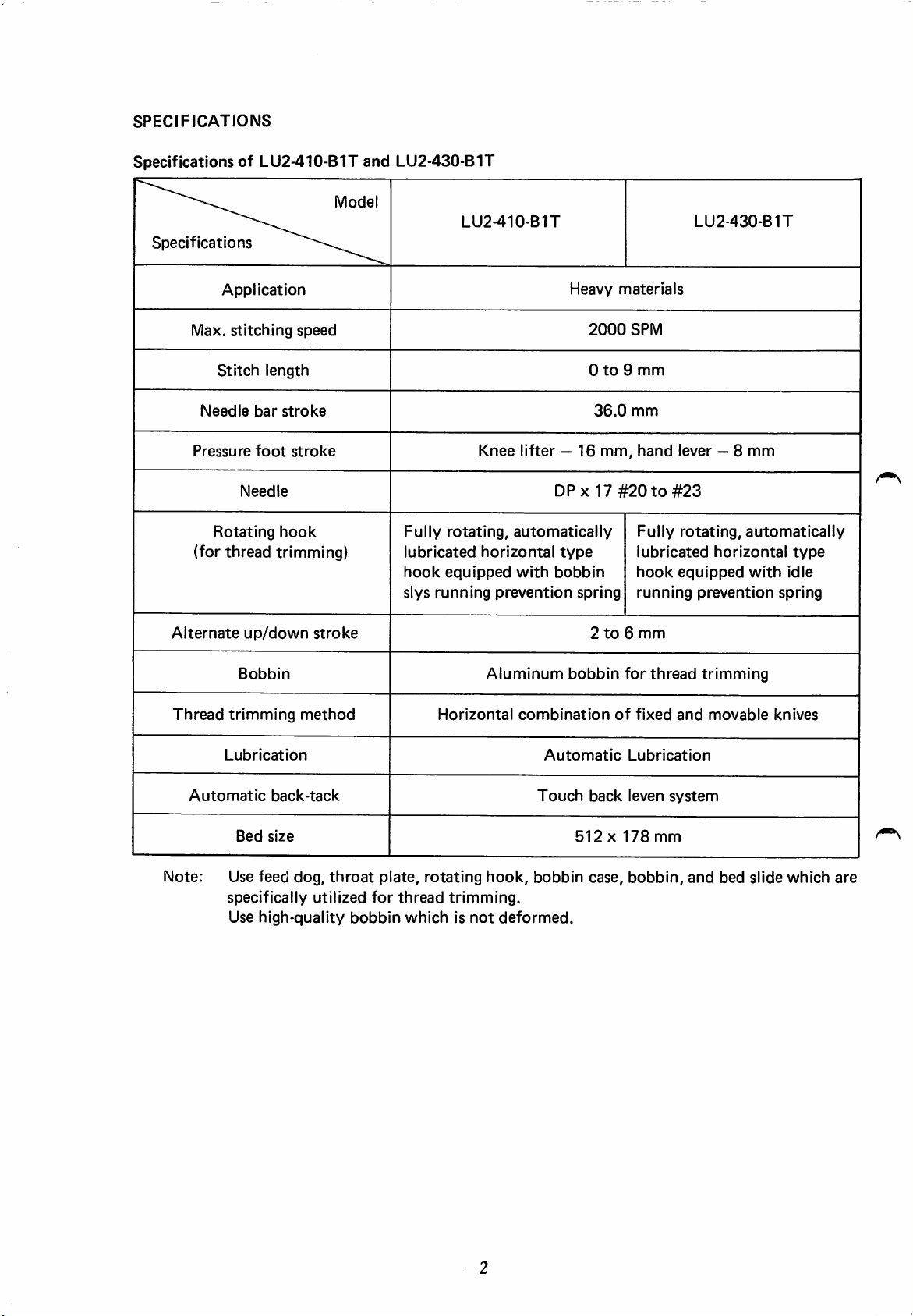
SPECIFICATIONS
SpecificationsofLU2-410-B1T
Model
Specifications
Application
Max.
Stitch
Needle
Pressure
Rotating
(for
thread
stitching
Needle
length
bar
stroke
foot
stroke
hook
trimming)
speed
and
LU2-430-B1T
Fully
lubricated
hook
slys
LU2-410-B1T
rotating,
equipped
running
Knee
lifter—16
automatically
horizontal
with
prevention
Heavy
2000
0to9
36.0
DPX17
type
bobbin
spring
materials
SPM
mm
mm
mm,
hand
#20to#23
Fully
lubricated
hook
running
LU2-430-B1T
lever —8
rotating,
horizontal
equipped
prevention
mm
automatically
type
with
idle
spring
Alternate
Thread
Automatic
up/down
Bobbin
trimming
Lubrication
back-tack
Bed
size
method
Note: Use feed dog,
specifically
Use
high-quality
stroke
throat
utilized
bobbin
plate,
for
thread
whichisnot
Horizontal
rotating
trimming.
Aluminum
combination
Automatic
Touch
hook,
bobbin
deformed.
2to6
bobbin
of
back
512X178
case,
mm
for
thread
fixed
Lubrication
leven
system
mm
bobbin,
trimming
and
movable
and
bed slide which
knives
are
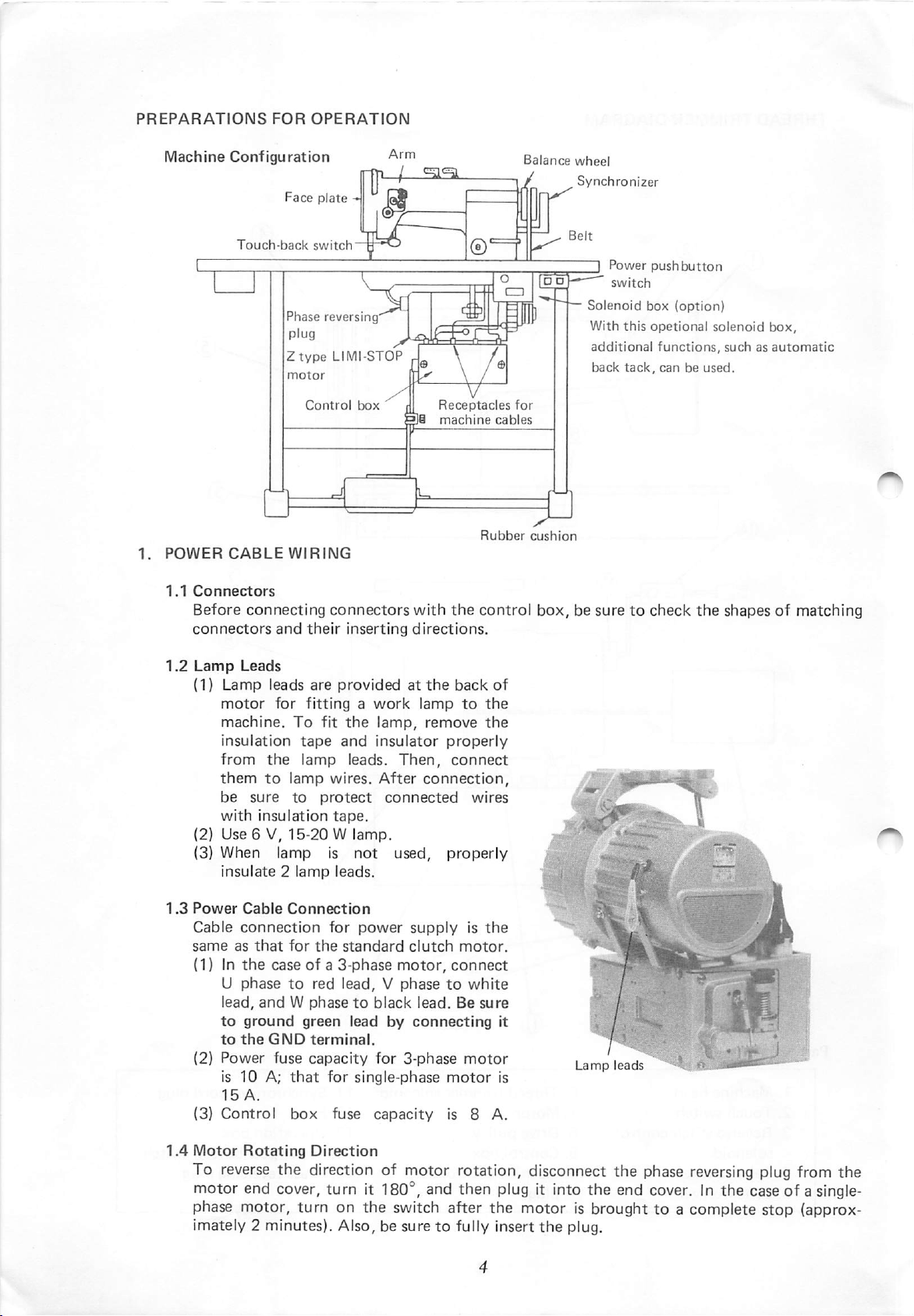
PREPARATIONS
FOR
OPERATION
1.
Machine
POWER
1.1
Connectors
Before
connectors
Configuration
Face plate
Touch-back
Phase
plug
Ztype
Control
CABLE
WIRING
connecting
and
switch'
reversing
LIMI-STOP
connectors
their
inserting
txDx
^
with
directions.
Receptacles
machine
Rubber
the
control
Balance
/
for
cables
wheel
Synchronizer
Solenoid
With
additional
back
cushion
box,besuretocheck
I Power
switch
this
tack,
pushbutton
box
(option)
opetional
functions,
canbeused.
the
solenoid
box,
suchasautomatic
shapesofmatching
1.2
1.3
Lamp
(1)
{2}
(3)
Power
Cable
same
(1) In
(2)
(3)
Leads
Lamp
motor
machine.
insulation
from
them
be
sure
with
insulation
Use6V,
When
insulate2lamp
Cable
connection
as
that
the
U
phasetored
lead,
andWphasetoblack
to
ground
Power
is 10 A;
15
A.
Control
leads
are
providedatthe
for
fittingawork
To
fit
tape
and
the
lamp
to
lamp
wires.
to
protect
tape.
15-20Wlamp.
lamp
caseofa
is
leads.
Connection
for
for
the
3-phase
lead,Vphasetowhite
green
fuse
capacity
that
for
box
fuse
back
lamp
to
the
lamp,
insulator
leads.
After
not
power
standard
remove
Then,
connection,
connected
used,
supplyisthe
clutch
motor,
properly
connect
wires
properly
motor.
connect
lead.Besure
leadbyconnecting
for
3-phase
single-phase
capacity
motor
motor
is 8 A.
of
the
the
w•
li
nilfc
JK'.j-
it
is
^
|
mniii
s-,
k
u
'$
I
JUBf
1.4
Motor
To
Rotating
reverse
Direction
the direction of motor rotation, disconnect the phase reversing plug from the
motor end cover, turn It 180°, and then plug it into the end cover. In the case of a
phase motor, turn on the switch after the motor is broughttoa complete stop (approx
imately 2 minutes). Also, be suretofully insert
the
plug.
single-
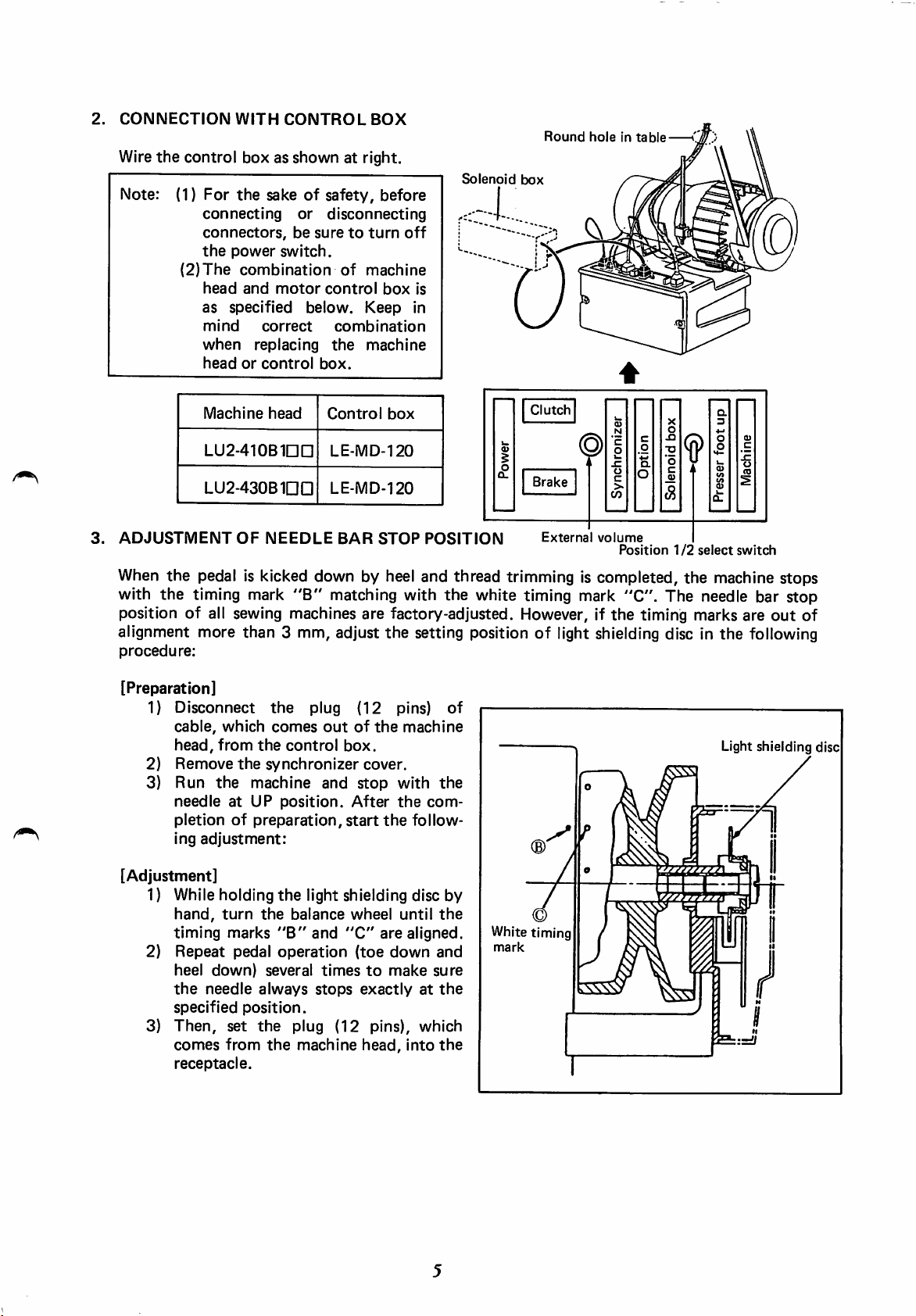
2.
CONNECTION
Wire
Note: (1)
the
WITH
control
boxasshownatright.
For
the
connecting
connectors,
the
power
(2)The
head
as
mind
specified
combination
and
when
headorcontrol
CONTROL
sakeofsafety,
or
disconnecting
be
suretoturn
switch.
motor
control
below.
correct
replacing
combination
the
box.
of
BOX
before
off
machine
box
Keep
machine
Round
holeintable
Solenoid
is
box
in
Clutch
Brake
External
volume
Position
the
timing marks are
1/2
select
switch
3.
ADJUSTMENT
When
with
Machine
LU2-410Binn
LU2-430BinD
the
pedal is kicked down by heel and thread trimming is completed, the machine stops
the
timing mark
OF
head
NEEDLE
"B"
Control
LE.MD-120
LE-MD-120
BAR
box
STOP
matching with
POSITION
the
white timing mark "C". The needle bar stop
position of all sewing machines are factory-adjusted. However, if
alignment more than 3 mm, adjust the setting position of light shielding disc in the following
procedure:
[Preparation]
1)
Disconnect
cable,
which
head,
from
2) Remove
3) Run
the
needle
pletionofpreparation,
ing
adjustment:
the
the
the
synchronizer
machine
at
UP
plug
comes
control
position.
(12
outofthe
box.
cover.
and
stop
After
start
pins)
machine
with
the
the
of
Light shielding disc
the
com
follow
out
of
[Adjustment]
1) While holding
hand,
turn
timing
Repeat
2)
heel
the
specified
3)
Then,
comes
receptacle.
marks
down)
needle
set
from
the
pedal
several
always
position.
the
the
the
light shielding disc by
balance
"B"
operation
plug
machine
wheel
and
"C"
are
(toe
down
timestomake
stops
exactlyatthe
(12
pins), which
head,
until
aligned.
and
sure
into
the
Whitetiming
mark
the