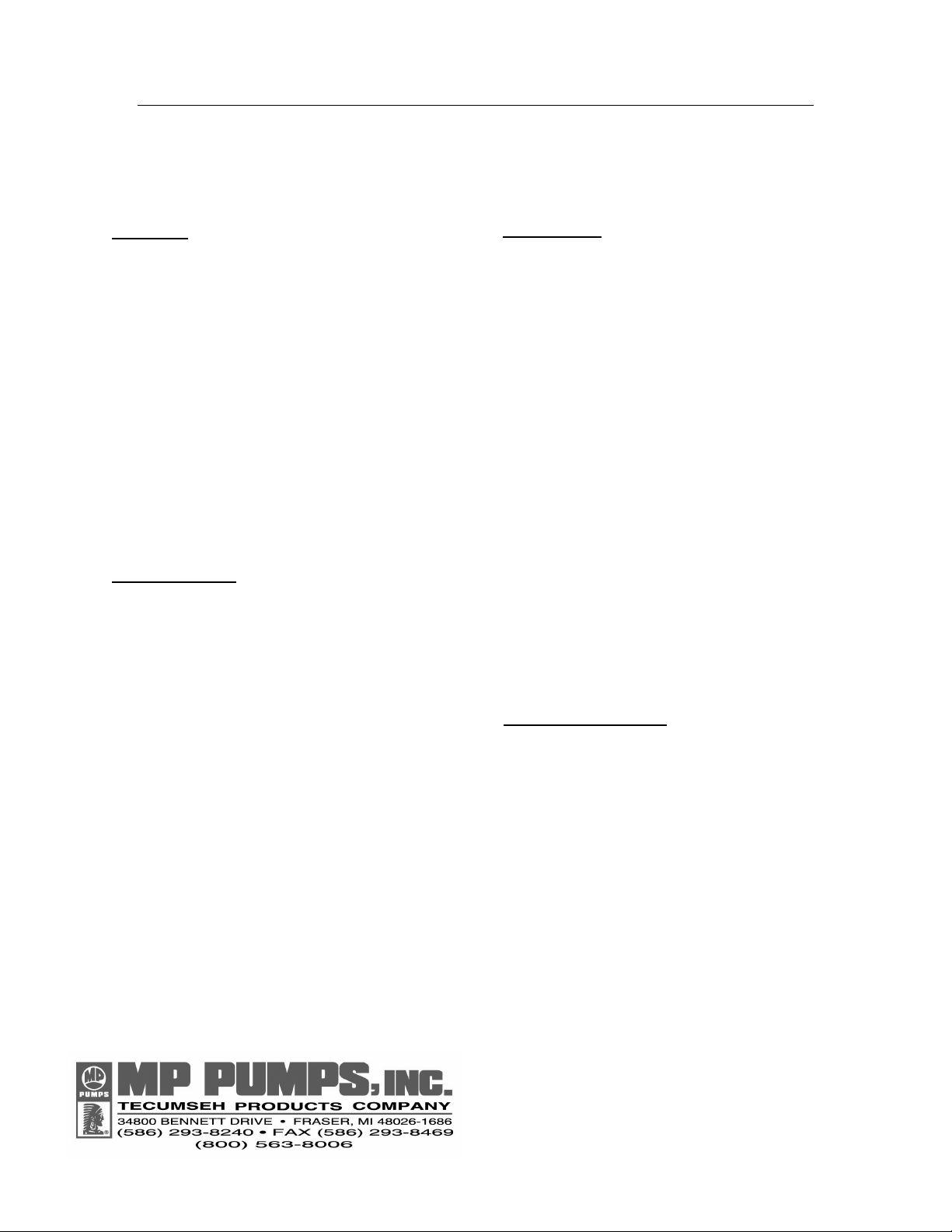
INSTRUCTION BULLETIN
HHLF Self-Priming Centrifugal Pumps
Overview:
It is important that this instruction bulletin be fully
read and understood prior to pump operation. These
instructions pertain to model HHLF pump end. Your
HHLF pump may have included a driver such as
close-coupled electric motor, engine, bearing pedestal
or hydraulic motor pedestal that will hereafter be
referred to as the driver.
Unpack and check the unit over carefully. Missing or
damaged parts should be reported to the freight
company.
Packed with each unit are instruction booklets, parts
list and performance information.
INSTALLATION:
Optimum performance can be attained by placing the
pump as close to the liquid source as possible.
Secure the pump by mounting it to a foundation or
base plate.
Hose or pipe can be used on the suction and
discharge. The suction line must not be reduced in
size. If hose is used, reinforced non-collapsible type
is recommended. The discharge line must be rated to
the maximum pressure developed by the pump.
Avoid kinks in the hose and unnecessary restrictions
that may affect pump performance.
All pipe connections must be sealed with adequate
thread sealant. A small air leak in the suction line
will affect priming performance. If a throttling valve
is used to adjust the flow rate, it should be mounted
to the discharge piping only - never in the suction.
A large low restriction de-watering type strainer must
be used whenever there are solids present in the
liquid source.
OPERATION:
Caution – Do not run the pump dry. The seal in
the HHLF pump is lubricated by the liquid in the
pump. Serious damage will result if the pump is run
without liquid in the housing.
Fill the pump with liquid through the fill-plug located
on the top of the housing. The pump housing should
be completely full. If the pump has a discharge valve
it must be fully open to expel air during priming at
initial start-up. Long horizontal suction lines require
extra time to prime, 2 additional minutes for every 10
feet of horizontal run.
Start the pump driver. The pump will prime the
suction hose and establish flow in about 5 minutes,
more or less, depending upon the lift distance and
length of horizontal run. After prime, the pump will
perform to its full flow capability.
After the initial prime, the pump will retain liquid in
the housing and may not need to be refilled after
shutdown and restart even if the suction pipe has air
in it.
TROUBLE SHOOTNG;
If the pump fails to prime or stops pumping check for
the following possible causes:
1) Insufficient liquid in the pump.
2) Air leak in the suction line due to loose
connections or pinholes in the hose.
3) Collapsed suction line or clogged strainer.
4) Seal worn and sucking air.
5) Worn impeller – impeller gap too large.
6) Pump not running fast enough.
7) Suction lift too high.
8) Priming against high head or obstruction such as
check valve in discharge line.
Form 3071-A
3/04
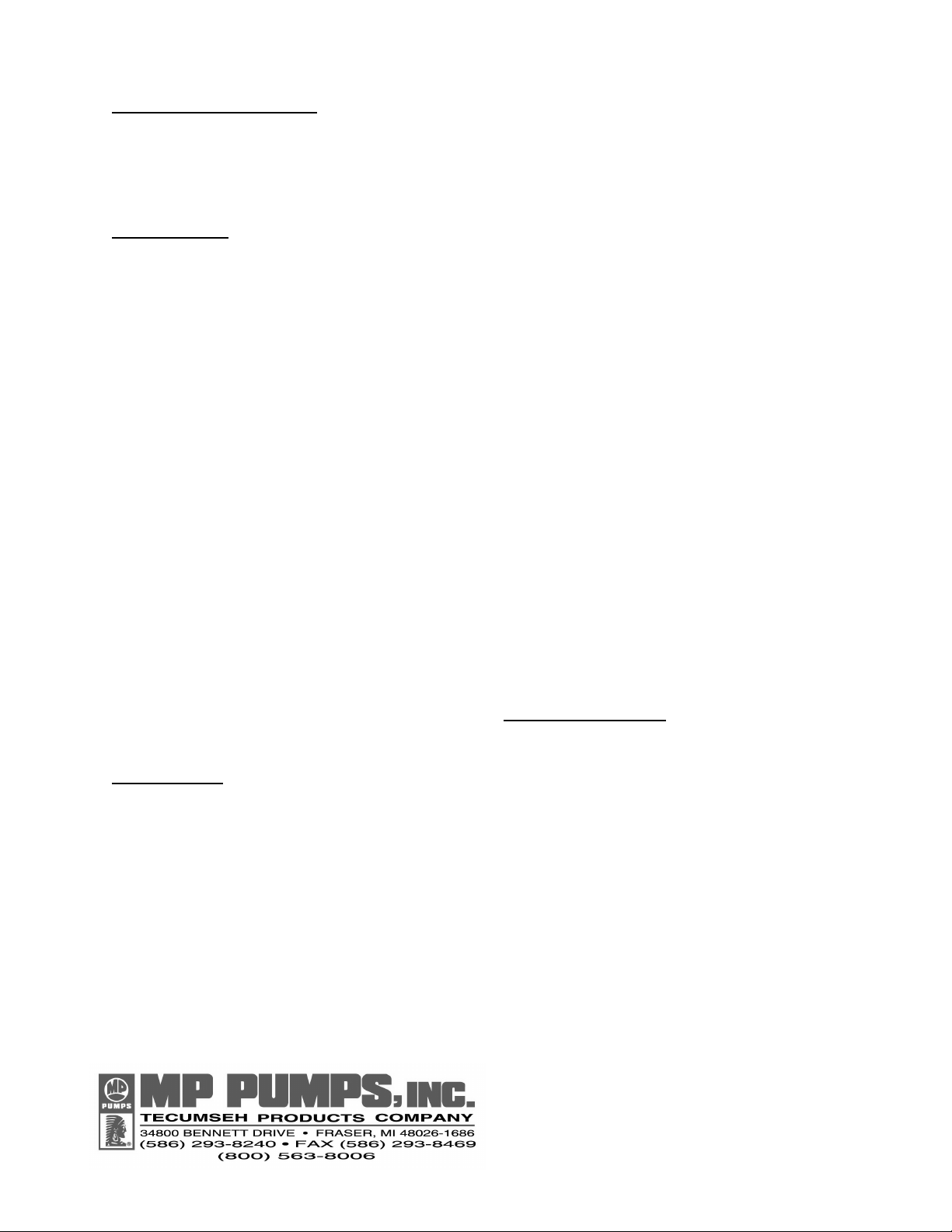
PERIODIC MAINTENANCE:
If the pump is to be idle for any length of time in
freezing weather it must be drained to prevent
damage.
DISASSEMBLY :
Use the exploded parts view with these instructions
and note recommended replacement parts for the
rebuild process.
1. Disconnect the power to the driver
2. Disconnect the lines and drain the pump
3. Loosen clamp and driver fasteners and
disconnect pump end from the driver. Some
means may be necessary to loosen the drive
sleeve if it has frozen to the driver shaft.
4. Remove and place the pump end suction down
on a bench.
5. Remove 4 nuts from the adaptor and remove the
rotating assembly form the housing.
6. Remove the inner volute and discard the gasket.
7. Remove the impeller/drive sleeve assembly from
the adaptor.
8. Remove seal from the drive sleeve and discard.
9. Remove the seal seat from the adaptor and
discard.
10. Inspect the impeller for abrasive wear at the
edges of the machined surfaces. If they are not
well defined the impeller should be replaced.
11. Should the impeller or drive sleeve require
replacement secure the drive sleeve and unthread
the impeller by rotating it in a counter-clockwise
direction.
4. Install the inner volute in the housing by first
placing gasket on the volutes suction. Align the
priming port with the bottom of the housing.
The two ribs on the volute that reassemble a “V”
shape are to be aligned with the top of the pump
housing
5. Place the impeller/drive sleeve assembly face
down in the inner volute.
6. Replace the housing o-ring then place the
adaptor with seal seat installed over the drive
sleeve. Install and tighten housing fasteners to
24 ft/lbs
7. Slide the drive sleeve clamp assembly on the
sleeve.
8. Remove inlet and discharge flanges from the
housing. Discard the discharge gasket and
flapper.
9. Pull the clamp assembly and sleeve backward
then slide a shim down the pump discharge
between the wearplate and impeller vanes. Shim
material thickness should be .01 -.03 inches.
Ideally the shim should be long enough to extend
out of the pump discharge.
10. With the shim still in place replace the
discharge gasket and flange. Tighten fasteners to
24 ft/lbs
11. Replace the flapper and suction flange. Tighten
fasteners to 24 ft/lbs
The pumpak is now ready to be assembled to the
driver.
PUMPAK ASSEMBLY;
REASSEMBLE:
1. Using a water-soluble lubricant, lubricate the
seal rubber parts and seal-housing bore. Install
new seal seat into the adaptor with the polished
side of the seat up. Install by hand using your
thumbs to squarely locate the seats against the
shoulder of the adaptors. Wipe the seal faces dry
with a rag.
2. Thread a new drive sleeve into the impeller.
3. Using a water-soluble lubricant, lubricate the
impeller sleeve and the seal rotary bellows inner
diameter. Install the seal rotary with the spring
against the impeller and seal face out.
1. With the drive clamp fasteners loose slide the
pumpak onto the driver shaft. This should not
require extreme force.
2. Install and tighten the four driver fasteners to 24
ft/lbs
3. Tighten the drive clamp fasteners to 24 ft/lbs.
Take care to center the clamp halves so they do
not come into contact.
4. Remove the metal shim. This should also not
require extreme force.
5. Rotate the shaft to insure that the pump rotates
freely before putting it into service.
Form 3071-A
3/04