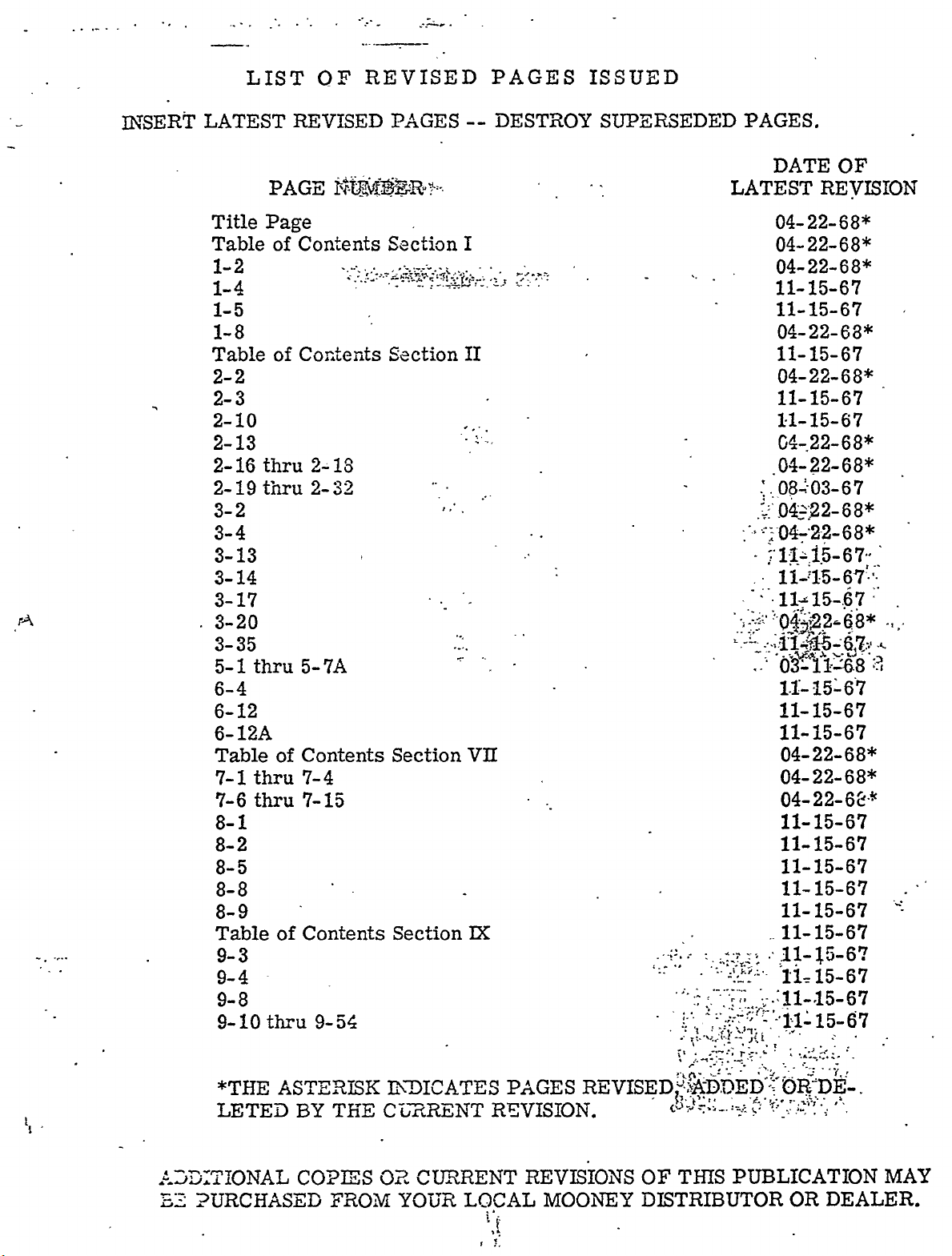
LIST
OF
REVISED
PAGES
ISSUED
~fSER’r
LATEST
Title
Table
REVISED
PAGE
Page
of
Contents
PAGES
Section
DESTROY
I
1-2
1-4
1-5
1-8
Table
2-2
of
Cor,tents
Section
II
2-3
2-10
2-13
2-16
rs,
2-
19
2
3-
3-4
3-
13
14
3-
3-17
3-20´•;
3-35
1
5-
6-4
6-12
6-12A
Table
7-1
7-6
8-1
thru
thru
thru
thru
thru
of
2;18
2-
32
7A
5-
Contents
7-4
7-
15
Section
VII
8-2
8-5
8-8
8-9
Table
9-3
9-4
9-8
9-
10
of
thru
Contents
54
9-
Section
M
SUPERSEDED
.´•´•i:.;
PAGES.
LATEST
r´•
.t_:
DATE
OF
REVISION
04-
22-
04-22-68"
04-22-68*
11-
15-67
11-15-67
04-22-68"
11-
15-
04-22-68"
11-15-61
11-15-67
04-22-68"
04-22-68"
03-
081
’10~-’9-2-68"
l~´•.i-
11-’15-67--
’olii~2-
i)
E~8
11-15-67
11-15-67
04-22-68"
22-
04-
22-
04-
11-15-67
11-15-67
11-15-67
11-15-61
11-15-67
11-15-67
~1-
15-67
:ll-d5-S7
68"
67
7
6
7´•´•
6
s*
68"
6%´•~
´•e
;rt
83
3URCHASED
*THE
LETED
kSTE~ISK
BY
COP~S
TIiE
FRO1Vi
~IzATEs
0~3*
CI~RENT
YO’iiFC
R~VISION.
LOCAL
PXGES
REVISIONS
MOONEY
i.’´•
TKIS
OF
DISTRIBUTOR
’O~DE-.
PUBLICATION
OR
MAY
DEALER.
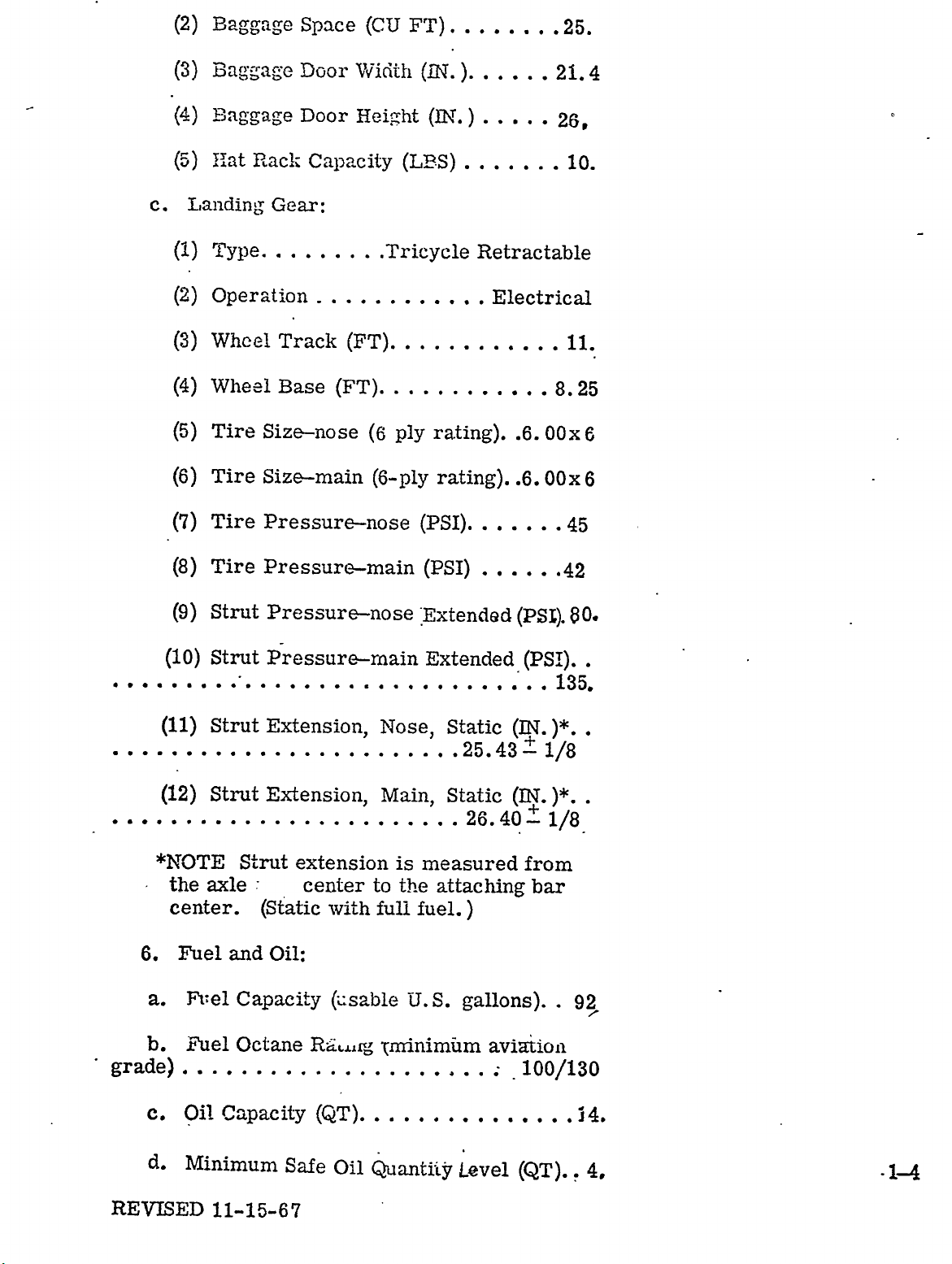
(2)
Baggage
Space
(CU
FT),,,,,,,,25,
c,
(3)
(bL)
(5)
Eandin~
(1)
(2)
(3)
(4)
0)
(6)
Baggage
Baggage
I:at
Racl~
Gear:
Type........
Operation
Wheel
Wheel
Tire
Tire
Tire
Size-nose
Size-main
Pressure-nose
~oor
Door
Track
Base
VJicith
Heiirht
Capacity
.Tricycle
(FT),,,.,,,,,,,.
(FT)......,.,,,,8,
(6
(6-ply
(~N.
(I]i~.
(LFS)
ply
rating),,6,
rating),,6,
(PSI).......45
Retractable
Electrical
21,
10,
II,
OOxB
00x6
4
25
Tire
(8)
Strut
(9)
Strut
(10)
the
center.
Fuel
FL:el
Strut
Strut
axle
(II)
(12)
´•´•´•´•´•´•´•´•´•´•´•´•´•´•´•´•´•´•´•´•´•´•´•´•26´•40L1/8
6,
a.
Pressure-main
Pressur~-nose
Pressure-main
Extension,
Extension,
Strut
(St’atic
and
Oil:
Capacity
extension
center
with
(r;sable
(PSI)
:ERtended
Extended
,,,,,,42
(PSI~
(PW)..
´•´•´•´•´•´•´•´•´•´•´•´•135.
measured
attaching
fuel.
U.S.
Static
43
Static
gallons).,
"1/8
from
Nose,
,,,,,25,
Main,
is
to
the
full
80´•
bar
92
b,
grade)
c,
d.
REVISED
r~el
Oil
Capacity
Minimum
11-15-67
Octane
(G~T)..............
Safe
Oil
Quantiijr
t~vel
aviation
(QT).,
.5~4.
4,
-1-4
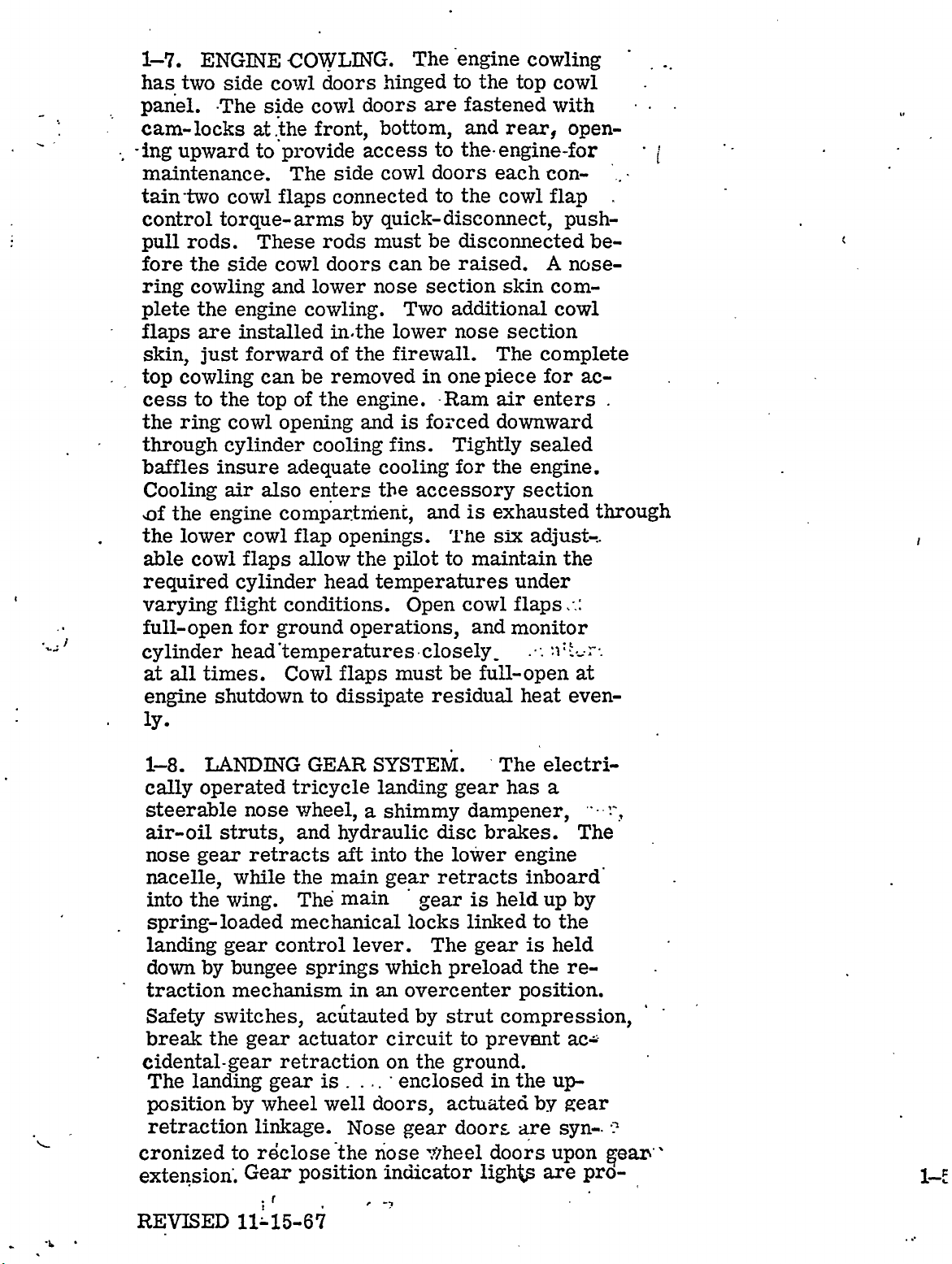
I-?.
has
ENGINE
two
panel,
cam-locks
-ing
upward
maintenance.
tain-two
control
rods.
pull
fore
plete
flaps
top
ring
skin,
cess
the
the
cowling
the
are
just
cowling
to
ring
through
baffles
Cooling
the
sf
the
lower
able
cowl
required
varying
full-open
cylinder
at
all
times.
engine
ly.
COWLJNG.
side
cowl
side
The
at.the
to
cowl
torque-arms
These
side
and
engine
installed
forward
can
the
top
cowl
cylinder
insure
air
also
engine
cowl
flaps
cylinder
fight
for
doors
cowl
doors
front,
provide
The
flaps
cowl
lower
cowling.
be
of
opening
cooling
access
side
connected
by
rods
doors
in.the
of
the
removed
the
engine.
and
adequate
enters
compartrrieni,
flap
openings.
dllow
conditions.
ground
the
head
operations,
fiinged
bottom,
cowl
quick-disconnect,
must
can
nose
Two
lower
firewall.
is
fins.
cooling
the
pilot
temperatures
Open
head’temperatures´•closely~
must
shutdown
Cowl
flaps
to
dissipate
The
engine
to
fastened
are
and
to
the´•engine-for
doors
the
to
be
disconnected
be
raised.
section
additional
nose
in
one
Ram
forced
Tightly
for
accessory
and
is
’I’he
to
maintain
cowl
and
be
residu~il
cowling
the
top
rear,
each
cowl
skin
section
The
piece
air
enters
downward
sealed
the
engine.
section
exhausted
six
adjust-..
under
flaps
monitor
full-open
heat
cowl
with
open-
con-
flap
push-
be-
A
n~se-
com-
cowl
complete
for
ac-
through
the
at
even-
1-8.
cally
steerable
LAND7NG
operated
air-oilstruts,
nose
gear
nacelle,
into
the
wing.
spring-loaded
landing
down
traction
Safety
break
gear
by
switches,
the
cidental-gear
The
landing
position
retraction
cronized
extension:
REVISED
nose
retracts
while
control
bungee
mechanism
gear
retraction
gear
wheel
by
linkage.
r$close’the
to
Gear
11;-15-61
GEAR
tricycle
wheel,
and
hydraulic
aft
the
main
main
The
mechanical
springs
in
acGtauted
actuator
is
well
Nose
position
SYSTER~.
landing
a
shimmy
into
gear
lever.
which
an
circuit
on
doors,
nose
indicator
disc
the
retracts
gear
locks
The
overcenter
strut
by
the
enclosed
gear
~heel
.The
gear
dampener,
brakes.
lower
held
is
linked
gear
preload
compression,
to
prevent
ground.
in
actuated
door~
doors
lighas
electri-
has
engine
inboard
up
to
is
the
position.
the
by
are
are
a
the
held
up
gear
syn-
upon
re-
ac~
The
by
pro-
I-E
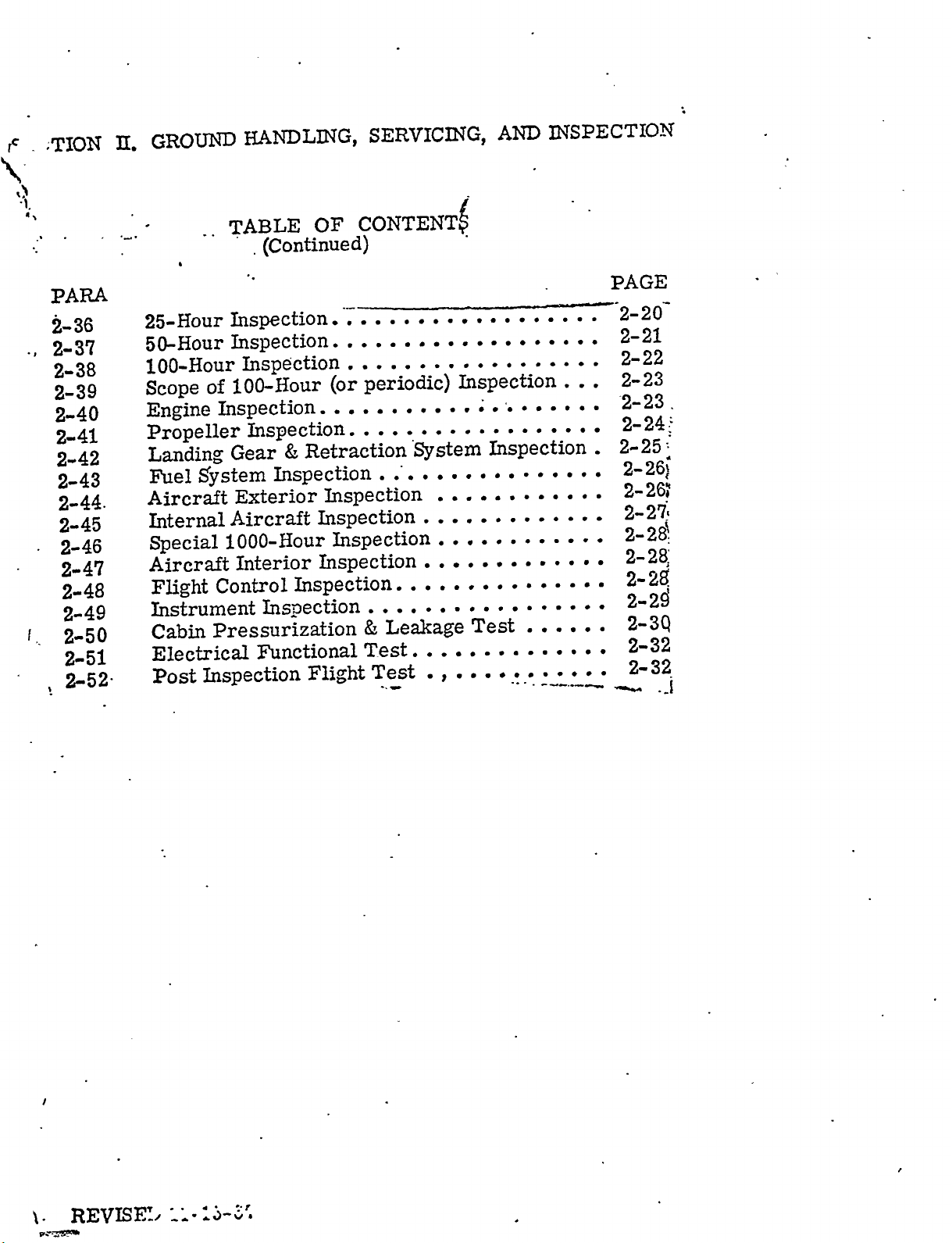
rC
;TION
II.
GROUND
HANDLING,
TABLE
(Continued)
SERVICn;IG,
CONTENTQ
OF
AND
INSPECTIOW
PARA
i-36
2-37
2-38
2-39
2-40
2-41
2-42
2-43
2-44.
2-45
2-46
2-47
2-48
2-49
2-50
2-5~
2-52´•
25-Hour
fj0-Hour
100-Hour
Scope
Engine
Inspection........´•
Inspection.
lOeHour
of
Inspection.......´•´•
Propeller
Landing
Fuel
AircraftExterior
Internal
Special
AircraftInterior
Flight
Instrument
Cabin
Electrical
Post
Gear
Sjrstem
Aircraft
1000-Hour
Control
Pressurization
Inspection
Inspection
periodic)
(or
Inspection.........´•´•´•´•´•´•
Retraction’System
Inspection
Inspection
Inspection.......´•´•
Inspection......´•´•´•
Inspection......´•´•´•
Inspection.........
Ins9ection
Leakage
Functional
Flight
Test...........´•´•´•
Test
Inspection...
Inspection
Test
PAGE
21
2-
2-22
2-23
2-23
2’
2-25]
2-26)
2-20’;
2-27
2-28!
2-28
2-28~
2-20j
2-30
2-32
2-
24
32
.,I
REVISEI/
’-.´•:j-5