
TECHNICAL & SERVICE MANUAL
Model nameModel name
PEFY-P72NMHSU-E
PEFY-P96NMHSU-E
2011
AIR CONDITIONERS
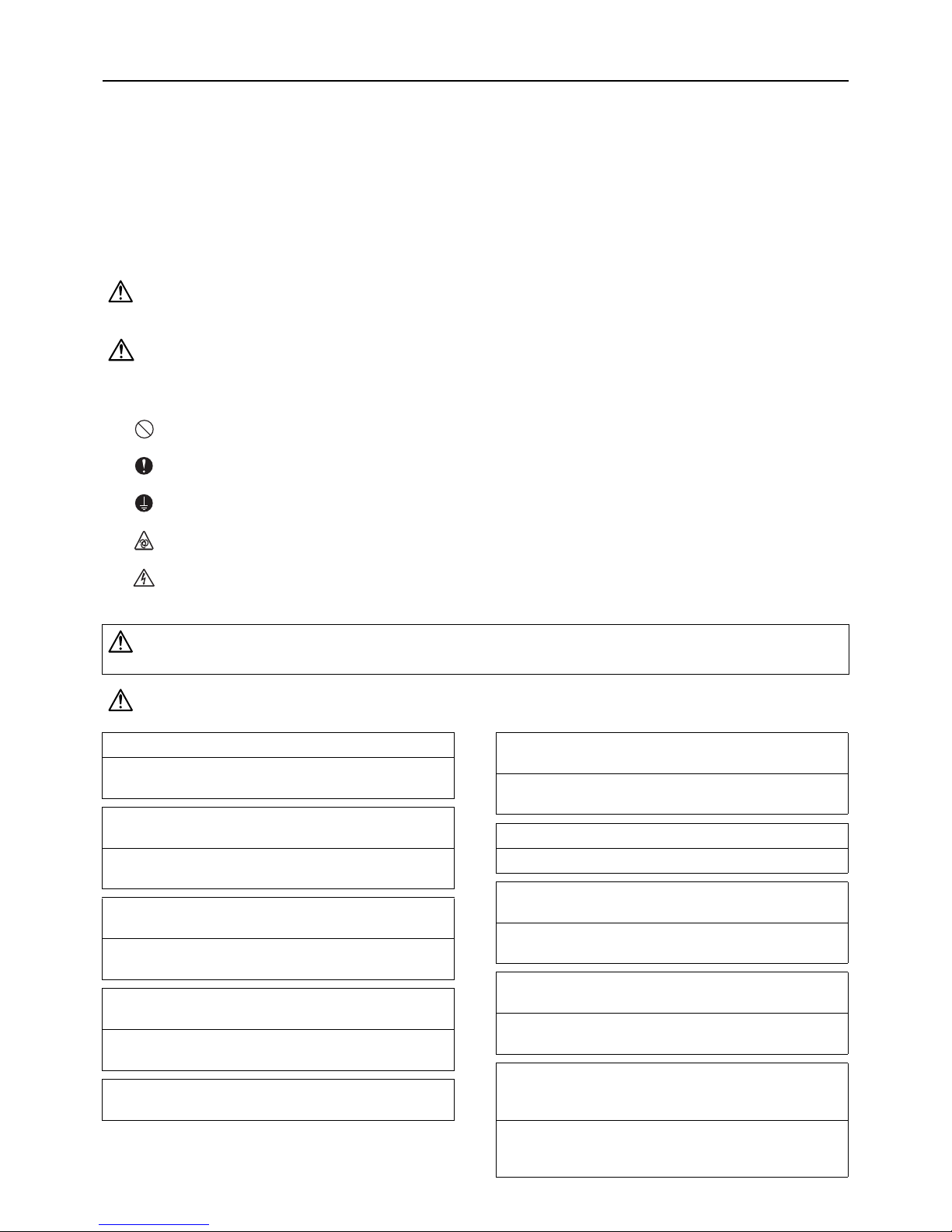
ii
HWE10170 GB
Safety Precautions
Read before installation and performing electrical work
Symbol explanations
Thoroughly read the following safety precautions prior to installation.
Observe these safety precautions for your safety.
This equipment may have adverse effects on the equipment on the same power supply system.
Contact the local power authority before connecting to the system.
This symbol indicates that failure to follow the instructions exactly as stated poses the risk of serious injury or death.
This symbol indicates that failure to follow the instructions exactly as stated poses the risk of serious injury or dam-
age to the unit.
Indicates an action that must be avoided.
Indicates important instructions.
Indicates a parts that requires grounding.
Indicates that caution must be taken with rotating parts. (This symbol is on the main unit label.) <Color: Yellow>
Indicates that the parts that are marked with this symbol pose a risk of electric shock. (This symbol is on the main
unit label.) <Color: Yellow>
Carefully read the labels affixed to the main unit.
Ask your dealer or a qualified technician to install the unit.
Improper installation by the user may result in water leakage, electric shock, or fire.
Properly install the unit on a surface that can withstand its
weight.
Unit installed on an unstable surface may fall and cause injury.
Only use specified cables. Securely connect each cable so
that the terminals do not carry the weight of the cable.
Improperly connected cables may produce heat and start a
fire.
Take appropriate safety measures against wind gusts and
earthquakes to prevent the unit from toppling over.
Improper installation may cause the unit to topple over and
cause injury or damage to the unit.
Only use accessories (i.e., air cleaners, humidifiers, electric
heaters) recommended by Mitsubishi Electric.
Do not make any modifications or alterations to the unit.
Consult your dealer for repair.
Improper repair may result in water leakage, electric shock,
or fire.
Do not touch the heat exchanger fins with bare hands.
The fins are sharp and pose a risk of cuts.
In the event of a refrigerant leak, thoroughly ventilate the
room.
If gaseous refrigerant leaks out and comes in contact with
an open flame, toxic gases will be generated.
Properly install the unit according to the instructions in the
Installation Manual.
Improper installation may result in water leakage, electric
shock, or fire.
Have all electrical work performed by an authorized electrician according to the local regulations and the instructions
in this manual. Use a dedicated circuit.
Insufficient power supply capacity or improper installation
of the unit may result in malfunctions of the unit, electric
shock, or fire.
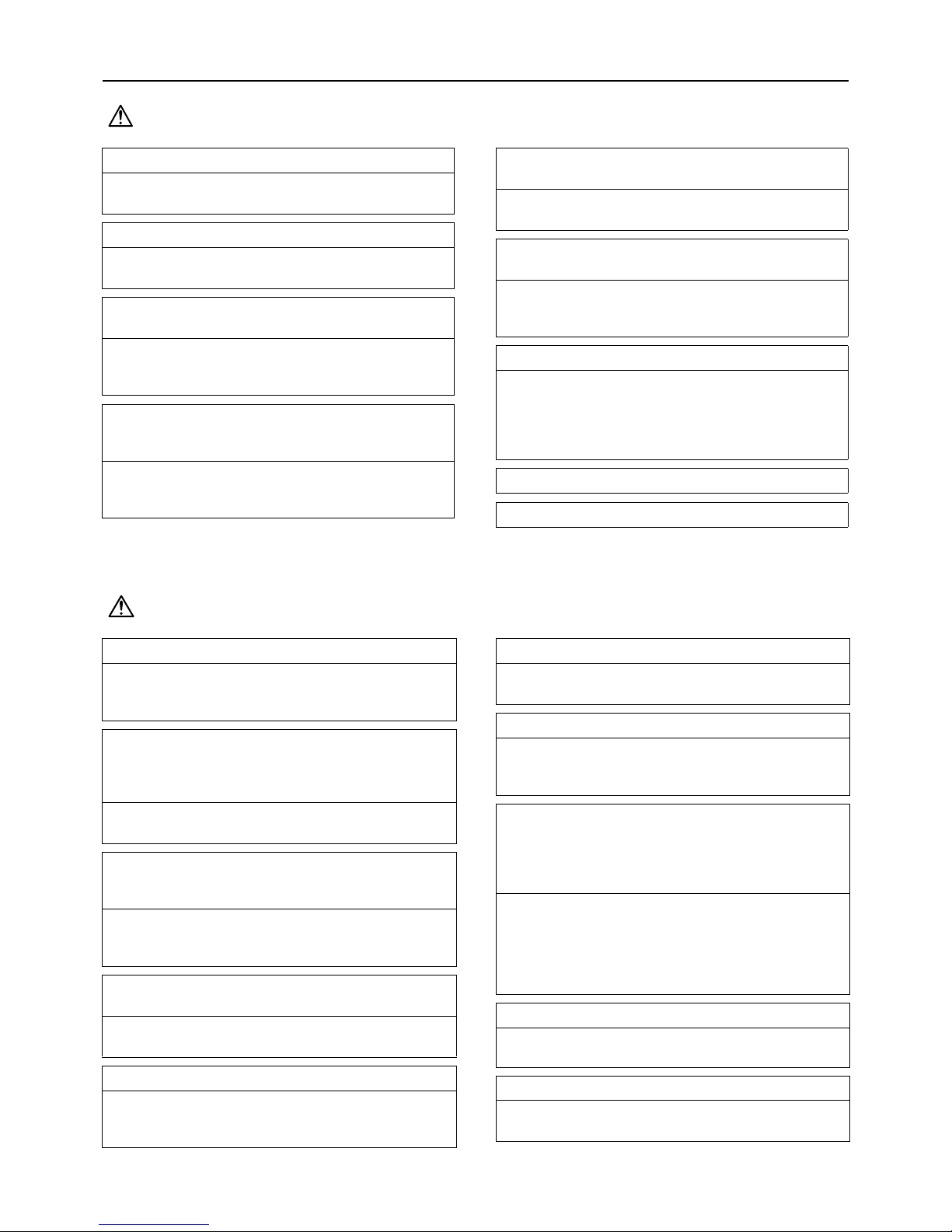
ii
HWE10170 GB
Precautions for handling units for use with R410A
Keep electrical parts away from water.
Wet electrical parts pose a risk of electric shock, smoke, or
fire.
Securely attach the control box cover.
If the cover is not installed properly, dust or water may infiltrate and pose a risk of electric shock, smoke, or fire.
Only use the type of refrigerant that is indicated on the unit
when installing or relocating the unit.
Infiltration of any other types of refrigerant or air into the unit
may adversely affect the refrigerant cycle and may cause
the pipes to burst or explode.
When installing the unit in a small space, take appropriate
precautions to prevent leaked refrigerant from reaching the
limiting concentration.
Leaked refrigerant gas will displace oxygen and may cause
oxygen starvation. Consult your dealer before installing the
unit.
Consult your dealer or a qualified technician when moving
or reinstalling the unit.
Improper installation may result in water leakage, electric
shock, or fire.
After completing the service work, check for a refrigerant
leak.
If leaked refrigerant is exposed to a heat source, such as a
fan heater, stove, or electric grill, toxic gases will be generated.
Do not try to defeat the safety features of the unit.
Forced operation of the pressure switch or the temperature
switch by defeating the safety features for these devices, or
the use of accessories other than the ones that are recommended by Mitsubishi Electric may result in smoke, fire, or
explosion.
Consult your dealer for proper disposal method.
Do not use a leak detection additive.
Do not use the existing refrigerant piping.
A large amount of chlorine that may be contained in the residual refrigerant and refrigerator oil in the existing piping
may cause the refrigerator oil in the new unit to deteriorate.
Use refrigerant piping materials made of phosphorus deoxidized copper. Keep the inner and outer surfaces of the
pipes clean and free of such contaminants as sulfur, oxides,
dust, dirt, shaving particles, oil, and moisture.
Contaminants in the refrigerant piping may cause the refrigerator oil to deteriorate.
Store the piping materials indoors, and keep both ends of
the pipes sealed until immediately before brazing. (Keep elbows and other joints wrapped in plastic.)
Infiltration of dust, dirt, or water into the refrigerant system
may cause the refrigerator oil to deteriorate or cause the
compressor to malfunction.
Use a small amount of ester oil, ether oil, or alkyl benzene
to coat flares and flanges.
Infiltration of a large amount of mineral oil may cause the refrigerator oil to deteriorate.
Charge the system with refrigerant in the liquid phase.
If gaseous refrigerant is drawn out of the cylinder first, the
composition of the remaining refrigerant in the cylinder will
change and become unsuitable for use.
Only use R410A.
The use of other types of refrigerant that contain chloride
may cause the refrigerator oil to deteriorate.
Use a vacuum pump with a check valve.
If a vacuum pump that is not equipped with a check valve is
used, the vacuum pump oil may flow into the refrigerant cycle and cause the refrigerator oil to deteriorate.
Prepare tools for exclusive use with R 410A. Do not use the
following tools if they have been used with the conventional
refrigerant: gauge manifold, charging hose, gas leak detector, check valve, refrigerant charge base, vacuum gauge,
and refrigerant recovery equipment.
If the refrigerant or the refrigerator oil that may be left on these
tools are mixed in with R410A, it may cause the refrigerator oil
in the new system to deteriorate.
Infiltration of water may cause the refrigerator oil to deteriorate.
Leak detectors for conventional refrigerants will not detect an
R410A leak because R410A is free of chlorine.
Do not use a charging cylinder.
If a charging cylinder is used, the composition of the refrigerant
in the cylinder will change and become unsuitable for use.
Exercise special care when handling tools for use with R410A.
Infiltration of dust, dirt, or water into the refrigerant system
may cause the refrigerator oil to deteriorate.
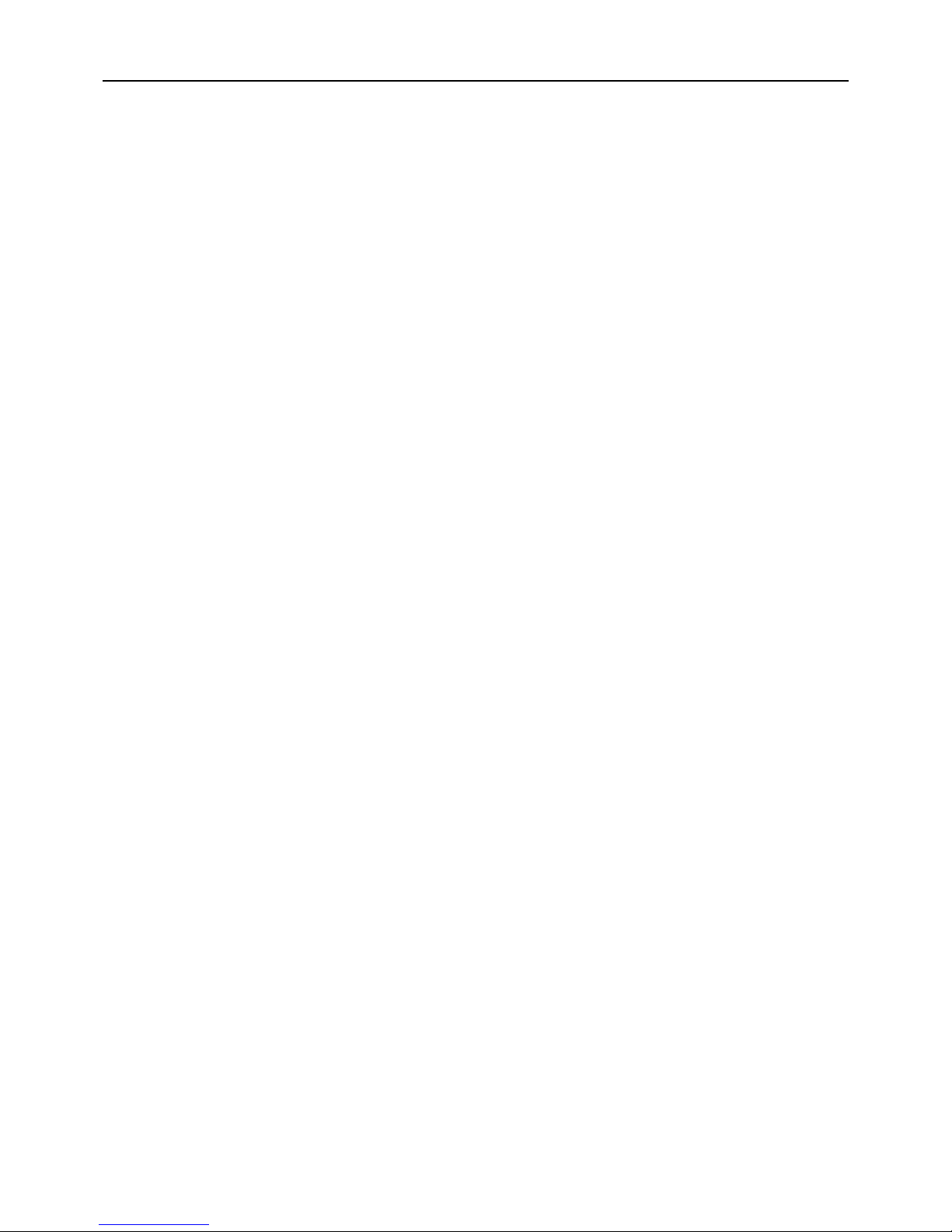
CONTENTS
HWE10170 GB
[1] Components and Functions...................................................................................................... 1
[2] Specifications............................................................................................................................ 3
[3] Sound pressure levels .............................................................................................................. 5
[4] Fan performance and corrected air flow ................................................................................... 8
[5] Outlines and Dimensions........................................................................................................ 10
[6] Wiring Diagram ....................................................................................................................... 11
[7] Refrigerant system diagram.................................................................................................... 12
[8] Troubleshooting ...................................................................................................................... 13
[9] Disassembly Procedure.......................................................................................................... 60
[10] Optional parts ....................................................................................................................... 67
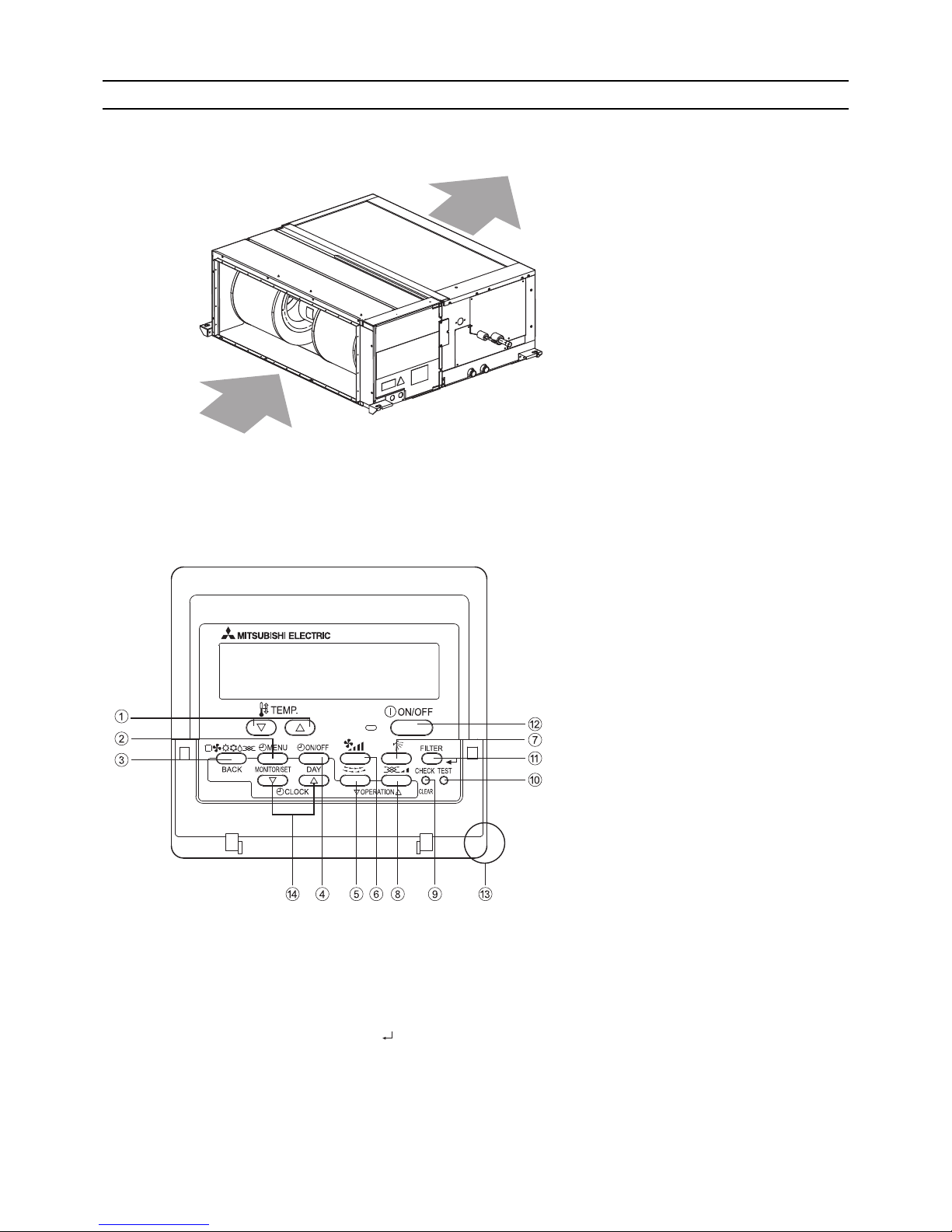
1- 1 -
HWE10170 GB
XI Indoor Unit
[1] Components and Functions
1. Indoor Unit
2. Remote Controller
[PAR-21MAA]
Once the operation mode is selected, the unit will remain in the selected mode until changed.
(1) Remote Controller Buttons
Keep the remote controller out of direct sunlight to ensure accurate measurement of room temperature.
The thermistor at the lower right-hand section of the remote controller must be free from obstructions to ensure accurate mea-
surement of room temperature.
(1) In case of rear inlet
1 [Set Temperature] Button 7 [Vane Control] Button
2 [Timer Menu] Button 8 [Ventilation] Button
[Monitor/Set] Button [Operation] Button
3 [Mode] Button 9 [Check/Clear] Button
[Back] Button 10 [Test Run] Button
4 [Timer On/Off] Button 11 [Filter] Button
[Set Day] Button [ ] Button
5 [Louver] Button 12 [ON/OFF] Button
[Operation] Button 13 Position of built-in room thermistor
6 [Fan Speed] Button 14 [Set Time] Button
Air inlet
Air outlet
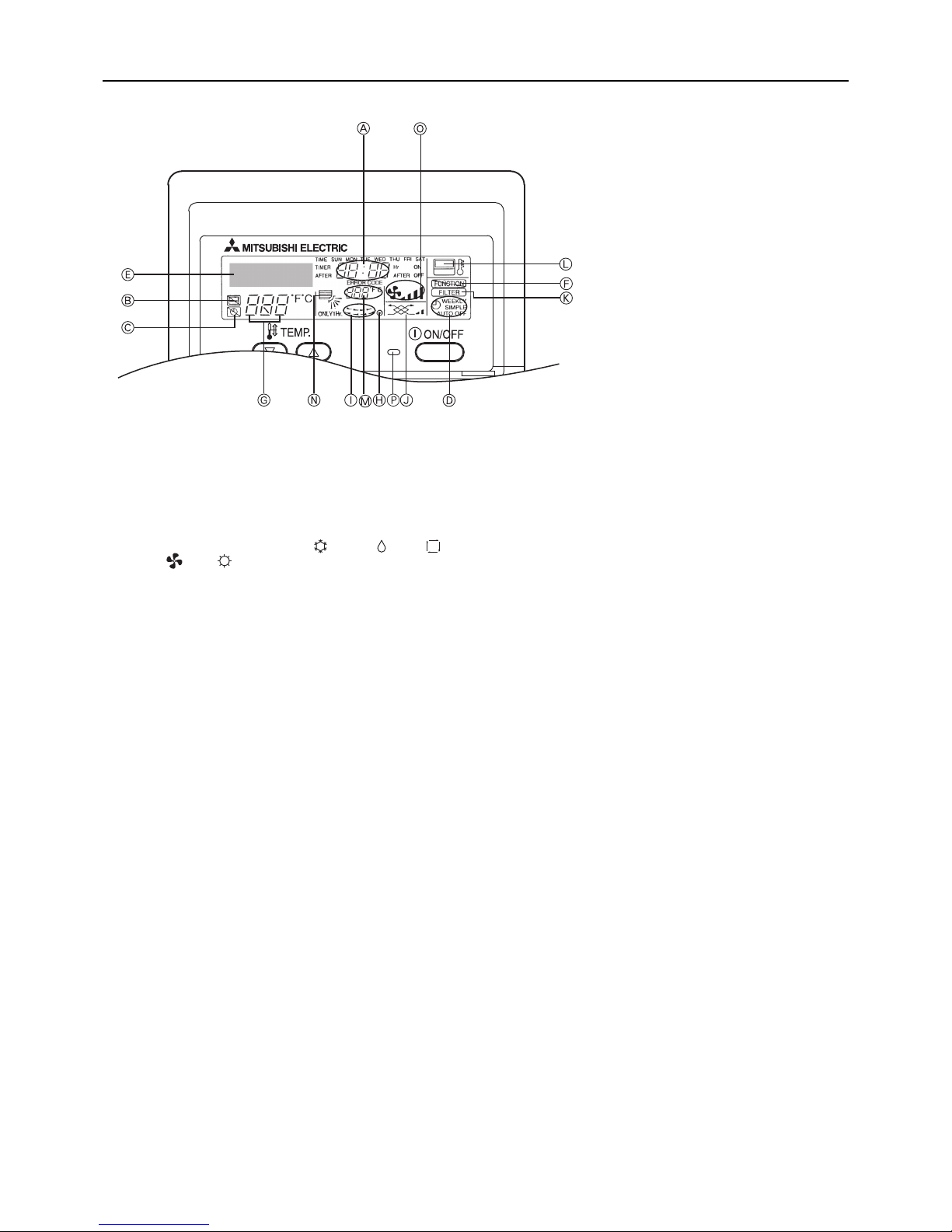
2- 2 -
HWE10170 GB
(2) Remote Controller Display
A Current time/Timer time I Louver swing
B Centralized control indicator J Ventilation
C Timer OFF indicator K Filter sign
D Timer mode indicator L Sensor position
E Operation mode display: COOL, DRY, AUTO,
FAN, HEAT
M Room temperature
F Function mode indicator N Vane setting
G Preset temperature O Fan speed
H Power indicator P Operation lamp
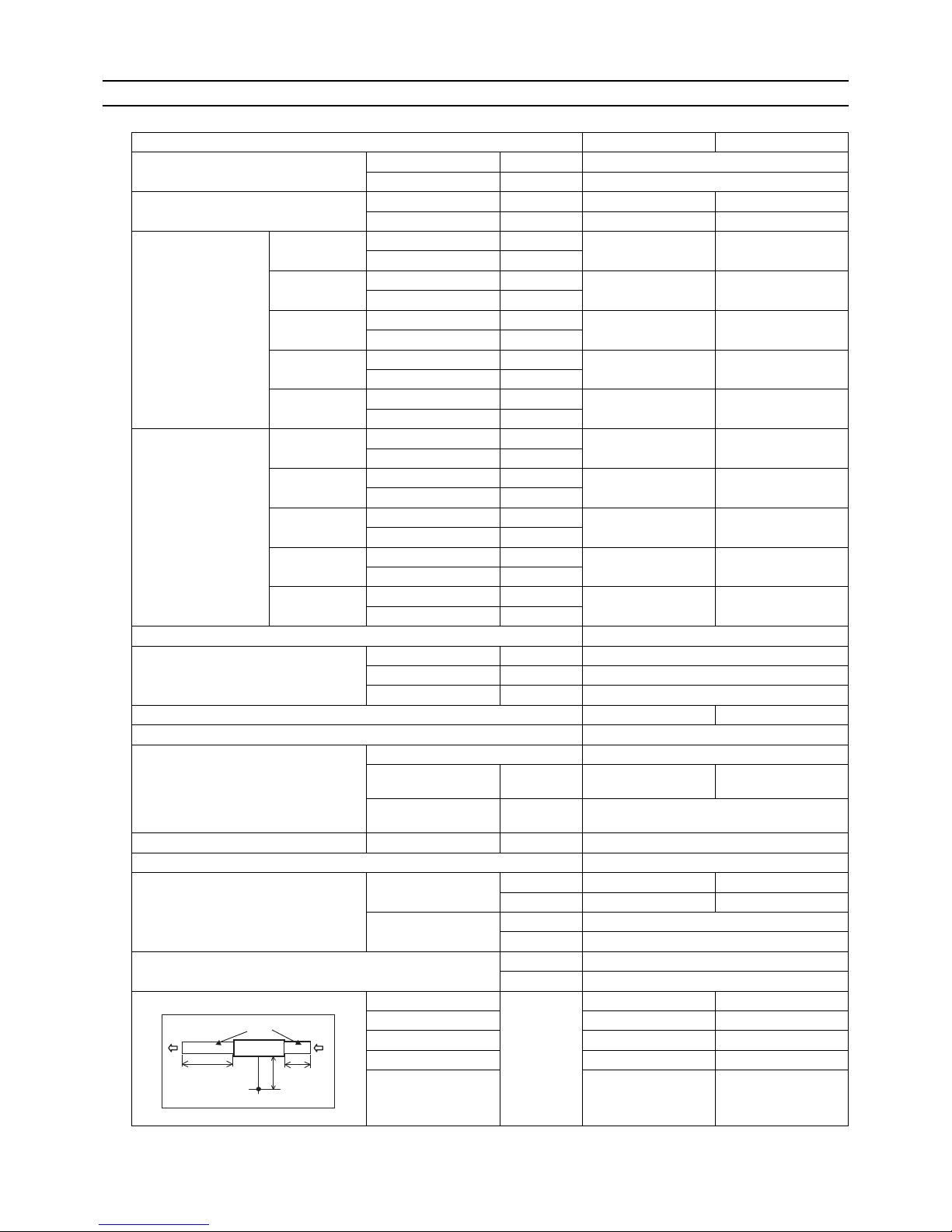
3- 3 -
HWE10170 GB
[2] Specifications
1. Specifications
*1 <Cooling> Indoor temperature: 80°FD.B./67°FW.B. (26.7°CD.B./19.4°CW.B.) Outdoor temperature: 95°FD.B.(35°CD.B.)
<Heating> Indoor temperature: 70°FD.B.(21.1°CD.B.) Outdoor temperature: 47°FD.B./43°FW.B. (8.3°CD.B./6.1°CW.B.)
*2 Measured at a power supply voltage of 230 V
Model PEFY-P72NMHSU-E PEFY-P96NMHSU-E
Power supply
Voltage V 1-phase 208-230
Frequency Hz 50/60
Capacity*1 Cooling kW[BTU/h] 21.1 (72,000) 28.1 (96,000)
Heating kW[BTU/h] 23.4 (80,000) 31.7 (108,000)
Power consumption
50Pa
[0.20in.WG]
Cooling kW
0.43 0.59
Heating kW
100Pa
[0.40in.WG]
Cooling kW
0.52 0.70
Heating kW
150Pa
[0.60in.WG]
Cooling kW
0.63 0.82
Heating kW
200Pa
[0.80in.WG]
Cooling kW
0.75 0.95
Heating kW
250Pa
[1.00in.WG]
Cooling kW
0.89 0.97
Heating kW
Current consumption
*2
50Pa
[0.20in.WG]
Cooling A
2.31 3.08
Heating A
100Pa
[0.40in.WG]
Cooling A
2.79 3.75
Heating A
150Pa
[0.60in.WG]
Cooling A
3.32 4.43
Heating A
200Pa
[0.80in.WG]
Cooling A
3.95 5.10
Heating A
250Pa
[1.00in.WG]
Cooling A
4.81 5.29
Heating A
External finish Galvanized
Dimensions Height mm[in.] 470 (18-9/16)
Width mm[in.] 1250 (49-1/4)
Depth mm[in.] 1120 (44-1/8)
Net weight 97 100
Heat exchanger Cross fin (Alminium fin and copper tube)
Fan Type Sirocco fan x 2
Airflow rate (H-M-L)
m
3
/min
[cfm]
72-61-50
2542-2154-1766
84-71-58
2966-2507-2048
External static
pressure
Pa
[in.WG]
(50)/(100)/150/(200)/(250)
(0.20)/(0.40)/0.60/(0.80)/(1.00)
Motor Output kW 0.87
Air filter Option
Refriferant pipe dimensions Gas
(Brazed connection)
mm ø19.05 ø22.2
[in.] ø3/4 ø7/8
Liquid
(Brazed connection)
mm ø9.52
[in.] ø3/8
Drain pipe dimensions mm O.D.32
[in.] 1-1/4
Operating noise (H-M-L) 50Pa [0.20in.WG] dB(A) 39-35-32 42-38-35
100Pa [0.40in.WG] 41-37-34 44-40-37
150Pa [0.60in.WG] 43-39-36 46-42-39
200Pa [0.80in.WG] 45-41-38 48-44-41
250Pa [1.00in.WG] 47-43-40 50-46-43
*
Measured in anechoic room.
2m
1m
Aux. duct
1.5m
Measurement location 2
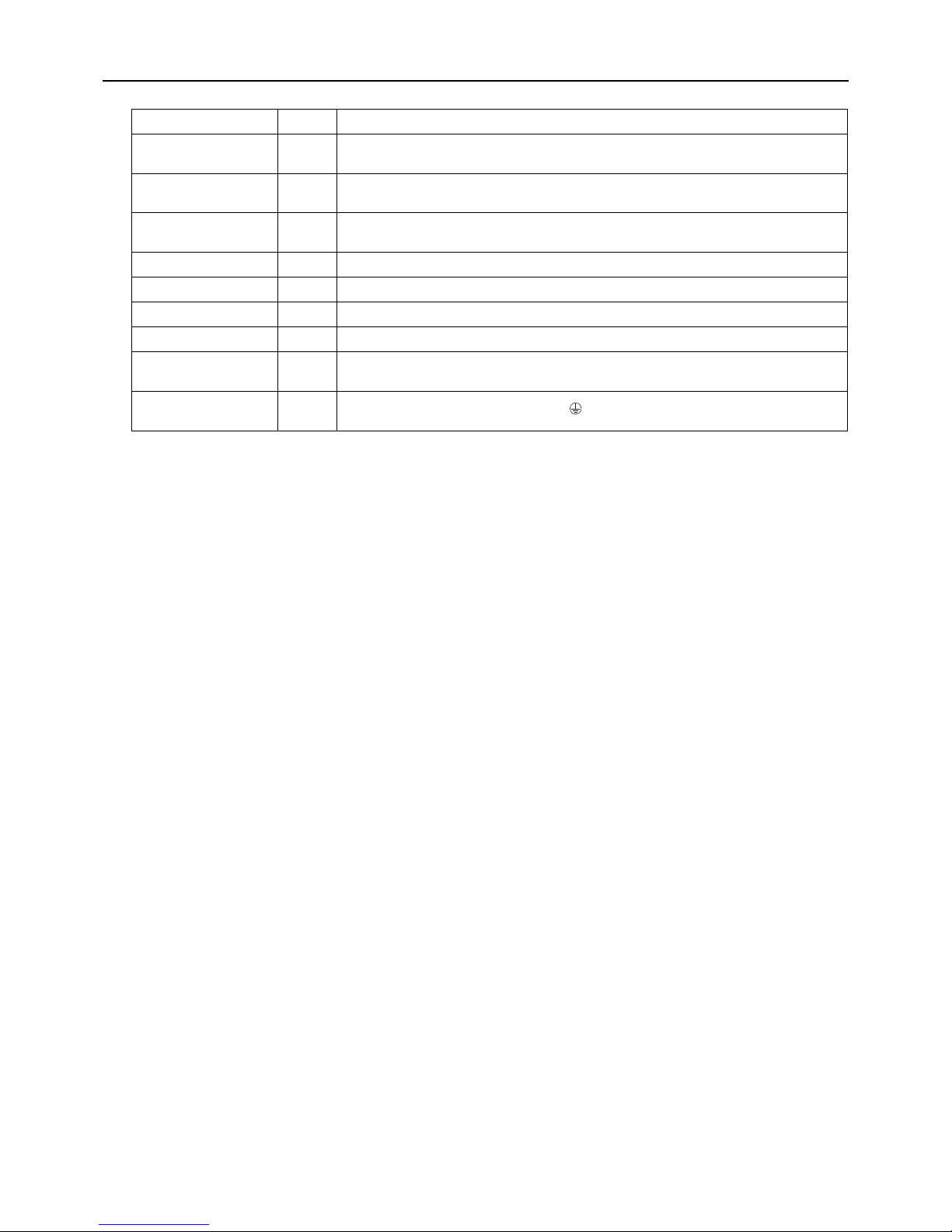
4- 4 -
HWE10170 GB
2. Electrical component specifications
Component Symbol
Room temperature
thermistor
TH21 Resistance 32°F (0°C)/15k, 50°F (10°C)/9.6k, 68°F (20°C)/6.3k,
77°F (25°C)/5.4k, 86°F (30°C)/4.3k, 104°F (40°C)/3.0k
Liquid pipe thermistor TH22 Resistance 32°F (0°C)/15k, 50°F (10°C)/9.6k, 68°F (20°C)/6.3k,
77°F (25°C)/5.4k, 86°F (30°C)/4.3k, 104°F (40°C)/3.0k
Gas pipe thermistor TH23 Resistance 32°F (0°C)/15k, 50°F (10°C)/9.6k, 68°F (20°C)/6.3k,
77°F (25°C)/5.4k, 86°F (30°C)/4.3k, 104°F (40°C)/3.0k
Fuse (INV board) F01 250V 15A
Fuse (NF board) F001 250V 10A
Fuse (NF board) F100 250V 3.15A
Fan motor MF 8-pole, Output 870W ERC8801AB
Linear expansion valve
LEV1
LEV2
12VDC Stepping motor drive port diameter ø3.2 (0~2000 pulse)
Power supply terminal
block
TB2
(L, N, ) 450V 30A
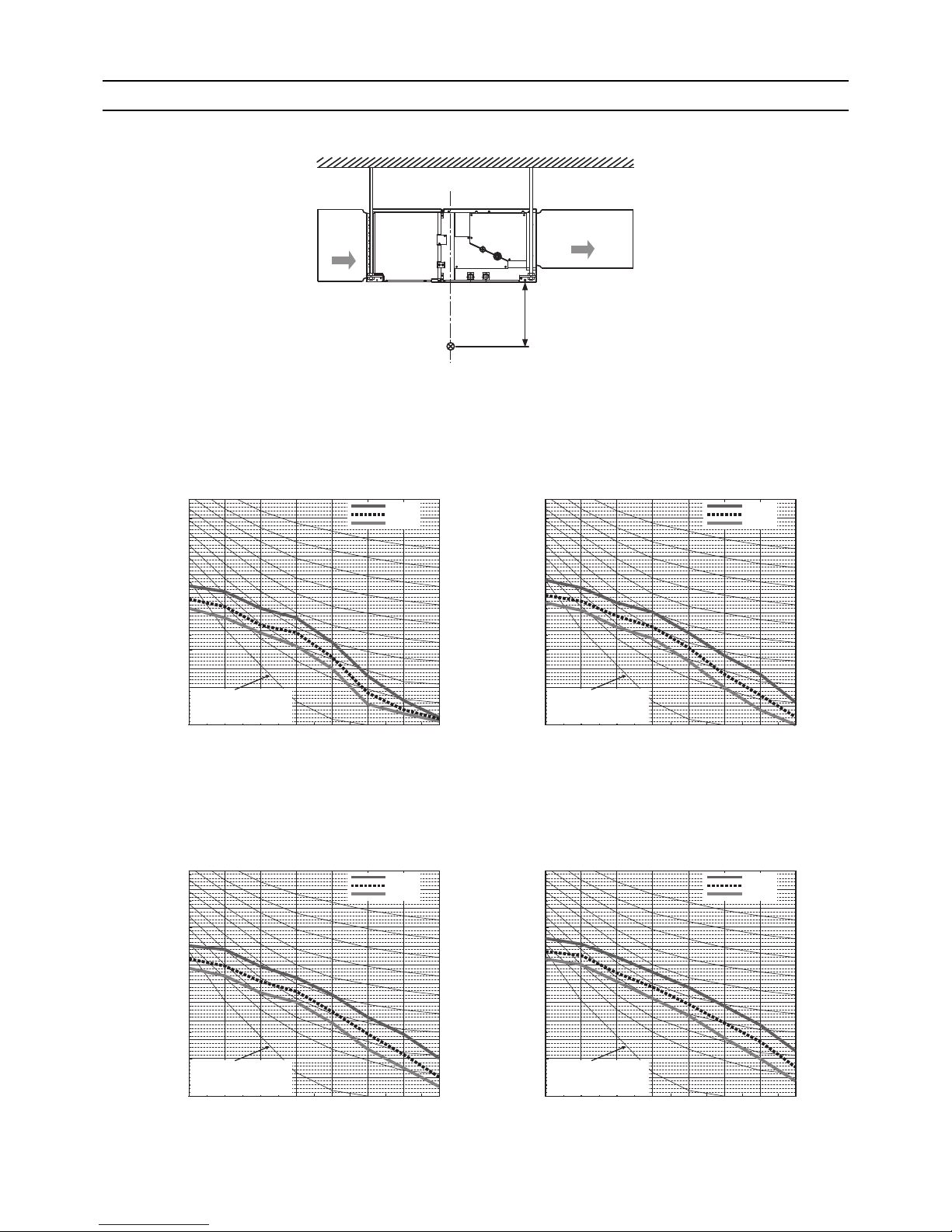
5- 5 -
HWE10170 GB
[3] Sound pressure levels
1. Sound pressure level
Ceiling concealed
2. NC curves
PEFY-P72NMHSU-E
Measurement point
Inlet
Outlet
1.5m
2m
1m
Approximate minimum
audible limit on
continuous noise
High
Middle
Low
10.0
15.0
20.0
25.0
30.0
35.0
40.0
45.0
50.0
55.0
60.0
65.0
70.0
63 125 250 500 1k 2k 4k 8k
NC-60
NC-50
Octave band pressure level (dB) 0dB=20μPa
NC-40
NC-30
NC-20
Octave band center frequencies (Hz)
External Static Pressure:50Pa, 0.20[in.WG]
Power Source: 208, 230V, 50Hz/60Hz
Approximate minimum
audible limit on
continuous noise
High
Middle
Low
10.0
15.0
20.0
25.0
30.0
35.0
40.0
45.0
50.0
55.0
60.0
65.0
70.0
63 125 250 500 1k 2k 4k 8k
NC-60
NC-50
Octave band pressure level (dB) 0dB=20μPa
NC-40
NC-30
NC-20
Octave band center frequencies (Hz)
External Static Pressure:100Pa, 0.40[in.WG]
Power Source: 208, 230V, 50Hz/60Hz
Approximate minimum
audible limit on
continuous noise
High
Middle
Low
10.0
15.0
20.0
25.0
30.0
35.0
40.0
45.0
50.0
55.0
60.0
65.0
70.0
63 125 250 500 1k 2k 4k 8k
NC-60
NC-50
Octave band pressure level (dB) 0dB=20μPa
NC-40
NC-30
NC-20
Octave band center frequencies (Hz)
External Static Pressure:150Pa, 0.60[in.WG]
Power Source: 208, 230V, 50Hz/60Hz
Approximate minimum
audible limit on
continuous noise
High
Middle
Low
10.0
15.0
20.0
25.0
30.0
35.0
40.0
45.0
50.0
55.0
60.0
65.0
70.0
63 125 250 500 1k 2k 4k 8k
NC-60
NC-50
Octave band pressure level (dB) 0dB=20μPa
NC-40
NC-30
NC-20
Octave band center frequencies (Hz)
External Static Pressure:200Pa, 0.80[in.WG]
Power Source: 208, 230V, 50Hz/60Hz
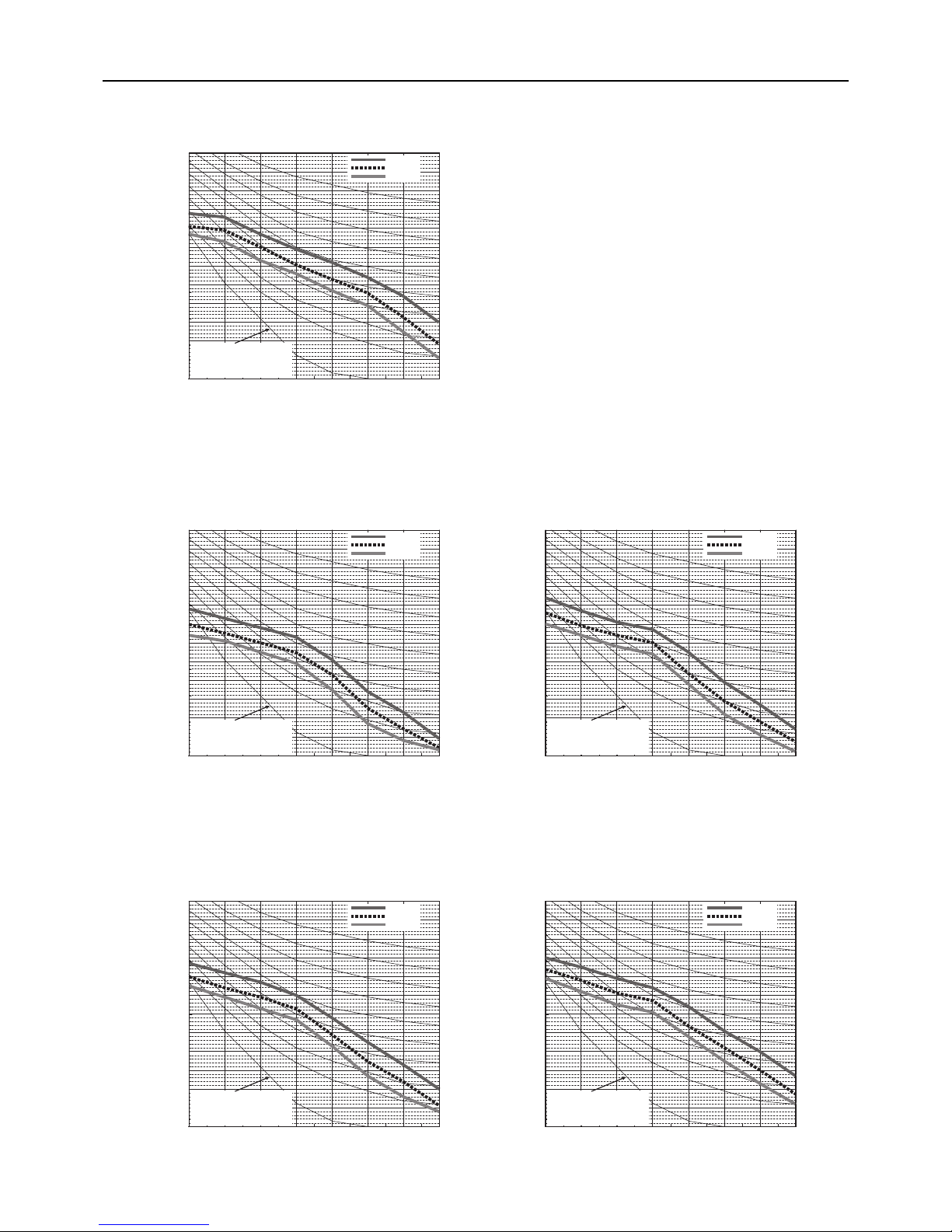
6- 6 -
HWE10170 GB
PEFY-P96NMHSU-E
Approximate minimum
audible limit on
continuous noise
High
Middle
Low
10.0
15.0
20.0
25.0
30.0
35.0
40.0
45.0
50.0
55.0
60.0
65.0
70.0
63 125 250 500 1k 2k 4k 8k
NC-60
NC-50
Octave band pressure level (dB) 0dB=20μPa
NC-40
NC-30
NC-20
Octave band center frequencies (Hz)
External Static Pressure:250Pa, 1.00[in.WG]
Power Source: 208, 230V, 50Hz/60Hz
Approximate minimum
audible limit on
continuous noise
High
Middle
Low
10.0
15.0
20.0
25.0
30.0
35.0
40.0
45.0
50.0
55.0
60.0
65.0
70.0
63 125 250 500 1k 2k 4k 8k
NC-60
NC-50
Octave band pressure level (dB) 0dB=20μPa
NC-40
NC-30
NC-20
Octave band center frequencies (Hz)
External Static Pressure:50Pa, 0.20[in.WG]
Power Source: 208, 230V, 50Hz/60Hz
Approximate minimum
audible limit on
continuous noise
High
Middle
Low
10.0
15.0
20.0
25.0
30.0
35.0
40.0
45.0
50.0
55.0
60.0
65.0
70.0
63 125 250 500 1k 2k 4k 8k
NC-60
NC-50
Octave band pressure level (dB) 0dB=20μPa
NC-40
NC-30
NC-20
Octave band center frequencies (Hz)
External Static Pressure:100Pa, 0.40[in.WG]
Power Source: 208, 230V, 50Hz/60Hz
Approximate minimum
audible limit on
continuous noise
High
Middle
Low
10.0
15.0
20.0
25.0
30.0
35.0
40.0
45.0
50.0
55.0
60.0
65.0
70.0
63 125 250 500 1k 2k 4k 8k
NC-60
NC-50
Octave band pressure level (dB) 0dB=20μPa
NC-40
NC-30
NC-20
Octave band center frequencies (Hz)
External Static Pressure:150Pa, 0.60[in.WG]
Power Source: 208, 230V, 50Hz/60Hz
Approximate minimum
audible limit on
continuous noise
High
Middle
Low
10.0
15.0
20.0
25.0
30.0
35.0
40.0
45.0
50.0
55.0
60.0
65.0
70.0
63 125 250 500 1k 2k 4k 8k
NC-60
NC-50
Octave band pressure level (dB) 0dB=20μPa
NC-40
NC-30
NC-20
Octave band center frequencies (Hz)
External Static Pressure:200Pa, 0.80[in.WG]
Power Source: 208, 230V, 50Hz/60Hz
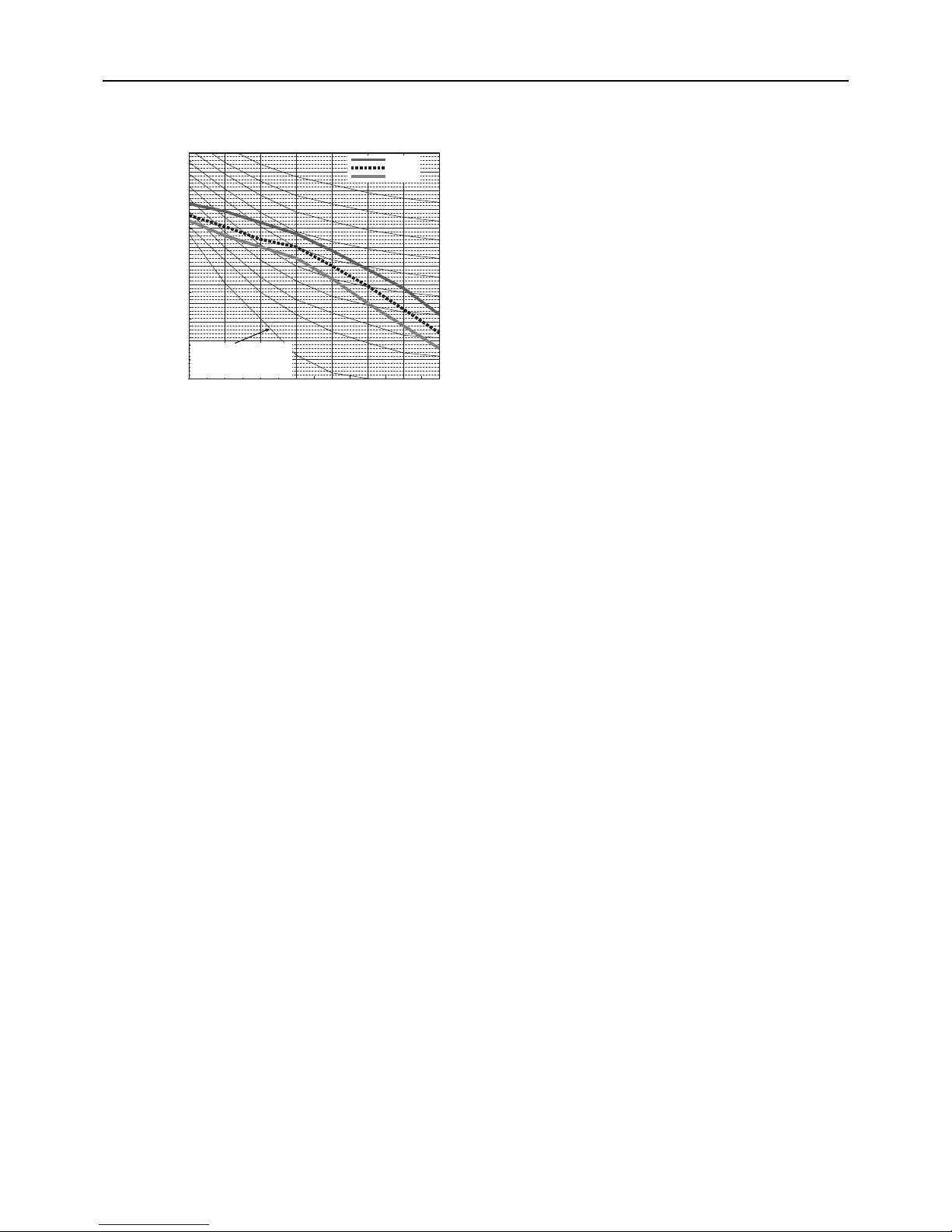
7- 7 -
HWE10170 GB
Approximate minimum
audible limit on
continuous noise
High
Middle
Low
10.0
15.0
20.0
25.0
30.0
35.0
40.0
45.0
50.0
55.0
60.0
65.0
70.0
63 125 250 500 1k 2k 4k 8k
NC-60
NC-50
Octave band pressure level (dB) 0dB=20μPa
NC-40
NC-30
NC-20
Octave band center frequencies (Hz)
External Static Pressure:250Pa, 1.00[in.WG]
Power Source: 208, 230V, 50Hz/60Hz
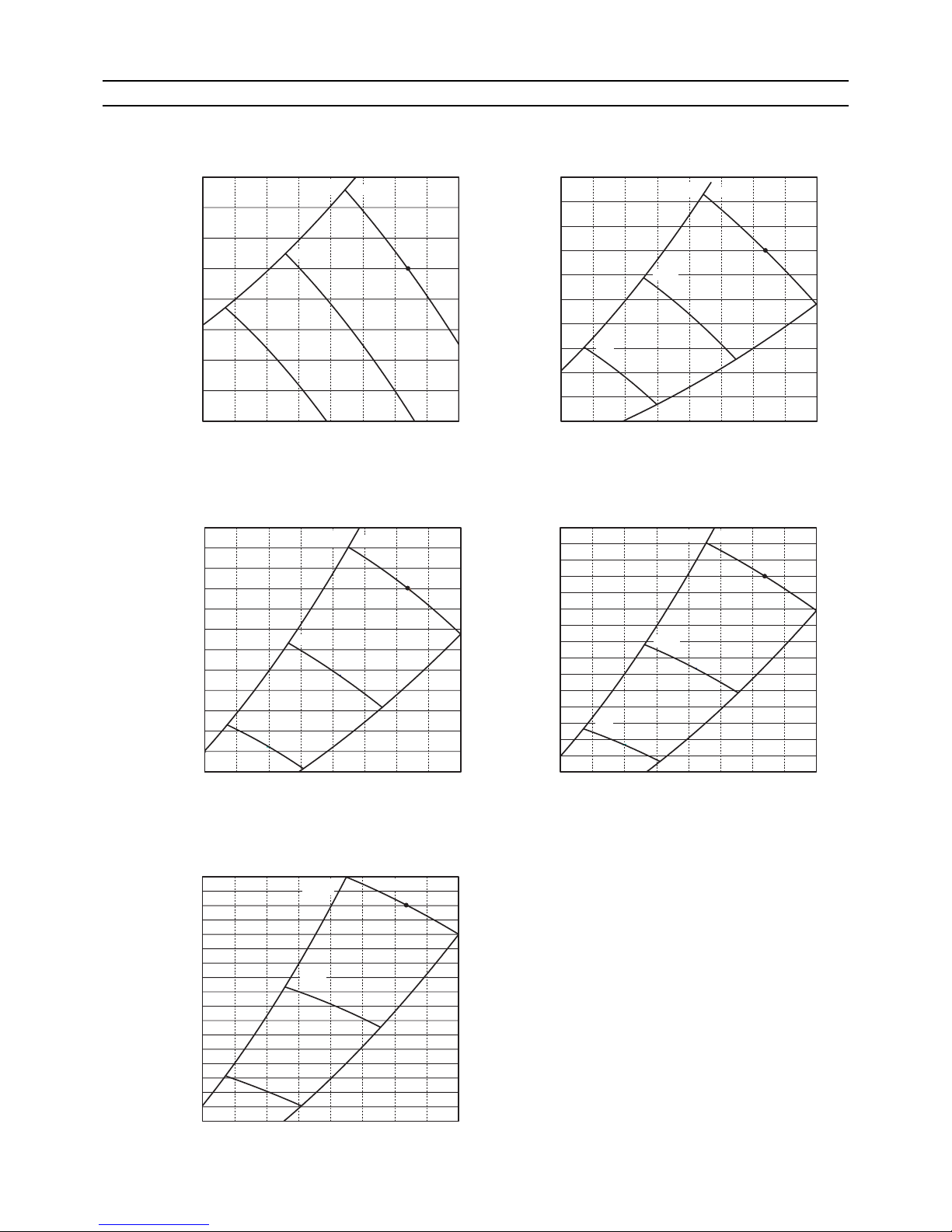
8- 8 -
HWE10170 GB
[4] Fan performance and corrected air flow
PEFY-P72NMHSU-E
Static pressure (Pa)
[in.WG]
Airflow rate (m3/min)
[cfm]
External static pressure :50Pa, 0.20[in.WG]
Power source:208, 230V, 50Hz/60Hz
Middle
High
Low
Limit
[2825]
80
[2648]
75
[2472]
70
[2295]
65
[2119]
60
[1942]
55
[1412]
40
[1766]
50
[1589]
45
10
[0.04]
20
[0.08]
30
[0.12]
40
[0.16]
50
[0.20]
60
[0.24]
70
[0.28]
80
[0.32]
0
[0]
Static pressure (Pa)
[in.WG]
Airflow rate (m3/min)
[cfm]
[2825]
80
[2648]
75
[2472]
70
[2295]
65
[2119]
60
[1942]
55
[1412]
40
[1766]
50
[1589]
45
30
[0.12]
40
[0.16]
50
[0.20]
60
[0.24]
70
[0.28]
80
[0.32]
90
[0.36]
100
[0.40]
110
[0.44]
120
[0.48]
130
[0.52]
External static pressure :100Pa, 0.40[in.WG]
Power source:208, 230V, 50Hz/60Hz
Middle
High
Low
Limit
External static pressure :150Pa, 0.60[in.WG]
Power source:208, 230V, 50Hz/60Hz
Middle
High
Low
Limit
Static pressure (Pa)
[in.WG]
Airflow rate (m3/min)
[cfm]
[2825]
80
[2648]
75
[2472]
70
[2295]
65
[2119]
60
[1942]
55
[1412]
40
[1766]
50
[1589]
45
60
[0.24]
70
[0.28]
80
[0.32]
90
[0.36]
100
[0.40]
110
[0.44]
120
[0.48]
130
[0.52]
140
[0.56]
150
[0.60]
160
[0.64]
170
[0.68]
180
[0.72]
External static pressure :200Pa, 0.80[in.WG]
Power source:208, 230V, 50Hz/60Hz
Middle
High
Low
Limit
Static pressure (Pa)
[in.WG]
Airflow rate (m3/min)
[cfm]
[2825]
80
[2648]
75
[2472]
70
[2295]
65
[2119]
60
[1942]
55
[1412]
40
[1766]
50
[1589]
45
80
[0.32]
90
[0.36]
100
[0.40]
110
[0.44]
120
[0.48]
130
[0.52]
140
[0.56]
150
[0.60]
160
[0.64]
170
[0.68]
180
[0.72]
190
[0.76]
200
[0.80]
210
[0.84]
220
[0.88]
230
[0.92]
External static pressure :250Pa, 1.00[in.WG]
Power source:208, 230V, 50Hz/60Hz
Middle
High
Low
Limit
Static pressure (Pa)
[in.WG]
Airflow rate (m3/min)
[cfm]
[2825]
80
[2648]
75
[2472]
70
[2295]
65
[2119]
60
[1942]
55
[1412]
40
[1766]
50
[1589]
45
100
[0.40]
110
[0.44]
120
[0.48]
130
[0.52]
140
[0.56]
150
[0.60]
160
[0.64]
170
[0.68]
180
[0.72]
190
[0.76]
200
[0.80]
210
[0.84]
220
[0.88]
230
[0.92]
240
[0.96]
250
[1.00]
260
[1.04]
270
[1.09]
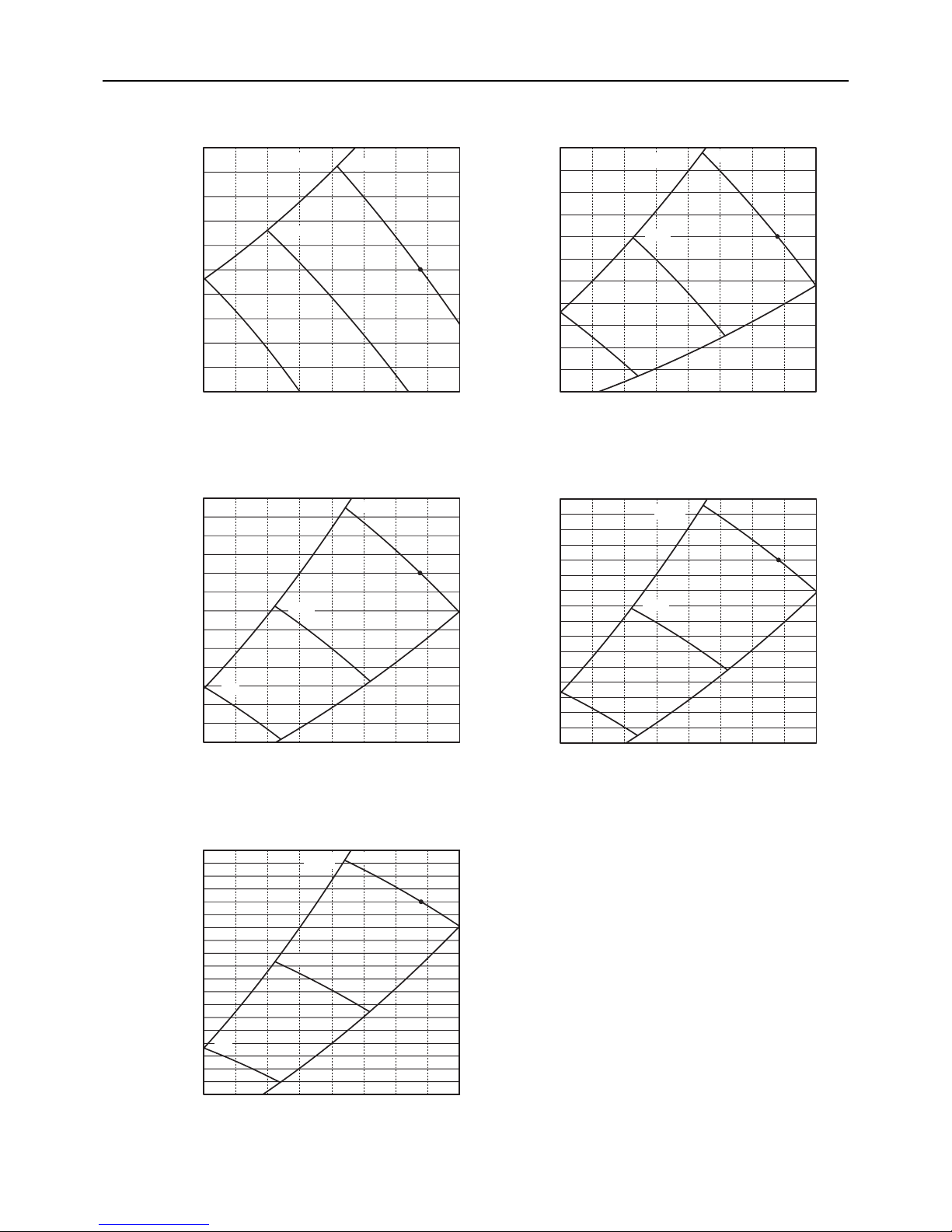
9- 9 -
HWE10170 GB
PEFY-P96NMHSU-E
Middle
High
Low
Limit
Static pressure (Pa)
[in.WG]
Airflow rate (m3/min)
[cfm]
External static pressure :50Pa, 0.20[in.WG]
Power source:208, 230V, 50Hz/60Hz
[3178]
90
[3001]
85
[2825]
80
[2648]
75
[2472]
70
[2295]
65
[1766]
50
[2119]
60
[1942]
55
10
[0.04]
20
[0.08]
30
[0.12]
40
[0.16]
50
[0.20]
60
[0.24]
70
[0.28]
80
[0.32]
90
[0.36]
100
[0.40]
0
[0]
Middle
High
Low
Limit
Static pressure (Pa)
[in.WG]
Airflow rate (m3/min)
[cfm]
30
[0.12]
40
[0.16]
50
[0.20]
60
[0.24]
70
[0.28]
80
[0.32]
90
[0.36]
100
[0.40]
110
[0.44]
120
[0.48]
130
[0.52]
140
[0.56]
External static pressure :100Pa, 0.40[in.WG]
Power source:208, 230V, 50Hz/60Hz
[3178]
90
[3001]
85
[2825]
80
[2648]
75
[2472]
70
[2295]
65
[1766]
50
[2119]
60
[1942]
55
External static pressure :150Pa, 0.60[in.WG]
Power source:208, 230V, 50Hz/60Hz
Static pressure (Pa)
[in.WG]
60
[0.24]
70
[0.28]
80
[0.32]
90
[0.36]
100
[0.40]
110
[0.44]
120
[0.48]
130
[0.52]
140
[0.56]
150
[0.60]
160
[0.64]
170
[0.68]
180
[0.72]
190
[0.76]
Middle
High
Low
Limit
Airflow rate (m3/min)
[cfm]
[3178]
90
[3001]
85
[2825]
80
[2648]
75
[2472]
70
[2295]
65
[1766]
50
[2119]
60
[1942]
55
Middle
High
Low
Limit
Airflow rate (m3/min)
[cfm]
External static pressure :200Pa, 0.80[in.WG]
Power source:208, 230V, 50Hz/60Hz
Static pressure (Pa)
[in.WG]
80
[0.32]
90
[0.36]
100
[0.40]
110
[0.44]
120
[0.48]
130
[0.52]
140
[0.56]
150
[0.60]
160
[0.64]
170
[0.68]
180
[0.72]
190
[0.76]
200
[0.80]
210
[0.84]
220
[0.88]
230
[0.92]
240
[0.96]
[3178]
90
[3001]
85
[2825]
80
[2648]
75
[2472]
70
[2295]
65
[1766]
50
[2119]
60
[1942]
55
Middle
High
Low
Limit
Airflow rate (m3/min)
[cfm]
External static pressure :250Pa, 1.00[in.WG]
Power source:208, 230V, 50Hz/60Hz
Static pressure (Pa)
[in.WG]
100
[0.40]
110
[0.44]
120
[0.48]
130
[0.52]
140
[0.56]
150
[0.60]
160
[0.64]
170
[0.68]
180
[0.72]
190
[0.76]
200
[0.80]
210
[0.84]
220
[0.88]
230
[0.92]
240
[0.96]
250
[1.00]
260
[1.04]
270
[1.09]
280
[1.13]
290
[1.17]
[3178]
90
[3001]
85
[2825]
80
[2648]
75
[2472]
70
[2295]
65
[1766]
50
[2119]
60
[1942]
55
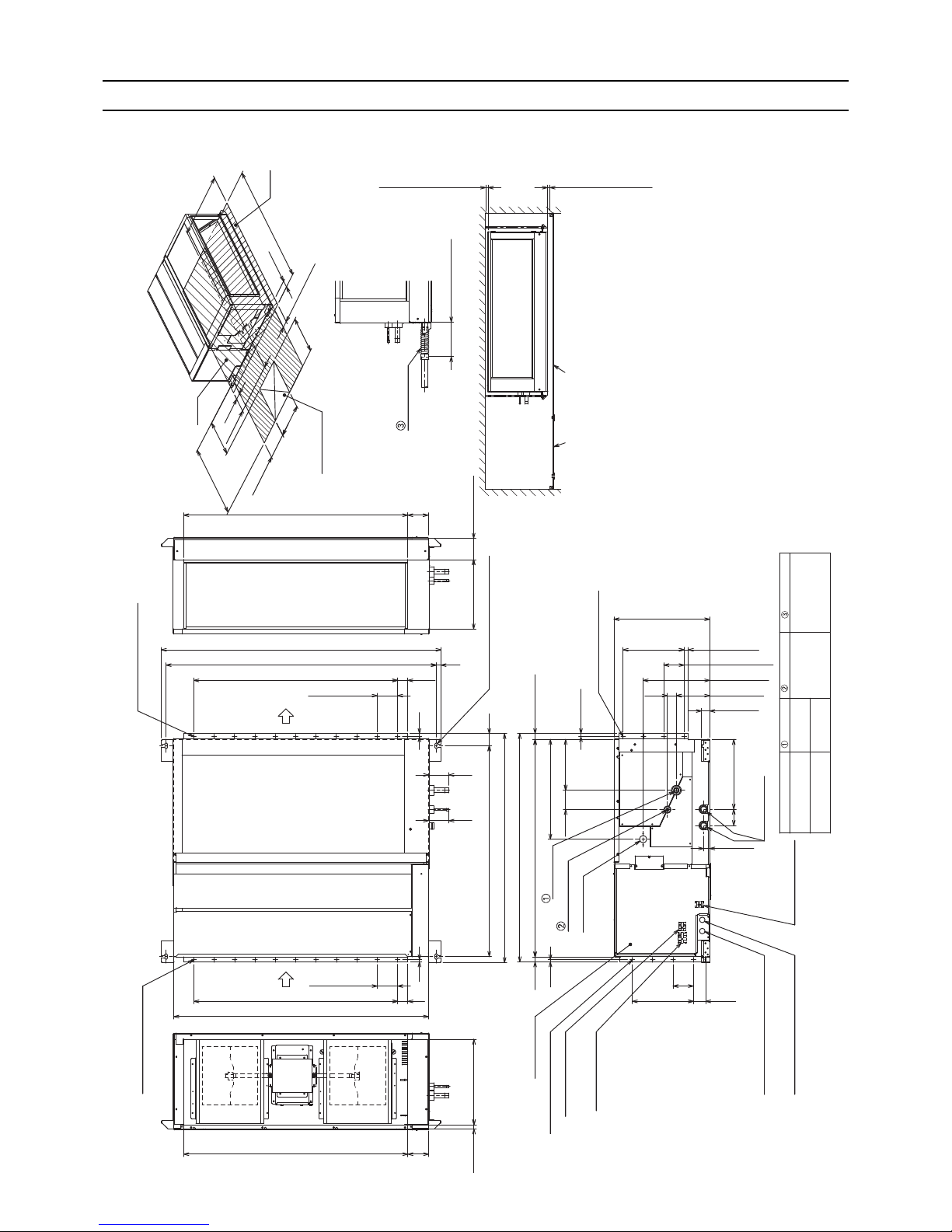
10- 10 -
HWE10170 GB
[5] Outlines and Dimensions
Air inlet Air outlet
(DUCT)
(7/16)
(2-3/8)
(3-3/16)
(2-3/8)
(3-15/16x3=11-13/16)
(3-15/16x3=11-13/16)
(1-3/4)
(9-13/16)
(DUCT)
(7/16)
(5/8)
(3-15/16)
(3-15/16)
(15/16)
(3-15/16)
(Actual length)
Drain Piping.
(21-11/16)
(7-7/8~11-13/16)
(17-3/4)
(5-15/16~7-7/8)
(17-3/4)
2X4-ø3(1/8) holes
2X11-ø3(1/8) holes
Drain hole
Drain hole
Control box
(Power source)
Terminal block
(MA remocon)
(Transmission wiring)
(Power souse wiring)
(Normal type)
(Option)
(Transmission)
Suspension bolt hole
Terminal blockKnockout hole ø22.2(7/8)
Knockout hole ø22.2(7/8)
Terminal block
4-14X30(9/16x3/16) Slot
2X4-ø3(1/8) holes
2X11-ø3(1/8) holes
Make the access door
at the appointed position properly
for service maintenance.
Access door Ceiling surface
Access door
Note2
Note3
Required space for service and maintenance.
MODEL
PEFY-P72NMHSU-E
PEFY-P96NMHSU-E
ø
19.05(3/4)
ø
22.2(7/8)
ø
9.52(3/8)
Drain hose 32mm
(1-1/4inch)
<flexible joint>
<accessory>
Note 1.Use M10 screw for the suspension bolt (field supply).
2.Keep the service space for the maintenance from the bottom
when the heat exchanger is cleaned.
3.Keep the service space for the maintenance from the bottom
when the fan motor is changed.
4.Make sure to install the air filter (field supply) on the air intake side.
In case field supplied air filter is used, attach it
where the filter service is easily done.
Unit:mm(in.)
Unit:mm(in.)
249
95(3-4/3)
342(13-1/2)
80
170(6-3/4±1/4)
23
100
470(18-9/16)
20(13/16)
102(4-1/16)
105(4-3/16)
420(16-9/16)
1100(43-5/16)(DUCT)
1250(49-1/4)
1372(54-1/16)
1124(44-5/16)
15
10
100x10=1000(3-15/16x10=39-3/8)
100(3-15/16)
50(2)
60
1326(52-1/4)(Suspension bolt pitch)
1034(40-3/4)(Suspension bolt pitch)
340(13-7/16)
1100(43-5/16)(DUCT)
100
100
29(1-3/16)
41(1-5/8)
1067(42-1/16)
24(1)
1120(44-1/8)
489(19-5/16)
327(12-7/8)
44
164(6-1/2)
30(1-3/16)
15(5/8)
100X3(=300)
100(3-15/16)
20(13/16)
100(3-15/16)
10
100x3=300
60
100x10=1000(3-15/16x10=39-3/8)
50(2)
100(3-15/16)
More than 20(13/16)
More than 20(13/16)
550
50(2)
150~200
50(2)
50(2)
450
800(31-1/2)
450
200~300
1350(53-3/16)
730(28-3/4)
PEFY-P72,96NMHSU-E
Gas pipe
Liquid pipe
Gas pipe
Liquid pipe
Drain hose
Drain hose
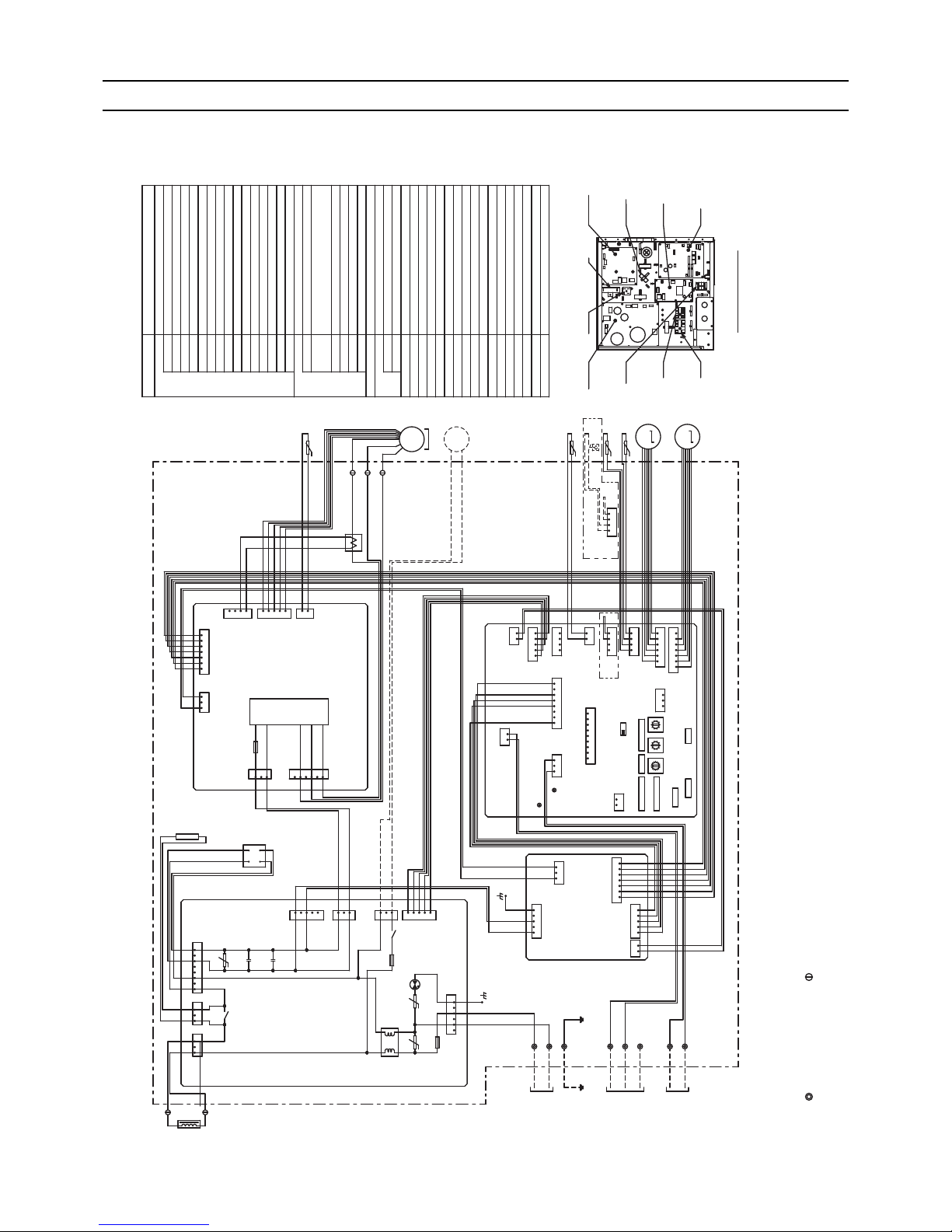
11- 11 -
HWE10170 GB
[6] Wiring Diagram
0
1
2
3
4
5
6
7
8
9
0
1
2
3
4
5
6
7
8
9
0
F
E
D
C
B
A
9
8
7
6
5
4
3
2
1
642
1
3
1
2
2
2
1
1
25431
21
85431
2131442331
4321
6
6
5
5
5
4
4
3
3
3
2
2
1
1
1
54321
12345
1
2
76543213
3
1
1
1
2
3
4
5
3
3
1
1
1
3
8
7
1
6
6
5
3
43
5
3
2
1
1
3
3
1
1
CN25
F01
IPM
(BLUE)
CNCT2
CNFAN
CNP
X010
X100
CNR1
(RED)
(RED)
CNACL
ZNR
003
C015
C016
ZNR
002
DSA
001
ZNR
001
F001
F100
CNPW1
CNRSC
CNRSP
CNXC1
CNXB1
CNDB
CNPW2
CN18V
(GREEN)
CNTH
(RED)
CNCT1
CNRS2
CN15V
CNVDC
CNDP
CNINV
NF
CNXC2
CN100
CN41
CN90
LED2
LED1
CN3A
(BLUE)
CN2M
(BLUE)
CN7V
CN60
CN44
CN4F CN4F
CN20
(RED)
CN32
SW3
SWC
SW5
SWA
SWE
ONOFF
SW2SW1
SW4
SW11SW12SW14
1s
DIGIT DIGIT
( ) ( ) ( )
10ths
BRANCH
No.
CNXB2
POWER SUPPLY
AC208-230V
60Hz
Note 1
Note 1
ACL
2
2
1
1
INSIDE SECTION OF CONTROL BOX
TO MA REMOTE
CONTROLLER
TO OUTDOOR UNIT
BC CONTROLLER
REMOTE CONTROLLER
MF
DP
MS
3
~
M
1
~
UVW
R
NF.B.
INV.B.
I.B.
P.B .
TB2
DB01
ACCT
TB5
TB15
LEV1
LEV2
THHS
TH21
TH22FSTH23
L1
3
4
2
1
33112
2
M1M2S(SHIELD)
L2
G
1
2
DB01 RNF.B.
TB2
TB5
TB15
P. B .
I.B.
ACCT
INV.B.
PARTS LOCATION
Inside < > is the optional parts.
NOTE:1.The part of thin dotted line indicates the circuit for optional parts.
2.To perform a drainage test for the drain pump turn on the SWE
on the control board while the indoor unit is being powerd.
*Be sure to turn off the SWE after completing a drainage test or test run.
3.The wirings to TB2,TB5,TB15 shown in dotted line are field work.
4.Mark indicates terminal block, connector.
5.Use copper supply wire.
SYMBOL NAME
SYMBOL EXPLANATION
Aux. relay
X010,X100
Var ist or
Arrester
Intelligent power module
Fuse(AC250V 15A)
DSA001
IPM
F01
Electronic linear expan.valve
LEV1,LEV2
F001
F100
NF
Fuse(AC250V 10A)
Fuse(3.15A)
Noise filter
Switch (for mode selection)
Switch (for capacity code)
Switch (for mode selection)
Switch (for model selection)
Switch (for mode selection)
Switch (1s digit address set)
Switch (10ths digit address set)
Switch (BRANCH No.)
Switch (for static pressure selection)
Switch (for static pressure selection)
TB2
TB5
TB15
CN25
I.B.
NF.B.
INV.B.
P. B.
TH21
TH22
TH23
THHS
<FS>
Connector
Indoor controller board
Noise filter board
Inverter board
Power supply board
Power source terminal block
Transmission terminal block
Transmission terminal block
Float switch
Thermistor(piping temp.detection/liquid)
Thermistor(piping temp.detection/gas)
Thermistor(heatsink)
Thermistor(inlet air temp.detection)
MF
Fan motor
AC reactor (Power factor improvement)
Resistor
Diode bridge
LED (Power supply)
Current Sensor (AC)
LED (Remote controller supply)
ACL
R
DB01
LED1
ACCT
LED2
Connector (emergency operation)
Connector (Remote switch)
CN32
Connector (HA terminal-A)
CN41
Connector (Wireless)
CN90
SW1
SW2
SW3
SW4
SW5
SW11
SW12
SW14
SWA
SWC
SWE
ZNR01~
ZNR03
Drain pump
<DP>
t°
t°
t°
t°
U
UU
M
M
PEFY-P72,96NMHSU-E
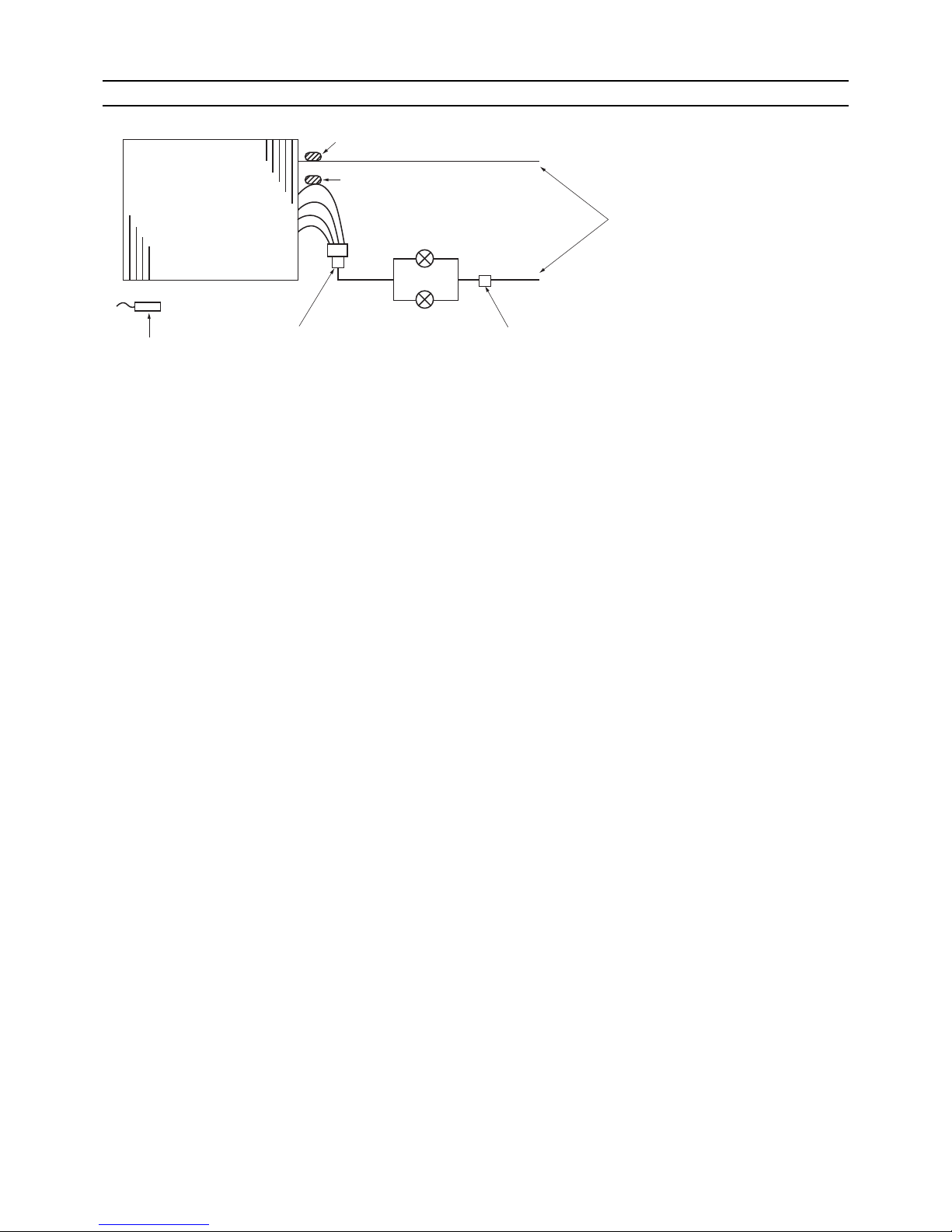
12- 12 -
HWE10170 GB
[7] Refrigerant system diagram
(A) Gas pipe thermistor TH23
(B) Gas pipe
(C) Liquid pipe
(D) Brazed connections
(E) Strainer (#100 mesh)
(F) Linear expansion valve
(G) Liquid pipe thermistor TH22
(H) Heat exchanger
(I) Room temperature thermistor TH21
(H)
(I)
(F)
(E)
(E)
(C)
(G)
(A)
(D)
(B)
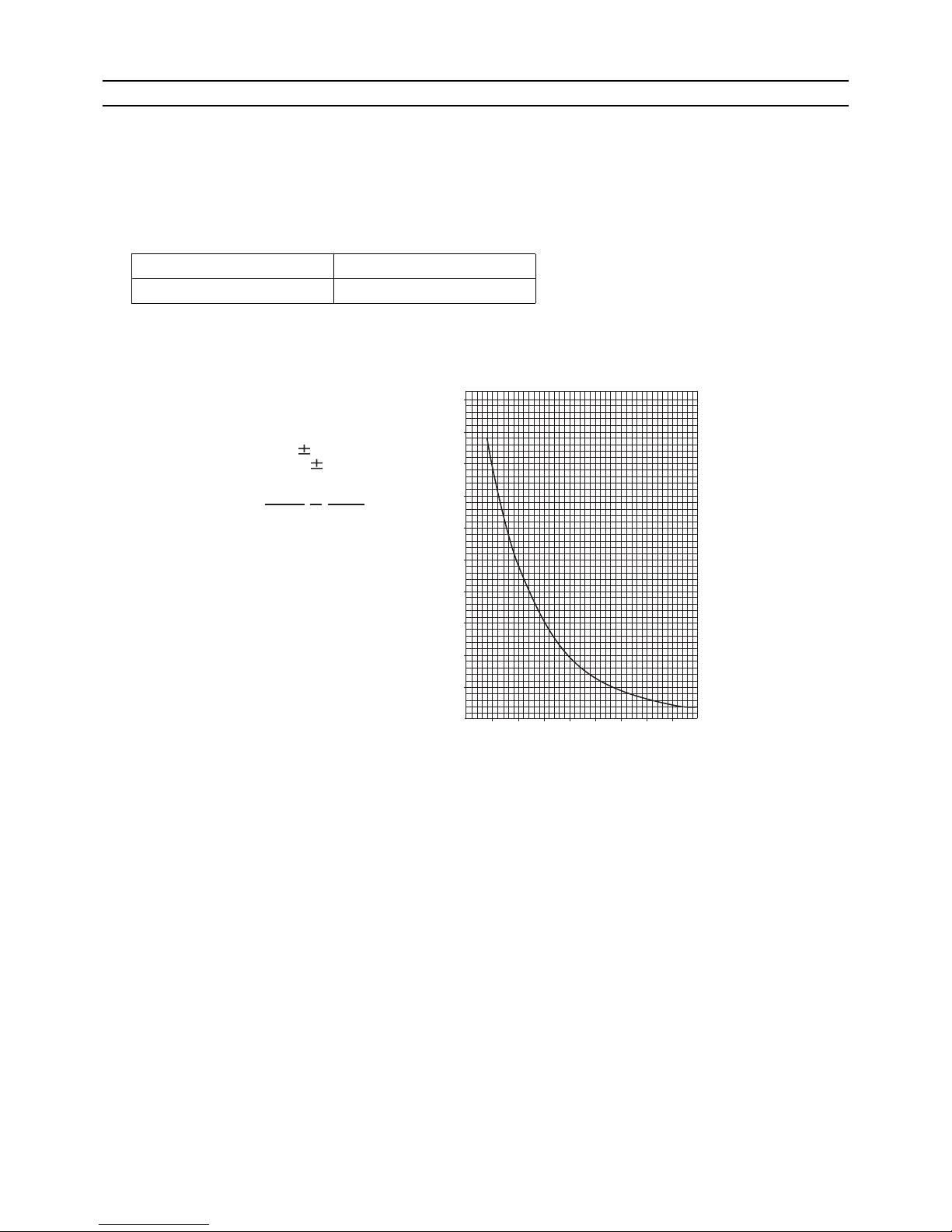
13- 13 -
HWE10170 GB
[8] Troubleshooting
1. Check methods
1. Component and check points
(1) Thermistor
Room temperature thermistor (TH21)
Liquid pipe thermistor (TH22)
Gas pipe thermistor (TH23)
Disconnect the connector and measure the resistance between terminals with a tester.
(Ambient temperature 50°F (10°C) - 86°F (30°C))
1) Thermistor characteristic graph
(2) Fan motor
Refer to the page on "DC fan motor (fan motor/INV board)."(page 47)
(3) Linear expansion valve
Refer to the page on "LEV". ([8] 4)(page 51)
Normal Abnormal
4.3kΩ - 9.6kΩ Open or short
(Refer to the thermistor characteristic graph below.)
Low-temperature thermistor
Room temperature thermistor (TH21)
Liquid pipe thermistor (TH22)
Gas pipe thermistor (TH23)
Thermistor R
0
= 15 kΩ 3%
Multiplier of B = 3480 kΩ 2%
32°F (0°C) 15kΩ
50°F (10°C) 9.6kΩ
68°F (20°C) 6.3kΩ
77°F (25°C) 5.2kΩ
86°F (30°C) 4.3kΩ
104°F (40°C) 3.0kΩ
(A) Temperature °F (°C)
(B) Resistance (kΩ)
Rt = 15 exp { 3480( ) }
1
273+t
1
273
0
10
20
30
40
50
-20 -10 0 10 20 30 40 50
(A)
(B)
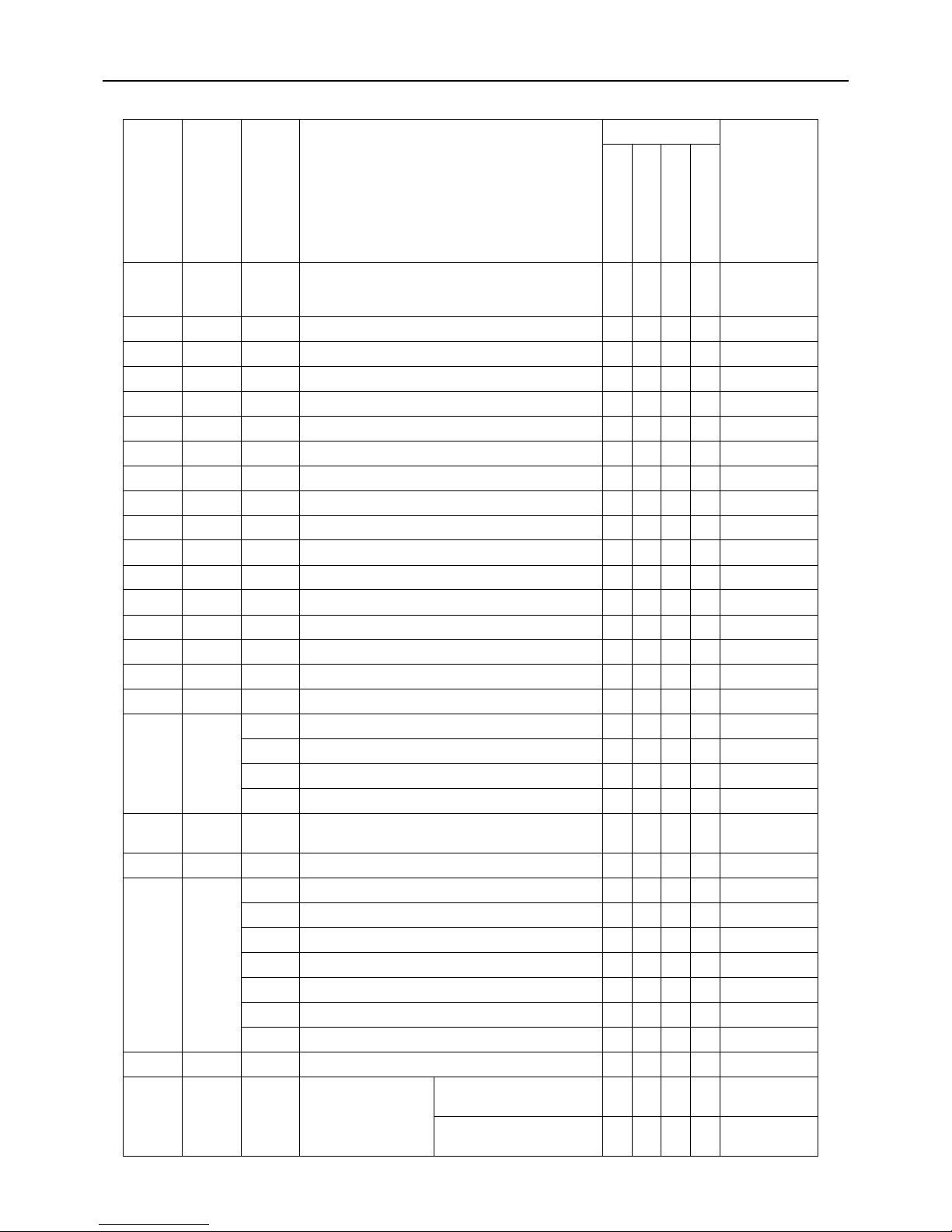
14- 14 -
HWE10170 GB
2. Error Code Lists
Error
Code
Prelimi-
nary
error
code
Error
(prelim-
inary)
detail
code
Error code definition
Searched unit
Notes
0403
4300
4305
01
05
(Note)
Serial communication error O O
0900 - - Test run O
1102 1202 - Discharge temperature fault O
1301 - - Low pressure fault O
1302 1402 - High pressure fault O
1500 1600 - Refrigerant overcharge O
- 1605 - Preliminary suction pressure fault O
2500 - - Drain sensor submergence O
2502 - - Drain pump fault O
2503 - - Drain sensor (Thd) fault O O
2600 - - Water leakage O
2601 - - Water supply cutoff O
4102 4152 - Open phase O
4106 - - Transmission power supply fault O
4109 - - Fan operation status detection error O
4115 - - Power supply signal sync error O
4116 - - RPM error/Motor error O O
4220
4225
(Note)
4320
4325
(Note)
[108] Abnormal bus voltage drop O O
[109] Abnormal bus voltage rise O O
[111] Logic error O O
[131] Low bus voltage at startup O
4230
4235
4330
4335
- Heatsink overheat protection O O
4240 4340 - Overload protection O
4250
4255
(Note)
4350
4355
(Note)
[101] IPM error O O
[104] Short-circuited IPM/Ground fault O O
[105] Overcurrent error due to short-circuited motor O O
[106] Instantaneous overcurrent (S/W detection) O O
[107] Overcurrent (effective value) (S/W detection) O O
[121] Position detection error at startup O
[122] Position detection error during operation O
4260 - - Heatsink overheat protection at startup O
5101 1202 -
Temperature sensor
fault
Return air temperature
(TH21)
O
OA processing unit inlet
temperature (TH4)
O
Outdoor unit
Indoor unit
LOSSNAY
Remote controller
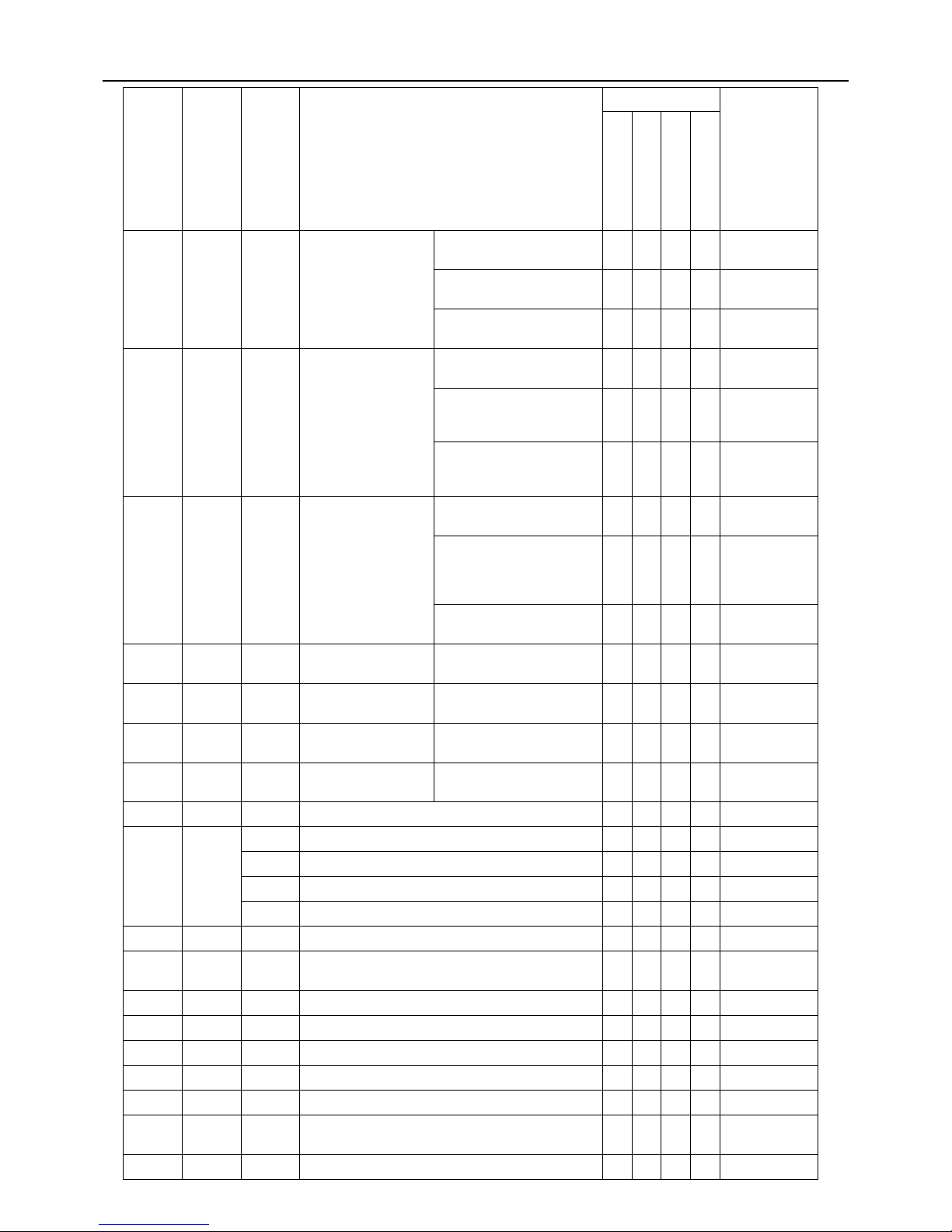
15- 15 -
HWE10170 GB
5102 1217 -
Temperature sensor
fault
Indoor unit pipe temperature (TH22)
O
OA processing unit pipe
temperature (TH2)
O
HIC bypass circuit outlet
temperature (TH2)
O
5103 1205 00
Temperature sensor
fault
Indoor unit gas-side pipe
temperature (TH23)
O
OA processing unit gasside pipe temperature
(TH3)
O
Pipe temperature at
heatexchanger outlet
(TH3)
O
5104 1202 -
Temperature sensor
fault
OA processing unit intake
air temperature (TH1)
O
Outside temperature
(TH24)
O
Detectable
only by the AllFresh type indoor units
Outdoor unit discharge
temperature (TH4)
O
5105 1204 -
Temperature sensor
fault
Accumulator inlet temperature (TH5)
O
5106 1216 -
Temperature sensor
fault
HIC circuit outlet temperature (TH6)
O
5107 1221 -
Temperature sensor
fault
Outside temperature (TH7) O
5110 1214 01
Temperature sensor
fault
Heatsink temperature
(THHS)
OO
5201 - - High-pressure sensor fault (63HS1) O
5301
5305
4300
4305
[115] ACCT sensor fault O
[117] ACCT sensor circuit fault O O
[119] Open-circuited IPM/Loose ACCT connector O O
[120] Faulty ACCT wiring O
5701 - - Loose float switch connector O
6201 - -
Remote controller board fault (nonvolatile memory
error)
O
6202 - - Remote controller board fault (clock IC error) O
6600 - - Address overlap OOOO
6601 - - Polarity setting error O
6602 - - Transmission processor hardware error OOOO
6603 - - Transmission line bus busy error OOOO
6606 - -
Communication error between device and transmission processors
OOOO
6607 - - No ACK error OOOO
Error
Code
Prelimi-
nary
error
code
Error
(prelim-
inary)
detail
code
Error code definition
Searched unit
Notes
Outdoor unit
Indoor unit
LOSSNAY
Remote controller
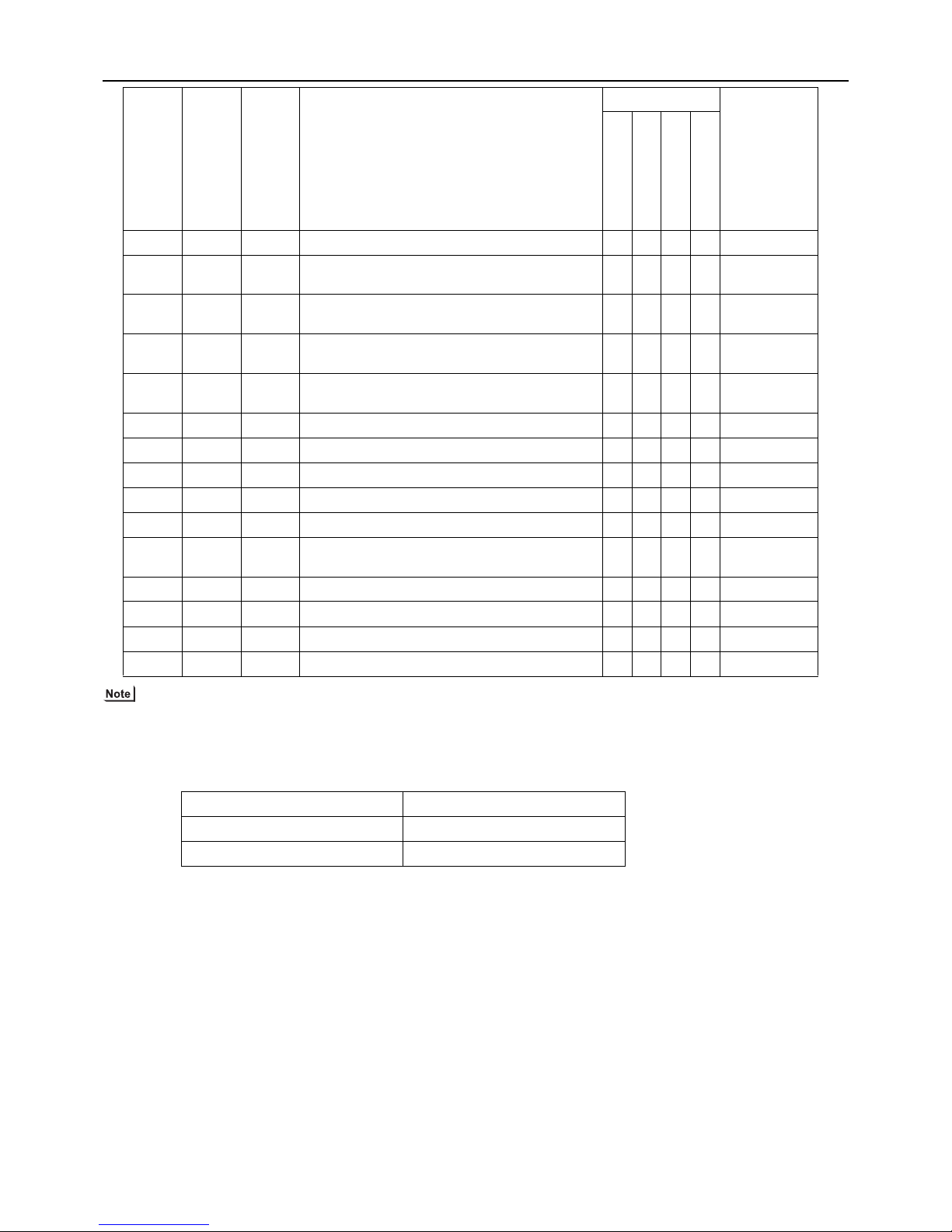
16- 16 -
HWE10170 GB
The last digit in the check error codes in the 4000's and 5000's and two-digit detail codes indicate if the codes apply to
compressor inverter on fan inverter.
Example
Code 4225 (detail code 108): Bus voltage drop in the fan inverter system
Code 4230 : Heatsink overheat protection in the compressor inverter system
There are no preliminary error codes or detail codes for indoor units.
XII
6608 - - No response error OOOO
6831 - -
MA controller signal reception error (No signal reception)
OO
6832 - -
MA remote controller signal transmission error
(Synchronization error)
OO
6833 - -
MA remote controller signal transmission error
(Hardware error)
OO
6834 - -
MA controller signal reception error (Start bit detection error)
OO
7100 - - Total capacity error O
7101 - - Capacity code setting error O O O
7102 - - Wrong number of connected units O
7105 - - Address setting error O
7106 - - Attribute setting error O
7110 - -
Connection information signal transmission/reception error
O
7111 - - Remote controller sensor fault O O
7113 - - Function setting error O
7117 - - Model setting error O
7130 - - Incompatible unit combination O
The last digit Inverter system
0 or 1 Compressor inverter system
5 Fan inverter system
Error
Code
Prelimi-
nary
error
code
Error
(prelim-
inary)
detail
code
Error code definition
Searched unit
Notes
Outdoor unit
Indoor unit
LOSSNAY
Remote controller
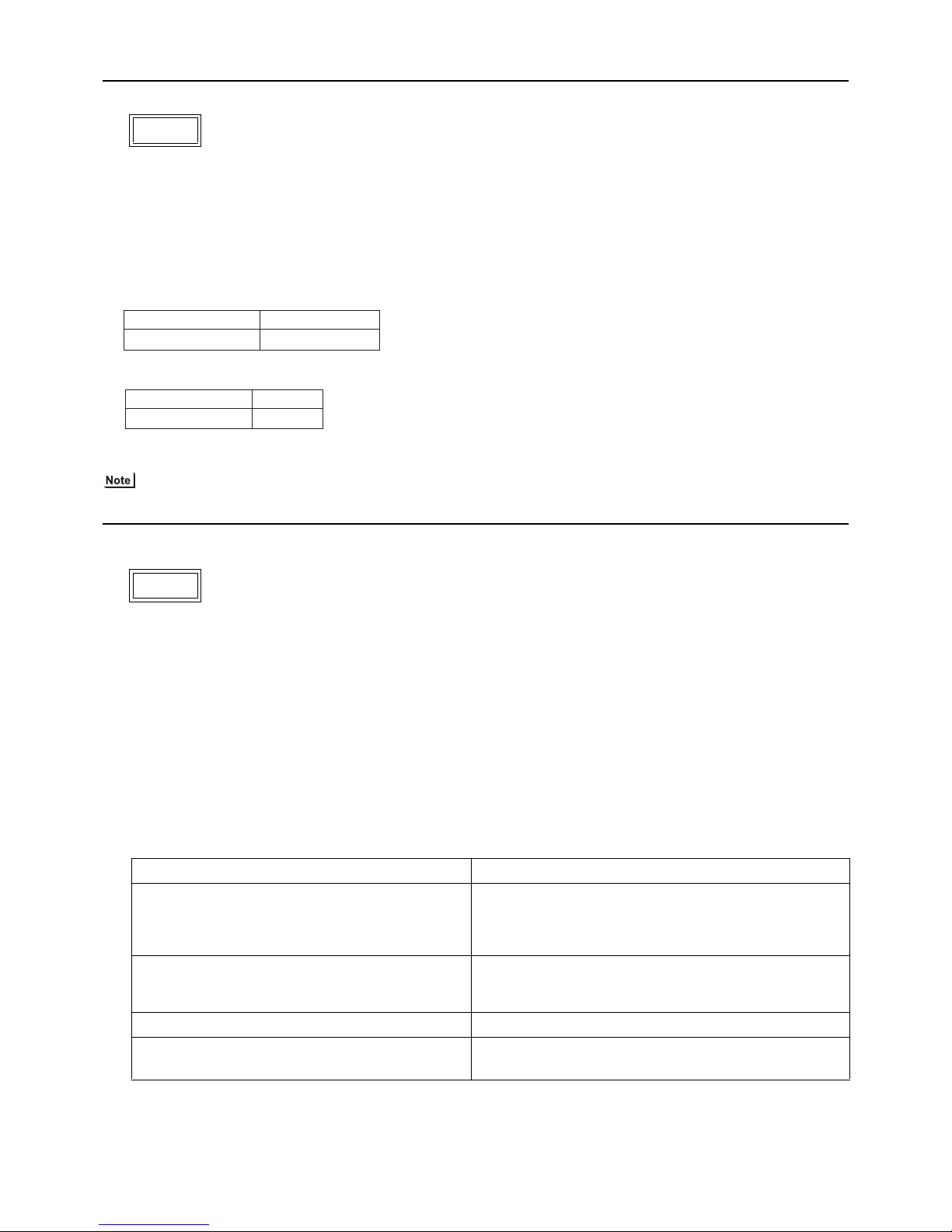
17- 17 -
HWE10170 GB
1. Error Code
Serial communication error (Indoor unit)
2. Error definition and error detection method
Serial communication cannot be established between the Indoor controller board and the INV board.
3. Cause, check method and remedy
(1) Faulty wiring
Check the following wiring connections.
1) Between Indoor controller board and Power supply board
2) Between Power supply board and INV board
(2) INV board failure or Indoor controller board failure or Power supply board failure
If the error persists after a power reset, replace the INV board, the Indoor controller board, or the Power supply board.
Refer to section [8] Troubleshooting, item 3. DC fan motor (fan motor/INV board) for error codes related to the inverter.
(page 47)
1. Error Code
Drain sensor submergence (Models with a drain sensor)
2. Error definition and error detection method
1) If an immersion of the drain sensor in the water is detected while the unit is in any mode other than the Cool/Dry mode and
when the drain pump goes from OFF to ON, this condition is considered preliminary water leakage. While this error is being
detected, humidifier output cannot be turned on.(Applicable to the units manufactured in or after October 2006)
2) If the immersion of the sensor in the water is detected four consecutive times at an hour interval, this is considered water leakage, and "2500" appears on the monitor.
3) Detection of water leakage is also performed while the unit is stopped.
4) Preliminary water leakage is cancelled when the following conditions are met:
One hour after the preliminary water leakage was detected, it is not detected that the drain pump goes from OFF to ON.
The operation mode is changed to Cool/Dry.
The liquid pipe temperature minus the inlet temperature is -10°C [-18°F] or less.
3. Cause, check method and remedy
0403
2500
CN100 CNRSC
Indoor controller board Power supply board
CNRSP CNRS2
Power supply board INV board
Cause Check method and remedy
(1) Drain water drainage problem
Clogged drain pump
Clogged drain piping
Backflow of drain water from other units
Check for proper drainage.
(2) Adhesion of water drops to the drain sensor
Trickling of water along the lead wire
Rippling of drain water caused by filter clogging
1) Check for proper lead wire installation.
2) Check for clogged filter.
(3) Failure of the relay circuit for the solenoid valve Replace the relay.
(4) Indoor controller board failure
Drain sensor circuit failure
If the above item checks out OK, replace the indoor controller board.