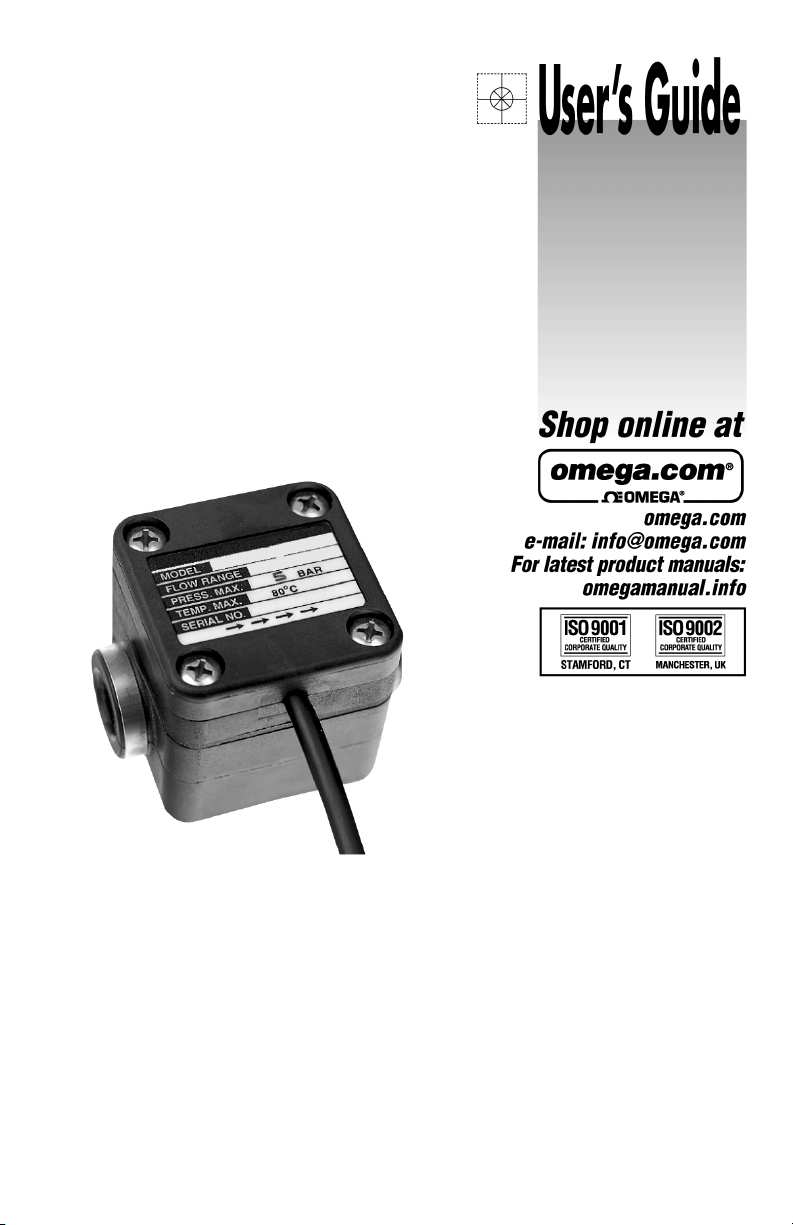
FPD1001B thru FPD1003B,
FPD1102B and FPD1103B,
FPD1201B thru FPD1203B
SERIES LOW FLOW
Positive Displacement Flowmeters
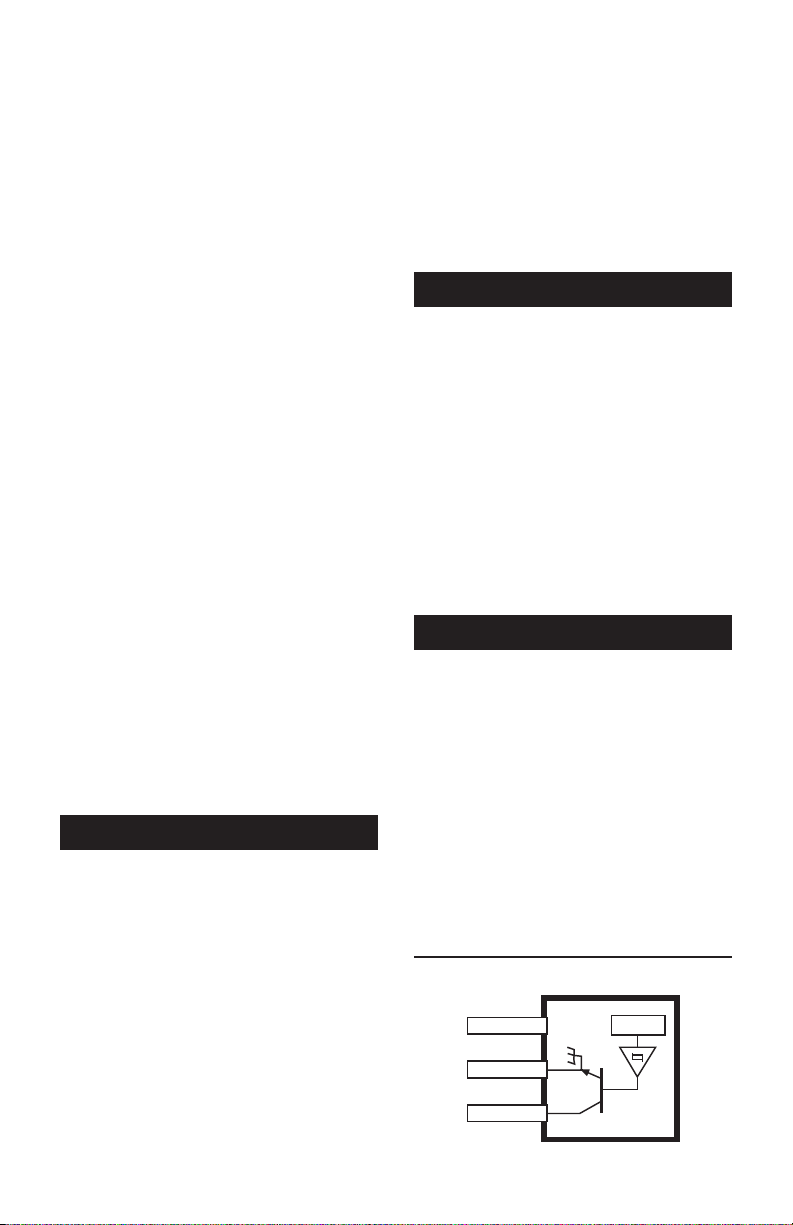
To the owner:
Red - Supply
Black - Ground
White - Output
X
V
cc
1 2 3
Please take a few minutes to read through
the manual before installing and operating
your meter. Always retain this manual for
future reference. If you have any problems
with the meter, refer to the Maintenance and
Troubleshooting sections of the manual.
This manual contains connection and operating instructions for the OMEGA FPD
Series meters. This includes the following
models:
FPD1001B FPD1202B-IP
FPD1201B FPD1003B
FPD1201B-IP FPD1203B
FPD1002B FPD1103B
FPD1202B FPD1203B-IP
FPD1102B
Part breakdowns for each model are located at the back of this manual. For models
with displays and /or 4-20 mA output, an
additional instruction manual is provided.
The flowmeter has incorporated the oval rotor principal into its design. This has proven
to be a reliable and highly accurate method
of measuring flow. Exceptional repeatability
and high accuracy over a wide range of
fluid viscosities and flowrates are features
of the oval rotor design. With low pressure
drop and high pressure rating, oval rotor
flowmeters are suitable for both gravity and
pump (in-line) applications.
NOTE: To prevent damage to the meter,
slowly fill the system with fluid (this will
prevent damage caused by air purge).
Failure to do this could damage the
meter.
To reduce pressure build up, turn off the
pump at the end of each day.
INSTALLATION
1. Use thread sealant on all pipe threads.
2. Ensure the meter is installed so that
rotor shafts are always in a horizontal
plane. Flow is bi-directional.
3. OMEGA recommends use of flexible
connections.
4. Extreme care must be taken when
installing the meter. Pipe strain or
overtightening the meter connections
can cause meter damage.
PULSER DETAILS
Your meter is equipped with both a Hall
Effect sensor and a Reed Switch sensor.
The equipment you are sending the pulse
signal to will determine which sensor you
use. The wires for the unused sensor will
not be used.
OPERATION
Please read this information
!
▲
carefully before use!
Before use, confirm the fluid to be used is
compatible with the meter. Refer to Industry
fluid compatibility charts or consult your
local representative for advice.
To prevent damage from dirt or foreign
matter it is recommended that a Y or basket type 200 mesh strainer be installed as
close as possible to the inlet side of the
meter. Contact your local representative
for advice.
Hall Effect Sensor Specifications:
•
4.5V to 24V (4.6 ~ 9 mA) operation
needs only an unregulated supply.
•
Open collector 25 mA output NPN
compatible with digital logic.
Figure 1
Hall Effect Sensor Wiring Details
1
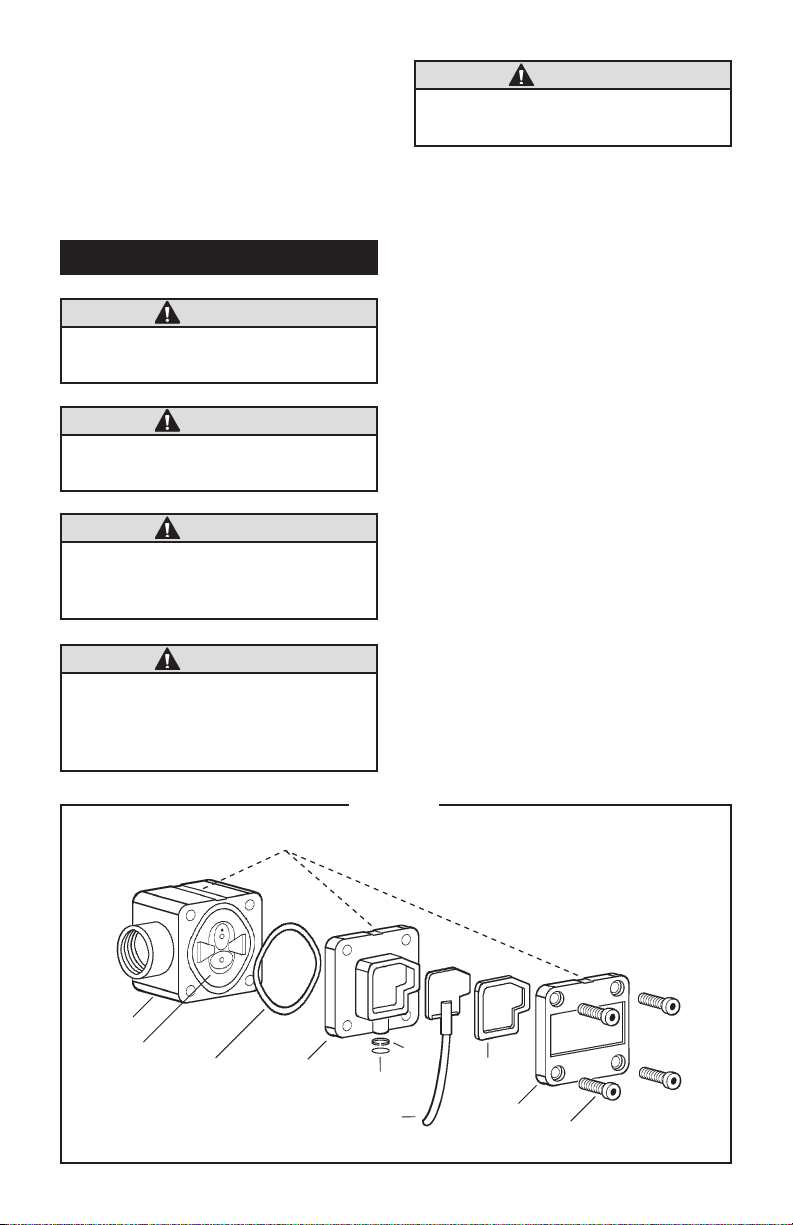
Reed Relay Specifications:
Alignment Marks
Body
Rotors
O-Ring
Inner Plate &
PCB Assembly
O-Ring
Meter
Cap
Screws
Inner Plate &
PCB Assembly
Wire
Clip
Seal
•
Wiring: Yellow wire / Green wire.
•
Two wire SPST N/O.
•
Switching voltage: 30 VDC; Maximum
current: 0.5 AMPS.
MAINTENANCE
CAUTION
Ensure the fluid is isolated from the
meter to be repaired.
CAUTION
Ensure the fluid line is depressurized
before commencing repairs.
CAUTION
Ensure electrical wiring is isolated
and disconnected before commencing repairs.
CAUTION
To prevent damage to the meter during re-commissioning, slowly fill the
piping system with fluid before starting the pumping system.
CAUTION
Refer to the Sensor Wiring section for
details.
Pulse Meter Disassembly
1. Loosen and remove four Phillips head
or cap head screws (see Figure 2).
2. Remove the meter cap and O-ring.
3. Remove the inner plate and PCB assembly. Refer to the PCB Removal
section for additional details.
4. Remove the O-ring.
5. Remove the rotors. Note the position
of the rotor with the magnet or grub
screws.
6. Clean and inspect all components,
replace as necessary.
Pulse Meter Reassembly
1. Replace the rotors. Refer to Figure 3 or
Figure 4 for correct orientation. Rotate
the rotors by hand to ensure correct
engagement.
Figure 2
2
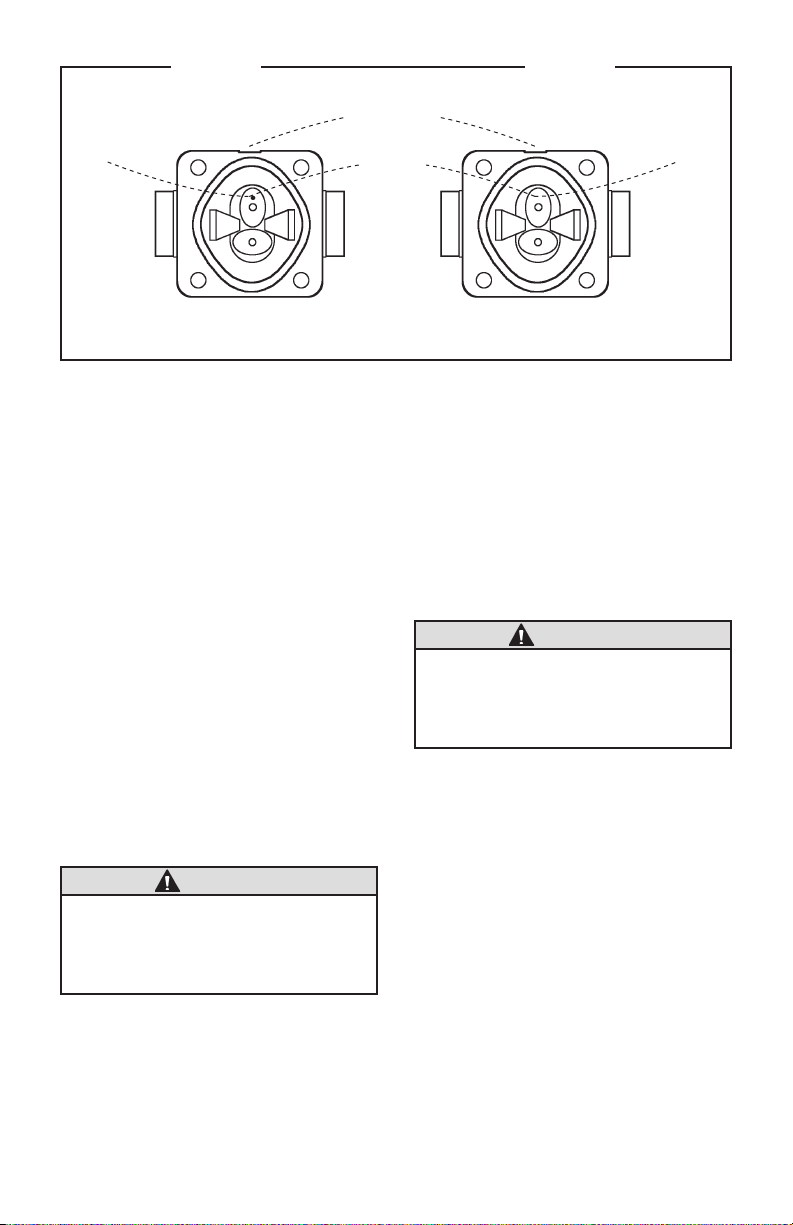
Figure 3
Rotors with
Magnets
Alignment Marks
Magnets
NOT Visible
Magnets
Visible
GM001 Meters
Figure 4
GM002 & GM003 Meters
Models: FPD1001B & FPD1201B Models: FPD1002B, FPD1003B, FPD1102B,
2. Fit the O-ring into the O-ring groove in
the meter body.
3. Combine the inner plate assembly
(Items 4-7). Form the O-ring into the inner plate and replace the meter cap.
NOTE: Ensure all the alignment marks are
lined up with the mark on the body
(see Figure 2).
4. Replace and tighten the four bolts
to the required torque. Refer to Bolt
Torque in the Specifications section
for details.
5. Check meter function using low air
pressure.
6. Restore the fluid and reconnect the
wiring as detailed in the Installation and
Pulser Details sections.
PCB Removal
CAUTION
The PCB contains components that
are sensitive to static shock. Ensure
all items and maintenance staff are
grounded before working on the PCB.
1. Using a thin blade or similar tool, remove
the wire clip and seal (see Figure 2).
2. While lifting the PCB with the blade
inserted near the alignment marks,
carefully push the cable into the inner
plate. Continue to lift the back of the
PCB until all components on the PCB
clear the inner plate.
FPD1103B, FPD1202B & FPD1203B
3. Grasp the cable near the PCB and pull
the cable through the opening in the
inner plate until the cable ferrules are
near the inner plate opening.
4. Push the cable ferrules into the PCB
opening, one at a time, and remove
the cable.
PCB Replacement
CAUTION
The PCB contains components that
are sensitive to static shock. Ensure
all items and maintenance staff are
grounded before working on the PCB.
1. Feed the cable ferrules, one at a time,
through the cable opening in the inner
plate.
2. Gently pull the cable through the inner
plate opening until the PCB almost
touches the inner plate.
3. While pulling the cable, tilt the PCB into
the recess in the inner plate. Ensure
components underneath the PCB do
not come into contact with the inner
plate.
4. Pull the cable until the cable ties contact the inner plate. Gently push the
PCB down into the housing.
5. Press the seal into the inner plate cable
entry, followed by the wire clip. Ensure
they both are seated correctly.
3