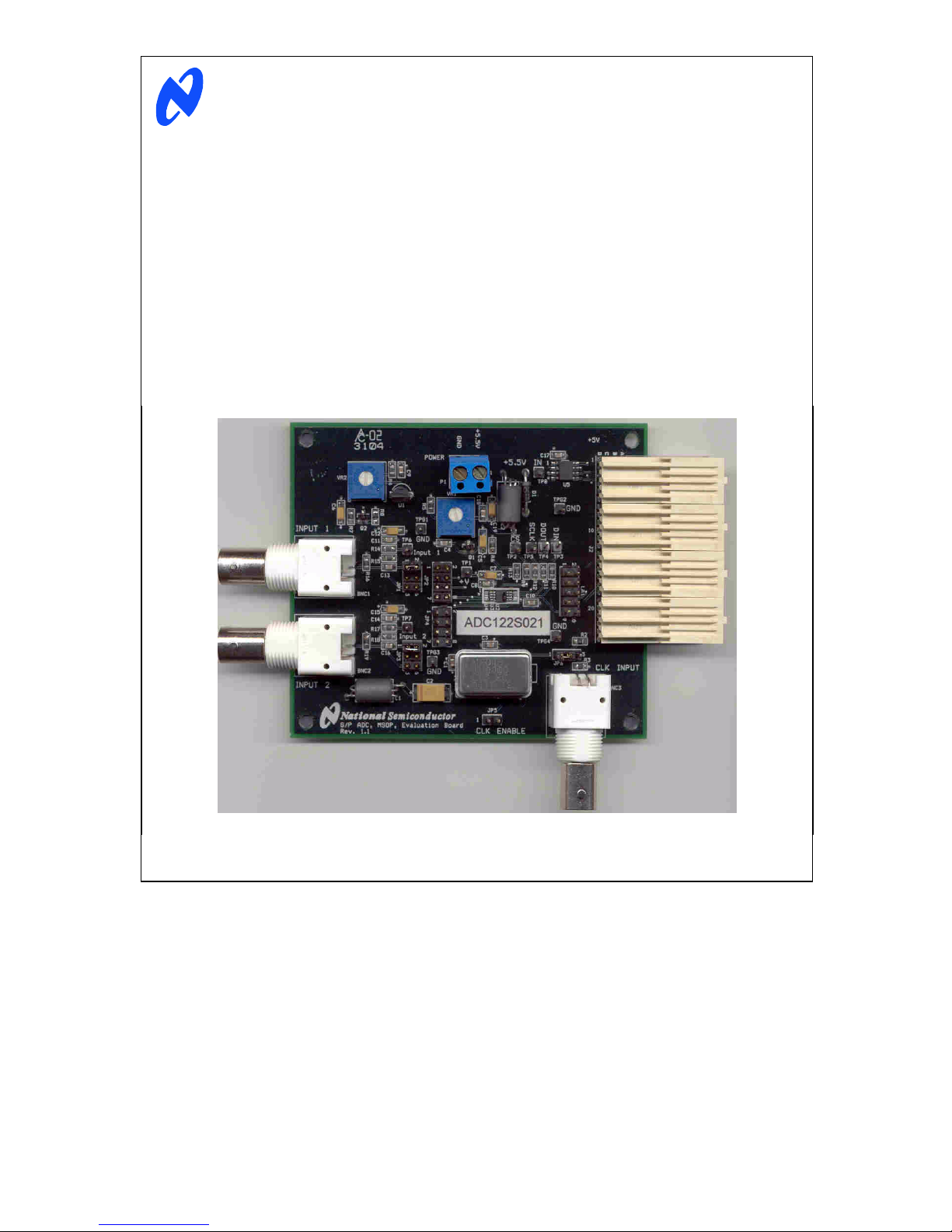
National Semiconductor
Evaluation Board User's Guide
12-, 10- and 8-Bit General Purpose
Analog-to-Digital Converters with Input Multiplexer
ADC122S101 / ADC102S101 / ADC082S101
ADC122S051 / ADC102S051 / ADC082S051
ADC122S021 / ADC102S021 / ADC082S021
ADC124S101 / ADC104S101 / ADC084S101
ADC124S051 / ADC104S051 / ADC084S051
ADC124S021 / ADC104S021 / ADC084S021
August 2005
Rev -
© 2005 National Semiconductor Corporation.
1 http://www.national.com

Table of Contents
1.0 Introduction.............................................................................................................................3
2.0 Board Assembly .....................................................................................................................3
3.0 Quick Start..............................................................................................................................3
4.0 Functional Description............................................................................................................4
4.1 Input (signal conditioning) circuitry............................................................................4
4.2 The ADC reference ...................................................................................................4
4.3 ADC clock circuit .......................................................................................................4
4.5 Digital Data Output....................................................................................................4
4.6 Power Supply Connections .......................................................................................4
4.7 Power Requirements.................................................................................................5
4.8 Analog Inputs ............................................................................................................5
5.0 Installing and Using the ADCxx1S101 Evaluation Board .......................................................5
5.1 Software Installation..................................................................................................5
5.2 Setting up the ADCxx1S101 Evaluation Board .........................................................5
5.2.1 Board Set-up .............................................................................................5
5.2.2 Quick Check of Analog Functions.............................................................5
5.2.3 Quick Check of Software and Computer Interface Operation...................5
5.2.4 Getting Consistent Readings.....................................................................6
5.2.5 Troubleshooting.........................................................................................6
6.0 Evaluation Board Specifications.............................................................................................6
7.0 Hardware Schematic..............................................................................................................7
8.0 ADCxx1S101 Evaluation Board Bill of Materials ....................................................................8
A1 Summary Tables of Test Points and Connectors ...................................................................9
2 http://www.national.com
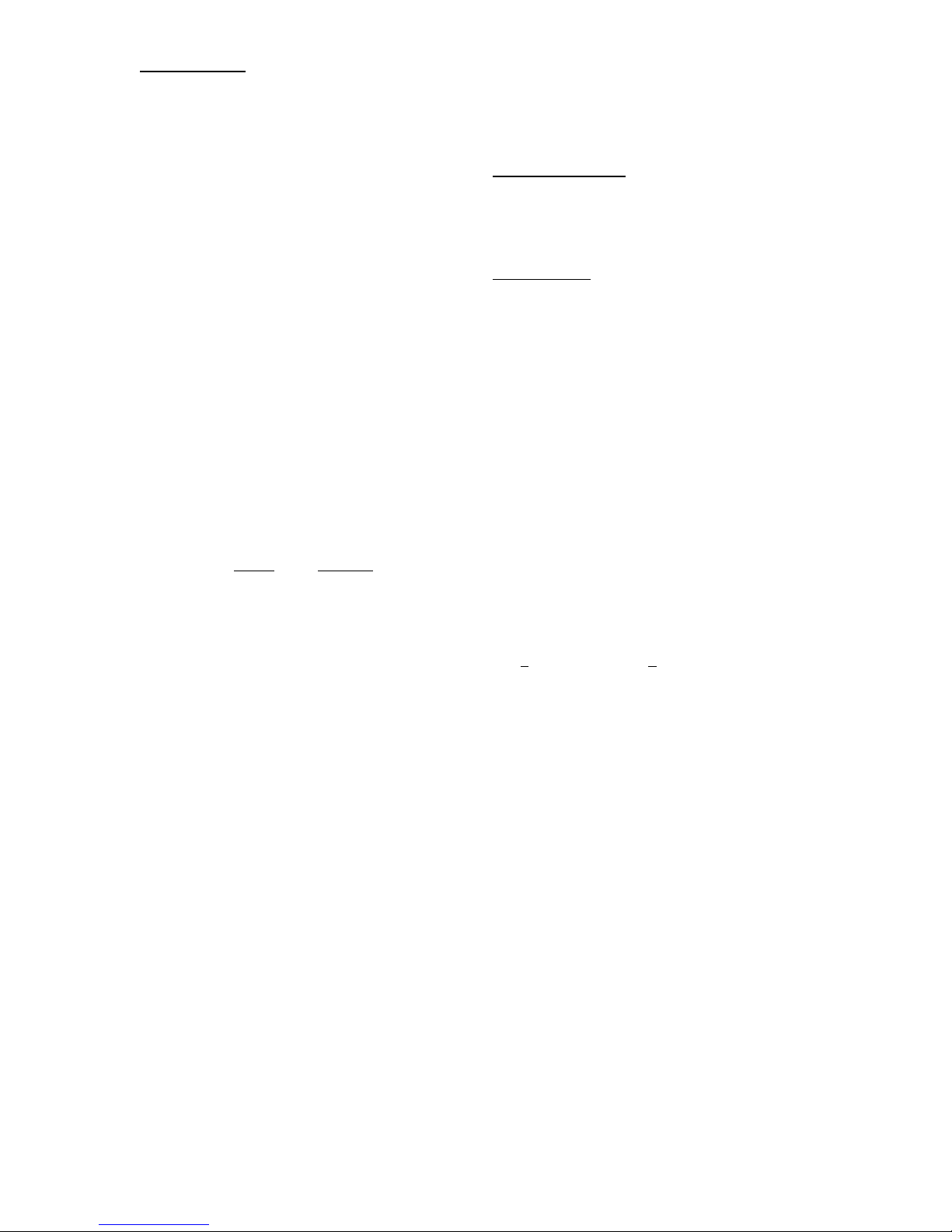
1.0 Introduction
These ADC Design Kits (consisting of one of these
evaluation boards: ADC12xS101, ADC10xS101,
ADC08xS101, ADC12xS051, ADC10xS051,
ADC08xS051, ADC12xS021, ADC10xS021,
ADC08xS021 and WaveVision4 hardware, where "x" in
the device types here could be a 2 or a 4, indicating the
number of multiplexer inputs) is designed to ease
evaluation and design-in of these National
Semiconductor Analog-to-Digital Converters. These
evaluation boards allow the desivgner to evaluate product
performance in a choice of two ways: in standalone mode
with a logic analyzer and appropriate software (including
National's WaveVision software), or with a personal
computer and WaveVision4 hardware and software.
Reference in this Guide to DUT is meant to refer to the
particular device for which you have the evaluation board.
For operation with a computer system, this evaluation
board should be coupled to a WaveVision4 data capture
board (National part number WAVEVSN BRD 4.0) using
the WaveVision software operating under Microsoft
Windows. The analog signal presented to the DUT is
captured by the WaveVision4 data capture board, and
displayed on the computer screen as a dynamic
waveform, FFT, and/or histogram. The software also
computes and displays dynamic performance in the form
of SNR, SINAD, THD, SFDR, and ENOB.
Important Note: The evaluation boards for all of these ADCs
look identical. The actual device placed on your evaluation
board can be identified by the label on the board and verified
by looking at the DUT (Device Under Test) top mark. The
devices have the following top marks:
Device Top Mark
ADC082S101 X22C
ADC082S051 X04C
ADC082S021 X16C
ADC084S101 X25C
ADC084S051 X10C 8. Run the WaveVision 4 software and click on
ADC084S021 X19C
ADC102S101 X23C
ADC102S051 X05C
ADC102S021 X17C
ADC104S101 X26C
ADC104S051 X11C
ADC104S021 X20C
ADC122S101 X24C
ADC122S051 X06C
ADC122S021 X18C
ADC124S101 X27C
ADC124S051 X12C
ADC124S021 X21C
The signal at the Analog Input to the board is digitized
and is available at FutureBus connector J2.
The board inputs are provided at BNC1 and BNC2.
Jumper headers JP1 and JP3 allow these inputs to be
either a.c. or d.c. coupled to the DUT. Provision is made
to adjust the DUT supply voltage (measured at TP1) with
potentiometer VR1.
VR2 is used to set the input offset.
2.0 Board Assembly
These Evaluation Boards come fully assembled and
ready to use. Refer to the Bill of Materials for a
description of components, to Figure 1 for major
component placement and to Figure 2 for the Evaluation
Board schematic.
3.0 Quick Start
Refer to Figure 1 for locations of test points and major
components.
1. Connect the evaluation board to the Capture Board
(order number WAVEVSN BRD 4.0). See the
Capture Board Manual for operation of that board.
2. Connect a clean power supply to the terminals of
connector P1. Adjust power supply to a voltage of
±5.5V to ±5.7V before connecting it to the board.
3. Connect a voltmeter to TP1 and use VR1 to set the
DUT analog supply voltage for the desired value
between +2.7V and +5.0V.
4. Set the jumper to short pins 1 and 2 of JP6 and be
sure there is a clock oscillator of the appropriate
frequency at Y1.
5. Put a jumper between pins 1 and 2 of JP1 and pins
1 and 2 of JP2.
6. Connect a signal, through an appropriate bandpass
filter, to BNC1. The peak-to-peak amplitude of this
signal at TP6 should be the same as or just under
the power supply voltage setting.
7. Connect a USB cable between the WaveVision
Capture Board and the PC.
Settings, then click on Capture. Under "Board Type"
select "WaveVision 4.0 (USB)".
9. Under "Communication" press the "Test" button. If
you get a "Communication Failed" message, check
all connections and be sure the power supply is on.
10. If the appropriate sample rate (not clock rate) is not
reported, check to be sure the clock signal has
adequate amplitude and repeat the previous step.
11. Click "Accept" then gather data by pressing F1 on
the keyboard. Perform an FFT on the data by
clicking on the FFT tab.
See the WaveVision Capture Board Manual for complete
data gathering instructions.
3 http://www.national.com
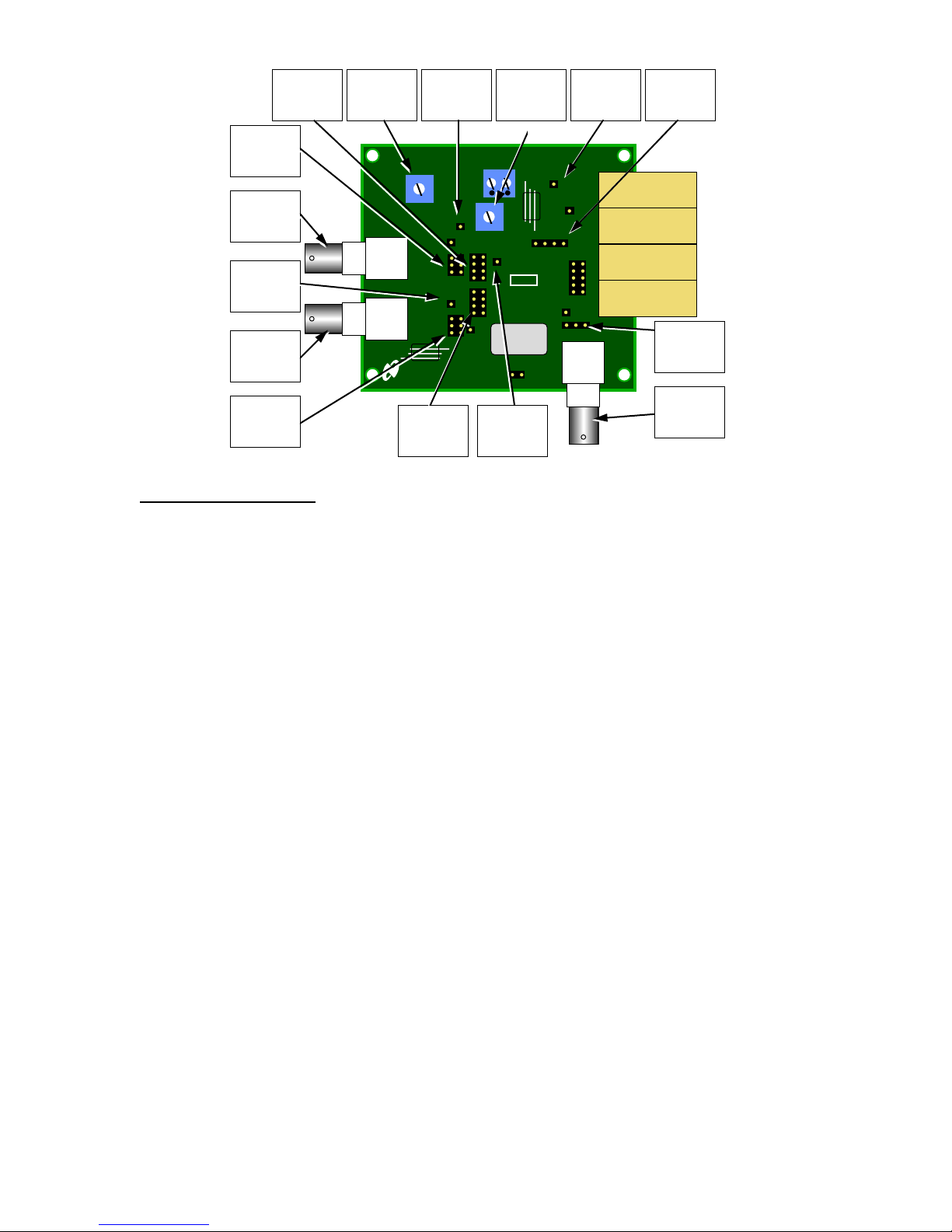
Input 1 Chan
JP1
INPUT 1
AC/DC Couple
BNC1
INPUT 1
Connection
JP2
Select
VR2
Offset
Adjust
INPUT 1
INPUT 1
Test Point
VR2
TP6
BNC1
TP7
INPUT 2
Test Point
BNC1
JP1
BNC2
JP3
BNC2
INPUT 2
Connection
JP3
INPUT 2
AC/DC Couple
BNC2
INPUT 2
National Semiconductor
G/P ADC, MSOP, Evaluation Board
Rev. 1.1
Input 1 Chan
L1
JP2
Select
Figure 1. Major Components and Test Points of the Evaluation Board
4.0 Functional Description
The Evaluation Board component locations are shown in
Figure 1. The board schematic is shown in Figure 2.
4.1 Input (signal conditioning) circuitry
The input signal to be digitized should be applied to BNC
connector BNC1 or to BNC2, or to both through (an)
appropriate filter(s). These 50 Ohm inputs are intended to
accept a low-noise sine wave signal of peak-to-peak
amplitude up to the power supply level. To accurately
evaluate the ADC dynamic performance, the input test
signal should be a single frequency passed through a
high-quality band pass filter as described in Section 5.0.
The input signal may be either a.c. or d.c. coupled to the
DUT with the setting of jumpers on J1 and JP3. See
schematic Figure 2.
4.2 The ADC reference
The reference voltage for the DUT is the device supply
voltage. Therefore, adjusting this voltage will change the
full scale range of the DUT. Since the operational supply
voltage range of the these ADCs is 2.7V to 5.25V, this is
also the range of the reference voltage.
TP6
TP7
Input2
TPG1
GND
POWER
Input1
JP2
JP4
TPG3
GND
P1
VR1
VA Supply
TP1
+V
U2, U3, U4
JP5
JP6
Clock
Select
VR1
Adjust
L2
TP2 TP5 TP4 TP3
Y1
+5.5V IN 1
TP8
TPG4
+5.5V Input
TPG2
GND
GND
JP6
BNC3
TP8
Test Point
J2
LA1
CLK INPUT
BNC3
TP2, TP3,
TP4, TP5
Serial Lines
Test Points
JP6
Clock
Select
BNC3
Ext. Clock
Connection
4.3 ADC Input Bias
To maximize ADC performance it is necessary that the
input signal swing cover nearly the entire ADC input
range. If the input biasing is not at the center of the signal
swing, it will not be possible to get maximum signal swing
without clipping of the signal, at which point there will be
excessive distortion.
VR2 is provided to allow adjustment of the input bias
point when a.c. input coupling is used. VR2 should be
adjusted to provide a d.c. voltage at TP6 and TP7 that
are one half the DUT supply voltage at TP1.
4.4 ADC clock circuit
The clock signal applied to the ADC can come from
BNC3 or from an on-board oscillator at position Y1 or Y2.
Y1 is for a through-hole TTL oscillator, while Y2 is for a
surface mounted TTL oscillator. Only one oscillator
should be mounted at a time and either an oscillator or
an external generator should be connected. JP6 is used
to select the oscillator source. Shorting pins 1 and 2 of
JP6 selects the on-board oscillator, while shorting pins 2
and 3 selects the oscillator signal at BNC3.
4 http://www.national.com