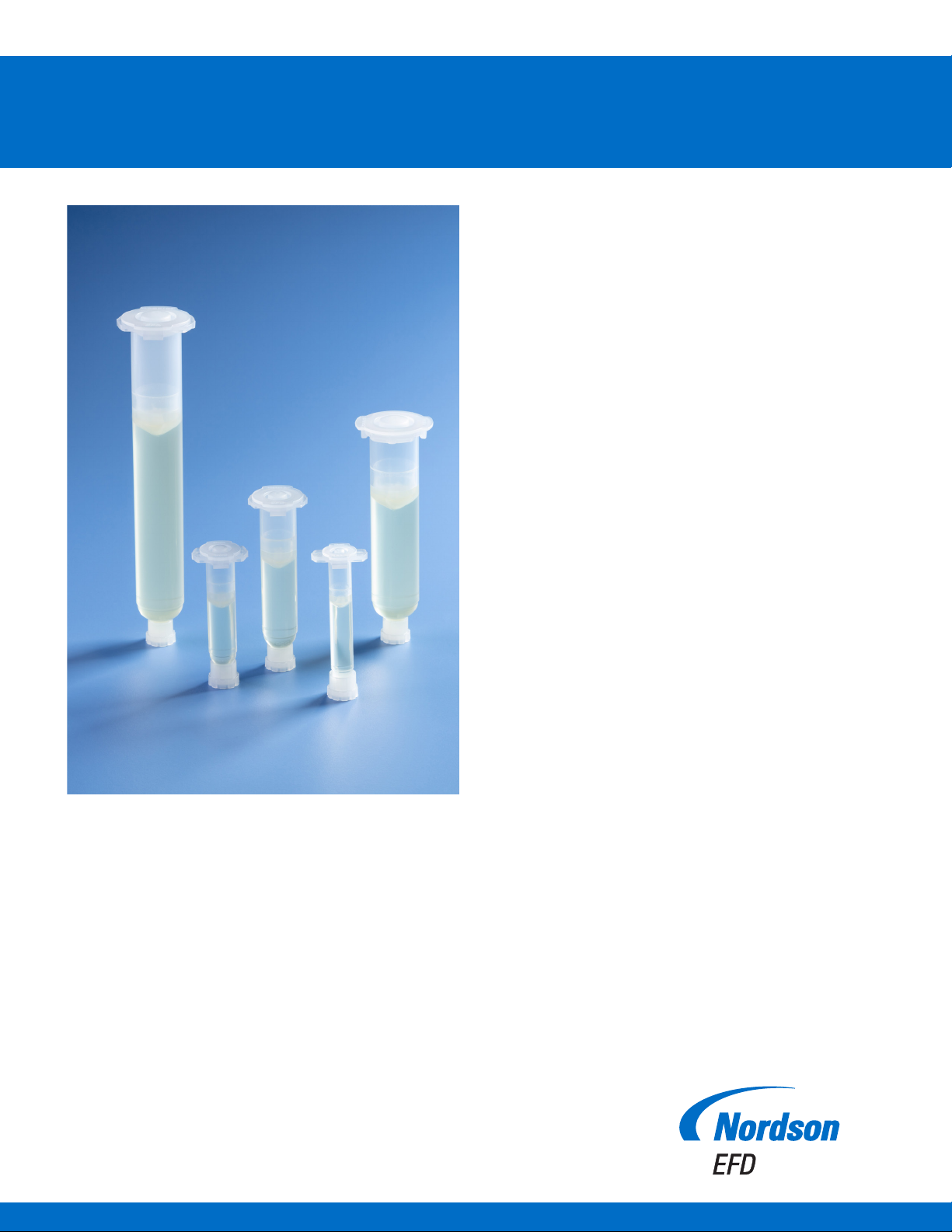
Optimum Class VI Dispensing Components
Sterilization Test Report
Introduction
This test report provides an evaluation of the impact of
various sterilization methods on the viability of Nordson
EFD’s Optimum® dispensing components. Class VI and
standard Optimum syringe barrels, pistons, and end and
tip caps, as well as general purpose and tapered
dispensing tips underwent industry standard gamma
irradiation, ethylene oxide (ETO), and autoclave
sterilizations. Components were evaluated for post
sterilization damage and loss of functional properties.
Please note that this document does not serve as
sterilization instructions but rather as a study of the
impacts of the most common sterilization methods on
Nordson EFD’s Optimum components.
Optimum Class VI syringe barrels, pistons, and end and tip caps.
Results Summary
Based on this test, ETO and gamma methods have little
to no impact on product properties, while autoclaving
causes heat damage, especially to low-density
polyethylene (LDPE) parts in tip and end caps.
All sterilization methods were observed to be compatible
with the Class VI polypropylene (PP) syringe barrels.
Gamma was observed to cause discoloration in the
Optimum syringe barrels made from Class VI medical
resin. Autoclave is only recommended for syringe barrels
and high-density polyethylene (HDPE) pistons, and caused
damage to all LDPE components including tip caps, end
caps, and Class VI pistons. General purpose and standard
tapered dispensing tips were observed to be compatible
with all three methods.
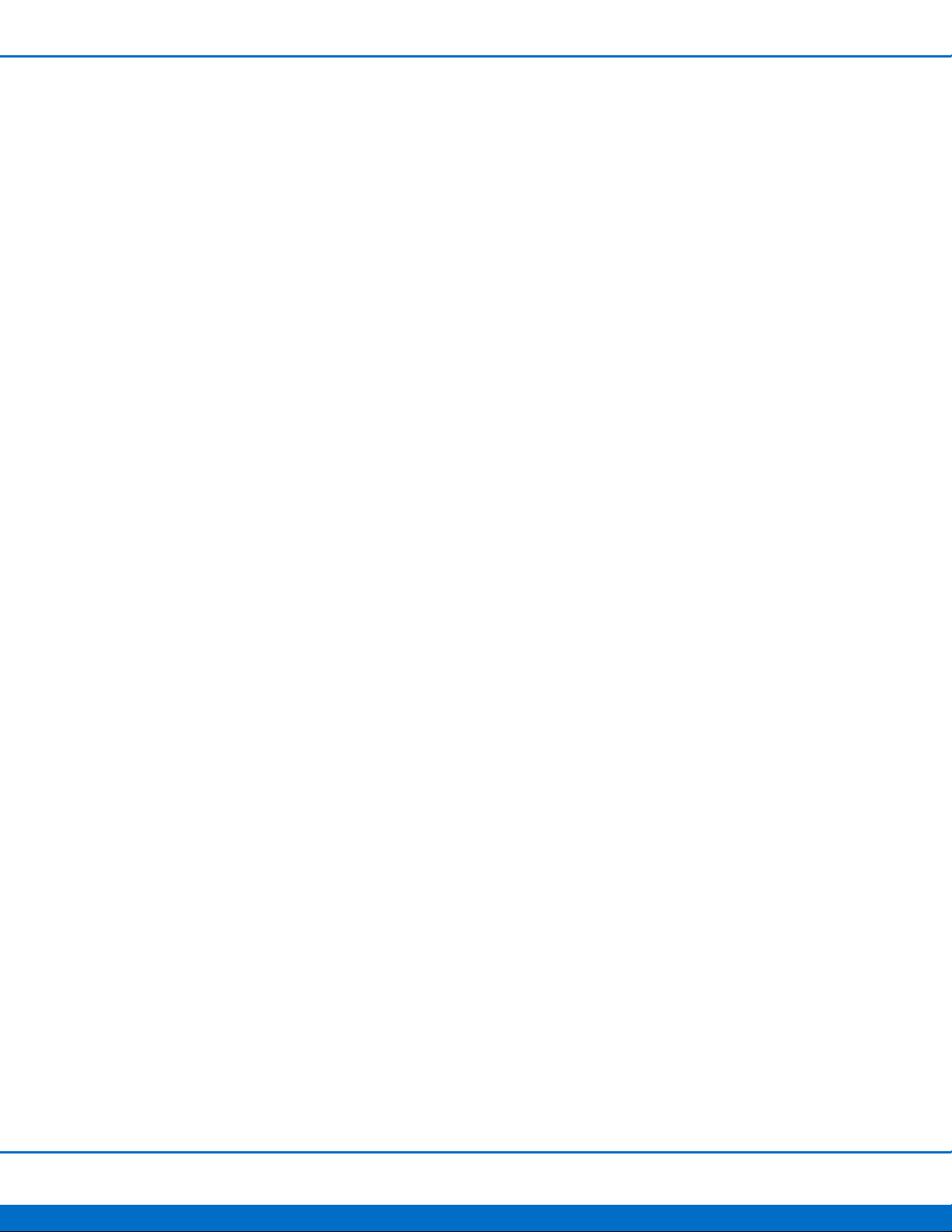
Sterilization Test Report
Test Methods
Ethylene Oxide (ETO) Sterilization
EFD standard anti-static bags were lled with a standard number of individual products, vented, and
placed inside cardboard boxes, which were loaded into the ETO chamber. The chamber was ooded with
2.0 in HgA/minute of ETO gas at 43° C (110° F) for 4 hours after conditioning for humidity and then cleaned
with a nitrogen post wash. Parts were placed in the same packaging for further analysis.
Gamma Irradiation Sterilization
EFD standard anti-static bags were lled with a standard number of individual products and then tted
with a 20 kGy radiation indicator and placed inside a cardboard box. Boxes were hand loaded into a
radiation chamber at a specied distance from the radiation source to ensure that a total dosage of 20-35
kGy could be achieved over 3 hours. Parts were placed back in the same packaging for further analysis.
Autoclave Sterilization
Nordson EFD products were re-bagged into Tyvek vented header bags and sterilized for 30 minutes at
121° C (249° F). Post-autoclave bags were re-packaged into cardboard boxes for further analysis.
Post Sterilization Test
Barrels were inspected for three primary attributes that would be impacted by sterilization:
1. Visual inspection (yellowing / clarity)
2. Impact strength
3. Hydrostatic burst strength
General purpose dispensing tips were tested with a cannula pull strength test using a Chatillon motorized
tester and inspected for needle damage, glue failure, hub slip, or hub failure.
Pistons and tapered dispensing tips were tested on the Instron® 5960 Series Dual Column Table Frames
tensile and compression tester with Bluehill V3.1 material testing software.
www.nordsonefd.com info@nordsonefd.com 800-556-3484 Sales and service of Nordson EFD dispensing systems are available worldwide.