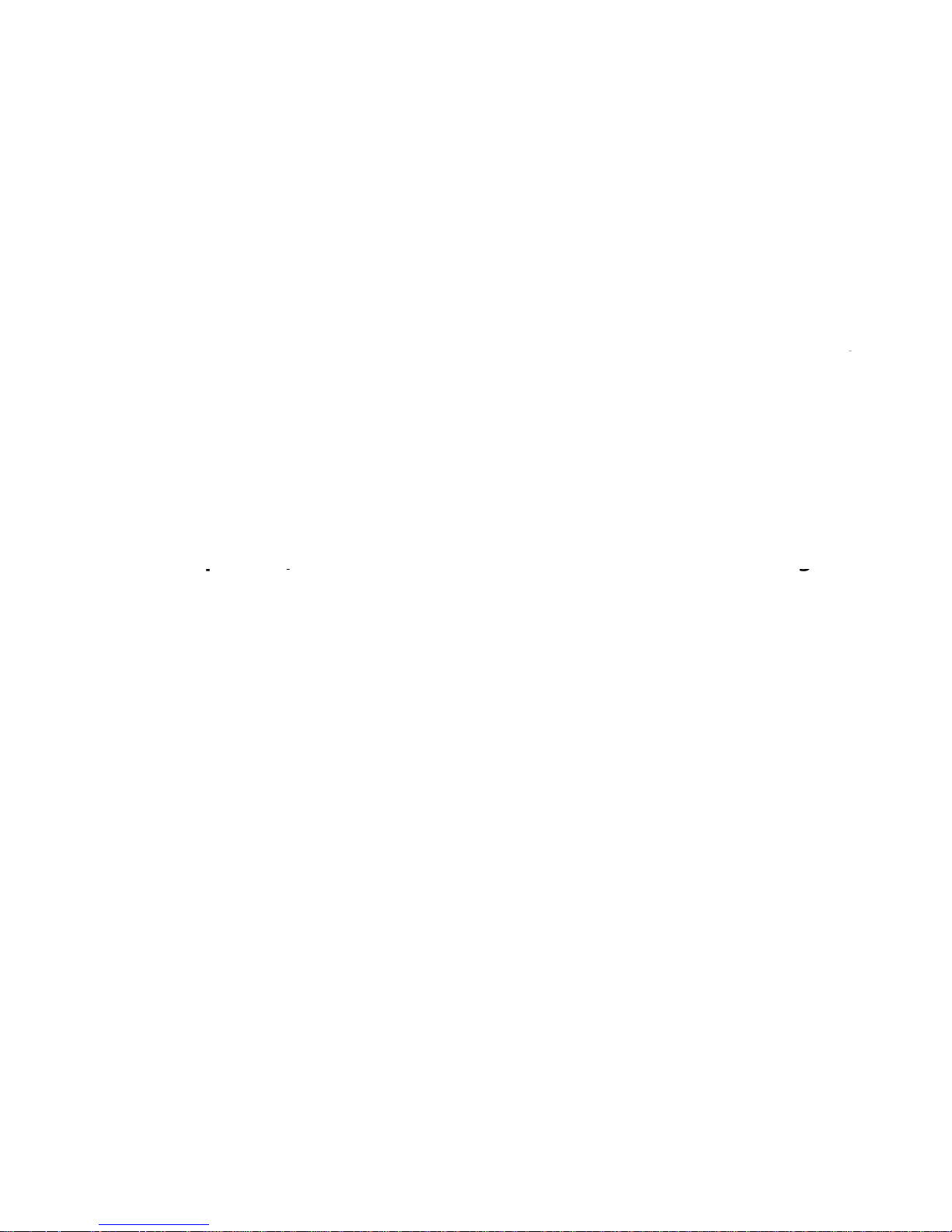
Contents
1 Warnings Page 6
2 General Information Page 7
3 Maintenance Intervals Page 8
3.1 Minuteman System Maintenance K (Customer) Page 9
3.2 Minuteman System Maintenance I (125 hours
of o
3.3 Minuteman System Maintenance II (250 hours
of operation) Page 11
3.4 Minuteman System Maintenance S (500 hrs of
operation, at least yearly)
4 Squeegee Cable and Recovery Tank Gasket Page 13
4.1 Squeegee Adjustment (First Version) Page 14
4.2 Squeegee Adjustment (new Style) Page 15
4.3 Squeegee Lift Cable, Micro Switch, Vacuum Motor
4.4 Squeegee Wheel Adjustment Page 17
5 Brush Head (Disk Brushes) Connections Page 18
5.1 Brush Motor Information Page 19
2
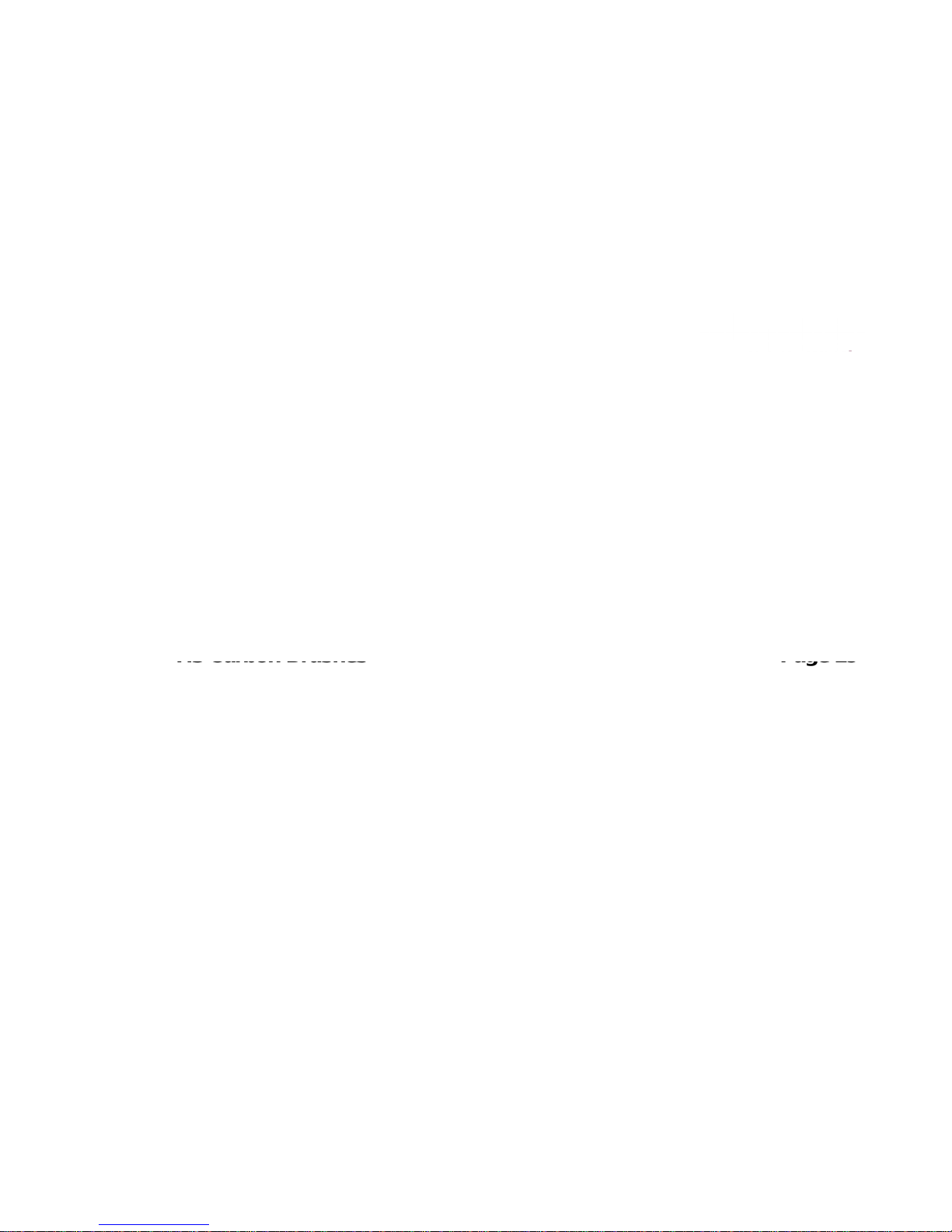
Contents
6 Brush Head Transport Position Page 21
6.1 Brush Switch Page 22
ustment on the Disk Models
6.3 Brush Pressure (Disk Decks) Page 24
6.4 Cylindrical Brush Head Electrical Connections Page 25
6.5 Cylindrical Brush Head Adjustment Page 26
7 Drive and Wheels - General Data Page 27
7.1 Electric Brake Page 27
7.2 Transaxle Motor Page 28
7.4 Drive Potentiometer Page 30
8 Water Supply Page 31
8.1 Solenoid Page 31
8.3 Solution Tank Cleanout Page 32
8.4 Solution Flow Rates Page 33
8.5 Water Pump Page 34
10 Table of Error Codes and Information Page 36
3
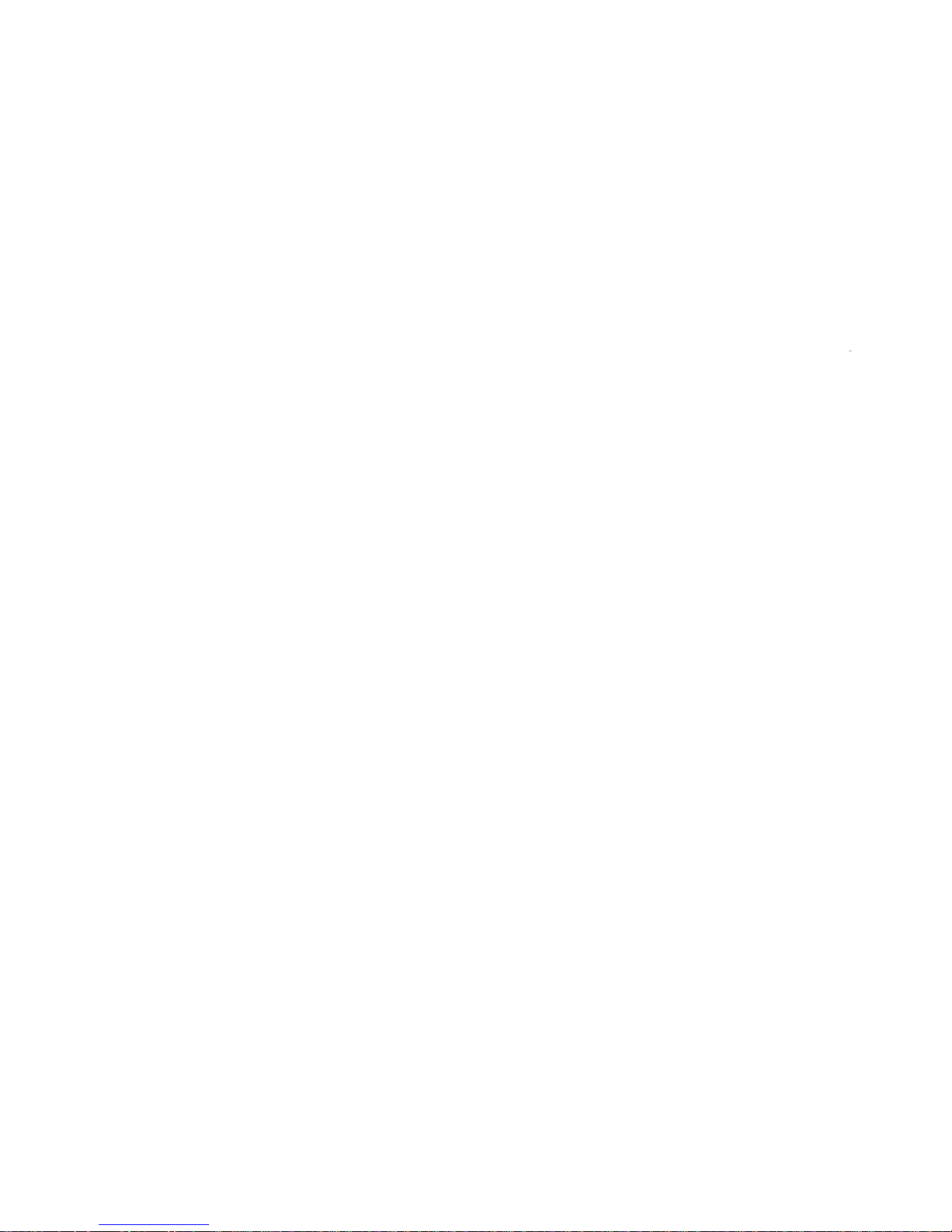
Contents
11 Battery Charger Page 38
11.1 Operating Instructions Page 40
11.2 Charger Error Codes Page 40
11.3 Charger Trouble Shooting
11.4 Charger Maintenance Points Page 45
11.5 Programming The Charger Page 46
11.6 Replacing The Charger Harness Page 49
12.1 Maintaining Wet Lead Acid Batteries Page 50
12.2 Load Testing Batteries Page 52
12.3 Hydrometer Testing Page 53
13 Fuse Locations Version 2 Page 56
13.1 Controller Version 3 Page 57
4
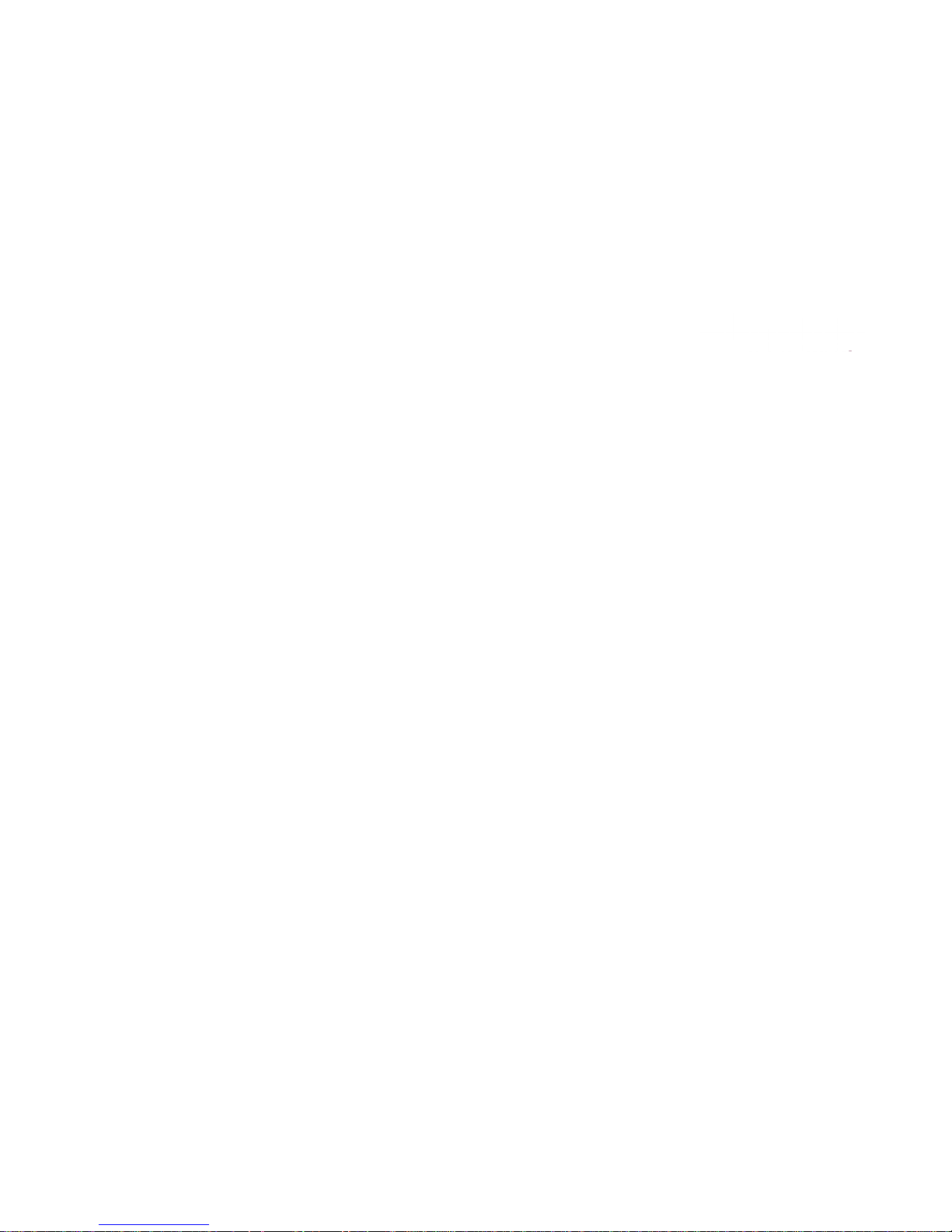
Contents
14 Controller Connections Page 58
15 Trouble Shooting Controller Page 59
16 Contactor Harness Page 60
g
17 Contactor Wiring Page 61
18
Testing the Main Power Relay Page 63
19 Wiring Diagram Models with 19 Gallon Tanks Page 68
20 Wiring Diagram Models with 24 Gallon Tanks Page
7220 Wiring Diagram Models with 24 Gallon Tanks Page 73
20 Wiring Diagram Models with 30 Gallon Tanks Page 7
8
21 Notes Page 83
5
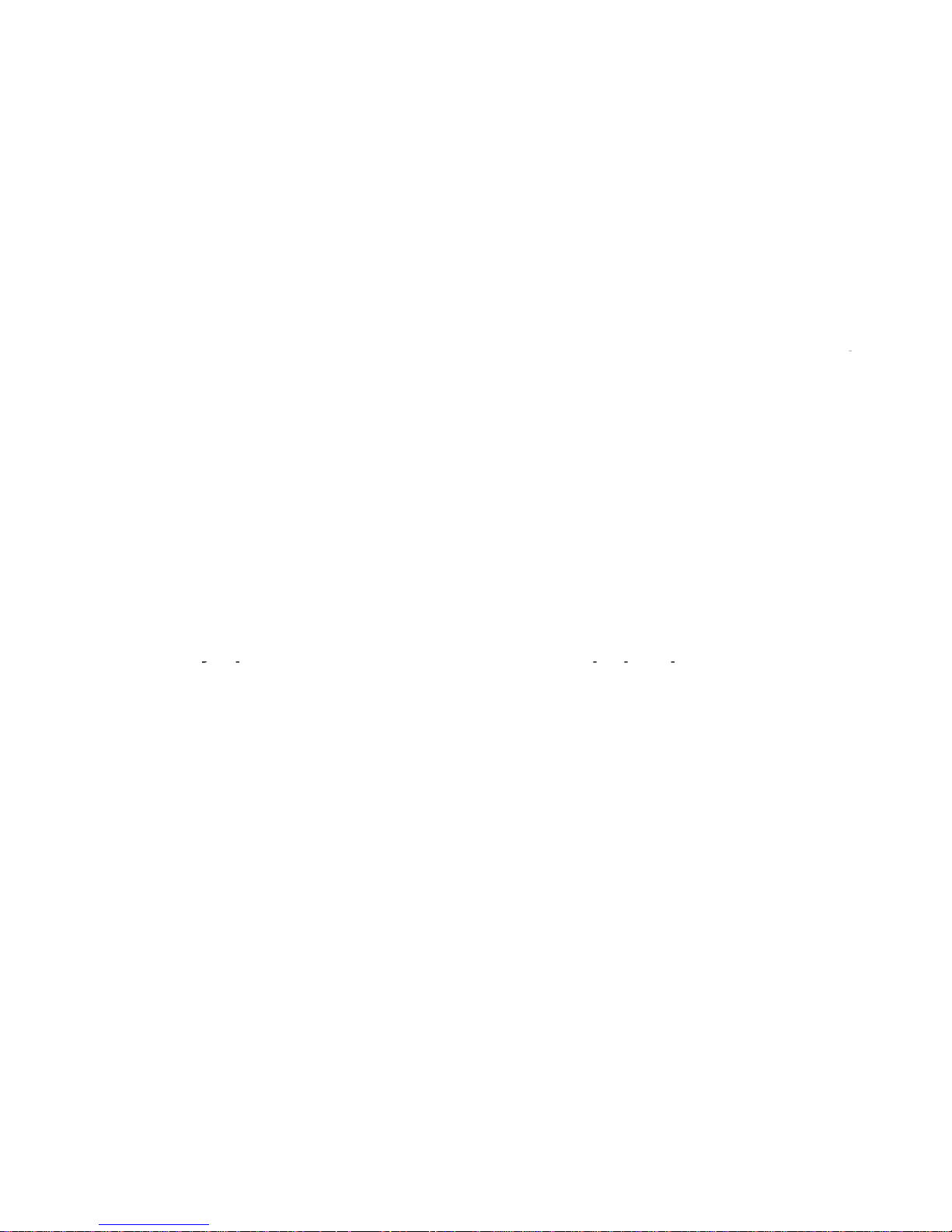
1. Warnings
• Disconnect the A.C. Cord from the outlet and and D.C. Cord from the battery
pack before servicing the machine
Except for making voltage and current
measurements.
• Before replacing the main fuses, only loosen the nuts. Do not remove them
completely. Failure to do so could cause a short circuit.
• Place the new stripe fuse fully and evenly under the nuts and washers and
make sure not to twist the end tabs, they can easily be torn.
• After an
repair work is done, test the machine for proper operation.
• When servicing the machine always observe the general safety and accident
prevention guidlines.
6

2. General Information
•The display offers a service indication. Upon turning on the key switch, a four digit
number describing the software version (e.g. 1.0.0.2) appears for about 3 seconds,
owed by another 4-digit code indicating the last error recorded, then followed by
the hour meter.
•If a failure occurs, the code appears in the control panel and an acoustic signal
sounds. The current error code appears as 4
flashing dots in the service display. Only if these criteria are met, the error is a
current one!
The error codes are listed in a tables in chapter 10.
•When raising the machine with a car
jack use the area of the frame in front of
the caster wheels on the left or the right.
7

3. Maintenance Intervals
In a modular structure, the Minuteman System Maintenance determines the specific
technical proceedures to be preformed and sets the time interval between the two
maintenance cycles.
For each of the maintenance cycle, the replaceable parts are determined as well.
Further details described in the specific chapters.
•Minuteman System Maintenance K:
e performed by the customer (in daily or weekly intervals) according to the maintenance
and care instructions as specified in the operating instructions.
The operator must be professionally instructed after delivery of the machine by selling
dealer .
•Minuteman System Maintenance I: (after every
To be preformed by an authorized Minuteman Service Center in accordance with the
machine-specific system maintenance.
•Minuteman System Maintenance II: (after every 250 hours of operation)
e preformed by an authorized Minuteman Service Center in accordance w
e
machine-specific system maintenance.
•Minuteman System Maintenance S: (after every 500 hours of operation, safety check) To
be performed by an authorized Minuteman Service Center in accordance with the machinespec
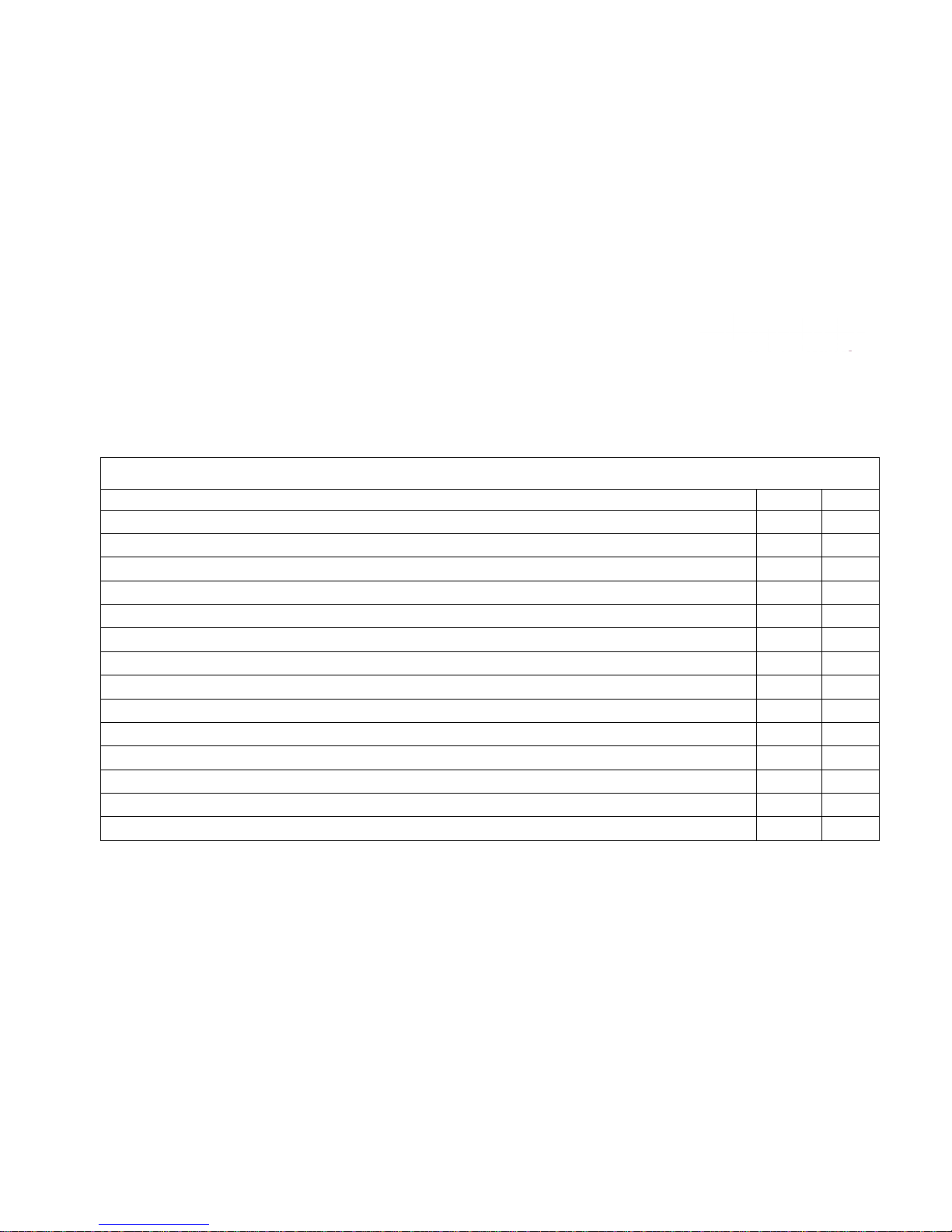
3.1 Minuteman System Maintenance K
Daily Weekly
Fillthecleanwatertankandmixtheproperamountandtypeofcleaningsolution. O
Chargethebatteries. O
thebrushhead,Cleanifneededwithadampcloth.Donotgetwaterinsidethemotor
Checkthesqueegee,cleanifneeded O
Checkthelidgasketontherecoverytank. O
Emptyandflushtherecoverytankwithcleanwater. O
Checkthewaterlevelsofallthebatteries.Adddistilledwater,ifneeded.Donotoverfill. O
Checkthepadsandbrushesforwear.Replaceifneeded. O
Checkthesqueegeehoseforclogs,damageandwear.Replaceifneeded O
thesqueegeerubbersforcutsandwear.Fliptheblade(s)overorreplace.
Checkthesolutionfilter.Cleanifneeded. O
Flushthecleanwatersolutiontankwithwarmwater. O
Testallthefunctionsofthemachine. O
9
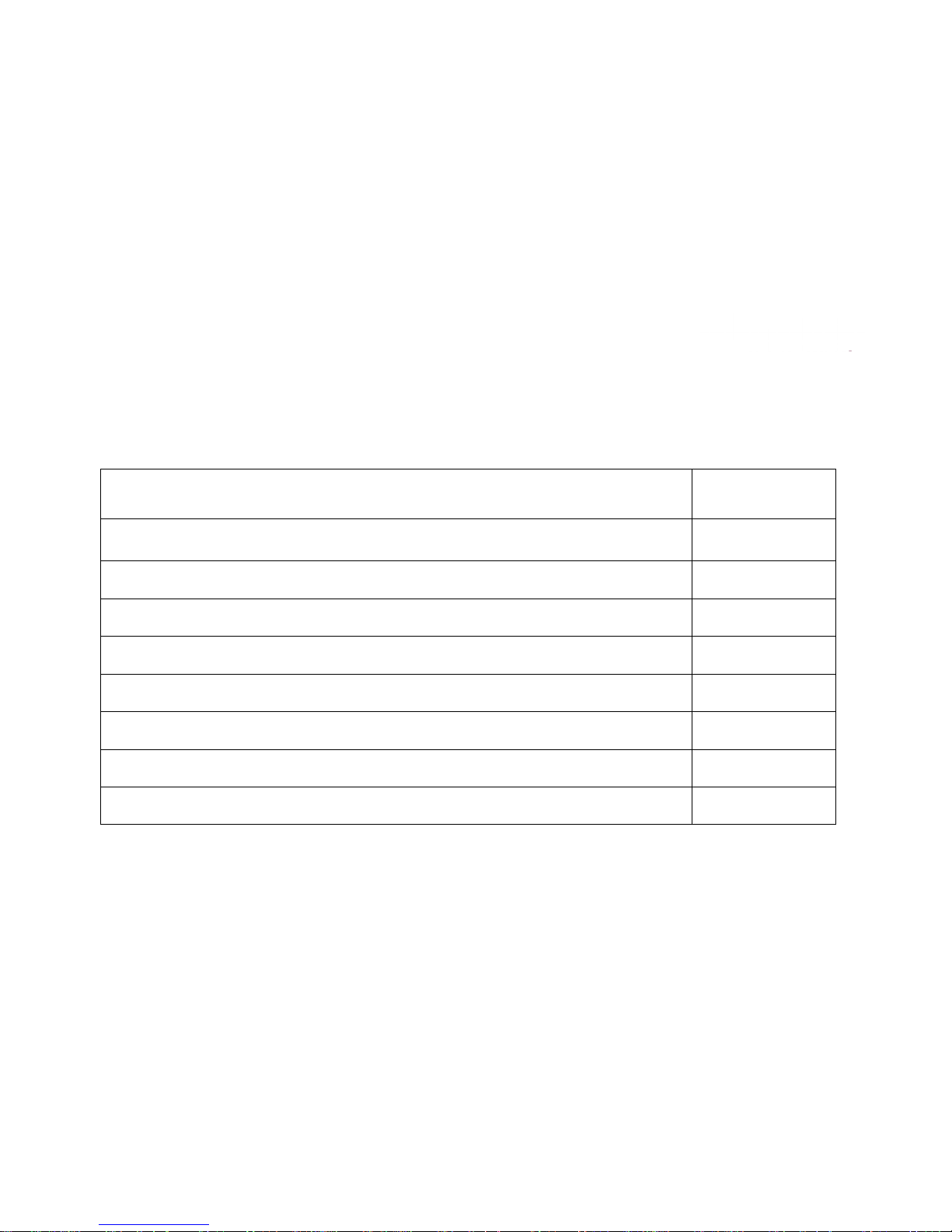
3.2 Minuteman System Maintenance I
Tobeperformedbytheauthorizedservicecenter
Interval
Every125hoursof
operation
Checkthebatterycharger.Makesureitisfunctioningproperly
O
Checktherecoverylidgasket.Replaceifneeded
O
thebrushliftlinkageswithgrease
Checkforloosehardware,tightenifneeded.
O
Checkthetirepressureonpneumaticwheelsat65PSI,ifequipped.
O
Lubricatethesqueegeelinkageswithgrease.Useasmallbrush.
O
Inspecttheentiremachinefordamage,wearandproperoperation.
O
10

3.3 Minuteman System Maintenance II
Tobeperformedbytheauthorizedservicecenter
Interval
Every250
hoursof
operation
thecasterwheelsforwearanddamage
Inspectthecarbonbrushesforwearinthetransaxle.Replace,ifneeded. O
Inspecttherecoverydrainhoseforwearordamage.Replace,ifneeded. O
thebrushbumperrollersforwearordamage
Inspectthecarbonbrushesforwearinthebrushmotorsforwear.
Blowoutwithcompressedair. O
Inspecttherecoveryhosefordamageorwear.Replace,ifneeded. O
Inspectthesqueegeeassemblyforproperadjustment.Repair,ifneeded. O
Testthemachineforproperoperation. O
11
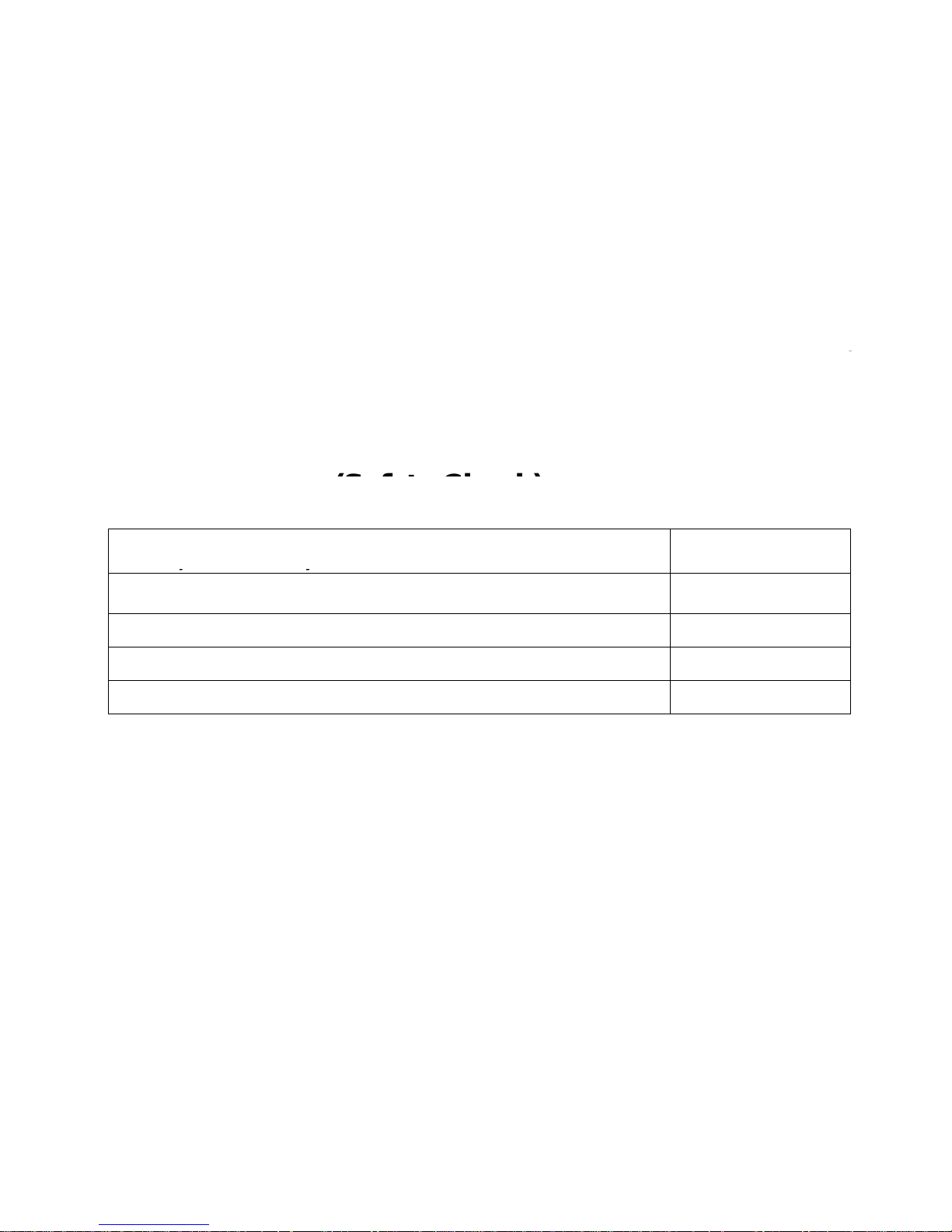
3.4 Minuteman System Maintenance S
Tobeperformedbytheauthorizedservicecenter Interval
Every500hoursof
operation
Replacethecarbonbrushesinthetransaxle. O
Replacethecarbonbrushesinthebrushmotors. O
Testthemachineforproperoperation. O
12
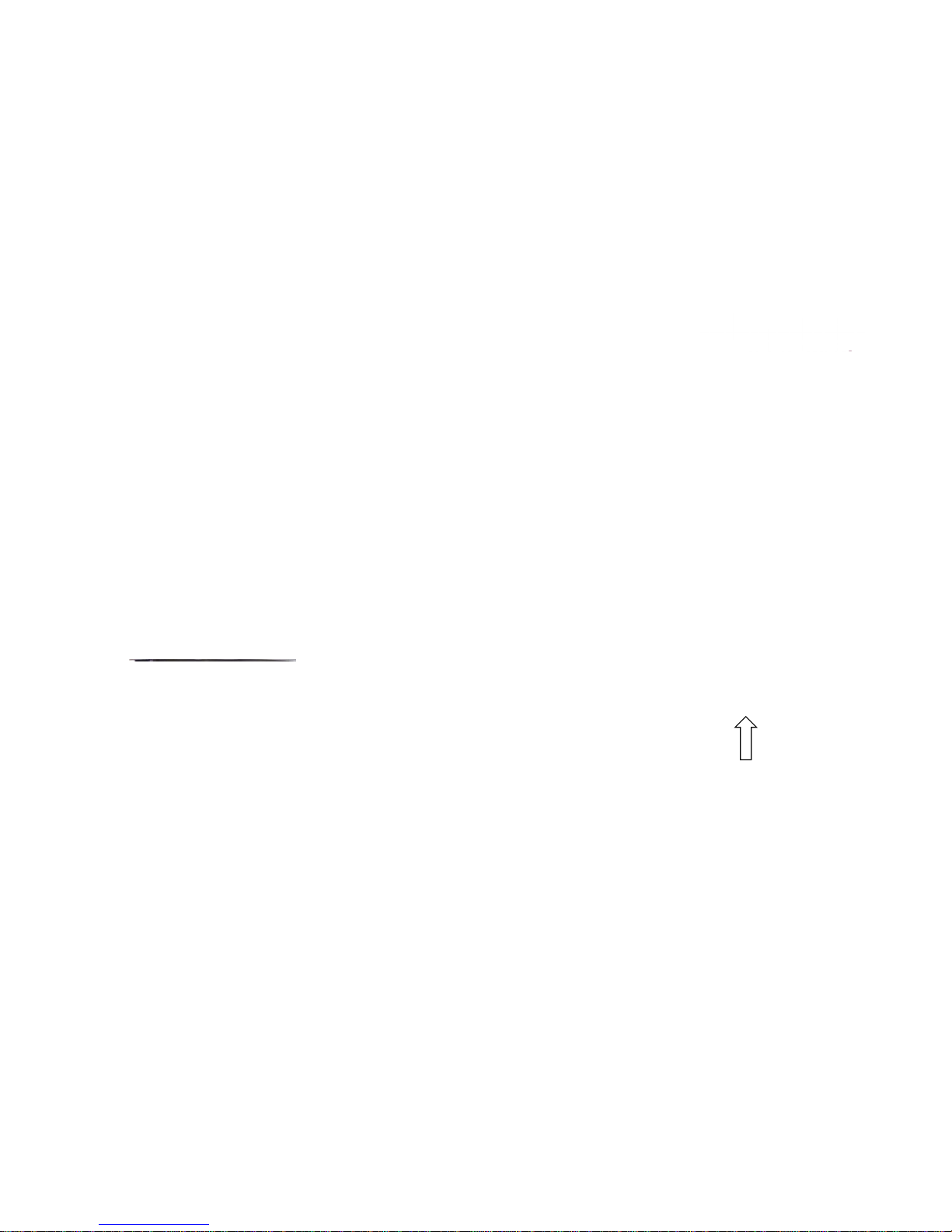
4. Squeegee Cable And Gasket
4. The squeegee cable is attached to the lift lever (top) via a spring (Fig. 5/5). The bottom is
attached to the eyebolt at the squeegee mechanism (Fig. 5/6). The squeegee lift cable can be
accessed after opening the electronic module cover at the rear of the machine.
The vacuum motor is connected to the A1 at A1.X34:5+6 on the controller. Current
consumption of the vacuum motor amounts to approx. 25A max.
The vacuum water lift in the closed tank is at least 65 inches (150mbar).
Insert the recovery tank cover gasket (Fig. 5/7) so that the seam is positioned at the front center
with a gap of approx. 1mm. The dirty drip water on the top sealing surface will be drawn into the
recovery water tank.
Fig. 5/5
Fig. 5/6
Fig. 5/7
13
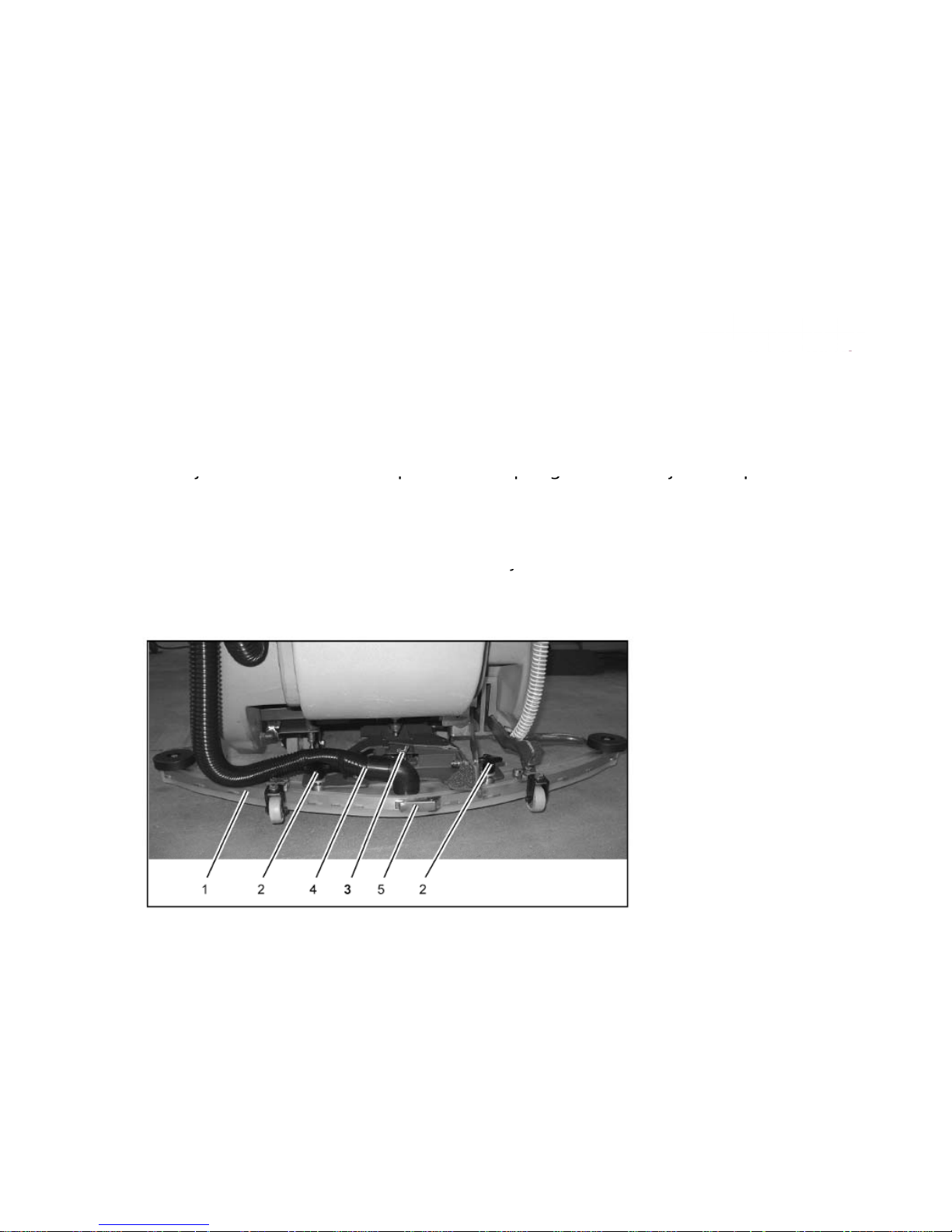
ersion one
4.1 Squeegee Adjustment
Correct squeegee adjustment is prerequisite for optimal suction results.
Before ad
ustment first check the pitch of the squeegee and re-adjust if required.
1. Place machine on level ground.
2. Loosen nut of the adjustment screw (pos. 3, Fig. 5/1) and adjust sealing strips in
parallel to the floor. Turn adjustment screw clockwise: clearance between squeegee
blade and floor broadens in the center. Turn ad
ustment screw counter-clockwise:
clearance between squeegee blade and floor narrows in the center.
3. Turn machine on, lower squeegee and check drying pattern.
1 Squeegee
2 Star-shaped knob
3 Adjustment screw
5 Toggle-type fastener
Fig. 5/1
14
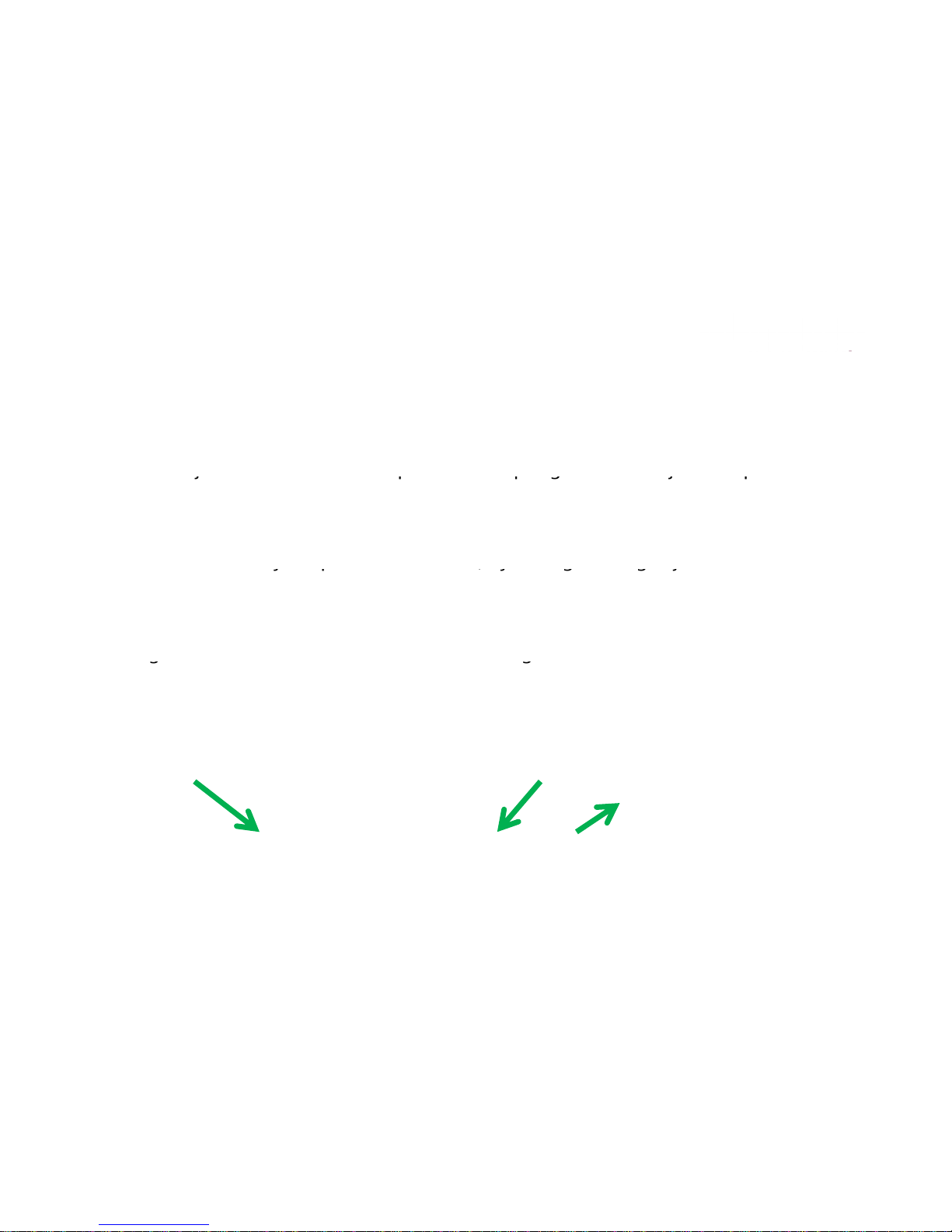
ersion Two
4.2 Squeegee Adjustment
Correct squeegee adjustment is prerequisite for optimal suction results.
Before ad
ustment first check the pitch of the squeegee and re-adjust if required.
1. Place machine on level ground.
2. Loosen the two bolts, located on each side (Fig 5/2A) with the squeegee attached
while holding another wrench on the location shown on Fig 5/2B. Adjust squeegee
rubbers so that the
are parallel to the floor, by turning the long adjustment shaft on the
right side with an open end or adjustable wrench (Fig 5/2B). Adjust until the rear
squeegee blade folds equally accross the entire length, while moving the machine
slightly forward.
3. Ti
hten the two bolts on the ends while holding the center shaft with the wrench.
4. Turn machine on, lower squeegee and check drying pattern.
Fig 5/2BFig 5/2A
15

4.3 Squeegee Wheel Adjustment
4.3 The clearance between the support roller and floor with squeegee unfolded
(Factory setting) is: 0.1181099 Inches
.
Note: Some floor surfaces may require adjusting the caster washers for optimum performance.
See following page.
16
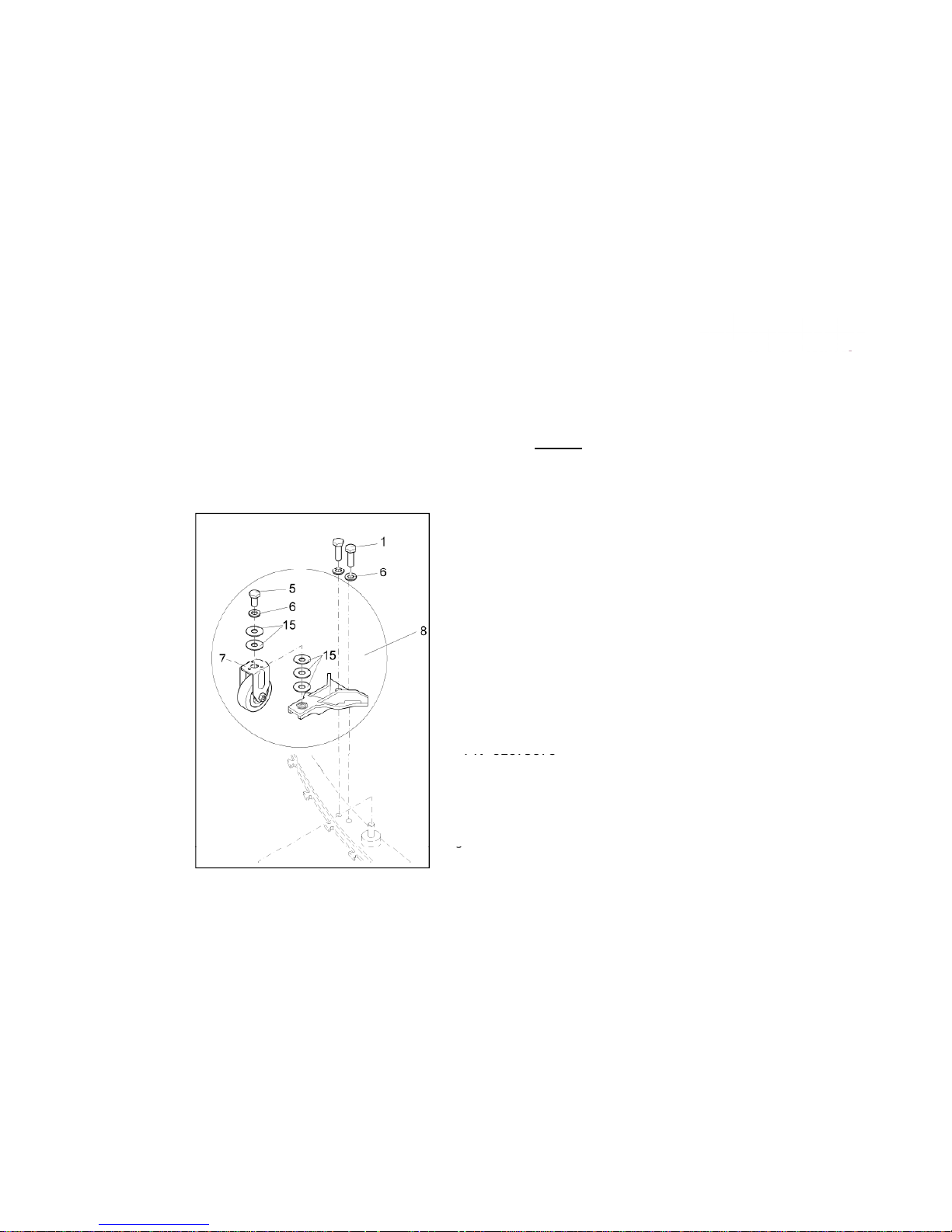
4.4 Squeegee Wheel Adjustment
4.4 Note: When adjusting the wheel height, there should always be 5 washers on each wheel
assembly position # 15 in order fully tighten bolts. Move washers from the top to the bottom of
Pos 1 – Hexagon screw M8x25 A2
PN 01059530
the bracket or visa versa when making adjustments
The caster controls the pressure on the
squeegee blade.
Pos 5 – Hexagon screw M8x16 A2
PN 01071740
Pos 6 – Washer B8,4
PN 00101550
Pos 7 – fixed Roller
PN 01077810
Pos 8 – Angle with fixed roller, complet
Pos 15 – Distance Washer
PN 01079080
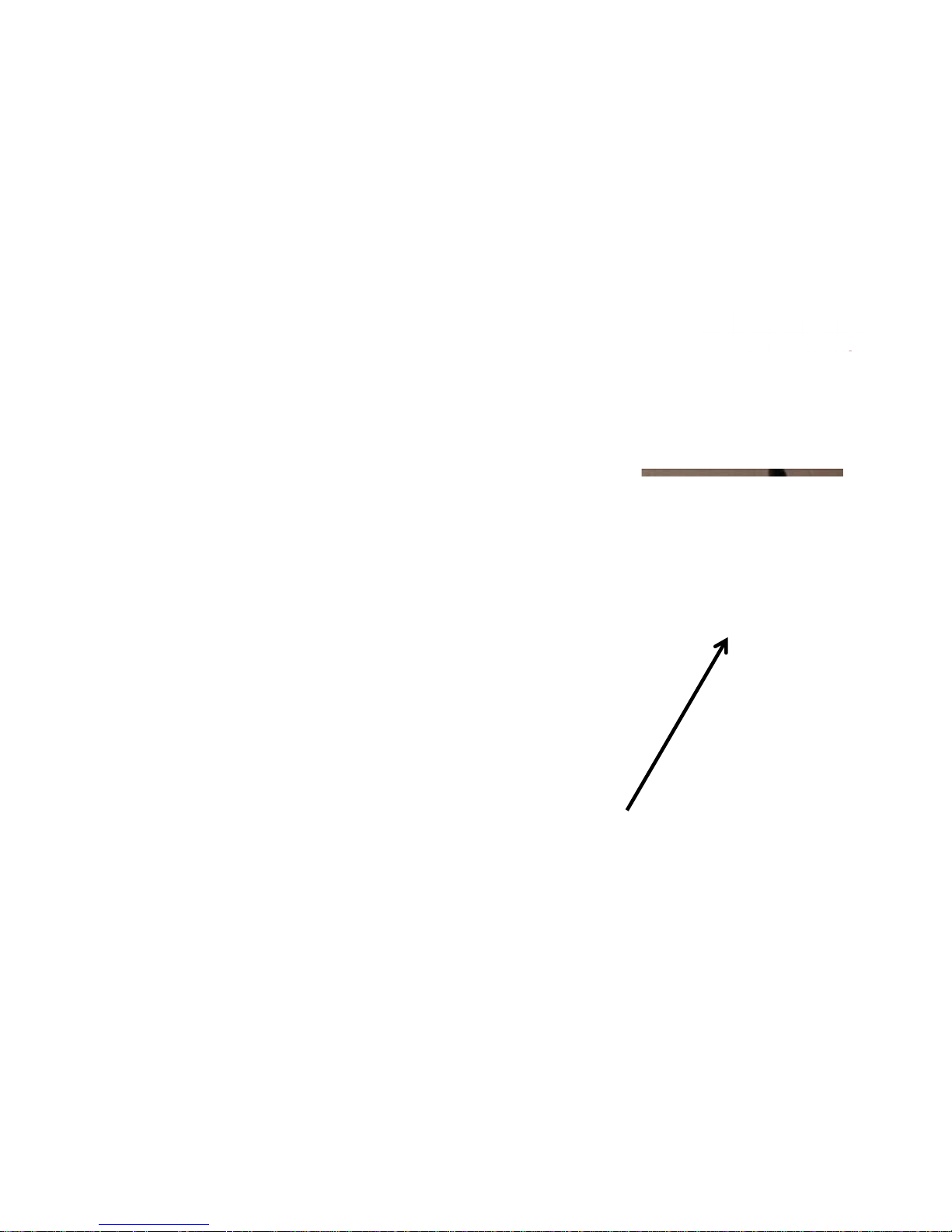
4.5 Squeegee Lift Cable, Switch & Motor
4.5 Squeegee Lift Cable, Lever, Micro Switch
•The vacuum motor micro switch is mounted
behind the squeegee lift lever (Fig. 5/4). Adjust the
micro switch so that the vacuum motor can be
turned off by lifting the squeegee by the lever.
Loosen the screws on the switch to adjust.
•Vacuum motor is switched on upon lowering of the
squeegee.
•The micro switch is a normally open switch which
is terminated to input A1.X9:3+9 on the controller.
When the squeegee is lowered, there should be
continuaty between both contacts (with the plug
A1.X9 being disconnected).
Fig. 5/4
NOTE: The squeegee lift cable spring will need to disconnected from the silver
18
lever before the squeegee lift lever plate can be removed from the machine.
Access can be made from the controller/charger area in the rear of the machine.
See Chapter 4.

5. Brush Head (Disk) Connections
onnection of Brush Motors to Disk Brush Hea
Connect the brush motors of the disk brush head in accordance with the electric diagrams. Find the
assignment of connecting stud of the motors listed in the below table. Then check the correct
direction of brush motor rotation.
The left-hand motor seen in direction of travel is M3, the right-hand one is M4.
Cable
Motor connection
Connectors
Harness
Disk brush
at the motor -M3/4
Stud bolt above
Connection N
Stud bolt below
Connection P
19
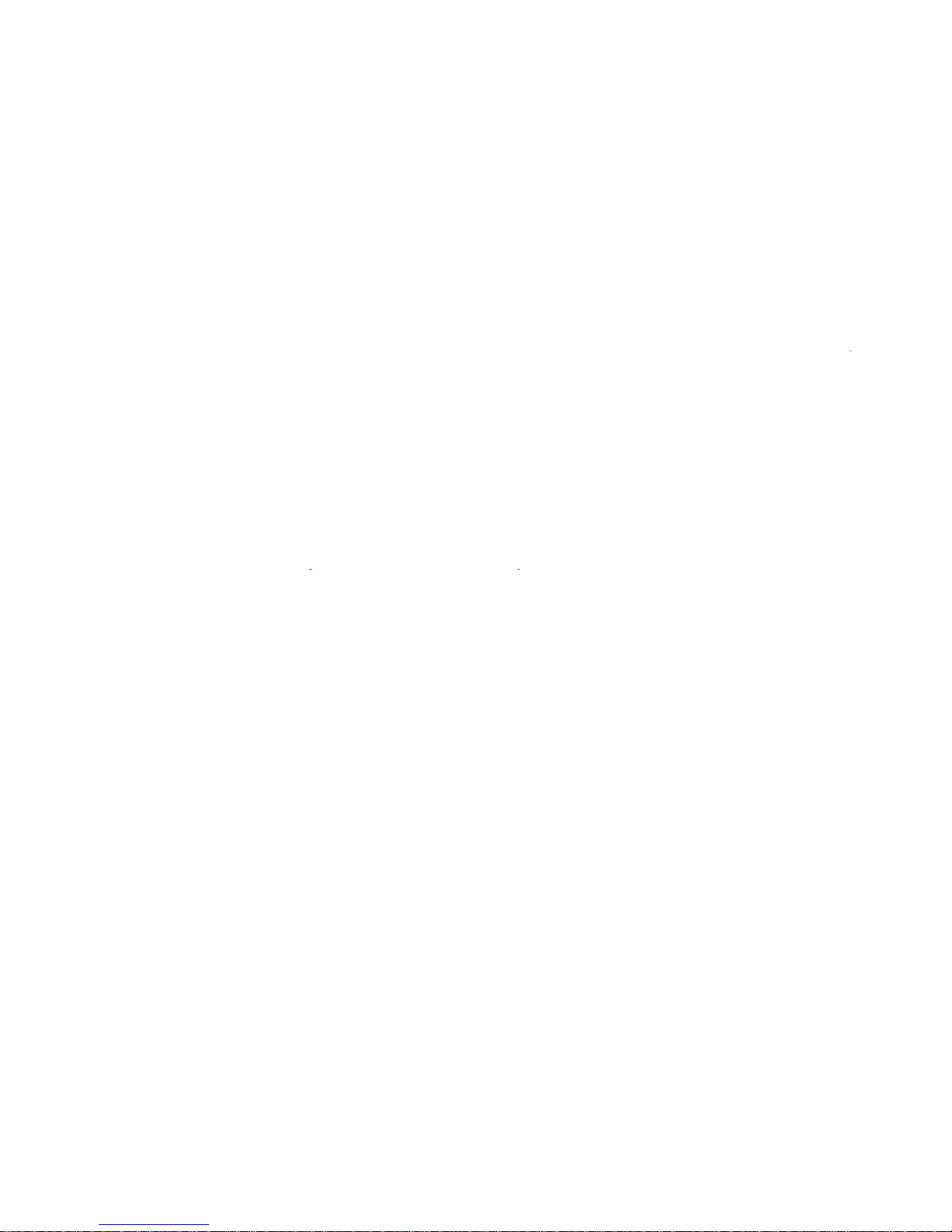
5.1 Brush Motor Information
The brush motors are switched on and off by a micro-switch located at the rear at the brush head
lift-out system. This switch is realised as NO (normally open) switch. To attain safe function of the
brush motors
correct adjustment of this switch is required.
Electric connection of the switch is realised at the central control at A1.X9:4 + 10.
Maximum current consumption of the brush motors (in practical use) must not exceed 30A per
motor on the 26 and 30“ disk brush decks. The maximum amperage for the 33“ disk decks is 40A.
Lower settings are recommended for longer motor life, run time and traction.
When checking the carbon brushes make sure that the scroll spring is pressing the carbon brush
against the commutator, does not contact the guide and that distance to carbon brush guide is
sufficient.
Replace the carbon brushes, if required.
20
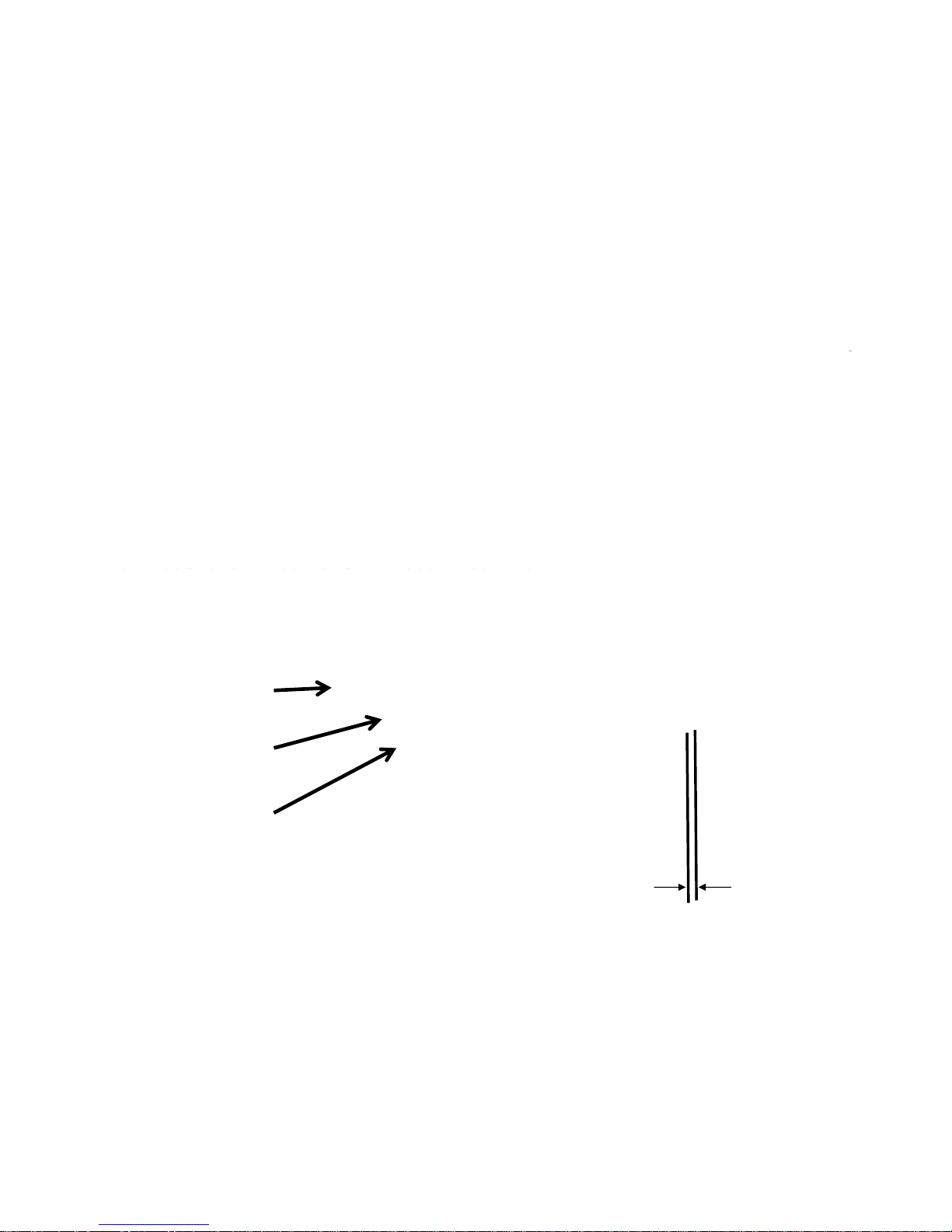
6. Brush Head
6. Brush Head Transport Position
•The lever provided is for lifting up the brush head. It features 3 positions for adjusting
the lift linkage (Fig. 6/1). The top hole is the transporting and ramp climbing position. In
this position, the lift linkage is to be adjusted so that a 1mm gap appears between the
lever and the screw head at the chassis (Fig. 6/2).
•The bottom hole (Fig. 6/1) is the normal scrubing position of the brush head.
Transport Position
Scrubbing position
with pads
Scrubbing position
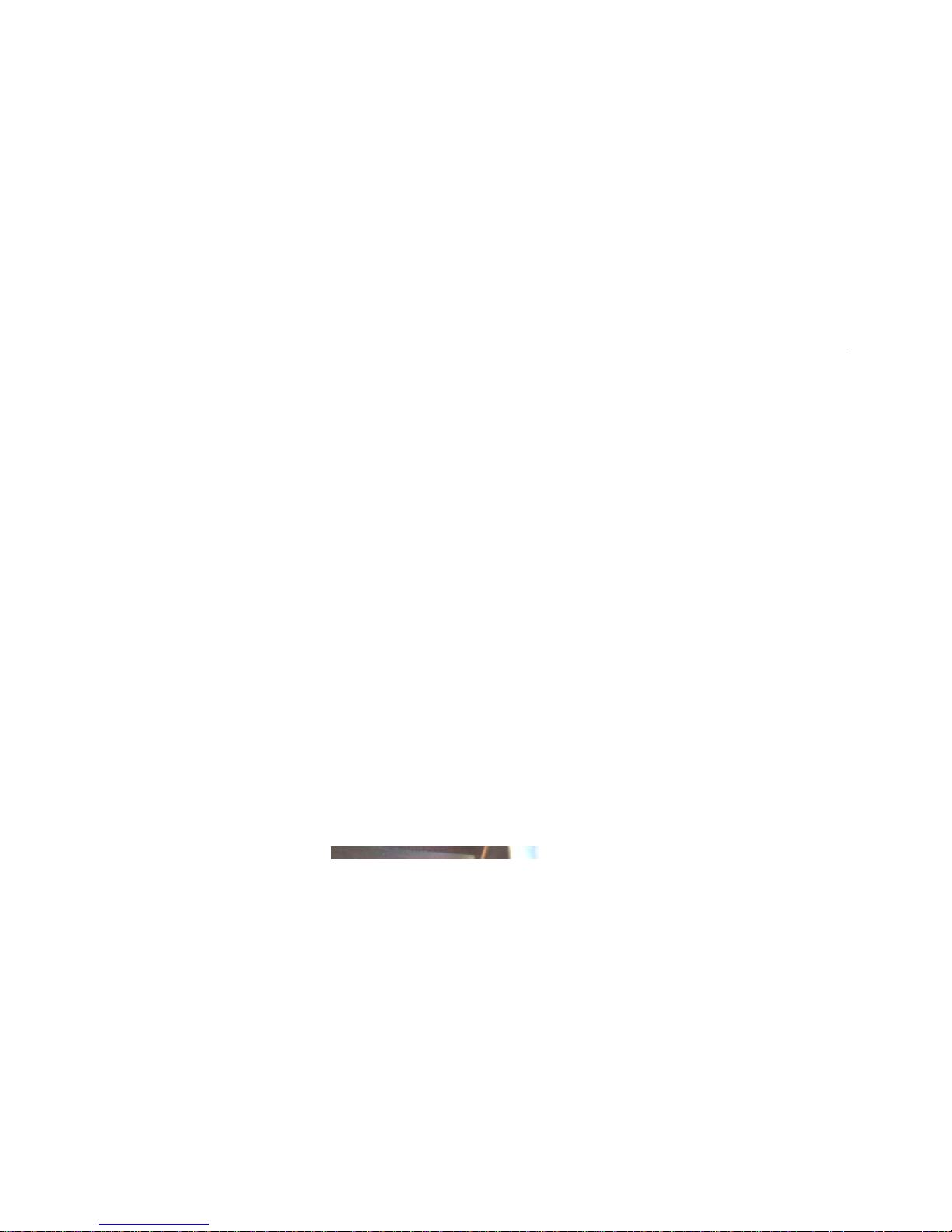
6.1 Brush Switch
6.1 Brush Switch
•The brush motors are switched on and off by a micro-switch located at the rear at the
out system Figure 6/3. This switch is a NO (normally open) switch. To
attain safe function of the brush motors, the correct adjustment of this switch is
required.
•Electric connection of the switch is connected to the central control circuit board at
up position, the switch should open and close
when brush head is lowered.
Fig. 6/3
22
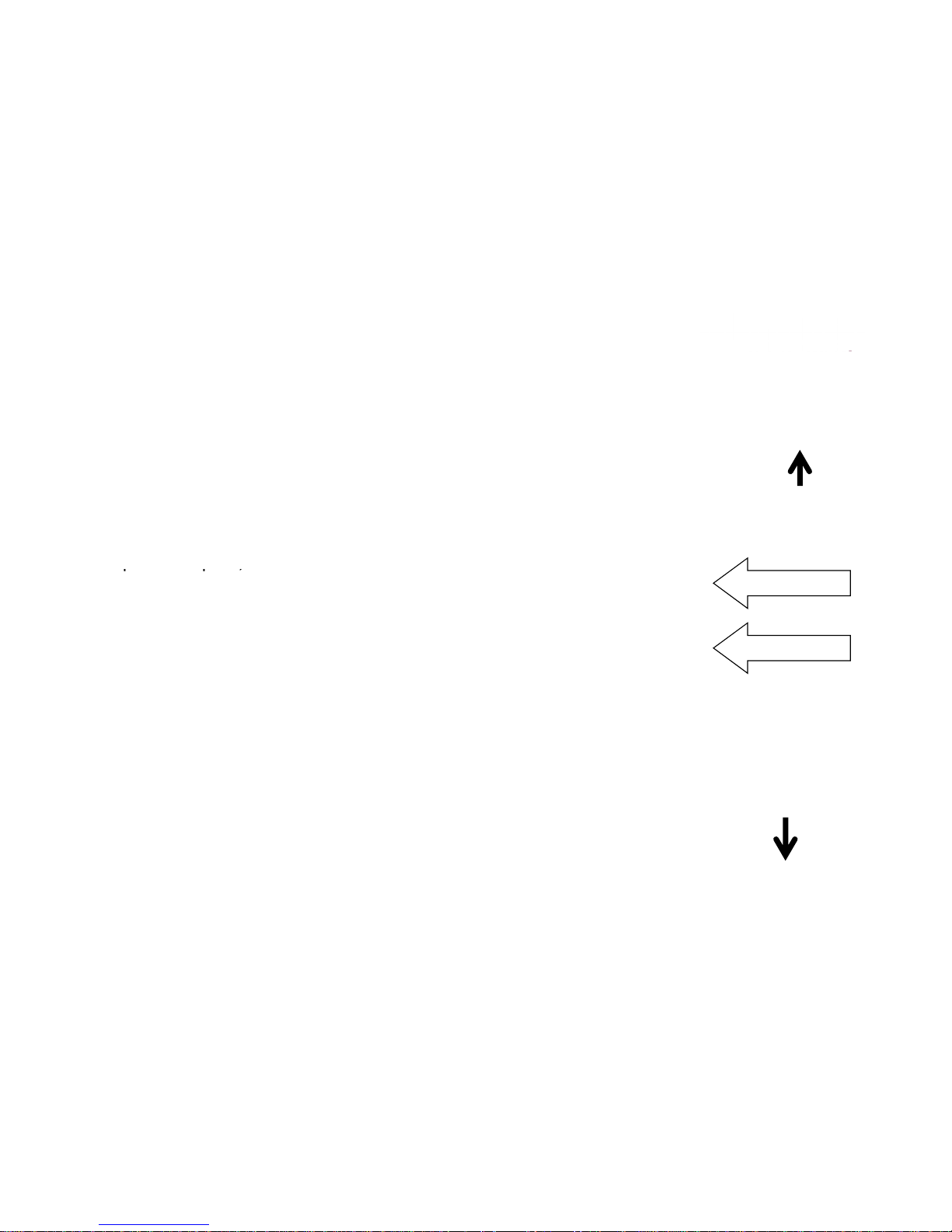
6.2 Brush Pressure Adjustment (Disk Models)
Brush Pressure Setting on Disk models.
•
The bolt on the left can be adjusted to increase or
decrease the brush pressure.
•Models with 19 gallon tanks This pressure adjustment
will affect the models in the normal scrubbing mode. (no
extra
Adjustment
Screw
Increase
pressure
•Models with 30 gallon tanks. This pressure adjustment
will only affect the models in the heavy pressure mode
only (second foot lever activated).
The indicator on the right should never be set past the
second notch.
•NOTE: When making changes, the current draw should
be less than 30 amps. per motor on the 26 and 30” disk
.
•Lower settings are recommended for longer motor life,
longer run time and traction.
•Verify the current with brushes under load, with a digital
Decrease
pressure
clamp-on meter.
•Only an authorized Minuteman Service Center should
make changes to the brush pressure setting.
23
Note: The factory setting
set at the second notch
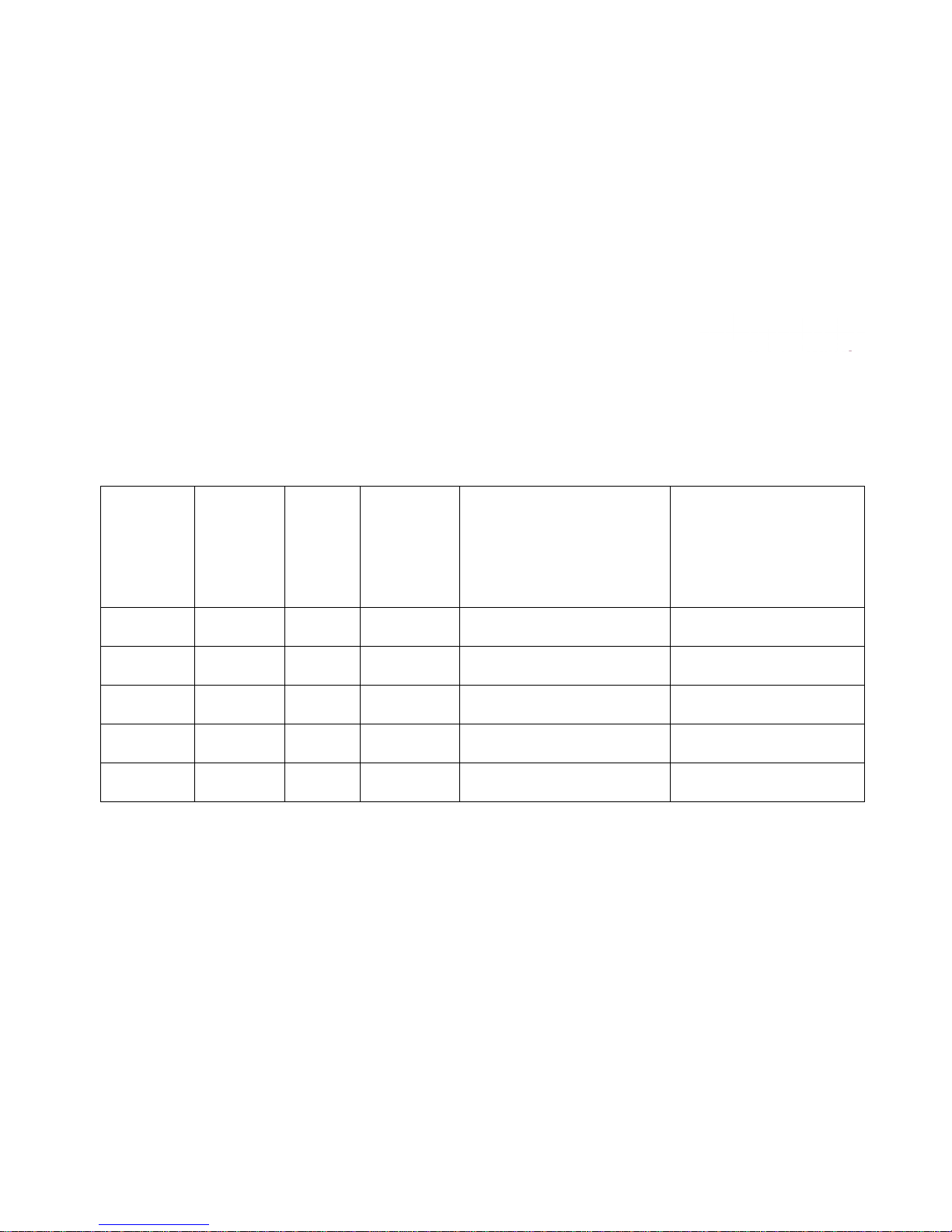
6.3 Brush Pressure (Disk Models)
Heavy
Brush
Pressure
(2nd Foot
Specific
Surface Pressure
Pressure
E3330
1055 cm²
163.525 inch²
400 N =
90 lb 600 N = 135 lb 0.19 N/cm² = .275 lbs per inch²
0.28 N/cm² = .406 lbs per
inch²
72 lb 600 N = 135 lb 0.21 N/cm² = .35 lbs per inch²
inch²
E2830
280 cm²
43.400 inch²
240 N =
54 lb NA 0.43 N/cm² = .623 lbs per inch² NA
58 lbNA0.54 N/cm = .783 lbs per inch
E26
586.5 cm²
90.908 inch²
350 N =
79 lb NA 0.3 N/cm² = .435 lbs per inch² NA
24
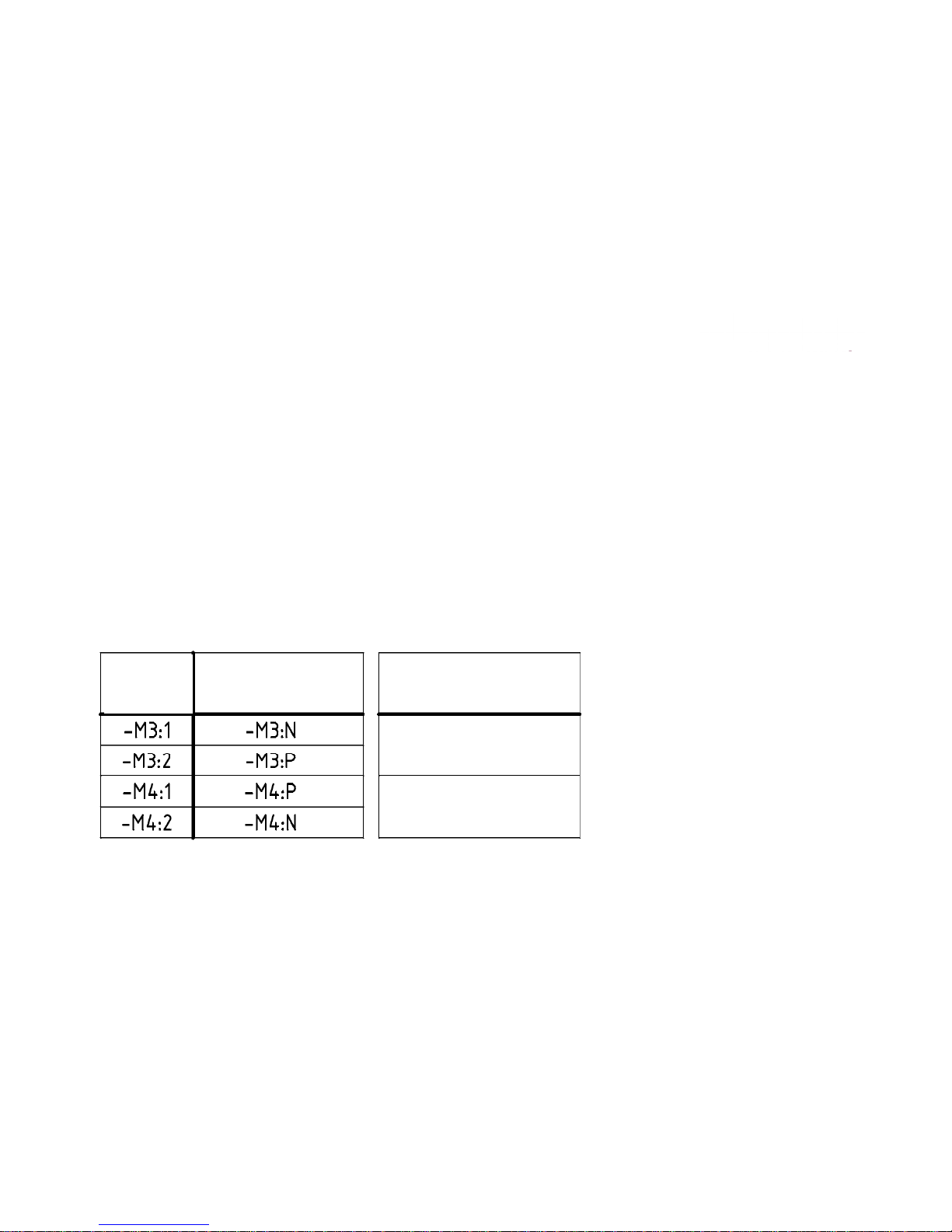
6.4 Brush Head (Cylindrical)
6.4 Electric Connections
• Connect the brush motors of the cylindrical broom head in accordance with
the electric diagrams. Find the assignment of connecting stud of the motors
listed in the below table. Then check the correct direction of brush motor
rotation.
• The left-hand motor seen in direction of travel is M3, the right-hand one is
M4.
M3 M4
Motor connection
Cyl. brush head
Cable
Harness
Connectors
at the motor -M3/4
Stud bolt above
Stud bolt below
Connection P