
Section:
MOYNO® 500 PUMPS
Page: 1 of 8
Date: March 1, 1998
SERVICE MANUAL
MOYNO® 500 PUMPS
300 SERIES
331, 332, 333, 344, 356 AND 367 MODELS
Mechanical Seal Models
Packing Gland Models
MODELS
DESIGN
FEATURES
33101 34401
33201 35601
33301 36701
33104 34404
33204 35604
33304 36704
33108 33308
33208 34408
34411
35611
35613
Housing: Cast Iron AISI 316 SS Nylon Cast Iron AISI 316 SS
Pump Rotor:
Chrome plated
416 SS
Chrome plated
316 SS
Chrome plated
416 SS
Chrome plated
416 SS
Chrome plated
316 SS
Pump Stator: NBR (Nitrile) NBR (Nitrile) NBR (Nitrile) NBR (Nitrile) NBR (Nitrile)
Shaft: 416 SS 316 SS 416 SS 416 SS 316 SS
Flexible Joint: Carbon steel/
NBR
316 SS/
NBR
Carbon steel/
NBR
Carbon steel/
NBR
316 SS/
NBR
Bearings: Ball (sealed) Ball (sealed) Ball (sealed) Ball (sealed) Ball (sealed)
Mechanical Seal: Carbon-ceramic Carbon-ceramic Carbon-ceramic --- ---
Packing:
--- --- --- Braided PTFE
Braided PTFE
Note: Alternate elastomers available. Refer to Repair/Conversion kit numbers, page 8.
INSTALLATION
Mounting Position. Pump may be mounted in any
position. When mounting vertically, it is necessary to keep
bearings above seals to prevent possible seal leakage into
bearings.
Pre-Wetting. Prior to connecting pump, wet pump
elements and mechanical seal or packing by adding fluid to
be pumped into suction and discharge ports. Turn shaft
over several times in a clockwise direction to work fluid into
elements.
Piping. Piping to pump should be self-supporting to avoid
excessive strain on pump housings. See Table 1 for suction
and discharge port sizes of each pump model. Use pipe
“dope” or tape to facilitate disassembly and to provide seal.
Drive. On belt driven units, adjust belt tension to point of
non-slip. Do not overtighten.
On direct drive units, coupling components should be
aligned and spaced at least 1/16” apart.
Pump rotation must be clockwise when facing shaft to
prevent damage to pump. Check direction of rotation before
startup.
Water Flush of Packing (356 Models Only). The packing
may be either grease lubricated through a grease fitting in
the stuffing box or have plumbing connected to the housing
to allow a water flush.
Maximum speed is 1750 rpm.
When the material being pumped is abrasive in nature, it
may be advantageous to flush the packing to prevent
leakage under packing and excessive shaft wear.
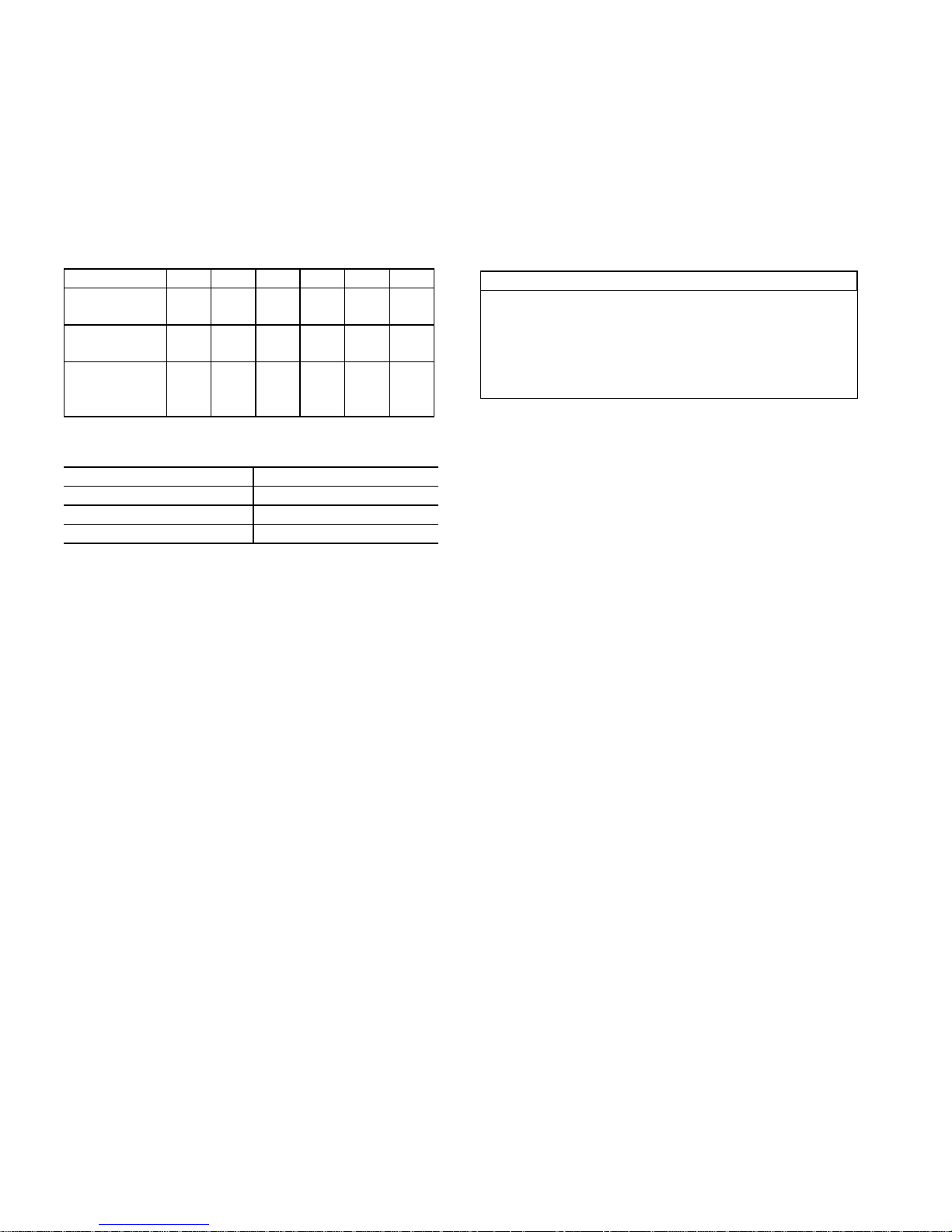
Page 2
Clean water can be injected through a 1/8” NPT tapped
hole that normally houses the grease fitting for lubricating the
packing. The water can be permitted to leak axially along the
shaft in either direction or can be removed from the second
tapped hole in the stuffing box. In both cases, the discharge
from the stuffing box should be throttled slightly to maintain
10-15 PSI higher pressure in the stuffing box than is present
in the discharge housing.
Table 1. Pump Data
Pump Models
Suction Port
(NPT)
Discharge
Port (NPT)
331 332 333 344 356 367
3/4* 3/4* 3/4* 3/4* 1-1/2 2
3/4 3/4 3/4 3/4 1-1/4 2
Discharge
Pressure
150 100 50 40 50 50
(psig)
*08 versions = 1” NPT
Table 2. Temperature Limits
Elastomer Temperature Limits
*NBR 10°-160°F
*EPDM 10°-210°F
*FPM 10°-240°F
*NBR = Nitrile
*EPDM = Ethylene-Propylene-Diene Terpolymer
*FPM = Fluoroelastomer
OPERATION
Self-Priming. With wetted pumping elements, the pump is
capable of 25 feet of suction lift when operating at 1750 rpm
with pipe size equal to port size.
DO NOT RUN DRY. Unit depends on liquid pumped for
lubrication. For proper lubrication, flow rate should be at least
10% of rated capacity.
Pressure and Temperature Limits. See Table 1 for
maximum discharge pressure of each model. Unit is suitable
for service at temperatures shown in Table 2.
Storage. Always drain pump for extended storage periods
by removing suction housing bolts and loosening suction
housing.
TROUBLE SHOOTING
WARNING: Before making adjustments, disconnect
Failure To Pump.
1. Belt or coupling slip: Adjust belt tension or tighten set
screw on coupling.
2. Stator torn; possibly excessive pressure: Replace stator,
check pressure at discharge port.
3. Wrong rotation: Rotation must be clockwise when facing
shaft.
power source and thoroughly bleed
pressure from system. Failure to do so
could result in electric shock or serious
bodily harm.
4. Threads in rotor or on shaft stripped: Replace part. Check
for proper rotation.
5. Excessive suction lift or vacuum.
Pump Overloads.
1. Excessive discharge pressure: Check discharge pressure
for maximum rating given in Table 1. Check for
obstruction in discharge pipe.
2. Fluid viscosity too high: Limit fluid viscosity to 20,000 CP
or 100,000 SSU.
Viscosity CP Limit RPM
1-300 1750
300-1,000 1200
1,000-2,000 700
2,000-5,000 350
5,000-10,000 180
10,000-20,000 100
3. Insufficient motor HP: Check HP requirement.
Noisy Operation.
1. Starved suction: Check fluid supply, length of suction line,
and obstructions in pipe.
2. Bearings worn: Replace parts; check alignment, belt
tension, pressure at discharge port.
3. Broken flexible joint: Replace part, check pressure at
discharge port.
4. Insufficient mounting: Mount to be secure to firm base.
Vibration induced noise can be reduced by using mount
pads and short sections of hose on suction and discharge
ports.
Mechanical Seal Leakage (Mechanical Seal Models
Only).
1. Leakage at startup: If leakage is slight, allow pump to run
several hours to let faces run in.
2. Persistent seal leakage: Faces may be cracked from
freezing or thermal shock. Replace seal.
Packing Leakage (Packing Models Only).
1. Leakage at startup: Adjust packing as outlined in
maintenance instructions.
Note: Slight leakage is necessary for lubrication of packing.
2. Persistent leakage: Packing rings and/or shaft may be
worn. Replace parts as required.
Pump Will Not Prime.
1. Air leak on suction side: Check pipe connections.
MAINTENANCE
General. These pumps have been designed for a minimum
of maintenance, the extent of which is routine lubrication and
adjustment of packing. The pump is one of the easiest to
work on in that the main elements are very accessible and
require few tools to disassemble.
Packing Lubrication (356 Models Only). The zerk
fitting on the side of the suction housing leads to the lantern
ring halves in the mid-section of the packings. At least once a
week, inject a small quantity of good quality grease, such as
MPG-2 Multi Purpose Grease (Du Bois Chemical), or
equivalent, into the zerk fitting to lubricate the packings.
Note: For Model 34411, lubricate packing by applying a
liberal amount of grease during assembly.