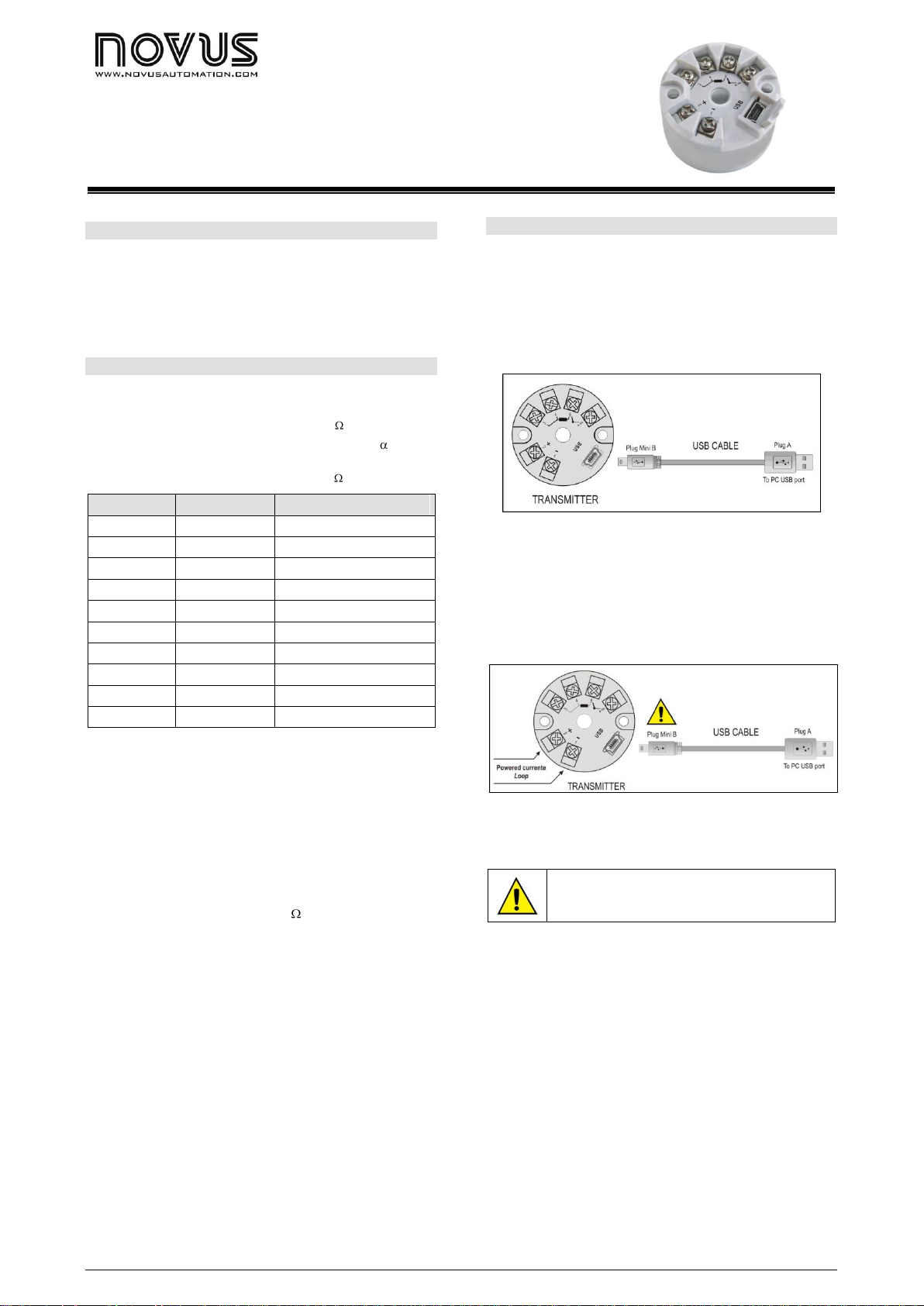
TxIsoPack
TEMPERATURE TRANSMITTER – OPERATING MANUAL V1.1x C
INTRODUCTION
Minimum Measurement Range
The USB communication port (interface) of the
TxIsoPack is not electrically insulated from the
transmitter’s input.
The TxIsoPack is an 4-20 mA 2-wire isolated temperature transmitter, for
head assembly. Powered by the current loop, its configuration is
accomplished by connecting the transmitter directly to the PC USB interface,
not requiring installation of additional drivers.
The output current is linearized and adjusted in fuction of the input sensor
type and range configured.
SPECIFICATIONS
Sensor input: Configurable.
Thermocouples: Types J, K, R, S, T, N, E and B, According to IEC
60584 (ITS-90) Impedance >> 1 M
Pt100: Types: 2, 3 and 4 wires, Excitation 0.17 mA, = 0.00385,
According to IEC60751 (ITS-90).
Voltage: 0 to 50 mVdc. Impedance >> 1 M
CONFIGURATION
When the transmitter is already configured with the sensor and desired
ranges, no intervention is necessary and its installation may be executed
immediately. When it is necessary to change the configuration, it should be
made through the TxConfig software.
USB cable and TxConfig software make up the Transmitter Setup Kit that
can be purchased from the manufacturer or any authorized representative.
The setup software may be updated at no charge at the manufacturer’s
website. To install, execute the file Tx_setup.exe and follow the instructions.
Table 1 – Sensors maximum measurement ranges
Total accuracy: Maximum error 0.3 % of the maximum range for
thermocouples, 0.2 % for Pt100 and voltage.
Response time: ≤ 500 ms
Isolation: 1000 Vac for 1 minute between input and output.
Output: 4-20 mA or 20-4 mA current, 2-wired; linear in relation to the
temperature measurement by the selected sensor.
Resolution: 0.004 mA (12 bits).
Power supply: 12 to 35 Vdc, voltage across the transmitter.
Maximum load (RL): RL= (VDC – 12) / 0.02
Were: VDC = Power supply voltage
Operating temperature: -20 to 75 °C
Humidity: 0 to 90 % RH
Electromagnetic compatibility: EN 50081-2, EN 50082-2
Internal protection against the supply voltage polarity inversion.
Cold junction compensation for thermocouples.
ABS box, diameter de 44 mm and max. height 24 mm.
5-pin USB mini-B 5 connection cable.
NOVUS AUTOMATION 1/3
Fig. 1 – USB cable connections
During the setup, the transmitter is powered by the USB, not requiring an
external power supply.
The transmitter setup can also be made by connecting it to the loop, using
the loop power supply. There is no electrical insulation between the
transmitter and the communication port (interface), therefore it is not
recommended to configure it with the sensor inlet connected to the process.
See Fig. 2.
Fig. 2 – USB cable connections – Loop powered
After these connections, the user must run the TxConfig software and, if
necessary, consult the Help topic to help using the software.
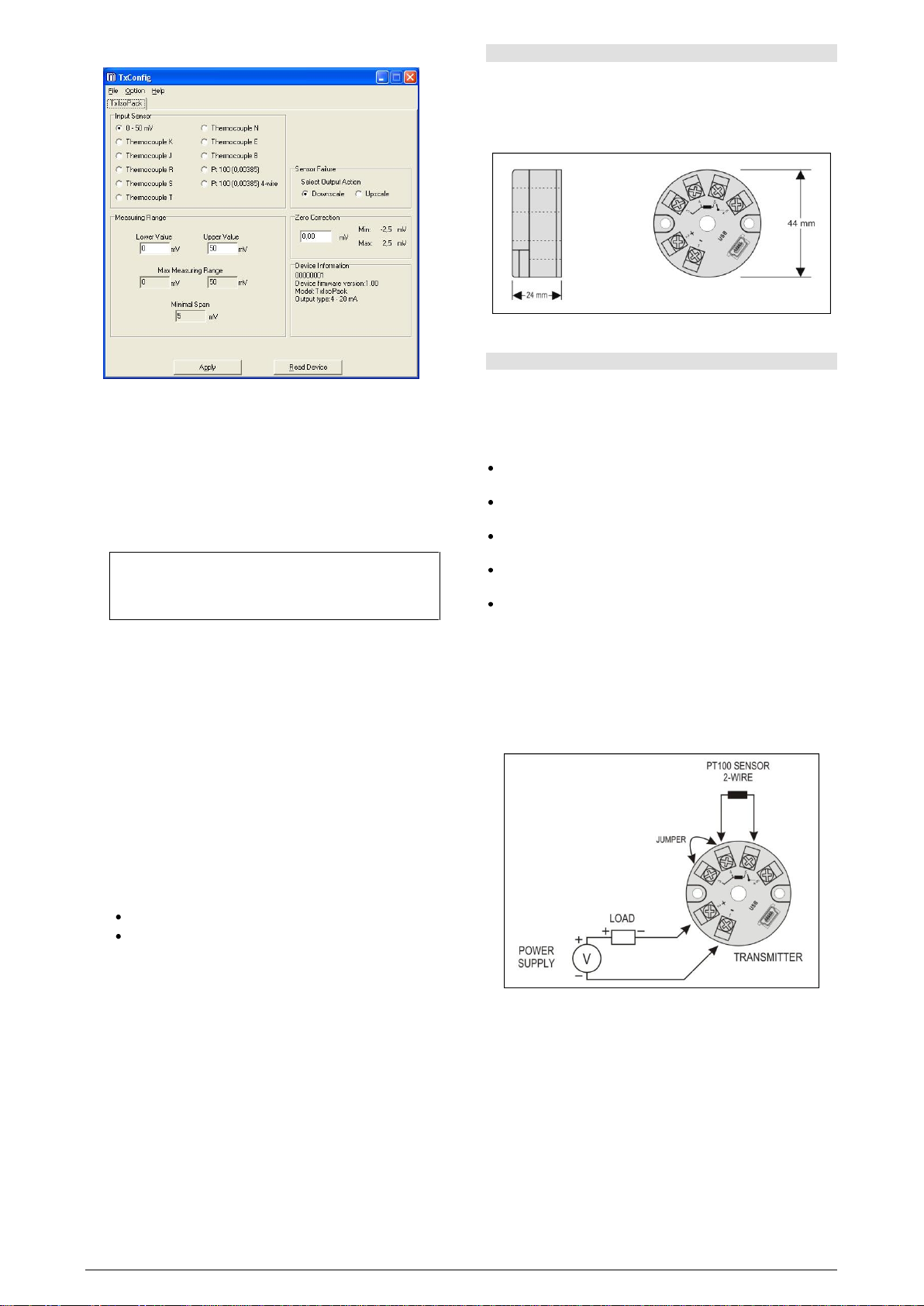
The TxConfig screen in shown in Fig. 3.
Note: The values chosen can not exceed the Sensor Range shown
in this same field, and also may not establish a range with width
(span) smaller than the Min. Range indicated later in this same field.
See Table 1 of this guideline.
MECHANICAL INSTALLATION
The TxIsoPack transmitter is suitable to be installed in heads. Vibrations,
moisture and extreme temperatures, electro-magnetic interference, high
voltage and other interferences can permanently damage the unit, and could
cause error in the measured value.
DIMENSIONS:
Fig. 3 – TxConfig main screen
The fields in the screen mean:
1. Input Sensor: Select the sensor to be used. See Table 1.
2. Measuring Range: Define the transmitter measurement range.
Range Lower Limit: temperature desired for a 4 mA current.
Range Upper Limit: temperature desired for a 20 mA current.
When the Lower Limit is set with a value greater than the Upper
Limit value of the output current operates from 20 to 4 mA (the
current decreases as the temperature increases).
3. Sensor Failure: It establishes the output behavior, when the transmitter
indicates a failure:
Minimum: output current goes to 3.8 mA (down-scale), typically used for
refrigeration.
Maximum: output current goes to 20.5 mA (up-scale), typically used for
heating.
4. Device Information: This field contains the data identifying the
transmitter. This information must be submitted to the manufacturer for
any queries.
5. Zero Correction: It corrects small deviations presented in the transmitter
outlet, for example, when the sensor is replaced.
6. Send Configuration: It applies the new setup. Once sent, the setup will
be immediately adopted by the transmitter.
7. Read Configuration: Reads the current setup in the transmitter
connected. The screen now presents the current setup that may be
changed by the user.
Note: The factory default configuration is:
Sensor Pt100, range 0 to 100 °C, 0 °C of zero correction.
Output at maximum for the sensor failures.
Upon purchase order, the user can define a specific setup.
NOVUS AUTOMATION 2/3
Fig. 4 – Transmitter dimensions
ELECTRICAL INSTALLATION
Polyamide enclosure.
Section of the cable used: 0.14 to 1.5 mm².
Recommended torque in the terminal: 0.8 Nm.
RECOMMENDATIONS FOR INSTALLATION
Sensor signals conductors must go through the plant system separate
from power leads (loop), if possible in grounded conduits.
The instruments must be powered from the instrumentation power supply
circuit.
In control and monitoring applications is essential to consider what can
happen when any part of the system fails.
It is recommended the use of suppressors in contact coils, solenoids and
any inductive load.
Use compensation cables in the connections using thermocouples.
ELECTRICAL CONNECTIONS
The figures below show the electrical connections required. The terminals 3, 4,
5 and 6 are dedicated to the sensor connection. LOAD represents the 4-20 mA
current measuring device (indicator, controller, recorder, etc.)
PT100 2-WIRES
Note: When the Pt100 2-wires the terminals 3 and 4 must be interconnected,
according to the figure below.
Fig. 5 – Transmitter electrical connections (Pt100 2-wires)