“1000” position when in Manual mode is not permitted
(per the IEEE 802.3 standard) and will result in
unpredictable port behavior.
Auto/Manual Crossover Enable P2 “AX/MANX”
DIP-Switch
When the Manual/Auto Crossover Enable DIP-Switch
is set to Auto Crossover “AX” (factory default), the
front panel crossover switch is disabled and the RJ-45
crossover is selected automatically. When it is set
to Manual Crossover “MANX,” the front panel RJ-45
Manual Crossover DIP-Switch is enabled to allow a
manual setting in either Crossover or Straight-Through
connection.
Page 12
LED INDICATORS
LED Color Description
Pwr: Yellow On--Power / Blink--test
Fiber FDX: Green On--Full-Duplex detected
Lk/Act Green On--Link / Blink--activity
AN: Green On--UTP Auto-Neg. enabled
10: Green On--10 Mbps link / Blink-activity
100: Green On--100 Mbps link / Blink-activity
1000: Green On--1000 Mbps link / Blink-activity
UTP FDX: Green On--Full-Duplex detected
Mounting and Cable Attachment
iConverter modules are hot-swappable and can be
installed into any chassis in the iConverter family.
1. Carefully slide the iConverter module into the
installation slot, aligning the module with the
installation guides. NOTE: Ensure that the module
is rmly seated against the backplane.
2. Secure the module by securing the panel fastener
screw (attached to module) to the chassis front.
3. Attach the UTP port via a category 5 cable to a
1000BASE-T, 100BASE-TX or 10BASE-T Ethernet
device.
4. Attach the ber port via an appropriate multimode or
single-mode ber cable to a 1000BASE-X Ethernet
device. The iConverter transmit (Tx) must attach to
the receive side on other device; the receive (Rx)
must attach to the transmit.
5. When using single-ber (SF) media converter models,
the Tx wavelength on one end has to match the Rx
wavelength on the other. Note that based on this
guideline, the SF media converter models must be
used in pairs, such as the 8530-1 matched with the
The operating description in this Instruction Manual is for use by
qualied personnel only. To avoid electrical shock, do not perform
any servicing of this unit other than that contained in the operating
instructions, unless you are qualied and certied to do so by
Omnitron Systems Technology, Inc.
Warranty
Warning
This product is warranted to the original purchaser against
defects in material and workmanship for a period of TWO
YEARS from the date of shipment. A LIFETIME warranty may be
obtained by the original purchaser by REGISTERING this product
with Omnitron within 90 days from the date of shipment. TO
REGISTER, COMPLETE AND MAIL OR FAX THE ENCLOSED
REGISTRATION FORM. Or you may register your product on
the Internet at www.omnitron-systems.com. During the warranty
period, Omnitron will, at its option, repair or replace a product
which is proven to be defective.
For warranty service, the product must be sent to an Omnitron
designated facility, at Buyer’s expense. Omnitron will pay the
shipping charge to return the product to Buyer’s designated US
address using Omnitron’s standard shipping method.
Limitation of Warranty
The foregoing warranty shall not apply to defects resulting from
improper or inadequate use and/or maintenance of the equipment
by Buyer, Buyer-supplied equipment, Buyer-supplied interfacing,
unauthorized modications or tampering with equipment (including
removal of equipment cover by personnel not specifically
authorized and certied by Omnitron), or misuse, or operating
outside the environmental specication of the product (including
but not limited to voltage, ambient temperature, radiation, unusual
dust, etc.), or improper site preparation or maintenance.
No other warranty is expressed or implied. Omnitron specically
disclaims the implied warranties of merchantability and tness for
any particular purpose.
Page 15
The remedies provided herein are the Buyer’s sole and exclusive
remedies. Omnitron shall not be liable for any direct, indirect,
special, incidental, or consequential damages, whether based
on contract, tort, or any legal theory.
TECHNICAL SUPPORT:
For help with this product, contact our Technical Support:
Phone: (949) 250-6510
Fax: (949) 250-6514
Address: Omnitron Systems Technology, Inc.
38 Tesla
Irvine, CA 92618 USA
E-mail: support@omnitron-systems.com
URL: www.omnitron-systems.com
Form: 040-08520-001F 10/13
Page 16
Exclusive Remedies