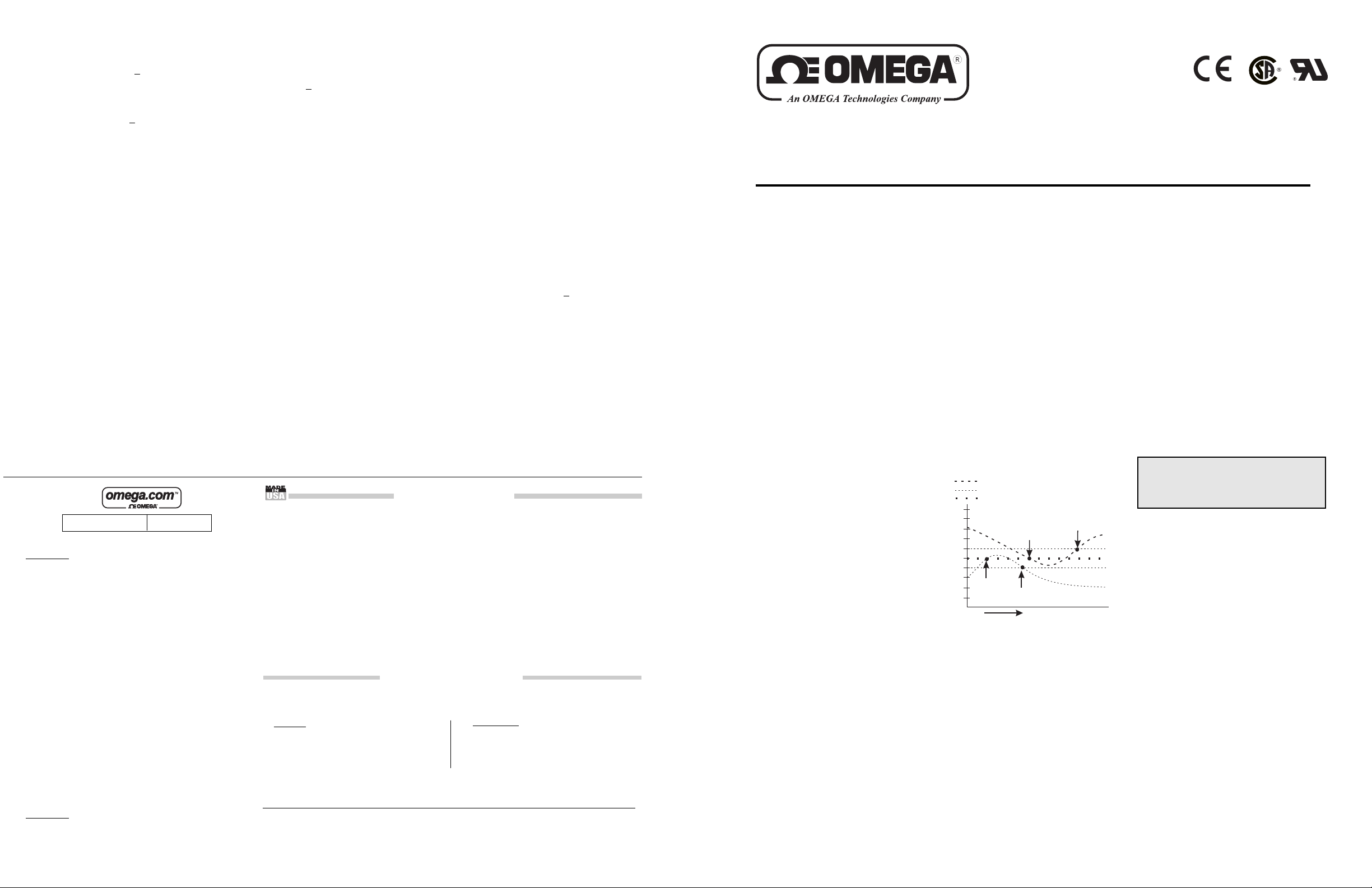
50
100
Process (% of Span)
Time
Relay Trips
(LED Red)
Relay Trips
(LED Red)
Relay returns to its
untripped condition
(LED Off)
Relay returns to its
untripped condition
(LED off)
} 10% Deadband
} 10% Deadband
Setpoint
Illustrating HI Setpoint
Illustrating LO Setpoint
Inputs
Voltage Input
Range: 10mV to +200V
Impedance: >100KΩ
Overvoltage: 200V rms, max.
Current Input
Range: 1mA to +100mA
Impedance: 20Ω, typical
Overcurrent: 170mA rms, max.
Overvoltage: 60VDC
(protected by self resetting fuse)
Common Mode (Input to Ground):
1800VDC, max.
LED Indicators
Input Range (Green)
>110% input: 8Hz flash
<0% input: 4Hz flash
Setpoint (Red)
Tripped: Solid red
Safe: Off
Limit Differentials (Deadbands)
>50mV/5mA: 0.25% to 5% of span
<50mV/5mA: 1% to 5% of span
Response Time
Dynamic Deadband: Relay status
will change when proper
setpoint/process condition exists
for 100msec.
Normal Mode (analog filtering):
<250mSec, (10-90%)
Setpoints
Effectivity: Setpoints are adjustable
over 100% of the selected input
span.
Repeatability (constant temp.):
OMEGAnetSM On-Line Service
http://www.omega.com
USA:
ISO 9001 Certified
Canada:
USA and Canada:
Mexico and
Latin America:
Benelux:
Czech Republic:
France:
Germany/Austria:
United Kingdom:
ISO 9002 Certified
One Omega Drive, Box 4047
Stamford, CT 06907-0047
Telephone: (203) 359-1660
e-mail:info@omega.com
976 Bergar
Laval (Quebec) H7L 5A1
Telephone: (514) 856-6928
e-mail: canada@omega.com
Sales Service: 1-800-826-6342 / 1-800-TC-OMEGA
Customer Service: 1-800-622-2378 / 1-800-622-BEST
Engineering Service: 1-800-872-9436 / 1-800-USA-WHEN
TELEX: 996404 EASYLINK: 62968934 CABLE: OMEGA
Tel: (95) 800-TC-OMEGA
En Espanol: (203) 359-1660 ext. 2203
Postbus 8034, 1180 LA Amstelveen, The Netherlands
Tel: (31) 20 6418405
Toll Free in Benelux: 06 0993344
e-mail: nl@omega.com
Ostravska 767, 733 01 Karvina
Tel: 42 (69) 6311899
e-mail: czech@omega.com
9, rue Denis Papin, 78190 Trappes
Tel:33 0130-621-400
Toll Free in France: 05-4-06342
e-mail: france@omega.com
Daimlerstrasse 26, D-75392 Deckenpfronn, Germany
Tel:49 (07056) 3017
Toll Free in Germany: 0130 11 21 66
e-mail: germany@omega.com
25 Swannington Road,
Broughton Astely, Leicestershire,
LE9 6TU, England
Tel: 44 (1455) 285520
Fax: 44 (1455) 283912
Servicing North America:
For immediate technical sevice or application assistance:
Servicing Europe:
Toll Free in England: 0800-488-488
e-mail: uk@omega.com
Internet e-mail
info@omega.com
SM
Fax: (203) 359-7700
Fax: (514) 856-6886
SM
SM
SM
Fax: (95) 203-359-7807
e-mail: espanol@omega.com
Fax: (31) 20 6434643
Fax: 42 (69) 6311114
Fax: 33 0130-699-120
Fax: 49 (07056) 8540
P.O. Box 7, Omega Drive
Irlam, Manchester,
M44 5EX, England
Tel: 44 (161) 777-6611
Fax: 44 (161) 777-6622
>50mV/5mA: 0.1% of full scale
<50mV/5mA: 0.2% of full scale
Stability
Temperature:
+0.05% of full
scale/°C, max.
Excitation Voltage
24VDC, 20mA, maximum
Common Mode Rejection
DC to 60Hz: 120dB
Isolation
1800VDC between contacts, input
and power
EMC Compliance (CE Mark)
Emmissions: EN50081-1
Immunity: EN50082-2
Safety: EN50178
Humidity (Non-Condensing)
Operating: 15 to 95% (@45°C)
Soak: 90% for 24hours (@65°C)
Temperature Range
1
Operating: 0 to 55°C (32 to 131°F)
Storage: -25 to 70°C (-13 to 158°F)
Power
Consumption: 1.5W typical,
2.5W max.
Supply Range: 9 to 30VDC,
inverter isolated
In-rush Current: 300mA, max.
Relay Contacts
2 SPDT (2 form C) Relays
1 Relay per setpoint
Current Rating (resistive)
120VAC: 5A
240VAC: 2A
28VDC: 5A
Material: Silver-Cadmium Oxide
Electrical Life:10
5
operations
at rated load
Note: External relay contact
protection is required for use
with inductive loads (see
Figures 2 & 3).
Mechanical Life: 107 operations
Wire Terminations
Screw terminations for 12-22 AWG
Agency Approvals
CSA certified per standard C22.2, No.
0-M91 and 142-M198 (File
No.LR42272) UL recognized per standard per standard UL508 (File
No.E99775). CE conformance per
EMC directive 89/336/EEC and Low
Voltage 73/23/EEC (Input<75VDC,
only).
Mounting
32mm and 35mm DIN Rail
PIN CONNECTIONS
11 N.O. Relay B
12 Com. Relay B
13 N.C. Relay B
21 DC Power (+)
22 DC Power (-)
23 No Connection
41 Analog Input (+)
42 Analog Input (-)
43 (+) 24VDC Excitation
OMEGA ENGINEERING, INC. warrants this unit to be free of manufacturing defects for the life of the product.
If the unit should malfunction, it must be returned to the factory for evaluation. OMEGA's Customer Service Department will issue an Authorized Return
(AR) number immediately upon phone or written request. Upon examination by OMEGA, if the unit is found to be defective it will be repaired or replaced at
no charge. OMEGA's WARRANTY does not apply to defects resulting from any action of the purchaser, including but not limited to mishandling, improper
interfacing, operation outside of design limits, improper repair, or unauthorized modification. This WARRANTY is VOID if the unit shows evidence of having
been tampered with or shows evidence of being damaged as a result of excessive corrosion; or current, heat, moisture or vibration; improper specification; misapplication; misuse or other operating conditions outside of OMEGA's control. Components which wear are not warranted, including but not
limited to contact points, fuses, and triacs.
OMEGA is pleased to offer suggestions on the use of its various products. However, OMEGA neither assumes responsibility
for any omissions or errors nor assumes liability for any damages that result from the use of its products in accordance with
information provided by OMEGA, either verbal or written. OMEGA warrants only that the parts manufactured by it will be as
specified and free of defects. OMEGA MAKES NO OTHER WARRANTIES OR REPRESENTATIONS OF ANY KIND WHATSOEVER,
EXPRESSED OR IMPLIED, EXCEPT THAT OF TITLE, AND ALL IMPLIED WARRANTIES INCLUDING ANY WARRANTY OF MERCHANTABILITY AND FITNESS FOR A PARTICULAR PURPOSE ARE HEREBY DISCLAIMED. LIMITATION OF LIABILITY: The
remedies of purchaser set forth herein are exclusive and the total liability of OMEGA with respect to this order, whether
based on contract, warranty, negligence, indemnification, strict liability or otherwise, shall not exceed the purchase price of
the component upon which liability is based. In no event shall OMEGA be liable for consequential, incidental or special
damages.
CONDITIONS: Equipment sold by OMEGA is not intended to be used, nor shall it be used: (1) as a "Basic Component" under 10 CFR 21 (NRC), used in
or with any nuclear installation or activity; or (2) in medical applications or used on humans. Should any Product(s) be used in or with any nuclear
installation or activity, medical application, used on humans, or misused in any way, OMEGA assumes no responsibility as set forth in our basic WARRANTY/DISCLAIMER language, and additionally, purchaser will indemnify OMEGA and hold OMEGA harmless from any liability or damage whatsoever
arising out of the use of the Product(s) in such a manner.
Direct all warranty and repair requests/inquiries to the OMEGA Customer Service Department. BEFORE RETURNING ANY PRODUCT(S) TO OMEGA, PURCHASER
MUST OBTAIN AN AUTHORIZED RETURN (AR) NUMBER FROM OMEGA'S CUSTOMER SERVICE DEPARTMENT (IN ORDER TO AVOID PROCESSING
DELAYS). The assigned AR number should then be marked on the outside of the return package and on any correspondence.
The purchaser is responsible for shipping charges, freight, insurance and proper packaging to prevent breakage in transit.
FOR WARRANTY RETURNS, please have the following information
available BEFORE contacting OMEGA:
1. P.O. number under which the product was PURCHASED,
2. Model and serial number of the product under warranty, and
3. Repair instructions and/or specific problems relative to the product
OMEGA's policy is to make running changes, not model changes, whenever an improvement is possible. This affords our customers the latest in technology and
engineering.
OMEGA is a registered trademark of OMEGA ENGINEERING, INC.
ã Copyright 1996 OMEGA ENGINEERING, INC. All rights reserved. This documentation may not be copied, photocopied, reproduced, translated, or reduced to any
electronic medium or machine-readable form, in whole or in part, without prior written consent of OMEGA ENGINEERING, INC.
It is the policy of OMEGA to comply with all worldwide safety and EMC/EMI regulations that apply. OMEGA is constantly pursuing certification of its products to the European
New Approach Directives. OMEGA will add the CE mark to every appropriate device upon certification.
The information contained in this document is believed to be correct but OMEGA Engineering, Inc. accepts no liability for any errors it contains, and reserves the right to alter
specifications without notice.
WARNING: These product are not designed for use in, and should not be used for, patient connected applications.
WARRANTY/DISCLAIMER
RETURN REQUEST/ INQUIRIES
FOR NON-WARRANTY REPAIRS, consult OMEGA for current repair
charges. Have the following information available BEFORE contacting OMEGA:
1. P.O. number to cover the COST of the repair,
2. Model and serial number of product, and
3. Repair instructions and/or specific problems relative to the product.
721−0607−00Β 11/97
DRG-AR-DC
DC Input, Field Configurable Limit Alarm
Instruction Sheet M2399/0796
DESCRIPTION
The DRG-AR-DC is a DIN rail mount,
DC voltage or current input limit alarm
with dual setpoints and two contact
closure outputs. The field configurable
input and alarm functions offer flexible
setpoint capability. Input voltage spans
from 10mV to 200V and input current
spans from 1mA to 100mA can be field
configured. Bipolar inputs are also
accepted.
The DRG-AR-DC is configurable as a
single or dual setpoint alarm, with HI or
LO trips and failsafe or non-failsafe
operation. Also included are adjustable deadbands (0.25 to 5% of full
scale input) for each setpoint, a 24VDC
voltage source (isolated from line
power) for transducer excitation, and
a flexible DC power supply which accepts any voltage between 9 and
30VDC.
DIAGNOSTIC LEDS
The DRG-AR-DC is equipped with
three front panel LEDs. The green
LED is a dual function LED labeled
INPUT. This LED indicates line power
and input signal status. Active DC
power is indicated by an illuminated
LED. If this LED is off, check DC
power and wiring connection. If the
input signal is more than 110% of the
full scale range, the LED will flash at 8
Hz. Below 0%, the flash rate is 4 Hz.
Two red LEDs indicate the relay state
for each setpoint. An illuminated red
LED indicates the tripped condition.
OUTPUT
The DRG-AR-DC is equipped with two
SPDT (form C) relays, rated at 120VAC
or 28VDC at 5 amperes. Each of these
relays is independently controlled by
the field configurable setpoint and
deadband.
OPERATION
The field configurable DRG-AR-DC
limit alarm setpoints can be configured
for HI or LO, failsafe or non-failsafe
operation. Each of the setpoints has
a respective HI or LO deadband. In a
tripped condition, the setpoint is exceeded and the appropriate red LED
will illuminate. The trip will reset only
when the process falls below the HI
deadband or rises above the low
deadband (see Figure 1). For proper
deadband operation, the HI setpoint
must always be set above the LO
setpoint. In failsafe operation, the
relay is energized when the process is
below the HI setpoint or above the LO
setpoint (opposite for non-failsafe). In
the failsafe mode, a power failure
results in an alarm state output.
Figure 1: Limit alarm operation
and effect of deadband(s).
DYNAMIC DEADBAND
LSI circuitry in the DRG-AR-DC prevents false trips by repeatedly sampling the input. The input must remain
beyond the setpoint for 100 milliseconds, uninterrupted, to qualify as a
valid trip condition. Likewise, the input
must fall outside the deadband and
remain there for 100 milliseconds to
return the alarm to an untripped condition. This effectively results in a
“dynamic deadband” —based on
time— in addition to the normal
deadband.
CONFIGURATION
Unless otherwise specified, the
factory presets the Model
DRG-AR-DC as follows:
Input: Current
Range: 0-20mA
Output: Dual, SPDT
Trip: A:HI, B:LO
Failsafe: N o
Deadband: A, B: 0.25%
The DC power input accepts any DC
source between 9 and 30V, typically a
12V or 24VDC source is used.
For other I/O ranges, refer to Table 1
and Figure 4. Reconfigure switche
SW1 for the desired input type, range
and function.
WARNING:
change any switch settings with power
applied. Severe damage will result!
1. With DC power off, set positions 9
and 10 of switch “SW1” for current or
voltage.
2. Set position 1 through position 4 of
input range switch “SW1” for the desired input range (see Table 1).
3. Set position 5 of input range switch
“SW1” to ON for unipolar (e.g. zero
based, 0-20mA) range or OFF for
bipolar (e.g. -100% offset,
-20 to 20mA) range (see Figure 4).
4. Set position 6 and 7 of input
range switch “SW1” to ON for a HI trip
setpoint or OFF for a LO trip setpoint
(see Figure 4).
5. Set position 8 of input range
switch “SW1” to ON for non-failsafe
operation or OFF for failsafe
operation (e.g. alarm trips upon
power failure).
Do not attempt to
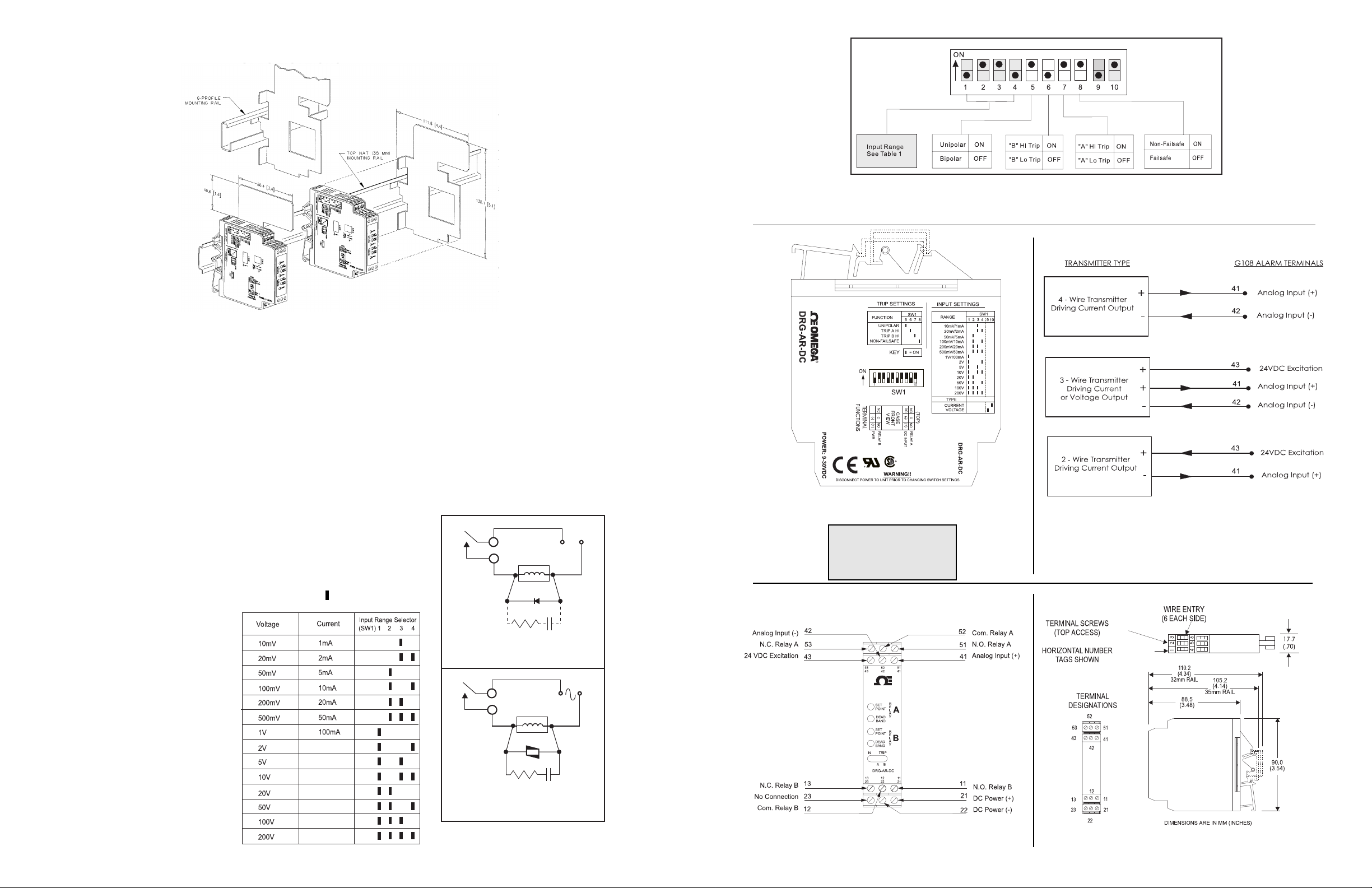
SPECIFICATIONS
Note1: All DRG Series modues are designed and tested to operate in ambient temperatures from 0 to
55°C, when mounted on a horizontal DIN rail. When five or more modules are mounted on a vertical
rail, circulating air or model DRG-HS01 Heat Sink is recommended.
Figure 4: DRG-AR-DC Input Range/Function
Selection (SW1) Factory Default Settings
CALIBRATION
1. After configuring the DIP switches,
connect the input to a calibrated DC
source and apply power. Refer to the
terminal wiring (Figure 7).
Note: To maximize thermal stability, final
calibration should be performed in the operating installation, allowing approximately
1 to 2 hours for warm up and thermal
equilibrium of the system.
2. Setpoint: set deadband at its minimum (fully counter clockwise) before
adjusting the setpoint. With the desired trip voltage or current input applied, adjust setpoint until the relay
trips. For HI trip calibration, start with
the setpoint above the desired trip (full
clockwise). For LO trip calibration,
start below the desired trip (full counter
clockwise).
3. Deadband: Set deadband to its
minimum (fully counter clockwise).
Set the setpoint to desired trip. Adjust
voltage/current input until relay trips.
Readjust deadband to 5% (fully clockwise). Set voltage/current input signal
to desired deadband position. Slowly
adjust deadband until relay untrips.
RELAY PROTECTION AND
EMI SUPPRESSION
When switching inductive loads,
maximum relay life and transient EMI
suppression is achieved using external protection (see Figures 2
and 3). Place all protection devices
directly across the load and minimize
all lead lengths. For AC inductive
loads, place a properly-rated MOV
across the load in parallel with a
series RC snubber. Use a 0.01 to
Table 1: DRG-AR-DC Input Range
switch settings (SW1 through 4)
KEY = ON
0.1µF pulse film capacitor (foil polypropylene recommended) of sufficient
voltage, and a 47Ω, 1/2W carbon
resistor. For DC inductive loads, place
a diode across the load (PRV > DC
supply, 1N4006 recommended) with
(+) to cathode and (-) to anode (the RC
snubber is an optional enhancement).
Power
+
-
Relay
Contacts
(optional)
Figure 2: DC Inductive Loads
Relay
Contacts
Load
47 ohm
1/2W
Load
47 ohm
1/2W
Diode
MOV
0.1uF
Film
0.1uF
Film
Power
Figure 5: DRG-AR-DC Factory Calibration;
0-20mA, A-HI/B-LO, Non-Failsafe
Warning: Do not attempt to
change any switch settings
with power applied. Severe
damage may occur!
Figure 6: Typical connections of voltage or
current inputs for DRG-AR-DC
DIMENSIONS
Figure 3: AC Inductive Loads
Figure 7: Terminal Wiring Diagram for DRG-AR-DC
Figure 8: Mechanical Dimensions for DRG-AR-DC