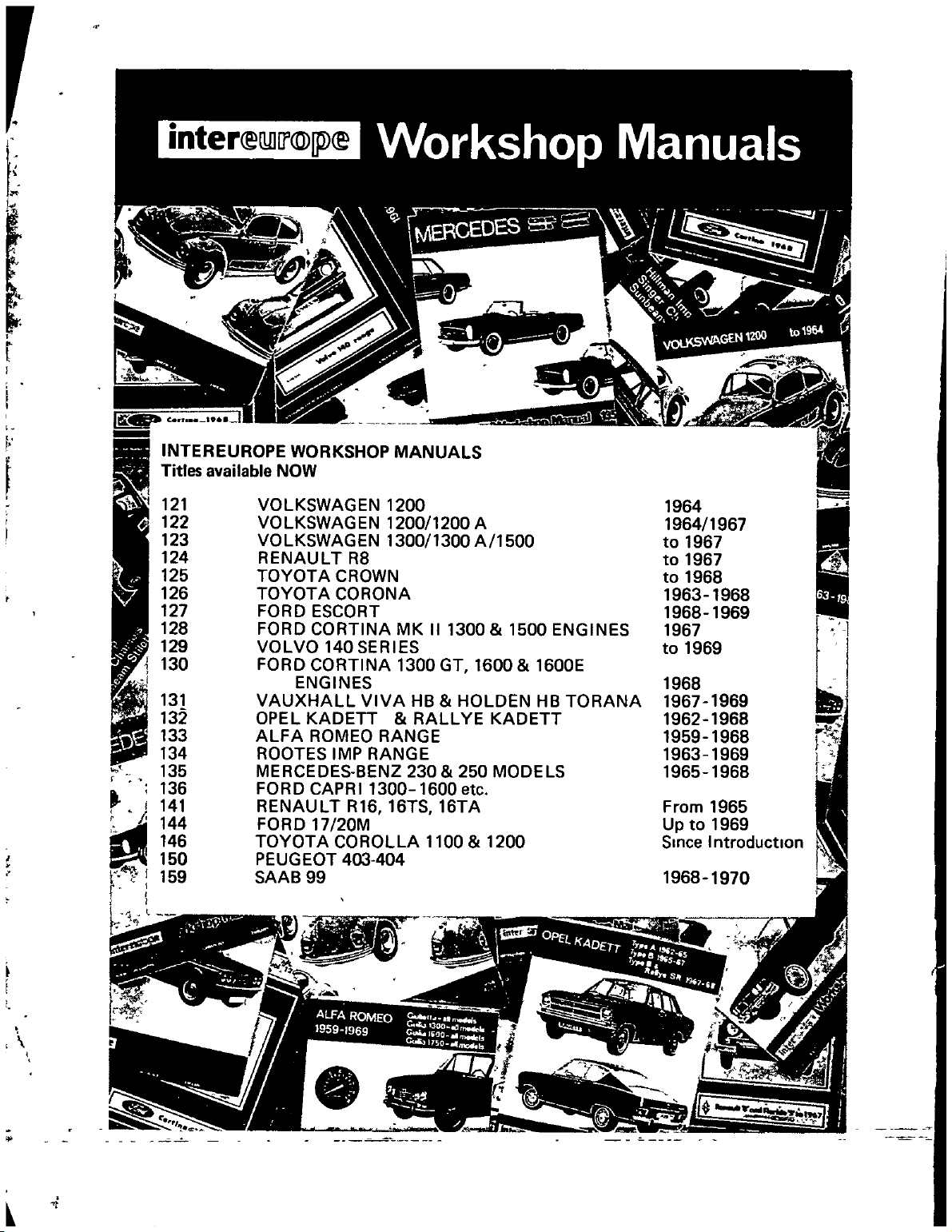
f
I
r
r
f
d
1
I
INTER
Titles
121
122
123
124
125
126
127
128
129
130
131
132
133
134
135
136
141
144
146
150
159
EUROPE
available
WORKSHOP
NOW
VOLKSWAGEN
VOLKSWAGEN
VOLKSWAGEN
RENAULT
TOYOTA
TOYOTA
FORD
FORD
VOLVO
FORD
ENGINES
VAUXHALL
OPEL
ALFA
ROOTES
MERCEDES BENZ
FORD
RENAULT
FORD
TOYOTA
PEUGEOT
SAAB
CROWN
CORONA
ESCORT
CORTINA
140
CORTINA
KADETT
ROMEO
IMP
CAPRI
17
20M
COROLLA
403
99
R8
SERIES
VIVA
RANGE
1300
R16
MANUALS
1200
1200
1300
MK
1300
RANGE
16TS
404
1200
1300
II
GT
HB
RALL
230
1600
16TA
1100
A
A
1500
1300 1500
1600
HOLDEN
YE
KADETT
250
MODELS
etc
1200
ENGINES
1600E
HB
TORANA
1964
1964 1967
to
1967
to
1967
to
1968
1963 1968
1968 1969
1967
to
1969
1968
1969
1967
1962 1968
1959 1968
1963 1969
1965 1968
From
1965
to
Up
Since
1968
1969
Introduction
1970
r
I
1
f7
I
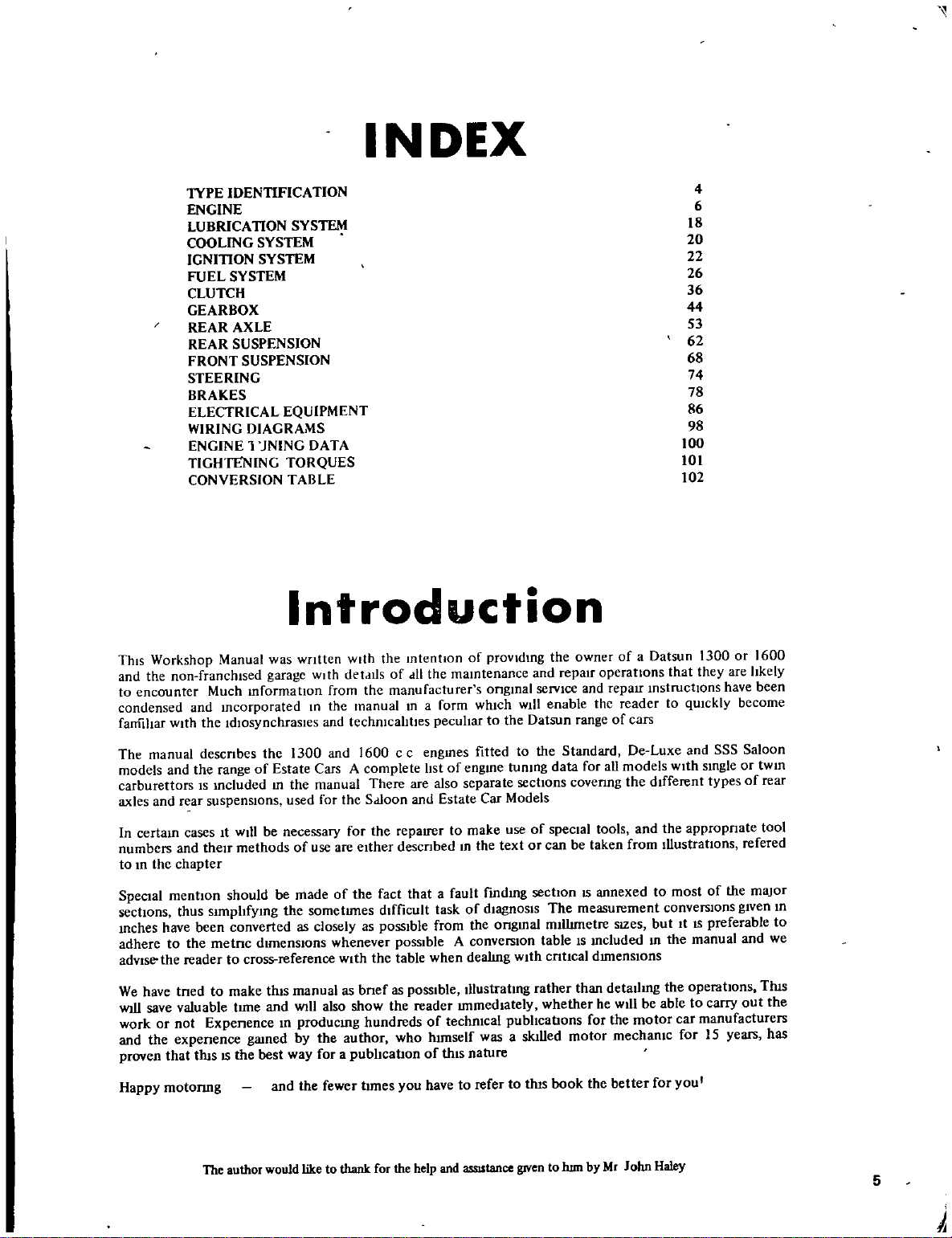
INDEX
l
This
Workshop
and
the
to
encounter
condensed
fanfihar
The
manual
models
carburettors
axles
and
In
certaIn
numbers
to
m
the
SpeCial
sechons
mches
adhere
adVise
We
have
WIll
save
or
work
and
the
proven
Happy
non
with
and
rear
cases
and
chapter
menlton
thus
have
to
the
reader
tned
valuable
not
expenence
that
motonng
lYPE
ENGINE
LUBRICATION
COOLING
IGNITION
FUEL
CLUTCH
GEARBOX
the
IDENTIFICATION
SYSTEM
AXLE
REAR
REAR
SUSPENSION
FRONT
SUSPENSION
STEERING
BRAKES
ELECTRICAL
WIRING
ENGINE
TIGHTENING
CONVERSION
Manual
franchised
Much
and
Incorporated
the
IdlOsynchrasles
descnbes
the
range
IS
Included
suspenSIOns
It
Will
thelf
methods
should
slmphfymg
been
converted
metnc
cross
to
make
to
tnne
Expenence
tillsISthe
SYSTEM
SYSTEM
SYSTEM
EQUIPMENT
DIAGRAMS
1
JNING DATA
TORQUES
TABLE
Introduction
was
garage
InformatIOn
the
of
Estate
m
be
be
dunenslons
reference
thiS
and
m
gamed
best
and
WrItten
1300
the
used
necessary
of
made
the
as
manual
WIll
prodUCIng
by
way
with
m
use
some
the
from
the
and
and
Cars
manual
for
the
are
of
tunes difficult
closely
whenever
With
as
also
the
for
a
fewer
wIth
the
detdlls
the
manual
techmcahtles
1600
A
complete
There
Sdloon
for
the
either
the
fact
as
pOSSIble
the
bnef
show
hundreds
author
pubhcatlOn
tnnes
IntentIon
of
dllthe
manufacturer
In
a
c c
engmes
hst
are
and
reparrer
descnbed
thatafault
pOSSible
table
when
as
pOSSible
the
reader
of
hunself
who
of
have
you
maIntenance
form
pecuhar
of
also
Estate
to
In
task
from
A
Iffimedlately
techmcal
thiS
to
of
providIng
s
ongInal
which
to
fitted
engme
separate
Car
make
the
text
findmg
of
diagnOSIS
the
ongInal
conversion
deahng
tllustratmg
was
nature
refertotills
the
and
selVlce
will
enable
the
Datsun
to
the Standard
data
tumng
secltons
Models
use
of
speCial
or
can
sechon
The
mtlhmetre
tableISmcluded
With
cnhcal
rather
whether
pubhcatIons
a skilled
book
owner
repalf
and
range
for
covenng
be
IS
measurement
than
for
motor
the
ofaDatsun
operatIOns
repalf
the
reader
of
all
tools
taken
annexed
SIZes
dlffienslons
detailing
he
Will
the
mechamc
better
cars
De
models
the
and
from
motor
Instructions
Luxe
different
the
Illustraltons
to
conversIOns
but
In
be
able
for
20
22
26
36
44
S3
62
68
86
100
101
102
that
to
qUickly
and
with
appropnate
most
It
the
the
car
for
you
4
6
18
74
78
98
1300
are
they
have
SSS
smgle
types
of
the
IS
preferable
manual
operahons
to
carry
manufacturers
15
years
I
or
hkely
become
Saloon
or
of
refered
major
gIVen
and
out
1600
been
tWIn
rear
tool
m
to
we
Tills
the
has
The
wouldliketothank
author
for
the
help
and
3SSIStance
gtven
to
bunbyMr
John
Haley
5
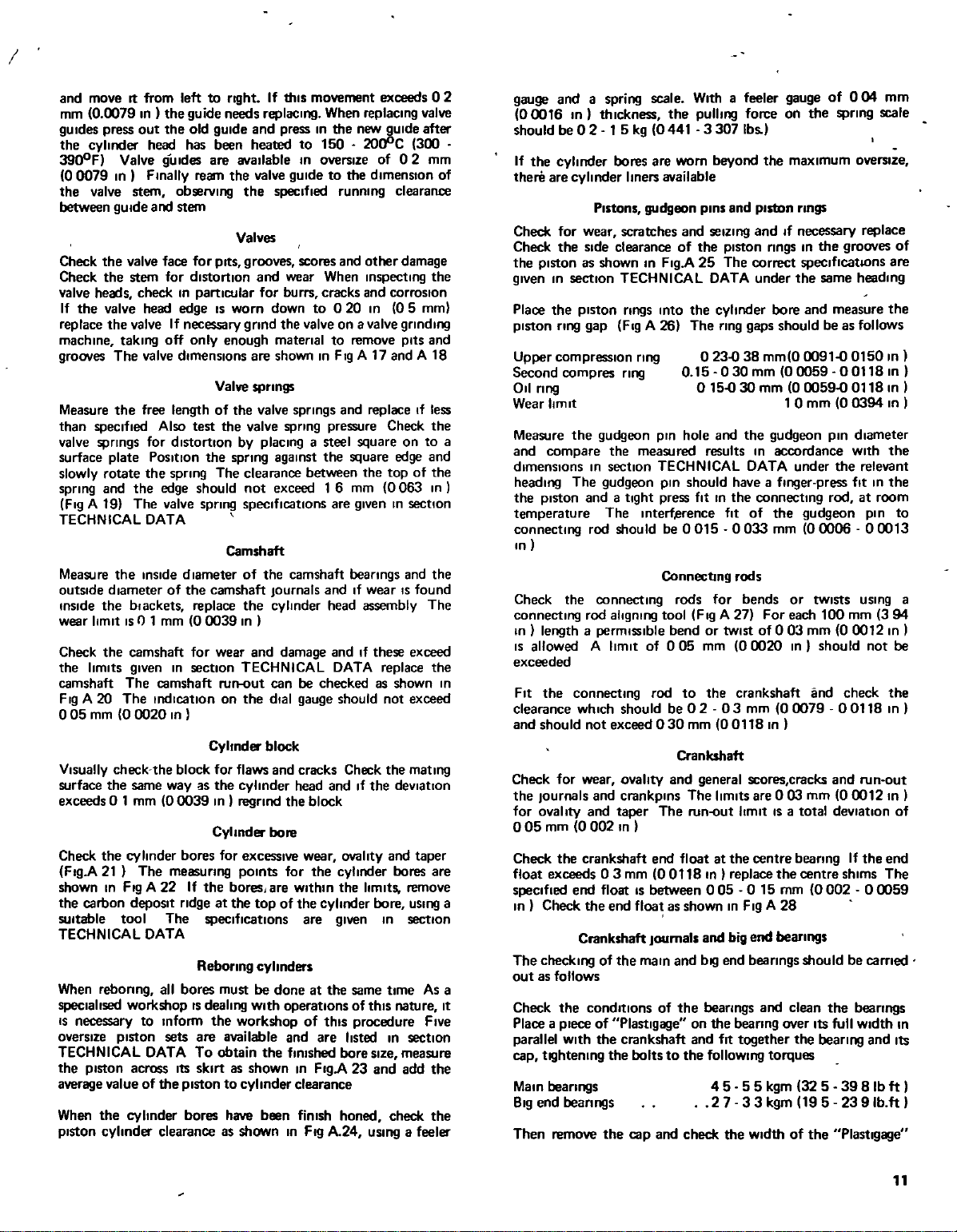
I
and
move
It
from left
10m
0
0079
10
1
press
Valve
10
valve
gUide
the
the
heads
valve
the
taking
The
the
speCified
sprongs
plate
rotate
and
191
1
stem
valve
stem
valve
the
The
out
head
Fmally
and
check
head
valve
free
Also
for
PosItion
the
gUides
the
3
JOOF
00079
the
between
Check
Check
valve
If
the
replace
machine
grooves
Measure
than
valve
surface
slowly
sprmg
Fig
cylinder
A
TECHNICAL DATA
Measurethe
outside
inSide
wear
limitISC
Check
the
limits
camshaft
A 20
Fig
005
10m
Visually
surface
exceeds01
Check
FlgA
shown
the
carbon
SUitable
diameter
the
blackets
the
camshaft
given
The
The
0002010
check
the
same
mm
the
cylinder
211The
10
Fig
depOSit
tool
InSide
1
camshaft
Indication
the
A 22
TECHNICAL DATA
When
rebonng
speclahsed
IS
necessary
oversize
workshopISdealing
to
piston
TECHNICAL DATA
the
average
When
piston
piston
valueofthe
the
cyhnder
across
cyhnder
clearance
the
guide
the
old
has
gUides
observmg
stem
face
for
for
distortion
10
edge
If
necessary
off
only
dimenSions
length
test
distortion
spring
edge
valve
diameter
of
the
replace
10m
00039
for
In
sectIOn
block
way
0
0039
bores
measunng
If
ridge
The
all bores
mfonn
sets
Its
piston
bores
to
nght
needs
and
gUide
heated
been
are
available
ream
the
the
Valves
pitS
grooves
particular
IS
worn
gnnd
enough
are
Valve
sprmgs
of
the
the
valve
by
the
spnng
The
clearance
should
not
specifications
spnng
Camshaft
of
camshaft
the
In
wear
and
TECHNICAL DATA
runout
on
the
Cylmder
for
flaws
as
the
cylinder
In
regnnd
Cylinder
for
excessive
pOInts
the
bores
at
the
specifications
Rebormg
must
With
the
workshop
available
are
To
obtain the
skirt
as
shown
to
cylinder
have
as
shown
If
thiS
replacmg
press
to
10
valve
gUide
specified
scores
and
wear
for
burrs
down
the
matenal
shown
valve
springs
sprong
plaCing
against
exceed16
the camshaft
Journals
cylinder
1
damage
can
be
dial
gauge
block
and
cracks
head
the
bore
for
are
Within
of
the
top
cyhnders
be
doneatthe
operations
and
fmlshed
10
clearance
been
finish
In
movement
10
150
oversize
cracks
to
valve
In
a
between
checked
block
wear
the
cylinder
are
of
are
FlgA
Fig
When
When
steel
the
and
thiS
replacmg
new
the
2000C
the
dimenSion
to
running
and
other
mspectmg
and
0
20 10
on
a
valve
remove
to
A17andA18
Fig
and
replace
pressure
square
square
the
10m
are
given
bearings
wear
If
head
assembly
andIfthese
as
should
Check
and
If
the
ovallty
cylinder
the
limits
bore
given
same
of
thiS
procedure
hsted
bore
Size
23
and
honed
24
A
usmg
exceeds
gUide
of
02
clearance
corrosion
0 5
Check
edge
top
0063
In
replace
shown
not
the
deViation
and
bores
10
time
nature
10
check
0 2
valve
after
300
10m
damage
the
10m
gnndlng
and
pitS
If
less
the
on
to
and
of
the
10
section
and
the
IS
found
The
exceed
the
exceed
mating
taper
are
remove
USing
section
As
Five
section
measure
add
the
the
a
feeler
spnng
oversize
replace
grooves
head
00118101
0
0394
diameter
With
relevant
fit In
at
pin
00013
uSing
10m
0
0012
not
scale
room
394
10m
109
the
In
In
the
the
In
of
are
1
to
a
be
scale
With
a
pullmg
3307
beyond
pins
seiZing
the
piston
The
cyhnder
nng
023
0381010
030mm
o15030
and
results
fit In
fit
for
A 27
FI
I
or
twist
10m
and
have
the
rods
bends
00020
feeler
force
Ibs
1
the
piston
and
correct
under
gaps
mm
the
10
DATA
a
connecting
of
For
of003
nngs
bore
should
gudgeon
accordance
finger
the
10m
and
be
cyhnder
are
for
the
In
the
nng
compression
compres
limit
compare
piston
a
10
thickness
1
0215
cyhnder
Pistons
wear
Side
as
shown
section
piston
gap
the
gudgeon
In
The
and
rod
spring
bores
kg
hners
0441
are
available
the
worn
gudgeon
scratches
clearance
TECHNICAL DATA
nngs
Fig
ring
the
section
gudgeon
a
tight
The
should
10
FIgA 25
mto
A
261
nng
prn
measured
TECHNICAL
pin
press
be
and
of
0 15
hole
should
Interf
erence
0015 0033
the
The
gauge
00016
should
If
of
the
there
Check
Check
the
piston
given
Place
piston
Upper
Second
011
nng
Wear
a
Measure
and
dimenSions
heading
the
temperature
connecting
In
Connecting
Check
connecting
In
IS
length
allowed
the
connecting
rod
aligning
a
permiSSible
A
limit
rods
tool
bend
of
005
of 004
gauge
on
the
maximum
rmgs
If
necessary
10 the
specificatIOns
same
the
and
measure
beasfollows
00059
1
0
mm
pm
under
press
rod
gudgeon
00006
or
twistS
each
100
mm
In
should
0009100150
00059
0011810
the
exceeded
In
Fit
the
clearance
and
should
connecting
which
not
rod
should
exceed030
to
be
crankshaft
the
02
03
mm
10m
0011810
00079
1
and
check
00118
the
In
1
Crankshaft
Check
for
wear
ovahty
the
Journals
for
ovallty
o
05
Check
float
a
speCified
In
Check
1
10m
the
exceeds
and
and
taper
0
002
crankshaft
03
end
floatISbetween
the
end
crankplns
In
Crankshaft
The
checking
out
Check
Place
as
a
a
It
parallel
tl
lhtemng
cap
Main
beanngs
end
81g
Then
follows
the
piece
With
bean
remove
of
the
conditions
of
the
the
ngs
the
Plastlgage
crankshaft
and
The
end
10m
00118
floatasshown
Journals
maIO
and
of
boltstothe
and
cap
general
The
limitS
runout
floatatthe
In
005
and
end
bl
l
the
bearings
on
the
and
fit
follOWing
4 5 5 5
27
check
hmlt
replace
10
Fig
big
beanng
together
33
the
scores
are
0
IS
centre
the
0 15
mm
A
28
end
bearings
beanngs
and
torques
kgm
kgm
Width
cracks
03
a
total
beanng
clean
over
the
of
10m
centre
should
32
195
the
and
deViation
0002
the
Its
full
bearing
5
run
out
00012
If
the
shims The
00059
be
carned
bearings
Width
and
8Ibft
39
23
9lb
Plastlgage
In
end
ft
of
In
Its
1
11
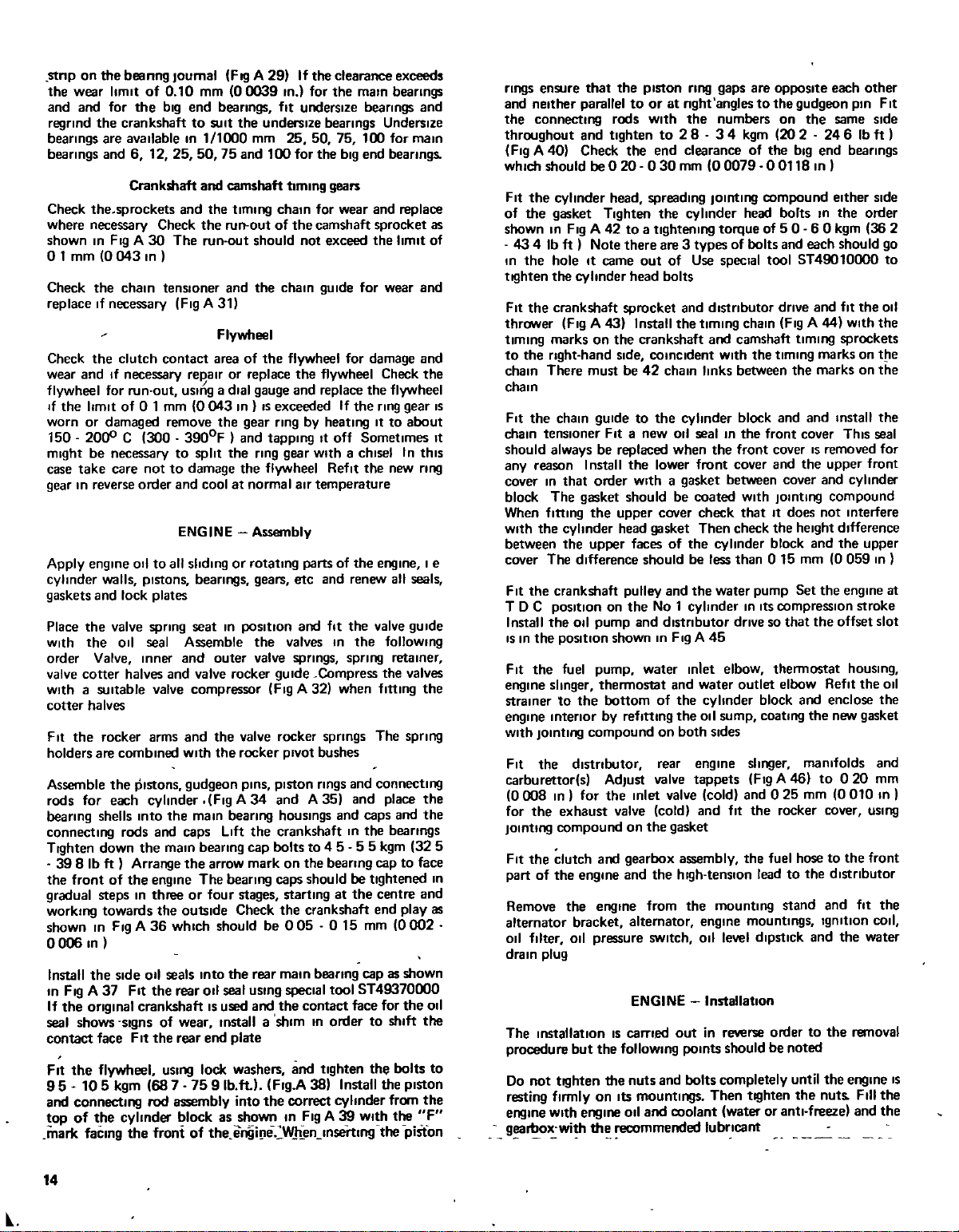
on
stnp
the
wear
and and
regrind
bearings
bearings
Check
where
shown
o
1
mm
Check
replace
Check
wear
and
flywheel
If
the
worn
150
might
case
take
In reverse
gear
Apply
cylinder
gaskets
Place
With
order
valve
With
cotter
Fit
the rocker
holders
Assemble
rods
bearing
connecting
Tighten
39
8
front
the
gradual
working
shown
00061n
Install
In
Fig
If
the
seal
shows
contact
Fit
the
95
and
connecting
of
top
mark
the
the
are
and
the
necessary
In
0
the
If
the
for
limit
or
damaged
2000
be
engine
walls
and
the
the
Valve
cotter
a
suitable
lves
ha
are
for
shells
down the
lb
ft
steps
towards
In
the
A 37
Original
face
flywheel
105
the
faCing
beanng
limit
for
the
crankshaft
available
6 12
Crankshaft
sprockets
A
Fig
043
chain
necessary
clutch
If
necessary
run
of01
C
necessary
care
order
011toall
lock
valve
011
halves
combined
the
pistons
each
Into
rods
Arrange
of
the
In
A 36
Fig
Side
Fit
crankshaft
slgns
FItthe
kgm
cylinder
the
of010
big
Check
30 The
In
tenslOner
contact
out
mm
300
notto
pistons
plates
spring
seal
Inner
valve
arms
cylinder
and
main
engine
three
the
011
the
of
USing
68
rod
front
Journal
mm
end
to
In
25
50
and
and
Fig
re
uSing
0043
remove
3900F
to
split
damage
and
ENGINE
sliding
bearings
seat
Assemble
and
and
valve
compressor
and
With
gudgeon
main
the
caps
bearing
the
The
or
outside
which
seals
Into
rear
wear
rear
7
75
assembly
block
of
A 29
FIQ
00039
beanngs
SUit
the
undersize
1000
the
75
camshaft
tlmll19
run
out
and
31
mm
and 100
out
should
the
1
the
run
A
Flywheel
area
of
the
alr
or
replace
a
dial
gauge
In
IS
the
gear
and
the
ring
the
coolatnormal
Assembly
or
rotating
gears
In
poSition
the
outer
valve
rocker
the
valve
the rocker
pinS
A 34
Fig
bearing
Lift
the
cap
mark
arrow
bearing
four
stages
Check
should
be
rear
the
seal
011
uSing
IS
used
and
Installashim
end
plate
lock
washers
9Ib
ft
I
into
the
as
shown
the
le
e
gi
If
the
In
for
fit
undersize
25 50 75
for
timing
chain for
of
the
not
chainguIde
flywheel
the
and
exceeded
ring
by
tapping
gear
flywheel
air
parts
etc
and
valves
springs
gUide
A 32
Fig
rocker
pivot
piston
and
A 35
hOUSings
crankshaft
boltsto4 5
on
the
shouldbe
caps
starting
the
crankshaft
005 015
main
special
the
contact
In
and
A
38
Flg
correct
In
Fig
h
en
W
clearance
the
main
bearings
bearings
100
end
the
big
gears
wear
camshaft
exceed
for
for
damage
flywheel
the
replace
If
the
heating
It
off
Sometimes
Withachisel
Refit the
temperature
of
the
and
renew
fit
the
In
the
spring
Compress
when
springs
bushes
and
rings
and
and
caps
In
the
55
bearing
tightened
the
at
mm
bearing
tool
order
tighten
Install
cap
ST49370000
face
to
the
cylinder
A39with
lnsertlng
exceeds
beanngs
Undersize
for
bearings
and
replace
sprocket
the
limit
wear
Check
flywheel
ring
It
to
In
new
engine
all
valve
follOWing
retainer
the
fitting
The
connecting
place
and
bearings
kgm
to
cap
centre
end
playas
0002
as
shown
for
the
shift
bolts
the
from the
the
the
and
main
and
and
the
gear
about
thiS
ring
I
seals
gUide
valves
the
Spring
the
the
325
face
and
the
piston
piston
of
011
to
F
ensure
rings
and
neither
the
connecting
throughout
A
Fig
which
Fit
the
of
as
the
shown
434Ib
In
the
tlQhten
Fit
the
thrower
timing
the
to
chain
chain
IS
It
e
Fit
the
chain
should
reason
any
cover
block
When
With
between
cover
Fit
the
TDC
Install
IS
In
the
Fit
the
engine
strainer
engine
With
Fit
carburettor
0008
for
the
JOinting
Fit
the
In
part
Remove
alternator
011
filter
drain
The
of
procedure
Do
not
resting
engine
g
that the
parallel
rods
and
Check
Fig
ft
cylinder
Fig
hand
be 0
A 42
Note
It
A 43
on
must
gUide
tighten
20
head
Tighten
there
came
sprocket
the
Side
be42chain
FIt
40
should
cylinder
gasket
In
hole
the
crankshaft
marks
right
There
chain
tensloner
alwaysbereplaced
I
nstall
In
that
order
The
gasket
the
fitting
the
cylinder
the
The
crankshaft
position
the
position
fuel
slinger
to
interior
JOinting
the
In
exhaust
upper
difference
011
pump
pump
thennostat
the
by
compound
distributor
s
for
upper
head
pulley
on
shown
bottom
refIning
AdjUst
the
valve
compound
clutch
and
engine
pressure
and
engine
the
the
bracket
011
plug
installation
tlQhten
flnnly
With
with
o
but
engine
IS
the
follOWing
the
on
Its
th
recommended
piston
toorat
With
the
end
030
spreading
a
to
tightening
out
head
Install
crankshaft
COinCident
to
the
a
new
the
lower
With
should
gasket
faces
should
No
the
and
In
water
of
rear
valve
Inlet
on
the
gearbox
the
from the
alternator
SWitch
ENGINE
carned
nuts
mountings
and
011
to
2 8 3 4
mm
the
are
3
of
bolts
and
the
cylinder
011
when
a
gasket
be
cover
of
and
1
dlstnbutor
Fig
and
the
the
on
both
valve
cold
gasket
assembly
high
out
points
and
coolant
ring
nght
the
clearance
cylinder
types
Use
timing
sealInthe
front
coated
check
Then
the
be
the
cylinder
A 45
Inlet
water
011
engine
tappets
and
engine
011
bolts
are
gaps
angles
numbers
00079
JOinting
torque
special
distributor
and
With
links
the
cylinder
less
water
elbow thennostat
cylinder
sump
Sides
cold
tenSion
mounting
opposite
to
the
on
20
kgm
of
the
00118
compound
head
borts
of
5 0
of
bolts
and
tool
drive
chain
Fig
camshaft
the
timing
between
and and
block
front
front
cover
cover
and
between
check
drivesothat the offset
fit
With
that
than
pump
In
Its
outlet
block
coating
slinger
Fig
and
the rocker
the
leadtothe
cover
JOinting
does
It
the
block
0 15
compressIOn
elbow
A 46
025
fuel
stand
mountings
level
dipstick
Installation
in
reverse
should
order
be
completely
Then
tlQhten
water
or
anti
lubricant
each
gudgeon
2
big
ST49010000
timing
the
cover
the
the
In
60
each
and
A 44
IS
same
246lb
end
I
either
In
kgm
marks
marks
Install
removed
upper
and
pin
bearings
the
should
fit
the
With
sprockets
on
on
ThiS
cylinder
compound
Interfere
not
difference
height
and
the
mm
0059
Set
the
engine
stroke
hOUSing
Refit the
and
enclose
new
the
manifolds
to
020
mm
0010
cover
hosetothe front
distributor
and
fit
Ignition
and
the
to
the
nuts
freeze
the
removal
engine
Fill
and
noted
until
the
other
Fit
Side
ft
Side
order
36
go
to
011
the
the
the
the
seal
for
front
upper
In
slot
011
the
gasket
and
mm
In
uSing
the
COil
water
the
the
2
at
IS
14
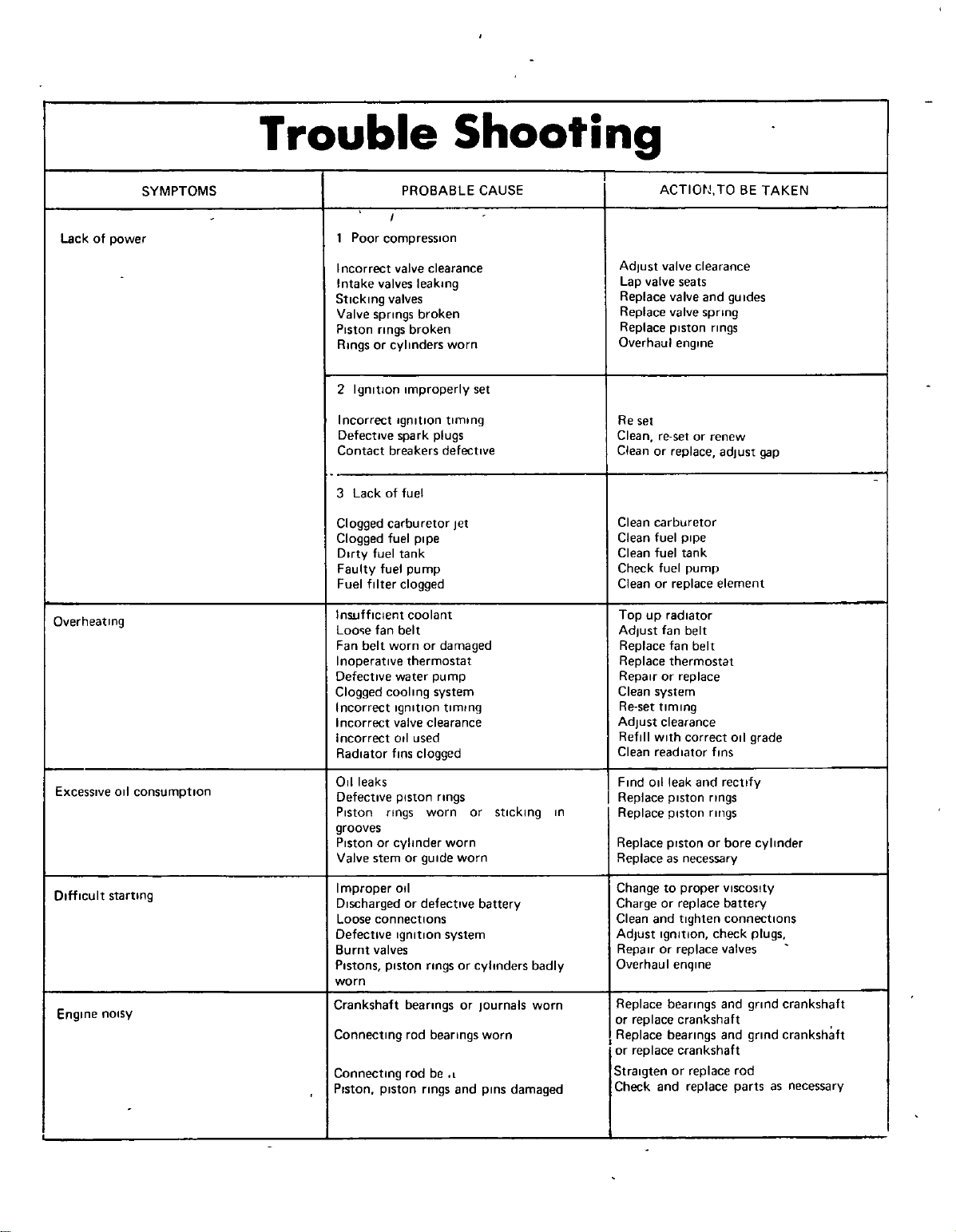
Trouble
Shooting
Lack
of
Overheating
ExceSSive
D
fficult
nOIsy
Engine
power
oil
starting
SYMPTOMS
consumptIon
PROBABLE
I
1
Poor
compresSion
Incorrect
Intake
Sticking
Valve
Piston
valves
valves
springs
rings
valve
broken
Ringsorcylinders
2
Ignition
Incorrect
DefectIve
Contact
3
Lackoffuel
Clogged
Clogged
Dirty
Faulty
Fuel
Insufficient
Looefan
Fan
Inoperative
Defective
Clogged
Incorrect
Incorrect
Incorrect
Radiator
Oil
DefectIve
Piston
grooves
Piston
Valve
Improper
Discharged
Loose
Defective
Burnt
PIstons
worn
Crankshaft
Connecting
ConnectIng
Piston
filter
belt
leaks
Ignition
spark
breakers
carburetor
fuel
fuel
tank
fuel
clogged
belt
worn
water pump
cooling
Ignition
valve
011
finS
piston
rings
or
cylinder
stem
0
connections
Ignition
valves
piston
piston
Improperly
pipe
pump
coolant
thermostat
used
or
1
or
beanngs
rod
rod
CAUSE
clearance Adjust
leaking
broken
worn
set
limIng
plugs
defective
Jet
or
damaged
system
liming
clearance Adjust
Clean
Clean
clogged
rings
worn
gUide
worn
worn
or
sticking
In
Replace
Replace
Change
defective
battery
system Adjust
Chargeorreplace
Clean
RepairOrreplace
nngs
bearings
be
nngs
or
or
l
and
cylinders
Journals
worn
pinS
badly
worn
damaged
Overhaul
Replace
or
Replace
I
or
Stralgten
Check
ACTIOtJ
valve
clearance
Lap
valve
seats
set
up
valve
valve
piston
engine
re
set
or
replace
carburetor
fuel
pipe
fuel
tank
fuel
or
replace
radiator
fan
fan
thermostat
or
pump
belt
belt
Replace
Replace
Replace
Overhaul
Re
Clean
Clean
Clean
Check
Clean
Top
Adjust
Replace
Replace
Repairorreplace
Clean
system
Re
set
timing
clearance
Refill
With
readlator
leak
piston
Piston
piston
as
to
and
Ignition
enqlne
correct
and
necessary
proper
tighten
Clean
Fnd011
Replace
Replace
bearings
crankshaft
replace
bearings
crankshaft
replace
or
replace
and
replace
TOBETAKEN
andguIdes
spring
rings
renew
adjust
element
oil
grade
finS
rectify
rings
rll1gs
or
bore
VISCOSity
battery
connections
check
plugs
valves
and
grind
and
gnnd
rod
parts
gap
cylinder
as
crankshaft
crankshaft
necessary
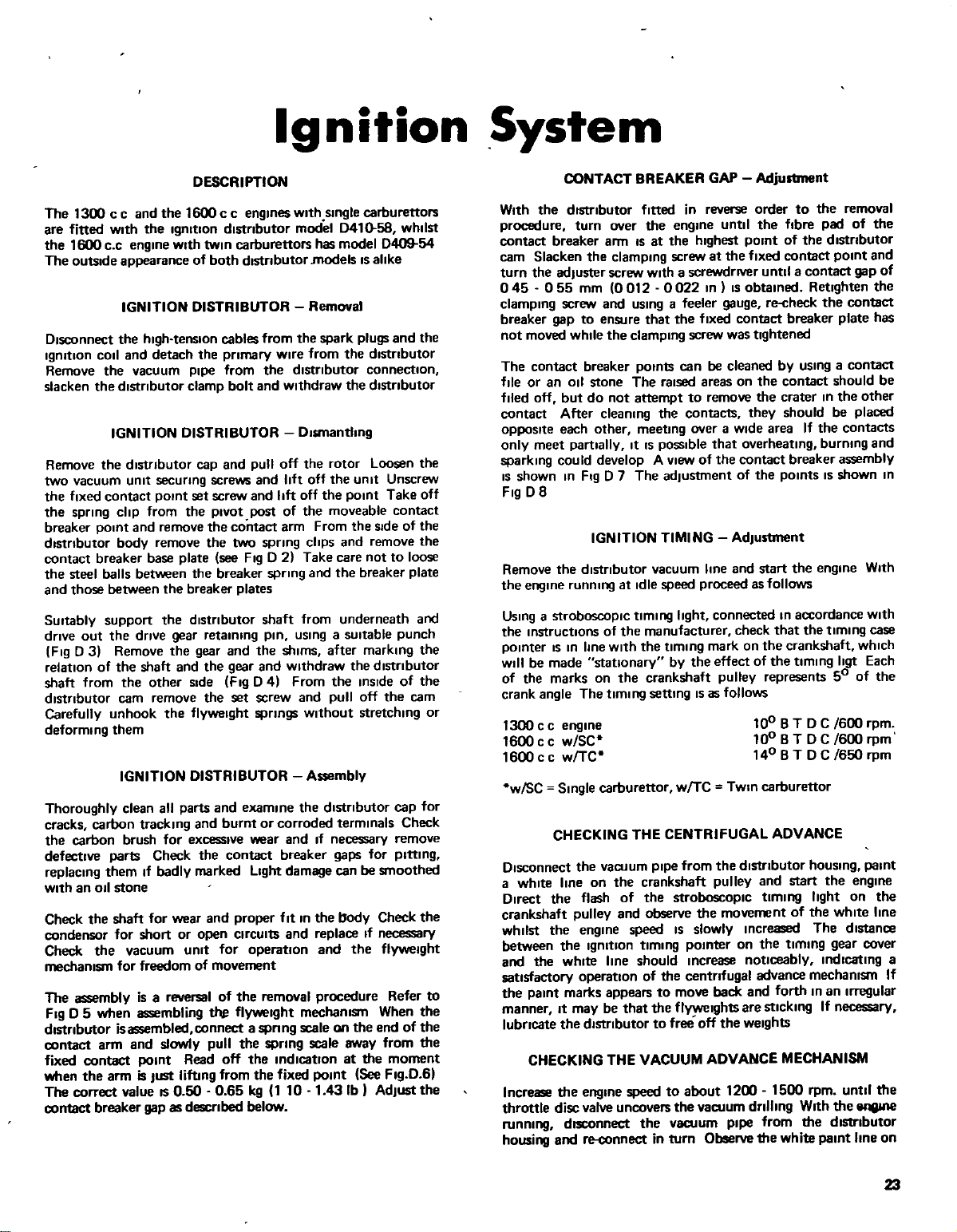
Ignition
System
The
1300
are
fitted
the
1600
The
outside
Disconnect
Ignition
Remove
slacken
Remove
vacuum
two
fixed
the
the
spring
breaker
distributor
contact
the
steel
and
those
SUitably
drive
out
D
3
Fig
relation
shaft
from the
distributor
Carefully
deforming
Thoroughly
cracks
carbon
the
carbon
defective
replaCing
an
With
Check
the
condensor
Check
mechamsm
The
assembly
D5when
Fig
distributor
contact
fixed
contact
when
the
The
correct
con1llct
c
c
With
c c
appearance
IGNITION
the
coli
the
distributor
the
IGNITION
the
contact
clip
pOint
body
breaker
balls
between
support
the
Remove
of
the
cam
unhook
them
IGNITION
clean
parts
them
stone
011
shaft
for
the
for
isassembled
arm
arm
valueIS0
breaker
and
the
the
engine
high
and
detach
vacuum
distributor
Unit
securing
POint
from the
remove
and
remove
base
between
the
drive
shaft
other
remove
all
tracking
brush
Check
If
badly
for
short
vacuum
freedom of
isareversal
assembling
and
slowly
POint
is
lust
gap
DESCRIPTION
1600
Ignition
With
of
DISTRIBUTOR
tension
pipe
clamp
DISTRIBUTOR
set
plate
the
breaker
the
distributor
gear
the
gear
and
Side
the
flyweight
DISTRIBUTOR
parts
and
for
excessive
marked
wear
or
Unit
connect
Read
lifting
50065
described
as
twin
both
the
cap
screws
screw
piVOt
the
the
retaining
the
the
and
the
and
open
movement
thJ
pull
c c
engines
distributor
carburettors
distributor
cables
primary
from the
bolt
and
contact
two
see
Fig
breaker
plates
and
gear
Fig
set
examine
burnt
contact
proper
circuits
for
operation
of
the
flyweight
a
the
off
the
from the
below
from
wire
and
withdraw
off
pull
and
11ft
and
11ft
of
post
arm
spring
D2Take
spring
shaft
pin
the
sI1Ims
and
Withdraw
D4From
screw
springs
or
corroded
wear
and
breaker
Light
damage
f
It
and
removal
spring
spring
indication
fixed
10143
kg
1
With
Single
D410
model
has
model
modelsISalike
Removal
the
spark
from the
distributor
Dlsmanthng
the
rotor
off
the
off
the
moveable
the
From
and
clips
care
and
the
underneath
from
a
uSing
after
the
and
pull
Without
Assembly
the
distributor
terminals
If
necessary
gaps
can
In
the
body
replace
and
procedure
mechamsm
scaleonthe
scale
at
POint
carburettors
58
D400
plugs
distributor
connection
the
distributor
Loosen
Unit
Unscrew
Take
pOint
the
Sideofthe
remove
not
to
breaker
SUitable
marking
the
distributor
InSideofthe
off
the
stretching
for
smoothed
be
Check
If
necessary
the
flyweight
Refer
When
endofthe
from the
lIWay
the
moment
See
FIgD
Ib
Adjust
whilst
and
contact
punch
cap
Check
remove
pitting
loose
plate
and
cam
54
the
the
the
the
the
off
the
the
CONTACT
With
the
distributor fitted
procedure
contact
earn
turn
045 055
clamping
breaker
not
moved
The
file
filed
contact
opposite
only
sparking
IS
shown
D8
Fig
Remove
the
engine
USing
the
pOinter
Will
of
the marks
crank
or
for
to
1300
1600
1600
wlSC
Disconnect
a white
Direct
crankshaft
whilst
between
and
satisfactory
the
manner
lubricate the
breaker
Slacken
the
adjuster
screw
gap
contact
or
an
off
but do
After
each
meet
could
In
the
a
stroboscopIC
instructIOns
IS
be made
angle
c c
engine
c c
w
c c
Single
CHECKING
line
the
the
the
white
the
marks
paint
It
CHECKING
turn
the
mm
to
while
breaker
011
partially
Fig
distributor
running
In
line With
The
SC
w
TC
the
flash
pulley
engine
operation
may
distributor
over
ann
clamping
screw
0012
and
ensure
the
stone
not
cleaning
other
develop
D7The
IGNITION
of
statIOnary
on
tlml
carburettor
vaaJum
on
the
IgnitIOn
line
appears
be
THE
BREAKER
the
IS
at
Withascrewdriver
uSing
that the
clamping
POints
The
attempt
the
meeting
It
IS
pOSSible
A
vacuum
at
Idle
tlml
ng
manufacturer
the
the
the
crankshaft
ng
setting
THE
pipe
crankshaft
of
the
and
observe
speed
timing
should
of
to
that the
to
VACUUM
GAP
in
reverse
engine
the
highest
at
screw
In
0022
a
feeler
fixed
screw
can
be
raised
areas
remove
to
contacts
over
that
View
of
adjustment
TIMING
line
proceed
speed
connected
light
mark
timing
the effect
by
IS
as
w
TC
CENTRIFUGAL
from the
stroboscopiC
the
IS
slowly
pOinter
Increase
the
centrifugal
move
flyweights
off
free
ADVANCE
Adjultment
order
until
the
POint
the
fixed
IS
obtained
gauge
contact
was
tightened
cleaned
on
the
the
they
a
Wide
overheating
contact
the
of
the
Adjultment
and
start
as
check
on
of
pulley
follows
100
1008
1408TDC
TWin
distributor
and
pulley
movement
Increased
on
the
noticeably
advance
back
and
are
the
weights
the
to
fibre
pad
of
the
contact
untilacontact
Retighten
rlH
heck
the
breaker
by
uSing
contact
crater
In
should
area
If
the
burning
breaker
pOints
the
In
accordance
that the
crankshaft
the
timing
T
8TD C
ADVANCE
engine
DC
follows
the
represents
carburettor
hOUSing
start
timing
light
of
the white
The distance
timing
Incheatlng
mechanism
forth
In
sticking
If
MECHANISM
removal
distributor
pOint
contact
plate
a
contact
should
the
be
contacts
assembly
IS
shown
timing
IIgt
50
1600
1600
650rpm
the
on
gear
an
Irregular
necessary
of
and
gap
other
placed
With
With
case
which
Each
of
rpm
rpm
paint
engine
cover
the
of
the
has
be
and
In
the
the
line
a
If
61
Increase
throttle
running
housing
the
engine
disc
valve
dISCOnnect
and
re
connect
speed
uncovers
the
1200 1500
about
to
the
vacuum
vacuum
in
turn
pipe
Observe
drllhng
from the
the white
rpm
With the
distributor
paint
until
8Q8IIIll
hne
the
on
23
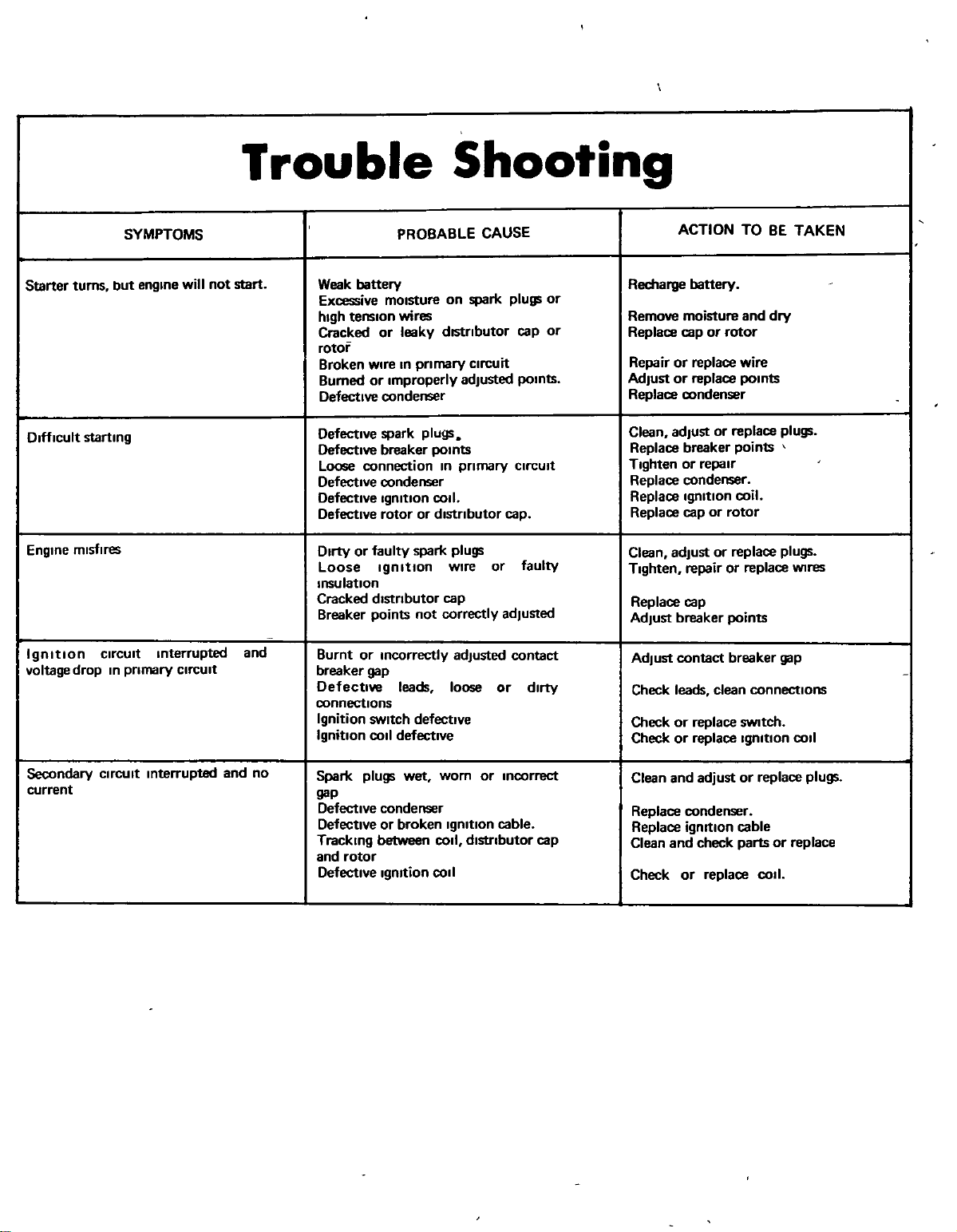
Trouble
Shooting
Starter
Difficult
Engine
Ignition
voltage
turns
starting
misfires
drop
SYMPTOMS
but
CirCUit
In
pnmary
engine
Interrupted
will
CircUit
ACTION
battery
moisture
cap
or
on
spark plugs
dlStnbutor
CAUSE
cap
or
or
Recharge
Remove
Replace
PROBABLE
not
start
Weak
Excessive
tension
high
Cracked
battery
mOisture
or
wires
leaky
rotor
TO
and
BE
dry
TAKEN
rotor
and
Broken
Burned
Defective
Defective
Defective
Loose
Defective
Defective
Defective
Dirty
Loose
Insulation
Cracked
Breaker
Burnt
breaker
Defective
connections
Ignition
Ignition
wire
or
spark
breaker
connection
condenser
Ignition
rotor
or
faulty
Ignition
dlstnbutor
points
or
Incorrectly
gap
SWitch
COil
In
pnmary
Improperly
condenser
plugs
or
spark
not
leads
defective
defective
points
In
COil
dlstnbutor
plugs
wire
cap
correctly
adjusted
loose
CircUit
adjusted
pnmary
or
points
CircUit
cap
faulty
adjusted
contact
or
dirty
Repairorreplace
Adjustorreplace
Replace
Clean
Replace
Tighten
Replace
Replace
Replace
Clean
Tighten
Replace
AdjUst
AdjUst
Check leads clean
Check
Check
condenser
adjUstorreplace
breaker
or
condenser
Ignition
cap
adjUst
repair
cap
breaker
contact
or
or
repair
or
or
replace
replace
wire
points
points
coil
rotor
replace
or
replace
points
breaker
SWItch
IgnitIOn
plugs
plugs
Wires
gap
connections
COil
Secondary
current
circuit
Interrupted
and
no
Spark
gap
Defective
Defective
Tracking
and
rotor
Defective
plugs
condenser
or
between
Ignition
wet
broken
worn
COil
COil
Ignition
distributor
or
inCOrrect
cable
cap
Clean and
Replace
Replace
Clean and
Check
adjustorreplace
condenser
ignition
or
check
replace
cable
parts
COIl
or
plugs
replace
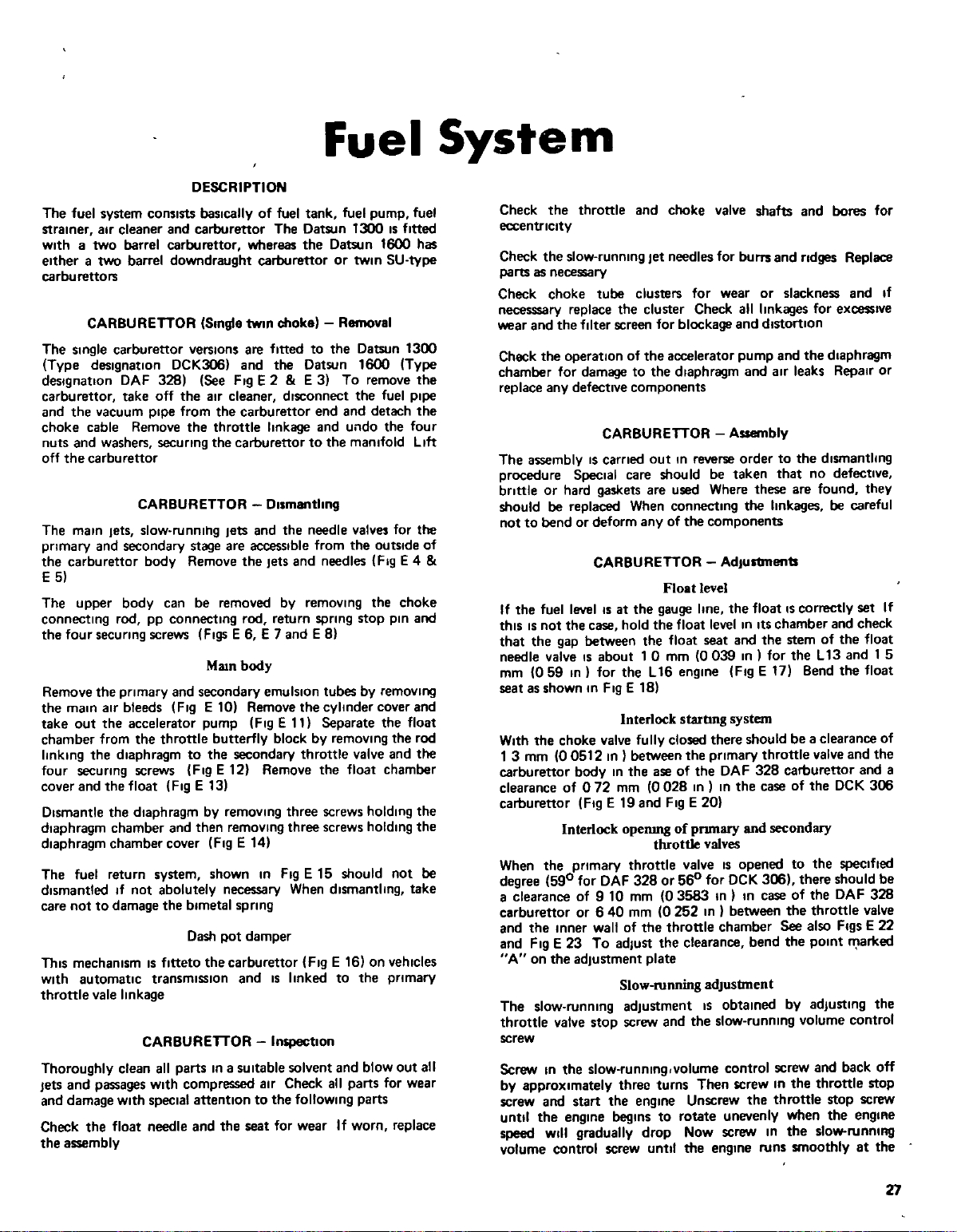
The
fuel
strainer
with
a
two
either
a
carburettors
CARBURETTOR
The
single
Type
designation
deSignation
carburettor
and
the
choke
cable
nuts
and
off
the
carburettor
The
main
pnmary
the
carburettor
E
5
The
upper
connecting
the
four
Remove
the
main air
take
out
chamber
the
linking
four
securing
cover
and
Dismantle
diaphragm
diaphragm
The
fuel
dismantled
care
not
This
mechanISm
With
automatic
throttle
vale
Thoroughly
and
Jets
and
damage
Check
the
the
assembly
system
air
cleaner
barrel
two
carburettor
OAF
take
vacuum
washers
Jets
and
secondary
body
rod
secunng
the
pnmary
bleeds
the
from the
diaphragm
the
the
chamber
chamber
return
If
to
damage
linkage
clean
passages
With
float
consists
and
carbu
barrel
downdraught
DCK306
328
off
pipe
Remove
securing
CARBURETTOR
slow
runnlhg
body
can
connecting
pp
screws
and
Fig
accelerator
throttle
screws
float
Fig
diaphragm
and
cover
system
not
abolutely
the
IS
fltteto
transmission
CARBURETTOR
all
parts
With
special
needle
DESCRIPTION
basically
carburettor
rettor
Single
versions
See
the
air
cleaner disconnect
from the
the
throttle
the
Jets
are
stage
Remove
removed
be
E6E 7
Figs
Mam
secondary
10
E
pump
butterfly
to
the
E
12
Fig
E
13
by
removing
then
removing
Fig
shown
necessary
bimetal
Dash
pot
thecarburettor
Inasu
compressed
attention
the
and
of
fuel
The
whereas
carburettor
choke
tWin
are
fitted
the
and
E
2
Fig
carburettor
linkage
carburettor
Dismantling
and
accessible
the
Jets
rod
return
body
emulSion
Remove
E
F
Ig
block
secondary
Remove
E
14
In
spring
damper
IS
and
Inspection
Itable solvent
air
to
the
seat
for
tank
Datsun
the
Datsun
E3To
to
the
needle
and
by
removing
andE8
the
11
throttle
three
three
E15should
Fig
When
Fig
linked
Check
follOWing
wear
Fuel
fuel
1300ISfitted
Datsun1600
or
twin
Removal
to
the
the
end and
and
undo
the manifold
valves
from the
needles
spring
tubes
cylinder
Separate
by
removing
valve
the
float
screws
screws
dismantling
E
16
to
and
all
parts
If
worn
pump
SU
Datsun
1600
remove
fuel
detach
the
outside
Fig
the choke
stop
removing
by
cover
the
chamber
holding
holding
on
the
blowout
for
parts
fuel
type
1300
Type
pipe
four
for
E
4
pin
float
the
and
not
take
vehicles
pnmary
wear
replace
System
Check
eccentriCity
has
the
the
Lift
the
of
and
and
rod
the
the
the
be
all
Check
parts
Check
necesssary
wear
Check
chamber
replace
The
procedure
brittle
should
not
to
If
the
thiS
that the
needle
mm
seat
With
1
3
carburettor
clearance
carburettor
When
degree
a
clearance
carburettor
and
and
A
The
throttle
screw
Screw
by approximately
screw
until
speed
volume
throttle
the
the
slow
as
choke
running
necessary
tube
replace
the
any
the
operation
for
defective
filter
damage
CARBURETTOR
IS
carned
and
assembly
Special
or
hard
replaced
level
the
gap
In
choke
00512
gaskets
CARBURETTOR
IS
case
between
for
In
valve
be
bendordeform
fuel
IS
not
valveISabout10
059
as
shown
the
mm
body
of 072
Fig
Interlock
the
pnmary
for
of
or
Inner
23
E
adjustment
running
valve
the
start
engine
gradually
control
OAF
9 10
6
wall
To
stop
slow
the
Fig
on
590
the
slow
In
and
the
Will
and
clusters
the
screen
of
to
components
care
When
at the
hold
the
E
Fig
Interlock
fu
In
between
In
the
mm
E19and
opemng
throttle
328
mm
40
mm
of
adjUst
Slow
adjustment
screw
runnlng
three
the
engine
beginS
screw
Jet
cluster
for
the
the
outIn
should
are
any
gauge
the
the
L16
18
lIy
ase
0028
throttle
or
the
the
plate
roORing
turns
to
drop
until
choke
needles
for
Check
blockage
accelerator
diaphragm
reverse
used
connecting
of
the
Float
float
float
mm
engine
startJng
closed
the
of
the
In In
E
Fig
of
prunary
valve
560
03583
252
0
throttle
clearance
and
the
volume
Then
Unscrew
rotate
Now
the
valve
for
burrs
wear
all
and
pump
Assembly
order
be
taken that
Where
components
Adjustments
level
line
the
In
level
and
seat
0039
In
Fig
system
there
pnmary
OAF
the
20
valves
IS
opened
for
DCK
In In
In
between
chamber
adjustment
IS
obtained
slow
control
screw
unevenly
screw
engine
shafts
or
linkages
and
these
the
float
ItS
E
should
328
case
and
bend
running
the
runs
and
slackness
distortion
and
air
leaks
to
the
are
linkages
IS
correctly
chamber
the
stem
for
the
17
be
throttle
carburettor
of
secondary
to
306
there
case
of
the
See
the
by
screw
In
the
throttle
when
In
the
smoothly
and
ndges
for
the
diaphragm
dismantling
no
found
of
L13
Bend
a
clearance
valve
the
the
the
throttle
also
pOint
adjusting
volume
and
throttle
stop
the
slow
bores
Replace
and
excessive
Repair
defective
be
careful
set If
and
check
the
and15
the
and
and
DCK
speCified
should
OAF
Figs
marked
control
back
screw
englfle
running
at
they
float
float
the
306
328
valve
E
stop
for
If
or
of
a
be
22
the
off
the
D