
Side
B
JY997D13901C
Side
A
JAPANESE ENGLISH
Side
B
FX3U-4AD-ADP
USER'S MANUAL
Manual Number JY997D13901
Revision C
Date June 2005
This manual describes the part na mes, dimensions, mounting, and
specifications of the product. Before use, read this manual and manuals of
relevant products fully to acquire proficiency in handling and operating the
product. Make sure to learn all the product information, safety information, and
precautions.
And, store this manual in a safe place so that you can take it out and read it
whenever necessary. Always forward it to the end user.
Registration
The company name and the product name to be described in thi s manual are
the registered trademarks or trademarks of each company.
Effective June 2005
Specifications are subject to change without notice.
Safety Precaution
This manual classify the safety precautions into two categories:
Depending on circumstances, procedures indicated by may also be
linked to serious results.
In any case, it is important to follow the directions for usage.
Associated Manuals
Note: FX
How to obtain manuals
For the necessary product manuals or documents, consult with the Mitsubishi
Electric dealer from where you purchase your product.
and .
Indicates that incorrect handling may cause hazardous
conditions, resulting in death or severe injury.
Indicates that incorrect handling may cause hazardous
conditions, resulting in medium or slight personal injur y
or physical damage.
Manual name Manual No. Description
FX
/ FX
Series
3U
3UC
User's Manual
- Analog Control
Edition
FX
/FX
Series
3U
3UC
Programming Manual
- Basic & Applied
Instruction Edition
Series
FX
3U
User’s Manual
- Hardware Edition
Series PLC specification details for I/O, wiring, installation, and
3UC
maintenance can only be found in the Japanese Manual.
2005 Mitsubishi Electric Corporation
(Read these precautions before use.)
JY997D16701
MODEL CODE:
09R619
JY997D16601
MODEL CODE:
09R517
JY997D16501
MODEL CODE:
09R516
Describes specifications for
analog control and
programming method for FX
/ FX
Series P LC.
3UC
Describes PLC programming
for basic/applied instructions
and devices.
Explains FX
specification details for I/O,
wiring, insta llation, and
maintenance.
Series PLC
3U
3U
Applicable Standard
FX3U-4AD-ADP made in June, 2005 or later comp lies with
Directive) and UL standards (UL, cUL)
following manual. However, FX
Directive), UL standards (UL, cUL).
1. Outline
The FX3U-4AD-ADP adapter for analog input (hereinafter called 4AD-ADP) is a special
adapter to add four analog input points.
1.1 Incorporated Items
Check if the following product and items are included in the package:
→
→
→ →
Caution for EC Directive
The analog special adapters have been found to be compliant to the European
standards in the aforesaid manual and directive. However, for the very best performance from what are in fact delicate measuring and controlled output device
Mitsubishi Electric would like to make the following points;
As analog devices are sensitive by nature, their use should be considered carefully. For users of proprietar y cables (integral with sensors or actuators), these
users should follow those manufacturers installation requirements.
Mitsubishi Electric recommend that shielded cables should be used. If NO other
EMC protection is provided, then users may experience temporary induced
errors not exceeding +10%/-10% in very heavy industrial areas.
However, Mitsubishi Electric sugges t that if adequate EMC precautions are followed with general good EMC practice for the users complete control system,
users should expect normal errors as specified in this manual.
• Sensitive analog cable should not be laid in the same trunking or cable
conduit as high voltage cabling. Where possible users should run analog
cables separately.
• Good cable shielding should be used. When terminating the shield at Earth
- ensure that no earth loops are accidentally created.
• When reading analog values, EMC induced errors can be smoothed out by
averaging the readings. This can be achieved either through functions on the
analog special adapters or through a users program in the FX
main unit.
Refer to FX
3U
.
Further information can be found in the
-32MT-LT does not comply with EC Directive (EMC
3UC
Series Hardware Manual (Manual No. JY997D18801)
Product
Manual
This
manual
the EC Directive (EMC
1.2 External Dimensions, Part Names, and Terminal Layout
FX3U-4AD-ADP
POWER
24+24-V1+I1+
COM1
V2+I2+
COM2
V3+I3+
COM3
V4+I4+
COM4
15.1
(0.6")
17.6
(0.7")
[10]
90(3.55")
[9]
98(3.86")
[3]
[5]
[4]
[6]
[2]
[1]
7(0.28")
74(2.92")
Special adapter
connector cover
is removed
[1] DIN rail mounting groove (DIN rail: DIN46277)
[2] Name plate
[3] Special adapter slide lock:
Used to connect special adapter on left side of this special adapter.
[4] Special adapter connector cover:
Remove this cover for connecting special adapter on the left side.
[5] Direct mounting hole:2 holes of φ4.5 (0.18") (mounting screw: M4 screw)
Not used when connecting to FX
[7]
[8]
15.5
(0.62")
[11]
Weight: Approx. 0.1 kg (0.22 lbs)
Series P LC.
3UC
Series PLC
3U
106(4.18")
24+
24-
V1+
I1+
COM1
V2+
I2+
COM2
V3+
I3+
COM3
V4+
I4+
COM4
[6] POWER LED (green):
Lit while 24V DC power is supplied properly to terminals '24+' and '24-'.
[7] Terminal block (European type):
Connect the analog voltage/current signal, and 24V DC power supply.
[8] Special adapter connector:
Used to connect this special adapter to PLC main unit or special adapter.
[9] DIN rail mounting hook
[10] Special adapter fixing hook
[11] Special adapter connec tor:
Used to connect communication special adapter or analog special adapter to this
adapter on left side.
2. Installation
The product can be mounted on a DIN rail (DIN46227) or mounted directly using
screws.
For installation/uninstallation and safety precautions, refer to the following manuals:
INSTALLATION
PRECAUTIONS
• Cut off all phases of the power source externally before starting the installation or
wiring work, thus avoiding electric shock or damages to the product.
INSTALLATION
PRECAUTIONS
• Use the product in the environment within the general specifications described in
PLC main unit manual (Hardware Edition).
Never use the product in areas with dust, oily smoke, conductive dusts, corrosive
gas (salt air, Cl
expose it to high temperature, condensation, or wind and rain.
If the product is used in such a pla ce described above, elect rical shock, fire,
malfunction, damage, or deterioration may be caused.
• When drilling screw holes or wiring, cutting chips or wire chips should not enter
ventilation slits.
Such an accident may cause fire, failure or malfunction.
• Do not touch the conductive parts of the product directly, thus avoiding failure or
malfunction.
• Fix the special adapter securely to the specified connector.
Incorrect connection may cause malfunction.
2.1 Connection to the FX3U Series PLC
• Refer to the procedure 2) for configuring a new system.
• Refer to the procedure 1) for adding product to an existing system.
Procedure
1) Turn off the power.
Disconnect all the cables connected to the PLC main unit and special adapter.
Dismount the main unit and special adapter mounted on DIN rail or mounted directly
using screws.
2) Install an expansion board to the main unit.
For installation of expansion board, refer to the following manual:
3) Remove the special adapt er connector cover on
the expansion board (Right fig .A).
In case of connecting this product to another
special adapter, please replace the 'expansion
board' in the above description with a 'special
adapter' and perform the procedure as
indicated.
4) Slide the special adapt er slide lock (Right fig.B) of
the main unit.
In case of connecting this product to anoth er
special adapter, pleas e replace the 'main unit' in
the above description with a 'special adapter' and
perform the procedure as indicated. (Please
replace the following procedures similarly.)
Refer to the FX
→
→
→ →
2
, H2S, NH3, SO2, or NO2), flammable gas, vibrations or impacts, or
Refer to the FX
→
→
→ →
3U
Series User's Manual - Hardware Edition.
3U
Series User's Manual - Hardware Edition
3
X
4)
3)
B
F
N
U
R
O
T
S
A
B
R
M
8
M
-4
8
U
4
3
-
U
FX
P
4)
5) Connect the
special adapter
(Right fig.C) to
the main unit as
shown on the
right.
6) Slide back the
special adapter
slide lock (Right
fig.B) of the main
unit to fix the
special adapter
(Right fig.C).
C
B
F
X
3
U
*
*
-
*
*
*
*
P
O
W
E
R
6)
5)
5)
5)
Connection precautions
Connect all the hi gh-speed I/O speci al adapters before co nnecting other
special adapters when they are used in combination.
Do not connect a high- speed I/O special adapt er on the left si de of a
communication or analog special adapter.
2.2 Connection to the FX
• Refer to the procedure 2) for configuring a new system.
• Refer to the procedure 1) for adding product to an existing system.
Procedure
1) Turn off the power.
Disconnect all the cables connected to the PLC.Dismount the PLC from the
DIN rail.
2) Install an expansion board to the main unit.
For installation of expansion board, refer to the following manual:
3) Remove the special adapter connector
cover on the expansion board (Right fig.A).
In case of connecting this product to
another special adapter, plea se replace
the 'expansion board' in the above
description with a 'special adapter' and
perform the procedure as i ndicated.
4) Slide the special ad apter slide lock (Right
fig.B) of the main uni t.
In case of connecting this product to
another special adapter, please replace
'main unit' in the above description wi th
'special adapter' and p erform the
procedure as indicated. (P lease replace
the following procedures similarly.)
5) Connect special
adapter (Rig ht
fig.C) to the
main unit as
shown on the
right.
6) Slide back the
special adapter
slide lock (Right
fig.B) of the
S
main unit to fix
/E
the special
adapter (Right
fig.C).
Refer to the manua l of the expansion board to be used.
→
→
→ →
C
Series PLC
3UC
P
O
W
4)
4)
B
A
B
FX
3
U
***
***
E
R
6)
5)
5)
5)
M
8
-4
U
3
X
F
S
/E
R
M
8
M
4
-
8
3U
-4
X
3U
F
X
F
N
U
R
P
O
T
S
6)
B
3)
4)
B
6)
B
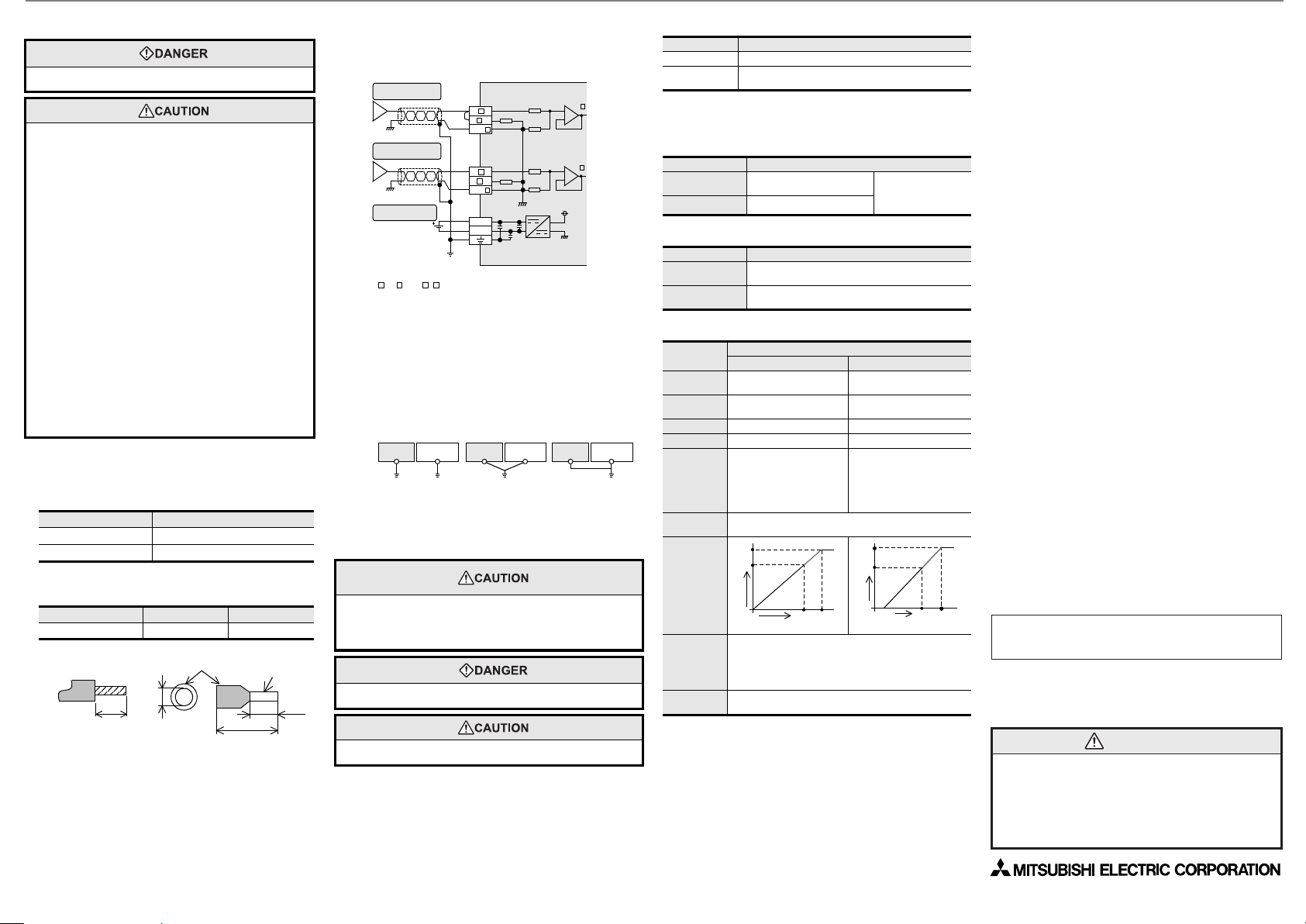
This manual confers no industrial property rights or any rights of any other kind,
nor does it confer any patent licenses. Mitsubishi Electric Corporation cannot be
held responsible for any problems involving industrial property rights which may
occur as a result of using the contents noted in this manual.
Warranty
Mitsubishi will not be held liable for damage caused by factors found not to be
the cause of Mitsubishi; machine damage or lost profits caused by faults in the
Mitsubishi products; damage, secondary damage, accident compensation
caused by special factors unpredictable by Mitsubishi; damages to products
other than Mitsubishi products; and to other duties.
For safe use
This product has been manufactured as a general-purpose part for general
industries, and has not been designed or manufactured to be incorporated in
a device or system used in purposes related to human life.
Before using the product for special purposes such as nuclear power, electric
power, aerospace, medicine or passenger movement vehicles, consult with
Mitsubishi Electric.
This product has been manufactured under strict quality control. However
when installing the product where major accidents or losses could occur if the
product fails, install appropriate backup or failsafe functions in the system.
•
•
•
HEAD OFFICE
HIMEJI WORKS
: MITSUBISHI DENKI BLDG MARUNOUTI TOKYO 100-8310
: 840, CHIYODA CHO, HIMEJI, JAPAN
3. Wiring
WIRING
PRECAUTIONS
• Cut off all phases of power source externally, before installation or wiring
work in order to avoid electric shock or damage of product.
WIRING
PRECAUTIONS
• Never let cutting chips and wire chips enter the ventilation slits of this product
or PLC when performing wiring.
Otherwise, fire, failure or malfunction may occur.
• Make sure to observe the precautions below in order to prevent any damage
to a machine or any accident which might be caused by abnormal data
written in the PLC due to the influence of noise:
1) Do not lay close or bundle with the main circuit, high-voltage power line,
or load line.
Otherwise effects of noise or surge induction are likely to take place.
Keep a safe distance of more than 100 mm (3.94") fr om the above when
wiring.
2) Ground the shield wire or shield of a shielded cable at one point on the
PLC. However, do not ground at the same point as high voltage lines.
• Observe the following items to wire the lines to the European terminal board.
Failing to do so may cause electric shock, shor t circuit, disconnection, or
damage of the product.
- The disposal size of the cable end should follow the dimensions described
in this manual.
- Tighten to a torque should follow the torque described in this manual.
- Twist the end of strands and make sure there is no loose wires.
- Do not solder-plate the electric wire ends.
- Connect only the electric wires of regulation size.
- Fix the electric wires so that the terminal block and connected parts of
electric wires are not directly stressed.
• Properly perform wiring to the terminal block of the FX
following the precautions below in order to prevent electrical shock, shortcircuit, breakage of wire, or damage to the product:
- The disposal size of the cable end should follow the dimensions described
in this manual.
- Tighten to a torque should follow the torque described in this manual.
Series PLC
3U
3.1 Applicable Cabl e and Terminal Tightening Torque
3.1.1 Terminal block (European type)
1) Wire size
Wiring to analog device should use 20-22 AWG wire.
2) Applicable cable
3) Termination of cable end
Strip the coating of strand wire and twist the cable core before connecting it,
or strip the coating of single wire before connecting it.
An alternative connection is to use a ferrule with insulating sleeve.
When using a stick terminal with insulating sleeve, choose a wire with proper
cable sheath referring to the above outside dimensions, or otherwise, the wire
cannot be inserted easily.
The tightening torque must be 0.22 to 0.25N
Type Wire size
Single-wire
2-wire
2
0.3mm
to 0.5mm2 (AWG22 to 20)
2 pieces of 0.3mm
2
(AWG22)
Manufacturer Model Caulking tool
Phoenix Contact Co., Ltd. AI 0.5-8WH CRIMPFOX UD6
- Strand wire/single wire
9mm
(0.35")
- Stick terminal with insulating sleeve
Insulation sleeve
2.6mm(0.1")
•
m.
Contact area
14mm(0.55")
8mm
(0.31")
3.2 Power Supply Wiring
3.3 Wiring of Analog Input
For the power supp ly wiring, refer to th e FX
→
→
→ →
→
→
→ →
Using current
input
Using voltage
input
External power
supply wiring
(Ground resistance: 100Ω or less)
24V DC
*1
*1
*3
Grounding
Terminal
User’s Manual - Analog Cont rol Edition
For the terminal configuration, refer to Section 1.2
V +
I +
V +
I +
24+
24-
250
250
4AD-ADP
147k
Ω
47k
147k
Ω
47k
block
*2
COM
COM
3U
3UC
/ FX
Series
Ω
ch
Ω
Ω
ch
Ω
+15V
V +, I +, ch : represents the channel number.
*1 Use 2-core shielded twisted pair cable for the analog input lines, and separate
the analog input lines from other power lines or inductive lines.
*2 Make sure to short -circuit the 'V+' and 'I+' terminals when current is input.
(: input channel number)
*3 24V DC servi ce power supply of the FX
3.4 Grounding
Grounding should be performed as stated below.
• The grounding resistance should be 100Ω or less.
• Independent grounding should be performed for best results.
When independent groundin g is not performed, perform "shar ed grounding"
of the following figure.
Another
PLC
equipment
Independent grounding
Best condition
• The grounding wire size should be AWG 22-20 (0.3-0.5 mm
• The grounding point should be close to the PLC, and all grounding wire
should be as short as possible.
4. Specification
STARTUP AND
MAINTENANCE
PRECAUTIONS
• Do not disassemble or modify the unit.
Doing so may cause failure, malfunction or fire.
* For repair, contact your local Mitsubishi Electric distributor.
• Do not drop the product or do not exert strong impact, doing so may cause
damage.
DISPOSAL
PRECAUTIONS
• Please contact a company certified in the disposal of electronic waste for
environmentally safe recycling and disposal of your device.
TRANSPORT AND
STORAGE PRECAUTIONS
• During transportation avoid any impact as the product is a precision instrument.
Check the operation of the product after transportation.
Series PLC can also be used.
3U
For details, refer to the FX
→
→
→ →
PLC
Shared grounding
Good condition
Manual - Hardware Edition.
Another
equipment
Series User's
3U
Another
PLC
equipment
Common grounding
Not allowed
2
).
4.1 Applicable PLC
Model name Applicability
Series PLC Ver. 2.00 (from the first product) and later
FX
3U
FX
Series P LC
3UC
The version number can be checked by monitoring D8001 as the last three digits
indicate it.
4.2 General Specification
For the general specification, refer to the manual of the PLC main unit.
The items other than the following are equivalent to those of the PLC main unit.
Ver. 1.20 (from the pr oduct manufactured in May, 2004 with SER
No. 45****) and later
Item Specification
Dielectric withstand
voltage
Insulation resistance
500V AC for one minute
5MΩ or more by 500V DC megger
Conforming to JEM-1021
Between all terminals and
ground termi nal of PLC
main unit
4.3 Power Supply Specification
Item Specification
A/D conversion
circuit driving power
Interface driving
power
24V DC +2 0%/-15%, 40mA for 24V D C
Connect a 24V DC power supply to the terminal block.
5V DC, 15mA
5V DC power is su pplied inte rnally from th e main unit.
4.4 Performance Specification
10V
Description
4 to 20mA DC
(Input resistance: 250 Ω)
•±0.5% (±80µA) for full scale of
16mA (when ambient
temperature is 25°C±5°C)
•±1.0% (±160µA) for full scale
of 16mA (when ambient
temperature is 0°C to 55°C)
1640
1600
Digital output
0
4mA
Analog input
20mA
20.4
mA
Item
Analog input
range
Maximum
absolute input
Digital output
Resolution
Total accuracy
A/D conversion
time
Input
characteristics
Insulation
method
Occupied
points
Voltage input Current input
0 to 10V DC
(Input resistance: 194 kΩ)
-0.5V, +15V -2mA, +30mA
12 bits, binary 11 bits, binary
2.5mV (10V/4000) 10µA (16mA/1600)
•±0.5% (±50mA) for full scale
of 10V (when ambient
temperature is 25°C±5°C)
•±1.0% (±100mA) for full scale
of 10V (when ambient
temperature is 0°C to 55°C)
200 µs
(The data will be updated at every scan time of the PLC.)
4080
4000
Digital output
0 10.2V
Analog input
• The photo-coupler is adopted to insulate the analog input area
from the PLC.
• The DC-DC converter is adopted to insulate the driving power
supply line from the analog input area.
• Channels are not insulated from each other.
0 point (Thi s number is n ot related to the maximum num ber of
input/output points of the PLC.)