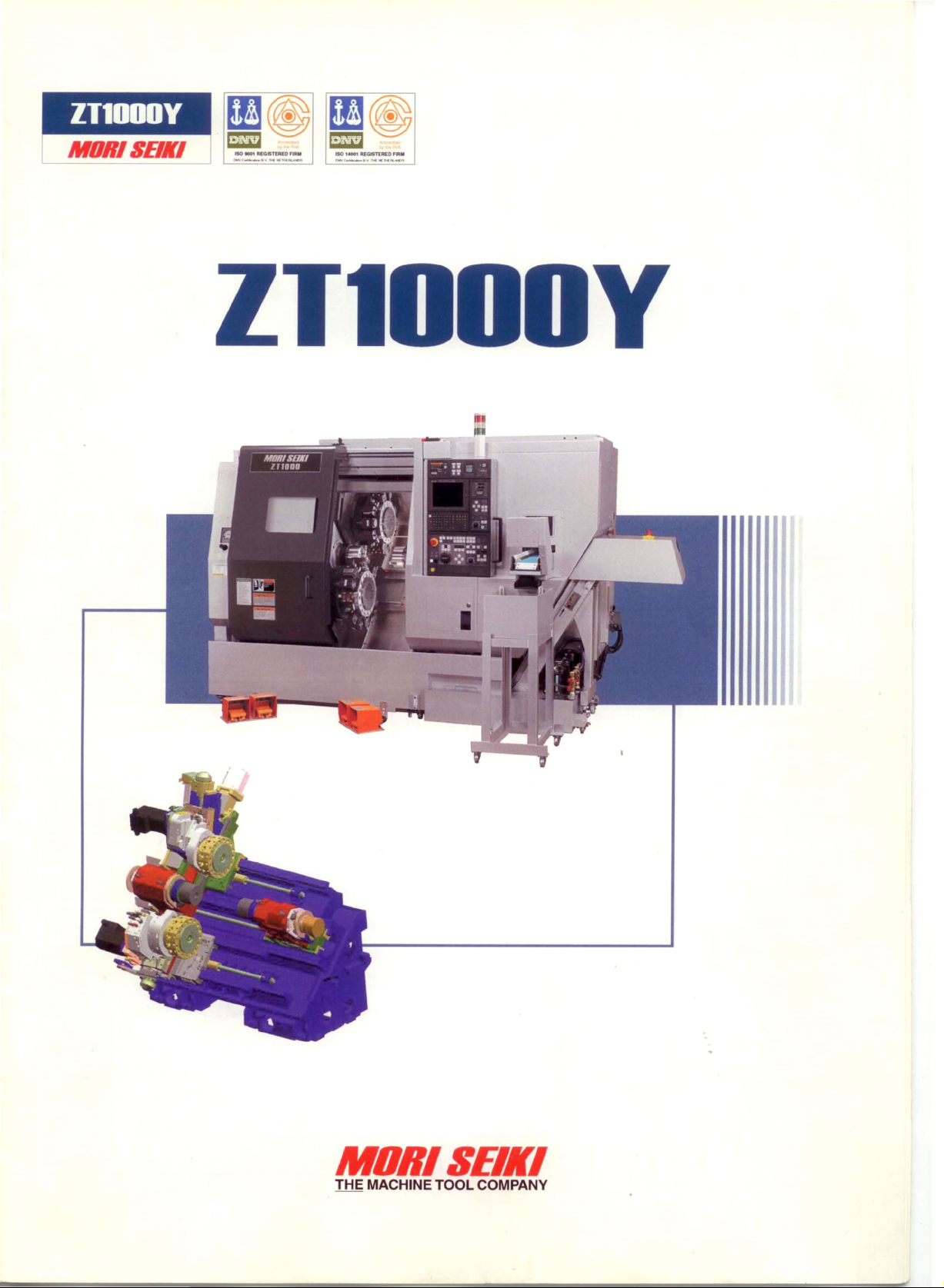
lTl000Y
MORI SElli
., ••• ~1nDlLDAUI 1:10,--.
_c-."......-__ _c- ....
1IIlGISTl1IIUI,....
M...-N ••.-
MORISElli
THE MACHINE TOOL COMPANV
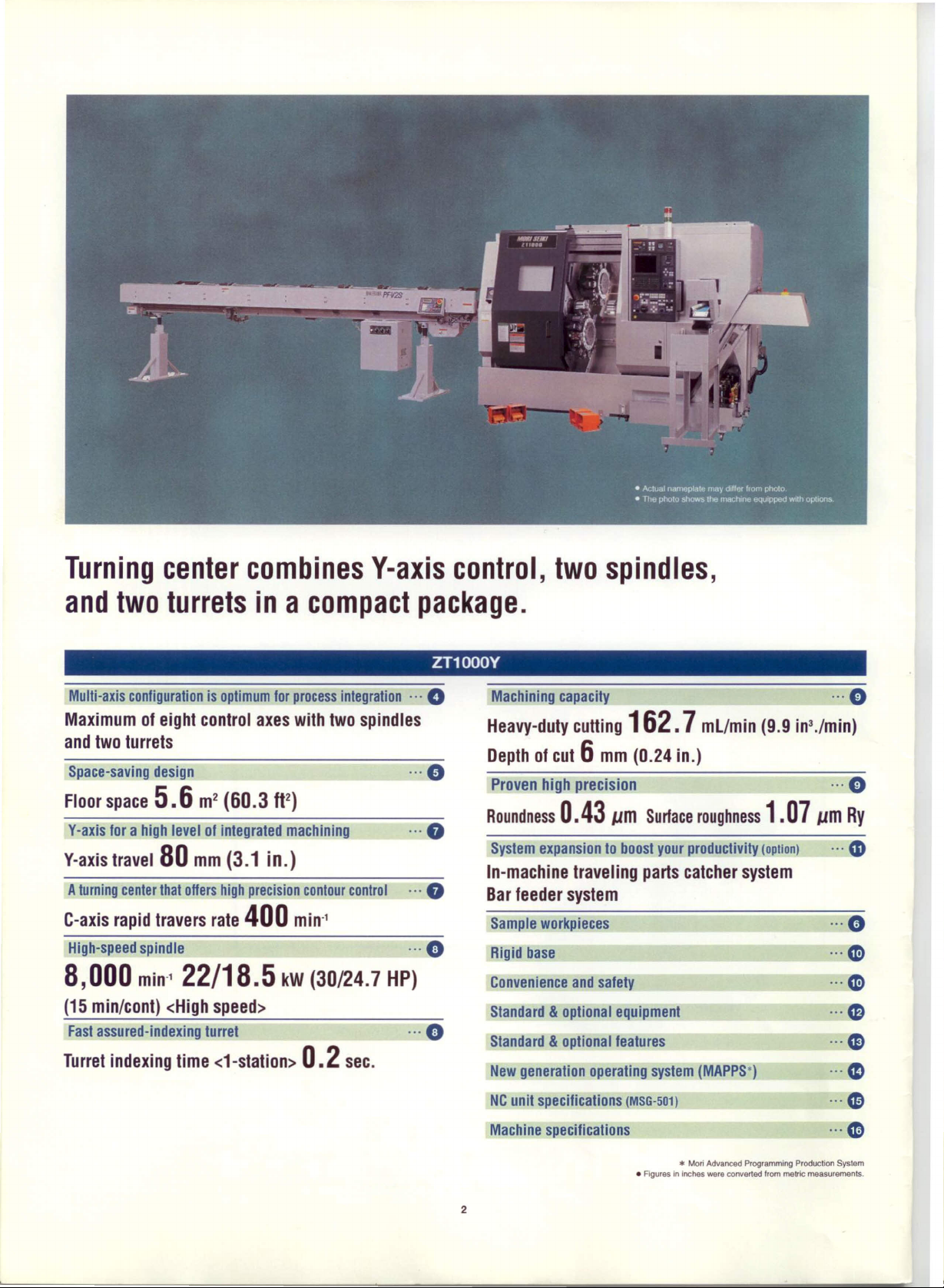
Turning center combines Y-axis control, two spindles,
and two turrets in a compact package.
ZT1000Y
Multi-axis configuration is optimum for process integration ...
Maximum01eight control axes with two spindles
and two turrets
Space-saving design ...
Floor space
Y-axis for a high level of integrated machining ...
Y-axis travel
Aturning centerthat offers high precision contour control ...
C-axis rapid travers rate
High-speed spindle ...
8,000
(15 mìn/com) <High
Fast assured-indexing turret ...
Turret indexing time et-statlon»
5.6
80
min·
2
m
(60.3 It
mm
(3.1 in.)
1
22/18.5
speens
2
)
400
mln'
kW (30/24.7 HP)
0.2
sec.
o
e
O
O
O
O
Machining capacity ...
Heavy-duty cutting
Depth01cut6mm (0.24 in.)
Proven high precision ...
Roundness
System expansion to boost your productivity
In-machine traveling parts catcher system
Bar leeder system
Sample workpieces
Rigid base
Convenience and safety
Standard&optional equipment
Standard&optional features
New generation operating system (MAPPS*)
NCunit specifications
Machine specifications ...
0.43
162.7
,.,m
Surface roughness
(MSG·501) •••
mL/min (9.9 in3./min)
1.07
(oplion) ...
,.,m
O
O
Ry
CD
O
O
O
G
eD
CD
CD
G
*
• Agures In inches were converted tram metrk: measurements.
2
Mori Advanced Programmlng Production System
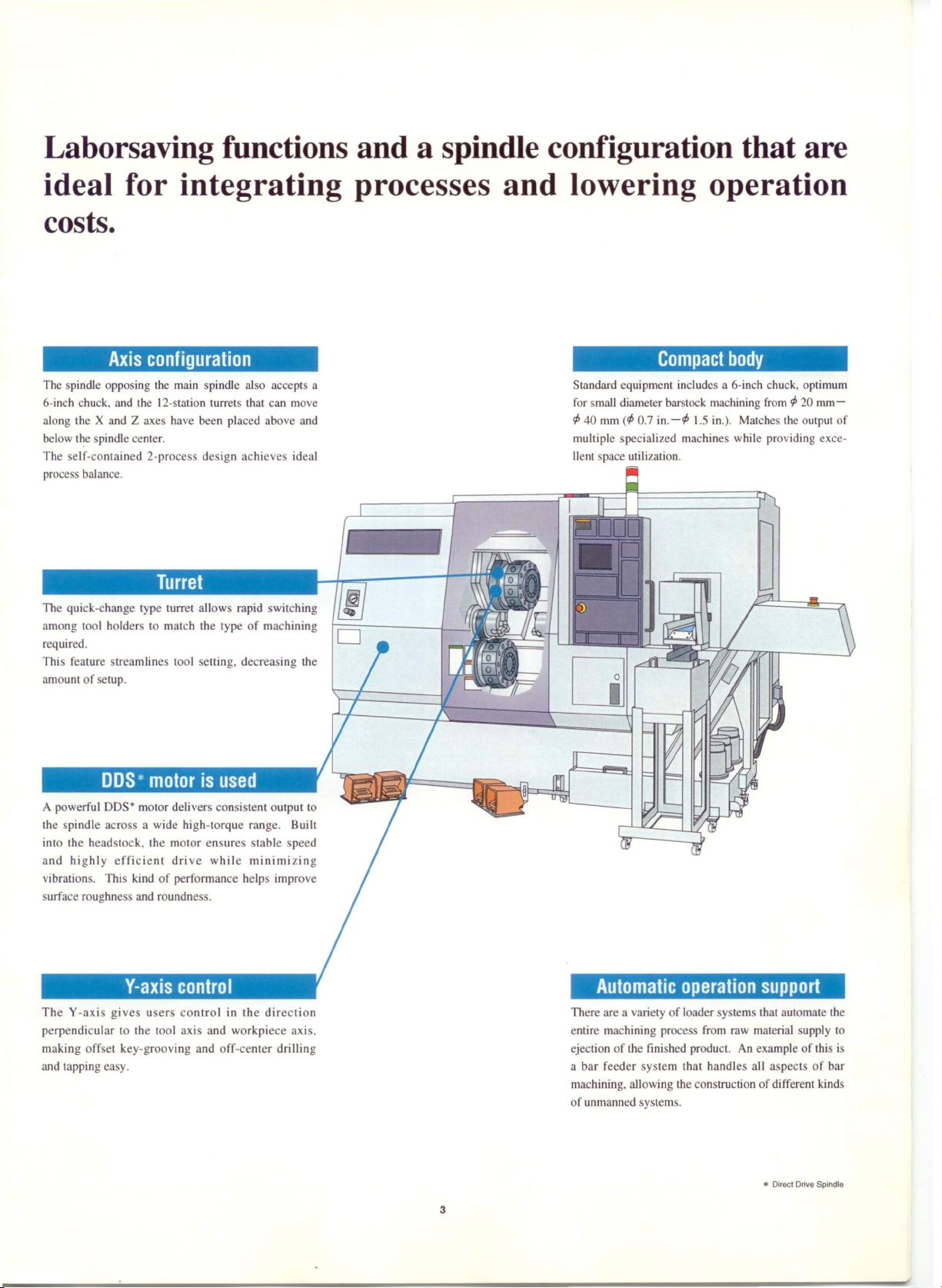
Laborsaving functions and a spindle configuration that are
ideai for integrating processes and lowering operation
costs.
Axis configuration
The spindle oppo ing the main spindle al o accepts a
6-inch chuck, and the 12-station turret that can move
along the X and Z axes have been placed above and
below l~e spindle center.
The seI f-contained 2-process de ign achieves ideaI
proces balance.
lurret
The quick-change type turret allows rapid switching
among 1001 holders to match the type of machining
required.
Thi feature treamlines 1001 euing, decreasing the
amount of setup.
DDS*motor is used
A powerful DDS· motor delivers consistent output to
the spindle across a wide high-torque range. Built
into the headstock, the rnotor ensure stable peed
and highly efficient drive while minimizing
vibralions. This kind of performance helps improve
urface roughnes and roundnes .
Compact body
Standard equipment includes a 6-inch chuck, optimum
for small diameter barstock machining from<P20 mm+
<P
40 mm
(<p
0.7 in.
-<P
1.5 in.). Matches the output of
multiple specialized machines while providing exce-
llent space utilizalion.
o
The Y-axi gi ves users control in the direction
perpendicular lO the 1001 axi and workpiece axi ,
making off et key-grooving and off-center drilling
and tapping easy.
Automatic operation support
There are a variety of loader y tems that automate the
entire machining process from raw material supply to
ejection of the fini hed producI. An example of this i
a bar feeder ystem that handles ali a pects of bar
machining. allowing the construction of different kinds
of unmanned y tem .
*
Direct Orfva Spindle
3
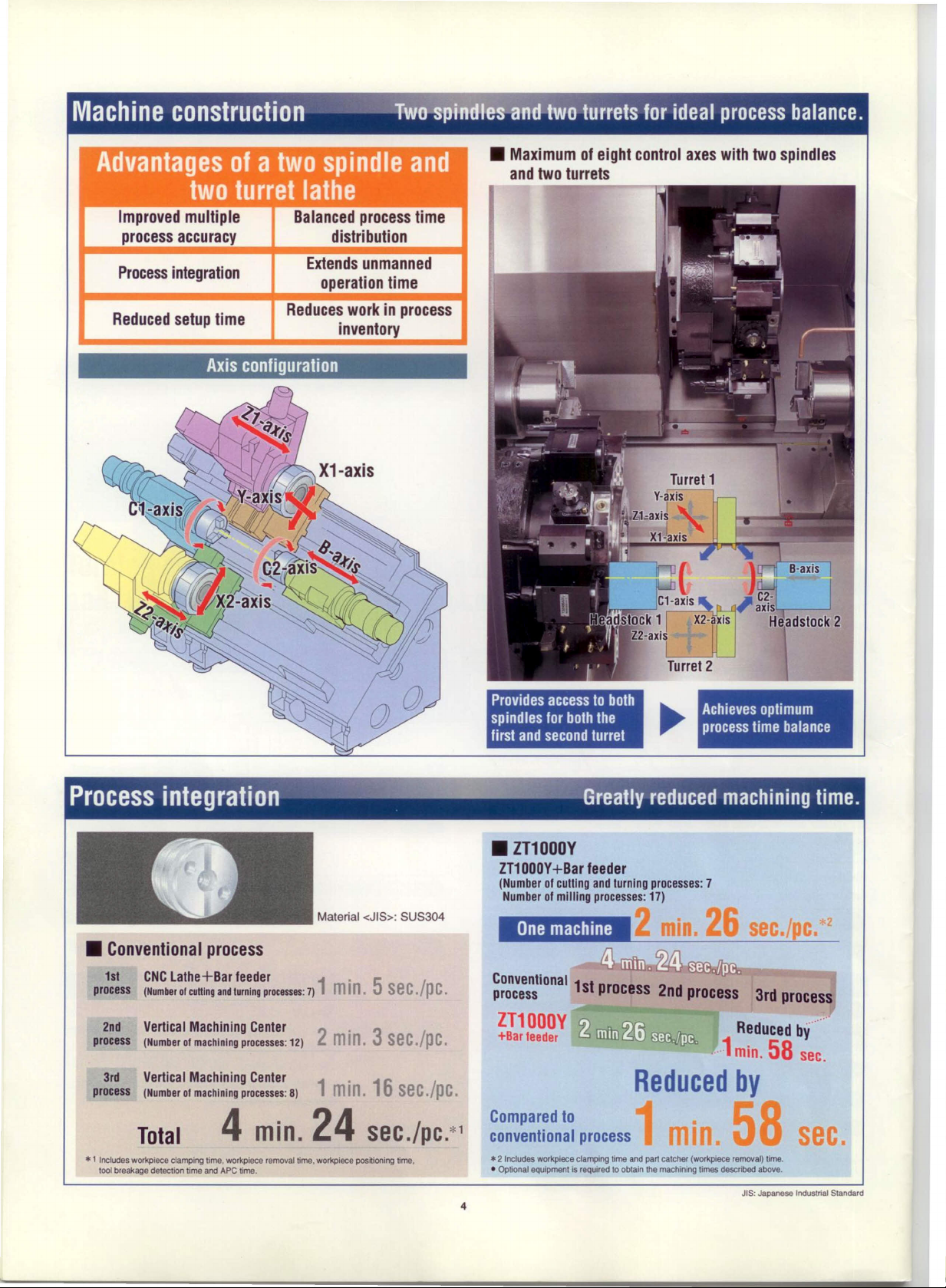
of a two spindle and
Improved multiple
process accuracy
turret lathe
Balanced process time
distribution
Processintegration
Reduced setup time
Axis configuration
Extends unmanned
operation time
Reduces work in process
inventory
Provides access lo bolh
spindles for bolh Ihe
first and second turret
Achieves optimum
process time balance
Material
<JIS>: SUS304
1s1 CNCLatha+Bar feeder
process (Number01cuttlngandlurningprocesses:7)
2nd Vertical Machining Center
process (Number 01machlnlng processes: 12)
3rd Vertical Machining Center
process (Numberolmachlnlngprocesses:8) 1
4
Total
• 1 Includes workptece clamping lime. workpiece removal lime. workpiece positioning tlme.
1001breakage detection lime and APe time.
min.
l'
mIn.5sec./pc.
2
min.3sec./pc.
min.16sec./pc.
24
sec./pc.*l
• ZT1000Y
ZT1OOOY+Bar feeder
(Number 01culling and turning processes: 7
Number 01milling processes: 17)
Onemachine
~~~::S~ional
1st process 2nd process 3rd process
ZT1000Y
+Bar leeder
Reduced
Compared to
conventional process
.2
Includes workplece clamping lime and part catcner (worl<plece removal) lime .
• Optional equipment is
4
reqUl1ed
lo obtain the machining limes descnbed above.
ec./pc.
Reducedby······
·1
min.
58
sec.
by
sec.
JIS: Japanese Industriai Standard
"'2
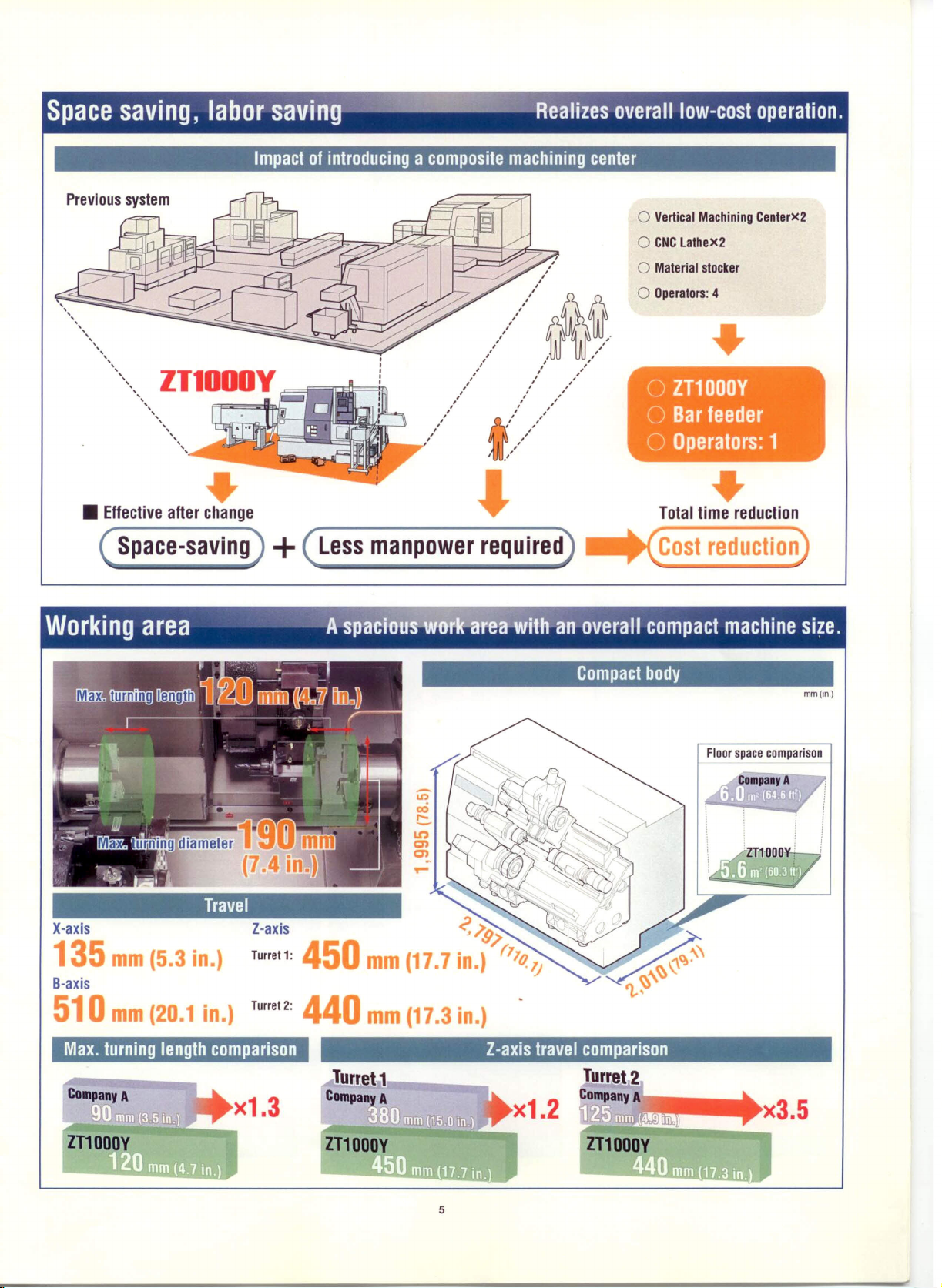
Space saving, labor saving'-Rèalizes overalllow-cosioperalion.
Impact01introducing a composite machining center
o
Vertical Machining Centerx2
o
CNClathex2
o
Material stocker
O
,
,
,
,
,
,
,
,
,
,
,
,
,
,
,
,
,
,
,
,
,
,
,
,
,
,
,
,
,
,
-,
Operators: 4
o
ZT1000Y
O
Barfeeder
O
Operalors:
•
1
• Effective after change
•
Space-saving
+
Less manpower required
Total time reduction
•
Cosl reduclion
Working area -':~òverall compaclmachinesìze.
Compact body
mm(ln.)
Floor space comparison
Travel
X-axis
135
B-axis
mm
(5.3
in.)
Z-axis
Turre! 1:
450
mm
(17.7
<';>9;>
in.)
(77Q lJ
510
Max. turning length comparison
mm
(20.1
in.)
Turre!2:
440
ZT1000Y
mm
j ,
(17.3
5
in.)
Z-axis travel comparison