
LM1819 Air-Core Meter Driver
LM1819 Air-Core Meter Driver
February 1995
General Description
The LM1819 is a function generator/driver for air-core
(moving-magnet) meter movements. A Norton amplifier and
an NPN transistor are included on chip for signal conditioning as required. Driver outputs are self-centering and devel-
g
op
4.5V swing at 20 mA. Better than 2% linearity is guar-
anteed over a full 305-degree operating range.
Typical Application
Features
Y
Self-centering 20 mA outputs
Y
12V operation
Y
Norton amplifier
Y
Function generator
Applications
Y
Air-core meter driver
Y
Tachometers
Y
Ruggedized instruments
TL/H/5263– 1
FIGURE 1. Automotive Tachometer Application. Circuit shown operates
with 4 cylinder engine and deflects meter pointer (270
) at 6000 RPM.
§
Order Number LM1819M or LM1819N
See NS Package Number M14A or N14A
*TRW Type X463UW Polycarbonate Capacitor
**RN60D Low TC Resistor (
²
Components Required for Automotive Load Dump Protection
²²
Available from FARIA Co.
C
1995 National Semiconductor Corporation RRD-B30M115/Printed in U. S. A.
g
100 ppm)
P O Box 983, Uncasville, CT 06382
Tel. 203-848-9271
TL/H/5263
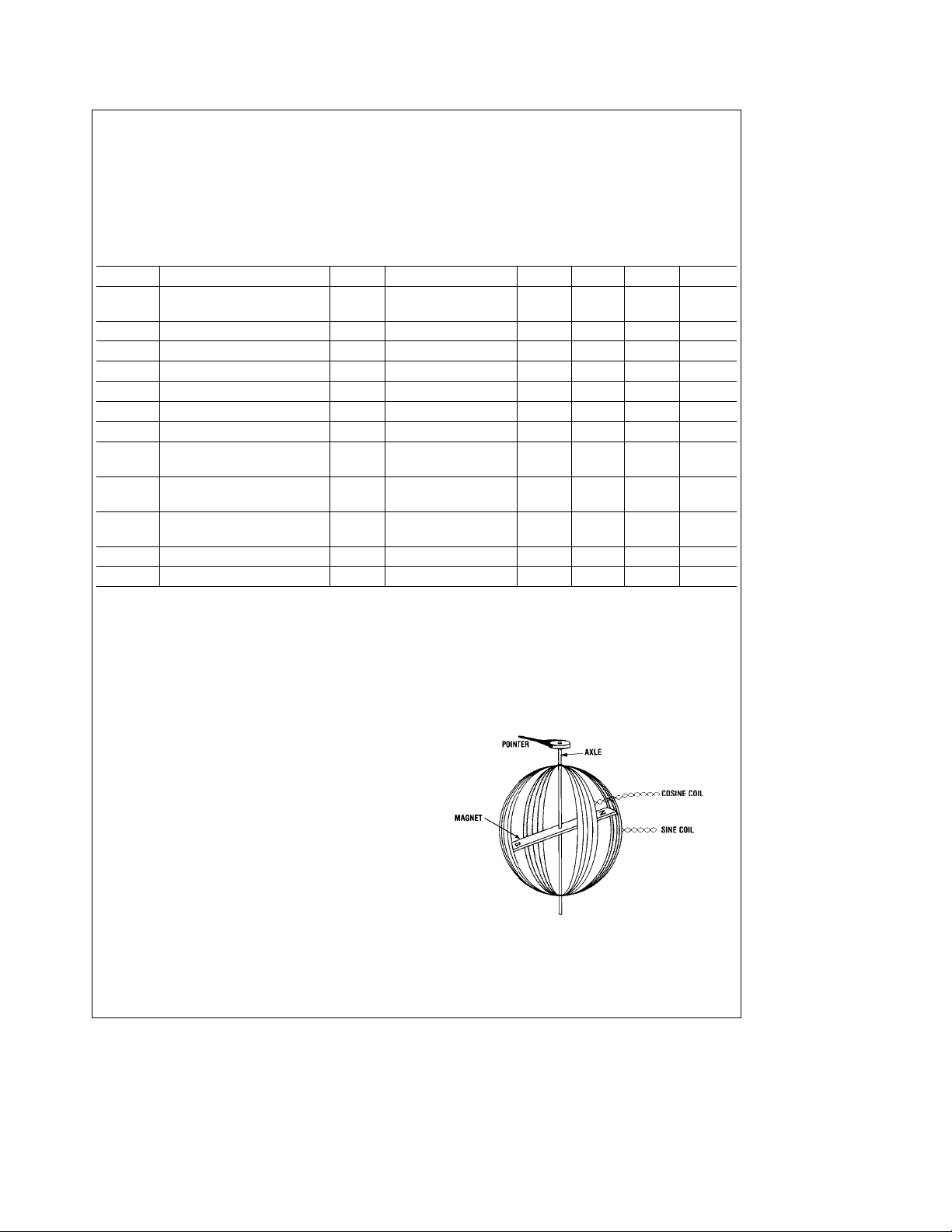
Absolute Maximum Ratings
If Military/Aerospace specified devices are required,
please contact the National Semiconductor Sales
Office/Distributors for availability and specifications.
Supply Voltage, V
Power Dissipation (note 1) 1300 mW
a
(pin 13) 20V
Operating Temperature
Storage Temperature
b
40§Ctoa85§C
b
65§Ctob150§C
Lead Temp. (Soldering, 10 seconds) 260§C
BV
CEO
20V
MIN
Electrical Characteristics V
S
e
13.1V T
e
25§C unless otherwise specified
A
Symbol Parameter Pin(s) Conditions Min Typ Max Units
I
S
V
REG
V
REF
h
FE
k Function Generator Gain Meter Deflection/DV
Note 1: For operation above 25§C, the LM1819 must be derated based upon a 125§C maximum junction temperature and a thermal resistance of 76§C/W which
applies for the device soldered in a printed circuit board and operating in a still-air ambient.
Supply Current 13 Zero Input Frequency
(See
Figure 1
)
Regulator Voltage 11 I
Regulator Output Resistance 11 I
Reference Voltage 4 I
Reference Output Resistance 4 I
Norton Amplifier Mirror Gain 5, 6 I
e
0 mA 8.1 8.5 8.9 V
REG
e
0 mA to 3 mA 13.5 X
REG
e
0 mA 1.9 2.1 2.3 V
REF
e
0 mAto50mA 5.3 kX
REF
j
20 mA 0.9 1.0 1.1
BIAS
NPN Transistor DC Gain 9, 10 125
Function Generator Feedback 1 V
Bias Current
Drive Voltage Extremes, 2, 12 I
Sine and Cosine
Sine Output Voltage 2 V
with Zero Input
Function Generator Linearity FSDe305
e
1
LOAD
e
8
5.1V
e
V
REF
20 mA
§
g
b
50.75 53.75 56.75
8
g
4
350 0
1.0 mA
65 mA
4.5 V
a
350 mV
g
1.7 %FSD
/V
§
Application Hints
AIR-CORE METER MOVEMENTS
Air-core meters are often favored over other movements as
a result of their mechanical ruggedness and their independence of calibration with age. A simplified diagram of an aircore meter is shown in
Figure 2
. There are three basic
pieces: a magnet and pointer attached to a freely rotating
axle, and two coils, each oriented at a right angle with respect to the other. The only moving part in this meter is the
axle assembly. The magnet will tend to align itself with the
vector sum of H fields of each coil, where H is the magnetic
field strength vector. If, for instance, a current passes
through the cosine coil (the reason for this nomenclature
will become apparent later) as shown in
Figure 3(a)
, the
magnet will align its magnetic axis with the coil’s H field.
Similarly, a current in the sine coil (
Figure 3(b)
) causes the
magnet to align itself with the sine H field. If currents are
applied simultaneously to both sine and cosine coils, the
magnet will turn to the direction of the vector sum of the two
H fields
(Figure 3(c)).
H is proportional to the voltage applied
to a coil. Therefore, by varying both the polarity and magnitude of the coil voltages the axle assembly can be made to
rotate a full 360
ter through a minimum of 305
. The LM1819 is designed to drive the me-
§
.
§
FIGURE 2. Simplified Diagram of an Air Core Meter.
2
TL/H/5263– 2
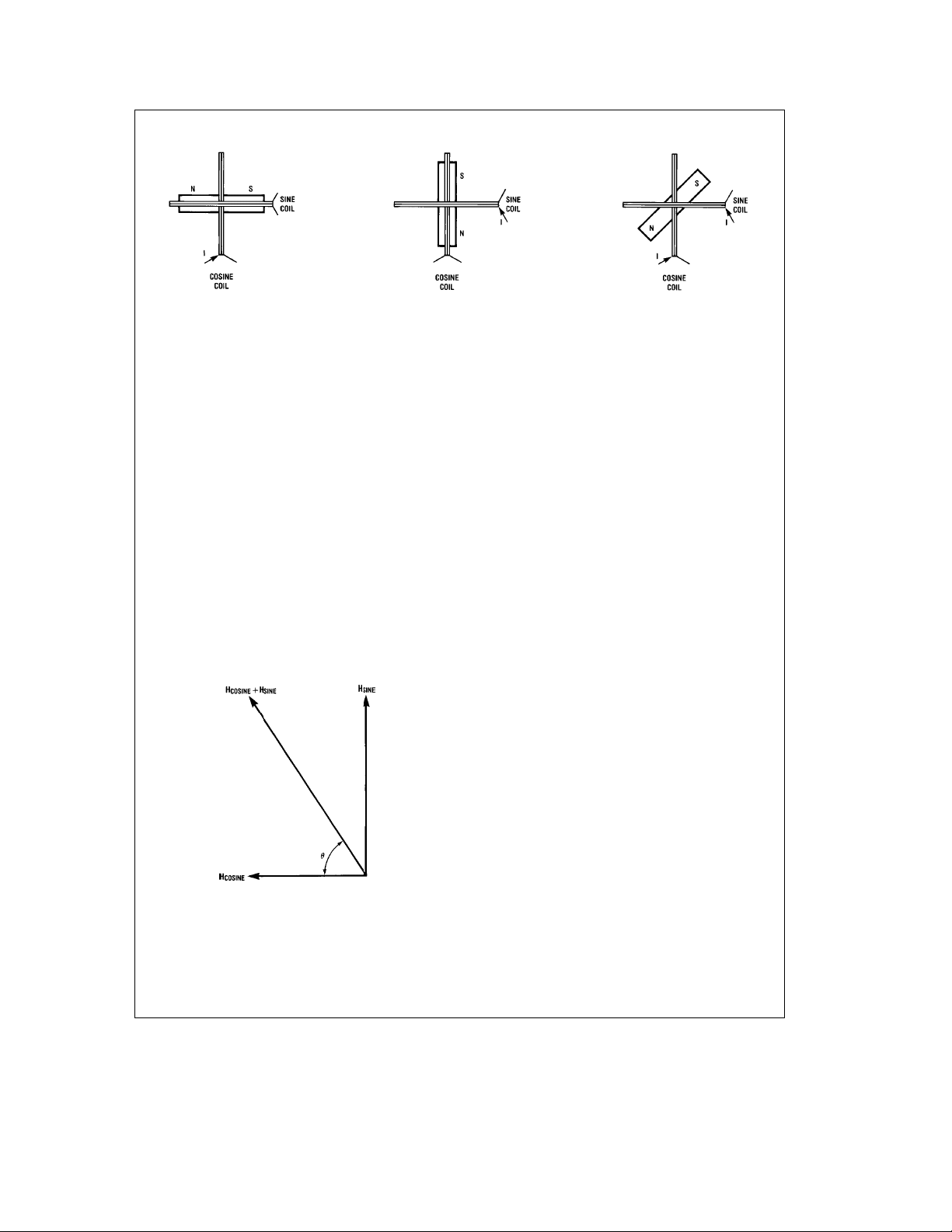
Application Hints (Continued)
FIGURE 3. Magnet and pointer position are controlled by the H field generated by the two drive coils.
In an air-core meter the axle assembly is supported by two
nylon bushings. The torque exerted on the pointer is much
greater than that found in a typical d’Arsonval movement. In
contrast to a d’Arsonval movement, where calibration is a
function of spring and magnet characteristics, air-core meter calibration is only affected by the mechanical alignment
of the drive coils. Mechanical calibration, once set at manufacture, can not change.
Making pointer position a linear function of some input is a
matter of properly ratioing the drive to each coil. The H field
contributed by each coil is a function of the applied current,
and the current is a function of the coil voltage. Our desired
result is to have i (pointer deflection, measured in degrees)
proportional to an input voltage:
e
i
kV
IN
[1]
where k is a constant of proportionality, with units of degrees/volt. The vector sum of each coils’ H field must follow
the deflection angle i. We know that the axle assembly
always points in the direction of the vector sum of H
and H
formula:
. This direction (see
COSINE
e
(i)
arctan
Figure 4
) is found from the
À
H
l
SINE
l/l
H
COSINE
Ó
l
SINE
[2]
Recalling some basic trigonometry,
e
(i)
arctan(sin (i) / cos(i ))
FIGURE 4. The vector sum of H
in a direction i measured in a clockwise direction from
H
.
COSINE
COSINE
and H
[3]
TL/H/5263– 4
points
SINE
(c)(b)(a)
TL/H/5263– 3
Comparing[3]to[2]we see that if H
of i, and H
ate a net H field whose direction is the same as i. And since
varies as the cosine of i, we will gener-
COSINE
varies as the sine
SINE
the axle assembly aligns itself with the net H field, the pointer will always point in the direction of i.
THE LM1819
Included in the LM1819 is a function generator whose two
outputs are designed to vary approximately as the sine and
cosine of an input. A minimum drive of
g
20 mA atg4V is
available at pins 2 (sine) and 12 (cosine). The common side
of each coil is returned to a 5.1V zener diode reference and
fed back to pin 1.
For the function generator, kj54
input (pin 8) is internally connected to the Norton amplifier’s
output. V
ference of the voltages at pins 8 (Norton output/function
as considered in equation[1]is actually the dif-
IN
/V (in equation 1). The
§
generator input) and 4. Typically the reference voltage at pin
4 is 2.1V. Therefore,
e
b
i
k(V
V
)e54 (V
8
REF
b
2.1)
8
As V8varies from 2.1V to 7.75V, the function generator will
drive the meter through the chip’s rated 305
range.
§
Air-core meters are mechanically zeroed during manufacture such that when only the cosine coil is driven, the pointer indicates zero degrees deflection. However, in some applications a slight trim or offset may be required. This is
accomplished by sourcing or sinking a DC current of a few
microamperes at pin 4.
A Norton amplifier is available for conditioning various input
signals and driving the function generator. A Norton amplifier was chosen since it makes a simple frequency to voltage
converter. While the non-inverting input (pin 6) bias is at one
diode drop above ground, the inverting input (5) is at 2.1V,
equal to the pin 4 reference. Mirror gain remains essentially
flat to I
designed to source current into its load. To bypass the Nor-
MIRROR
e
5 mA. The Norton amplifier’s output (8) is
ton amplifier simply ground the non-inverting input, tie the
inverting input to the reference, and drive pin 8 (Norton output/function generator input) directly.
An NPN transistor is included on chip for buffering and
squaring input signals. Its usefulness is exemplified in
ures 1
&6where an ignition pulse is converted to a rectan-
Fig-
gular waveform by an RC network and the transistor. The
emitter is internally connected to ground. It is important not
to allow the base to drop below
b
5Vdc, as damage may
occur. The 2.1V reference previously described is derived
from an 8.5V regulator at pin 11. Pin 11 is used as a stable
supply for collector loads, and currents of up to 5 mA are
easily accommodated.
[4]
3