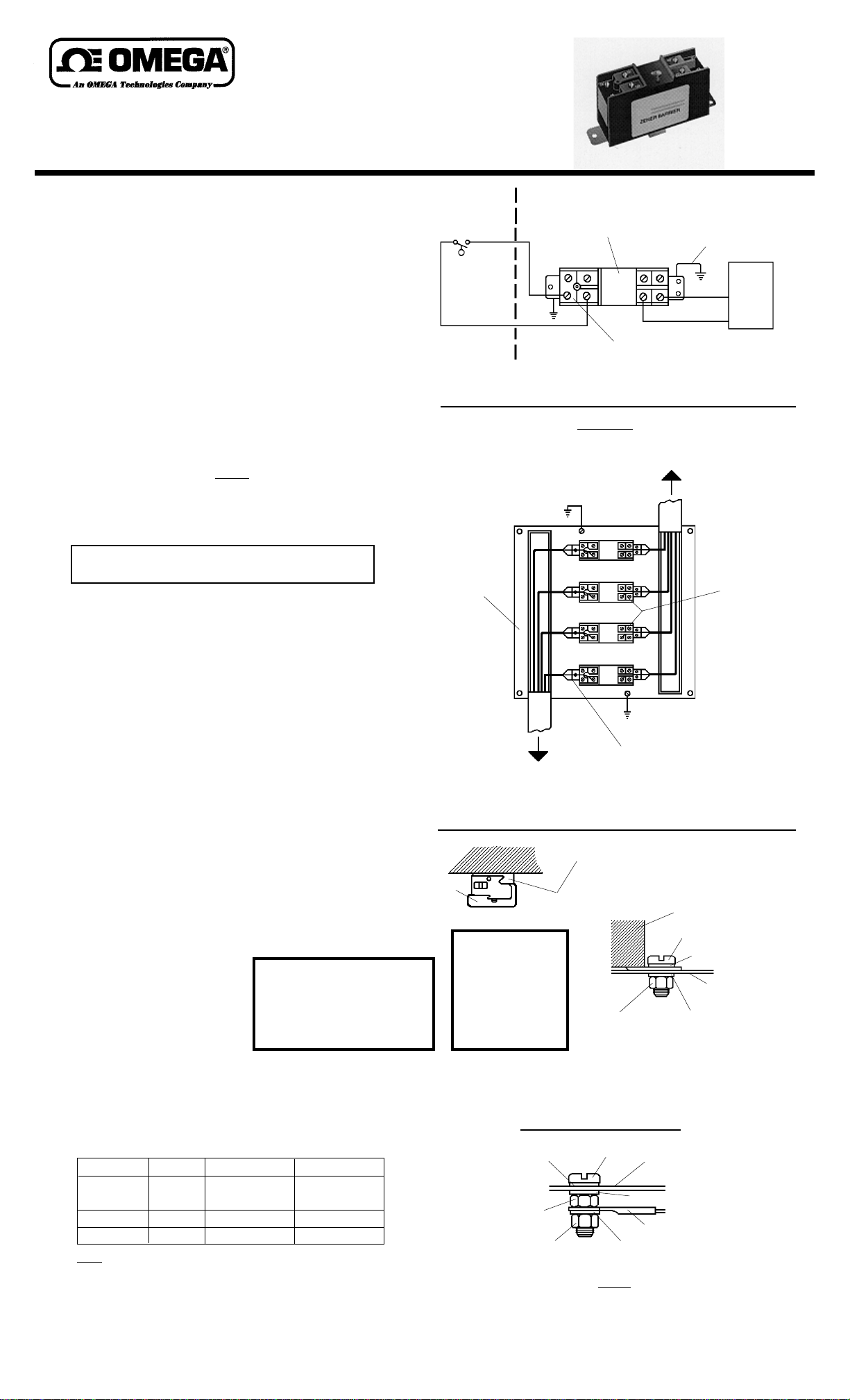
SBG54803 Solid-State Relays
for Intrinsic Safety Use
Instruction Sheet M1775/0594
DESCRIPTION
The OMEGA® SBG54803 Dual Channel Zener Barrier is a
solid-state, energy-limiting device for transmitting direct current signals of less than 20V and less than 100mA in an intrinsically safe manner. The unit is designed to be used in
conjunction with indicating equipment in hazardous areas
defined as Class I, Division 1, and inclusive of Groups A
through D. This zener barrier is used where circuit common
is earth-ground-referenced.
THE AMBIENT TEMPERATURE OPERATING RANGE
OF THIS DEVICE IS 0° TO 60°C. (+32° TO +140°F).
UNPACKING
Remove the Packing List and verify that you have received all
equipment. If you have any questions about the shipment,
please call the OMEGA Customer Service Department at
1-800-622-2378 or (203) 359-1660. When you receive the
shipment, inspect the container and equipment for any signs of
damage. Note any evidence of rough handling in transit.
Immediately report any damage to the shipping agent.
NOTE
The carrier will not honor any claims unless all shipping material
is saved for their examination. After examining and removing
contents, save packaging material and carton in the event
reshipment is necessary.
Important: Read carefully and completely before
installing or connecting the solid-state relays.
CONSIDERATIONS FOR INSTALLATION AND USE
Only one sensor per channel may be connected to a barrier
(See Figure 1).
Hazardous
Area
Sensor
Non-Hazardous Area
Zener
Barrier
6
8
5
7
Stud Cover Must Be In
Place When Barrier Is In Use
Earth Ground Bracket
2
4
1
3
Fig. 1. Installation Diagram
(One Sensor Shown)
All barriers used for multiple barrier
mounting must be of the same polarity.
Mounting
Panel
Important
At Two Points
(See Fig. 3)
Term.
Equip.
Non-Intrinsically
Safe Wiring
To Receiver
Zener
Barriers
The barrier and receiving station must be located in a nonhazardous location.
The mounting bracket on the barrier must be connected to an
earth ground from both mounting points and two lines for
redundancy. The grounding should be adequate for conduction of line generated fault currents. The resistance of either
line to earth ground should be maintained at less than one
ohm.
To serve multiple tank installations, additional barriers may
beplaced in an enclosure using a common earth ground
(See Figure 2). In this enclosure, the intrinsically safe wiring
should be segregated from non-intrinsically safe wiring by
independent raceways, wiring trays or other adequate means
to insure the integrity of the installation. Additionally, when
internal terminations are used, intrinsically safe wiring and
non-intrinsically safe wiring should not be adjacent or
arranged in such a way as to create the potential to miswire
or bypass the barrier during servicing or testing. (See
typical installation depicted in Figure 2.)
Common, commercially available
signal wire may be used for field
wiring and distances of up to
1000 ft. are acceptable using
twisted wire. Characteristics of
the signal line should not be
Product must be maintained and installed in strict accordance with the
National Electrical Code. Failure to
observe this warning could result in
serious injuries or damages.
WARNING
modified by addition of capacitive
or inductive components.
Intrinsically
Safe Wiring
To Transmitter
Rail**
**6" Mounting Rail:
SBG-RAIL-6
12" Mounting Rail:
SBG-RAIL-12
18" Mounting Rail:
SBG-RAIL-18
Earth Ground
(See Fig. 3)
Resistance to ground must be
from bracket to earthing member
to insure integrity of system.
(Must be below one ohm.)
Fig. 2. Multiple Barrier Mounting
SBG61783 MountingClip
(Optional)
Zener Barrier
#10 Screw
#10 Lockwasher*
#10
Nut
#10 Lockwasher*
Mounting
Plate
Each sensor must have its own ground return wire to pin 5.
The governing parameters for various groups are as follows:
GroupGroup
Group
GroupGroup
Hydrogen
& Acetylene
Ethylene
Methane
Note: *Values are for any one loop in the hazardous area.
(i.e., Terminals 7 to 5 or 8 to 5)
A & B
C
D
CapicitanceCapicitance
Capicitance
CapicitanceCapicitance
0.4 µF
1.2 µF
3.2 µF
**
*
**
InductanceInductance
Inductance
InductanceInductance
0.9 mH
5.0mH
10.0mH
**
*
**
Field Testing of Barrier
A. Never conduct tests while circuit is active. The use of
instruments between input and output terminals will
bypass the barrier.
Detail of Earth Grounding
*Lockwasher
Nut
Nut
1. Grounding Hardware to be #8 or larger and stainless
steel
2. *(Lockwashers to be internal or external tooth type)
Screw
Notes
Mounting
Plate
*Lockwasher
Terminal Lug
*Lockwasher
Fig. 3. Details of Mounting and Grounding
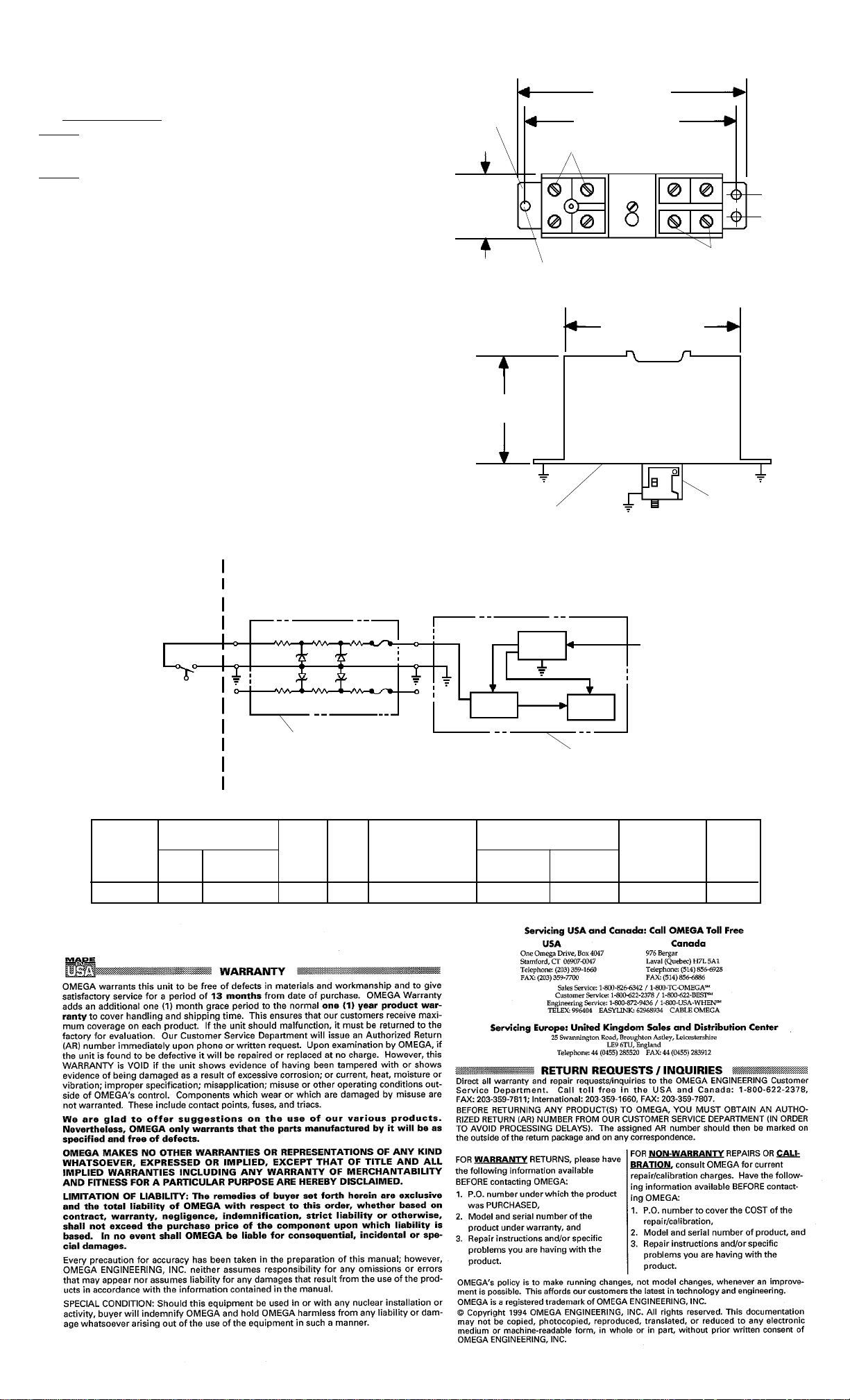
B. All testing is to be done with circuit inactive using the
following instruments:
1. Ohmmeter with resolution down to less than 1 ohm.
2. D. C. power supply with an output of 0 to +25 VDC.
3. D. C. voltmeter.
C.
Test performance (See Fig. 5)
Step 1:
Disconnect all leads to unit under test except to the
earth
grounding mounting tabs.
Step 2:
a. Measure the resistance between terminals 1 & 7 and then
2 & 8. This resistance should be 250 ohms ±5% (± instrument tolerance).
b. Measure the resistance between terminals 5 & 3 and then
terminal 5 and the mounting tab. Both readings should be
below one ohm.
c. Apply 24 volts to terminals 7(+) and 5 (common). Then
read the voltage between the terminals 1 (+) and 3 (common)
*.
This voltage must be between 18.5 and 21.5 volts. In the
same fashion, conduct this same test with the voltage connected across 8 (+) and 5 (common) and measure the output
across 2 (+) and 3 (common).
d. Connect an ohmmeter between the mounting tab (not the
mounting screw) and the earth ground reference. The reading must be less than one ohm. The barrier must pass all
parts of this test or it is unacceptable.
* The fuses located in the circuits 7-1 and 8-2 are
rated at 100mA. Therefore, care should be exercised
in testing this device so that no accidental current
greater than 100mA enters or leaves terminal 1 or 2.
Note: Every effort should be made to keep these barriers clean and
free of contaminating atmospheres. A periodic check should be made
to verify that they are in good condition, physically and electrically.
Mounting
Tab
1-5/8"
(41.3 mm)
2-3/4"
(69 mm)
6" (152.4 mm)
5-1/2" (139.7 mm)
Output Terminals No. 6-32 Thd.
8
8
5
7
7/22" (5.6 mm) Dia.
3 Mtg. Holes
4-3/4" (120.7 mm)
Housing
Fig. 4. Dimensions
4
2
1
7
Input Terminals
No. 6-32 Thd.
Rail-Mounting
(Optional)
Hazardous
Area
Sensor
DC Input to
MM
odelodel
M
odel
odelodel
MM
NumberNumber
Number
NumberNumber
SBG54803SBG54803
SBG54803
SBG54803SBG54803
Housing material is blue Lexan.
Barrier, Max.
Voltage
20
7
5, 6
8
Fuse Rating
Current, mA
100
Non-Hazardous
Area
120Ω
120
Ω
20 V
20 V
120Ω 120Ω
Zener Barrier
Fig. 5. Intrinsically Safe Loop Schematic
Series
Signal
Polarity
Positive
Resist.
10Ω
20 V
20 V
10Ω
1
3, 4
2
Table 1. Specifications
Applications
Groups
Class i & II, Div 1, 2
Ω
270
Groups A, B, C, D
Power
Supply
Logic
Reactive Limits
Capacitance
µµ
µF
µµ
0.4
Indication
Receiver
Inductance
mHmH
mH
mHmH
0.9
Input
Power
Ambient
Oper.
Temp.
0° to +60°C
Weight
495g
P/N 158351P/N 158351
P/N 158351
P/N 158351P/N 158351