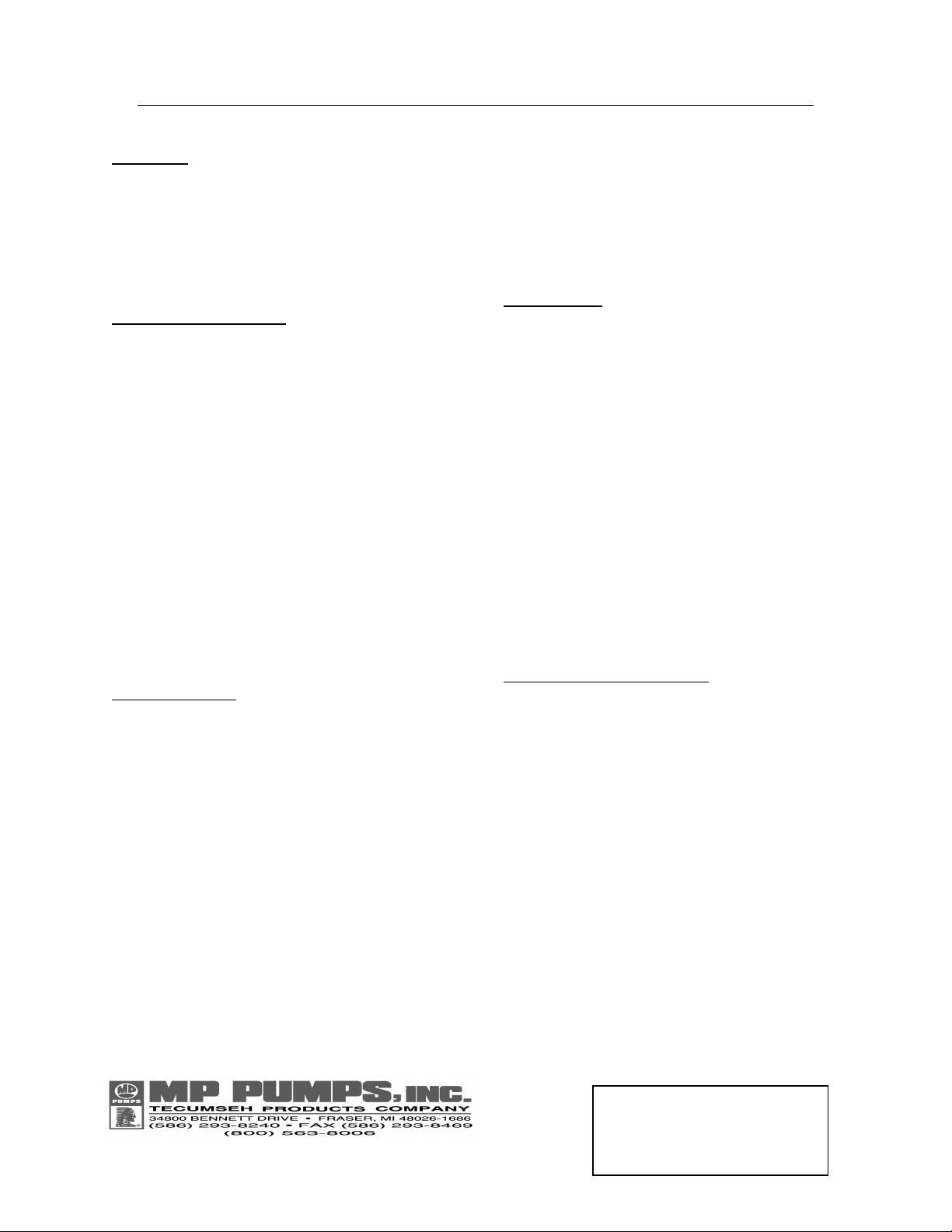
INSTRUCTION BULLETIN
Flomax 5, 8, 10 and 15 - Self Priming Double Seal Pumps
Overview:
These instructions pertain to double seal Flomax 5,
8,10 & 15 pump end installation and assembly. Your
Flomax pump may have included a driver such as
close-coupled electric motor, engine, bearing pedestal
or hydraulic motor pedestal that will hereafter be
referred to as the driver.
PUMPAK ASSEMBLY: (pump end suitable for
mounting to various drivers).
1. Loosen the drive sleeve clamp.
2. Slide the pump onto the driver by hand. This
should not require extreme force.
3. Install and tighten fasteners (4 screws) into the
pump adaptor securing the driver.
4. Tighten the FM5 &8 drive sleeve clamp nuts to
10 to 14 ft-lbs. FM10 & 15 tighten 20 to 26 ftlbs.
®
A large low restriction de-watering type strainer must
be used whenever there are solids present in the
liquid source.
OPERATION:
Fill the pump with liquid prior to starting through a
fitting on the discharge piping. The pump housing
should be completely full. If the pump has a
discharge valve it must be fully open to expel air
during priming at initial start-up. Long horizontal
suction lines require extra time to prime, 2 additional
minutes for every 10 feet of horizontal run.
Start the pump driver. The pump will prime the
suction hose and establish flow in about 5 minutes,
more or less, depending upon the lift distance and
length of horizontal run. After prime, the pump will
perform to its full flow capability.
5. Remove the metal shim strap that spaces the
impeller by pulling it out of the discharge.
6. Rotate the shaft to ensure that the pump rotates
freely before putting the pump into service.
INSTALLATION:
Optimum performance can be attained by placing the
pump as close to the liquid source as possible.
Secure the pump by mounting it to a foundation or
base plate.
Hose or pipe can be used on the suction and
discharge. The suction line must not be reduced in
size. If hose is used, reinforced non-collapsible type
is recommended. The discharge line must be rated to
the maximum pressure developed by the pump.
Avoid kinks in the hose and unnecessary restrictions
that may affect pump performance.
All pipe connections must be sealed with adequate
thread sealant. A small air leak in the suction line
will affect priming performance. If a throttling valve
is used to adjust the flow rate, it should be mounted
to the discharge piping only - never in the suction.
After the initial prime, the pump will retain liquid in
the housing and may not need to be refilled after
shutdown and restart even if the suction pipe has air
in it.
PERIODIC MAINTENANCE:
The double seal reservoir uses grease to lubricate and
cool the shaft seals. The grease cavity should be
greased with a polyurea based NLGI #1 (preferred
grease). Other grease types may yield adequate
performance. The grease maintenance interval is 6
months. Grease can be added by using a grease gun
to fill until the relief valve opens and expels
additional grease.
The relief valve may open up and expel additional
grease during the first thermal cycle. This is normal
where about ¼ ounce of grease may be relieved.
WWW. MPPUMPS. COM
Form 3064-A
9/03
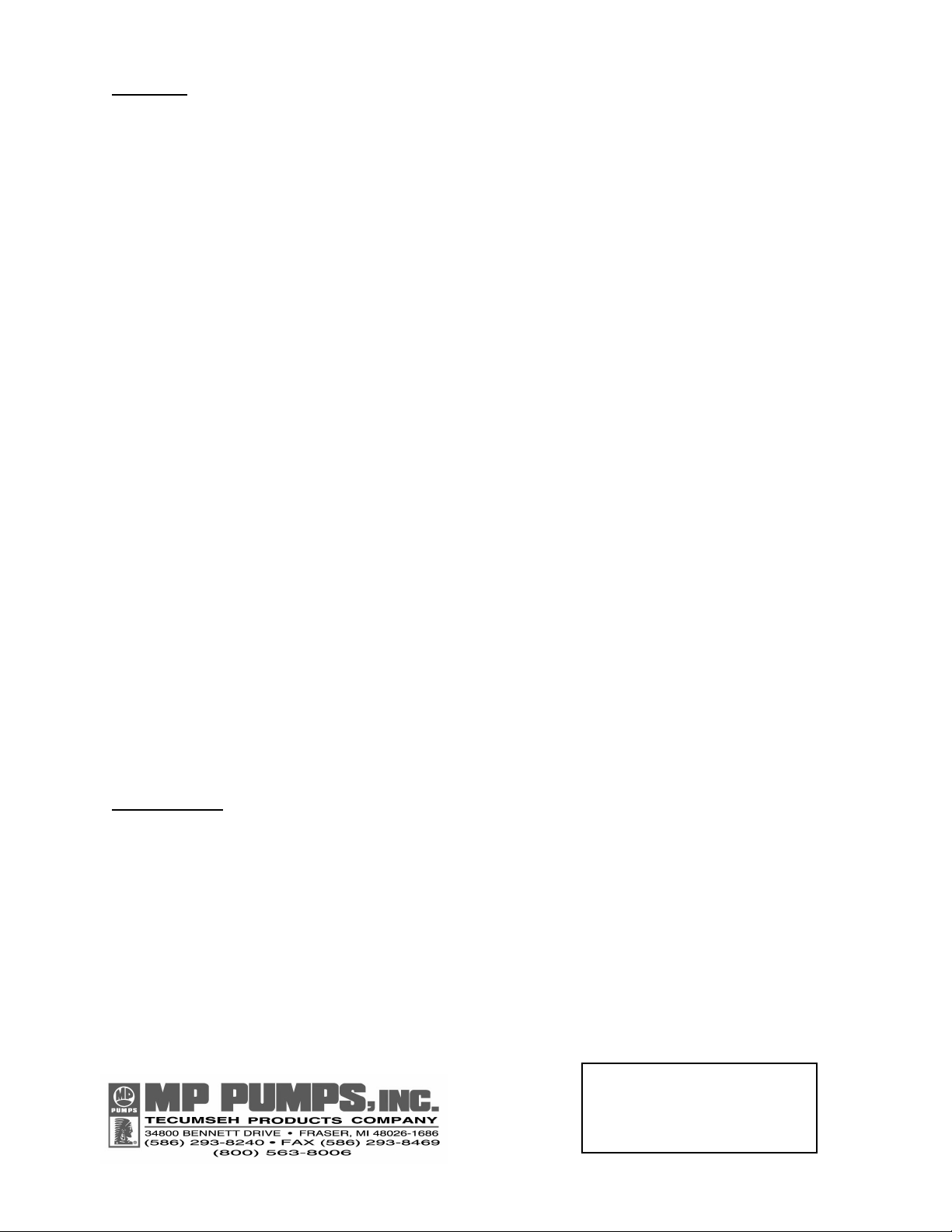
REBUILD:
Use the exploded parts view with these instructions
and note recommended replacement parts for the
rebuild process.
3. Install the housing gasket over the housing studs
and position it on the housing gasket face.
1. Disconnect and removed the pump end from the
driver.
2. Relieve the double seal cavity pressure by
pulling the pin on the relief valve.
3. Remove and replace the flapper assembly and
discharge gasket. Tighten the inlet and discharge
flange fasteners to 24 ft-lbs.
4. Remove 6 nuts from the adaptor and disassemble
the rotating assembly form the housing.
5. Inspect the wearplate for abrasive wear and
replace if necessary using new screws, gaskets
and acorn nuts.
6. Clean and remove all grease from the adaptors
and impeller sleeve. Discard the seal rotating
parts.
7. Remove the seal seats from the adaptors and
discard.
8. FM5&8 impellers are threaded onto a drive
sleeve and fastened with a jam nut. The sleeve
of a FM10&15 is an integral part of the impeller.
9. Inspect the impeller for abrasive wear at the
edges of the machined surfaces. If they are not
well defined the impeller should be replaced.
10. Remove the grease reservoir from the adaptor.
REASSEMBLE:
4. Slide the double seal adaptor over the impeller
and studs with the relief valve properly aligned
and the seal seat facing up. The adaptor should
rest on the pump housing gasket squarely.
5. Using a water-soluble lubricant, lubricate the
impeller sleeve and the seal rotary bellows inner
diameters.
6. Install the seal rotary with the hard silicon
carbide face so that the face is against the seal
seat. Use care to push on the tail of the bellows
and not on the seal head outer diameter.
7. Position the spring over the sleeve onto the seal
head.
8. Install the remaining seal rotary (carbon face) tail
first over the sleeve to make contact with the
spring.
9. Place another housing gasket over the studs and
install the driver adaptor onto the pump
assembly to compress the seal spring. Tighten 6
nuts with lockwashers to 28 ft-lbs. with a
crosswise pattern.
10. Slide the drive sleeve clamp assembly on the
sleeve.
11. Pull the clamp assembly and sleeve back out of
the pump and slide a shim inside the pump
discharge between the wearplate and impeller
vanes. Shim material thickness should be .02.03 inches.
1. Using a water-soluble lubricant, lubricate the
seal seat o-rings and seal housing bores. Install
new seal seats into the adaptors with the polished
sides of the seat up. Install by hand using your
thumbs to squarely locate the seats against the
shoulder of the adaptors. Wipe the seal faces dry
with a rag.
2. Place the impeller inside the pump housing.
12. Fill the seal cavity with grease using a suitable
grease gun until grease comes out of the pipe tee
(approx. 9 ounces).
13. Install and tighten the reservoir
14. Add more grease to fill the reservoir until the
relief valve opens.
The pump can now be installed to the driver as a
pumpak.
WWW. MPPUMPS. COM
Form 3064-A
9/03