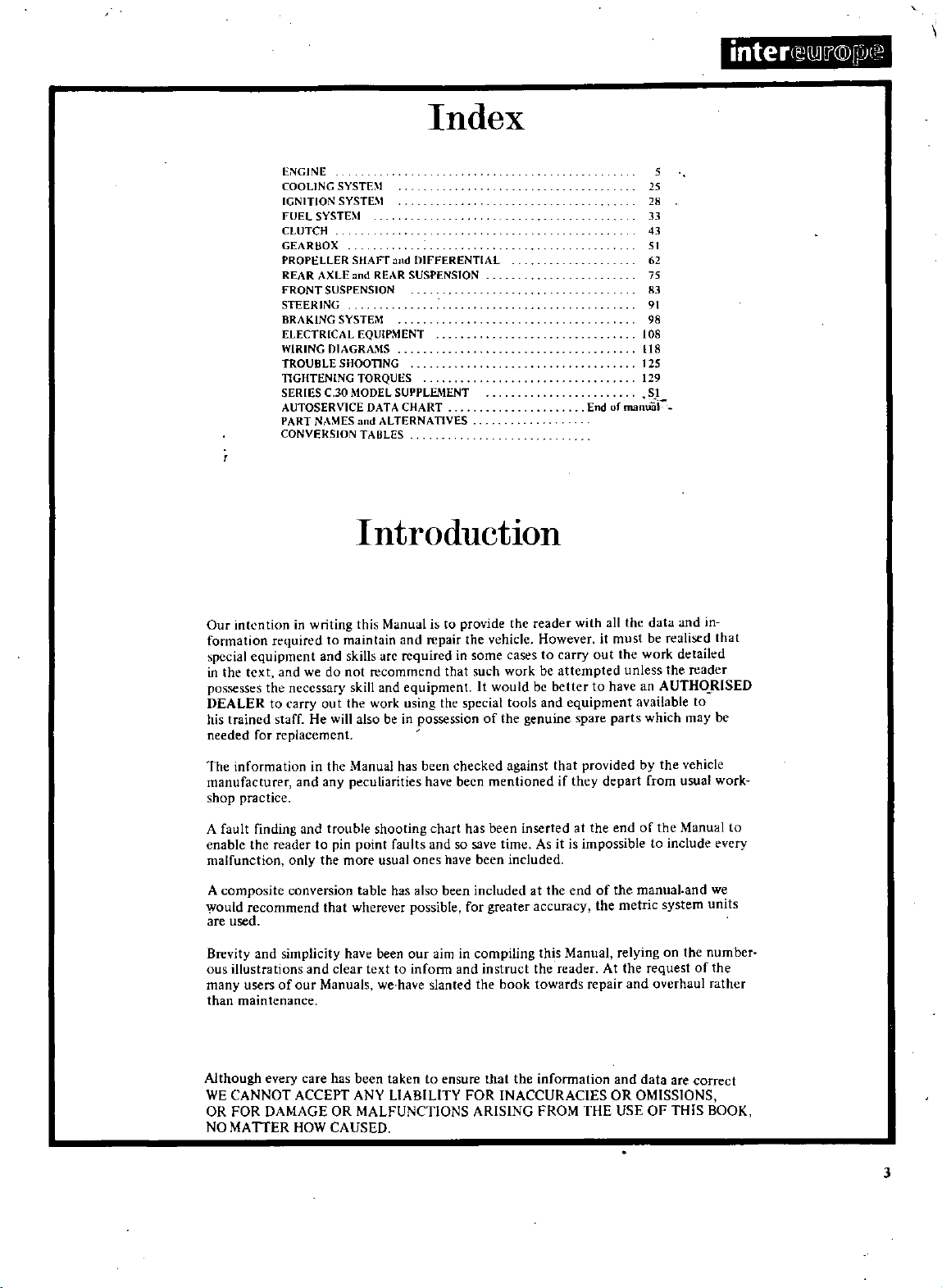
Index
inteN
j
@IP
B
OUf
intention
formation
special
in
the
text
possesses
DEALER
his
trained
needed
The
information
manufacturer
practice
shop
A
fault
enable
malfunction
A
composite
recommend
would
are
used
ENGINE
COOLING
IGNITION
FUEL
CLUTCH
GEARUOX
PROPELLER
REAR
FRONT
STEERING
BRAKING
ELECTRICAL
WIRING
TROUBLE
TIGHTENING
SERIES C30MODEL
AUTOSERVlCE
PART
CONVERSION
in
required
equipment
andwedo
the
necessary
to
carry
staff
for
replacement
and
and
finding
the
reader
only
conversion
l
SYSTE
SYSTE
SHAFT
nd
SYSTEM
I
REAR
SYSTBl
AXLE
SUSPENSION
EQUIP
JAGRA
IS
SHOOTING
TORQUES
NA
DATA
ESndALTERNATIVES
TABLES
IntroductIon
Manual
this
writing
to
maintain
and
skills
arc
not
recommend
skill
and
the
out
will
the
any
trouble
pin
the
that
work
alsobein
Manual
peculiarities
shooting
point
more
usual
table
wherever
He
in
to
Id
DIFFERENTIAL
SUSPENSION
JENT
SUPPLEMENT
CHART
and
repair
required
equipment
using
possession
has
been
have
faults
and
ones
has
also
possible
is
chart
to
that
the
have
been
provide
the
in
some
such
It
special
checked
been
has
so save
been
included
for
vehicle
caseS
work
would
tools
the
of
against
mentioned
been
time
included
greater
the
End
with
reader
However
to
carry
be
attempted
be
bettertohave
and
equipment
genuine
that
if
spare
provided
they
insertedatthe
it
is
As
impossible
at
the
end
accuracy
of
all
it
must
out
parts
depart
endofthe
of
the
the
manuir
the
the
unless
metric
15
2S
33
43
51
62
7S
83
91
9S
lOB
liB
I2S
129
51
data
be
work
an
available
which
by
manual
S
and
in
realised
that
detailed
the
reader
AUTHQRISED
to
be
may
the
vehicle
usual
rom
to
system
Manual
include
and
work
every
we
units
to
Brevity
ous
illustrations
many
than
Although
WE
CANNOT
OR
FOR
NO
MATTER
and
simplicity
users
of
maintenance
every
DAMAGE
and clear
our
Manuals
care
ACCEPT
HOW
have
text
has
been
ANY
OR
MALFUNCTIONS
CAUSED
been
to inform
we
taken
LIABILITY
have
our
aim
slanted
to
ensure
in
and
FOR
ARISING
compiling
instruct
the
that
this
the
the
reader
towards
information
book
INACCURACIES
FROM
Manual
At
repair
OR
THE USE
relying
the
and
and
OMISSIONS
request
overhaul
data
OF
on
are
THIS
the
number
of
rather
correct
BOOK
the
I
3
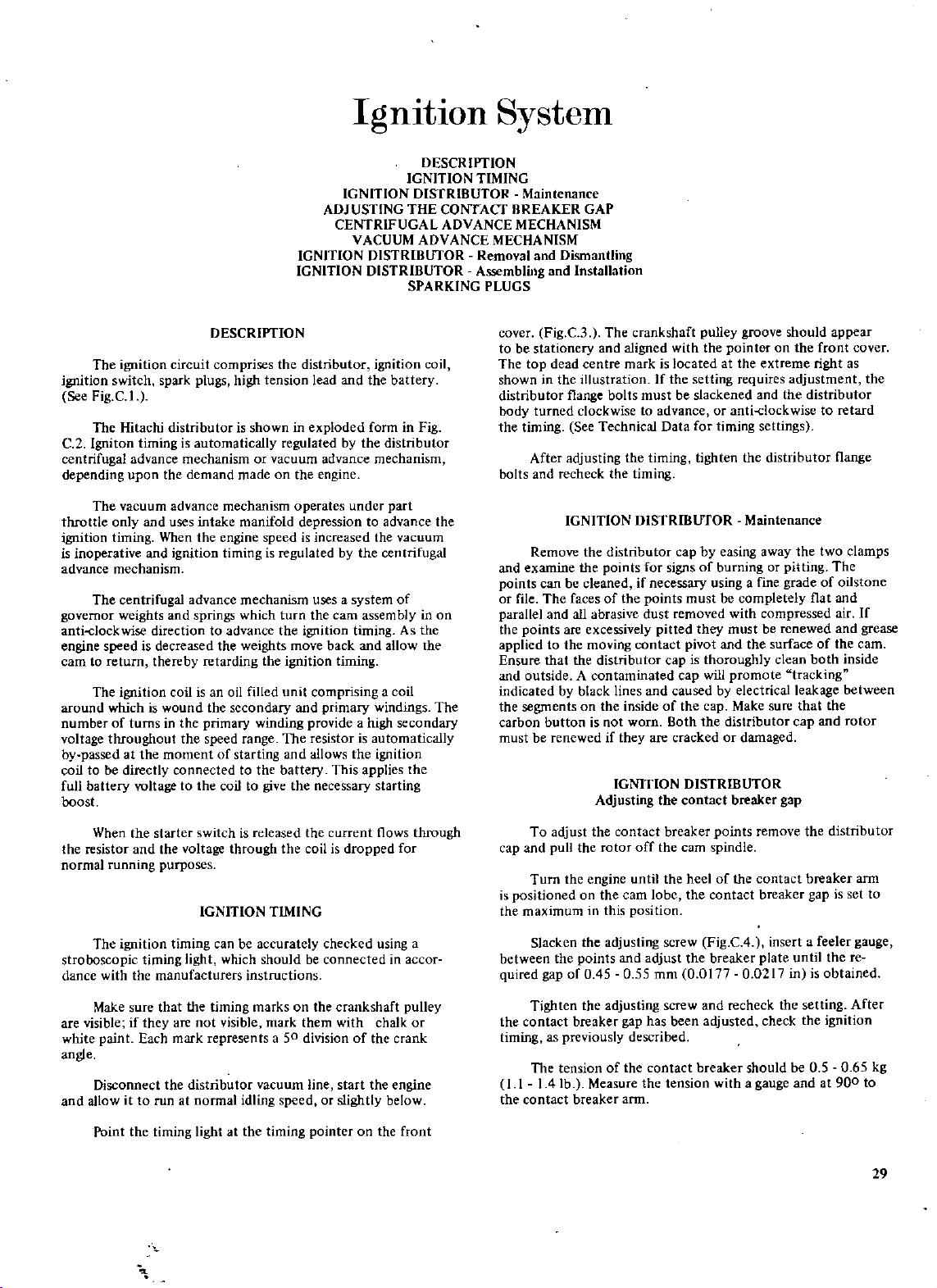
The
ignition
See
Fig
The
2
C
19niton
centrifugal
depending
The
throttle
ignition
is
inoperative
advance
The
governor
anti
clockwise
engine
speed
cam
to
return
The
around
whichiswound
number of
voltage
throughout
by
passed
coiltobe
full
battery
boost
When
the
resistor
normal
running
ignition
switch
1
C
Hitachi
timing
advance
upon
vacuum
and
only
timing
and
mechanism
centrifugal
weights
is
ignition
turns
at
the
directly
voltage
the
and
DESCRII
TION
circuit
spark
distributor
is
the
advance
uses
When
comprises
plugs
automatically
mechanism
demand
intake
the
high
is
shown
or
made
mechanism
manifold
engine
tension
vacuum
speed
ignition timingisregulated
and
direction
decreased
thereby
coil
in
the
the
moment
connected
to
starter
the
purposes
advance
voltage
mechanism
which
springs
to
advance
the
weights
retarding
isanoil
the
the
filled
secondary
primary winding
speed
range
of
starting
to
coil
the
to
give
the
switchisreleased
through
IGNITION
TIMING
ADJUSTING THE
IGNITION
IGNITION
the
distributor
lead
in
exploded
regulated
advance
on
the
engine
operates
depression
is
increased
uses
turn
the
the
ignition
move
back
ignition timing
unit
comprising
and
primary
provideahigh
The
resistor
and
allows
the
necessary
the
coil
This
current
is
battery
the
IgnItIon
IGNITION
CENTRIFUGAL
VACUUM
and
by
under part
by
a
system
carn
timing
the
dropped
IGNITION
DISTRIBUTOR
ADVANCE
DISTRIBUTOR
DISTRIBUTOR
SPARKING
ignition
the
battery
form
in
the
distributor
mechanism
to
advance
the
vacuum
the
centrifugal
of
assembly
As
and
allow
a
coil
windings
secondary
is automatically
ignition
the
applies
staTting
flows
through
for
coil
Fig
in
the
the
CONTACT
ADVANCE
the
on
The
System
DESCRII
TION
TIMING
Maintenance
BREAKER
MECHANISM
MECHANISM
Removal
Assembling
PLUGS
cover
to
be
The
top
showninthe
distributor
body
the
timing
bolts
examine
and
points
or
file
parallel
the
points
applied
Ensure
and
outside
indicated
the
segments
carbon
must
and
cap
is
positioned
the
maximum
and
and
Fig
stationery
dead
turned
After
and
Remove
can
The
and
to
that
button
be
renewed
To
pull
Turn
GAP
Dismantling
Installation
C3The
centre
illustration
flange
clockwise
See
adjusting
recheck
IGNITION
the
the
be
cleaned
faces
all
are
excessively
the
moving
the
A
black
by
on
is
adjust
the
the
engine
on
in
crankshaft
and
aligned
markislocated
bolts
Technical
the
the
timing
DISTRIBUTOR
distributor
points
if
the
of
abrasive
contact
distributor
contaminated
lines
the
insideofthe
not
worn
if
they
IGNITION
Adjusting
the
contact
off
rotor
until
cam
the
this
position
groove
pulley
with
the
pointer
at
the
If
the
setting
must
be
to
advance
Data
timing
cap
for
signsofburningorpitting
necessary
must
points
removed
dust
pitted
pivot
cap
cap
and
causedbyelectrical
Both
are
cracked
DISTRIBUTOR
contact
the
breaker
the
cam
the
heelofthe
lobe
the
slackened
or
for
timing
tighten
by
using
they
is
thoroughly
will
cap
the
points
spindle
contact
requires
the
Maintenance
easing
a
be
completely
with
must
and
the
promote
Make
distributor
or
damaged
breaker
should
on
the
extreme
adjustment
and
the
anti
clockwise
settings
distributor
away
fine
grade
compressed
renewed
be
surface
clean
tracking
leakage
sure
cap
gap
remove
contact
breaker
right
distributor
the
flat
both
that
the
breaker
gap
appear
front
to
flange
two
The
of
and
air
and
of
the
the
and
distributor
is
cover
as
retard
clamps
oilstone
inside
between
rotor
arm
set
the
If
grease
cam
to
The
stroboscopic
dance
with
Make
are
visible
white
paint
angle
Disconnect
allow
and
Point
ignition timing
timing
manufacturers
that
they
Each
the
to
run
timing
light
the
are not
mark
distributor
at
the
sure
if
it
the
can
which
timing
visible
represents
normal
light
be
idling
at
the
accurately
should
instructions
marks
on
mark
a
50
vacuum
speedorslightly
timing
be
the
them
division
line
pointer
checked
connected
crankshaft
with
of
start
a
using
in
accor
pulley
chalk
or
the
crank
the
engine
below
on
the
front
between
quired
the
contact
timing
II4
I
contact
the
Slacken
the
gap
Tighten
as
The
the
points
of045 0
the
breaker
previously
tension
lb
Measure
breaker
adjusting
adjusting
of
and
55
gap
described
the
arm
adjust
mm
has
contact
the
screw
the
0
screw
been
breaker should
tension
Fig
breaker
017700217
and
adjusted
with
CA
recheck
a
insertafeeler
until
plate
in
the
setting
the
check
be 050 65
andat900
gauge
is
the
obtained
ignition
gauge
re
After
kg
to
29