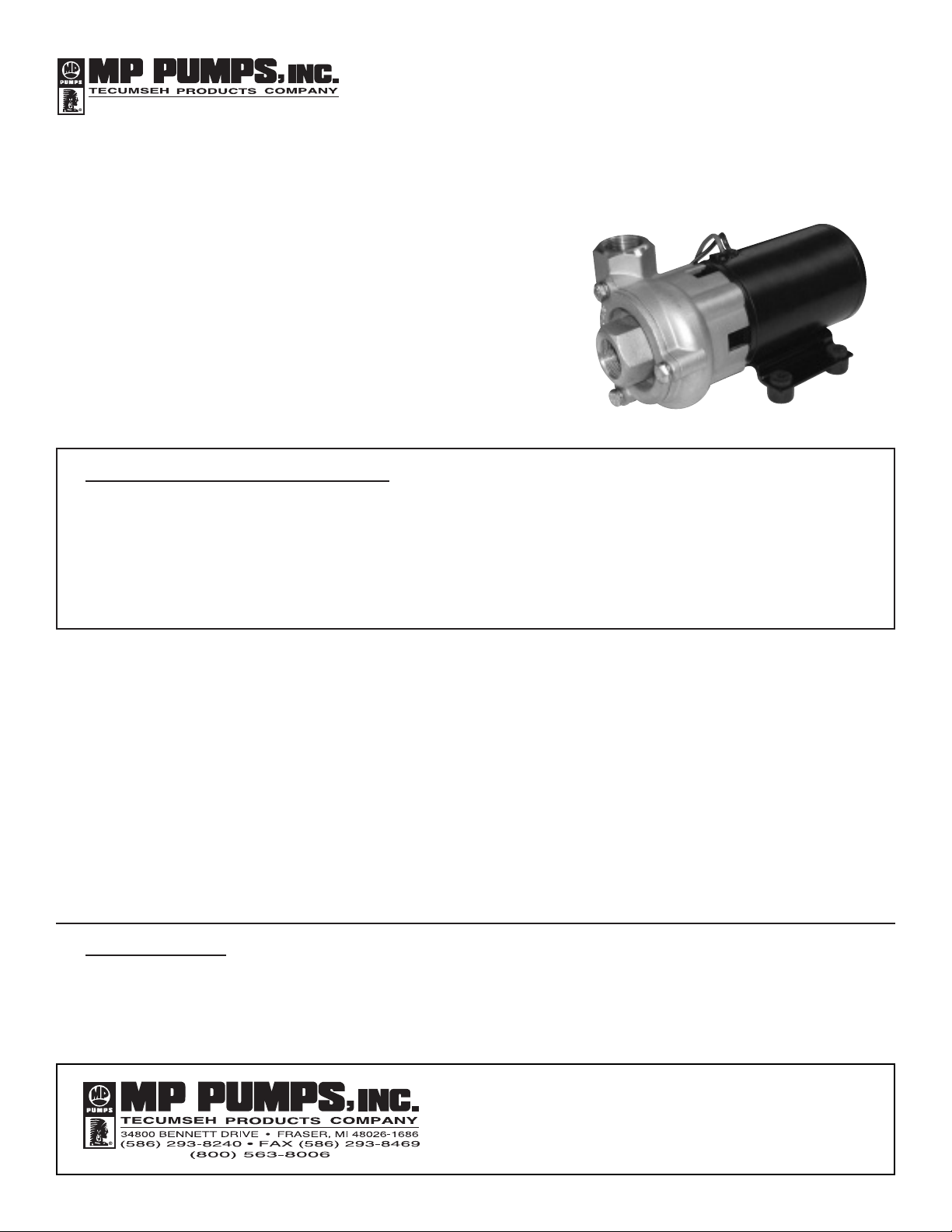
FRX 75 316 STAINLESS STEEL CENTRIFUGAL PUMP
INSTALLATION, OPERATION, AND REPAIR MANUAL
FRX 75 is a high performance stainless steel centrifugal
pump. Its uses are marine, commercial, and industrial
transfer of chemicals or potable water. FRX 75 features
a totally enclosed long life, ball bearing, 12VDC motor
with marine ignition protection. All pump parts are
316 stainless for superior corrosion resistance when
pumping chemical compounds, A carbon, ceramic, viton,
bellows shaft seal is standard. 3/4 inch NPT
flanges and base mounted vibration isolators simplify
installation.
GENERAL SAFETY INFORMATION:
THE FOLLOWING WARNINGS ARE USED TO NOTIFY AND ADVISE THE USER OF THIS PRODUCT OF
PROCEDURES THAT MAY BE DANGEROUS TO THE USER OR RESULT IN DAMAGE TO THE PRODUCT.
THIS BULLETIN MUST BE READ COMPLETELY BEFORE INSTALLING, OPERATING, OR SERVICING,
THE PUMP.
• DO NOT perform service or maintenance
when the pumping system is pressurized.
Injury or death may occur.
• DO NOT operate the pump in a manner
that it was not intended to be used.
• DO NOT mount the pump such that high
piping loads exist on the pump flanges, or
in a rigid piping system that does not allow
the pipe to expand and cause the pump to
be strained.
ALLATION:
INST
Install the pump wher
pump for service. The pump is not self-priming and needs the inlet to be flooded at start-up.
The motor is splash r
e the inlet is below the liquid level. A valve may be used to isolate the
esistant, not submersible, and should be located in a dr
• DO NOT continue to operate the pumping
system when a known leak exists.
• DO NOT continue to operate the pump
when unusual noise or vibration occurs.
• DO NOT operate beyond the pressure or
temperature limits stated in the product
literature. See Form 8110.
• DO NOT allow severe temperature changes
to occur in a short time period within the
pumping system.
y envir
onment.
FORM 3805A (05-04)
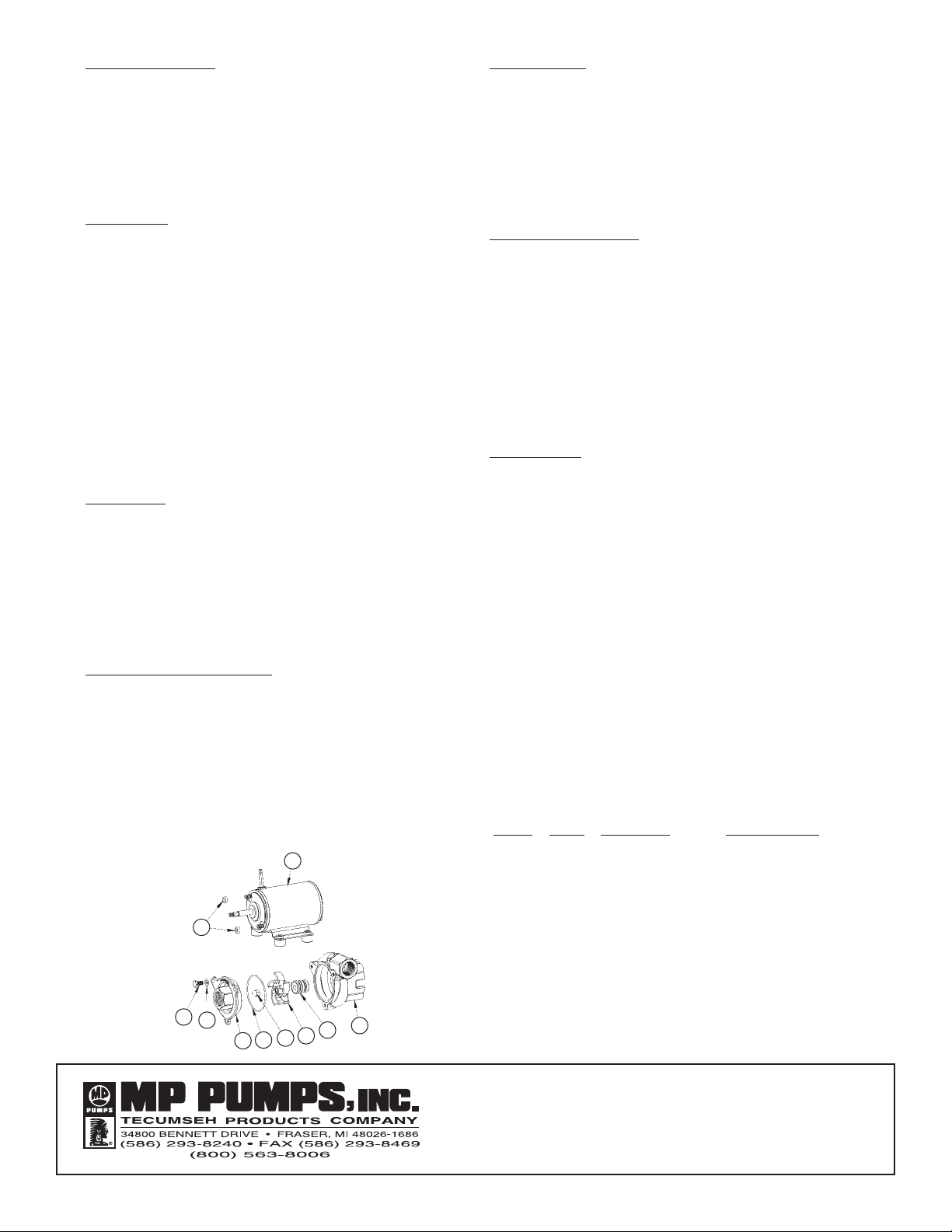
PIPING/MOUNTING:
The pump inlet and outlet has 3/4" pipe connections. Use
pipe sealant on the threads and other connections. The base
does not require direct mounting if one of the pipe flanges is
rigid mounted. Do not rigid mount both the flanges and the
base to avoid mounting tolerances that may distort the motor
ase. Install the pump with the shaft in a horizontal direction.
b
Never install the pump vertical with the motor below the
pump.
ELECTRICAL:
The motor must be protected from over current by using a
fuse or circuit breaker (see chart below for correct protection).
The proper minimum wire size is stated for each voltage
application. Make sure that the pump has the proper voltage
ating to match the installation power. Do not use or install if
r
the voltage on the label is different than the installation. All
wire connections must be secure and sealed to protect
arcing. Follow all local installation codes.
MOTOR VOLTAGE FUSE/CB WIRE SIZE
ON NAME PLATE AMPS AWG
12VDC 15 14
24VDC 10 16
32VDC 6 18
115VAC 2 18
230VAC 1 18
OPERATION:
The pump should be operated with liquid in the pump
otherwise seal damage may occur. If an inlet valve is present,
the valve should always be completely open during
operation to avoid cavitation. An outlet valve may be used to
throttle the flow rate. Avoid repeated starts and stops; the
pump can operate for a long period of time without any flow.
DC motors are brush type and may emit a noise from the
brush that can sound like a squeal, this is normal. The pump
will be extremely quiet unless there is air in the system.
REPAIR AND MAINTENANCE:
DC motor brush life expectancy is 6,000 hours total brush life.
The motor is not rebuildable after the brushes have worn to
the limits.
The pump has a carbon/ceramic seal that may last several
thousand hours based upon the application. If the motor is
replaced, the mechanical shaft seal should also be replaced.
A seal that leaks will show leakage thr
ough the slot between
the pump housing and the motor. Extreme leakage may
damage the motor bearings and contaminate the
inside of the motor.
1
2
10
9
5
6
7
8
3
4
DISASSEMBLY:
1. Remove three cover screws and remove the cover,
discarding the o-ring.
2. Secure the impeller and remove the impeller locknut.
Pull the impeller straight out off the motor shaft.
3. Remove the seal-rotating portion by pulling the seal off
y hand.
b
4. Remove the capscrews that hold the pump housing
onto the motor. Remove the pump housing and push the
seal seat out using a screwdriver.
INSPECT PUMP PARTS:
Always replace the mechanical seal. Check the seal for
dry run wear or damage. Check the motor shaft for wear
at the secondary sealing surface from the mechanical
eal. If worn, replace the motor. Check the motor bearings
s
by rotating the motor by hand. If the shaft rotation is
not smooth or has radial/axial endplay, replace the
motor. Check the impeller running surface between the
impeller and cover. If the surfaces are worn or
irregular, replace each item.
Clean the parts that are to be reused using a solvent or
mild cleaner. Remove abrasive material.
REASSEMBLY:
1. Press the new seal seat into the pump housing. A light
lubricant may be used to aid the assembly. Install the
pump housing onto the motor and fasten the screws
through the motor.
2. Install the rotating portion of the mechanical seal by
sliding the seal over the motor shaft. Do not use any
lubricant.
3. Place the impeller onto the shaft over the D drive
against the shoulder and tighten the impeller lock nut
until the impeller is securely shouldered on the motor
shaft. Thread locking grade Loctite should be used to
secure the nut.
4. Stretch the o-ring over the cover pilot. Install the cover
onto the housing and fasten the capscrews and
lockwashers.
Check the pump for internal interference by rotating the
impeller. The pump should rotate freely with only seal
friction.
ITEM QTY. PART NO. DESCRIPTION
34036
1
1
34293
12VDC MOTOR
24VDC MOTOR
34504 115VDC ODP
35178 115V
AC TENV
35179 230VAC TENV
2 2 34369 GROMMET
3 1 34032 HOUSING- 316 SS
4 1 34038 MECH SEAL- VITON
5 1 34033 IMPELLER- 316 SS
28766
6
7
1
1 34040 O-RING- VITON
ACORN NUT 316 SS
8 1 34035 COVER- 316 SS
9
10
33564 LOCKW
3
34037
3
1/4-20 CAPSCREW 316 SS
ASHER 316 SS
FORM 3805A (05-04)