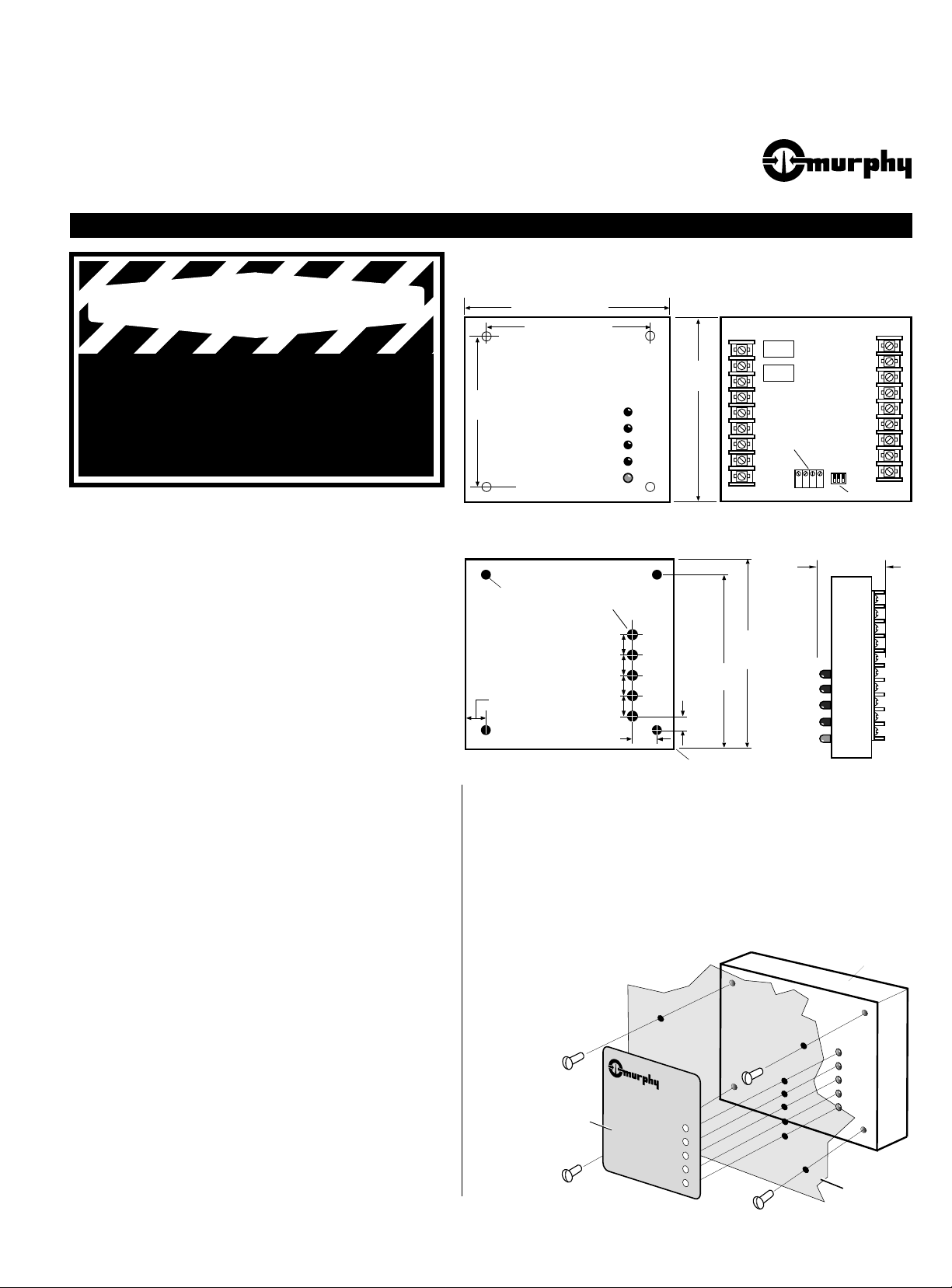
Description
The ASM160 is an engine controller with automatic start/stop, and selectable
warmup/cooldown or glowplug capabilities.
The ASM160 operates from a 12 or 24 volt battery. It includes crank and rest
cycles, sensing circuit for crank disconnect and overspeed, overcrank, and recrank protection on false starts. Four LEDs indicate first-out shutdown for:
Low Oil Pressure, High Temperature, Overcrank, Overspeed. Afifth LED
indicates Engine Running. There are also two (2) spare inputs that will cause
the unit to shut down without annunciation on the front LED’s.
Specifications
Power Input: 12 or 24 VDC.
Operating Temperature: -40 to 185°F (-40 to +85°C).
Inputs: Ground or positive inputs for High Temperature, Low Pressure, and
two spares.
Lamp and Output Test: One ground only input for lamp and output test.
Outputs: 5 Arelay for cranking and fuel valve. 300 mAtransistor for fault
annunciation, warmup/cooldown, or glowplug.
Cycle Crank Timer: Selectable to 3, 5, 10 or infinite attempts.
Crank/Rest Cycle Timing: Crank time 10 seconds. Rest time 15 seconds.
Glow Plug Time Delay: Field adjustable from 1 to 300 seconds.
Warmup T ime Delay: Field adjustable from 1 to 300 seconds.
Cooldown Time Delay: Field adjustable from 1 to 300 seconds.
Shutdown Lockout Time Delay: 15 second lockout for low oil,
high temperature, one spare and loss of speed shutdown on start-up.
Crank Disconnect Speed Setting: Field adjustable from 30 to 8500 Hz.
Overspeed Trip Point Setting: Field adjustable from 30 to 8500 Hz.
Magnetic Pickup Input: Requires 3V rms minimum 30 to 100 Hz;
Requires 2V rms minimum 100 Hz and up; Maximum 35V rms.
Installation Accessories
●
Tools as needed for module mounting, such as drill and screw driver.
●
12 and 14 AWG (4.0 mm2and 2.5 mm2) wire for hook up.
●
Set of wire termination tools.
●
Wire termination; such as spade terminals.
ASM160 MURPHYMATIC®Micro-controller
Installation and Operation Instructions
Please read the following information before installing. A visual inspection of this product for damage
from shipping is recommended before installing. It is your responsibility to have a qualified person install
this unit and make sure it conforms to local codes.
GENERAL INFORMATION
BEFORE BEGINNING INSTALLATION OF THIS MURPHY PRODUCT
✔ Disconnect all electrical power to the machine.
✔ Make sure the machine cannot operate during installation.
✔ Follow all safety warnings of the machine manufacturer.
✔ Read and follow all installation instructions.
ASM160 Mounting Dimensions
ASM-97073N
Revised 3-00
Section 40
(00-02-0276)
Mounting Drill Pattern
Side View
Front View
Back View
0.45 in. (11 mm)
0.45 in. (11 mm)
0.45 in. (11 mm)
0.45 in. (11 mm)
Origin
0.59 in.
(15 mm)
0.20 in.
(5 mm)
0.68 in. (17 mm)
4.32 in.
(110 mm)
4.82 in.
(122 mm)
5-7/16 in. (138 mm)
1-63/64 in.
(50 mm)
4-53/64 in.
(122 mm)
0.250 in.
(6 mm) dia.
Potentiometers
DIP switches
0.203 in.
(5 mm) dia.
3-53/64 in.
(97 mm)
4-1/4 in. (108 mm)
Mounting the ASM160 Module
1.
To mount the ASM160 module to a panel, drill five (0.250 in. [6 mm] dia.) holes
for LED indicators and four (0.203 in. [5 mm] dia.) holes for the mounting
screws. See “Mounting Drill Pattern”, above, for dimensions.
2.
Insert the ASM160 module from the back of the panel into the pre-drilled holes.
See schematic below.
3.
Secure the module in place with the four mounting screws provided.
4.
Make sure the panel is clean and free of oil. Remove the adhesive cover from the
back of the ASM160 label. Position the label
on the panel and press firmly.
®
Label
Module
Panel or Wall
OIL PRESSURE
ENGINE TEMPERATURE
OVERCRANK
OVERSPEED
RUN
WARNING

The ASM160 is a pilot duty device. The outputs are designed for control only .
1.
Wire the ASM160, using 14 AWG (2.5 mm2) stranded wire. When wiring to
terminal 18 (the common power for the external relay loads), we suggest using
larger wire size (12 AWG [4.0 mm2]).
2.
When hooking the battery positive (+) and ground wires to the ASM160, route
them directly from the battery to the unit. This will help reduce electrical noise
coupling and avoid voltage losses from other devices.
3.
If a standby battery charger is installed, it must be wired directly to the battery,
NOT to the ASM160. This could cause electronic "noise" produced by the
charger to be coupled into the microprocessor. If the "noise" is severe, erratic
operation will occur.
4.
Do not route low voltage DC (battery) control wires in the same conduit as
high voltage AC wires.
5.
Use shielded cable for connecting the magnetic pickup to the ASM160.
Ground only one end of the shield (suggest to ground it at the engine).
6.
Always place reverse bias diodes across inductive loads (see “Typical Wiring
Diagram”, Note: 2, below). This increases the contact life and helps eliminate a
source of electromagnetic noise.
7.
Output terminals 1 and 2 are rated for 5 A. Output terminals 3, 4, 5, 6, 7 and 8
are rated for 300 mA sinking.
WARNING:
Disconnect ALL electrical power before beginning the wiring. STOP ALL machinery before performing the hook up.
Any load connected to the panel which exceeds current ratings MUST be piloted at the load.
WIRING THE ASM160
MAKING ADJUSTMENTS TO THE ASM160
Typical Wiring Diagram
On the back of the ASM160, you will find four
(4) potentiometers and three (3) DIP switches
for customizing your controller. The four
potentiometers are designated as follows:
R1 = Overspeed Adjustment
(30-8500 Hz)
R 2 = Crank Disconnect Adj.
(30-8500 Hz)
R3 = Glow Plug or Warmup
Delay (1-300 seconds)
R4 = Cooldown Delay
(1-300 seconds) not used when
Glow Plug feature is selected.
Overspeed (R1 Pot)
The OVERSPEED pot is used to set the point at
which the unit will signal for a shutdown if the
engine speed should reach excessive RPM.
To set the OVERSPEED value, turn the OVERSPEED Pot (R1) fully clockwise and run the
engine up to the maximum operating speed.
Next, slowly turn the Pot (R1) counterclock-
wise until the engine shuts down on OVERSPEED. Now, turn Pot (R1) clockwise two
turns. This will adjust the OVERSPEED setpoint slightly higher than the maximum engine
operating speed.
Potentiometers
DIP Switches
7
8
9
10
123
ON
R1 R2
R3
R4
ASM160 Module
Back View Detail
Potentiometer
Detail
2
NOTES:
1
Close to start and run, open to stop.
2
For Pilot Duty Only. External Load not to exceed 5 A.
Place reverse bias diodes across induction loads.
3
Remote lights (if used) not to exceed 300 mA.
4
At Load/Glow Plug Relay not to exceed 300 mA.
Fuel Test
1
Crank
2
At Load/
3
Glow Plug
Overcrank
4
Overspeed
5
Oil Pressure
6
7
O Temp.
H
2
Run
8
9
Lamp Test (IN)
Overspeed Adj.
Crank Disconn. Adj.
Spare (delayed)
Spare (immediate)
Relay Com. (B+)
Cooldown Delay
Glowplug / Warmup Delay
Auto
Gnd (-)
Mag. P/U
Oil Pressure
H2O Temp.
Number of cranks
Warmup or Glow Plug
Mode Select
2
Pilot
Relay
Starter
Assembly
4
To Battery (+)
2
3
3
Solenoid
Fuel Valve
Glowplug/At load
Pilot Relay
3
3
3
Closed Switch
For Lamp Test
Auto
Off
1
Remote
Start/Stop
10
Switch
Test
Selector
Switch
11
12
13
14
15
16
17
18
Ground or
Positive Input
Ground or
Positive Input
Ground or
Positive Input
Ground or
Positive Input
This Shutdown
is immediate with
no LED indication.
Shielded
Cable
Magnetic
Pickup
These Shutdowns
are locked out during
shutdown lockout delay
12 AWG (4.0 mm2) min.
F-1
15 Amp
12/24VDC
Battery
Battery Cable