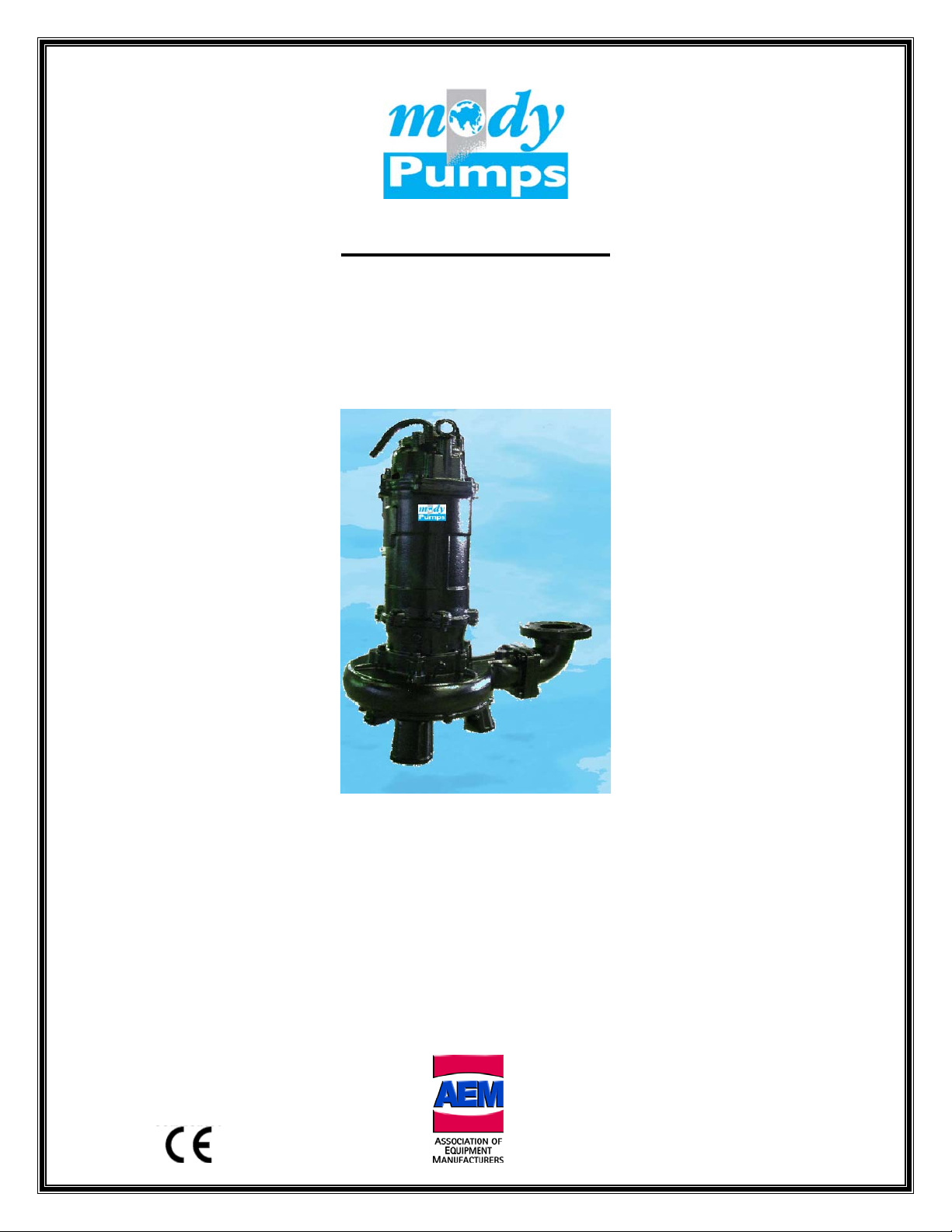
MODELS: MHC6, 10HP
OPERATING INSTRUCTIONS, INSTALLATION & MAINTENANCE
MANUAL INCLUDING SPARE PARTS LIST
Tel.: (661) 392-7600 FAX.: (661) 392-7601
EMAIL: sales@modypump.com
ISO 9001 Certified
Mody Pumps Inc.
2166 Zeus Court
Bakersfield, CA 93308
http://www.modypump.com
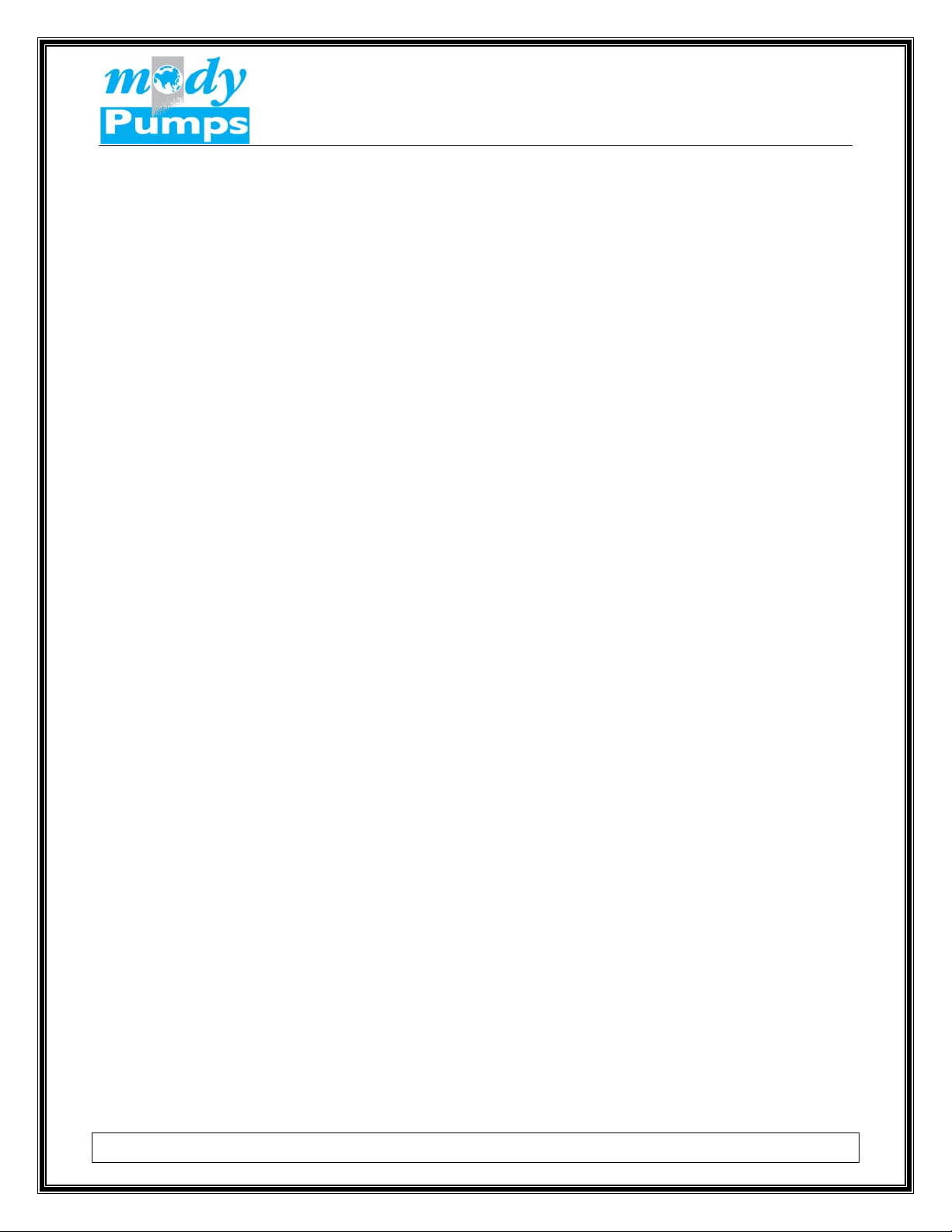
LLIIFFEE IISS PPRREECCIIOOUUSS -- TTHHIINNKK SSAAFFEETTYY
1. Most accidents can be avoided by using COMMON SENSE.
2. Please read the operation and maintenance instruction manual supplied with the
pump. If you did not receive one, please call your local distributor before pump
installation.
3. Do not wear loose apparel that may become entangled in the impeller or other
moving parts.
4. Always use appropriate safety equipment, such as safety glasses, when working on
the pump or piping.
5. Pumps build up heat and pressure during operation-allow time for pumps to cool
before handling or servicing.
6. Only qualified service personnel should install, operate and repair pump.
7. Keep clear of suction and discharge openings. DO NOT insert fingers in pump with
power connected.
8. Do not pump flammable or hazardous materials (gasoline, acids, alkalis, etc.)
9. Do not block or restrict discharge hose, as it may whip or burst catastrophically
under pressure.
10. Make sure lifting handles/hooks are securely fastened each time before lifting.
11. Do not lift pump by the power cord under any circumstances.
12. Do not exceed manufacturer's recommendation for optimum performance, as this
could cause the motor/pump to overheat and lead to premature wear or failure.
13. Secure the pump in its operating position so it does not tip over, fall or slide.
14. Keep away from impeller when power is connected.
15. Submersible Pumps are not approved for use in swimming pools, recreational water
installations, decorative fountains or any installation where human contact with the
pumped fluid is common.
16. Do not operate pump without adequate protection and safety devices in place.
17. Always replace safety devices that have been removed during service or repair.
18. To reduce risk of electrical shock, pump must be properly grounded in accordance
with the National Electric Code and all applicable state and local codes and
ordinances.
19. To reduce risk of electrical shock, always disconnect the pump from the power
source before handling or servicing.
20. Any wiring of pumps should be performed by a qualified electrician.
21. Never operate a pump with a power cord that has frayed or brittle insulation.
22. Cable should be protected at all times to avoid punctures, cuts, and
abrasions - inspect frequently.
23. Never handle connected - "hot" power cords with wet hands.
24. Never operate a pump with a plug-in type power cord without a ground fault circuit
interrupter, adequate overload and short circuit protection.
IMPORTANT !!! MODY Pumps Inc. is not responsible for losses, injury, or death resulting
from a failure to observe these safety precautions, misuse or abuse of pumps or
equipment.
Mody Pumps Inc.
:
2166 Zeus Court, Bakersfield, CA 93308 Tel.: (661) 392-7600 Fax: (661) 392-7601
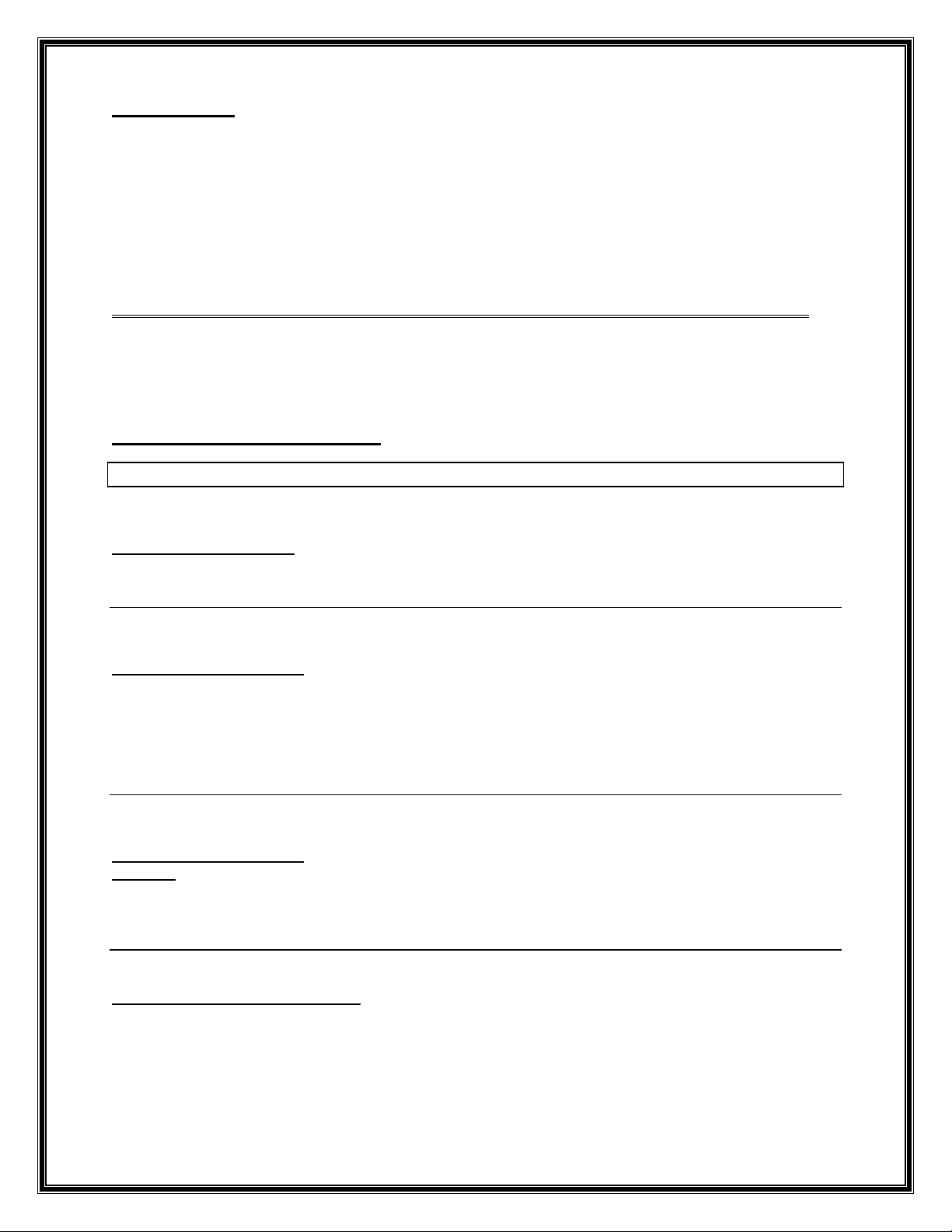
PURPOSE:
THE PUMP HAS BASICALLY BEEN DESIGNED AS A HIGH CHROME UNIT WITH AN OPTIONAL
AGITATOR TO PUMP OUT FLOODED INSTALLATIONS OR ANY CONDITIONS THAT NEED
DEWATERING OF UNWANTED FLUIDS. THE PUMP HAS BEEN DESIGNED TO HANDLE WATER
CONTAMINATED WITH OIL AS WELL AS ABRASIVE PARTICLES NORMALLY ASSOCIATED WITH
RAW WATER. THE MAXIMUM SIZE OF PARTICLES THAT CAN BE HANDLED IS APPROX. 2.4”.
THE MAXIMUM SPECIFIC GRAVITY OF THE PUMPED FLUID SHOULD NOT EXCEED 1.1.
MAINS VOLTAGE AT SITE HRC FUSE RECOMMENDED
220 VOLTS / 3 PHASE 20 AMPERES
380 VOLTS / 3 PHASE 16 AMPERES
460 VOLTS / 3 PHASE 15 AMPERES
FAULT FINDING IN THE UNIT.
TROUBLE GUIDE CAUSE REMEDY
1.FUSES BLOWN. 1.REPLACE FUSES
2.CABLE DAMAGED 2.SHORTEN/REPLACE CABLE
PUMP DOES NOT START.
4.BLOCKED IMPELLER. 4.CLEAN BOTTOM PARTS.
6.STATOR WINDING BURNT. 6.REPLACE STATOR/REWIND
1.BLOCKED IMPELLER. 1.CLEAN BOTTOM PARTS.
2.IMPELLER ROT.WRONG 2.SHIFT TWO PHASE CONN.
PUMP STARTS BUT STOPS
VOLTAGE.
4.VOLTAGE LOW/HIGH 4.CONTACT POWER CO.
5.CLOGGED STRAINER 5.CLEAN STRAINER
6.PUMP RUNNING DRY 6.SWITCH OFF POWER
7.WATER TOO WARM 7.SWITCH OFF POWER
(ABOVE 60 DEGREES C)
1.IMPELLER ROT.BACKWARD. 1.SHIFT TWO PHASE CONN.
2.PUMP WORN DOWN. 2.REPLACE WEAR PARTS
PUMP GIVES TOO LITTLE
OUTPUT
4.PRESSURE HEAD TOO HIGH 4.USE PUMPS IN TANDEM.
5.DISCHARGE HOSE TORN 5.USE NEW HOSE
6.LEAKING/CRACKED OUTLET 6.REPL.OUTLET/GASKET.
TOO SMALL.
3.NO POWER. 3.CHECK POWER SUPPLY.
. 3.CONNECTED FOR WRONG 3.CHECK & RECONNECT.
3.LONG HOSE AND DIAMETER 3.CHECK PRESSURE LOSSES
TECHNICAL DESCRIPTION:
THE MODY SUBMERSIBLE PUMP IS IN ITSELF A COMPLETE PUMPING STATION. BESIDES A
POWER SUPPLY AND A DISCHARGE HOSE NO EXTRA EQUIPMENT IS REQUIRED. THE COMPLETE
PUMPSET IS IN A MODULAR CONSTRUCTION ENSURING GOOD AND SIMPLE SERVICEABILITY.
THE MAJOR DESIGN FEATURES ARE AS UNDER:
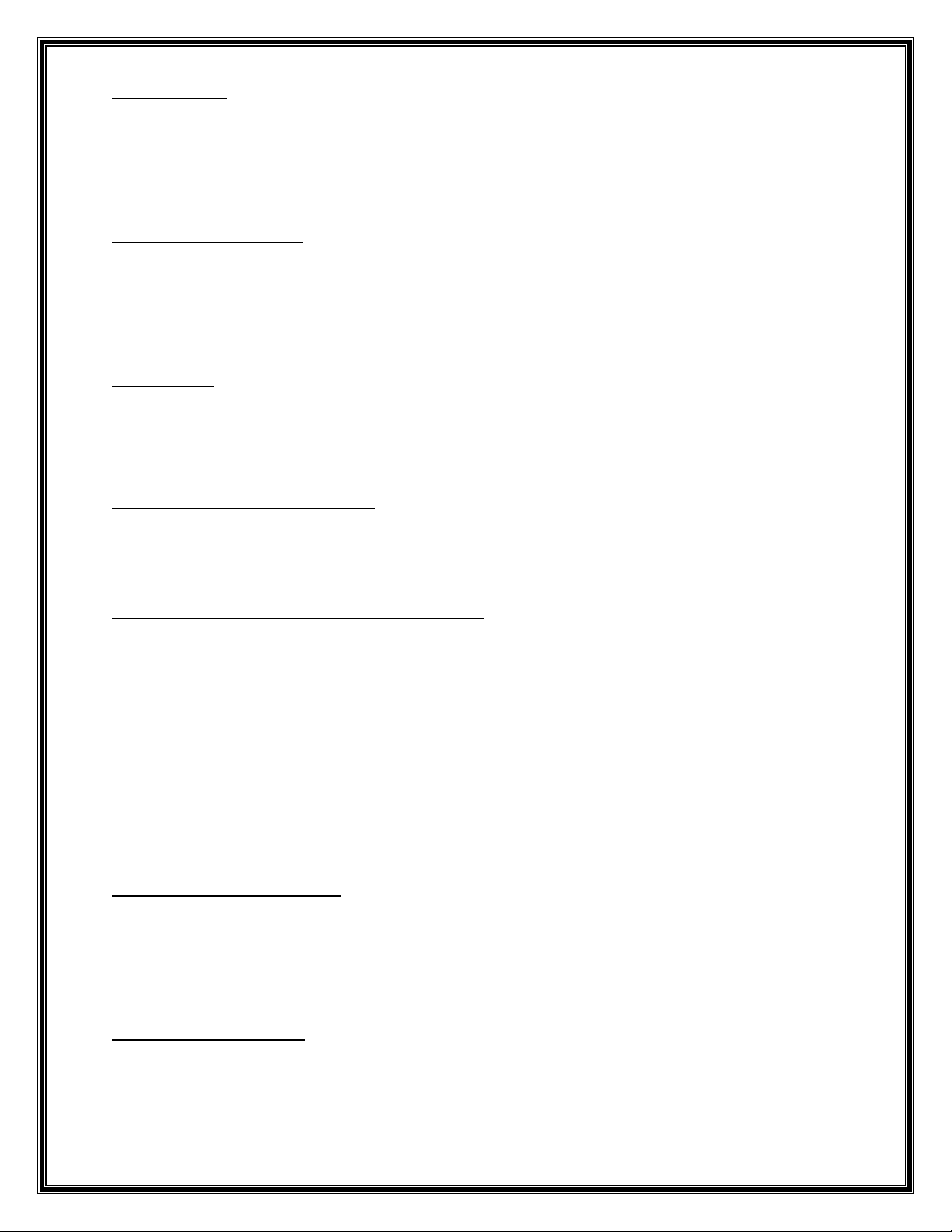
THE MOTOR
A RUGGED ALUMINUM DIE CAST/COPPER ROTOR DYNAMICALLY BALANCED TO GRADE 2.5
ACCURACY OF ISO 942.A STAINLESS STEEL SHAFT RUNNING IN TWO BALL BEARINGS.
INSULATION CLASS "H" (180 DEGREES CELSIUS). END WINDINGS DULY EPOXY COATED TO
PREVENT DETERIORATION OF INSULATION EVEN IN EXTREMELY HUMID CONDITIONS. WINDING
WIRE IS DUAL COATED SUITABLE FOR "H" CLASS INSULATION.
THE SEAL CHAMBER
THE HEART OF THE MODY PUMP. DOUBLE MECHANICAL SILICON CARBIDE V/S SILICON
CARBIDE SEAL FACES - SECONDARY SEALS OF HNBR RUBBER AND METAL PARTS IN
STAINLESS STEEL, RUNNING IN AN OIL BATH, ENCLOSED IN A PRESSURE COMPENSATING
RUBBER OIL CHAMBER - CREATES THE ULTIMATE SEAL SOLUTION. THE DESIGN OPTIMIZES
SEAL LIFE AND ALLOWS FOR SIX MONTHLY (2500 HOURS) SERVICE INTERVALS.
BEARINGS:
SINGLE ROW DEEP GROOVE UPPER BALL BEARINGS SEALED FOR LIFE WITH SPECIAL HIGH
TEMPERATURE BEARING GREASE REQUIRING NO PERIODIC MAINTENANCE WHATSOEVER.
ANGULAR CONTACT LOWER BEARINGS.
THE HYDRAULIC ELEMENTS:
28% HI-CHROME IMPELLER, SUCTION COVER, VOLUTE AND WEAR PLATE PROVIDE THE
HIGHEST LEVEL OF ABRASION RESISTANCE FOR SLURRY PUMPING.
CABLE GLAND ASSEMBLY. (REFER DRG.)
THE PUMP IS SUPPLIED WITH 25 FEET CABLE AS STANDARD. THE CABLE IS A 4 CORE EPR
SHEATHED AND INSULATED CABLE CONFORMING TO INTERNATIONAL STANDARDS. THE CABLE
IS WATERPROOF AND CAN BE COMPLETELY SUBMERGED IN WATER. THE CABLE IS TERMINATED
IN THE PUMP AT THE CABLE GLAND. THE GLAND ASSEMBLY SEALS THE CABLE ON THE
OUTSIDE SHEATH AS WELL AS A WATER DAM ARRANGEMENT IS PROVIDED WHICH SEALS THE
INDIVIDUAL CORES OF THE CABLE. THIS FEATURE IS UNIQUE AND IS ESSENTIAL TO
PREVENT WATER SEEPING THROUGH THE CORES OF THE CABLE INTO THE CONTACTOR CHAMBER
IN THE EVENT OF A CUT CABLE. THE CABLE IS ALSO SHEATHED FOR THE FIRST ONE METER
BY MEANS OF A CABLE GRIP MADE OF STAINLESS STEEL. THIS IS ESSENTIAL TO ENSURE
THAT THERE IS NO UNDUE STRAIN ON THE CABLE IF THE PUMP IS PULLED OR LOWERED
INADVERTENTLY BY MEANS OF THE CABLE. COMPLETE DETAILS OF THE CABLE GLAND
ASSEMBLY ARE SHOWN IN THE DRAWING.
NON REPAIRABLE ITEMS
1. ALL "O" RINGS TO BE REPLACED WHENEVER PARTS ARE DISMANTLED.
2. SEAL ELASTOMER PARTS SHOULD NEVER BE RE-USED AFTER DIS-ASSEMBLY.
3. DO NOT REFILL BEARING GREASE. ALWAYS REPLACE COMPLETE NEW BEARING WITH
SPECIAL HIGH TEMPERATURE GREASE.
OIL SPECIFICATIONS
USE NON-CONDUCTING, NON-FOAMING OIL ONLY
A) H.P. ENKLO OIL 46/48
B) SHELL TELLUS 29.
C) CHEVRON SUPERLA WHITE # 9