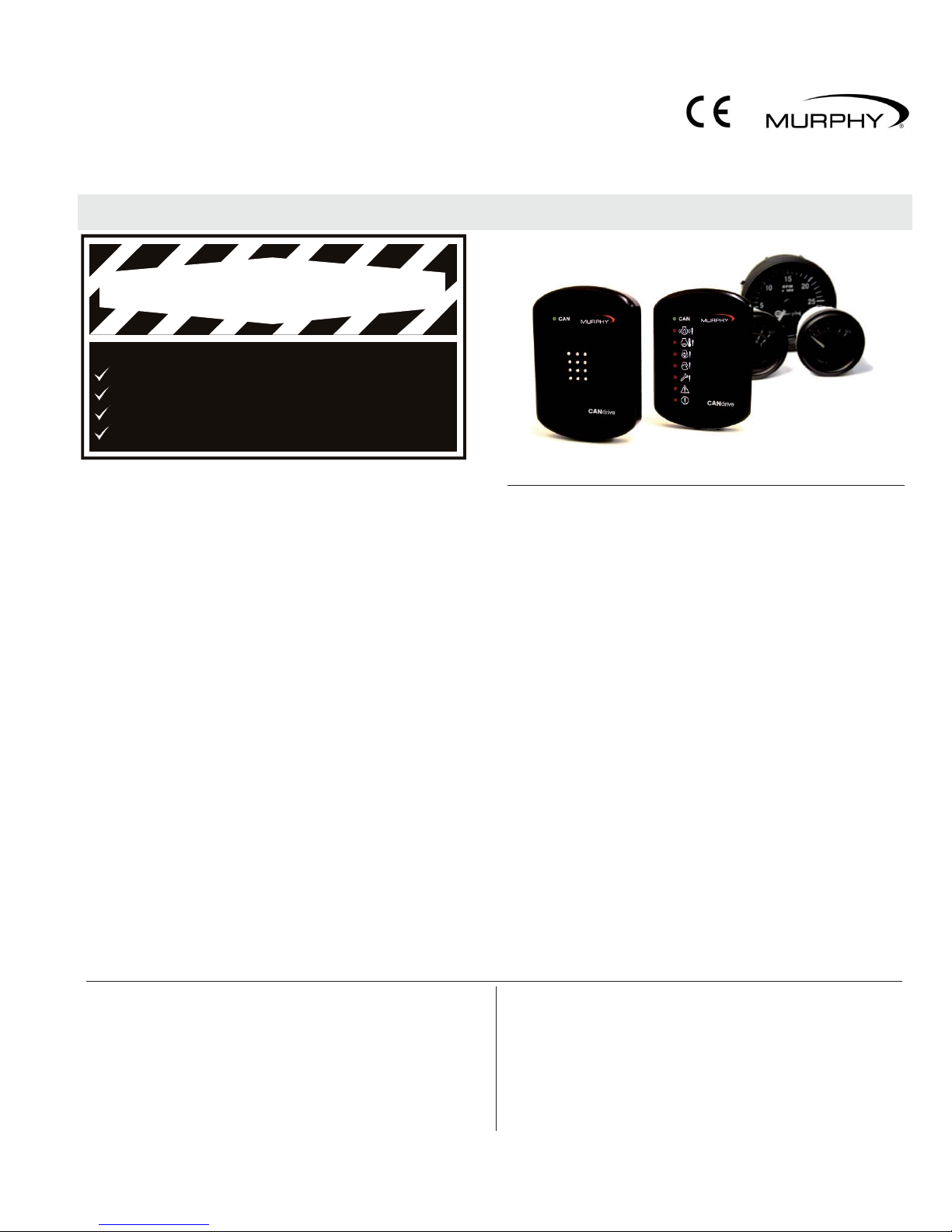
CANdrive™
CANbus SAE J1939 to Electric Gauge Interface
revision F, 7
00-02-0618
th
January 2011
section 78
Installation and Operating Instructions
Please read the following information before installing.A visual inspection of this product for damage during
shipping is recommended before installation. It is your responsibility to ensure that qualified mechanical and electrical
technicians install this product. If in doubt, please contact your local Murphy representative.
General Information
WARNING
BEFORE BEGINNING INSTALLATION OF THIS PRODUCT
Disconnect all electrical power to the machine
Make sure the machine cannot operate durin
Follow all safety warnings of the machine manufacturer
Read and follow all installation instructions
As part of the MurphyLink® family, CANdrive offers a cost
effective instrument solution for modern electronic engines.
CANdrive modules read engine ECU CANbus/J1939 data,
drive standard electric panel gauges, and provide LED
indication of status and faults.
CANdrive has three dedicated outputs for tachometer, oil
pressure and coolant temperature gauges, with DIP switchselectable compatibility for Murphy, VDO or Datcon gauges.
For volume orders, the outputs can be custom-configured for
other gauge types, lamps, relays or remote signalling.
CANdrive advantages include:
x
the retrofitting of existing electric gauge panels to new,
J1939 compatible engines
x
the use of standard, economical electric gauges with
new J1939 engines
x
no need for installation of additional gauge senders,
tachometer magnetic pickups and wiring.
CANdrive is packaged in a compact, surface mounted
case with epoxy encapsulation for maximum durability
and environmental sealing. Electrical connection is via a
12-way automotive type connector. Model CDV100F has
a forward facing connector and one power/CAN status
LED. Model CDV300R has 8 LEDs for indication of
J1939-transmitted engine faults and status. All models
include a 6-way DIP switch for flexible configuration.
Standard models & accessories
installation
Patent applied for GB2424280
Specifications
Power supply
Operating voltage,
12V range (switch S5 on/up): 7 to 16 VDC
24V range (switch S5 off/down): 19 to 30 VDC
Current consumption:
CDV100: 25 mA typ.
CDV300: 50 mA typ. (2 LEDs lit)
Inputs
CANbus: SAE J1939 protocol. Input has a 120 Ohm terminating
resistor, removable by switch S4.
Outputs (all ratings non-reactive)
Oil pressure gauge, engine temperature gauge:
switch selectable for Murphy, VDO or Datcon gauges:
see Gauge Compatibility section for pressure/temperature verses
equivalent sender resistance tables
Tachometer: pulsed DC, 119 Hz ±1% @ 1500 RPM
Physical
Electromagnetic compatibility: 2004/108/EC
Case material: polycarbonate / polyester / epoxy encapsulation
Overall dimensions (w x h x d):
68 x 92 x 22mm / 2.7 x 3.7 x 0.9 in.
(allow 50mm / 2.0 in. depth with connector)
Weight: approx 80g / 0.2 lb
Temperature:
operation: –40 to +85°C / –40 to +185°F, 70% RH
storage: –55 to +105°C / –67 to +221°F
Environmental sealing: IP60
(CDV300R: IP65 from front with optional CDVG gasket)
Vibration: 15g, 10 to 2000 Hz, 3-axis
Shock: 50g, 11 mS, 3-axis
Stock code Description
79.70.0001 CDV100F, CANdrive™ J1939 to gauge interface,
1 x CAN status LED, connector forward
79.70.0002 CDV300R, CANdrive™ J1939 to gauge interface,
8 x status/fault LEDs, connector rearward
78.00.0437 CDV-PW-30, 8 way wiring harness,
length 30 in./760mm
In order to consistently bring you the highest quality, full featured products, we reserve the right to change our specifications and designs at any time.
MURPHY products and the Murphy logo are registered and/or common law trademarks of Murphy Industries, LLC. This document, including
textual matter and illustrations, is copyright protected by Frank W Murphy Ltd., with all rights reserved. © 2011 Frank W Murphy Ltd.
Stock code Description
79.70.1003 CDVG, optional sealing gasket for CDV300R
78.70.0363 CDV100F plus CDV-PW-30 harness
78.70.0364 CDV300R, CDV-PW-30 and CDVG gasket
79.70.1001 CANdrive connector plug shell
79.70.1002 Connector pins for above (pack of 50)

General Information (cont.)
CDV100F
front view
CDV300R
front view
Rear view System connection
Panel Installation
CANdrive modules are surface-mounted with 4 x no.4 screws, fixing centre dimensions as
shown. Select screw length according to panel thickness, ensuring a maximum of 13mm
(½ inch) screw depth into the CANdrive fixing holes.
Model CDV100F, with forward facing connector, is designed for surface mounting inside
an enclosed panel. Model CDV300F, with 8 LED indicators and rearward facing connector,
is designed for front-of-panel mounting: this module requires an additional 60 x 40mm
(2.4 x 1.6 in.) panel cut-out for rear access to connector and switches. A CDV300F with
optional gasket CDVG (fitted into a well behind the case rim) provides IP65 front-of-panel
environmental sealing.
Before installing, ensure that the final mounting location meets operating temperature and
environmental sealing requirements, and allows access for:
a) connection of the wiring harness
b)
configuration of DIP switches S1 to S5 (location as shown above right). Alternatively,
set these switches before panel fixing – see Configuration section below for full details.
Dimensions
mm (in.)
Configuration
DIP switches S1 to S5 allow OEM- or user-configuration of
CANdrive operating options. Switch S6 is not used. CANdrive
is supplied with all switches in the ON (up) position.
Switch settings must be made as appropriate, according to
the configuration table right. Adjustment of the switch
positions must be made while CANdrive is powered down.
Pressure gauge compatibility table: pressure versus approximate equivalent sender resistance (Ohms)
Pressure psi 0 10 20 30 40 50 60 70 80 90 100 110 10 130 140
bar 0 0.7 1.4 2.1 2.8 3.4 4.1 4.8 5.5 6.2 6.9 7.6 8.3 9.0 9.7
Murphy 240 205 171 143 123 103 88 74 60 47 33
Datcon 0 – 7 bar 240 195 160 140 115 100 82 68 55 43 35
Datcon 0 – 10 bar 240 215 190 168 150 135 118 107 97 87 77 67 58 50 42
VDO 0 – 5 bar 10 38 61 85 110 130 155 180
VDO 0 –10 bar 15 30 45 60 70 81 92 103 114 125 136 148 160 170 182
Temperature gauge compatibility table: temperature versus approximate equivalent sender resistance (Ohms)
Temperature °C 40 50 60 70 80 90 100 110 120 130 140
°F 104 122 140 158 176 194 212 230 248 266 284
Murphy 1029 680 460 321 227 164 120 89 74 52 40
Datcon 360 160 80 50 38
VDO 282.4 190.0 134.0 95.2 69.1 51.2 38.5 29.4 22.7 18.0 14.5
FW Murphy – CANdrive installation and operation 00-02-0618 revision F 7th January 2011 p2/4
Switch
position
S1 S2 S3 S4 S5
on (up)
off (down)
Options:
Murphy temp. and pressure gauge
Datcon temp. and 0 – 7 bar pressure gauges
atcon temp. and 0 – 10 bar pressure gauges
VDO temp. and 0 – 5 bar pressure gauges
VDO temp. and 0 – 10 bar pressure gauges
CAN 120 Ohm terminating resistor in circuit
CAN 120 Ohm terminating resistor removed
12V DC ower supply
24V DC power supply