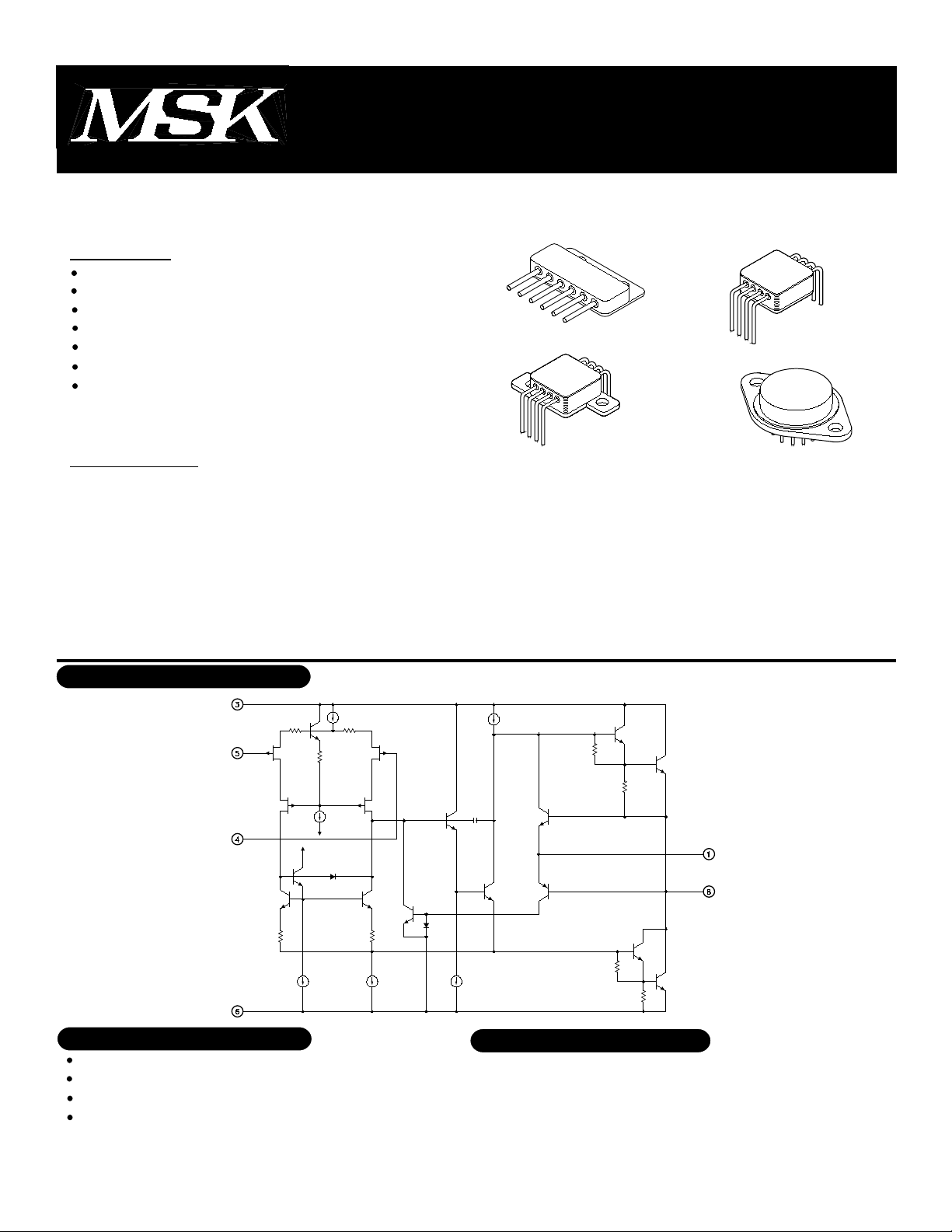
ISO 9001 CERTIFIED BY DSCC
HIGH POWER
HIGH POWER
OP-AMP
M.S KENNEDY CORP.
4707 Dey Road Liverpool, N.Y. 13088 (315) 701-6751
FEATURES:
Available as SMD #5962-8870101
High Output Current - 10 Amps Peak
Wide Power Supply Range - ±10V to ±40V
Programmable Current Limit
FET Input
Isolated Case
Replacement for OMA 541SKB - MSK 541
OMA 541SDB - MSK 146
OMA 541SZB - MSK 147
OP-AMP
MIL-PRF-38534 QUALIFIED
MSK145
541
SERIES
MSK146
DESCRIPTION:
The MSK 541 Series is a high power monolithic amplifier ideally suited for high power amplification and magnetic
deflection applications. This amplifier is capable of operation at a supply voltage rating of 80 volts and can deliver
guaranteed continuous output currents up to 5A, making the 541 series an excellent low cost choice for motor drive
circuits. The amplifier and load can be protected from fault conditions through the use of internal current limit
circuitry that can be user programmed with a single external resistor. The MSK 541 is pin compatible with popular
op-amps such as the Burr-Brown OPA501, OPA511, OPA512, OPA541 and 3573. The MSK 541 is available in a
hermetically sealed 8 pin TO-3 package. Other package styles are also available for a wide range of applications.
The MSK 145 is available in a 6 pin SIP Package. The MSK 146 is an 8 pin Power DIP Package and the MSK 147
is available in an 8 pin Power Z-TAB Package for applications requiring bolt down heat sinking.
EQUIVALENT SCHEMATIC
MSK 541 ONLY
MSK147
MSK541
TYPICAL APPLICATIONS
Servo Amplifer
Motor Driver
Audio Amplifier
Programmable Power Supply
PIN-OUT INFORMATION
1 Current Sense 5 Inverting Input
2 No Connection 6 Negative Power Supply
3 Positive Power Supply 7 No Connection
4 Non-Inverting Input 8 Output Drive
The above pin out table is for the MSK 541 (TO-3). Refer to the
mechanical specifications page for the pin out information of addi-
tional package styles.
1
Rev. C 3/01
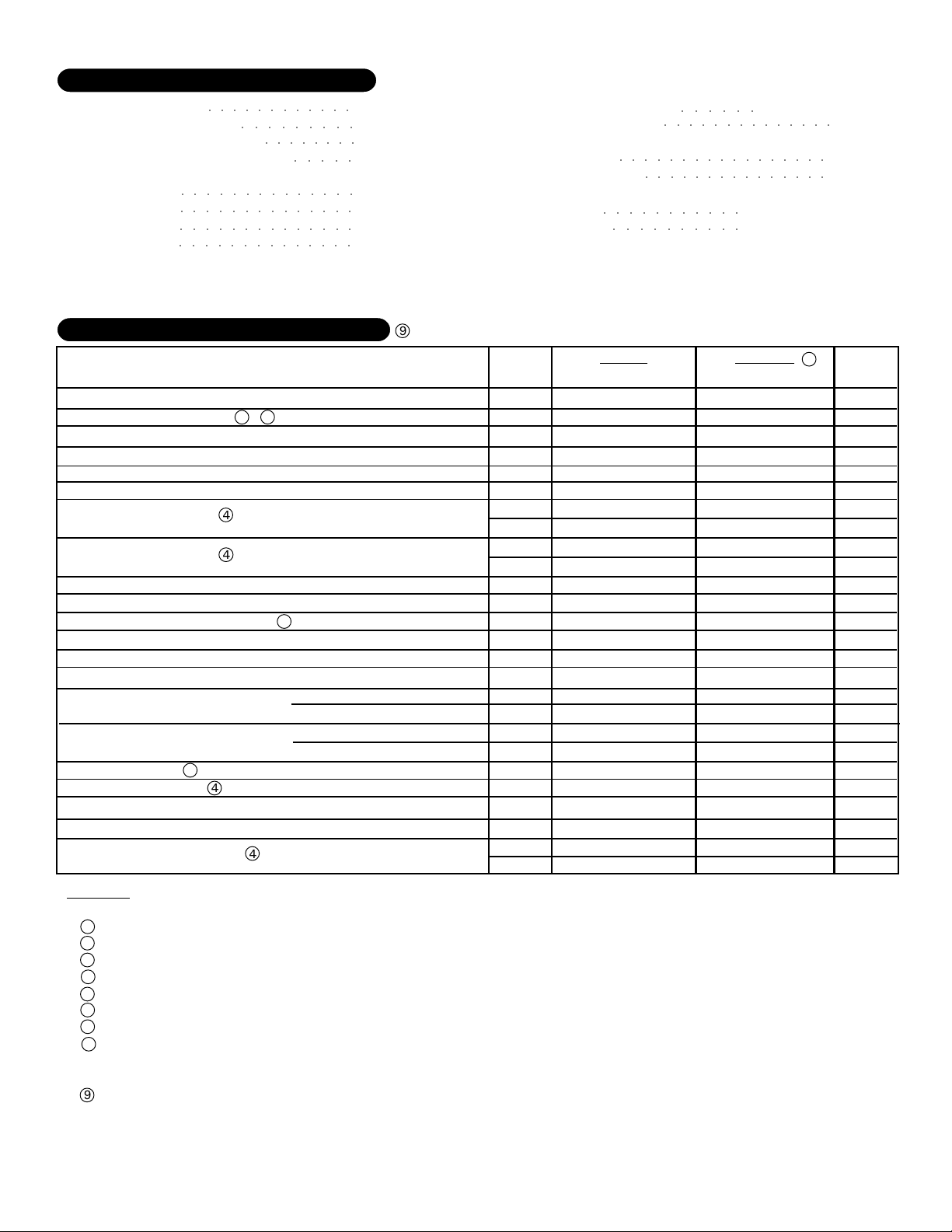
ABSOLUTE MAXIMUM RATINGS
±VCC Supply Voltage ±40V
OUT Peak Output Current See S.O.A.
I
V
IN Differential Input Voltage ±VCC
VIN Common Mode Input Voltage ±VCC
RTH Thermal Resistance-Junction to Case
MSK 541 1.9° C/W
MSK 145 1.2° C/W
MSK 146 1.2° C/W
MSK 147 1.2° C/W
○○○○○○○○○○○○
○○○○○○○○○
○○○○○○○○
○○○○○
○○○○○○○○○○○○○○
○○○○○○○○○○○○○○
○○○○○○○○○○○○○○
○○○○○○○○○○○○○○
TST Storage Temperature Range -65° to +150°C
TLD Lead Temperature Range 300°
○○○○○○
○○○○○○○○○○○○○○
(10 Seconds)
PD Power Dissipation 125W
TJ Junction Temperature 150°C
T
C Case Operating Temperature Range
Military Versions -55°C to +125°C
Industrial Versions -40°C to +85°C
○○○○○○○○○○○○○○○○○
○○○○○○○○○○○○○○○
○○○○○○○○○○○
○○○○○○○○○○
ELECTRICAL SPECIFICATIONS
Parameter
STATIC
Supply Voltage Range
Quiescent Current
INPUT
Input Offset Voltage
Input Offset Voltage Drift
Input Bias Current
Input Offset Current
Input Capacitance
Input Impedance
Common Mode Rejection Ratio
Power Supply Rejection Ratio
Input Noise Voltage
OUTPUT
Output Voltage Swing
Output Current
Settling Time
Power Bandwidth
3
4
TRANSFER CHARACTERISTICS
Slew Rate
Open Loop Voltage Gain F = 10 H
4
2
4
4
4
RL = 5.6Ω F = 10 KHz
R
L =10Ω F = 10 KHz
R
L = 5.6Ω F =10 KHz
R
L = 10Ω F = 10 KHz
0.1% 2V step
R
L = 10Ω VO = 20 VRMS
4
Test Conditions
F = DC V
V
CC = ±10V to ±40V
F = 10 Hz to 1 KHz
VOUT = ±10V RL = 10Ω
9
V
IN = 0V
IN = 0V
V
V
IN = 0V
V
CM = 0V
Either Input
VCM=0V
F = DC
CM = ±22V
Z RL = 10 KΩ
Group A
Subgroup
-
1, 2, 3
1
2, 3
1
2, 3
1
2, 3
-
-
-
-
-
4
5, 6
4
5, 6
-
4
4
4
5, 6
Military Industrial
Typ.
±35
±20
±0.1
±15
±4
±0.2
2.0
-
5
10
113
90
10
±29
±31
±8
-
2
55
10
100
-
Max.
±40
±30
±1.0
±5 0
±50
±10
30
20
-
12
-
-
-
-
-
-
-
-
-
-
-
-
-
Min.
±10
-
-
-
-
-
-
-
-
-
95
-
-
±28
±30
±5
±3.0
-
45
6
95
85
Min.
±10
-
-
-
-
-
-
-
-
-
90
-
-
±28
-
±5
-
-
40
6
90
-
Typ.
±35
±20
±1.0
±15
±4
±0.2
2.0
-
5
10
113
90
10
±29
-
±8
-
2
50
10
100
-
5
Max.
±40
±35
±10
±100
12
30
Units
V
mA
mV
-
µV/°C
pA
-
nA
pA
-
nA
-
-
-
-
-
-
-
-
-
-
-
-
-
-
pF
W
dB
dB
µV
µS
KHz
V/µS
dB
dB
RMS
V
V
A
A
NOTES:
1 Unless otherwise specified RCL = 0Ω, ±VCC = ±34 VDC
2 Electrical specifications are derated for power supply voltages other than ±34 VDC.
3 AV = -1, measured in false summing junction circuit.
4 Devices shall be capable of meeting the parameter, but need not be tested. Typical parameters are for reference only.
5 Industrial grade devices shall be tested to subgroups 1 and 4 unless otherwise specified.
6 Military grade devices ('B' suffix) shall be 100% tested to subgroups 1, 2, 3 and 4.
7 Subgroup 5 and 6 testing available upon request.
8 Subgroup 1, 4 TA = TC = +25°C
Subgroup 2, 5 TA = TC = +125°C
Subgroup 3, 6 TA = TC = -55°C
Rereference DSCC SMD 5962-8870101 for electrical specifications for devices purchased as such.
9
2
Rev. C 3/01
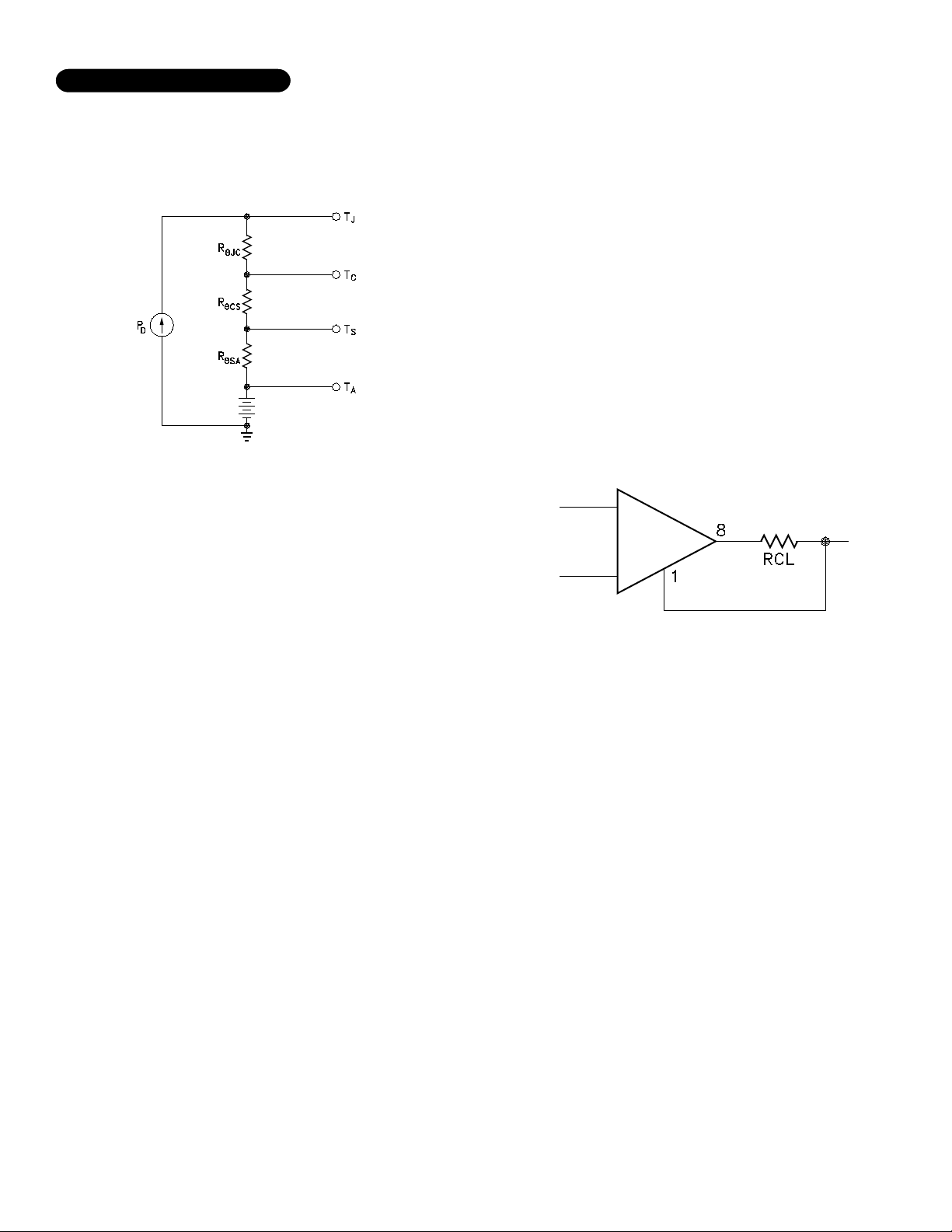
APPLICATION NOTES
HEAT SINKING
To select the correct heat sink for your application, refer to the
thermal model and governing equation below.
Thermal Model:
Governing Equation:
TJ = PD X (RθJC + RθCS + RθSA) + TA
Where
TJ = Junction Temperature
PD = Total Power Dissipation
RθJC = Junction to Case Thermal Resistance
RθCS = Case to Heat Sink Thermal Resistance
RθSA = Heat Sink to Ambient Thermal Resistance
C = Case Temperature
T
TA = Ambient Temperature
TS = Sink Temperature
Example: (TO-3 PACKAGE)
CURRENT LIMIT
The MSK 541 has an on-board current limit scheme designed
to limit the output drivers anytime output current exceeds a
predetermined limit. The following formula may be used to
determine the value of the current limit resistance necessary to
establish the desired current limit.
RCL (OHMs) = (0.809 volts / current limit in amps) - 0.057 OHM
The 0.057 OHM term takes into account any wire bond and
lead resistance. Since the 0.809 volt term is obtained from the
base emitter voltage drop of a bipolar transistor, the equation
only holds true for operation at +25°C case temperature. The
effect that temperature has on current limit may be seen on the
Current Limit vs. Case Temperature Curve in the Typical Perfor-
mance Curves.
Current Limit Connection
See "Application Circuits" in this data sheet for additional
information on current limit connections.
In our example the amplifier application requires the output to
drive a 20 volt peak sine wave across a 5 ohm load for 4 amps of
output current. For a worst case analysis we will treat the 4 amps
peak output current as a D.C. output current. The power supplies
are ±35 VDC.
1.) Find Power Dissipation
PD = [(quiescent current) X (+VCC - (VCC))] + [(VS - VO) X IOUT]
= (30 mA) X (70V) + (15V) X (4A)
= 2.1W + 60W
= 62.1W
2.) For conservative design, set TJ = +150°C
3.) For this example, worst case TA = +25°C
4.) RθJC = 1.2°C/W typically for the TO-3 package
5.) RθCS = 0.15°C/W for most thermal greases
6.) Rearrange governing equation to solve for RθSA
RθSA =(TJ - TA) / PD - (RθJC) - (RθCS)
= (150°C - 25°C) / 62.1W - (1.2°C/W) - (0.15°C/W)
= 0.66°C/W
The heat sink in this example must have a thermal resistance of
no more than 0.66°C/W to maintain a junction temperature of no
more than +150°C. Since this value of thermal resistance may be
difficult to find, other measures may have to be taken to decrease
the overall power dissipation.
POWER SUPPLY BYPASSING
Both the negative and the positive power supplies must be
effectively decoupled with a high and low frequency bypass
circuit to avoid power supply induced oscillation. An effective
decoupling scheme consists of a 0.1 microfarad ceramic ca-
pacitor in parallel with a 4.7 microfarad tantalum capacitor from
each power supply pin to ground. It is also a good practice
with very high power op-amps, such as the MSK 541, to place
a 30-50 microfarad nonelectrolytic capacitor with a low effec-
tive series resistance in parallel with the other two power sup-
ply decoupling capacitors. This capacitor will eliminate any
peak output voltage clipping which may occur due to poor
power supply load regulation. All power supply decoupling
capacitors should be placed as close to the package power
supply pins as possible (pins 3 and 6 for the MSK 541).
SAFE OPERATING AREA
The safe operating area curve is a graphical representation of
the power handling capability of the amplifier under various
conditions. The wire bond current carrying capability, transis-
tor junction temperature and secondary breakdown limitations
are all incorporated into the safe operating area curves. All
applications should be checked against the S.O.A. curves to
ensure high M.T.B.F.
3
Rev. C 3/01